烃类蒸汽转化制氢装置中变换单元设置浅析
烃类水蒸气转化法制氢概述

烃类水蒸气转化法制氢概述摘要:本文以烃类水蒸气转化法为例概述了原料经过预处理、转化、中温变换、PSA变压吸附等步骤转化为氢气纯度达到99.9%以上的过程。
关键词:烃类水蒸气转化预处理吸附提纯1 烃类水蒸气转化法原理烃类水蒸汽转化是以烃类为原料,在一定温度和催化剂作用下使烃类和水蒸汽经过一系列的分解、裂化、脱氢、结炭、消炭、氧化、变换、甲烷化等反应,最终转化为H2、CO、CO2、和少量残余的CH4,其中H2是本阶段的目的产物。
烃类的蒸汽转化反应如下:CnHm+nH2O=nCO+(n+m/2)H2――QCH4+H2O=CO+3H2――206000KJ/KmolCO+H2O=CO2+H2――41200KJ/Kmol转化炉内进行的烃类蒸汽转化反应是一个极复杂的平行、顺序反应体系。
从以上反应原理中可以看出其反应过程需需要吸收大量的热,这就要就反应要有较高的反应温度,而烃类易在高温下裂解结炭特别是烯烃,结炭是转化过程中的必然反应,当结炭反应速度大于消炭反应速度时,转化催化剂就会积炭,使催化剂活性下降甚至丧失。
为保证催化剂活性,就要有大于反应所需求过量的水蒸气来进行消炭,从转化后阶段来看,反应生成的CO也需要水蒸汽与之反应,所以生产时要求转化进料始终保持一定的水碳比,使消炭速度大于结炭速度,避免催化剂上炭的沉积。
烃类水蒸气转化法其催化剂主要活性组分为单质Ni,其对原料品质有较高要求,原料中的硫、氯等有害杂质能与转化催化剂活性组分Ni反应生成不可逆转的化合物,从而使其永久性中毒失去活性。
为了充分发挥转化催化剂的活性,并获得较高的氢收率,转化床层一般装填有两种不同性能的催化剂,一般选用Z417/Z418转化催化剂。
Z417/Z418转化催化剂可以适应多种原料,并且对脱毒的需求相对较低。
Z417含有一定钾碱金属的抗结炭助剂因此作为上段催化剂使用,其具有较好的低温活性及抗积炭性能,Z418具有较高的转化活性作为下段床层催化剂。
制氢装置转化工艺管理和操作规程

制氢装置转化工艺管理和操作规程1.1 转化部分的任务及主要工艺指标1.1.1 转化部分的任务及主要工艺指标转化部分的任务是将合格的脱硫气在催化剂存在条件下与水蒸汽发生复杂的强吸热氢解反应,生成含H2、CO、CO2和未反应的水蒸汽、CH4的转化气。
1.1.2 转化部分的主要工艺指标入口温度480~520℃出口温度≯820℃炉膛最高温度≯1020℃炉膛温差≯100℃入口压力 3.1MPa出口压力 1.85MPa炉管压差≯0.38MPa碳空速1000h-1水碳比 3.3~5.0转化气中CH4≯10%1.2 转化入口温度与转化率操作转化温度是烃类-水蒸汽转化法制H2的重要影响因素。
提高温度,甲烷转化率提高,转化气CH4含量降低。
但考虑到设备的承受能力,转化炉的炉膛温度最高不能超过1020℃。
转化炉温度根据转化炉对流段入口温度TI7208的变化情况进行控制。
对流段入口温度信号通过切换开关,同时进入TCA7201A及TCA7201B,使燃料系统在不同的情况下,可采用不同的控制回路。
(1)开停工期间装置开停工时转化炉使用高压瓦斯(副燃料)燃料,采用燃料气流量FC7201与转化炉对流段入口温度TCA7201A的串级控制回路控制转化炉炉温。
(2)变换气作燃料当装置生产出变换气后,根据需要可投用变换气。
变换气通过PC7501控制阀后压力为0.05MPa,送入燃料气混合器MI2001,然后进入转化炉作为燃料使用,其燃料热值不够部分由副燃料提供。
(3)PSA脱附气作燃料PSA运行以后,转化炉燃料投用脱附气作主燃料,脱附气流量可通过FC7503投自动进行控制,其燃料热值不够部分可通过FC7502补充高压瓦斯来提供。
