饲料生产线自动化控制系统的设计(1)
食品加工生产线自动化控制系统设计

食品加工生产线自动化控制系统设计第一章:引言随着工业自动化的不断深入发展,自动化控制系统已经在许多领域得到广泛的应用。
食品加工生产线自动化控制系统是其中之一,其在提高生产效率、质量稳定性和安全性等方面具有很大的优势。
该系统可以帮助企业节省大量的人力和物力成本,并且可以降低生产过程中的风险和错误率。
本文就食品加工生产线自动化控制系统设计进行探讨。
第二章:食品加工生产线自动化控制系统分类食品加工生产线自动化控制系统大致可分为以下几类:1. 前段生产自动化控制系统:自动完成蔬菜、肉类等食材的清洗、切块、研磨、混合等准备工作。
2. 食品加工自动化控制系统:用于完成烘焙、蒸煮、烧烤、炸制、冷却等加工工序,可以实现多种工艺配方,保证生产线的稳定性和一致性。
3. 后段生产自动化控制系统:主要用于完成包装、称重、贴标、封口等工序,确保产品的质量卫生和生产的效率。
本文主要讨论第2种食品加工自动化控制系统的设计。
第三章:自动化控制系统的组成食品加工自动化控制系统由以下几个部分组成:1.电气控制系统:主要包括自动控制设备、电力配电系统和电缆线缆等,其中,自动控制设备是核心,它能根据预设的程序和信号,自动实现生产过程中的各项控制操作。
2. 控制装置:根据生产的流程和工艺要求,对生产过程中所涉及的机械元件、传送带、输送带等进行自动控制,并可以对温度、压力、流量等重要参数进行采集和监控。
3. 传感器:主要负责采集压力、温度、重量、速度等生产关键参数的信息,并将其传递给控制装置。
4. 执行机构:能够自动完成机械元件的启停、升降、输送带的运转和成品包装等工艺要求,以实现生产线上的自动化生产。
5. 人机界面:主要是指触摸屏、显示屏、键盘等设备,它们负责控制系统的显示、输入、操作和信息输出。
第四章:使用PLC进行自动化控制系统的设计PLC(Programmable Logic Controller)是一种通用现场可编程控制器。
主要用于自动化领域中的执行控制、序列控制、计时计数、数据处理等,广泛应用于各种工业控制系统中。
PLC与组态软件的饲料加工自动控制系统的设计开题报告
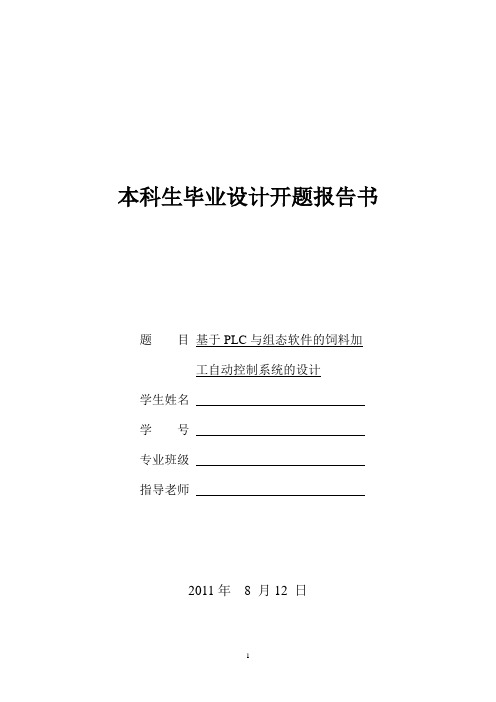
本科生毕业设计开题报告书题目基于PLC与组态软件的饲料加工自动控制系统的设计学生姓名学号专业班级指导老师2011年8 月12 日论文(设计)题目基于PLC与组态软件的饲料加工自动控制系统的设计课题目的、意义及相关研究动态:饲料工业是畜牧养殖业的基础。
我国饲料工业从上世纪70年代中后期,经过近四十年的发展,我国饲料业已完成了从手工作坊式的生产到世界第二大饲料生产国的飞越,成为我国重要的支柱产业之一。
但是饲料厂的配套自动控制系统和高精度配料控制系统还相对滞后,因此实现安全可靠的自动控制系统和高精度配料系统就显得十分迫切和必要。
饲料厂自动控制系统的发展经历了人工手动控制、机械电气控制、单片机控制、工业计算机集中控制等几个阶段。
第一阶段:饲料加工技术比较简单,各机械之间没有逻辑联系,现场操作人员一般只负责一到两个设备的操作与监控,并手工记录各项数据,产品质量人为因素很大。
第二阶段:继电器手工控制在很大程度上降低了工人的劳动强度,但大量的中间继电器和时间继电器组成的电控系统非常复杂,可靠性极低,特别是调试和改造时难度很大。
第三阶段:随着大规模集成芯片技术的的成熟,单片机控制系统应运而生。
单片机配料系统较之前两种系统设计电路复杂程度降低,可靠性大大提高,但其抗干扰能力比较差也局限了它的应用。
第四阶段:随着计算机技术的迅猛发展和广泛应用,基于工控机的饲料厂自控系统也开始出现,这种系统大多采用集中控制方式。
计算机除具有工艺流程控制、工况实时显示、提供数据存储、报表打印等功能等功能外,还要完成对各象的直接控制和数据采集任务。
在经济不断发展,科技日新月异的今天,科学技术越来越多的应用于饲料工业中,特别是现场总线和计算机技术的迅猛发展,饲料工业的自动化控制水平也在相应提高。
美国及欧洲的一些国家的饲料厂从进料到成品散装出料,全部为计算机自动控制,整厂单班操作人员只需要两人。
饲料厂的管理和控制全部通过计算机进行操作,管理系统采用先进的模块化结构,可根据各部门职能选择不同的系统模块。
智能饲料系统的设计与优化研究

智能饲料系统的设计与优化研究随着人们对食品安全、环保和动物福利的重视,畜牧业也迎来了新的挑战和机遇。
在现代畜牧业中,饲料作为一个重要的环节,关系着畜牧业的生产效率、生产成本和产品质量。
为了满足畜牧业的需求,越来越多的农民和养殖场开始采用智能化饲料系统来优化饲料的调配、提高饲料的利用率和节约生产成本。
