MLCC制作过程中分层开裂原因分析
多层陶瓷电容破裂失效原因
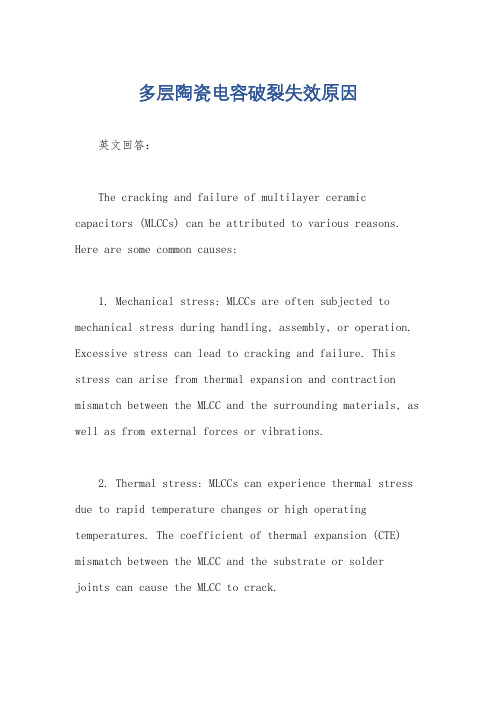
多层陶瓷电容破裂失效原因英文回答:The cracking and failure of multilayer ceramic capacitors (MLCCs) can be attributed to various reasons. Here are some common causes:1. Mechanical stress: MLCCs are often subjected to mechanical stress during handling, assembly, or operation. Excessive stress can lead to cracking and failure. This stress can arise from thermal expansion and contraction mismatch between the MLCC and the surrounding materials, as well as from external forces or vibrations.2. Thermal stress: MLCCs can experience thermal stress due to rapid temperature changes or high operating temperatures. The coefficient of thermal expansion (CTE) mismatch between the MLCC and the substrate or solderjoints can cause the MLCC to crack.3. Moisture and humidity: Ceramic materials are susceptible to moisture absorption. When moisture enters the MLCC, it can cause expansion and contraction during temperature cycling, leading to cracking and failure. Humidity can also cause corrosion of the internal electrodes, resulting in electrical failure.4. Manufacturing defects: MLCCs can have inherent defects introduced during the manufacturing process. These defects can include voids, delamination, or improper electrode connections. These defects can weaken the structural integrity of the MLCC and make it more susceptible to cracking and failure.5. Voltage and current overload: Exceeding the maximum voltage or current ratings of an MLCC can cause it to fail. High voltage or current can generate excessive heat, leading to thermal stress and cracking. It is important to operate MLCCs within their specified limits to avoid failure.中文回答:多层陶瓷电容破裂失效的原因有多种。
