旋切单板干燥质量检测
旋切单板的流程

旋切单板的流程
1.原木的选材和切割。
选用具有良好纹理和结构的原木,并按照需要的尺寸和形状进行切割。
2. 旋切。
将原木固定在旋转台上,并通过旋转台的旋转将原木逐渐分解成薄片。
3. 干燥。
将旋切出的单板进行干燥处理,以保证其含水率在一定范围内。
4. 分级。
根据单板的质量和用途,对其进行分级和分类。
5. 切割。
将单板按照需要的尺寸和形状进行切割,以备后续加工使用。
6. 包装和出货。
将切好的单板进行包装,并进行出货和交付。
以上是旋切单板的基本流程,不同的生产厂家和加工工艺会有所不同,但总体流程大致相同。
旋切单板作为一种高效、节约原木、且可广泛应用于建筑和家具等领域的生产工艺,已经得到了广泛的应用和推广。
- 1 -。
旋切薄竹单板工艺

旋切薄竹单板工艺李德青1.概述随着全球木材资源的减少及我国木材代用工程的实施,资源丰富及代木性良好的竹材人造板工业在我国迅速发展起来。
我国现在已能生产竹编胶合板、竹片胶合板、竹材碎料板、竹材复合板、竹纤维板和竹刨花板等竹材人造板产品。
竹材人造板中,竹胶合板用途最广,发展较快。
我国竹胶合板主要产品有竹片胶合板、竹片木材复合板(竹木复合板)、竹席及竹编胶合板。
其中竹片胶合板和竹木复合板能在竹材原料准备及热压过程中保持竹材的天然物理性能,代木性能最好。
但所用竹片是用平压刨刨削出来的,其厚度一般大于3 ~4mm,因此制出来的竹片.胶合板、竹木复合板按最少层三层计算,其厚度也大.于10 ~12mm.而小于10 ~ 12mm的竹胶合板只能是竹席胶合板和竹编胶合板,该两种胶合板在原料准备及热压过程中,其物理性能遭到较大破坏,代替薄木板性能较差。
为此,笔者对用旋切方法制造薄竹单板的工艺加以探讨,以弥补薄竹单板胶交合板(厚度小于10mm)的空缺,提高薄竹胶合板代木性能。
2 薄竹单板旋切及应用工艺旋切薄竹单板的工艺流程劫:原料挑选→截断并去竹青→,水煮软化→定心装卡→旋切薄竹胶合板↘→剪板→干燥、涂胶、组坯、热压成型一↗↘裁边、检验人库。
薄竹贴面复合板↗2.1 原料挑选由于竹材直径小,壁薄中空且存在三度(长度方向上的尖削度、弯曲度,周向的椭圆度),为了提高旋切出材率,必须严格控制竹材的三度和壁厚。
生产实践证明,增加竹龄不仅壁厚增大,而且三度误差大大降低。
因此旋切竹材要求:竹龄在6 ~8年以上,竹材外径在120mm 以上,壁厚大于20mm,.椭圆度要大小径差小于3mm弯曲度、尖削度小于4 ~5mm/m.否则,旋切出材率太低,失去旋切意义。
2.2 截断、去竹青竹材刚性差,故旋切竹材(也称竹筒材)不能太长,一般在1.5 ~1.8m以内,并且去除虫眼、腐朽及三度误麦大的缺陷部分。
旋切竹单板主要利用竹肉部分。
因竹青较硬难吃刀、胶粘性差,所以竹筒材必须去掉外面的竹青。
加工生产胶合板的工艺流程

加工生产胶合板的工艺流程加工生产胶合板的工艺流程非常复杂,大致分为原木加工和单板加工两种流程。
其中,原木加工流程包括原木锯断、木段蒸煮、木段剥皮、单板旋切、单板干燥、单板整理、涂胶组坯、预压、热压、裁边、砂光、检验分等和包装入库。