一、智能饲料系统的设计与构成智能饲料系统是一种自动化控制系统,它主要由三部分组成:饲料配料系统、饲喂系统和监控系统。
1.饲料配料系统饲料配料系统是智能饲料系统最关键的部分,它主要由配料仓、配料机、输送机、称量系统、料斗等组成。
配料仓是饲料配料系统的核心部件,其作用是存放各种原料和辅料。
而配料机、输送机、称量系统等设备则是完成食品加工工作的重要组成部分,通过它们将各种饲料原料按照配方比例混合制成具有一定营养成分的饲料。
2.饲喂系统饲喂系统是智能饲料系统的第二大部分,它主要由饲喂装置、控制器、传感器等设备组成。
饲喂装置是饲喂系统的核心部分,其作用是将配好的饲料自动供给到动物嘴边。
控制器则是负责控制饲喂装置的运转和精准控制饲喂量的设备,传感器也是非常重要的组成部分,它可以实时感知到动物的饮食状态,并根据情况进行调整。
3.监控系统监控系统是智能饲料系统的第三大部分,它主要由监控器、计算机、传感器等设备组成。
可以通过监控系统获得饲料的各种参数,例如:饲料的重量、饲喂量、饲喂时间等。
同时,监控系统还可以记录饲料的消耗量和动物的饮食情况,提供数据参考用于饲料调配优化。
二、智能饲料系统的优势与应用与传统饲料系统相比,智能饲料系统具有以下优势:1.减少饲料浪费: 能够精准控制饲料的投喂量,减少饲料的浪费,节约生产成本。
2.提高饲料的利用率: 将各种饲料原料按照配方比例混合制成具有一定营养成分的饲料,提高饲料的利用效率。
3.节省生产成本: 智能饲料系统的运转需要较少的人力,降低了生产成本。
4.保障动物健康: 合理的饲料配方和饲喂量可以提高动物的饮食质量,保证动物的健康。
基于单片机的饲料自动供给系统设计论文

摘要现代工业生产正处于一个劳动密集型,设备密集型,信息密集型向知识密集型转变的过程。
在这一过程中,智能控制无疑起着重要的作用,单片机为核心的智能控制系统具有成本低,可靠性好的特点,同时具有实现下载和灵活设置参数的功能,具备扩展功能,可以增加控制方式,有很好的扩展性和兼容性.本设计主要通过单片机对步进电机的控制完成带传动,实现饲料的自动供给.根据现有条件和项目的要求,本文综合分析和对比了几种改造方案,最后使用单片机与步进电机组成系统。
单片机系统是整个控制系统的核心,数据的读取和处理、电机的调速控制、数据的显示和报警都由它完成。
本论文详细的分析了单片机控制板及其接口的组成和开发过程,介绍如何使用单片机、步进电机控制系统,以及使用单片机、键盘与显示、报警控制系统。
对于实际应用系统实用方便与实用性是重要的,因此在论文中,从硬件和软件两方面分析和研究了整个系统的实用性与方便性,使得整个系统能够安全、稳定地工作。
关键字:单片机; 步进电机;自动调速ABSTRACTModern times industry production is in a change process of labor denseness, facility denseness and information denseness to knowledge denseness. Aptitude control plays a important role in this process. As a result of the aptitude control system based on SCM has the characteristic of low cost and good reliability and it has the function of download and agile parameter setup, agile spread at the same time, the system will be expansibility and compatibility.The design mostly gets across the SCM control about stepping motor to fulfill belt drive, and achieve feed automatic-provide. According to the current condition and the request, this paper analyses and contrasts some reform project, then using single chip computer and stepping motor to constitutes the system .two stage control system. The SCM