小尺寸高容量MLCC切割侧裂问题的解决方法
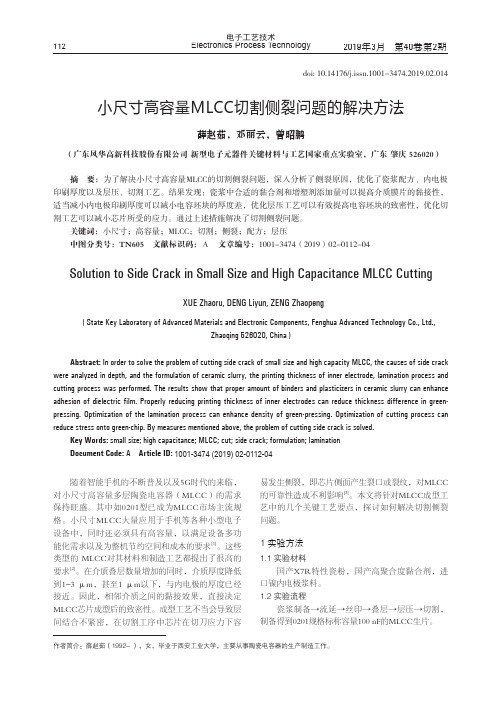
摘 要:为了解决小尺寸高容量MLCC的切割侧裂问题,深入分析了侧裂原因,优化了瓷浆配方、内电极印刷厚度以及层压、切割工艺。
结果发现:瓷浆中合适的黏合剂和增塑剂添加量可以提高介质膜片的黏接性,适当减小内电极印刷厚度可以减小电容坯块的厚度差,优化层压工艺可以有效提高电容坯块的致密性,优化切割工艺可以减小芯片所受的应力。
通过上述措施解决了切割侧裂问题。
关键词:小尺寸;高容量;MLCC;切割;侧裂;配方;层压中图分类号:TN605 文献标识码:A 文章编号:1001-3474(2019)02-0112-04Abstract: In order to solve the problem of cutting side crack of small size and high capacity MLCC, the causes of side crack were analyzed in depth, and the formulation of ceramic slurry, the printing thickness of inner electrode, lamination process and cutting process was performed. The results show that proper amount of binders and plasticizers in ceramic slurry can enhance adhesion of dielectric film. Properly reducing printing thickness of inner electrodes can reduce thickness difference in green-pressing. Optimization of the lamination process can enhance density of green-pressing. Optimization of cutting process can reduce stress onto green-chip. By measures mentioned above, the problem of cutting side crack is solved.Key Words: small size; high capacitance; MLCC; cut; side crack; formulation; lamination Document Code: A Article ID: 1001-3474 (2019) 02-0112-04小尺寸高容量MLCC切割侧裂问题的解决方法Solution to Side Crack in Small Size and High Capacitance MLCC Cutting薛赵茹,邓丽云,曾昭鹏XUE Zhaoru, DENG Liyun, ZENG Zhaopeng(广东风华高新科技股份有限公司 新型电子元器件关键材料与工艺国家重点实验室,广东 肇庆 526020)作者简介:薛赵茹(1992- ),女,毕业于西安工业大学,主要从事陶瓷电容器的生产制造工作。
