炼铁技术发展
炼钢工艺发展的趋势
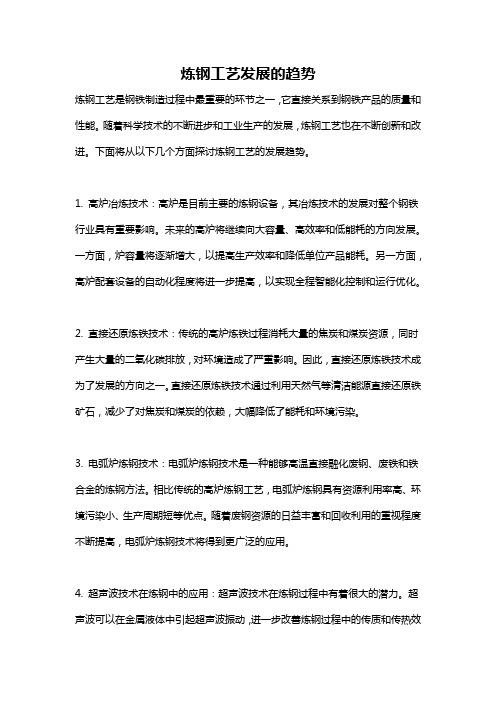
炼钢工艺发展的趋势炼钢工艺是钢铁制造过程中最重要的环节之一,它直接关系到钢铁产品的质量和性能。
随着科学技术的不断进步和工业生产的发展,炼钢工艺也在不断创新和改进。
下面将从以下几个方面探讨炼钢工艺的发展趋势。
1. 高炉冶炼技术:高炉是目前主要的炼钢设备,其冶炼技术的发展对整个钢铁行业具有重要影响。
未来的高炉将继续向大容量、高效率和低能耗的方向发展。
一方面,炉容量将逐渐增大,以提高生产效率和降低单位产品能耗。
另一方面,高炉配套设备的自动化程度将进一步提高,以实现全程智能化控制和运行优化。
2. 直接还原炼铁技术:传统的高炉炼铁过程消耗大量的焦炭和煤炭资源,同时产生大量的二氧化碳排放,对环境造成了严重影响。
因此,直接还原炼铁技术成为了发展的方向之一。
直接还原炼铁技术通过利用天然气等清洁能源直接还原铁矿石,减少了对焦炭和煤炭的依赖,大幅降低了能耗和环境污染。
3. 电弧炉炼钢技术:电弧炉炼钢技术是一种能够高温直接融化废钢、废铁和铁合金的炼钢方法。
相比传统的高炉炼钢工艺,电弧炉炼钢具有资源利用率高、环境污染小、生产周期短等优点。
随着废钢资源的日益丰富和回收利用的重视程度不断提高,电弧炉炼钢技术将得到更广泛的应用。
4. 超声波技术在炼钢中的应用:超声波技术在炼钢过程中有着很大的潜力。
超声波可以在金属液体中引起超声波振动,进一步改善炼钢过程中的传质和传热效果,提高钢的纯净度和均匀性。
此外,超声波还可以用于检测和监测钢铁产品中的缺陷和杂质,提高质量控制的准确性和效率。
5. 粉煤气化技术:粉煤气化技术是一种利用煤炭资源进行炼钢的新技术。
通过对煤炭进行气化,产生合成气,再利用合成气进行炼钢,既能够提高煤炭资源的利用率,又能够减少对传统能源的依赖和环境污染。
粉煤气化技术属于绿色环保型炼钢工艺,对于改善钢铁行业的能源结构和减少碳排放具有重要意义。
总体来说,炼钢工艺的发展趋势是朝着高效、环保、智能化和资源综合利用的方向发展。
国内外高炉炼铁技术的发展现状和趋势

国内外高炉炼铁技术的发展现状和趋势高炉炼铁技术是金属冶炼工业发展的基础,是保证金属铁质量和产量的关键技术,也是社会经济发展的重要依托。
近年来,随着金属冶炼工业的快速发展,国内外高炉炼铁技术的发展也取得了显著的成就,为保证金属铁质量、提高产量、提高经济效益发挥了重要作用。
首先,国内外高炉炼铁技术取得了重大突破,进一步提高了金属铁质量。
随着科学技术的进步,添加剂和冶炼工艺的改进,使高炉炼铁工艺取得重大进展,不仅能够有效提高铁素体组成,同时也能够改善铁水的流动性,有利于铁块的全面成型。
此外,利用新型炉料和改进的热处理技术,可以有效降低铁水的含氧量,提高铁液的液相容量,从而获得更高品质的铁。
其次,国内外高炉炼铁技术的发展,还大大提高了铁的产量。
传统的高炉炼铁工艺存在着大量的炉料损失,限制了铁的产量。
随着国内外高炉炼铁技术的发展,炉料损失大大减少,产量得到提高。
通过对炼铁工艺及其参数进行优化调整,获得合理的炉料计算和分配,进而有效提高铁的产量。
此外,结合智能技术、自动化技术和智能控制技术,还可以实现远程监控和智能化管理,可以使高炉炼铁效率更高,产量更大。