而单板加工流程则包括单板整理、涂胶组坯、预压、热压、裁进、砂光、检验分等和包装入库。
在整个生产过程中,胶合板的加工工艺损耗是不可避免的。
这些损耗主要来自于原木锯断、单板旋切、单板干燥、单板整理、热压、裁边和砂光等环节。
这些损耗可以分为有形损耗和无形损耗两种类型。
有形损耗主要来自于加工剩余物,而无形损耗则是由于干缩和压缩等原因导致的。
原木锯断是生产胶合板的第一步,其目的是将原木按要求的长度和质量进行锯断,并截取出胶合板成品尺寸外加加工余量的长度。
原木的长度和弯曲度、缺陷等因素直接影响胶合板的出材率,同时也会产生小木段、截头和锯屑等废料。
一般来说,原木锯断损耗率在3%~10%之间。
单板旋切是生产胶合板的关键步骤之一,也是损耗最大的工序之一。
由于木段不圆度、旋切机卡头对木段两端的夹牢以及木芯损耗等原因,单板旋切产生的废料包括碎单板和木芯等。
这部分损耗率在15%~25%之间,与木段的材质、直径以及设备性能等因素有关。
单板干燥是将旋切后的单板干燥到符合胶合工艺要求的步骤。
干燥后,木材尺寸会变小,称为干缩。
干缩损耗与单板的树种、含水率以及厚度等因素有关,一般在4%~10%之间。
单板整理包括剪切、拼板和修补等步骤。
该工序产生的废料量与原木材质、旋切单板质量、干燥单板质量以及操作工人对单板标准的熟悉程度等因素有关,损耗率一般在4%~16%之间。
直接进口单板加工成胶合板的该工序损耗率一般为2%~11%。
热压是一种将涂胶组坯好的板坯通过一定温度和压力牢固地胶合起来的工艺。
在热压过程中,随着板坯温度和含水率的变化,木材逐渐被压缩,板坯厚度也逐渐减少。
这种损耗被称为压缩损耗,其损耗率一般在3%至8%之间,具体取决于胶合板的热压温度、单位压力、热压时间、树种和含水率等因素。
看《人造板工艺学》(1)
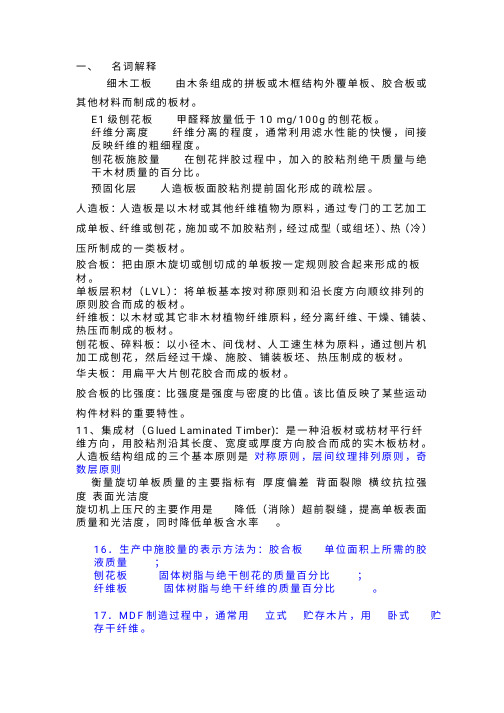
一、名词解释细木工板 由木条组成的拼板或木框结构外覆单板、胶合板或其他材料而制成的板材。
E1级刨花板 甲醛释放量低于10mg/100g的刨花板。
纤维分离度 纤维分离的程度,通常利用滤水性能的快慢,间接反映纤维的粗细程度。
刨花板施胶量 在刨花拌胶过程中,加入的胶粘剂绝干质量与绝干木材质量的百分比。
预固化层 人造板板面胶粘剂提前固化形成的疏松层。
人造板:人造板是以木材或其他纤维植物为原料,通过专门的工艺加工成单板、纤维或刨花,施加或不加胶粘剂,经过成型(或组坯)、热(冷)压所制成的一类板材。
胶合板:把由原木旋切或刨切成的单板按一定规则胶合起来形成的板材。
单板层积材(L V L):将单板基本按对称原则和沿长度方向顺纹排列的原则胶合而成的板材。
纤维板:以木材或其它非木材植物纤维原料,经分离纤维、干燥、铺装、热压而制成的板材。
刨花板、碎料板:以小径木、间伐材、人工速生林为原料,通过刨片机加工成刨花,然后经过干燥、施胶、铺装板坯、热压制成的板材。
华夫板:用扁平大片刨花胶合而成的板材。
胶合板的比强度:比强度是强度与密度的比值。
该比值反映了某些运动构件材料的重要特性。
