压力机液压及控制系统设计(plc控制),DOC
液压系统的PLC控制
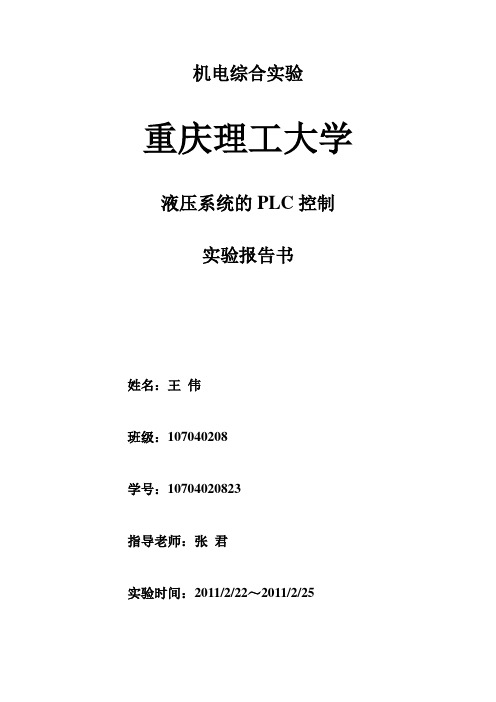
机电综合实验重庆理工大学液压系统的PLC控制实验报告书姓名:王*班级:107040208学号:***********指导老师:张*实验时间:2011/2/22~2011/2/25目录一、实验目的与要求 (3)二、总体方案 (4)三、液压控制回路 (5)四、得失电状态表 (8)五、电气原理图 (9)六、I/O端口分配 (11)七、程序设计与系统流程图 (12)八、自我总结 (16)九、程序清单 (18)附录本组成员名单及任务分配 (23)一、实验目的与要求1、实验目的(1)能熟悉基于plc控制的液压系统开发流程,并设计一个具体的气动、液压系统。
(2)熟悉并掌握各种液压元件的技术参数和使用方法。
(3)熟练掌握plc编程方法。
(4)能熟练使用梯形图编写液压系统的控制软件。
(5)搭建具体硬件(含油、电路)连接,并完成软硬件的联调。
2、实验器材计算机、液压泵、各种液压阀、气动元件、油管、液压接头、plc实验板、导线。
3、实验要求根据本人在本次实验中学习到的相关知识作答。
(1)详细说明本次实验设计思路、方案,画出动作循环、系统油路、控制电路原理图,并文字说明。
(2)详细说明plc控制流程,确定输入/输出口,作I/O规划。
(3)画出plc控制梯形图,要求自锁、定时器。
(4)说明本次实验使用的传感器,与控制电路的接口。
(5)自我总结。
二、总体方案1、根据实验要求,本组最终确定的方案为能够在X-Y方向上铣削出工件的平面,机械本体如图(1)所示。
图(1)如图(1)是一个XY轴十字滑台,其上面有一个可以固定工件的平台。
此XY轴十字滑台是在铣平面的时候用的,采用液压缸控制。
其各个阶段的速度包括工进,快进,快退都是由液压回路里的调速阀控制。
由于铣床只要求铣完整个平面,而不要求其能够加工出各种图案。
故采用这样的方法来调速是可以的。
图中的ST1、ST2、ST3、ST4接近开关所在的位置是滑台整个的工作范围。
ST0是滑台的原点位置。
液压系统PLC控制

天津工业大学毕业设计(论文)题目:挤压机液压系统及PLC控制姓名朱永生学院机械电子学院专业机械工程及自动化班级机自S071班学号**********指导教师肖放王恩鸿职称教授2009年6月18日本文主要介绍了挤压机的现状,挤压机液压系统的工作原理、特点,从设计角度出发分析液压系统各个元件的特点、工作条件,根据计算通过对电控阀、流量控制阀、压力控制阀等元件的选择设计连接液压回路,形成液压的传动系统;根据液压系统的传动特点设计电气接线图,分析在电气控制与液压系统的自动、手动控制方式、开闭环特点,利用原理分析、计算找出可能出现的控制问题,编写PLC梯形图程序,最终由PLC程序控制液压系统形成一个统一的控制系统整体,达到利用自动化手控制液压系统完成特定的工作行程的目的。
关键词:液压系统 PLC控制挤压机This paper introduces the present situation of extruder, the working principle and the characteristics of hydraulic system, , from the design point of view of analysis the various components of hydraulic system characteristics, working conditions, according to the calculation of electric control valves, flow control valves, pressure control valves, such as the choice of components designed to connect the hydraulic circuit to forming the hydraulic drive system; the transmission hydraulic system in accordance with the characteristics of the design of