that is the center of the whole control system is used to collect and process the data, adjust the speed of the electromotor and display the data, give the alarm. This thesis not only fully discusses the constitution and designed process but also introduces how to use single chip computer, stepping motor control system and single chip computer, keyboard and vision, alarm control system.For the practical and applied system, the reliability and facility is very important. So the reliability and facility of the whole system is analyzed from hardware to software o make the whole system operate safely and steadily.Key W ords:SCM; stepping motor; speed regulation目录1绪论 (1)1.1课题的研究背景 (1)1.2 课题的研究意义 (1)1.3 课题的研究内容 (1)2 饲料自动供给系统设计分析 (3)2.1供给控制系统方案分析 (3)2.1.1方案理论实现的理论设计基础 (3)2.1.2单片机的选择 (4)2.1.3步进电机的选择 (5)2.2 供给系统控制设计 (6)2.3 系统总电路设计 (7)3供给系统带传动的调速 (9)3.1步进电动机的工作原理与动态特征 (9)3.1.1步进控制与驱动系统的构成 (9)3.1.2 步进电机的选用 (10)3.1.3 步进电机的工作原理 (11)3.1.4步进电机的动态特性 (11)3.2 步进电动机的控制与调速 (12)3.2.1 步进电机控制系统的构成 (12)3.2.3 步进电机的速度控制 (13)4 控制系统硬件设计分析 (15)4.1 系统的硬件结构 (15)4.2 AT89S52 单片机的选用 (16)4.2.1 89S52单片机基本结构 (16)4.2.2 AT89S52单片机存储器的结构 (18)4.3系统的硬件分析与扩展 (20)4.3.1 键盘电路的设计 (20)4.3.2 显示电路设计 (21)4.3.3 报警电路的设计 (22)I4.3.4步进电机及其驱动电路的设计 (22)4.4 硬件系统的合成 (23)4.5 系统的抗干扰设计 (24)5系统的软件设计分析 (25)5.1 编写单片机应用程序的基本方法 (25)5.2 饲料供给系统程序流程 (26)结论 (29)参考文献 (30)附录一系统软件程序 (31)附录二系统总电路图 (37)附录三总电路PCB板图 (38)致谢............................................................................................... 错误!未定义书签。
饲料厂配料自动控制系统

图2配料仓配料示意 图
2 系统 的硬 件设 计
在进行具体电路设计之前 ,得根据系统及实际情况 的要求 ,进行各 个硬件器 件的选型 ,具体 包括 :传感器 、电动机 、接触 器 、电磁 阀和 Dk O I 卡等的选型 , D 使之符合生产 的要求 。 21 电源模块设计 . 本 系统 电路分为多个模块 ,而不同的模块对 电源的 电压 、电源质量 等要求都不一样 。电源对于每个 电路单元来说都 十分重要 ,尤其在系统 设计精度比较高时 ,整机的指标和 电源的质量密切相关 ,因此设计性能 优越并适合系统的电源电路是很有必要的。 对于数字电源和模拟电源 , 控制器采用从交流20 经变压为较低 电 2 V 压后 经过整 流桥为直流 ,然后经三端正 向稳压电源7 1和7 2后变成直 82 84 流l 和2 电源 。模拟 电源和数字电源分别用不 同变压绕组 , 2 V 4 V 两路 电 源互不 干扰 。由于模拟电源对 电压纹波等指标要求较为严格 , 在设计模 块地 时需加入更为严格的滤波措施 ,模拟地需通过 电感和担电容进一步
图1 系统整体结构框图
12 系统 的 工 艺 流 程 .
