铜基自润滑复合材料摩擦磨损性能研究
铜基复合材料的摩擦磨损性能研究现状

n a n o t u b e s ,f r i c t i o n a nd we a r
0 引言
铜 基复 合材 料具有 较高 的强 度及 良好 的导 电导 热 性 、 减 磨 耐磨 性 、 耐蚀 性 等一系 列优 点 , 在摩 擦 减磨 材 料 、 电接触 材 料 和机 械零 件材料 等领 域发 挥着 重 要 的作 用 _ 1 ] 。随 着铜 基 复合材 料应 用 的越 来越 广 泛 , 其 对摩 擦 性 能 要 求 越 来 越 高 , 因此需 要不 断开 发耐磨 铜基 复合材 料 。 颗 粒增 强是 常见 的 在 提高 复 合 材 料 整体 强度 的 同时 还
增强体 , 利 用 微 波烧 结 技 术 制 备 出了 ( 5 ~1 5 ) T i C - ( 5 ~1 O ) C的铜基 复合 材料 , 同 时 以纯铜 试 样 作 对 比, 在 销 盘式 摩擦试 验机 上测 试两 种材 料 的摩 擦性 能 。结 果 表 明 , 纯 铜磨 损量 远大 于含增 强体 的复 合材 料 , 并且随着 T i C和 C 含 量 的增加磨 损 率 呈 降低 趋 势 。这 是 由于 随着 石 墨含 量 的
愈加严格 。综述材料的摩擦磨损 性能 , 并简述 了
目前 铜 基 复 合 材 料 存 在 的 一 些 问题 及 展 望 。
关 键 词
铜基复合材料的摩擦磨损性能研究现状_蒋娅琳

铜基复合材料的摩擦磨损性能研究现状*蒋娅琳,朱和国(南京理工大学材料科学与工程学院,南京210094)摘要 铜基复合材料具有优异的性能及广泛的应用,而随着其应用的愈加广泛,对其摩擦磨损性能的要求也愈加严格。
综述了国内外颗粒增强、石墨自润滑、纤维增强和碳纳米管增强铜基复合材料的摩擦磨损性能,并简述了目前铜基复合材料存在的一些问题及展望。
关键词 铜基复合材料 颗粒增强 石墨自润滑 碳纤维 碳纳米管 摩擦磨损中图分类号:TB333 文献标识码:AResearch Status of Friction and Wear Properties of Copper Matrix CompositesJIANG Yalin,ZHU Heguo(School of Materials Science and Engineering,Nanjing University of Science &Technology,Nanjing 210094)Abstract Reinforced copper matrix composites has excellent performance and a wide range of applications,astheir applications become more widespread,it requires better friction and wear performance.Friction and wear per-formance of copper matrix reinforced by particles,self-lubricating graphite,fibers both at home and abroad are ana-lyzed.Some existing problems and prospect of the current research status are introduced briefly.Key words copper matrix composites,particle reinforcement,self-lubricating graphite,carbon fiber,carbonnanotubes,friction