贴片电容失效分析

由于贴片电容的材质是高密度、硬质、易碎和研磨的MLCC,所以在使用过程中,需要十分谨慎。
经有关工程师分析,以下几种情况容易造成贴片电容的断裂及失效:1、贴片电容在贴装过程中,若贴片机吸嘴头压力过大发生弯曲,容易产生变形导致裂纹产生;2、如该颗料的位置在边缘部份或靠近边源部份,在分板时会受到分板的牵引力而导致电容产生裂纹最终而失效.建议在设计时尽可能将贴片电容与分割线平行排放.当我们处理线路板时,建议采用简单的分割器械处理,如我们在生产过程中,因生产条件的限制或习惯用手工分板时,建议其分割槽的深度控制在线路板本身厚度的1/3~1/2之间,当超过1/2时,强烈建议采用分割器械处理,否则,手工分板将会大大增加线路板的挠曲,从而会对相关器件产生较大的应力,损害其可靠性.3、焊盘布局上与金属框架焊接端部焊接过量的焊锡在焊接时受到热膨胀作用力,使其产生推力将电容举起,容易产生裂纹.4、在焊接过程中的热冲击以及焊接完后的基板变形容易导致裂纹产生:电容在进行波峰焊过程中,预热温度,时间不足或者焊接温度过高容易导致裂纹产生,5、在手工补焊过程中.烙铁头直接与电容器陶瓷体直接接触,容量导致裂纹产生。
焊接完成后的基板变型(如分板,安装等)也容易导致裂纹产生。
多层陶瓷电容(MLCC)应用注意事项一、储存为了保持MLCC的性能,防止对MLCC的不良影响储存时注意以下事项:1.室内温度5~40℃,温度20%~70%RH;2.无损害气体:含硫酸、氨、氢硫化合物或氢氯化合物的气体;3.如果MLCC不使用,请不要拆开包装。
如果包装已经打开,请尽可能地重新封上。
缩带装产品请避免太阳光直射,因为太阳光直射会使MLCC老化并造成其性能的下降。
请尽量在6个月内使用,使用之前请注意检查其可焊性。
二、物工操作MLCC是高密度、硬质、易碎和研磨的材质,使用过程中,它易被机械损伤,比如开裂和碎裂(内部开裂需要超声设备检测)。
MLCC在手持过程中,请注意避免污染和损伤。
电容开裂的原因

电容开裂的原因
•很多人说贴片电容使用时会遇到电容开裂,短路,烧毁等现象,那么碰到这些现象该如何应对呢,首先我们需要先找到原因,X2电容厂家给我们分析了有以下原因。
• 一、开裂是指电容器上出现裂痕导致产品无法正常工作这种现象一般是为低阻造成的原因有
• 1.PCB受外力后断路居多。
• 2.非电容本体受了外力也会导至MLCC电容失效,一般是短路或低阻,但此类现象在预留足够余量的情况下应该不多。
• 这种情况一般要先检查产品工作时是否需要震动或者摇晃,再检查产品容量是否达到要求。
• 二、短路烧毁是指电容在PCB板工作时出现毁坏现象导致产品无法继续工作造成这种原因的一般有。
• 1.电容封装型号不够大
• 2.预留余量不足够
• 3.耐压过小或者产品电流过大
• 如果这种情况发生的话,我们需要换掉贴片电容型号,可检查出具体原因在选择更换贴片电容容量耐压或者型号,如找不到合适的型号更换可把电容并联或者串联来解决问题。
MLCC破裂、短路案例分析
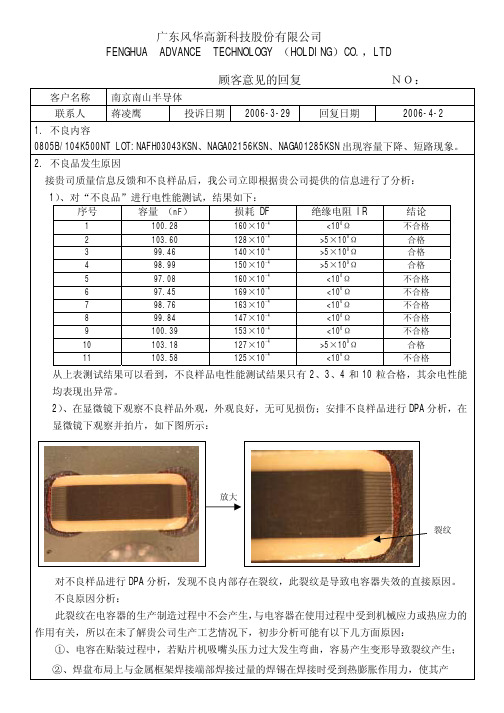
放大
裂纹