主要 工艺设备 :①螺旋给料机一 用于输送和分配原料 ; 电子配料 ② 秤一用 于饲料称 重 ;③电动 闸门一 用于控制进 料 ;④料位器一 用于检 测控制筒仓里原料 的料位 ;⑤混合机一 用于把各种不 同品质的饲料进行
混合。 系统工艺流程 简介 :
2 . 负载传感器的联接 .1 2 由于 电子秤采用四个传感器来进行物料 的称重 ,这就涉及 到传感器 是串联还是并联 ,现对两种联接方式介绍如下 。 1 串联组合称重方式 :每个传感器使用独立电源单独供 电,而4 ) 个 传感器 的输出端 串联连接。 对于型号规格相 同的多个传感器来说 如果 激励电源电压 u 相同 ,而 且输出电压敏度s 也~致相等 ,那么这样 ,就可以保证传 感器串联组合 后总输 出信号与秤体承载总重量w成正 比。串联组合后 ,总的输 出信号 为各传感器输 出信号之和∑u ,总的输 出阻抗为各感器输 出阻抗之和 。 2 并联组合称重方式 :各个传感器输入 端并联 , 用一个公共电 ) 使 源供 电,输出端也 以并联 的方式工作 。 多传感器输出端并联组合后 ,多个传感器并联工作 和一个传感器_ T 作时的输 出电压 是相等 的;总的输出信号为各传感 器输 出信号之 和的 I ;但并联后的输出电阻却减小 为一个传感器的1 。 / n , n 多传感器 串、并联联接方式如图4 。
饲料混合机的自动化控制系统研究与应用
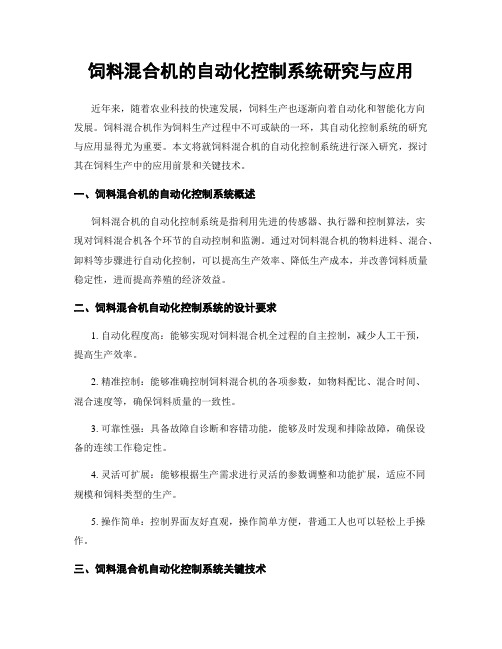
饲料混合机的自动化控制系统研究与应用近年来,随着农业科技的快速发展,饲料生产也逐渐向着自动化和智能化方向发展。
饲料混合机作为饲料生产过程中不可或缺的一环,其自动化控制系统的研究与应用显得尤为重要。
本文将就饲料混合机的自动化控制系统进行深入研究,探讨其在饲料生产中的应用前景和关键技术。
一、饲料混合机的自动化控制系统概述饲料混合机的自动化控制系统是指利用先进的传感器、执行器和控制算法,实现对饲料混合机各个环节的自动控制和监测。
通过对饲料混合机的物料进料、混合、卸料等步骤进行自动化控制,可以提高生产效率、降低生产成本,并改善饲料质量稳定性,进而提高养殖的经济效益。
二、饲料混合机自动化控制系统的设计要求1. 自动化程度高:能够实现对饲料混合机全过程的自主控制,减少人工干预,提高生产效率。
2. 精准控制:能够准确控制饲料混合机的各项参数,如物料配比、混合时间、混合速度等,确保饲料质量的一致性。
3. 可靠性强:具备故障自诊断和容错功能,能够及时发现和排除故障,确保设备的连续工作稳定性。
4. 灵活可扩展:能够根据生产需求进行灵活的参数调整和功能扩展,适应不同规模和饲料类型的生产。
5. 操作简单:控制界面友好直观,操作简单方便,普通工人也可以轻松上手操作。
三、饲料混合机自动化控制系统关键技术1. 传感器技术:通过安装适当的传感器,实时监测饲料混合机各项参数,如物料流量、温度、湿度等,提供准确的数据支持。
2. 控制算法:利用先进的控制算法,对饲料混合机进行精准控制,实现自动化生产过程中的配比、搅拌、卸料等操作。
3. 数据通信技术:通过网络通信技术,实现饲料混合机与上位机之间的数据传输和控制指令的交互,实现遥控和远程监控。
4. 故障诊断技术:通过故障诊断技术,对饲料混合机在生产过程中出现的故障进行诊断和处理,提高设备的可靠性和稳定性。
5. 人机界面技术:通过友好直观的人机界面,实现对饲料混合机的操作和监控,提高操作的简易性和工作效率。
自动化控制系统设计方案

自动化控制系统设计方案引言概述:自动化控制系统是现代工业生产中的重要组成部份,它能够提高生产效率、降低成本、提高产品质量。