and wear *国家自然科学基金面上项目(51371098) 蒋娅琳:女,1990年生,硕士生,主要从事原位合成铜基复合材料方面的研究 E-mail:983435845@qq.com 朱和国:通讯作者,男,1963年生,副教授,工学博士,主要从事铜基、铁基、钛基、铝基等原位合成复合材料方面的研究 E-mail:zhg1200@sina.com0 引言铜基复合材料具有较高的强度及良好的导电导热性、减磨耐磨性、耐蚀性等一系列优点,在摩擦减磨材料、电接触材料和机械零件材料等领域发挥着重要的作用[1,2]。
α-SiC的粒度对铜基摩擦材料摩擦磨损性能的影响
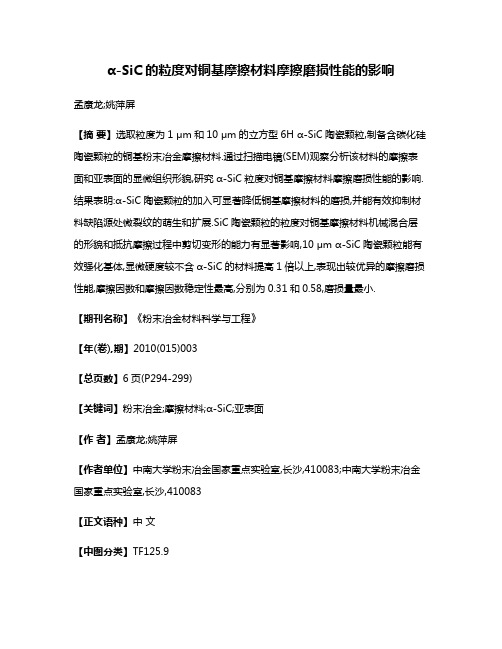
α-SiC的粒度对铜基摩擦材料摩擦磨损性能的影响孟康龙;姚萍屏【摘要】选取粒度为1 μm和10 μm的立方型6H α-SiC陶瓷颗粒,制备含碳化硅陶瓷颗粒的铜基粉末冶金摩擦材料.通过扫描电镜(SEM)观察分析该材料的摩擦表面和亚表面的显微组织形貌,研究α-SiC粒度对铜基摩擦材料摩擦磨损性能的影响.结果表明:α-SiC陶瓷颗粒的加入可显著降低铜基摩擦材料的磨损,并能有效抑制材料缺陷源处微裂纹的萌生和扩展.SiC陶瓷颗粒的粒度对铜基摩擦材料机械混合层的形貌和抵抗摩擦过程中剪切变形的能力有显著影响,10 μm α-SiC陶瓷颗粒能有效强化基体,显微硬度较不含α-SiC的材料提高1倍以上,表现出较优异的摩擦磨损性能,摩擦因数和摩擦因数稳定性最高,分别为0.31和0.58,磨损量最小.【期刊名称】《粉末冶金材料科学与工程》【年(卷),期】2010(015)003【总页数】6页(P294-299)【关键词】粉末冶金;摩擦材料;α-SiC;亚表面【作者】孟康龙;姚萍屏【作者单位】中南大学粉末冶金国家重点实验室,长沙,410083;中南大学粉末冶金国家重点实验室,长沙,410083【正文语种】中文【中图分类】TF125.9铜基粉末冶金摩擦材料具有导热性和耐热性好、摩擦因数高以及耐磨损等特点,目前已被广泛用作航空飞机和高速列车的制动材料。
铜基粉末冶金摩擦材料通常由几种甚至十几种组元组成[1], 这些组元按其作用可分为基体组元、润滑组元和摩擦组元。
SiC颗粒具有强度大、弹性模量高、热膨胀系数低和价格便宜等优点,是金属基粉末冶金摩擦材料最常使用的摩擦组元之一。
目前,SiC对铜基复合材料摩擦磨损性能的影响报道较多[2-4],但关于SiC粒度对铜基粉末冶金摩擦材料的摩擦性能的影响鲜有报道。
SiC是1种典型的多型结构化合物,迄今为止已发现160余种晶体[5]。
繁多的SiC多型体中,以6H α-SiC最为常见,其应用也最为广泛。
湿式铜基摩擦材料
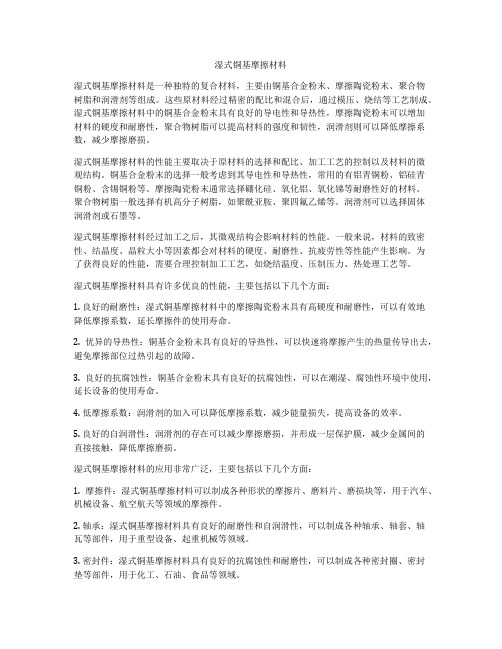
湿式铜基摩擦材料湿式铜基摩擦材料是一种独特的复合材料,主要由铜基合金粉末、摩擦陶瓷粉末、聚合物树脂和润滑剂等组成。
这些原材料经过精密的配比和混合后,通过模压、烧结等工艺制成。
湿式铜基摩擦材料中的铜基合金粉末具有良好的导电性和导热性,摩擦陶瓷粉末可以增加材料的硬度和耐磨性,聚合物树脂可以提高材料的强度和韧性,润滑剂则可以降低摩擦系数,减少摩擦磨损。
湿式铜基摩擦材料的性能主要取决于原材料的选择和配比、加工工艺的控制以及材料的微观结构。
铜基合金粉末的选择一般考虑到其导电性和导热性,常用的有铝青铜粉、铝硅青铜粉、含锡铜粉等。
摩擦陶瓷粉末通常选择硼化硅、氧化铝、氧化锑等耐磨性好的材料。
聚合物树脂一般选择有机高分子树脂,如聚酰亚胺、聚四氟乙烯等。
润滑剂可以选择固体润滑剂或石墨等。
湿式铜基摩擦材料经过加工之后,其微观结构会影响材料的性能。
一般来说,材料的致密性、结晶度、晶粒大小等因素都会对材料的硬度、耐磨性、抗疲劳性等性能产生影响。