对不良样品进行 DPA 分析,发现不良内部存在裂纹,此裂纹是导致电容器失效的直接原因。 不良原因分析: 此裂纹在电容器的生产制造过程中不会产生, 与电容器在使用过程中受到机械应力或热应力的 作用有关,所以在未了解贵公司生产工艺情况下,初步分析可能有以下几方面原因: ①、电容在贴装过程中,若贴片机吸嘴头压力过大发生弯曲,容易产生变形导致裂纹产生; ②、焊盘布局上与金属框架焊接端部焊接过量的焊锡在焊接时受到热膨胀作用力,使其产
1 2 3 4 5 6 7 8 9 10 11 100.28 103.60 99.46 98.99 97.08 97.45 98.76 99.84 100.39 103.18 103.58 160×10 -4 128×10 -4 140×10 -4 150×10 -4 160×10 -4 169×10 -4 163×10 -4 147×10 -4 153×10 127×10 125×10
此裂纹在电容器的生产制造过程中不会产生与电容器在使用过程中受到机械应力或热应力的作用有关所以在未了解贵公司生产工艺情况下初步分析可能有以下几方面原因
广东风华高新科技股份有限公司 FENGHUA ADVANCE TECHNOLOGY (HOLDING)CO.,LTD 顾客意见的回复
客户名称 联系人 1. 不良内容 0805B/104K500NT LOT:NAFH03043KSN、NAGA02156KSN、NAGA01285KSN 出现容量下降、短路现象。 2. 不良品发生原因 接贵司质量信息反馈和不良样品后,我公司立即根据贵公司提供的信息进行了分析: 1) 、对“不良品”进行电性能测试,结果如下: 序号 容量 (nF) 损耗 DF
-4 -4 -4
NO:
回复日期 2006-4-2
光学薄膜多层膜裂纹
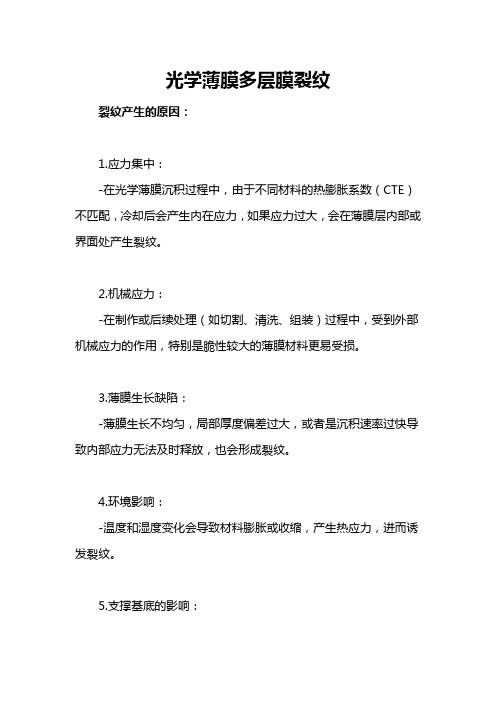
光学薄膜多层膜裂纹
裂纹产生的原因:
1.应力集中:
-在光学薄膜沉积过程中,由于不同材料的热膨胀系数(CTE)不匹配,冷却后会产生内在应力,如果应力过大,会在薄膜层内部或界面处产生裂纹。
2.机械应力:
-在制作或后续处理(如切割、清洗、组装)过程中,受到外部机械应力的作用,特别是脆性较大的薄膜材料更易受损。
3.薄膜生长缺陷:
-薄膜生长不均匀,局部厚度偏差过大,或者是沉积速率过快导致内部应力无法及时释放,也会形成裂纹。
4.环境影响:
-温度和湿度变化会导致材料膨胀或收缩,产生热应力,进而诱发裂纹。
5.支撑基底的影响:
-基底材质的选择和处理不当,或者基底与薄膜的结合力不足,也可能导致薄膜在后期使用中产生裂纹。
解决办法:
1.材料选择与匹配:
-选择与基底材料热膨胀系数相近的薄膜材料,或者采用梯度过渡层来缓解应力。
2.控制沉积参数:
-优化薄膜沉积工艺,包括沉积速率、温度、气氛压力等,确保薄膜生长均匀且内部应力最小化。
3.应力调控:
-设计合理的多层膜结构,通过补偿层来抵消应力,或者采用退火处理降低薄膜内的残余应力。
4.精细化加工与处理:
-加工过程采用温和的操作手法,避免剧烈的机械应力,对完成的薄膜进行适当的后处理,如低温退火消除应力。
5.基底预处理:
-提前对基底进行恰当的表面处理,增强薄膜与基底之间的附着力。
6.环境控制:
-在薄膜制作和封装过程中严格控制环境条件,确保整个流程在恒温恒湿环境下进行。
MLCC制造中产生内部开裂的研究_张尹
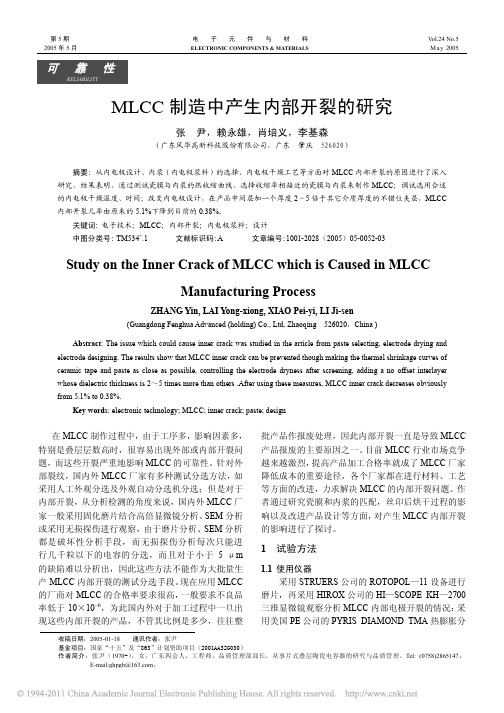