设计一个合理的自动化控制系统方案对于企业的发展至关重要。
本文将从硬件选型、软件设计、通信网络、安全性和可靠性等方面介绍一个完善的自动化控制系统设计方案。
一、硬件选型1.1 选择适合的控制器:根据控制系统的需求,选择性能稳定、可靠性高的控制器,如PLC、DCS等。
1.2 选用合适的传感器和执行器:根据控制系统的具体要求,选择适合的传感器和执行器,如温度传感器、机电执行器等。
1.3 电源和接线选型:选择合适的电源和接线材料,确保系统稳定可靠。
二、软件设计2.1 确定控制算法:根据系统的控制需求,设计合适的控制算法,如PID控制、含糊控制等。
2.2 编写控制程序:根据控制算法,编写相应的控制程序,确保系统能够按照预定的控制逻辑运行。
2.3 调试和优化:在实际运行中对控制程序进行调试和优化,确保系统运行稳定、效率高。
三、通信网络3.1 选择合适的通信协议:根据系统的通信需求,选择适合的通信协议,如Modbus、Profibus等。
3.2 设计网络拓扑结构:根据系统的通信规模和复杂度,设计合适的网络拓扑结构,确保通信畅通。
3.3 确保通信安全:采取相应的安全措施,如数据加密、防火墙等,确保通信过程安全可靠。
四、安全性4.1 设计安全控制策略:在系统设计阶段就考虑安全性问题,设计合适的安全控制策略,确保系统运行安全。
4.2 安全监控和报警:设计安全监控系统,及时监测系统运行状态,设定相应的报警机制,确保及时处理异常情况。
4.3 定期维护和更新:定期对系统进行维护和更新,确保系统设备正常运行,防止安全隐患。
五、可靠性5.1 设计冗余系统:在系统设计中考虑冗余系统,确保系统在部份设备故障时仍能正常运行。
5.2 定期检测和维护:定期对系统进行检测和维护,发现问题及时处理,确保系统可靠性。
5.3 持续改进:不断改进系统设计方案,根据实际运行情况进行调整和优化,提高系统的可靠性和稳定性。
自动化控制系统设计方案

自动化控制系统设计方案一、引言自动化控制系统设计方案是为了实现工业生产过程的自动化控制,提高生产效率和质量,减少人力资源的浪费,降低生产成本。
本文将详细介绍自动化控制系统设计方案的内容和要求。
二、系统概述1.系统目标本系统旨在实现对工业生产过程的自动化控制,包括生产线的自动化监测、控制和优化,以及数据的采集、存储和分析。
2.系统架构本系统采用分布式控制架构,包括传感器、执行器、控制器、通信网络和人机界面等组成。
其中,传感器负责采集环境参数,执行器负责控制设备运行,控制器负责处理数据和控制算法,通信网络负责传输数据,人机界面负责与操作人员进行交互。
三、系统设计1.硬件设计(1)传感器选择:根据生产过程的特点,选择适合的传感器进行环境参数的采集,包括温度、压力、流量等。
(2)执行器选择:根据设备的控制需求,选择适合的执行器进行设备的控制,包括电动阀门、机电等。
(3)控制器选择:根据系统的控制要求,选择适合的控制器进行数据处理和控制算法的实现,包括PLC、DCS等。
(4)通信网络设计:设计合理的通信网络结构,确保数据的可靠传输,包括以太网、Modbus等。
(5)人机界面设计:设计直观、易用的人机界面,方便操作人员进行监控和控制。
2.软件设计(1)数据采集与存储:设计数据采集模块,实现对传感器数据的采集和存储,包括历史数据和实时数据。
(2)控制算法设计:根据生产过程的特点,设计合适的控制算法,实现对设备的自动控制和优化。
(3)数据分析与报表:设计数据分析模块,对采集到的数据进行分析和统计,生成相应的报表和图表,为决策提供支持。