electrical wiring diagram, analysis in the electrical control and hydraulic system of automatic,manual control mode, the closed-loop e of the principle to analysis and computation the control to identify possible problems and the preparation of PLC ladder program, ultimately form the PLC control hydraulic system to control the formation, achieved the popuse of automated hand-controlled hydraulic system to complete the work of a particular trip.Keywords:PLC 、Order control、 Hydraalic system目录摘要ABSTRACT第一章绪论 (1)1.1液压传动与控制概述 (1)1.2 液压机的发展及工艺特点 (1)1。
基于PLC的液压工装控制系统设计

基于PLC的液压工装控制系统设计摘要PLC可编程序控制装置具有程序设计简便、反应迅速等优点,在液压传动装置上得到了广泛地使用,使其工作特性得到了极大的改善。
论文的第一部分,以所要完成的工作为基础,对压力机上的液压系统展开了一系列的设计和分析,确定了液压系统的方案,并对液压元件进行了选取,并以此为基础,对液压装置进行了电动控制回路的设计,从而使得液压装置可以按照不同的工作条件,按照不同的工作条件来进行各种操作。
编写了PLC的控制程序,并画出了一个阶梯的形状,然后对PLC的输入、输出液压回路中的电磁阀进行了控制,最终在液压实验台上对压力机上的液压系统进行了操作。
关键词:液压系统控制电气控制1.研究背景与意义PLC (Programming Controller, PLC)是一种专用于对多种工业装备进行控制的自动控制器件。
由于其具有高的性能,高的灵活性和良好的可扩充性,所以在各个行业尤其是在工业中得到了广泛地使用。
在实际应用中,液压传动是最为普遍的一种。
常规的液压控制一般由手工完成,效率低,精度低,劳动强度大,已无法适应现代化的要求。
而采用PLC作为液力驱动的控制方式,更显其优越性。
首先,PLC具有响应速度快、精度高、工作稳定等特点,能够很好地适应液压传动的需要;其次,利用PLC软件进行程序设计,使整个液压传动的控制更加精确,更加稳定。
通过与上位机等其他电子装置的通讯,可以对系统进行远距离的监测与控制[1]。
采用可编程控制器实现的液压自动调节,是一种极具实用意义的液压自动调节系统。
因此,设计高效、可靠和智能化的液压传动系统势在必行。
2液压系统设计在常规液压设计中,液压系统的设计与分析是必不可少的。
在对液压系统进行的设计中,既要满足对主要机械的循环、作用力和运转速度的需求,又要满足结构简单、工作安全可靠、操作方便等优点,还应将标准化、系列化、通用性等方面贯彻到底。
本文所研制液压装置为一台单圆柱式水压机冲床,可完成冲床、折弯及切断等作业,具有较大的工程实用价值。
液压系统PLC控制教学设计 (2)

液压系统PLC控制教学设计概述液压系统广泛应用于各种机械及工业设备中,随着现代工业技术的不断发展,PLC(可编程序控制器)作为自动化控制领域的重要组成部分,已经被广泛应用于液压系统的控制和调节。
本文主要介绍一种针对液压系统的PLC控制教学设计,该教学设计旨在提高学生对液压系统中PLC控制和调节的认识和实践技能,使学生能够掌握基本的液压系统PLC控制原理和方法,为未来从事液压系统控制和调节相关工作打下坚实的基础。
教学内容基本原理液压系统是一种利用流体压力来传递能量并实现力的传递的动力系统,液压系统由液压泵、储油器、控制阀、执行器和管路等部分组成。
PLC是一种常用于自动化控制系统的电子控制器,它能够完成各种复杂的控制和调节功能。
在液压系统中,PLC主要用于控制和调节各种执行器的运动和位置。