转化炉出口温度采用瓦斯流量FC7502与转化炉对流段入口温度TCA7201B的串级控制。
以上转化炉温度的主副燃料气两种不同控制回路之间的切换,可将一个控制回路由串级控制切换至副表单控,再切换至另一个控制回路的副表单控,然后由另一个控制回路的副表单控切换至串级控制。
211086490_甲烷蒸汽重整制氢技术及进展浅析
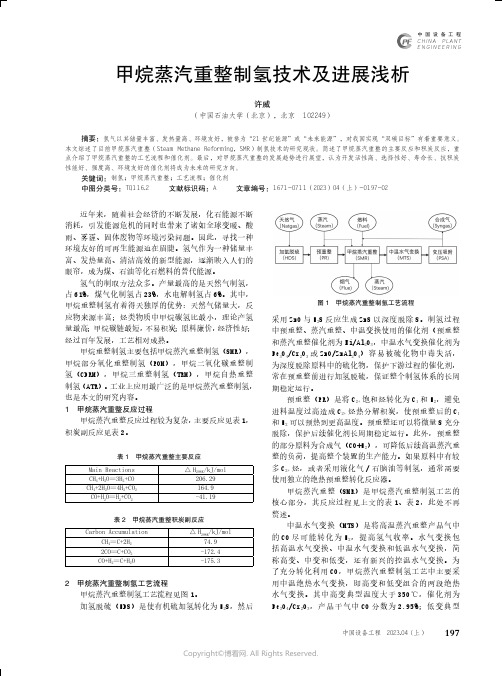
甲烷蒸汽重整制氢技术及进展浅析采用ZnO与H2S反应生成ZnS以深度脱除S。
制氢过程中预重整、蒸汽重整、中温变换使用的催化剂(预重整和蒸汽重整催化剂为Ni/Al2O3,中温水气变换催化剂为Fe3O4/Cr2O3或ZnO/ZnAl2O4)容易被硫化物中毒失活,为深度脱除原料中的硫化物,保护下游过程的催化剂,常在预重整前进行加氢脱硫,保证整个制氢体系的长周期稳定运行。
预重整(PR)是将C2+饱和烃转化为C1和H2,避免进料温度过高造成C2+烃热分解积炭,使预重整后的C1和H2可以预热到更高温度。
预重整还可以将微量S充分脱除,保护后续催化剂长周期稳定运行。
此外,预重整的部分原料为合成气(CO+H2),可降低后续高温蒸汽重图1 甲烷蒸汽重整制氢工艺流程198研究与探索Research and Exploration ·工程技术与创新中国设备工程 2023.04 (上)温度约200℃,催化剂为Cu/ZnO/Al 2O 3,产品干气中CO 分数为0.25%。
变压吸附(PSA)是一种应用广泛的低成本氢气提纯工艺,利用不同气体分子在一些高比表面积吸附材料表面的吸附能力差异,通过多次反复吸附-脱附,最终将不同吸附能力的组分分离出来。
变压吸附包含吸附(A-Adsorption)、降压/均压(E 1-Pressure equalization)、顺放(PP-Provide purge)、逆放(D-Dump)、冲洗(P-Purging/Regeneration)、升压/均压(R 1/R 0-Repressurization)等六个步骤。
常规的吸附分离具有能耗低、压损小、纯度高、投资小、流程短、操作弹性范围大、原料适应性强等众多优点,但收率较低。
采用变压吸附后,氢气回收率提高到75~95%,氢气纯度提高到99.9%以上。
若氢气价值高,还可以采用真空变压吸附(VPSA)提高氢气回收率至95%以上。
甲烷蒸汽重整制氢技术经百年发展,工艺成熟,装置完善,经济可靠,制氢能力强,适合规模化生产,但也存在原料利用率不高和工艺复杂、操作难度大的缺点,不容忽视。
浅析制氢转化炉炉管失效

出相 、氧化层 和金相 组织 转变 ; 材 质从 内到外 ,局部 区域产生高温蠕变 ,材质劣化 ,机械性能大幅度降低。
关键词 :炉管;ห้องสมุดไป่ตู้失效 ;分析
中图 分类 号 :T G 1 7 4 . 2
文 献标 识码 :A
文章编 号 :1 0 0 1 — 9 6 7 7 ( 2 0 1 3 ) 0 4— 0 1 6 1 — 0 3
为H P 4 0 N b ,离心浇铸 原始铸 态 ,炉管 内填 装活性 成分 为镍 的
催化剂 。该 制氢 装置是采用焦 化干气为原 料的烃类蒸 汽转化 制 氢装 置 ,原 料 经脱 硫后 与蒸 汽 混合 ,经转 化 炉对 流 段 预热 至 5 0 0 o C 左右 ( 压力 2 . 0 MP a )进入 转化 炉 ,在高温 及催 化剂 作
( 中国石油锦 西石化公 司,辽宁 葫芦岛 1 2 5 0 0 1 )
摘 要 :在制氢装置停工检修中, 发现转化炉炉管有部分炉管发生了失效。通过对失效炉管材料进行成分分析、力学性能
分 析 、金相 组织评价以及 扫描电镜分析 ,结果表明 :炉管材料成分合 格 ,内壁金相组 织基本正 常 ;由于高温作用 ,外 表面存 在析
