食品加工生产线自动化控制系统设计
自动化生产线控制系统设计实践报告
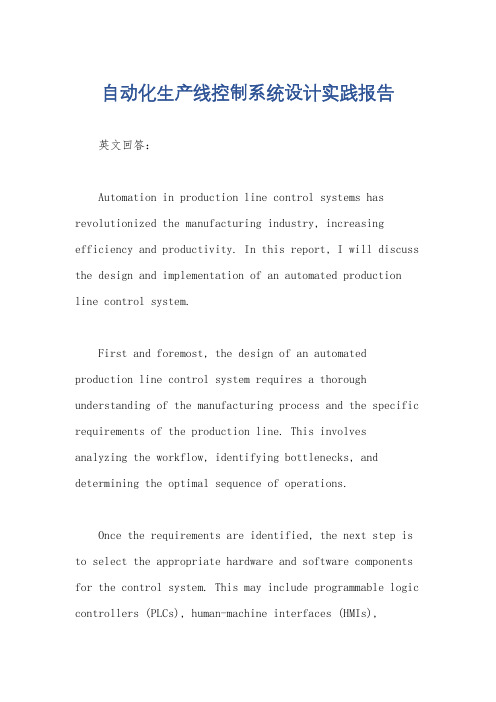
自动化生产线控制系统设计实践报告英文回答:Automation in production line control systems has revolutionized the manufacturing industry, increasing efficiency and productivity. In this report, I will discuss the design and implementation of an automated production line control system.First and foremost, the design of an automated production line control system requires a thorough understanding of the manufacturing process and the specific requirements of the production line. This involves analyzing the workflow, identifying bottlenecks, and determining the optimal sequence of operations.Once the requirements are identified, the next step is to select the appropriate hardware and software components for the control system. This may include programmable logic controllers (PLCs), human-machine interfaces (HMIs),sensors, actuators, and communication protocols. For example, in a car manufacturing plant, PLCs can be used to control the assembly line, HMIs can provide real-time information to operators, and sensors can detect any abnormalities in the production process.After selecting the components, the control systemneeds to be programmed to execute the desired tasks. This involves writing code to control the sequence of operations, monitor the status of various components, and handle any exceptions or errors. The programming language used canvary depending on the specific control system, but commonly used languages include ladder logic, structured text, and function block diagram.Once the control system is programmed, it needs to be tested and validated before it can be deployed in the production line. This involves simulating various scenarios and verifying that the control system behaves as expected. For example, in a food processing plant, the control system can be tested by simulating different ingredient mixtures and verifying that the correct proportions are maintained.In addition to the design and implementation of the control