最后,国内外高炉炼铁技术的发展,对提高经济效益具有重要意义。
国内外高炉炼铁技术的发展,不仅缩短了铁的生产周期,提高了产量,而且可以减少能耗消耗和废气排放,降低了生产成本,有利于提高企业的竞争力,实现更高的经济效益。
此外,国内外高炉炼铁技术的发展还可以改善炼铁终端的工作环境,为炼铁行业的发展创造更加良好的条件。
以上是国内外高炉炼铁技术的发展现状和趋势的概述,未来的发展趋势可以简单地总结为以下几点:继续提高高炉炼铁质量和产量,推广智能技术,进一步优化炼铁工艺,合理设计炉料配比,提高炼铁效率,减少能耗和污染,改善炼铁环境,提高经济效益,实现绿色经济发展。
未来,相信国内外高炉炼铁技术将取得更好的发展,为我们社会的经济发展提供更多的依托。
世界冶铁技术发展史
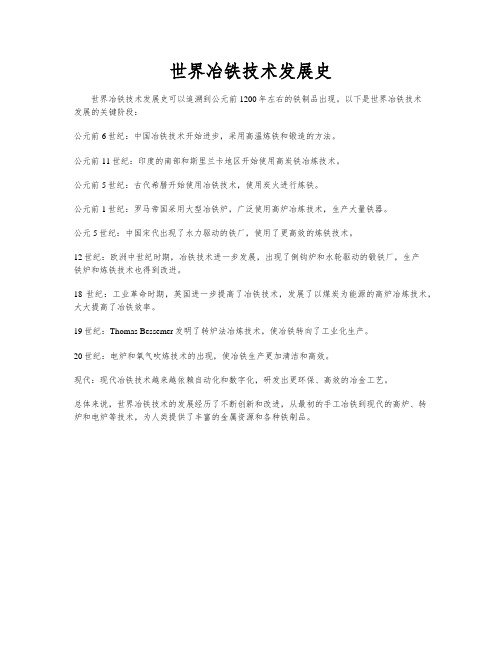
世界冶铁技术发展史
世界冶铁技术发展史可以追溯到公元前1200年左右的铁制品出现。
以下是世界冶铁技术
发展的关键阶段:
公元前6世纪:中国冶铁技术开始进步,采用高温炼铁和锻造的方法。
公元前11世纪:印度的南部和斯里兰卡地区开始使用高炭铁冶炼技术。
公元前5世纪:古代希腊开始使用冶铁技术,使用炭火进行炼铁。
公元前1世纪:罗马帝国采用大型冶铁炉,广泛使用高炉冶炼技术,生产大量铁器。
公元5世纪:中国宋代出现了水力驱动的铁厂,使用了更高效的炼铁技术。
12世纪:欧洲中世纪时期,冶铁技术进一步发展,出现了倒钩炉和水轮驱动的锻铁厂,生产
铁炉和炼铁技术也得到改进。
18世纪:工业革命时期,英国进一步提高了冶铁技术,发展了以煤炭为能源的高炉冶炼技术,大大提高了冶铁效率。
19世纪:Thomas Bessemer发明了转炉法冶炼技术,使冶铁转向了工业化生产。
20世纪:电炉和氧气吹炼技术的出现,使冶铁生产更加清洁和高效。
现代:现代冶铁技术越来越依赖自动化和数字化,研发出更环保、高效的冶金工艺。
总体来说,世界冶铁技术的发展经历了不断创新和改进,从最初的手工冶铁到现代的高炉、转炉和电炉等技术,为人类提供了丰富的金属资源和各种铁制品。
炼铁工艺的发展与创新从传统到现代

炼铁工艺的发展与创新从传统到现代炼铁工艺是铁矿石经过一系列工艺流程,将其转化为钢铁的过程。
随着科学技术的不断进步与发展,炼铁工艺也在不断创新和改进。
本文将从传统到现代的角度,探讨炼铁工艺的发展与创新。
一、传统炼铁工艺的演进传统炼铁工艺主要包括高炉法和直接还原法两种。
高炉法是将铁矿石、焦炭和石灰石等原料放入高炉中,在高温下进行还原反应,产生炼铁渣和铁水。
而直接还原法则是将铁矿石与还原剂(如氢气、甲烷等)直接反应,得到铁水。
然而,传统炼铁工艺存在一些问题。
首先,高炉法需要大量使用焦炭作为还原剂,导致能源消耗和环境污染问题。
其次,直接还原法虽然能够节约部分能源,但其还原效率较低,产出的铁水品质也不稳定。
二、基于传统的工艺改进为了解决传统炼铁工艺存在的问题,研究人员开始进行基于传统的工艺改进。
其中一个重要的改进是炼铁炉的结构优化。
通过改变炉膛形状、燃烧方式等,提高炼铁的效率和品质。
此外,还通过添加助熔剂、改变添加时间等方式,进一步优化炼铁工艺。
除了结构改进,工艺改进还包括了炼铁原料的优化选择。
研究人员通过对不同铁矿石的分析和试验,选择更优质的原料,以提高炼铁产品的品质。