教学目标1.熟悉液压系统的基本构成和工作原理;2.掌握PLC控制的基本原理和方法;3.学习搭建液压系统和PLC控制系统的实验平台;4.能够进行液压系统PLC控制的实验操作和故障排除;5.最终能够完成一个液压系统PLC控制的实验项目。
实验平台本次教学设计所使用的实验平台是基于PLC的液压控制系统,其中PLC采用西门子S7-200系列控制器,可实现对液压系统中某些执行器的运动和位置进行控制和调节。
实验步骤1.搭建液压系统实验平台,包括液压泵、储油器、控制阀、执行器和管路等部分;2.搭建PLC控制系统,包括PLC控制器、输入输出模块和人机界面等部分;3.设计液压系统PLC控制的控制程序,包括监测和读取系统状态、输出指令到执行器等部分;4.进行实验操作,测试液压系统PLC控制的功能和性能,如执行器的位置和速度控制等;5.分析和解决液压系统PLC控制的故障,如执行器的失控、传感器故障等;6.实现液压系统PLC控制的实验项目,如利用PLC控制液压缸的伸缩运动。
结论通过本次液压系统PLC控制的教学设计,学生可以深入了解液压系统中PLC的基础原理和实践技能,掌握液压系统中PLC控制的主要方法和技术;同时,学生在实验操作中还能够培养自己的实验技能和创新能力,为未来从事液压系统控制工作打下坚实的基础。
液压机械手PLC控制系统的设计

液压机械手PLC控制系统的设计概述本文档旨在介绍液压机械手PLC(可编程逻辑控制)控制系统的设计。
液压机械手是一种常见的工业设备,通过液压系统实现运动控制,而PLC作为控制系统的核心,负责控制信号的处理和输出。
设计要求液压机械手PLC控制系统的设计要满足以下要求:1. 稳定性:系统必须具有高稳定性,以确保机械手的运动精准度和安全性。
2. 功能性:系统需要具备多种功能,如位置控制、速度调节等,以满足不同场景的需求。
3. 可扩展性:系统应具备良好的可扩展性,以便于将来的升级和功能增加。
4. 易维护性:设计应考虑到系统的维护和故障排除,以便于后续维护工作的进行。
硬件设计液压机械手PLC控制系统的硬件设计包括以下方面:1. 选型:选择适合的PLC设备,根据需求选用不同型号和规格的PLC,确保其性能和稳定性。
2. 传感器:选择合适的传感器,如位移传感器、压力传感器等,用于采集机械手运动状态和环境信息。
3. 执行器:选择合适的液压阀、液压泵等执行器,保证系统能够精确控制机械手的各项动作。
4. 电气线路:设计合理的电气线路,确保信号传输的可靠性和稳定性。
软件设计液压机械手PLC控制系统的软件设计包括以下方面:1. PLC程序设计:使用PLC编程软件,根据机械手的运动逻辑和控制要求,编写PLC程序,实现各项功能。
2. 信号处理:对传感器采集的信号进行处理和分析,以获取机械手的状态信息。
3. 控制算法:设计合理的控制算法,根据机械手的控制需求,实现位置控制、速度调节等功能。
4. 用户界面:设计友好的用户界面,方便操作人员对机械手进行参数设置和监控。
系统测试与调试设计完成后,需要进行系统测试与调试,以验证系统的功能和性能:1. 单元测试:对各个模块进行单元测试,确保其功能正常。
2. 组装测试:将各个模块组装成完整的系统,对整个系统进行综合测试。
3. 调试优化:根据测试结果进行系统调试和优化,确保系统的稳定性和性能满足设计要求。
液压试验台PLC控制系统设计.doc

第一章绪论1.1 概述液压传动技术是机电一体化技术的重要组成部分,而且液压传动相对于机械传动来说是一门新技术,随着流体力学、自动控制、计算机等技术的不断发展,液压传动技术已经发展成为包括传动、控制、检测技术、机电一体化的一门完整的自动化技术,并且在工业生产、设备控制等方面都得到了广泛应用。
液压实验台是生产和开发液压元件和液压系统的重要实验设备。
传统的液压实验台内容固定、控制方式单一。
随着液压技术和现代控制技术的发展,传统液压实验台的缺陷愈来愈明显,已不能很好地适应生产和研究的需要。
为了可以更好的适应教学的发展,增强学生解决实际问题的能力,以及满足现代科研的需求,在传统液压试验台的基础上,加入PLC先进控制技术,构建了由PLC作为下位机控制现场设备,由PC作为上位机在线监控的控制系统,可以实现机、电、液、计算机的完美结合,实现实验处理的自动化,实时监控等。
采用了由PLC控制技术来控制液压试验台的自动控制响应快、智能化,学生不仅可以根据需求搭建各种液压回路或液压系统,还可以独立的进行液压设计、安装、调试、编写PLC程序、等,有利于提高学生在机电液计算机综合控制等方面的综合能力。