(4)人机界面设计:设计友好、易用的人机界面,包括监控界面和操作界面,方便操作人员进行监控和控制。
四、系统实施1.系统安装根据系统设计方案,进行硬件设备的安装和调试,确保各个组件的正常工作。
2.软件开辟根据系统设计方案,进行软件模块的开辟和测试,确保各个功能的正常运行。
3.系统集成将硬件设备和软件模块进行集成,进行整体测试和调试,确保系统的稳定性和可靠性。
- 1、下载文档前请自行甄别文档内容的完整性,平台不提供额外的编辑、内容补充、找答案等附加服务。
- 2、"仅部分预览"的文档,不可在线预览部分如存在完整性等问题,可反馈申请退款(可完整预览的文档不适用该条件!)。
- 3、如文档侵犯您的权益,请联系客服反馈,我们会尽快为您处理(人工客服工作时间:9:00-18:30)。
上传通讯信息。上位机和PLC之间采用主从轮询控制方式,上 位机作控制主站,PLC作控制从站,根据控制规模可由一台或多 台组成。称量检测单元采用高精度S型称重传感器、称重变送 器、和A/D模块组成,配料称斗上安装了3只称重传感器。计算 机通讯单元由通讯卡、通讯协议软件、通讯转换器、电缆及接头 组成,控制规模不同形式有所区别。控制单元由电气控制电路组 成,PLC通过输出点控制电气电路按程序工作,控制单元控制配 料绞龙起停、称斗放料、混合机计时、手自动转换、手动控制、状 态设定、报警输出等。
S7—200 PLC作下位机,接受处理上位机传递的控制指令及控
述缺点外,还存在以下缺点:④抗电磁干扰能力差,测量值经常波 动,系统稳定性差。②计算机的输入、输出板受外界影响,经常损 坏,尤其输出板更容易损坏,后期维护工作量大,维护费用高。⑧
控制集成程度过高,并且计算机系统本身的稳定性有限,一旦计
算机出现故障,整个自动控制系统瘫痪。④计算机寿命短。随时间
《工业控制计算机)2005年18卷第11期
饲料生产线自动化控制系统的设计
孟庆才 王焕荣
赵宝国
(河北裕丰实业股份有限公司,衡水053000)
摘要
介绍了饲料生产线电气设计、计算机自动配料、自动打包及计算机通讯技术在饲料生产线的应用、软硬件设计。 关键词:饲料流水线,电气控制,PLC,自动配料,自动打包,控制系统,现场总线控制,通讯技术 2002年5月,兴亚饲料公司新建一条饲料生产线,生产工 艺流程、电气配套设计及自动化控制设计由本公司独立完成,开 发了具有独特特点的计算机与PLC总线控制19动配料系统、自 动打包控制系统。 1计算机自动配料控制系统 1.1方案设计 计算机自动配料是饲料生产的核心工序,直接影响饲料产 品质量。目前国内计算机配料同类系统中,主要有在三种形式。 1)一种形式是PC机+数据采集卡+配料绞龙点动配料方式。 这种方式主要由计算机、数据采集卡、外围继电器、接触器等外 围电路组成。配料时通过A/D转换,将称重信号送人计算机,然 后计算机根据配方,直接通过插在内部插槽的输出板,信号放 大,直接驱动继电器、接触器吸和断开。采用工业控制机直接控 制绞龙配料控制方式,硬件投资较低、控制形式简单,配料采用 点动配料形式,但存在一个缺陷,即随机误差很大。我们曾做过 实验,如采用点动配料形式,点动时间即使控制在O.1s,较轻的 物料如烘干的酒精糟下料绝对误差大于0.7kg,比重较大的石 粉下料误差则在1.5kg以上。这种控制方式,在配料过程中不断 地靠继电器、接触器反复吸合,这样会产生了较大的电感电势和 电磁干扰,造成计算机控制输出板等器件损坏。这种系统主要应 用在对配料精度要求不高的场合,正逐渐淘汰。 2)另一种形式是PC机+数据采集卡+变频器+配料绞龙点 动配料方式。