p r e s e n t o n t h e o u t e r s u r f a c e o f p r e c i p i t a t e s ,a n d t h e o x i d e l a y e r a n d t h e mi c r o s t mc t u r e c h a n g e . Ma t e r i l a f r o m t h e i n s i d e t o t h e o u t s i d e ,l o c a l h i g h t e mp e r a t u r e c r e e p,ma t e r i a l d e g r a d a t i o n,a n d me c h a n i c a l p r o p e r t i e s s u b s t a n t i ll a y r e d u c e d . Ke y wo r d:t u b e ;f a i l u r e ;a n ly a s i s
提高转化率降低制氢装置成本

提高转化率降低制氢装置成本摘要:制氢装置是天津石化加氢精制、加氢裂化等用氢装置的重要配套生产装置,分A、B两个系列,可实现2×30000 Nm3/h制氢能力。
本文就如何提高制氢转化炉转化率,降低成本,进行了讨论。
关键词:制氢装置;转化炉出入口温度;炉管压力;水碳比前言中石化股份公司天津分公司炼油部联合三车间制氢装置于1998年建成,分为A、B两个系列,采用钴钼加氢,氧化锌脱硫,烃类水蒸汽转化,氧化铁中温变换,变压吸附氢提纯等工艺过程,其中变压吸附氢提纯为A、B两系列共用,规模为6万标立/时,与公司加氢裂化,加氢精制,柴油加氢,脱硫制硫以及化工装置区的大芳烃等装置直接联系和影响,使制氢装置具有的临氢,高温,高压,易燃,易爆,工艺操作复杂,关联广泛等特点,是关键生产装置。
1.烃类水蒸汽转化制氢反应机理烃类水蒸汽转化过程是一个多种串联反应和平行反应,并且能够同时发生复杂的反应体系,包括高级烃的热裂解、脱氢、催化裂解、积碳、加氢、氧化、变换、甲烷化等一系列反应,其反应过程可用下式表示:CnHm+nH2O=nCO+(n+m/2)H2-Q (1)CO+3H2=CH4+H2O+206KJ/mol (2)CO+H2O=CO2+H2+41KJ/mol (3)为了能够提高烃类的转化率,该转化反应在很高的温度下进行,但是不利于放热反应(3)的进行,因此,有较多的一氧化碳存在于天然气转化产物中,同时该转化反应是体积增大的反应。
1.影响因素从转化反应原理可知,影响其化学平衡的因素有温度压力、水碳比、空速和催化剂性能。
2.1 操作压力从平衡转移的角度来讲,低压有利于反应的正向进行,但我们选择的操作压力并不是很低,为3.0Mpa左右,原因主要是出于以下三方面考虑,第一,加压可以节省压缩功率;第二,在一定程度内加压可以节省设备投资;第三,加压有利于生产余热的利用。
2.2 物料空速空速的选择依催化剂的活性及系统压力高低而定。
烃类蒸汽转化制氢装置高效开工进料操作法

烃类蒸汽转化制氢装置高效开工进料操作法发布时间:2021-08-13T10:45:34.130Z 来源:《科学与技术》2021年4月10期作者:赵健[导读] 作为公司炼油产品结构调整和油品质量升级的重要组成部分,10万标立/小时制氢装置为下游赵健中国石化天津分公司炼油部天津300270摘要:作为公司炼油产品结构调整和油品质量升级的重要组成部分,10万标立/小时制氢装置为下游多个加氢装置提供优质纯氢。
随着公司对加工损失和整体物料平衡的要求愈加严格,环保压力不断增大,装置定员越来越少,车间基于装置自身特点,优化制氢装置开工进料操作,在装置开工进料阶段具有火炬零排放,初期产氢低,出产品即合格,并节省人力的特点。
