催化剂与工艺
石油炼制工艺及相关催化剂简介

石油炼制工艺及相关催化剂简介石油炼制工艺是将原油中的各类有机化合物分离、转化和加工,以生产出石油产品的过程。
在石油炼制工艺中,催化剂起着至关重要的作用,可以加速反应速率、降低反应温度和能量消耗,提高产品质量和产量。
石油炼制工艺主要包括以下几个步骤:1. 原油分离:原油经过蒸馏塔分离成不同沸点范围的馏分,如汽油、柴油、润滑油和残渣等。
2. 加氢:加氢是将重油经过加氢装置,使用氢气作为催化剂,去除硫、氮和重金属等杂质,同时减少饱和烃和芳香烃之间的不饱和度,提高产品质量。
3. 裂化:裂化技术是通过使用裂化催化剂将高碳烷烃分子打断为低碳烷烃分子,以获得更多的汽油和石化产品。
4. 重整:通过重整催化剂将低辛烷值的芳烃转化为高辛烷值的芳烃。
5. 脱蜡:脱蜡是通过脱蜡催化剂将柴油中的蜡质转化为液体烃,提高柴油的流动性。
6. 脱脂:脱脂是使用脱脂剂去除润滑油中的杂质,提高产品质量。
催化剂在石油炼制工艺中起着至关重要的作用。
常见的催化剂包括以下几种:1. 氢化催化剂:常见的氢化催化剂是采用铜、镍、钴等金属为活性组分,将有机硫、氮化合物和多环芳烃加氢,以去除杂质,净化油品。
2. 裂化催化剂:裂化催化剂通常由沸石和金属组成,能够有效打断高分子链,提高汽油产率。
3. 重整催化剂:重整催化剂一般采用铂、铑等贵金属作为活性组分,通过重排和氢化反应提高芳烃的辛烷值。
4. 脱蜡催化剂:脱蜡催化剂通常由沸石和金属组成,能够将柴油中的蜡质转化为液体烃,提高柴油的流动性。
催化剂是石油炼制过程中不可或缺的关键因素,可以提高产量、改善产品质量、节约能源等。
随着石油需求的不断增长和环境要求的提高,对高效、环保的催化剂研发和应用也提出了更高的要求。
石油炼制工艺及相关催化剂的发展石油炼制是现代工业的重要组成部分,随着全球石油需求的不断增长,石油炼制工艺及相关催化剂也在不断发展和创新。
近年来,石油炼制工艺和催化剂的研发重点主要集中在以下几个方面:1. 高效能源利用:随着能源问题的日益突出,石油炼制工艺对能源的高效利用提出了更高要求。
催化剂的作用与分类,如何制造催化剂
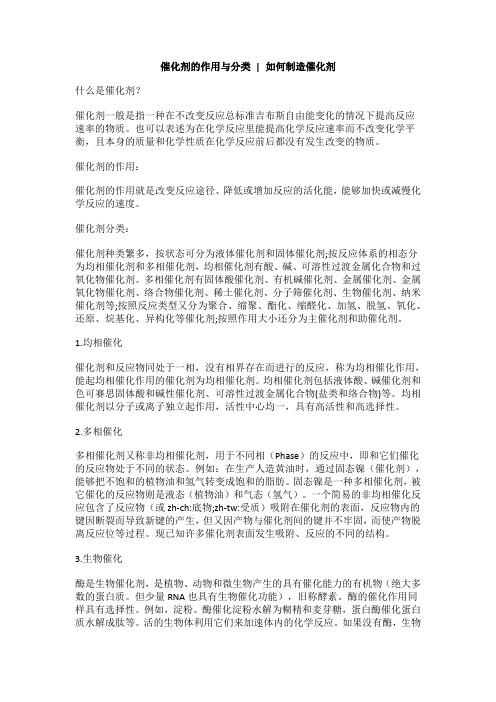
催化剂的作用与分类| 如何制造催化剂什么是催化剂?催化剂一般是指一种在不改变反应总标准吉布斯自由能变化的情况下提高反应速率的物质。
也可以表述为在化学反应里能提高化学反应速率而不改变化学平衡,且本身的质量和化学性质在化学反应前后都没有发生改变的物质。
催化剂的作用:催化剂的作用就是改变反应途径、降低或增加反应的活化能,能够加快或减慢化学反应的速度。
催化剂分类:催化剂种类繁多,按状态可分为液体催化剂和固体催化剂;按反应体系的相态分为均相催化剂和多相催化剂,均相催化剂有酸、碱、可溶性过渡金属化合物和过氧化物催化剂。
多相催化剂有固体酸催化剂、有机碱催化剂、金属催化剂、金属氧化物催化剂、络合物催化剂、稀土催化剂、分子筛催化剂、生物催化剂、纳米催化剂等;按照反应类型又分为聚合、缩聚、酯化、缩醛化、加氢、脱氢、氧化、还原、烷基化、异构化等催化剂;按照作用大小还分为主催化剂和助催化剂。
1.均相催化催化剂和反应物同处于一相,没有相界存在而进行的反应,称为均相催化作用,能起均相催化作用的催化剂为均相催化剂。
均相催化剂包括液体酸、碱催化剂和色可赛思固体酸和碱性催化剂、可溶性过渡金属化合物(盐类和络合物)等。