为了获得良好的性能,需要合理控制加工工艺,如烧结温度、压制压力、热处理工艺等。
湿式铜基摩擦材料具有许多优良的性能,主要包括以下几个方面:1. 良好的耐磨性:湿式铜基摩擦材料中的摩擦陶瓷粉末具有高硬度和耐磨性,可以有效地降低摩擦系数,延长摩擦件的使用寿命。
2. 优异的导热性:铜基合金粉末具有良好的导热性,可以快速将摩擦产生的热量传导出去,避免摩擦部位过热引起的故障。
3. 良好的抗腐蚀性:铜基合金粉末具有良好的抗腐蚀性,可以在潮湿、腐蚀性环境中使用,延长设备的使用寿命。
4. 低摩擦系数:润滑剂的加入可以降低摩擦系数,减少能量损失,提高设备的效率。
5. 良好的自润滑性:润滑剂的存在可以减少摩擦磨损,并形成一层保护膜,减少金属间的直接接触,降低摩擦磨损。
湿式铜基摩擦材料的应用非常广泛,主要包括以下几个方面:1. 摩擦件:湿式铜基摩擦材料可以制成各种形状的摩擦片、磨料片、磨损块等,用于汽车、机械设备、航空航天等领域的摩擦件。
温度对Cu—Sn10—Pb10减摩复合材料摩擦磨损性能的影响

采用粉末冶金方法制造的铜基减摩复合材料
是一 种理 想 的减摩 材料 , 可制 成 滑 动轴 承 、 止推 垫
学研究已成 为摩擦学领 域的重要研究热点 一 。 J 要求相对摩擦的零部件 能长 时问工作 在高温件 。同其他工艺 ( 铸 造、 压合) 制造的零件相 比, 不仅具有摩擦系数低、 承载 能 力大 、 劳 强 度 高 、 摩 性 能 好 等 特 点 , 疲 减 而 且可节约大量贵重有色金属材料 。现代科学技 J 术的发展使得材料在不 同条件下 的摩擦、 磨损 和 润 滑 问题 日益 受 到重 视 , 殊服 役 条 件 下 的摩 擦 特
收稿 日期 : 0 2 8—0 0 ; 修 回 日期 :0 8— 9— 6 0 9— 2 20 0 1
MA h o—b , in —w i IW e —rn ,Y N Ya Sa o YU Ja e ,L i o g I n—g o X E Tn u , I ig (ntueo r o g , ee U i r t o eh o g , e i 30 9 C ia Istt f i l y H f n esy f cnl y H f 0 0 , h ) i Tb o i v i T o e2 n
o .T i t e i a ay e ef c in a d we rp o e t so t e f m o m mp rt r O5 0 . h S hss o t a d h s h ss n l z d t r t a r p r e f h m o r o t h i o n i r e e au et 0 ℃ T e r u h w t o h
了摩擦磨损特性研究 。结果表明 , 材料摩擦表面随着试验温度的升高磨损加剧 ,O 4 O℃ 时材料基体发生 严重变
铜基摩擦材料的摩擦磨损研究

铜基摩擦材料的摩擦磨损研究摩擦磨损是各种机械设备中常见的现象,也是科学家们长期以来一直在研究的问题。
在这方面,铜基摩擦材料已经成为一种特别引人注意的材料。
铜基摩擦材料在工业生产中广泛应用,具有高温下具有较强的耐磨性能、化学惰性、优异的导电性和导热性,是一种理想的摩擦材料。
本文将对铜基摩擦材料的摩擦磨损性能进行研究和探讨。
一、铜基摩擦材料的特点铜基摩擦材料是一种由铜及其合金制成的材料,具有较高的强度和硬度,同时也具有良好的加工性、焊接性能和耐腐蚀性。
铜基摩擦材料具有优异的导电性和导热性,可以应用于电气设备和焊接行业。
此外,铜基摩擦材料的化学惰性非常强,熔点低,具有良好的塑性和韧性。
二、铜基摩擦材料的摩擦磨损机理铜基摩擦材料的摩擦磨损机理主要与其微观状态有关。