system, it is important to consider the maintenance and troubleshooting aspects. This includes regular inspections, software updates, and addressing any issuesthat arise during operation. For example, if a sensor malfunctions in a packaging line, it needs to be replacedor repaired promptly to avoid disruptions in the production process.中文回答:自动化生产线控制系统的设计与实施,对于提高制造业的效率和生产力起到了革命性的作用。
食品行业中的智能产线控制系统的应用案例分析

食品行业中的智能产线控制系统的应用案例分析引言:随着科技的发展和创新,智能产线控制系统在各个行业得到了广泛应用,其中食品行业也不例外。
智能产线控制系统能够提高生产效率、降低成本、提高产品质量,并具有自动化、智能化和可追溯性等特点。
本文将分析食品行业中智能产线控制系统的应用案例,探讨其在提高食品生产效率和质量方面的优势。
一、智能产线控制系统在食品行业中的应用案例1. 生产工艺的自动化控制智能产线控制系统在食品行业中的一个主要应用是对生产工艺的自动化控制。
通过传感器、机器视觉和自动化设备,智能产线控制系统能够实时监测和控制生产过程中的温度、湿度、压力等参数,从而实现生产工艺的自动化调节和优化。
例如,在面包制造过程中,智能产线控制系统可以自动调节烤箱温度和时间,以确保面包在烘烤过程中的质量和口感。
2. 产品质量的在线检测与控制智能产线控制系统在食品行业中的另一个重要应用是对产品质量的在线检测与控制。
通过借助机器视觉和传感器技术,智能产线控制系统能够实时检测和分析产品的外观、大小、重量等参数,从而实现对产品质量的精确控制。
例如,在蔬菜加工过程中,智能产线控制系统可以通过机器视觉技术对蔬菜进行分类和分级,从而保证产品的一致性和品质。
3. 供应链管理的优化智能产线控制系统在食品行业中还可以用于供应链管理的优化。
通过与上下游供应链的数据共享和实时通信,智能产线控制系统可以帮助企业实现对供应链中各个环节的实时监控和调度。
例如,在食品生产过程中,智能产线控制系统可以根据销售数据自动调整生产计划和原材料采购计划,从而降低库存成本和生产风险。
二、智能产线控制系统的优势1. 提高生产效率智能产线控制系统能够实现生产过程的自动化和优化,提高了生产效率。
通过自动监测和调整生产参数,智能产线控制系统能够减少人工干预,提高生产的精度和速度。
例如,在饮料生产过程中,智能产线控制系统可以自动完成瓶装、封口和包装等工序,大大减少了人工操作的时间和成本。
食品加工生鲜生产线设计方案

食品加工生鲜生产线设计方案一、引言食品加工生鲜生产线是指在食品加工过程中,对生鲜食材进行连续的加工、分拣、包装等作业的自动化设备。
它的设计方案直接影响着生产效率、产品质量以及生产成本。
因此,合理的设计方案对于企业的发展至关重要。
二、生产线设计原则1. 适应性原则:根据不同的生鲜食材特性和加工要求,设计出适应性强、可调整的生产线,以满足不同产品的加工需求。
2. 效率原则:通过优化工序、合理布局设备、减少人工操作等方式,提高生产效率,降低生产成本。
3. 卫生安全原则:生鲜食材加工需要符合卫生标准,因此生产线设计应考虑设备的易清洁性、防止交叉污染等要素。
4. 灵活性原则:生产线应具备一定的灵活性,能够适应市场需求的变化,快速调整生产线的产能和产品种类。
三、生产线设计步骤1. 前期准备工作:确定生产线的规模、产品种类、生产能力等基本信息,并进行市场调研,了解市场需求和竞争情况。
2. 工艺流程设计:根据产品的加工要求,确定生产线的工艺流程,并考虑到原材料的处理、加工、包装等环节。
3. 设备选型:根据工艺流程和生产能力需求,选择适合的设备,并考虑设备的性能、技术指标、售后服务等因素。
4. 布局设计:根据生产线的工艺流程和生产能力,合理布置设备的位置,考虑到人员流动、物料输送等因素。
5. 控制系统设计:根据生产线的自动化程度,设计合理的控制系统,实现自动化控制和生产数据的采集与分析。
6. 安全环保设计:考虑生产过程中的安全和环保问题,设计合理的防护措施和废弃物处理方案。
7. 维护保养计划:制定合理的设备维护保养计划,确保设备的正常运行和寿命。
8. 成本控制:根据生产线设计方案,对设备投资、人工成本、能源消耗等进行成本控制,确保生产线的经济效益。