关键词: 烃类水蒸汽转化制氢;开工进料;1装置简介100000Nm3/h制氢装置采用LEPC的低能耗蒸汽转化制氢技术,PSA净化部分采用成都华西变压吸附(PSA)技术,是目前国内最大的采用国产工艺包的同类装置,也是中石化最大的烃类蒸汽转化制氢装置。
本装置由原料预热部分、原料精制部分、预转化转化部分、变换及工艺气热回收部分、PSA净化部分、工艺冷凝水回收部分、转化炉热量供应和烟气预热回收部分以及产汽部分组成。
本装置原设计原料为天然气,不具备低压干气进料条件,天然气硫含量低于3ppm。
设置一台开工压缩机,一级压缩设计,用于装置开停工、事故处理和气密工况,开工压缩机入口设计压力达到2.35MPa。
2开工进料操作的具体步骤2.1进料前状态1)装置采用高压循环,系统压力始终保持在可达到的最高压力,因系统充氢气位置与压缩机出口接近,所以,系统压力在启动PSA前维持在1.8MPa。
2)转化剂还原结束,变换反应器升温结束,具备进料条件。
3)PSA各塔按步序建压完成,吸附状态的吸附塔升至与氢气管网平压。
4)加氢反应器升温结束,已切出系统,预转化反应器在系统外。
5)配汽量调整至满负荷的50%,在进料过程中保持配汽量不变即可,简化开工操作。
制氢装置中温变换与低温变换部分工艺管理和操作规程

制氢装置中温变换与低温变换部分工艺管理和操作规程1.1 中温变换低温变换部分的任务与主要工艺指标1.1.1 中温变换低温变换部分的任务本部分的目的是将转化气中CO在催化剂的作用下与水蒸汽反应,变换成CO2和H2,使得低变气含CO<0.3%。
以提高产氢率降低原料消耗。
1.1.2 中温变换低温变换部分的主要工艺指标(1)中温变换反应器入口温度350~370℃出口温度412℃入口压力 2.83MPa出口压力 2.80MPa空速2000h-1床层最高温度≯ 450℃出口CO含量<3%(2)低温变换反应器入口温度205~215℃出口温度215℃床层最高温度≯ 230℃出口CO含量<0.3%空速2000h-1入口压力 2.77MPa出口压力 2.74MPa1.2 中温变换反应器R2003入口温度的调节中温变换反应是放热反应,中温变换的目的是提高变换反应的速率,在实际生产中,只要能达到工艺指标(中变出口CO含量<3%)。
中温变换反应器入口温度是通过转化气蒸汽发生器E2001管程转化气出口温控TC7202来调节的。
因此在实际操作中,操作人员要根据中变反应器床层温度的变化来调节中变入口温度。
影响中温变换反应器R2003入口温度的因素:(1)转化炉操作的影响转化炉出口温度直接影响到中变入口温度,所以转化炉燃料气压力、流量、燃料气调节阀是否失灵以及火嘴燃料效果等都会引起转化炉出口温度的波动,从而影响中变入口温度。
(2)催化剂结焦的影响催化剂层结焦不是很严重时,会造成反应器局部温度上升。
这是因为催化剂结焦,阻力大,气体流动困难,故不能将这处的热量带走,造成温度局部上升。
若催化剂层结焦严重,气体更难通过,则形成气体偏流或短路,使壁温升高。
(3)催化剂的活性在新装催化剂使用初期,催化剂活性好,由于中温度变换反应是放热反应,温升大;随着催化剂使用时间的延长,活性降低。
因此,在实际操作中,要根据催化剂活性周期,认真控好TC7202。
制氢装置中温变换与低温变换部分工艺管理和操作规程

制氢装置中温变换与低温变换部分工艺管理和操作规程1.1 中温变换低温变换部分的任务与主要工艺指标1.1.1 中温变换低温变换部分的任务本部分的目的是将转化气中CO在催化剂的作用下与水蒸汽反应,变换成CO2和H2,使得低变气含CO<0.3%。
以提高产氢率降低原料消耗。