摩擦磨损的主要原因是材料表面上的微观凹坑,当机件运动时会形成一定的摩擦力,使材料表面产生塑性变形和热变形,表面上的颗粒会磨损、脱落,在同等条件下,颗粒脱落越多,则表明材料的磨损越严重。
铜基摩擦材料摩擦磨损的机理是磨粒磨损和熔角磨损。
材料表面的微小颗粒形成摩擦磨损的磨料,而在微小颗粒上的热分解产物和金属离子则成为了磨损的溶剂,促进铜基摩擦材料的摩擦磨损过程。
三、铜基摩擦材料的摩擦磨损试验铜基摩擦材料的摩擦磨损试验是对材料性能进行测试的重要方法。
试验条件是由材料的使用情况决定的,影响试验结果的条件有很多,例如试验参数、操作人员、试验设备、试验环境等。
根据铜基摩擦材料的应用领域和需要进行的试验,可以选择多种试验方法,如滑动磨损试验、旋转磨损试验、劈裂试验、磨粒磨损试验及高温试验等。
四、铜基摩擦材料的改性研究铜基摩擦材料的改性研究是为了提高其摩擦磨损性能、延长其使用寿命。
改性材料的方法有很多种,如添加一些特殊材料、改变材料的晶体结构等。
添加适量的纳米粒子或纳米管可以修饰材料表面,使其抗氧化能力增强、增加其硬度和强度,从而提高其耐磨性和防腐蚀性。
利用表面处理等方法,可以改变铜基摩擦材料的摩擦磨损性能及其相应的机理。
自润滑复合材料论文-自润滑材料及其摩擦特性(精)

自润滑复合材料论文-自润滑材料及其摩擦特性摘要:自润滑复合材料是材料科学研究领域的一个重要发展方向,由于其在特殊使用条件下具有优良的摩擦学特性而受到人们的广泛关注。
本文主要介绍国内外自润滑复合材料的开发与进展,讨论了对材料摩擦学性能的影响因素。
关键词:固体润滑摩擦磨损自润滑复合材料一、前言:液态润滑(润滑油、脂是传统的润滑方式,也是应用最为广泛的一种润滑方式。
但液体润滑存在一下问题:1.高温作用下添加剂容易脱落;2。
随温度升高,其粘性下降,承载能力下降;3.高温环境下其性能衰减等问题;4。
液体润滑会增加成本,如切削加工中的切削液;5.液体润滑会造成环境污染.所以,自润滑材料已成为润滑领域的一类新材料,成为目前摩擦学领域的重要研究热点。
二、自润滑材料的种类自润滑材料一般分为金属基自润滑材料、非金属基自润滑材料和陶瓷自润滑材料。
其制备方法通常为粉末冶金法,此外,等离子喷涂、表面技术和铸造法也被应用于自润滑复合材料的制备。
1金属基自润滑材料金属基自润滑复合材料是以具有较高强度的合金作为基体,以固体润滑剂作为分散相,通过一定工艺制备而成的具有一定强度的复合材料。
目前已开发的金属基自润滑复合材料,如在铁基、镍基高温合金中添加适量的硫或硒及银基和铜基自润滑材料,都已得到一定程度的应用。
2非金属基自润滑材料非金属基自润滑材料主要是指高分子材料或高分子聚合物,如尼龙等.它在航空航天、汽车制造、电子电气、医疗和食品加工等领域得到广泛应用。
目前高分子基自润滑材料的制备途径主要是通过聚合物与聚合物共混及添加纤维、晶须等来提高基体的机械强度;通过添加各类固体自润滑剂来提高摩擦性能。
3陶瓷自润滑材料陶瓷材料以其独特的特点和优点,使得陶瓷及陶瓷复合材料的自润滑研究已经引起了较为广泛的重视。
三、自润滑减摩材料的特点、性能1 粉末冶金法制造减摩材料的特点(1在混料时可掺入各种固体润滑剂(如石墨、硫、硫化物、铅、二硫化钼、氟化钙等,以改善该材料的减摩性能;(2利用烧结材料的多孔性,可浸渍各种润滑油,或填充固体润滑剂,或热敷和滚轧改性塑料带等,使材料更具自润滑性能,减摩性能特佳;(3优良的自润滑性,使它能在润滑剂难以到达之处和难以补充加油或者不希望加油(如医药、食品、纺织等工业的场合,能安全和无油污染的使用;(4较易制得无偏析的、两种以上金属的密度差大的铜铅合金-钢背、铝铅合金-钢等双金属材料;(5材料具有多孔的特性,能减振和降低噪声;(6材质成分选择灵活性大,诸如无机材料金属及合金、非金属、化合物和有机材料聚合物等,均可加入其中,并能获得较理想的减摩性能,例如高石墨含量的固体润滑减摩材料等;(7特殊用途的减摩材料,如空气轴承、液压轴承、耐腐蚀性轴承等,更发挥了粉末冶金减摩材料的特点。