均相催化剂以分子或离子独立起作用,活性中心均一,具有高活性和高选择性。
2.多相催化多相催化剂又称非均相催化剂,用于不同相(Phase)的反应中,即和它们催化的反应物处于不同的状态。
例如:在生产人造黄油时,通过固态镍(催化剂),能够把不饱和的植物油和氢气转变成饱和的脂肪。
固态镍是一种多相催化剂,被它催化的反应物则是液态(植物油)和气态(氢气)。
一个简易的非均相催化反应包含了反应物(或zh-ch:底物;zh-tw:受质)吸附在催化剂的表面,反应物内的键因断裂而导致新键的产生,但又因产物与催化剂间的键并不牢固,而使产物脱离反应位等过程。
现已知许多催化剂表面发生吸附、反应的不同的结构。
3.生物催化酶是生物催化剂,是植物、动物和微生物产生的具有催化能力的有机物(绝大多数的蛋白质。
废催化剂回收利用提炼工艺有哪些

废催化剂回收利用提炼工艺有哪些废催化剂指的是在催化剂使用过程中变得无法再继续使用的残留物。
由于催化剂的高价值,从废催化剂中回收和利用其中的有用成分已成为一项重要的环保和资源节约措施。
废催化剂回收利用的提炼工艺主要包括以下几种:1. 焙烧方法焙烧法是一种常用的废催化剂回收利用工艺。
通过将废催化剂在高温下进行焙烧,将其中的有害物质和杂质烧除,得到高纯度的有用成分。
这种方法的优点是操作简单、成本较低,但同时也存在能耗高、排放污染物等问题。
2. 溶液浸取法溶液浸取法利用溶剂的选择性溶解性质,将废催化剂中的有用成分溶解出来。
常用的溶剂包括酸、碱和有机溶剂等。
通过对废催化剂的多次浸取和分离,可以逐步提取出目标成分。
这种方法的优点是选择性强、回收率高,但同时也需要处理大量的废液,对环境造成一定的影响。
3. 燃烧还原法燃烧还原法是一种通过高温气氛中的燃烧和还原反应,将废催化剂中的有害物质和杂质转化为无害物质,并回收利用有用成分的方法。
在高温还原气氛中,有害物质和杂质被还原为气体或金属等形式,而有用成分则以固体形式存在。
这种方法的优点是可回收高纯度的有用成分,但同时也需要高温和特殊的还原气氛条件。
4. 调整反应条件法调整反应条件法是一种通过改变反应条件来实现废催化剂回收利用的方法。
催化剂的活性往往与反应条件密切相关,通过调整反应温度、压力、气氛等条件,可以促使废催化剂中的有用成分重新表现出活性。
这种方法的优点是操作简单、成本低,但对于不同的废催化剂,需要找到最合适的反应条件。
5. 粉碎提取法粉碎提取法是一种通过机械碾磨废催化剂,再利用物理或化学方法提取有用成分的工艺。
通过细碎废催化剂,增加表面积,有利于后续的提取操作。
然后利用不同的提取剂、溶剂或分离技术,将有用成分从废催化剂中分离出来。
这种方法的优点是操作简便、废催化剂利用率较高,但对于废催化剂的破碎和提取过程会产生一定的能耗和环境污染。
6. 超声辅助提取法超声辅助提取法是一种利用超声波在液体中产生的空化效应,促进物质的溶解和扩散的技术。
催化剂生产工艺流程

催化剂生产工艺流程
催化剂的生产工艺流程可以分为以下几个步骤:
1. 原材料准备:选择合适的原材料,包括载体、活性组分和助剂等。
原材料需要进行粉碎、筛分等处理,以获得合适的颗粒大小和分布。
2. 原料混合:将粉末状的原材料进行混合。
通常采用干法或湿法混合,通过搅拌或混合设备将原材料均匀混合。
3. 模压成型:将混合好的原料进行成型。
通常采用压片或挤出成型等方法,以产生具有一定形状和大小的颗粒。
4. 烧结处理:将成型后的颗粒进行烧结处理。