1.2液压传动的发展及其研究对象液压传动技术的发展,可追溯到17世纪帕斯卡提出了著名的帕斯卡定律,开始奠定了流体静压传动的理论基础。
从18世纪末英国制成了世界上第一台水压机算起,已经有近300年的历史,但真正的发展只是在第二次世界大战后,液压技术由军用工业迅速转向民用工业,而我国的液压工业只经过40余年的发展,就已经形成门类齐全、有一定的技术水平并初具规模的生产科研体系,其生产的液压产品广泛应用于工业、农业和国防等各个部门。
近20年来,我国液压工业通过引进先进技术,科研攻关,产品应用技术飞快发展,设计生产了许多新型的液压元件。
此外通过计算机辅助技术(Computer Aided Design,简称CAD)、计算机辅助测试(Computer Aided Translation,简称CAT)、污染控制、故障诊断、机电一体化等方面研究成果的应用,液压技术水平得到很大的提高。
基于PLC控制的液压压装设备设计

车辆工程技术60机械电子1 翻转轴轴套压装整体设计方案重卡前悬翻转轴主要承担驾驶室翻转作用,每件翻转轴需压入四个轴套用于驾驶室的支撑旋转。
应公司业务需求,急需开发一套压装系统满足翻转轴加工需求。
该套设备本体部分为钢结构压装平台、液压油缸、定位气缸、伺服电机、轴套压装平台及设备防护外壳组成。
其中钢结构压装平台由方钢、钢板等材料焊接而成主要作用为支撑液压油缸、气缸等工作元件。
液压油缸主要作用为压装轴套提供压力并检测轴套压装距离。
定位气缸主要作用为因车型不同轴套压装之前压装平台的前后方向的定位以及不同系列前悬支架的支撑。
伺服电机主要作用为因车型不同轴套压装之前支架摆放位置、压装定位位置的控制。
轴套压装平台主要作用为支架摆放、定位以及安装轴套工装。
设备防护外壳主要作用防护设备碰撞损伤及外观整洁。
整套设备通过PLC 控制伺服电机及伸缩气缸对压装工件进行压装定位,定位完成后通过对液压站电磁阀控制油缸进行压装,压装完成后缩回油缸,依次完成压装工序。
2 程序控制编程2.1 控制系统流程针对不同型号翻转轴,需提前在系统内设置参数保存,下一次使用时直接调用,提高系统对不同产品的兼容性首先确定车型型号是不是已有车型,如果是直接查询到相应的车型型号查询出数据,然后压装。
如果不是,则需要重新建立相应车型数据,保存在系统中,以后出现时则可以直接调用。
2.2 控制系统硬件设计及PLC I/O 分布综合分析三菱、西门子、欧姆龙等几种常用PLC 及其组件功能后,从开发简单、使用方便、功能强大、经济效益等方面综合分析考虑,最后使用三菱FX 系列PLC 及其组件进行开发设计。
(1)部分I/O 分配表如表1,表1中详细标注了系统操作输入及系统输出端口,表明该设备进入系统的程序信号情况,操作系统以此为基础进行各项操控及信号输出。
表1 I/O 分配表数字量输入数字量输出X000急停X011气缸降落检测Y000轴1脉冲Y014气缸升起X001油泵过载X012气缸A 锁紧Y001轴2脉冲Y015气缸降落X002轴1正限位X013气缸A 松开Y002轴1方向Y016气缸A 锁紧X003轴1负限位X014气缸B 锁紧检测Y003轴2方向Y017气缸A 松开X004轴2正限位X015气缸B 松开Y004油缸A 前Y020三色灯/红X005轴2负限位X016初始位置Y005油缸A 后Y021三色灯/黄X006轴1DOG X017放置位置Y006油缸B 前Y022三色灯/绿X007轴2DOG X020压装启动Y007油缸B 后Y012油缸D 后退X010气缸升起X021举升按钮Y010油缸C 后Y013油缸D 前进Y011油缸C 前Y014举升升起Y012油缸D 后Y015举升降落Y013油缸D 前 (2)系统内模拟量分配表如表2,针对不同型号产品制作数据配方,依据型号名称快速查找相应加工数据,针对不同型号的油缸进给距离数据及压装压力数据,利用模拟量采集模块,进行模数转换,得到相应加工数据,通过与标准数值比较,从而确定加工件是否合格。
压力机液压系统的电气控制设计(DOC)