11、集成材(G l u e dL a mi n a t e dT i mb e r):是一种沿板材或枋材平行纤维方向,用胶粘剂沿其长度、宽度或厚度方向胶合而成的实木板枋材。
人造板结构组成的三个基本原则是对称原则,层间纹理排列原则,奇数层原则衡量旋切单板质量的主要指标有厚度偏差背面裂隙横纹抗拉强度表面光洁度旋切机上压尺的主要作用是降低(消除)超前裂缝,提高单板表面质量和光洁度,同时降低单板含水率。
16.生产中施胶量的表示方法为:胶合板单位面积上所需的胶液质量;刨花板固体树脂与绝干刨花的质量百分比;纤维板固体树脂与绝干纤维的质量百分比。
17.MD F制造过程中,通常用立式贮存木片,用卧式贮存干纤维。
18.刨花板、纤维板板坯常用的成型方法有机械成型和气流成型。
中山杉旋切单板质量评价

ZHU Yuehua1, PAN Biao1∗, YU Chaoguang2, YIN Yunlong2, ZHANG Yaoli1
(1. College of Materials Science and Engineering, Nanjing Forestry University, Nanjing 210037, China; 2. Insitute of Botany, Jiangsu Province and Chinese Academy of Sciences, Nanjing 210014, China)
摘 要:中山杉是江苏省中国科学院植物研究所经人工杂交培育出来的优良树种,在使用过程中易干裂、翘曲变 形。 本研究对中山杉旋切单板的质量进行评价,为中山杉单板类人造板材的开发利用提供依据。 测试了单板的 厚度偏差、背面裂隙,并用高分辨率三维扫描技术测定了单板的变形程度,研究结果表明:中山杉原木边材部分 旋切单板厚度公差为-0.12 ~ +0.15,单板背面裂隙率为 49.22%,单板变形程度平均 21.18%;心边材转化部分旋 切单板厚度公差为-0.17 ~ +0.17,单板背面裂隙率为 53.69%,单板变形程度平均 28.20%;心材近髓心部分旋切 单板厚度公差为-0.38 ~ +0.76,单板背面裂隙率为 55.85%,单板变形程度平均 40.88%;单板厚度公差、单板背面 裂隙率及单板变形程度从小到大依次为边材部分单板、心边材转化部分单板、心材近髓心部分单板。 采用无卡 轴旋切机旋切出的中山杉单板,其边材至心边材转化部分的旋切单板厚度公差达到 LY / T 1599—2011《 旋切单 板》 的要求;单板背面裂隙率小于人工林杨木单板,满足工业生产需求;中山杉单板变形程度大于人 工 林 杨 木单 板;高分辨率三维扫描技术评价单板变形程度的方法是可行的。 关键词:中山杉单板;3D 扫描技术;厚度;背面裂隙;变形 中图分类号:S784 文献标志码:A 文章编号:2096-1359(2019)04-0047-06
竹单板旋切工艺简介

进行蒸煮处理.其目的有 3 () 个:1软化竹材, 增加 竹材塑性;2减小旋切力, () 保护旋刀;3浸提出竹 () 材中的淀粉和糖类等有机物, 加人防腐剂和防霉剂
等.