1.1.2 中温变换低温变换部分的主要工艺指标(1)中温变换反应器入口温度350~370℃出口温度412℃入口压力 2.83MPa出口压力 2.80MPa空速2000h-1床层最高温度≯ 450℃出口CO含量<3%(2)低温变换反应器入口温度205~215℃出口温度215℃床层最高温度≯ 230℃出口CO含量<0.3%空速2000h-1入口压力 2.77MPa出口压力 2.74MPa1.2 中温变换反应器R2003入口温度的调节中温变换反应是放热反应,中温变换的目的是提高变换反应的速率,在实际生产中,只要能达到工艺指标(中变出口CO含量<3%)。
中温变换反应器入口温度是通过转化气蒸汽发生器E2001管程转化气出口温控TC7202来调节的。
因此在实际操作中,操作人员要根据中变反应器床层温度的变化来调节中变入口温度。
影响中温变换反应器R2003入口温度的因素:(1)转化炉操作的影响转化炉出口温度直接影响到中变入口温度,所以转化炉燃料气压力、流量、燃料气调节阀是否失灵以及火嘴燃料效果等都会引起转化炉出口温度的波动,从而影响中变入口温度。
(2)催化剂结焦的影响催化剂层结焦不是很严重时,会造成反应器局部温度上升。
这是因为催化剂结焦,阻力大,气体流动困难,故不能将这处的热量带走,造成温度局部上升。
若催化剂层结焦严重,气体更难通过,则形成气体偏流或短路,使壁温升高。
(3)催化剂的活性在新装催化剂使用初期,催化剂活性好,由于中温度变换反应是放热反应,温升大;随着催化剂使用时间的延长,活性降低。
因此,在实际操作中,要根据催化剂活性周期,认真控好TC7202。
- 1、下载文档前请自行甄别文档内容的完整性,平台不提供额外的编辑、内容补充、找答案等附加服务。
- 2、"仅部分预览"的文档,不可在线预览部分如存在完整性等问题,可反馈申请退款(可完整预览的文档不适用该条件!)。
- 3、如文档侵犯您的权益,请联系客服反馈,我们会尽快为您处理(人工客服工作时间:9:00-18:30)。
中圈分类号 : 5 T 0 Q
文献标识码 : B
文章编号 : 0— 1( 1)1 2 3 1 1 29 0 10— — 0 9 2 40
随着石 油化工 和精 细化 工等 的发展 , 各种 规 对 模 的氢气 原料 的需 求也越 来越大 。烃类 转化制 氢是 当今主要 的氢气制 取方法 之一 。天然气 是烃类转 化
Fi. The pr c s t ou hes it g1 o e swih tt hf
度为 10C, 5 o 燃烧 配人 的空 气温度 为 2 o 0C;
() 3 天然气转 化后通 过热 量 回收进 入 P A系统 S
的温度为 4  ̄ 根据 P A系统所需 ) 0 C( s ;
氢气 。P A 的解 吸气 返 回转 化炉 , s 并据需 要补 充适 量燃料 天 然 气后 , 入 转化 炉 炉膛 燃 烧 , 反应 提 进 为
供 热量 。
1 烃类 制氢 的不 同工艺 流程及 其 比较
目前 国内天 然气 蒸汽 转化 制氢 装 置工艺 流 程一
般 有如下两种 , 图 1和图 2所示 。 如
为 了对 比计:
( ) 艺 天 然 气 和 用 于 产 生 蒸 汽 的 脱 盐 水 的温 1工
度均为 常温 2 ℃; 0
( ) 然 气 燃 烧 后 的 烟 气 热 量 回 收后 的 排 烟 温 2天
图 1 无变 换 单元 的 制 氢流 程
图 1和 图 2两 种 流 程 的 主要 区别在 于 变换 单
元 的设置 与否 , 考虑 到不 同 流程 的热量 回收方 案可 能不同, 我们 根据 C H 的标 准 热 值 , 回收 的热 量 将
折成 C H 的量 , 然后 比较 两种 流程的 C H 净消耗 量
在理论 上是否一 致 。
工 艺天 然气 与工 艺蒸 汽按 规定 比例混 合 , 预 并