SiC_(p)Cu复合材料的研究进展

SiC p /Cu 复合材料的研究进展曾昭锋 1,2)✉,周波涛 1),熊宣雯 1),李 翔 1),李著龙 1),王国强 1)1) 汉江师范学院物理与电子工程学院,十堰 442000 2) 汉江师范学院新型功能材料制备与物性研究中心,十堰 442000✉通信作者,E-mail:****************摘 要 SiC p /Cu 颗粒增强铜基复合材料是目前金属陶瓷复合材料的研究热点。
本文简述了SiC p /Cu 颗粒增强复合材料的制备方法及优缺点,分析了影响SiC p /Cu 颗粒增强复合材料性能的主要因素,包括SiC p 颗粒含量、SiC p 颗粒尺寸及烧结工艺等方面,提出了SiC p /Cu 颗粒增强复合材料存在的问题,总结了制备方法及工艺的选择原则,并对其发展方向进行了展望。
关键词 铜基复合材料;颗粒增强;研究进展;性能分类号 TB331Research progress of SiC p /Cu compositesZENG Zhao-feng 1,2)✉, ZHOU Bo-tao 1), XIONG Xuan-wen 1), LI Xiang 1), LI Zhu-long 1), WANG Guo-qiang 1)1) School of Physics and Electronic Engineering, Hanjiang Normal University, Shiyan 442000, China2) Center for Research on the Preparation and Properties of New Function Materials, Hanjiang Normal University, Shiyan 442000, China✉Correspondingauthor,E-mail:****************ABSTRACT SiC p /Cu particle-reinforced Cu-matrix composites are the current hotspots of the metal-ceramic composites. The main preparation methods of the SiC p /Cu particle-reinforced composites were introduced in this paper and the advantages and disadvantages were compared. The main factors which affected the performance of the SiC p /Cu particle-reinforced composites were analyzed,including the content of SiC p particles, the size of SiC p particles, and the sintering process. The existing problems of the SiC p /Cu particle-reinforced composite materials were proposed. The selection principles of the preparation methods and processes were summarized, and the development direction was prospected.KEY WORDS copper matrix composites; particle reinforcement; research progress; properties金属陶瓷复合材料在现代科技和生活中显示出越来越重要的地位。