同时,也研究了不同焦炭种类和添加量对炼铁过程的影响,为提高炼铁效率和环保性做出了贡献。
三、现代炼铁工艺的创新随着新材料和新技术的不断涌现,现代炼铁工艺得到了进一步的创新。
其中一个重要的创新是氧化还原反应的电磁过程控制技术。
通过在炼铁炉中加入电磁线圈,对炼铁过程中的温度、浓度等参数进行准确控制,提高炼铁效率和产品品质。
另外,为了降低能源消耗和环境污染,现代炼铁工艺还采用了先进的喷射燃烧技术。
该技术通过将高温燃烧产生的废气进行再循环利用,提高炼铁过程中的能量利用率。
同时,还采用了新型炉衬材料和高效能耗炉墙结构,减少了炼铁过程中的热损失。
除了这些技术创新,现代炼铁工艺还注重炼铁过程的数据采集与分析。
通过对炼铁过程中各个参数进行监测和分析,研究人员能够更好地控制和优化炼铁工艺。
高炉炼铁产业发展趋势

高炉炼铁产业发展趋势高炉炼铁产业发展趋势近年来,随着中国经济的快速发展,高炉炼铁产业也得到了蓬勃的发展。
高炉炼铁是指通过高温将铁矿石还原为金属铁的一种工艺。
作为炼铁产业的核心环节,高炉炼铁在我国的工业生产中具有重要地位。
本文旨在对高炉炼铁产业的发展趋势进行探讨和分析,以期为该行业的发展提供参考。
一、发展历程与现状高炉炼铁技术起源于20世纪初,经过百年的发展,已成为当今炼铁产业的主流工艺。
在我国,高炉炼铁产业经历了起步阶段、扩张阶段和优化阶段三个发展阶段。
起步阶段(20世纪初至20世纪60年代):我国高炉炼铁产业在本阶段逐步建立起炼铁技术体系和生产基地。
20世纪初,我国开始引进和消化吸收国外的高炉炼铁技术。
到20世纪50年代,我国已具备自主研发高炉炼铁技术的能力,并开始大规模建设高炉。
到20世纪60年代,我国高炉炼铁产能稳步增长,但存在一些技术问题和设备落后的情况。
扩张阶段(20世纪70年代至21世纪初):我国高炉炼铁产业在本阶段实现了快速发展。
70年代初,我国高炉炼铁产能再次扩大,技术水平也有了一定的提高。
80年代初,我国高炉炼铁产能突破5000万吨,成为世界第一大炼铁国。
90年代至21世纪初,我国高炉炼铁产能进一步提升,技术水平逐步接近国际先进水平。
优化阶段(21世纪至今):我国高炉炼铁产业在本阶段实施了一系列的技术创新和产业升级。
21世纪初,我国高炉炼铁产量再次出现大幅增长,技术水平和设备质量也有了明显提高。
在优化阶段,我国高炉炼铁产业始终围绕提高效能、降低能耗、减少环境污染等方面进行升级改造。
现在,我国高炉炼铁技术已基本达到国际先进水平,生产效益和环保水平也有了明显提高。
二、发展趋势与问题1. 产量稳步增长:随着国内经济的持续发展和钢铁需求的增加,我国高炉炼铁产业的总体产能仍然保持稳步增长的态势。
根据统计数据,我国高炉炼铁产量在过去十年中基本保持在4亿吨以上。
未来,我国高炉炼铁产量仍有望继续增长,但增速可能会逐渐放缓。
钢铁冶炼技术的发展和改进
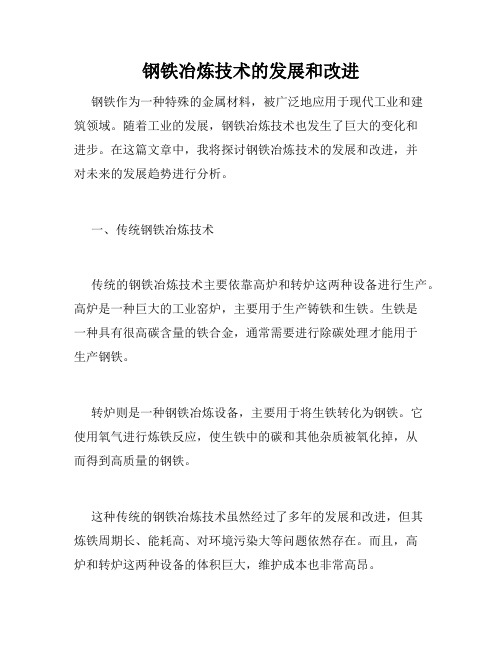
钢铁冶炼技术的发展和改进钢铁作为一种特殊的金属材料,被广泛地应用于现代工业和建筑领域。
随着工业的发展,钢铁冶炼技术也发生了巨大的变化和进步。
在这篇文章中,我将探讨钢铁冶炼技术的发展和改进,并对未来的发展趋势进行分析。
一、传统钢铁冶炼技术传统的钢铁冶炼技术主要依靠高炉和转炉这两种设备进行生产。