四、生产线设计案例以肉类加工生产线为例,该生产线包括肉类分割、去骨、腌制、熟化等工序。
在工艺流程设计时,根据不同产品的要求,确定了不同的工艺参数和操作流程。
在设备选型上,选择了适合不同工序的切割机、去骨机、腌制机、熟化机等设备,并考虑了设备的加工能力和卫生要求。
PLC在食品加工行业的应用案例分析

PLC在食品加工行业的应用案例分析在食品加工行业中,自动化技术的应用已经成为提高生产效率和产品质量的重要手段。
其中,可编程逻辑控制器(PLC)作为一种广泛应用的自动化控制设备,发挥着重要作用。
本文将通过分析几个食品加工行业中PLC应用的案例,来探讨PLC在这一领域中的应用价值。
案例一:饼干生产线某食品加工厂为了提高饼干生产线的自动化程度和生产效率,引入了PLC技术。
通过PLC,生产线上的各个工序可以实现自动控制和调节。
例如,根据饼干的不同口味和尺寸,PLC可以精确控制搅拌机的搅拌时间和速度,保证面糊的均匀性。
同时,PLC还可以根据生产计划自动调节烤箱的温度和时间,确保饼干的烘烤质量和口感。
通过PLC的应用,饼干生产线的自动化程度得到了大幅提升,生产效率也得到了明显的提高。
案例二:果汁灌装机一家果汁生产企业在灌装过程中引入了PLC控制系统。
PLC通过传感器实时检测果汁的流量和温度,根据设定的参数进行控制。
如此一来,可以精确控制每瓶果汁的灌装量,确保产品质量的一致性。
而且,当检测到异常情况时,PLC可以及时发出报警信号,以便操作人员采取措施。
通过PLC的引入,果汁生产企业实现了灌装工序的自动化和智能化,提高了生产效率和产品质量。
案例三:奶酪生产设备一家奶制品加工厂将PLC应用于奶酪生产过程中的一台发酵机。
通过PLC的控制,可以实时监控发酵机内的温度、湿度等参数,并根据预设的发酵曲线自动调节发酵过程中的温度和湿度。
这样一来,不仅能够保证奶酪发酵的质量和稳定性,还能够减少操作人员的工作量和人为错误的发生。
通过PLC的应用,奶制品加工厂提高了奶酪生产的自动化程度,同时也确保了产品质量和生产效率。
综上所述,PLC在食品加工行业的应用具有重要的意义。
通过PLC 的引入,食品加工企业可以实现生产线的自动化控制和优化,提高生产效率和产品质量。
随着自动化技术的不断发展,相信PLC在食品加工行业中的应用将不断扩大,并为行业带来更多的效益和价值。
DCS系统在食品加工中的应用案例

DCS系统在食品加工中的应用案例随着科技的不断发展,自动化控制系统在各个领域的应用越来越广泛。
在食品加工行业中,DCS(分散控制系统)的应用已经成为提高生产效率、降低成本、保证产品质量的重要工具。
本文将以几个具体的案例来说明DCS系统在食品加工中的应用。
案例一:面包烘焙工厂在面包烘焙工厂中,面团的制作是一个关键环节。
传统上,面团的制作过程需要大量的人工操作,容易出现工艺上的差异,同时也存在着一定的安全风险。
而引入DCS系统后,各个生产环节可以实现自动化控制,从原料投料、面团搅拌到面团发酵,都可以通过DCS系统进行监控和调整。
同时,系统还可以根据不同的面团种类和配方进行调整,保证产品质量的一致性和稳定性。
案例二:乳品生产线乳品生产线是一个高度复杂、多环节的过程,需要严格控制各个参数,以确保产品的安全和质量。
传统的控制方式往往依赖于独立的控制设备,操作不方便且容易出现数据不一致的问题。
而通过DCS系统,可以将各个环节的参数集中监控和调整,实现数据的一致性和及时性。
例如,牛奶的原料进料温度、杀菌温度、冷却温度等参数可以通过DCS系统进行自动控制,大大提高了生产效率和产品质量。
案例三:饼干生产工厂在饼干生产工厂中,通过DCS系统实现对生产过程的全面控制可以极大地提升生产效率和产品质量。
通过DCS系统,可以实时监控饼干生产线上各个环节的温度、湿度、速度等参数,并进行自动调整。
此外,通过DCS系统还可以实现多种饼干口味和规格的切换,仅需要简单的操作就可以完成整个生产线的调整,大大提高了生产线的灵活性和生产能力。
综上所述,DCS系统在食品加工中的应用具有重要的意义。
通过自动化控制,可以提高生产效率、降低成本、保证产品质量,帮助企业提升竞争力。
随着技术的不断进步,DCS系统在食品加工中的应用将越来越广泛,为食品行业的发展带来更多的机遇和挑战。
PLC在食品加工行业中的自动化控制案例

PLC在食品加工行业中的自动化控制案例自动化控制在食品加工行业中起着至关重要的作用。
随着科技的不断进步,PLC(可编程逻辑控制器)作为一种先进的控制设备,被广泛应用于食品加工过程中。
本文将以PLC在食品加工行业中的自动化控制案例为例,详细介绍其应用和优势。
一、案例背景某食品加工厂为了提高生产效率和质量,决定引入PLC自动化控制系统来替代传统的人工操作。