第5期电子元件与材料V ol.24 No.5 2005年5月ELECTRONIC COMPONENTS & MATERIALS M a y2005MLCC制造中产生内部开裂的研究张尹,赖永雄,肖培义,李基森(广东风华高新科技股份有限公司,广东 肇庆 526020)摘要:从内电极设计、内浆(内电极浆料)的选择、内电极干燥工艺等方面对MLCC内部开裂的原因进行了深入研究,结果表明,通过测试瓷膜与内浆的热收缩曲线,选择收缩率相接近的瓷膜与内浆来制作MLCC;调试选用合适的内电极干燥温度、时间;改变内电极设计,在产品中间层加一个厚度2~5倍于其它介质厚度的不错位夹层,MLCC 内部开裂几率由原来的5.1%下降到目前的0.38%。
关键词: 电子技术;MLCC;内部开裂;内电极浆料;设计中图分类号: TM534+.1 文献标识码:A 文章编号:1001-2028(2005)05-0052-03Study on the Inner Crack of MLCC which is Caused in MLCCManufacturing ProcessZHANG Yin, LAI Yong-xiong, XIAO Pei-yi, LI Ji-sen(Guangdong Fenghua Advanced (holding) Co., Ltd, Zhaoqing 526020,China )Abstract: The issue which could cause inner crack was studied in the article from paste selecting, electrode drying and electrode designing. The results show that MLCC inner crack can be prevented though making the thermal shrinkage curves of ceramic tape and paste as close as possible, controlling the electrode dryness after screening, adding a no offset interlayer whose dielectric thickness is 2~5 times more than others .After using these measures, MLCC inner crack decreases obviously from 5.1% to 0.38%.Key words: electronic technology; MLCC; inner crack; paste; design在MLCC制作过程中,由于工序多,影响因素多,特别是叠层层数高时,很容易出现外部或内部开裂问题,而这些开裂严重地影响MLCC的可靠性。
MLCC 失效分析及对策
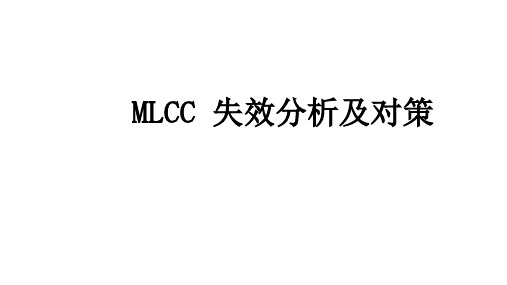
MLCC 失效分析及对策失效的原因•裝配过程中<工艺应用上>失效的原因;•热应力与热冲击;•金属的溶解;•基板和元件过热;•超声波清洗的损坏;•机械负载;•运输的振动;•机械冲击;•应力与热冲击;•老化<腐蚀、基板材料老化、蠕变斷裂、焊接疲劳>电容器的失效模式与常见故障•钽电解电容器—电压过载击穿烧毁;浪涌电压冲击漏电流增大;极性反向短路;高温降额不足失效;•铝电解电容器—漏电流增大击穿;极性反向短路;高温降额不足失效;•有机薄膜电容器—热冲击失效;寄生电感过大影响高频电路功能实现;•MLCC(2类)—SMT工艺不当导致断裂或绝缘失效;Y5V温度特性不佳导致电路故障;•MLCC(1类)—RF设计选型匹配。