高炉是一种巨大的工业窑炉,主要用于生产铸铁和生铁。
生铁是一种具有很高碳含量的铁合金,通常需要进行除碳处理才能用于生产钢铁。
转炉则是一种钢铁冶炼设备,主要用于将生铁转化为钢铁。
它使用氧气进行炼铁反应,使生铁中的碳和其他杂质被氧化掉,从而得到高质量的钢铁。
这种传统的钢铁冶炼技术虽然经过了多年的发展和改进,但其炼铁周期长、能耗高、对环境污染大等问题依然存在。
而且,高炉和转炉这两种设备的体积巨大,维护成本也非常高昂。
二、新型钢铁冶炼技术近年来,随着科技的不断发展,新型钢铁冶炼技术也逐渐崭露头角。
其中,最值得关注的是电弧炉、氧气底吹炉和直接还原炉这三种设备。
1. 电弧炉电弧炉是一种基于电弧效应而产生高温的冶炼设备。
它采用电流通过两个电极之间的气体或其他介质,从而产生电弧,在电弧的高温下将铁矿石和废钢铁材等冶炼原料进行融化,最终生产钢铁。
与传统的高炉和转炉相比,电弧炉具有炼铁周期短、能耗低、污染少、生产效率高等优点。
此外,电弧炉还可以利用废钢铁材进行再利用,节约能源和降低成本。
2. 氧气底吹炉氧气底吹炉利用氧气将生铁中的碳和杂质物进行氧化,实现对生铁进行脱碳和加碳的过程,从而得到高质量的钢铁。
相比传统的转炉,氧气底吹炉具有能耗低、生产效率高、操作简便等优点。
3. 直接还原炉直接还原炉是一种钢铁冶炼设备,可以直接利用铁矿石进行冶炼。
它利用还原剂将铁矿石还原为铁,在不经过转炉等其他设备的情况下生产出高质量的钢铁。
这三种新型的钢铁冶炼设备,都具有能耗低、环境污染小、生产效率高等优点。
它们的使用,将进一步降低钢铁冶炼过程中的成本和能源消耗,也将对环境保护产生积极的影响。
炼铁厂技术人员的职业发展路径与前景展望

炼铁厂技术人员的职业发展路径与前景展望【前言】炼铁厂技术人员,作为重要的行业人才,其职业发展路径和前景一直备受关注。
今天,我们就来探讨一下炼铁厂技术人员的职业发展道路和未来前景展望。
【职业发展路径】炼铁厂技术人员是炼铁生产中不可或缺的一环,从事的主要工作是铁矿石的选矿、配料、炼制等,在整个生产过程中扮演着重要的角色。
对于炼铁厂技术人员而言,职业发展路径主要由以下几个方面构成。
【技能提升】对于炼铁厂技术人员而言,不断提升自己的专业技能是非常重要的。
新技术的出现使得炼铁生产不断地向智能化、自动化、数字化等方向发展,这就需要技术人员不断地学习新技术、研究新工艺,掌握先进的生产技能和实践经验。
只有在技能上不断提升,才能逐步晋升到高级岗位,并得到更高的薪资待遇。
【职业晋升】对于炼铁厂技术人员而言,职业晋升是必经之路。
在炼铁生产中,技术人员的职业晋升主要分为三个层次:技术工、技术员、高级技术员。
技术工是炼铁生产的基础工人,主要承担炼铁生产中一些基础的工作任务;技术员则需要具有一定的技术能力,能够对生产中出现的问题进行处理和解决;高级技术员需要具有较高的专业技能和领导能力,能够在炼铁生产中承担更重要的任务工作。
【管理岗位】对于一些炼铁厂技术人员而言,他们可以向管理岗位转型。
在炼铁生产中,除了技术人员外,还需要有管理人员来进行统筹协调、调度运作等工作。
如果技术人员在工作中积累了丰富的实践经验,并且具有较高的领导能力,那么他们就可以向管理岗位方向发展。
例如担任炼铁厂的生产主管、工长等职位,领导团队进行生产运作和管理。