目前是国内采用最多的控制形式,最具中国特色。 采用工业计算机直接控制驱动电路工作,改善了点动配料的不 足,使配料精度提高,具有一定的性价比。目前,大多还是采用 DOS操作系统,由C语言开发的系统,系统界面较差,系统的网 络通讯功能和管理功能有限,人机交互不方便。通过对控制软件 的改造及更换操作系统,在理论上可望提高系统运行可靠性。 第一种和第二种配料控制形式由于都采用了计算机+数据采 集板的方式,由计算机直接控制外围电路工作,它们除具有以上 通讯的控制模式。上位机采用工业计算机,下位机一般采用智能 数字模块或PLC。系统采用先进的计算机控制技术与多层次网 络结构+先进的控制算法对生产工序进行控制。这是自动化领域 先进的控制形式,它结合了计算机的通讯和管理功能强、存储能 力大的优势特点和智能数字模块或PLC现场控制功能强、稳定 性高的特点,有效避免了计算机集中控制的缺陷。这种系统稳定 性很高,上位机可兼容多种通讯协议(如TCP/IP协议等),便于 下一步与管理网络联结,这种控制方式是国内饲料生产线自动 化控制的主流方向。这种方式设备投资较大,除了较高的硬件投 资外,还需较高的软件开发费用。在下位机采用PLC性能的可 靠性高于采用智能数字模块,一般PLC连续工作寿命可达10 年以上。我们在该系统中采用工业计算机+PLC的分布总线控 制的方式。该系统由我公司自己独立设计,软件开发费用低,基 本上只投资硬件,设备投资不会增加太多。具有良好的设备替换 性。整套设备全部采用了标准器件,如上位机可进行软件升级, 或用更高档的计算机代替原计算机,系统不受影响。下位机由 PLC及模块组成,即使损坏的情况下,可直接更换。 1.2主要工作过程 首先计算机根据生产工艺单把相应的配方和生产工艺参数 传递到下位机PLC,生产开始后,由下位机PLC根据配方参数 及下料顺序,控制变频器启动配料绞龙工作,称重信号由PLC 检测。称量完成后,配料秤斗门自动打开,当混合机内有料时,秤 斗门等着混合机放料关门到位后打开。秤称斗开门时间到达后, 检测称斗上的余料,当余料超过设定的限制值,系统进行报警, 秤称斗门不关闭;当低于限制值,秤门关闭。称门关闭到位后,如 果没有达到预定生产批次,配料继续,同时发出添加预混料和油 脂添加信号。预混料添加完成应答复位后,混合机开始混合计 时,达到混合时间后,混合机根据缓冲斗的料位情况开门放料。 混合机开门记时,开门时间到达后,混合机门自动关闭,等下一 批料落下后,开始新一轮的循环。在整个生产过程中,由PLC控 制现场所有设备,工控机通过与PLC通讯方式监控PLC的运 行状况,并在线记录生产数据,提供报警、数据汇总查询、文档打 印等。另外,粒料打包机PLC和粉料打包机的PLC也可以通过 通讯电缆直接和自动配料的PLC相连,进而与上位机通讯,在 控制室监控自动打包系统运行。 1.3硬件设计 该控制系统主要由工业控制机、PLC、现场控制屏丁D200、 称重信号检测单元、重量信号处理单元、计算机通讯单元、输入 控制检测单元、输出控制单元等组成。研华工业控制机作上位 机,负责下位机运行监控、数据记录查询、配方管理、参数处理传 递、异常报警记录、文档管理打印,计算机网络通讯等;西门子
制参数、采集称量信号、检测输入单元状态、控制输出单元工作、
78