MLCC异常汇总分类一、裂纹(微裂、断裂、开裂和击穿)二、端头脱落三、电性能异常(C、DF、IR和TC)四、抛料(国标GB≤0.3%,具体依设备定)五、上锡不良(假焊)六、其它(Q、ESR等)开裂一、MLCC本身制造方面的因素:1、MLCC排烧时温控失调,有机物挥发速率不均衡,严重时会出现微裂纹;2、内电极金属层与陶瓷介质烧结时因热膨胀系数不同,收缩不一致导致瓷体内部产生了微裂。
(MLCC质量隐患);3、编织线裂纹二、MLCC应用生产工艺方面因素:1、热冲击(结构本身不能吸收短时间内温度剧烈变化产生的机械应力所导致的机械性破坏,该力由于不同的热膨胀系数、导热性及温度变化率产生) 2、贴装应力(主要是真空吸放头或对中夹具引起的损伤<目前都使用视觉对中或激光对中取代机械对中>)3、上电扩展的裂纹(贴装时表面产生了缺陷,后经多次通电扩展的微裂纹)4、翘曲裂纹(在印制板裁剪、测试、元器件安装、插头座安装、印制版焊接、产品最终组装时引起的弯曲或焊接后有翘曲的印制板主要是印制板的翘曲)5、印制板剪裁(手工分开拼接印制板、剪刀剪切、滚动刀片剪切、冲压或冲模剪切、组合锯切割和水力喷射切割都有可能导致印制板弯曲)6、焊接后变形的印制版(过度的基材弯曲和元器件的应力)MLCC微裂实例MLCC外观图MLCC DPA图MLCC外观图MLCC DPA图MLCC外观图MLCC DPA图击穿产生的原因:1、MLCC本身耐压不够大(介质厚度偏薄、内部有短路缺陷);2、PCB板模块电路设计不合理,存在漏电短路的缺陷;3、SMT生产工艺中造成的锡渣、锡珠、锡桥等短路现象;4、上电测试时电压过高、或产生的瞬间脉冲电压过大等不良操作。
- 1、下载文档前请自行甄别文档内容的完整性,平台不提供额外的编辑、内容补充、找答案等附加服务。
- 2、"仅部分预览"的文档,不可在线预览部分如存在完整性等问题,可反馈申请退款(可完整预览的文档不适用该条件!)。
- 3、如文档侵犯您的权益,请联系客服反馈,我们会尽快为您处理(人工客服工作时间:9:00-18:30)。
粉介质膜片密度,增大瓷粉介质收缩率,缩小瓷粉
与内浆TMA曲线间的差异;在MLCC电极印刷时,减
小金属电极的质量,减少电极与瓷粉之间的收缩应
力。通过以上措施制作的MLCC分层开裂现象都有明
显改善。
综上讨论:内浆与瓷粉这两者之间TMA曲线的
差异相差越大,烧结过程中产生应力越大,就越易
导致MLCC分层开裂。
1 试验结果与讨论 本试验使用气氛烧结炉、HI-SCOPE KH-2700
型三维显微镜、EXATAR600型热机械分析仪和 L0L0P0L-5型磨片机等分别对MLCC芯片的内浆与瓷
粉的匹配、排胶效果和回火参数等进行试验[5]。 1.1 内浆与瓷粉的匹配性
采用与瓷粉匹配更好的内浆来生产制作MLCC是 每个厂家必须遵循的原则,它是MLCC不分层开裂的 先决条件[6]。本实验选用一种NPO瓷粉,有针对性地 选取三种不同内浆与之匹配,在其他工艺相同条件 下进行同规格容量的试制,试制样品烧结后的结果 见表1。
MLCC(Multi-layer Ceramic Capacitor )具有体积 小、内部电感低、介质损耗低、绝缘电阻高和可靠 性优良等特点,被广泛应用在各种电子设备上[1-4]。 如果MLCC本身存在内部缺陷,则会对其可靠性产生 严重影响。MLCC的内部缺陷有: 陶瓷介质内空洞、 烧结裂纹和分层开裂等。因此在MLCC制作过程中, 避免MLCC产生内部缺陷,提高MLCC的可靠性尤为 重要。本文针对MLCC分层开裂的原因进行分析归 类,提出导致MLCC开裂的原因机理。