【前景展望】虽然随着时间的推移,炼铁厂技术人员的职业路径会有所变化,但未来的发展前景仍然非常可观。
在“十四五”期间,钢铁产业迎来了高质量发展的重要阶段,国家也将进一步加大职业教育培训力度,提高员工的技能水平,从而推动炼铁厂技术人员职业发展方向呈现出以下几点趋势。
【朝智能化方向发展】炼铁厂技术人员将会在智能化方面得到更多的发展机会。
我国炼铁生产的发展历程

我国炼铁生产的发展历程自古以来,铁器一直是人类生活中不可或缺的重要工具。
作为重要的原材料,铁在我国的生产历程经历了漫长而丰富的发展历程。
本文将从古代冶铁技术的起源开始,一直追溯到我国现代炼铁工业的发展,带您了解我国炼铁生产的发展历程。
古代冶铁技术的起源可以追溯到公元前2000年左右的商代。
商代时期,我国的冶铁技术已经相对成熟,采用的主要方法是“出铁法”。
这种方法是通过烧炼铁矿石,将铁矿石中的铁与杂质分离,得到铁。
当时的炼铁技术主要使用木炭作为燃料,因此炼铁的规模有限,产量相对较低。
随着时间的推移,炼铁技术逐渐得到改进。
到了西汉时期,我国的冶铁技术已经取得了重要的突破,采用的方法是“高炉法”。
这种方法通过将铁矿石与石灰石和木炭一起放入高炉中进行炼制,得到高纯度的铁。
高炉法的采用使得炼铁的规模大大扩大,生产效率也大幅提高。
这一技术的出现,标志着我国冶铁技术进入了一个新的阶段。
在隋唐时期,我国的炼铁技术继续发展。
唐代的炼铁工艺以“风炉法”为主,这是一种采用风力增强燃烧的炼铁方法。
这种方法的使用,使得炼铁的产量再次大幅提高,炼铁工业进入了一个繁荣时期。
唐代的炼铁技术对于后来的炼铁工业的发展产生了深远的影响。
到了宋代,我国的炼铁技术再次得到改进和创新。
宋代的炼铁工艺主要采用“炼炉法”,这种方法通过将铁矿石和石炭一起烧炼,得到高质量的铁。
炼炉法的使用,使得炼铁的质量得到了极大的提升,炼铁产量也大幅度增加。
宋代的炼铁工业不仅为当时的国家经济发展做出了巨大贡献,同时也为后来的炼铁工业提供了宝贵的经验。
到了现代,我国的炼铁工业经历了一系列的发展和变革。
特别是改革开放以来,我国炼铁工业经历了迅猛的发展。
在20世纪80年代,我国开始引进国外先进的炼铁技术,如转炉炼铁技术和电炉炼铁技术。
这些新技术的引进使得我国的炼铁工业实现了跨越式发展,炼铁产量大幅度增加。
同时,我国还加大了炼铁工业的投资,提高了炼铁设备的自动化程度,不断提升炼铁的生产效率。
- 1、下载文档前请自行甄别文档内容的完整性,平台不提供额外的编辑、内容补充、找答案等附加服务。
- 2、"仅部分预览"的文档,不可在线预览部分如存在完整性等问题,可反馈申请退款(可完整预览的文档不适用该条件!)。
- 3、如文档侵犯您的权益,请联系客服反馈,我们会尽快为您处理(人工客服工作时间:9:00-18:30)。