饲料生产线自动化控制系统的设计 包机控制方式中采用西门子PLC控制,称重传感器采用两套抗 侧偏能力强的剪切梁式称重传感器,参数设定通过TD200中文 显示控制器,有手动/自动切换功能。打包机电控部分、软件开发 根据技术要求和物料性质来设计的。 粒料由于流动性好,不易结弓,采用重力自落料形式,通过 调节物料下落的闸门开度控制落料速度,闸门全开时为快速加 料,当达到设定的快加料量时,软件进行惯性自动检测,根据惯 性量的大小,自动调整快加料量,然后系统进入慢加料状态,在 该过程中也进行惯性量检测,自动调整慢加料量,最后判断误差 进行点动加料。与国内同类设备相比,计量精确、打包速度快。 对于粉料物料性质相反,粉碎越细,纤维物料越多,流散性越 差,喂料方式为皮带称。通过调节皮带称的转速和料层厚度,做到 精确控制落料。其工作过程与粒料基本相同。控制流程图如图2。
匝r当隰露卜叫互
通讯光电转换 隔离器
!竺!:
EM277
EM277
现场控制I!塑竺型!!!I厂磊再茅石—;夏]厂磊再jj石面
矢量 变频器
AID
uO模
AdD
UO模 块
AdD
模块Jj块
模块J
模块】J
l∞模
块
配料 绞龙
I#2#I l输入,输l l#2撑传l l输入/『 3#传感l l出摔制l l感器l l输出控l 图1系统结构
延长故障率越来越大,由于器件、板卡更新得很快,往往稍老一些 的计算机板卡损坏后,往往找不到配件,从而造成整个系统报废。
⑤器件的可替换性差。采用一种型号的板卡很难被其它型号或其
它厂家的产品代替,尤其有些系统应用了一些自己开发的一些板 卡电路,损坏后备件的来源受很大限制。在第二种方式中,虽然采 用了变频配料形式,但测量、控制上的一些根本性问题没有解决, 系统很难达到很高的精度和很好的控制效果。 3)第三种控制方式为分布式控制形式,采上位机与下位机
饲料生产线自动化控制系统的设计
作者: 作者单位: 孟庆才, 王焕荣, 赵宝国 河北裕丰实业股份有限公司,衡水,053000
本文链接:/Conference_6195702.aspx
1#2撑传I I输入/输 I感器I l出控制
围◇ 困◇
—__——一Y
快加料
稠承篙岛
泸 雩汴
—}
■R
在本工程设计中,为了避免电源对系统造成的干扰,计算 机、所有PLC、工控仪表、变送器采用一体化供电方式,它们的电 源均由在线式UPS连续供电。 1.4软件设计 该控制系统软件主要包括三部分:上位计算机控制软件、 PLC控制软件、计算机与PLC通讯软件设计 (1)上位机控制软件 上位机软件采用VB编程语言开发,软件主要由配方管理、 生产工艺单管理、成品入库管理、生产过程监控、数据记录查询 系统、通讯程序、故障自诊断、掉电数据保护、生产报表打印等部 分组成,各部分相互衔接,组成了一个有机整体。生产时,只要输 入生产工艺单,将工艺参数和生产配方传到下位机,启动系统即 可进行配料。在生产过程中,根据需要可随时进行暂停、跳仓操 作,还可在线传送配方。 (2)下位机PLC控制软件 下位机PLC软件采用西门子专用语句开发,下位机有两个 通讯口,一个通讯口连接TD200现场控制屏,另一个与通讯电 缆、通讯转换器、通讯卡与计算机相连。工作时PLC随时接收上 位机下达的各项指令,执行现场控制操作、上传生产数据、输入 输出工作状态。上位机故障时,可由现场控制屏输入生产数据, 下位机脱离上位机,照常能进行自动配料工作。 (3)计算机与PLC通讯软件设计 计算机和PLC采用Profibus—DP工业总线通讯方式,工作 方式为主从轮询方式。上位机通讯软件由VB编程实现,下位机 通过编程实现。 2自动打包控制系统 本工程有两台自动打包机,1台用于粒料打包、1台用于粉 料打包,打包称的量程设定范围为20-50kg/袋,每台可储存24 个品种的打包参数,静态误差小于等于±0.1%FS,打包动态误差 小于等于士0.2%FS,符合了国家对饲料打包称的计量标准。在打