通过加热到适当的温度和时间,使颗粒中的原料发生化学反应,形成结构稳定的固体催化剂。
5. 洗涤处理:烧结后的催化剂可能含有一定的杂质和未反应的原料。
通过洗涤处理,可以去除这些杂质,提高催化剂的纯度。
6. 干燥:洗涤后的催化剂需要进行干燥处理,去除水分并固化颗粒。
7. 表面处理:根据需要,可以对催化剂的表面进行一些处理,例如添加表面活性剂、改变颗粒形态等。
8. 包装和质检:将生产好的催化剂进行包装,以防止污染和损
坏。
同时进行质量检验,确保产品满足规定的品质标准。
以上是一般的催化剂生产工艺流程,实际生产中可能还涉及其他特殊步骤和处理,具体流程会根据产品的不同而有所变化。
催化剂制备工艺
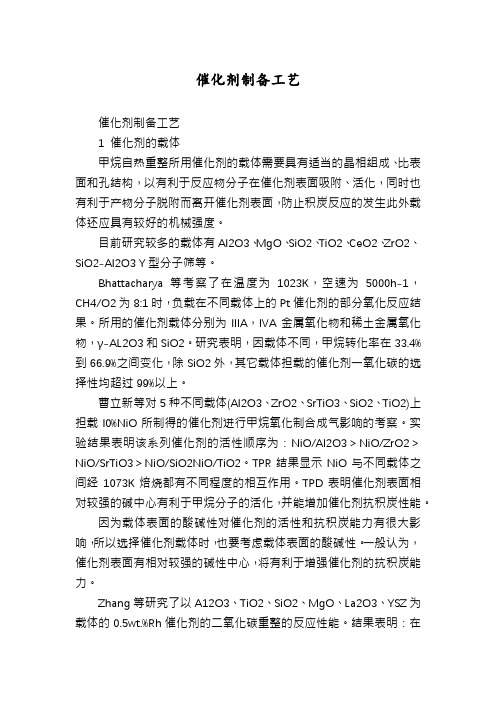
催化剂制备工艺催化剂制备工艺1 催化剂的载体甲烷自热重整所用催化剂的载体需要具有适当的晶相组成、比表面和孔结构,以有利于反应物分子在催化剂表面吸附、活化,同时也有利于产物分子脱附而离开催化剂表面,防止积炭反应的发生此外载体还应具有较好的机械强度。
目前研究较多的载体有Al2O3、MgO、SiO2、TiO2、CeO2、ZrO2、SiO2-Al2O3 Y型分子筛等。
Bhattacharya等考察了在温度为1023K,空速为5000h-1,CH4/O2为8:1时,负载在不同载体上的Pt催化剂的部分氧化反应结果。
所用的催化剂载体分别为IIIA,IVA金属氧化物和稀土金属氧化物,γ-AL2O3和SiO2。
研究表明,因载体不同,甲烷转化率在33.4%到66.9%之间变化,除SiO2外,其它载体担载的催化剂一氧化碳的选择性均超过99%以上。
曹立新等对5种不同载体(Al2O3、ZrO2、SrTiO3、SiO2、TiO2)上担载l0%NiO所制得的催化剂进行甲烷氧化制合成气影响的考察。
实验结果表明该系列催化剂的活性顺序为:NiO/Al2O3>NiO/ZrO2>NiO/SrTiO3>NiO/SiO2NiO/TiO2。
TPR结果显示NiO与不同载体之间经1073K焙烧都有不同程度的相互作用。
TPD表明催化剂表面相对较强的碱中心有利于甲烷分子的活化,并能增加催化剂抗积炭性能。
因为载体表面的酸碱性对催化剂的活性和抗积炭能力有很大影响,所以选择催化剂载体时,也要考虑载体表面的酸碱性。
一般认为,催化剂表面有相对较强的碱性中心,将有利于增强催化剂的抗积炭能力。
Zhang等研究了以A12O3、TiO2、SiO2、MgO、La2O3、YSZ为载体的0.5wt.%Rh催化剂的二氧化碳重整的反应性能。
结果表明:在923K,CH4/CO2=1.0的反应条件下,重整的初活性顺序是YSZAl2O3TiO2SiO2La2O3MgO。
在1023K,20%CH4,20%CO2,60%He 的反应条件下,在Rh/SiO2和Rh/YSZ上进行50h的重整反应,没有发现催化剂的失活。
丙烷脱氢制丙烯工艺流程设计与催化剂评价
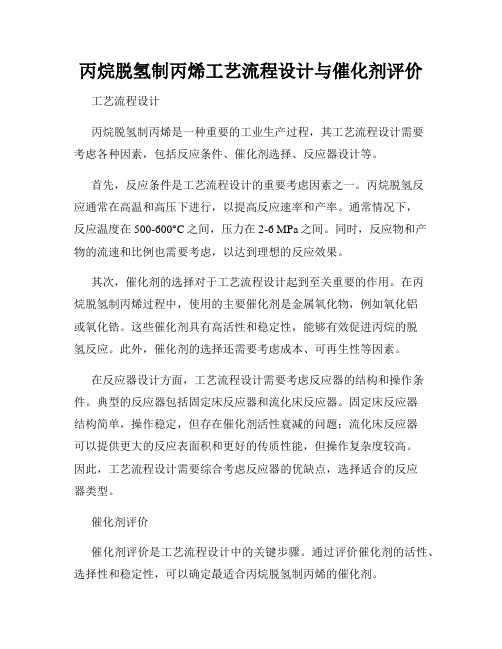
丙烷脱氢制丙烯工艺流程设计与催化剂评价工艺流程设计丙烷脱氢制丙烯是一种重要的工业生产过程,其工艺流程设计需要考虑各种因素,包括反应条件、催化剂选择、反应器设计等。
首先,反应条件是工艺流程设计的重要考虑因素之一。
丙烷脱氢反应通常在高温和高压下进行,以提高反应速率和产率。
通常情况下,反应温度在500-600°C之间,压力在2-6 MPa之间。