机电控制技术课程设计资料袋机械工程学院学院(系、部)2012 ~ 20 13 学年第 2 学期课程名称机电控制技术课程设计指导教师职称教授学生姓名专业班级学号题目压力机液压系统的电气控制成绩起止日期2013 年 6 月14 日~2013 年6 月23 日材料目录机电控制技术课程设计设计说明书压力机液压系统的电气控制设计起止日期:2013 年6 月14 日至2013 年6月23 日学生姓名班级学号成绩湖南工业大学课程设计任务书2012—2013学年第二学期机械工程学院(系、部)机械设计制造及其自动化专业课程名称:机电控制技术设计题目:压力机液压系统的电气控制完成期限:自2013 年 6 月14 日至2013 年 6 月23 日共1 周指导教师(签字):2013年6月23 日系(教研室)主任(签字):2013年6月23 日目录一、课程设计的内容与要求 (1)1.1课程设计对象简介 (1)1.2压力机结构及工作要求 (1)1.3液压系统工作原理及控制要求 (2)二、电气控制线路的设计…………………………………….4.2.1继电器-接触器电气控制电路的设计 (4)2.2继电器-接触器电气控制电路图分析及介绍 (5)2.3选择电气元件 (10)三、压力机的可编程控制器系统的设计 (11)3.1可编程控制器控制系统设计的基本原则 (11)3.2可编程控制器系统的设计 (11)1)可编程控制器硬件接线图 (13)2)控制梯形图 (14)3)压力机的状态转移图和步进梯形图 (16)四、设计心得体会 (18)五、参考资料 (18)一、课程设计的内容与要求1.1 课程设计对象简介压力机是锻压、冲压、冷挤、校直、弯曲、粉末冶金、成形、打包等加工工艺中广泛应用的压力加工机械设备。
液压压力机(简称液压机)是压力机的一种类型,它通过液压系统产生很大的静压力实现对工件进行挤压、校直、冷弯等加工。
液压机的结构类型有单柱式、三柱式、四柱式等形式,其中以四柱式液压机最为典型,它主要由横梁、导柱、工作台、上滑块和下滑块顶出机构等部件组成,。
- 1、下载文档前请自行甄别文档内容的完整性,平台不提供额外的编辑、内容补充、找答案等附加服务。
- 2、"仅部分预览"的文档,不可在线预览部分如存在完整性等问题,可反馈申请退款(可完整预览的文档不适用该条件!)。
- 3、如文档侵犯您的权益,请联系客服反馈,我们会尽快为您处理(人工客服工作时间:9:00-18:30)。
plc课程设计Cad版本PLC控制图---------------------------------------------(P5)1.4负载分析与计算---------------------------------------------(P6)2.液压系统的设计-------------------------------------------------(P8)2.1执行元件类型的选择----------------------------------------(P8)2.2控制回路选择与设计----------------------------------------(P8)-----------------------------------(P19)2.2.5PLC控制程序设计--------------------------------------(P21)4.结论----------------------------------------------------------( P22)参考文献--------------------------------------------------------(P2 3)10T压力机液压及控制系统设计摘要:液压压力机是一种利用液体静压力来加工金属、塑料、橡胶、木材、粉末等制品的机械。
它常用于压制工艺和压制成形工艺,如:锻压、冲压、冷挤、校直、弯曲、翻边、薄板拉深、粉末冶金、压装等等。
液压压力机由主机及控制机构两大部分组成。