竹材蒸煮的方法是将截好的竹段放入 4 - 0
5℃的水中浸泡 6 1h 0 一 0 后逐渐缓慢升温,升温速 度以 4 5 / 为宜 ,温度升至 8 - 2℃后保温 一c h C 0- 0 1 1 h然后 自 - 2, 然冷却到 5 - 0 0 7℃即可出池旋切 蒸 煮的温度选择非常重要, 太低竹材软化不充分, 旋 切困难, 容易出现断板现象; 温度太高, 竹材纤维间
(i ag o Poe i S c Gop id pn, a Xnag 00Ci ) Xn n W d csn t k u L t Cm ayHnn yn 440, a y o r sg o r ie o m e i 6 h n
, 概述
人造板薄木贴面是 目前较受欢迎的一种高档
装饰方法. 将具有漂亮纹理的木材旋切或刨切成薄 木贴覆在人造板上能给人以清新自 然, 真实淡雅的
的结合力被破坏 , 旋切的竹单板的质量差.值得注
竹单板旋切工艺流程如图 1 :
2 1 选材 .
生产竹单板的主要原料是楠竹.竹子径级小 ,
意的是出池的温度必须在 5 - , 0 0 低于50, 70 C 0 软 C 化的竹材变硬, 旋切变得困难; 7c, 高于 0 塑性太大 C
尖削度大, 中空, 壁薄, 为了提高生产效率, 旋出高
整.干燥后的竹单板含 水率应控制在 1} a 0 2 - % 1 26 剪切拼花 .
竹单板经干燥处理后, 为了增加装饰效果, 将竹 单板剪切成不同长度,大小和角度的单板块.剪切 后的竹单板应符合规定的尺寸要求 ,切 口整齐干 净.另外剪切时还必须剪去不符合质量要求的缺陷 部分.竹单板的剪切最好选用机械剪板机,因为这 种剪板机容易人为控制, 适合不连续人工操作. 一 剪切好的单板块按用户要求或美术设计的图案 拼接成一定幅面.目 前,拼接的方法主要是手工拼 接.在操作台上使用电熨斗, 胶带纸, 可以将剪切好 的单板块按图案要求胶拼成一定幅面待用,也可以 将单板块直接贴在涂过树脂胶的基材上.
建筑模板的生产制度

建筑模板的生产制度建筑模板在建筑工程中扮演着重要的角色,它是施工过程中必不可少的一种材料。
建筑模板的生产过程需要严格按照一定的制度进行,以确保模板的质量和使用效果。
本文将详细介绍建筑模板的生产制度。
一、原材料采购与检验制度1. 原材料采购:建筑模板的原材料主要是木材,应选择优质的桉木原木。
采购时应根据生产需求,合理预算锯断长度,确保资源的合理利用。
2. 原材料检验:原木进入工厂后,应进行严格的检验,包括检查原木的纹理、直径、含水率等。
只有符合要求的原木才能进入下一道生产工序。
二、单板切割与干燥制度1. 单板切割:利用精密的旋切机将原木切割成单板。
切割过程中应根据模板的尺寸大小,将单板裁切成比例相同的木层,并清除表面的杂质。
2. 单板干燥:切割后的单板含有较高的水分,应利用天然阳光大型晒场进行自然晾干,或通过木材烘干机进行烘干处理。
干燥后的单板应保持一定的韧性,以确保在后续的生产过程中不易断裂。
三、单板涂胶与组坯制度1. 单板涂胶:采用精密的四辊涂胶机将胶均匀涂抹在单板表面。
涂胶过程中应确保每张单板涂胶均匀,以达到最高的胶合强度。
2. 组坯:将涂有胶层的单板按照横竖交错的方式组合成模板层。
组坯过程中应确保模板层的层数符合设计要求,以保证模板的整体性能。