同时,反应物和产物的流速和比例也需要考虑,以达到理想的反应效果。
其次,催化剂的选择对于工艺流程设计起到至关重要的作用。
在丙烷脱氢制丙烯过程中,使用的主要催化剂是金属氧化物,例如氧化铝或氧化锆。
这些催化剂具有高活性和稳定性,能够有效促进丙烷的脱氢反应。
此外,催化剂的选择还需要考虑成本、可再生性等因素。
在反应器设计方面,工艺流程设计需要考虑反应器的结构和操作条件。
典型的反应器包括固定床反应器和流化床反应器。
固定床反应器结构简单,操作稳定,但存在催化剂活性衰减的问题;流化床反应器可以提供更大的反应表面积和更好的传质性能,但操作复杂度较高。
因此,工艺流程设计需要综合考虑反应器的优缺点,选择适合的反应器类型。
催化剂评价催化剂评价是工艺流程设计中的关键步骤。
通过评价催化剂的活性、选择性和稳定性,可以确定最适合丙烷脱氢制丙烯的催化剂。
催化剂的活性评价通常使用丙烷转化率和丙烯选择性来衡量。
丙烷转化率是指反应中丙烷转化为丙烯的比例,丙烯选择性是指生成丙烯的反应物摩尔比。
通过不同催化剂的活性评价,可以确定最适合丙烷脱氢的催化剂类型。
催化剂的稳定性评价是确定其使用寿命的关键因素。
长时间的反应会导致催化剂表面的积炭和活性衰减,从而降低丙烷转化率和丙烯选择性。
因此,在工艺流程设计中,需要评价催化剂的稳定性,并选择具有较长使用寿命的催化剂。
此外,催化剂的再生性也是评价的重要因素。
一些催化剂在反应过程中会逐渐失去活性,需要定期进行再生或更换。
通过评价催化剂的再生性,可以在工艺流程设计中考虑到催化剂维护和管理的成本。
催化剂培训材料培训课件PPT工业催化剂制备与使用

• 对沉淀剂选择有以下要求:
① 尽可能使用易分解并含易挥发成分的沉淀剂
– 常用的沉淀剂有:
• 碱类(NH4OH、NaOH、KOH) • 碳酸盐[(NH4)2CO4、Na2CO4、CO2] • 有机酸(乙酸、草酸)等 • 最常用的是NH4OH和(NH4)2CO4,因为铵盐在洗涤和热处
涤、干燥、粉碎和机 械成型,最后经500℃ 焙烧活化得到 γ-Al2O3。
– 该法生产设备简单、 原料易得且产品质量 稳定。
② 碱中和法
• 将铝盐溶液[Al(NO3)3、AlCl3、 Al2(SO4)3等]用氨水或其它碱 液( NaOH、KOH、NH4OH ) 中和,得到水合氧化铝:
Al3+ + OH- ==== Al2O3·nH2O↓
易洗涤。
④ 形成沉淀物的溶解度应小些
– 沉淀反应愈完全、原料消耗愈小;
• 对于贵金属尤为重要。
⑤ 无毒
– 不应使催化剂中毒或造成环境污染。
• 对金属盐类选择有以下要求:
– 一般选用硝酸盐的形式提供金属盐,硝酸根易于洗 脱或加热时分解而无残留。
– 而氯化物或硫化物残留在催化剂中,在使用时会呈 现H2S或HCl形式释放出来,致使催化剂中毒。
1、载体选择
• 浸渍法首先要选择合适载体,根据用途可选择 – 粉末状载体 – 成型载体
• 根据反应类型特点选择不同性质的载体
– 外扩散控制
不需比表面较大的载体;
– 内扩散控制
载体孔径不宜过小;
• 阻挡反应物分子进入孔道内部;
• 生成物返回气相受阻。
烯烃水合反应工艺与催化剂研究进展

化工进展Chemical Industry and Engineering Progress2023 年第 42 卷第 7 期烯烃水合反应工艺与催化剂研究进展韩恒文,韩伟,李明丰(中石化石油化工科学研究院有限公司,北京 100083)摘要:综合介绍了多种烯烃水合反应的机理、生产工艺及催化剂的研究成果。