热 到一 定温 度 后 , 入转 化 炉 管 , 进 在管 内的催 化 剂
作用下 发生 蒸汽转 化 反应 , 转化 炉 出 口的转 化气 经
制 氢 的常用 原料 , 其成 分 以 C 主 , 余 C 以上 H为 其 2
的高烃 的转化反应 机理也是 首先氢解 为 C H ,再 继
2 有 变换 ) ( 的制 氢 流程 历来 都 有争 议 。根 据天 科股 份公 司多年 来 设 计 和 成功 开 车 的多 套 规 模 不 等 的
催 化剂 活性 表 面被覆 盖 而使 催化 剂 活性 降低 , 至 甚 造 成转 化管 的堵 塞 。多碳 烃 含量 越 高 , 结炭 的可 能
性越 大 , 水碳 比也 应 相应 提 高 。常用 的水 碳 比范 围
废热锅 炉 回收热量 产 生蒸汽 后 ,根据 具体流 程 , 直
接或 变换 后 经进 一 步 热 量 回收 ,降温 并 分离 冷凝 水, 然后 进入变 压吸 附( S 装置 , 离后 得到产 品 P A) 分
续 进一步 反应 。因此本 文仅 以 C H 为原料 来讨论 其 转 化过程 。
4 3
碳 比增 加 , 化 反 应平 衡 向右 移 动 , 在 一 定程 度 转 可
Ta l Co s mp in o L e 0 0m p o u t be1 n u t fCI p r1 0 o r d c H2 CL总 消 I 回收热量 回收热 折算 后 流程方 案 耗 量 m/ : 3 Q + 5Q1Q (J )C 消耗量 m 3 2Q Q + 4 Q 一 一 2k/ H 净 1 1 h
图 2 设 置 变换 单 元 的 制氢 流程
F g2 Th r c s ih t e s i i . ep o e s w t h h f t
等的, 故这两 种 流程的 C H 理论 消耗 量是基 本相 等
的。
收 稿 日期 :0 00 .5; 者 简 介 : 莉 ( 9 0 ) 女 , 级 工 程 2 1 — 80 作 申 17 一, 高
是 30 40 . ̄ .。 ’
4 2
天 然 气化 工
2 1 年第 3 01 6卷
烃类蒸汽转化制氢装置 中变换单元设置浅析
中 莉, 杨先 忠 , 李 林
( 四川 天 一科 技股 份 有 限公 司 , 四川 成 都 , 1 2 5 60 2 )
摘要: 以物 衡 和 热衡 为 基 础 , 从工 程 角 度 的多 个 方 面论 述 了不 同规 模 烃类 蒸 汽 转化 制 氢 装 置 中变 换 单元 设 置 的优 劣 。 关 键词 : 然 气 ; ; 汽转 化 ; 换 ; 氢 天 烃 蒸 变 制
上 增加 反应速 度 和烃 的转 化率 。但水碳 比的增 加要
求 转化 炉辐 射段 提 供 的热量 更 多 , 即是 以增 加燃 料 气 消耗 为代价 的 。 因此 , 水碳 比不 宜过 高 。 从理论 上 说, 水碳 比越低 , 燃料 的需 要量越 少 。但 过低 的水 碳 比不 仅对 转 化 反 应不 利 , 还会 引 起 结 炭 , 而 造 成 从
师 , 邮 si 0 @1 3c r。 电 l 2 7 6 .o 一 n
但 在 实 际生 产 中 , 于采 用 图 1 无变 换 ) 图 对 ( 或
第 1 期
申 莉等 : 烃类 蒸汽转 化制 氢装 置 中 变换单 元设 置浅析
表 1 1 0 m3 气 的 C 消耗 值 00 氢 地
() 4 由于 C O为较难 吸附 的杂质 , 故无变换单 元 时 P A氢 气 收率约 7 % ,有 变换单元 时 P A氢 气 S 2 S
收率 约为 7 %。 8 根 据 以上 条件设置 程序计 算得 出如 下数据 :
气
由计算 结果可 知 , 有无 变换单 元消 耗 的 C H 量 理论 计算值 相差 很小 , 误差 范围 内可 以认 为是 相 在