- 1、下载文档前请自行甄别文档内容的完整性,平台不提供额外的编辑、内容补充、找答案等附加服务。
- 2、"仅部分预览"的文档,不可在线预览部分如存在完整性等问题,可反馈申请退款(可完整预览的文档不适用该条件!)。
- 3、如文档侵犯您的权益,请联系客服反馈,我们会尽快为您处理(人工客服工作时间:9:00-18:30)。
铜基自润滑复合材料摩擦磨损性能研究前言随着电子技术、信息技术以及航空、航天技术等的迅猛发展,焊接电极、接触导线、轴瓦和集成电路引线框架、仪器仪表、电子通信器件中的接触元件等部件种类增多,需求量急剧增大,而且器件向高整化、高集成电路化、高密实装化等方向变化,要求材料不仅具有良好的导电性、导热性、弹性极限和韧性,而且还应具有较好的耐磨性、较高的拉伸强度、较低的热膨胀系数,并具有良好的成型性和电镀及封装性能。
很多金属材料虽然有较高的强度,但摩擦学性能较差。
采取合金化措施使硬组分分布在韧基体中,便可改善合金的摩擦学特性。
把几种各具不同特点的材料(如软金属和其他固体润滑剂)进行人工复合,构成复合材料,使各组分间能相互取长补短,从而得到力学性能、化学性能和摩擦学性能都较为理想的金属基复合材料。
铜具有很高的导电性、导热性,优良的耐腐蚀性能和工艺性能,广泛应用于电力、电工、机械制造等工业。
但是铜的屈服强度一般较低,高温下抗变形能力更低,因而限制了其进一步应用。
如何在不降低或稍降低铜的导电性等物理性能的前提下,提高铜的力学性能,是材料工作者研究的热点。
现有的铜基复合材料可分为显微复合铜合金、颗粒增强铜基复合材料及纤维增强铜基复合材料[1]。
显微复合铜合金是一种Cu-X二元合金,以其超高强度、高导电率以及良好耐热性能引起人们的重视,有望用于热交换器、推进器、焊接电板等。
颗粒增强铜基复合材料与铜基合金相比,具有更高的比强度和较好的高温强度,因而备受重视。
常用的颗粒有金属颗粒(如钢颗粒、钨颗粒等)和陶瓷颗粒(如SiC、A1 03、A1N 、TiC、TiB5 、ZrC、WC 、纳米碳管等),其中以Al2 03颗粒和SiC颗粒研究得较多。
碳纤维/铜复合材料由于综合铜的良好导电、导热性,及碳纤维的高比强度、高比模量和低热膨胀系数,具备较高的强度、良好的传导性、减摩耐摩性、耐蚀性、耐电弧烧蚀性和抗熔焊性等一系列优点,已被广泛应用于电子元件材料、滑动材料、触头材料、集成电路散热板及耐磨器件等领域口。
这类材料的性能可设计性好,可通过控制碳纤维的种类、含量及分布来获得不同的性能指标,是一类很有发展前途的新型功能材料。
主题1、铜基复合材料的研究现状1-1、SiC颗粒增强铜基复合材料SiC颗粒增强铜基复合材料的制备主要有粉末冶金法、复合电铸法、复合电沉积法等,但不能采用液态法,原因是在高温液态下铜和SiC会发生严重的化学反应口而损害增强体。
香港城市大学s.C.Wjong等应用热等静压法制备了SiC颗粒增强铜基复合材料,并测定了其耐磨性能、屈服强度和维氏硬度,虽然其耐磨性能和维氏硬度提高了,但其屈服强度却比基体铜还低。
其原因是SiC颗粒和基体铜之间在固态条件制备下既不润湿,又没有界面反应,因而界面结合太弱了,Kuen-ming Shu等采用化学镀的方法在SiC颗粒表面包覆一层铜后通过粉末冶金法制备成型,并对比了无涂层和有涂层处理两种试样的显微组织和热膨胀特性,发现有涂层的界面结合较好,而且其热膨胀系数也能得到有效的减少。