约1.6‰芯片分层、 200
端角裂
100
合格
从表3可以看出,在同一温度下,不同回火氧含量的
工艺中,氧含量大于一定数值时,烧结后的芯片会
出现分层及端角开裂情况;同一氧含量下,不同温
度回火工艺,芯片也会出现分层及端角开裂情况。
根据吉布斯-亥姆霍茨(Gibbs-Helmholtz)公式
Hale Waihona Puke 可以证实,在一定的氧分压下,随着温度的提高,
第32卷第6期
刘新,等:MLCC制作过程中分层开裂原因分析
337
比排胶效果好的内浆收缩温度低。排胶效果差导致 内浆收缩温度降低的原因是在空气排胶过程中,内 电极金属镍会出现镍的氧化层,若存在排胶不良, 芯片中会存在碳残留,在烧结过程中碳残留会将内 电极氧化镍层还原。因为金属镍的烧结收缩温度会 比表面有氧化的金属镍烧结收缩温度低,又由于瓷 粉的烧结收缩温度会比内浆的收缩温度高的规律, 我们可以发现排胶质量减少率低的排胶效果差的 芯片其内浆与瓷粉的TMA曲线差异会增大,应力加 剧,MLCC芯片开裂分层就会增多;相反排胶质量减 少率高的排胶效果好的芯片其内浆与瓷粉的TMA曲 线差异会减小,应力减少,MLCC芯片开裂分层就会 减低。
(Fenghua advanced technology Co.Ltd., Zhaoqing 526020, China)
Abstract: MLCC consists of multi layers of dielectric and metal electrodes sintering together. delamination is one of the main quality defects during the manufacturing, which has a significant effect on the reliability during the application. Classify the reasons of delamination, and find failure reasons are non- matching between ceramic dielectric and inner electrode paste, not well of binder burn out before sintering; high reoxidation temperature or high oxygen content during the sintering.
分层开裂情况 90%分层开裂,100%电极内
部分层 约0.6%分层开裂,10%电极
内部分层(如图4所示) 约0.16%分层开裂,未发现
电极内部分层 约 0.04%分层开裂,未发现
电极内部分层 合格,未发现电极内部分层
(如图5所示)
图4 电极内部分层
图5 未发现电极内部分层
从表2可以看出,排胶后的质量减少率低,排 胶效果差的芯片在烧结倒角后存在较大比例开裂分 层;排胶后的质量减少率高,排胶效果好的芯片在 烧结倒角后未发现开裂分层现象。
Key words: MLCC; Delamination; Inner electrode paste; Ceramic powder; TMA; Binder burn out; Re-oxidation; Oxygen content.