分类详细归纳了环己烯、丙烯、高碳烯烃等通过水合反应生产相应产物醇的生产工艺和催化剂的最新研究进展,并分析了烯烃水合技术的未来发展趋势。
分析发现:烯烃水合反应的路径主要分为直接路径和间接路径;其反应机理主要有马氏规则的亲电加成机理、反马氏规则的亲电加成机理、自由基反应机理等;烯烃水合反应用催化剂从液体酸、碱,过渡金属盐或氧盐,不断向分子筛、固体酸、合成树脂、光催化剂、酶催化剂方向发展。
未来,光催化和生物酶催化是烯烃水合科技研究的重点方向;而反应设备参数优化、提升催化剂性能、强化物料混合效果、改善传质过程等,则是烯烃水合生产工艺优化的发展趋势。
关键词:烯烃;水合;醇;分子筛;催化剂;选择性中图分类号:TE6;TQ2 文献标志码:A 文章编号:1000-6613(2023)07-3489-12Research progress in olefin hydration process and the catalystsHAN Hengwen ,HAN Wei ,LI Mingfeng(SINOPEC Research Institute of Petroleum Processing Co., Ltd., Beijing 100083, China)Abstract: Researches of the mechanism, process and catalysts for various olefin hydration reactions were reviewed. The latest progress in the processes and catalysts of cyclohexene hydration to produce cyclohexanol, propylene hydration to produce isopropanol, and high-carbon olefin hydration to produce high-carbon alcohol were summarized in detail, together with the development trend of olefin hydration reaction in the future. The reaction pathways of olefin hydration could be mainly divided into direct and indirect ones, and the reaction mechanisms were mainly the electrophilic addition mechanism ofmartensitic rule, the electrophilic addition mechanism of anti -martensitic rule and the radical mechanism. The olefin hydration catalysts are changing from liquid acid, alkali, transition metal salt or oxygen salt, to molecular sieve, solid acid, synthetic resin, photocatalyst