上海交通大学湛永钟等也采用化学处理工艺在SiC颗粒增强物表面均匀地包覆了一层铜,使复合材料获得紧密的界面结合,图2 2 所示为其断口形貌,有SiC颗粒脱粘的明显迹象。
经过界面改性后,发挥了SiC 颗粒的增强作用,使复合材料获得了更高的强度和硬度,而电导率只有稍许下降。
1-2、碳纤维增强铜基复合材料对碳纤维/铜基复合材料制备工艺的探讨一直是该类材料的研究热点之一。
由于碳纤维与铜之间既不润湿,在固、液态下又不发生反应,因此在制备碳纤维/铜基复合材料时,首先遇到的难题就是解决两相之间的润湿性。
目前的研究主要从两个方面来改善润湿性:在基体中加入合金元素或对碳纤维进行表面处理。
由于合金元素的加入往往会在界面处形成反应层,造成纤维的损伤,影响复合材料的力学性能及导电性能,所以常用的方法是对碳纤维进行表面处理。
目前较有成效的纤维表面处理方法是在碳纤维的表面涂覆一层金属,最常见的是用涂覆铜来改善碳纤维与铜液的润湿性,以提高复合材料的界面结合强度。
碳纤维表面镀铜的方法很多,常用的方法有化学镀铜、电镀铜和气相沉积镀铜等。
无论采用何种镀铜方法,一般都要求在镀铜前对纤维进行表面清洗及改性处理。
目前,国内天津大学的王玉林和万怡灶等、合肥工业大学的凤仪等以及国外的C.Schrank等在这方面做了大量工作。
王玉林等通过在C f/Cu复合材料的基体Cu中添加不同的合金元素(Sn、Ni、Fe)来改善界面结合强度,他们制备C f/Cu复合材料采用的方法是连续三步电沉积后真空热压,其工艺流程为:碳纤维预处理一第一步电沉积Cu一第二步电沉积一第三步电沉积Cu一真空热压。
合金元素sn、Ni、Fe 的加入由第二步电沉积来实现。
热压后的C/Cu(无中间层)、C/Cu(Ni)、C/Cu(Fe)复合材料的界面结合强度分别为40.7MPa、65.8MPa和73.7MPa。
通过正交实验发现,对C/Cu(无中间层)复合材料,当Vr=0.32、T=700℃、P= 10MPa、t=40min时,其抗拉强度最大能达到586MPa;对C/Cu(Ni)复合材料,当V{=0.35、T一750℃、P=15MPa、t=60min时,最大抗拉强度为720MPa对C/Cu(Fe)复合材料,当Vf—O.40、T=700℃、P一15MPa、t:40min时,最大抗拉强度为625MPa 。
有人设计了一套特殊的碳纤维连续电镀装置。
该装置采用3级电镀,分别用3个整流器控制,采用焦磷酸盐镀液,在合适的工艺条件及设备上,可在碳纤维表面均匀、完整地电镀上一层铜,镀铜层完全由结晶铜组成。
此碳纤维电镀设备、工艺比其他方法简单,适用于工业化生产。
C.Schrank等为了模拟纤维镀铜实验,以碳板材为基板,将碳板用氮气等离子体清理(有的试样没有清理,以作比较)后采用磁控溅射法在其上溅射了约为300nm厚的一层铜,测得铜与碳板的结合强度约为750N/cm2,进行800℃退火处理后测得其结合强度下降到约为100N/cm2,与没有经过等离子体清理的试样差不多。
分析其原因发现,镀铜层球化反应润湿现象严重。
后来改进工艺,溅射了约为100nm厚的Mo作为中间层,进行800℃退火处理后发现其结合强度约为450N/cm2,显微分析发现涂覆的铜层没有再发生球化现象,这表明用Mo作为中间层能有效阻止铜涂层的反润湿,提高碳与铜的界面结合强度,为进一步改进C f/Cu复合材料界面指明了方向。
1-3、连续siC纤维增强铜基复合材料A.Brendel等采用的纤维为SCS-6SiC纤维,其表面为富碳涂层。
他们对直接纤维涂层法和引入Ti作为中间层两种方法制得的试样进行了对比。
直接纤维涂层法是指直接在SiC纤维表面电镀一层一定厚度的铜,然后将其装入铜制的包套中,抽真空并焊封后进行热等静压成型;引入Ti作为中间层是在纤维上溅射一定厚度的Ti(通常为几十到lOOnm左右),然后溅射一定厚度的铜(用来防止钛的氧化),再在已被涂覆的纤维上电镀一定厚度的铜(其厚度可根据复合材料纤维体积分数的要求确定),最后也是按直接纤维涂层法一样进行热等静压成型。