Document Code: A Article ID: 1001-3474(2011)06-0335-03
电子工艺技术
2011年11月 第32卷第6期
Electronics Process Technology
335
MLCC制作过程中分层开裂原因分析
刘新,李筱瑜,陈长云
(广东风华高新科技股份有限公司, 广东 肇庆 526020)
摘 要:MLCC是经过多层材料堆叠共烧后制成的,在其制作过程中,产生分层是比较严重的质量缺陷之 一,严重影响MLCC在使用过程中的可靠性。对MLCC产生分层的原因进行分析归类,总结出MLCC产生分层的 原因为:制作MLCC内浆与瓷粉TMA(热机械分析)曲线匹配性不佳;MLCC在烧结前存在排胶不良;烧结回火 温度或氧含量高。
关键词:MLCC 分层;内浆;瓷粉;TMA;排胶;回火;氧含量 中图分类号:TN604 文献标识码:A 文章编号:1001-3474(2011)06-0335-03
Analysis of Reasons for MLCC Delamination During Manufacturing
LIU Xin, LI Xiao-yu, CHEN Chang-yun
三种不同的内浆分别和这种NPO瓷粉做TMA(热机
械分析)曲线分析,得出曲线结果如图3所示。从
TMA曲线结果再结合试制MLCC的分层开裂程度可以
发现,内浆与瓷粉的TMA曲线越接近,烧结后分层
开裂产生的机率越小,相反内浆与瓷粉的TMA曲线
相差越大,烧结后分层开裂的现象越严重。这主要
是由于内浆与瓷粉在烧结过程中均产生收缩,而收
温度θ /℃
内浆A —质量减少率为10.2%的内浆; 内浆B —质量减少率为5.3%的内浆
图6 镍金属表面有氧化与无氧化的内电极浆料TMA曲线
从图6中可以发现,内浆A约在920 ℃开始收缩, 内浆B 约在800 ℃就开始收缩,排胶效果差的内浆会
样品长度变化率/% 施加在样品上的恒力F /N
样品长度变化率/% 施加在样品上的恒力F /N
艺进行排胶,芯片排胶后的质量减少率数据及烧成
后开裂情况见表2。
表2 不同排胶效果芯片烧结后分层开裂情况
排胶时间 试验
t /h
试验 4 12 试验 5 18 试验 6 34 试验 7 48 试验 8 54
排胶后质量
烧结倒角后
减少率/% 4.8~5.4 6.5~7.2 8.0~8.5 9.0~9.5 9.8~10.6
为近一步分析排胶质量减少率对MLCC分层开裂 的影响,分别取芯片排胶后质量减少率高和芯片排 胶后质量减少率低的内浆做热机械分析,分析结果 如图6所示。
0.00 -4.00 -8.00 -12.00
内浆B
内浆A
-50.00 -50.00
-50.00
-50.00
-16.00 0
-50.00 200 400 600 800 1000 1200 1400
0.00 -4.00 -8.00 -12.00
瓷粉
内浆1
-50.00
内浆3
内浆2
-50.00
-50.00
-50.00
-16.00 0
-50.00 200 400 600 800 1000 1200 1400
温度θ /℃
图3 三种不同内浆与NP0材料瓷粉TMA曲线
1.2 排胶效果
选取NP0材料MLCC芯片,采用不同空气排胶工
综上讨论得出:排胶效果不良导致MLCC分层开 裂,其根本原因是排胶不良的芯片中碳残留相对较 多,导致内电极的TMA收缩提前,加大了内电极与 瓷体收缩的差异,即烧结内应力增大,MLCC就产生 分层开裂。 1.3 回火温度及氧含量
MLCC在还原气氛中烧结,烧结后瓷体会出现氧 缺位,影响MLCC的绝缘性能,需对烧结后的芯片进 行回火补氧缺位,改善绝缘性能。但回火温度的高 低和氧含量的大小需控制在一个最佳的范围,否则 会造成MLCC烧结后的分层开裂。为进一步分析证 实,本文选取Y5V材料芯片,采用不同的回火温度及 氧含量对烧结后的芯片进行回火,芯片出现的分层 开裂情况见表3。
缩程度的差异取决于这两者之间TMA曲线相差的大
小,它是导致应力大小的直接原因,应力越大就越
易导致分层开裂。
上述的分析结果在制作MLCC过程中也能够得到
论证,MLCC的生产厂家经常采用以下几种方式改善
内浆与瓷粉之间TMA曲线的差异:在内浆中添加瓷
粉小料,延迟内浆收缩,使得内浆与瓷粉的TMA曲
线接近;在使用瓷粉配制浆料制作膜片时,降低瓷
氧化反应会发生;同样在一定的温度下,随着氧分
压的提高氧化反应也会发生。氧化反应发生后,内
电极金属镍氧化后膨胀,在芯片内部产生内应力,
其应力会从芯片薄弱处释放应力,从而导致端角开 裂。图7为烧结倒角后端角开裂图片,图8为产生端 角开裂芯片的内部电极氧化情况。