四、坯板热压成型制度1. 预压:将组坯后的模板层通过预压工艺,使其初步成型,降低坯板错位的几率。
2. 热压:采用合理的压力和温度对模板层进行热压,使其充分粘合,提高模板的密实度和硬度。
热压过程中应严格控制温度和压力,确保模板的质量。
五、裁边质检与包装制度1. 裁边:利用精密的纵横裁边机将热压成型的毛坯板裁切成所需的尺寸。
裁边过程中应确保模板的尺寸精确,满足施工需求。
2. 质检:对裁边后的模板进行质量检验,检查模板的平整度、强度、粘合度等指标。
只有符合标准的模板才能进入包装环节。
3. 包装:将检验合格的模板进行包装,防止在运输和储存过程中受到损坏。
包装过程中应确保模板的包装牢固,便于长途运输。
影响单板出板率的因素及优化措施
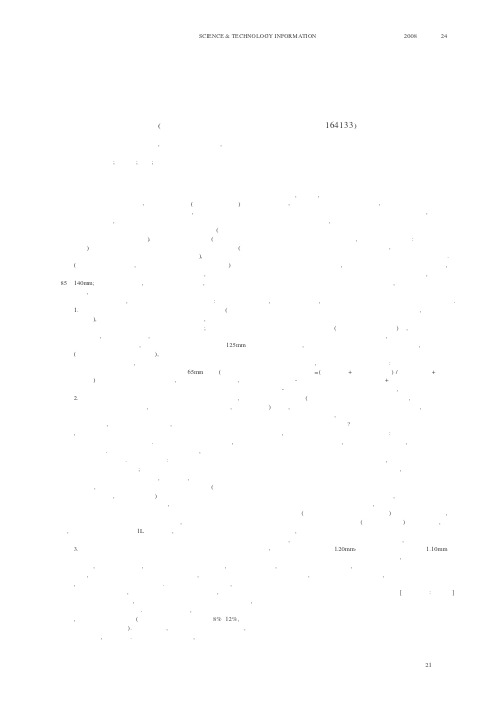
科技信息2008年第24期SCIENCE&TECHNO LO GY INFORMATION提高单板出板率是合理利用木材资源和降低产品成本的重要措施之一。
提高旋切单板的体积,减少无用的材积(如缩小木芯直径)是一个重要方面。
提高单板旋切质量。
减小厚度偏差,减小实际厚度和单板名义厚度之间差值,也是提高单板出板率的一个主要方面。
木段在旋切时可分成四大部分。
第一部分是由于木段形状不规则(木段弯曲、尖削度和木段横断面形状不规则).而形成的碎单板部分(其长度小于木段的长度)。
第二部分是由于木段在旋切机的卡轴上安装不正确(即木段最大内切圆柱体的轴线与卡轴中心线没有重合),而引起的长单板部分(其长度为木段的长度,但其宽度小于旋切木段的圆周长)。
第三部分是连续的单板带部分。
第四部分剩余的木芯部分,一般木芯直径为85—140m m;但木段直径大时,则木芯直径必须增大,以利于旋切。
可见,在旋切时产生了一定量的碎单板、窄长单板和木芯等。
为了提高有用单板的出材率,在木材加工时可采用下列措施:1.减小木芯直径。
改善木段在旋切机卡轴上的安装基准(即正确定中心和上木),在大型旋切机上要直接减小木芯直径,可采用双卡头带压辊的旋切机。
最初旋切时大小卡头一起卡住木段;当直径变小接近大卡头直径时,大卡头退出木段,而小卡头继续卡住木段进行旋切。
为了避免木段旋切时发生弯曲,一般当旋切木段直径减小到125mm左右时(依木段树种、材质、长度而定),压辊可以自动地在木段的上部和相对于旋刀位置压住木段,防止木段向上和离开旋刀的方向发生弯曲。
这样同一台旋切机上可将木芯直接旋到65m m左右(依木段长度和材质而定)。
为了使木段转动阻矩减小,有利于缩小木芯直径,可采用动力压辊和动力压尺。
2.合理组织单板挑选流水线。
要减小厚单板干燥后的变形,可用带齿压尺在单板正面刺上齿痕,消除背面裂缝引起的不平衡,这种处理称为单板木芯锯断再旋有些木段由于带有心腐、开裂等缺陷不能直接减小木芯直径,可把这部分缺陷断去,在专用的小型旋切机上进行旋切,得到的单板可作为大幅面胶合板芯板或制成小幅面胶合板。
- 1、下载文档前请自行甄别文档内容的完整性,平台不提供额外的编辑、内容补充、找答案等附加服务。
- 2、"仅部分预览"的文档,不可在线预览部分如存在完整性等问题,可反馈申请退款(可完整预览的文档不适用该条件!)。
- 3、如文档侵犯您的权益,请联系客服反馈,我们会尽快为您处理(人工客服工作时间:9:00-18:30)。