**炼铁发展综述摘要:**公司自2005年以来,推行稳本固基、苦练内功、转变思维、审时度势,随机应变等一系列管理理念,以提高高炉装备水平为保障,通过狠抓“精料”工作、积极探索炼铁新技术、开创性的发展炼铁新理论,以及计算机辅助管理,使炼铁生产获得了高水平发展,高炉主要技术经济指标显著改善。
关键词:炼铁管理理念技术进步精整炉料高炉装备高炉操作制度The Development of Iron-making of**SteelAbstract: Since 2005, the implementation of ** Steel iron company is stabilization of the solid base, Obtain, change thinking,, deal with the situation and act according to circumstances and a series of management concepts in order to improve the level of equipment for the protection of blast furnace, by implementing the "concentrate materials " work , and actively explore new iron-making technology, pioneering the development of new iron-making theory, as well as computer-aided management, which makes it reach a high level development of iron production , main technical and economic indicators of blast furnace improve significantly.Key words:iron-making,management concepts,technological improvement,finishing furnace, blast furnace equipment ,blast furnace operating system近几年,**炼铁的快速发展,引起了业界同行的关注,特别是08年金融危机来临后,**炼铁凭借其铁前低成本优势,使得**钢铁能率先走出困境,成为行业的少有赢利企业,短短几年里,高炉经济技术指标由同行垫底走向处于领先水平见表一,条件并不优越的青钢炼铁,是凭借什么力量崛起的,**炼铁的核心竞争力是什么?回顾**炼铁的发展史,特别是2005年以来的历程,一条明确的主线贯穿于炼铁生产管理的始终,它就是“创造性思维,突破性进展”,这条主线正是青钢炼铁快速发展的核心竞争力。
四年来,围绕强化冶炼、节能降耗不间断地进行了“精料、高风温、均衡生产”等适应性技术改造和管理创新工作,整体工作的有效、有序、有度、协调组织,提升了炼铁在同行中的竞争能力,实现了快速、健康、持久的发展。
表一**炼铁高炉主要技术经济指标年份利用系数焦比/kg 煤比入炉品位热风温度休风率工序能耗t.m-3.d-1 kg.t-1 kg.t-1% ℃% kg/t2001 3.06 509 0 59.38 1018 0.82 463.97 2002 2.91 533 0 60.25 995 1.58 479.44 2003 3.44 543 0 59.86 915 1.91 511.05 2004 3.52 540 41 60.09 895 1.97 519.33 2005 3.50 458 96 59.36 969 1.34 524.11 2006 