A.Brendel等采用的分析方法为纤维顶出测试法和显微分析法。
利用纤维顶出试验能计算出界面剪切应力rd和界面摩擦应力rf,rd和rf的高低能直接反应复合材料的界面结合强度。
rd和rf越高,界面结合强度越高,则复合材料力学性能越好,反之亦然。
其测试结果表明:没有溅射Ti进行改性的界面剪切应力rd和界面摩擦应力rf均不到10MPa,纤维很容易被从基体里顶出所示,纤维和基体之间有较大的裂缝。
分析其原因可能是SiC纤维表面的富碳涂层与铜既不润湿和相互扩散,又不发生反应,这使得碳涂层犹如纤维和基体之间的润滑剂,因此纤维和基体之间的界面机械结合强度很低。
而纤维表面涂覆一层钛之后,钛和碳在一定温度下发生反应生成TiC。
这层TiC形成了一个从基体到纤维的过渡区,具有介于基体和纤维中间的物理性质,使其模量具有渐变特征,能使复合材料在受力过程中基体和纤维的承载均匀。
通过纤维顶出实验计算出涂覆钛之后的界面剪切应力和界面摩擦应力rf分别达到70MPa和54MPa,是没有涂覆Ti的界面结合强度1O倍左右,显著改善了纤维和基体之间的润湿性和界面结合情况。
另外,当载荷较高时C/Cu复合材料磨损表面塑性变形加剧且Cu和Fe富集明显,不利于发挥石墨态碳的固体润滑作用,因此C/Cu复合材料作为减摩材料不宜在40 N以上载荷下使用。
1-4石墨对混杂增强铜基复合材料摩擦磨损特性的影响近年来的研究发现,SiC、Al2O3、TiC等硬质陶瓷颗粒、晶须可显著提高复合材料的室温、高温耐磨性,而使其在汽车、航空工业获得很多应用。
然而,硬质颗粒单一增强的复合材料对配对材料的磨损较严重,且摩擦系数较大,限制了其在要求相对滑动平稳、摩擦噪音低的领域的应用。
石墨、MoS2等固体润滑剂添加到金属中可获得低的摩擦系数、低磨损率及优异的抗咬合性能。
但是,由于固体润滑颗粒的强度较低,会引起材料力学性能降低,在高载荷条件下由于发生剥层磨损而使得摩擦磨损性能下降。
近期的研究表明,使用性能不同的增强体混杂增强金属基体时,由于它们的共同作用而获得比单一增强复合材料更优异的力学和摩擦磨损特性。
因此,混杂增强复合材料的设计已成为结构功能一体化复合材料研究领域的重要方向之一。
2、碳纤维/铜基复合材料的主要制备工艺目前,碳纤维/铜基复合材料的制备方法主要有固态法(粉末冶金法、热压固结法等)和液态金属法(挤压铸造法、液态金属浸渍法、真空压力浸渍法等)2-1、粉末冶金法:粉末冶金法是一种应用较广泛的工艺方法,是将铜粉末充满在排列规整或无规则取向的短碳纤维间隙中,然后进行烧结或挤压成型,生产工艺过程见图1:用该方法制造的短碳纤维/铜复合材料具有较高的热导率以及可调节的热膨胀系数,具有良好的减磨、耐磨性能,可用做电接触材料。
但粉末冶金法制备材料,容易损伤纤维,工艺复杂,成本高,材料的导电率相对于其他制备方法偏低。
2-2、热压固结法:热压固结法是制备碳纤维复合材料的传统方法,其实质是扩散焊接,在塑性变形不大时,利用接触部位的原子在高温下相互扩散而使纤维和基体金属(铜箔叠层)结合到一起。
其中,预制片及热压过程是最重要的两个工序,直接影响复合材料中纤维的分布和界面的性能。
为了防止基体金属的氧化,热压过程必须在真空或保护性气氛下进行,其中热压温度和压力为主要工艺参数。
热压过程中,基体金属逐渐充填到增强纤维之间的间隙中,发生基体与纤维之间原子的相互扩散,形成复合材料。
在烧结过程中,由于加压烧结,避免了在粉末冶金法烧结过程中纤维回弹引起的密度下降,制得的复合材料孔洞少、致密度高、纤维分布均匀,相对粉末冶金法而言,对纤维损伤小,材料性能较好。