评定长度:1L-5L(可选) ,L 为取样长度 4.3.3 测量方法 打开并确认粗糙度仪处于正常工作状态,选择测量位置,调整好粗糙度仪与单板的相对位置,使粗 糙度仪触针沿被测表面缓慢滑行, 触针的上下位移量由电学式长度传感器转换为电信号, 经放大、 滤波、 计算后由显示仪表指示出表面粗糙度数值, 也可用记录器记录被测截面轮廓曲线, 或用电子计算机自动 计算出 Ra、Rz 和 Ry。 测量参数:Ra:轮廓算术平均偏差,单位为:毫米(mm) ; Rz:微观不平度十点高度,单位为:毫米(mm) ; Ry:轮廓最大高度,单位为:毫米(mm) 。 4.4 翘曲变形 4.4.1 仪器 尺子:长度≥2000mm,精度≥1mm。 4.4.2 试样 4.4.2.1 质量要求 试件须表面平整,厚度均匀且没有节子、开裂、腐朽等缺 陷。 4.4.2.2 规格 参考 KL/T 1599-2011 4.4.3 计算
4.5.2 试样 4.8.2.1 质量要求 试件须表面平整,厚度均匀且没有节子、开裂、腐朽等缺陷。 4.8.2.2 规格 参考 KL/T 1599-2011 4.5.3 计算 开裂条数 开裂延长度 4.5.4 测量方法 开裂的测量:采用卷尺进行测量,干燥前对开裂进行标记,干燥后测量开裂增加的条数以及开裂的增长 量。 4.6 干燥单板背面裂隙度 4.6.1 仪器 4.6.1.1 绘图用墨水,可以是黑色,也可以是蓝色。 4.6.1.2 显微镜,性能指标。 4.6.1.3 切刀 4.6.2 试件规格与数量 在单板条上截取大小 100 mm ×100 mm 各 20 块作为检测试件, 4.6.3 干燥单板背面裂隙度计算
4.2 干燥单板的接触角 4.2.1 仪器 接触角测定仪 性能:测试分辨率:0.01° 测试精度: 0.1° 4.2.2 试样 4.2.2.1 质量要求 试件须表面平整,厚度均匀且没有节子、开裂、腐朽等缺陷。 4.2.2.2 规格 试样规格约为:110mm×30 mm×干燥单板厚度 (长×宽×厚) 4.2.3 测量方法 测试条件:实验室环境温度为 28±2 ℃,环境湿度 35±2%。 首先用纯水清洗微型注射器, 然后将待测液体注入注射器中, 然后将样品表面灰尘和木粉清理干净 后置入注射器下方的样品台上,调整注射器的位置,使其高度距试件 3~4 厘米高。设定接触角测定仪 的参数,调整注射器每次滴出胶滴的体积为 4 ul,胶滴滴出的速度为 1.00 ul/s,测试时间为 80 s。 4.3 单板背面粗糙度 4.3.1 仪器 粗糙度仪(很好,要对之前的标准进行修订! ! ! ) 性能: 测量范围 显示范围 Ra:0.025-12.5μ m Ra、Rq:0.005-16μ m, Rz、Ry、Rt、Rp、Rv、Rmax、R3z:0.02-160μ m 量程范围:±20μ m、±40μ m、±80μ m 最高显示分辨率:0.001μ m 示值误差:≤±10% 示值变动性:≤6% 工作环境温度:0ºC- 40ºC,相对湿度:<90% 4.3.2 取样 规格:100mm(纤维方向)×20mm(垂直纤维方向) 取样长度:0.25mm、0.8mm、2.5mm、自动
3 术语与定义
下列术语和定义适合于本文件。
3.1
干燥单板的终含水率 也可称为单板绝对终含水率,是单板中所含水分的质量占单板绝干质量的百分数。