主机部分包括液压缸、横梁、立柱及充液装置hine.Thecontrolmechanismiscomposedofanoiltank,ahighpres surepump,acontrolsystem,amotor,apressurevalve,adirection valve,etc..HydraulicmachineusingPLCcontrolsystem,throught hepumpandtheoilcylinderandavarietyofhydraulicvalvestoac hieveenergyconversion,regulationanddelivery,tocompleteth ecycleofvariousprocesses.Inthisdesign,thesizeofthehydrauliccylinderisdesigned,andthehydraulicprinciplediagramisdrawnup.Hydraulicpumps,motors, controlvalves,filters,andotherhydrauliccomponentsandauxilia rycomponentsareselectedaccordingtothesizeofpressureandfl ow.Keywords:hydraulicmachine;hydraulicsystem;PLC引言液压机是根据静态下液体压力等值传递的帕斯卡原理制成的,它生产出许多新型元件,未来几年我国压力机行业的发展将会越来越好,不断的向高端市场挺进,众多压机制造厂正在不断的改进技术,争取生产研究出更加出色的控制系统。
在国内外液压机产品中,按照控制系统,液压机可分为三种类型:一种是以继电器为主控元件的传统型液压机;一种是采用可编程控制器控制的液压机;第三种是应用高级微处理器的高性能液压机。
三种类型功能各有差异,应用范围也不尽相同。
但总的发展趋势是高速化、智能化。
在国际上来看,由于技术发展趋于成熟,国内外机型无较大差距,主要差别在于加工工艺和安装方面。
良好的工艺使机器在过滤、冷却及防止冲击和振动方面,有较明显改善。
1.工况分析与计算1.1工况分析压制力:压制时工作负载可区分为两个阶段。
第一阶段负载力缓慢地线性增加,初始压力为最大压制力的10%左右,其上升规律也近似于线性,第二阶段负载力迅速线性增加到最大压制5100.1⨯N。
回程力(压头离开工件时的力):一般冲压压力机的压制力与回程力之比为5~10,本压力机取为10,故回程力为410F N。
=0.1⨯h滑块质量m=300kg 。
(b)行程及速度快速空程下行:行程mm S 501=,速度m in /4.21m v =;工作下压:行程mm S 52=,初始速度m in /6.02m v =,之后随着油缸压力的增大而减小;(2)顶出液压缸(a)负载:被压件质量kg m 300'=F -----液压缸载荷a F -----下行部件所受惯性力m -----模具质量 v -----活塞速度变化量t -----活塞缸速度变化所用时间。
2.确定主液压缸结构尺寸根据有关资料,压力机的压力范围为2030MPa ,现有标准液压泵、液压阀的最高工作压力为25MPa,如选此压力为系统工作压力,液压元件的工作性能会不够稳定,对密封装置的要求以较高,泄漏较大。
参考系列中现己生产的其它规格同类压力机所采用的工作压力,本机选用工作压力为22MP柱塞缸内径D可根据最大总负载和选取的工作压力来确定。
(1)主液压缸内径D:F-----最大总载荷;P-----工作压力快下0 4.188工进18.32 1.47(8)活塞杆缸筒长度活塞长度B=(0.6~1.0)D=0.8⨯10=8mm;导向套长度A=(0.6~1.5)d=1.0⨯6=6mm;故主液压缸缸筒长度=L+B+A+l=834+l(mm)l-----活塞密封长度和特殊需要的其他长度2.液压系统的设计2.1执行元件类型的选择根据设计要求,液压机要实现“空程快速下降—慢速下降加压—保压—卸压及回程—停止”的工作循环,故采用液压传动方式来实现,采用液压缸作为执行机构。
进给速度改变的速度换接回路。
调速回路是通过事先的调整或工作过程中自动调节来改变执行器的运动速度。
考虑到液压机工作时所需功率大,故采用容积调速方式,本液压机采用泵—缸式。
速度换接回路的功用是使液压执行器在一个工作循环中从一种运动速度变换成另一种运动速度。
该液压机主要是实现从空载快速下行到慢速工进加压的速度转换。
为了自动实现“空程快速下降—慢速下降加压—保压—卸压及回程—停止”这一工作循环,采用行程开关、电磁换向阀和液控单向阀来实现顺序动作。
压力控制回路的作用主要是控制液压系统整体或某部分的压力,以使执行元件获得所需的力或力矩、或保持受力状态的回路。