他们的主要目标是实现精确的控制和调节,并确保生产过程中的安全性和稳定性。
二、PLC在食品加工行业中的应用1. 原料配料控制在食品加工中,原料的配料过程是一个关键环节。
传统的人工操作容易导致误差和浪费。
而PLC可以通过精确的控制和计量系统,自动完成原料的配料过程,减少误差,并提高配料的准确性。
2. 温度控制食品加工中的温度控制对于产品的质量至关重要。
传统的温度控制往往需要人工监测和调节,容易受到人为因素的影响。
而PLC可以通过传感器实时监测温度,并自动调节加热或冷却设备,保持恒定的温度,从而提高生产效率和产品质量。
3. 流程控制食品加工涉及多个工序和流程,而传统的人工操作容易出现疏忽和误操作。
PLC可以通过编程来控制不同工序的顺序和时间,并确保每个流程的准确执行。
同时,PLC还具备报警功能,可以及时发现和处理异常情况,保证生产的连续性和稳定性。
三、PLC在食品加工行业中的优势1. 灵活性和可编程性PLC具有良好的灵活性和可编程性,可以根据不同的需求和工艺进行定制和调整。
食品加工行业的工艺和需求常常会变化,PLC可以快速适应这些变化,并进行相应的调整和优化。
2. 可靠性和稳定性PLC作为一种专门设计用于控制和监控的设备,具有良好的可靠性和稳定性。
它不受环境和人为因素的干扰,可以长时间稳定运行,有效地保证了生产过程的连续性和稳定性。
3. 效率和精确性PLC可以实现高速、精确的控制和调节。
通过传感器的实时监测和PLC的快速响应,可以准确地控制温度、压力、流量等参数,提高生产效率和产品质量。
食品工厂自动化的设计

食品工厂 自动化 的设计
李百秋 ( 麦肯食 品( 哈 尔滨 ) 有限公司 , 黑龙江 哈 尔滨 1 5 0 0 6 0 )
摘 要: 随着我 国经济和科技的快速发展 , 人 们的生活水平不断提 高 , 对于 日常生活的质量要求也不断提 高。 作 为最为基本的食 品加 工业迎来 了新 的发展 高潮 , 现代人们大量的需求给 予他们足 够的发展机会 , 但 是竞争压 力也十 分 巨大 , 又加 上人 们对于食 品质量 的要 求
关键词 : 食品工厂 ; 自动化 ; 设计
食 品加工行业还有一个特点就是 , 再生 产的过程中需要运算 大 民以食为天 ,因此食 品加工业 的发展对于人们来说十分重要 , 它关 系到我们 的基本生活质量 了。随着我 国经济 的迅速崛起 , 越来 量 的数据 , 监测并加以管理 , 从而实现企业的食品的安全 , 例 如某个 0 0 — 1 1 0之 间,这就 需要我们 进行细致 的观 越多 的人们开始追求生 活的质量 ,对于食 品质量 的要求也不断 提 食 品的加 工温度应在 1 高, 这无疑给食品加工业带来 了挑战 。一些食 品加工业 由于没有很 察 。 以往的人工操作总会出现各种各样 的问题。 但是智能化系统的 好的接受住挑战 , 最终被不断进步 的社会所淘汰。那么究竟怎么才 实现, 使得这种工作变得异常简单。 通过计算机进行数学建模 , 然后 使加 工简化且 准确 , 在有外界干扰和操 能接受住挑 战呢? 传统的食品加工工艺 已经不能满 足现代人们的需 实现 自动控制系统正确判 断,
不断提 高, 使得机遇与挑战并存 。传统 的食品加工工艺已经不能满足现代人们对 于食品工业的需求了, 因此 , 一个食品加工企业要 想快速 的发展起 来就必须引进 先进 的食品加工工艺, 让食 品工厂实现 自动化 , 从而满足现代人们的需求。本文将 具体 分析 一下食 品工厂 自动 化
DCS系统在食品加工过程中的自动化控制

DCS系统在食品加工过程中的自动化控制随着科技和工业的发展,自动化控制系统在各个领域中发挥着越来越重要的作用。
特别是在食品加工行业中,自动化控制系统的应用已经成为提高生产效率和质量的关键因素。
其中,DCS(分散控制系统)在食品加工过程中的应用尤为突出。
本文将探讨DCS系统在食品加工过程中的自动化控制。
一、DCS系统简介DCS系统是一种将数据采集、控制运算和数据处理完全集成在一起的自动化控制系统。
它可以通过分布在不同位置的控制单元进行数据采集和处理,并通过集中控制终端进行监控和操作。
相比传统的PLC (可编程逻辑控制器)系统,DCS系统具有更高的可扩展性和灵活性。
二、DCS系统在食品加工过程中的应用1. 原料处理在食品加工的最初阶段,原料处理是一个至关重要的环节。
DCS系统可以实现对原料配料、贮存和供给的自动化控制。
通过提前设置好的配方和参数,DCS系统可以准确地控制原料的供给量和混合比例,保证产品质量的稳定性。
2. 生产过程控制DCS系统还可以实现食品加工过程中的各个环节的自动化控制。
比如,温度、压力、流量、pH值等参数的监测和调节。
通过传感器和执行器的实时反馈,DCS系统可以自动调节生产过程中的各种参数,确保产品的生产过程符合标准要求。