3.2
干燥单板终含水率分布 指在干燥单板的含水率测量区域内,各个测定点的含水率散布状况。
3.3
干燥单板平均终含水率 指在干燥单板的含水率测量区域内,各个测定点的含水率的平均值。
3.7
干燥翘曲变形 单板翘曲是单板未按照原有的形状成形, 却因外力作用而表面发生的不均匀收缩的扭转变形; 单板 中间部分隆起,俗称“大肚皮”的缺陷;单板的端部呈现波浪形的变形,俗称“荷叶边”的缺陷。
3.8
单板开裂 单板受内应力、外部冲击或环境条件等的影响而在其表面或内部所产生的裂纹。
3.9
单板背面裂隙 单板背面在各种应力作用下,破裂变形而产生的无明显位移的裂缝,以裂隙率表示。
L=
∑h × 100% n⋅h
式中:L—干燥单板上的平均裂隙度,%; h—在一定长度的干燥单板上,各个裂隙深度,单位是:毫米(mm) ; ∑—求和; n—在一定长度的干燥单板上,裂隙的个数; S—干燥单板的厚度,单位为:毫米(mm) 。 4.6.4 检测方法 (1)清洁单板背面,去除毛刺等; (2)将试样的含水调整至 30%左右; (3)以适量的绘图墨水涂于单板背面,干后沿试件横纤维方向切开,观察裂隙的特征;
(4)用 10 倍放大镜测定 30 mm 长度范围内单板断面上的裂隙深度和条数。 4.7 厚度偏差 4.7.1 设备仪器:螺旋测微器 4.7.2 试件:在单板上截取 80mm 宽的单板条作为检测试件 4.7.3 计算: S X X S—单板厚度偏差
X —单板实测厚度的平均值
X —单板名义厚度
3.4
干燥单板终含水率均匀性
指在干燥单板的含水率测量区域内,衡量各个测点之间的含水率的范围。
3.5 接触角
接触角是指在单板的水平平面上滴一液滴, 固体表面上的固-液-气三相交界点处, 其气-液界面和固 -液界面两切线把液相夹在其中时所成的角,是湿润程度的量度。
3.6
干燥单板背面粗糙度 木制件表面粗糙度是表征各种加工方法在木制件表面留下的具有较小间距的峰和谷组成的微观几 何形状误差。
3.10
单板厚度偏差 单板在刨切过程中会出现反向弯曲,使其背面的纤维劈裂,产生的裂隙以裂隙率表示。
3.11
干燥单板残余干燥应力 是单板在干燥过程中由于横切面上含水率分布的不均匀和单板构造上的各向异性引起的单板内应 力。
3.12ห้องสมุดไป่ตู้
干燥单板横纹抗拉强度 表征干燥单板最大均匀塑性变形的抗力。
4 质量检测方法
2 引用标准
下列文件对于本文件的应用是必不可少的。凡是注日期的应用文件,仅注日期的版本适用于本文 件。凡是不注日期的引用文件,其最新版本(包括所有的修改单)适用于本文件。 GB 12472(—90)木制件表面粗糙度参数及其数值 GB/T 6491—2012 锯材干燥质量(残余应力、含水率) LY/T 1599—2011 旋切单板
4.1 单板终含水率(均匀性、平均终含水率、终含水率分布、终含水率均匀性) 4.1.1 称重法测量单板含水率 4.1.1.1 单板样本取样及编号 干燥单板的规格参考 LY/T 1599—2011,每种厚度的单板,随机选取 2 张幅面尺寸符合规定的优质 单板,在每张单板上按照图 1 所示位置,选取试样,制备规格约为 100mm×100mm 左右的单板试样。
V S / X 100% S
V—单板厚度变动系数
w