3.60 396 126 58.75 1058 1.24 451.57 2007 3.57 393 133 58.26 1095 1.06 448.8 2008 3.52 404 123 58.34 1074 2.71 446.61 2009(1-10) 3.51 341 156 57.22 1117 2.24 421.22一:高炉炉料结构优化:精整炉料“料”是高炉生产之本,在当今生产中,炉料即要满足高炉稳定生产的需要更要满足企业低成本高效益的需要。
“精料”的概念也因此发生了变化,以往“精料”的概念是全熟料、高品位、粒度均匀干净,目前的“精料”以笔者认为是通过一定的手段使高炉的炉料更适合现代工业生产的要求,也就出现了我们近期常常听到的“粗粮细做、综合炉料优化”等词语。
**炼铁首先抓住强化冶炼的关键——精整炉料,进行了长时间艰苦的摸索,通过不断的优化和改善炉料结构,实现了生产指标的一步步提高。
从最早的土烧到高碱度烧结矿生产,从烧结生熔剂到目前的全熟熔剂,从高碱度烧结矿配加球团的豪华炉料到高碱度烧结矿配加30%的块矿的经济性炉料等等,每走一步,都能因时而异在当时条件下做到冶炼稳定性、产量、成本的最佳搭配,从而使得企业经济效益最高。
1、占高炉整体炉料体积40%多的高碱度烧结矿的生产实践:由于烧结矿碱度的提高,矿物组成发生了变化,铁酸钙含量明显增加,铁酸钙还原性能好,强度高,而且大量的铁酸钙存在,可以防止β-2CaO·SiO2在冷却时产生粉化现象,随着碱度的提高,总黏结相升高,软化开始温度和软化终了温度降低,还原度增加,炉内所承受的压差提高,管道形成、风压冒尖等炉况现象得以杜绝,是保证高炉适应其他外界变化的基础,因此**自始至终保持烧结矿碱度1.9以上,不惜以每吨铁加30kg的硅石来平衡碱度。
2、占高炉整体炉料体积45%的入炉焦炭控制:随着焦炭的骨架作用越来越重要,焦炭的强度和入炉粉末的控制形同烧结矿一样。
焦炭的强度受市场和资源的影响,我们能够把控的只有入炉焦炭含粉和水份。
**高炉生产多年来深受焦炭水份波动大、焦炭粉末多的影响,尤其是在焦炭质量不好及下雨、雪天气情况下,而焦炭烘干技术的使得入炉焦炭含粉、水分完全得以控制。
为此我们于2008年至2009年上半年先后在1#—6#高炉槽下投入使用焦炭烘干工程,利用热风炉废气对料仓内的焦炭进行预烘干,不但使焦炭水份降低约5%,还能保持焦炭水份的稳定性,减少焦炭水份波动对炉况的不利影响,特别是雨季时效果更加明显,焦炭粉末降低3%以上,保证了高炉顺行。
3、“粗粮细做”:2007年为解决进口块矿粉末逐渐增多问题,对入炉块矿全部实行预筛分,确保入炉块矿尤其雨天的含粉率<4%;同时实现各种炉料二次筛分,即在入高炉料仓之前进行一次预处理;再者加强槽下筛分管理,通过采用双层棒条自清理机烧筛代替原有的梳齿筛等设备改造,以及采用控制料流、及时清理筛面等措施降低入炉粉末,目前高炉入炉粉末基本控制在3%—4%左右。
4、调整炉料结构:以上三项是炼铁稳定生产和实现低成本战略的基础,在此基础上通过块矿的预筛分等措施保证了不同时期采取不同的炉料结构从而造就了炼铁成本的最优(成本的降低关键在结构,2008年下半年以后,受国际金融危机的影响,根据原料的性价比以经济效益最大化为切入点调整炉料结构,用价格较低的原料代替高价球团矿直至全部取消球团的炉料结构,大幅度提高块矿比例直至30%)。