3. 质量监控食品加工行业对产品质量的要求非常高。
DCS系统可以通过监测关键参数和采样分析,实时监控产品质量,并及时调整生产过程,以确保产品的一致性和稳定性。
同时,DCS系统还可以记录和保存生产过程中的各种数据,为产品质量的追溯提供依据。
4. 报警和故障处理DCS系统可以设定各种报警机制,当生产过程中出现异常情况时,自动发送告警信息给操作人员。
同时,DCS系统还可以对故障进行自动诊断和处理,并提供相应的解决方案。
这样可以大大提高故障处理的速度和效率,减少生产过程中的停工时间。
三、DCS系统的优势和挑战1. 优势(1)整合性:DCS系统可以集成多个子系统,实现全面的自动化控制。
- 1、下载文档前请自行甄别文档内容的完整性,平台不提供额外的编辑、内容补充、找答案等附加服务。
- 2、"仅部分预览"的文档,不可在线预览部分如存在完整性等问题,可反馈申请退款(可完整预览的文档不适用该条件!)。
- 3、如文档侵犯您的权益,请联系客服反馈,我们会尽快为您处理(人工客服工作时间:9:00-18:30)。
食品加工生产线自动化控制系统设计第一章:引言
随着工业自动化的不断深入发展,自动化控制系统已经在许多
领域得到广泛的应用。
食品加工生产线自动化控制系统是其中之一,其在提高生产效率、质量稳定性和安全性等方面具有很大的
优势。
该系统可以帮助企业节省大量的人力和物力成本,并且可
以降低生产过程中的风险和错误率。
本文就食品加工生产线自动
化控制系统设计进行探讨。
第二章:食品加工生产线自动化控制系统分类
食品加工生产线自动化控制系统大致可分为以下几类:
1. 前段生产自动化控制系统:自动完成蔬菜、肉类等食材的清洗、切块、研磨、混合等准备工作。
2. 食品加工自动化控制系统:用于完成烘焙、蒸煮、烧烤、炸制、冷却等加工工序,可以实现多种工艺配方,保证生产线的稳
定性和一致性。
3. 后段生产自动化控制系统:主要用于完成包装、称重、贴标、封口等工序,确保产品的质量卫生和生产的效率。
本文主要讨论第2种食品加工自动化控制系统的设计。
第三章:自动化控制系统的组成
食品加工自动化控制系统由以下几个部分组成:
1.电气控制系统:主要包括自动控制设备、电力配电系统和电
缆线缆等,其中,自动控制设备是核心,它能根据预设的程序和
信号,自动实现生产过程中的各项控制操作。
2. 控制装置:根据生产的流程和工艺要求,对生产过程中所涉
及的机械元件、传送带、输送带等进行自动控制,并可以对温度、压力、流量等重要参数进行采集和监控。
3. 传感器:主要负责采集压力、温度、重量、速度等生产关键
参数的信息,并将其传递给控制装置。
4. 执行机构:能够自动完成机械元件的启停、升降、输送带的
运转和成品包装等工艺要求,以实现生产线上的自动化生产。
5. 人机界面:主要是指触摸屏、显示屏、键盘等设备,它们负
责控制系统的显示、输入、操作和信息输出。
第四章:使用PLC进行自动化控制系统的设计
PLC(Programmable Logic Controller)是一种通用现场可编程
控制器。
主要用于自动化领域中的执行控制、序列控制、计时计数、数据处理等,广泛应用于各种工业控制系统中。
在食品加工
自动化控制系统中,PLC通常被用来进行控制。
常见的PLC包括模块化PLC和集成式PLC。
模块化PLC可以
根据需求进行组合,从而实现对控制系统的灵活配置;而集成式PLC则拥有更为紧凑的结构和更高的可靠性,可以为食品加工自
动化控制系统提供更为稳定和快捷的控制余地。
在食品加工自动化控制系统的设计中,PLC可以实现对温度和
湿度等环境参数的自动控制,使得生产过程中的各项参数能够始
终受到精确的监控和控制,并且PLC还可以实现对加工工艺的自
动调整和预警功能。
第五章:控制系统的安全性和可靠性设计
在自动化控制系统的设计中,安全性和可靠性都是非常重要的
考虑因素。
食品加工涉及到的是人们的健康和安全,因此在设计
中必须严格遵守相关法规和标准。
对于食品加工自动化控制系统中的机械设备、传感器等元件,
需要进行定期的检测和维护,以确保其正常运行和准确性。
此外,系统应具备足够的容错能力,即当发生故障时,能够快速地检测
和隔离问题,并避免引起更严重的后果。
同时,自动化控制系统
中应设置完善的应急措施,以保证生产过程中的安全性。
第六章:总结
食品加工自动化控制系统可以帮助企业提高生产效率、降低成
本和提高产品质量。
本文基于PLC技术,对食品加工自动化控制
系统的设计进行了详细的分析和探讨。
同时,在设计中,我们也
必须考虑安全性和可靠性等因素,以保证系统的稳定和运行效果。
随着自动化技术的不断发展,食品加工自动化控制系统在未来的
生产中将继续发挥越来越重要的作用。