溢流阀在此系统中实际就起安全保护阀的作用。
在压力调定回路中,溢流阀呈常开状态,起溢流和维持回路压力恒定作用。
回路的压力靠溢流阀调定,并在不断的溢流过程中保持回路的压力基本稳定。
保压回路的图2-11即为液压机的液压系统原理图,可实现空程快速下降、慢速下降、工作加压、保压、卸压回程、浮动压边及顶出等动作。
图2-4油路控制原理图中电磁铁动作顺序见表2-4。
表2-1电磁铁动作顺序表油缸动作名称电磁换向阀电动机1YA 2YA 3YA 4YA 5YA 1D主缸电机启动 + 快速下行 + + + 减速加压 + + 保压 + 卸压回程 + + 回程停止 + 顶出顶出 + + P ∑P ∑=0.5~1.5Mpa 。
因为系统工况中执行元件的最高压力是并且这个系统相对来说比较简单,所以本文选取压力损失P ∑=0.4Mpa ,这时系统工况中泵最高的压力为P ∑=17.99Mpa泵的最大流量回路系统的泄漏量和工况中执行元件的最大工作流量确定了液压系统中泵的最大供油量,即式中K 为液压系统中的泄漏或其他因素的修正系数,修正系数一般来K=1.1~1.3,小流量的时候通常取大值,大流量的时候通常取小值:max q ∑是同时动作的执行元件所需流量之和的最大值。
由工况图知快速下降行程中q 为最大(q=6104.188-⨯L/min ) 由此可知,行程油缸快速下行时所需要最大的流量为153.8L/min ,取修正系数K=l.l 。
则p Q =1.1⨯4.188=24.207L/min3.选择液压泵的规格由于液压系统的工作压力高,负载压力大,功率大。
大流量。
所以选轴向柱塞变量泵。
柱塞变量泵适用于负载大、功率大的机械设备,柱塞式变量泵有以下的特点,设计要求该系统工作效率高,发热少,能耗低,结构简单,因此该设计选择80CY(M)14-1B 型,根据《液压油管内径主要由油液通过的流速来确定,直径小流速高,压力损失小,甚至产生噪声和振动;直径大,不但难以弯曲安装,而且管路所占空间加大,机器重量增加,因此要合理选择油管内径。
可有下式确定:则油管内径:d =式中Q —液体流量,3m /s ;V —流速,m/s ,对于压油管,取v ≤3~6 m/s ;对于回油管路,v ≤1.5~2.5 m/s 。
因此管道直径计算如下:液压泵吸油管道:(取v=2.5m/s ,q=207.24L/min )mm vQd 5465.124.207464=⨯⨯⨯==ππ取mm d 601=液压系统压油管道:(取v=6m/s ,q=207.24L/min )液压系统初步设计是在某些估计参数情况下进行的,当回路形式、液压元件及连接管路等完全确定后,针对实际情况对所涉及的系统进行各项性能分析。
主要包括计算液压回路各段压力损失、统计损失及系统效率、压力冲击和发热温升等。
1.液压系统压力损失压力损失包括管路的沿程损失1P ,管路的局部压力损失2P 和阀类元件的局部损失3P ,总的压力损失为:由于供油流量的变化,其快上时液压缸的速度为10m/min 此时油液在进油管中的流速为:326169.2510v 1.44501060/4pQ x A π--===⨯⨯⨯m/s(1)沿程压力损失v 的功率损失大引起发热量较大,所以只考虑工进时的发热量,然后取其值进行分析。
当v=0.4m/min 时:此时泵的效率为0.85,泵的出口压力为27.3MP ,则有;27.324.63=13.2600.85P KW KW ⨯=⨯输入此时的功率损失为:假定系统的散热状况一般,取32=2010/()K KW cm -⨯⋅℃ 油箱的散热面积A 为: 系统的温升为:室温为20℃,热平衡温度为44.06℃,根据《机械设计手册》成大先P20-767:油箱中温度一般推荐30℃-65℃,验算表明没有超出允许范围。
3.液压压力机控制系统设计进步和提高。
但是其控制部分还采用传统的控制手段,例如继电器的控制系统,接线比较复杂,机械触点较多,可靠性偏低。
这些局限性和缺点都可以通过采用可编程控制器来克服和弥补。
可编成控制器(PLC)是20年代60年代末,它随着计算机的发展而发展起来,是一种新型的工业通用控制器。
它的使用非常简单、方便,能够让工程技术人员熟悉的传统继电器的梯形图进行编程,来满足设备多变的控制要求,对控制系统来说有极大的柔性、通用性,它能够取代传统的继电器控制或者是其他类型的控制器。