近几年高炉炉料结构情况时间机烧矿,% 球团,% 块矿,%2006年70.66 18.36 10.982007年71.59 15.73 12.682008年73.72 12.52 13.762009年76.93 4.59 18.485、以煤代焦:已往的炼铁理论认为,在没有富氧的情况下,煤比达到150kg/t 是极限,然而,通过采取选择煤种控制煤成分及高炉理论燃烧温度、冶炼强度、造渣制度、热制度等措施煤比是可以实现170kg/t的,同时也是最为经济的。
二:操作工艺发展近年来,随着资源的匮乏和金融危机的影响,高炉炼铁理念也随着环境的变化发生了巨大的变化,从追求高强度冶炼转变为以经济效益为先,高炉操作制度、冷却制度、渣铁处理工艺、停开炉技术等日新月异。
一)操作制度的变化1、装料制度:由大矿批分装料制改为中小矿批分装料制从2006年开始逐步探索大矿批分装的规律。
在一定的条件下,扩大矿批有利于矿石均匀分布,有利于稳定上部气流,改善软熔带透气性。
分装有利于减少炉料分布中的界面效应,从而可以促进炉况的稳定顺行和焦比的降低。
大矿批分装装料制度已在全国许多高炉成功使用,并取得了良好的经济效益。
大矿批分装在**一段时期曾取得了良好的效果,但大矿批分装对原燃料条件变化的适应能力比较差。
自2008以来随着市场的变化,市场指导生产成为主流,<精料方针>定义发生本质变化,根据原燃料条件及高炉冶炼强度,**逐步摸索中小矿批分装在高炉上的应用,各项经济技术指标均有明显改善,尤其是随着生矿比例的增加,中小矿批分装更显示出其优越性,2009年,生矿配比已达到25%,而入炉综合焦比却下降到了490Kg/t以下,中小矿批分装在节能降耗中起到了重要作用。
2、热制度:以物理热为指导,低硅冶炼,并不定期将物理热提高到1500℃来活跃炉缸。
大量块矿进入高炉由于受到物料和气流的冲击以及铁矿石还原Fe2O3─Fe3O4─FeO过程发生晶形变化,导致块矿破裂粉碎。
大量的粉碎的块矿直接影响高炉内部气流分布和炉料的顺行,从而影响高炉冶炼的产量和质量。
图哈块爆裂实验结果(如上图,哈块试验过程中,当温度达到200℃时开始通入还原气体,流量是3L/min,哈块大约在650℃时在矿石表面出现裂纹,随着温度的升高,裂纹逐渐增大,裂纹数目逐渐增多,大约770℃时试验中矿石已经完全裂开。
)因此,合适的热制度是保证高比例块矿冶炼下稳定炉况的关键,炉缸必须有充足的热量,青钢的经验是保证铁水和炉渣的物理温度>1470℃,并且根据高炉的实际情况不定期的将物理温度提高到1500℃来活跃炉缸。
高炉树立低硅冶炼,平均硅为0.4-0.50%,硅偏差0.10-0.20%。
3、送风制度:全风温作业,风口长度以230-280-310mm为主流。
近年来随着钢铁产能过剩和钢铁市场的变化,高强度冶炼已不再是经济高效炼铁,控制好炉内煤气流速寻找合适的冶炼强度,低消耗的生产成为今后高炉生产的主流,在送风制度上,全风温作业成为铁定的原则,风口长度以230-280-310mm为主流,在鼓风动能上则选择合适的动能。
高炉顶压随装备TRT 以后,逐步提高,600m3 以下高炉压差要控制在115—135kpa之间是最佳的。
4、造渣制度:保证渣中的MgO/ Al2O3>0.65~0.7。