2
n 1
w Xi X
X —单板实测厚度的平均值
X i —单板实测厚度,i 取值是 1,2,3
4.7.4 检测方法: 在旋切好的单板横纹方向上截取 80mm 宽的单板条作为检测试件,用螺旋测微器分别测量三点的单板 厚度,即距离单板条左右两端 100mm 处和中心处,按照公式进行计算。 4.8 残余干燥应力 4.8.1 设备与仪器:游标卡尺(精度为 0.1mm,量程为 10mm~200mm) 切片刀干燥箱 4.8.2 试样:
LY/T 2016-LY-184
旋切单板干燥质量检测方法
Detection method of rotary veneer drying quality
(征求意见稿)
× × × × -× × -× × 发布
× × × × -× × -× × 实施
国家林业局发布
LY/T× × × × —× × × ×
γ=
H L
× 100%
式中:γ —干燥单板翘曲度; H—干燥前后单板端部最大拱高,单位为:毫米(mm) ; L—干燥前后单板横纹方向的水平尺寸,单位为:毫米(mm) 。 图 2 翘曲变形
4.4.4 测量方法 (1)将单板平放于水平操作台面上; (2)用尺子量取单板的横纹方向的水平尺寸,L,如图 2 所示; (3)量取单板端部最大拱高尺寸,H,如图 2 所示。 4.5 开裂 4.5.1 仪器 尺子:长度≥2000mm,精度≥1mm。
本标准由国家林业局归口。 本标准负责起草单位:北京林业大学、山东省费县金利旋切机械厂。 本标准参加起草单位:江苏省旁氏木业集团有限公司 本标准主要起草人:王天龙、伊松林、朱景振、庞树贵、曹友霖、何正斌马青、徐敏、安大昆。
LY/T× × × × —× × × ×
旋切单板干燥质量检测方法
1 范围
本标准规定了单板干燥的终含水率及其分布状况、干燥单板背面裂隙、干燥单板开裂、干燥单板背 面裂隙度、干燥单板背面粗糙度、或表面平整度、干燥翘曲变形、干燥单板横纹抗拉强度、干燥单板的 接触角、干燥单板横纹弹性模量、干燥单板残余干燥应力、单板厚度偏差等等的干燥质量等干燥质量检 测规则。 本标准适合于各种用途的干燥的旋切单板。
前言
单板干燥是胶合板生产过程中的一个重要工序。 单板干燥的终含水率及其分布状况、 干燥单板背面 裂隙、干燥单板开裂、干燥单板背面裂隙度、干燥单板背面粗糙度、或表面平整度、干燥翘曲变形、干 燥单板横纹抗拉强度、干燥单板的接触角、干燥单板横纹弹性模量、干燥单板残余干燥应力、单板厚度 偏差等等的干燥质量。一方面,干燥单板的质量会直接影响胶合板的产品质量,如会造成胶合板脱胶、 变形、开裂等产品缺陷,不仅造成能源浪费,产量减少,成本增加,而且也会因单板表面出现局部碳化 或纤维的物理性能受损而危及胶合板产品质量;另一方面,在直接进行单板销售和使用的生产商、销售 商、用户和消费者之间,建立对干燥单板干燥质量所包括的主要内容及其检测方法的统一认知,对缓解 和解决供需双方的矛盾,具有积极意义。 因此本标准在基本原则与国家有关标准、 规定一致的前提下, 对现有的零散的有关单板干燥质量相 关内容以及方法进行了较为系统的优化, 采用了一些简便易行的测试和计算方法, 既适用于专业监测机 构的检测,又适用于企业自我检测。本标准规定的术语与定义、检测方法标既切合我国单板干燥质量的 实际情况,又具有一定的先进性。