and enzyme catalyst. In thefuture, photocatalysis and enzyme catalysis will be the key research directions of olefin hydration technology, and the optimization of reaction equipment parameters, the enhancement of catalyst performance, and the improvement of material mixing and mass transfer are the development trends of olefin hydration process optimization.Keywords: olefin; hydration; alcohol; molecular sieve; catalyst; selectivity综述与专论DOI :10.16085/j.issn.1000-6613.2022-1590收稿日期:2022-08-29;修改稿日期:2022-11-05。
- 1、下载文档前请自行甄别文档内容的完整性,平台不提供额外的编辑、内容补充、找答案等附加服务。
- 2、"仅部分预览"的文档,不可在线预览部分如存在完整性等问题,可反馈申请退款(可完整预览的文档不适用该条件!)。
- 3、如文档侵犯您的权益,请联系客服反馈,我们会尽快为您处理(人工客服工作时间:9:00-18:30)。
主要内容
一. 催化裂化工艺简介
重质油加工技术现状 催化裂化工艺发展史 催化裂化过程中的化学反应 催化裂化反应现有的一些认识
二. 催化裂化催化剂概述
催化裂化催化剂发展史 催化剂的主要性能与组成 催化裂化催化剂的制备
三. 分子筛特性与催化剂设计
分子筛材料重要性 分子筛基本性质 分子筛酸性及其催化反应 分子筛渣油催化剂的设计
12
KBR
ExxonMobil
Shell S&W(Shaw)
1.2 催化裂化工艺发展史
国内催化裂化技术发展历程
技术名称
1961-1965 同高并列式流化床FCC装置 1966-1970 同高并列式带管反FCC装置 1971-1975 高低并列式全提升管装置 1976-1980 同轴式半工业化FCC装置 烧焦罐式再生装置 掺渣油工业试验 能量回收机组 1981-1985 同轴式掺渣油(内取热)FCC装置 高低并列式常渣(内取热)FCC装置 高低并列式掺渣(内外取热)FCC装置 1986-1990 掺渣两段再生FCC装置 同轴式烧焦罐及床层两段再生装置 1991-1995 管式再生器 派生多产烯烃技术(MGG、ARGG、DCC) 1996-2000 派生多产柴油技术(MGD) 2000派生降烯烃技术(MIP、FDFCC、TSRFCC) 派生清洁油品多产烯烃技术(MIP-CGP、TMP)
项目
实施场所 内涵 核心组件
催化裂化
催化裂化装置 重要的劣质原料轻质 化过程 催化裂化催化剂
手术
手术台 重要的治病方法 剪刀
主要功能 重油大分子切割与整 合,本身不变化,改 变反应速度与方向
原料 产品 最大不同 重油大分子 轻质化产品 原油越来越少
伤病区切除与整 合,本身不变化 ,加快手术进行
病人 康愈人 病人越来越多
工业化时间
SSSC-166 FCC Ⅶ, 2007 P229
①
中国重油 催化裂化 占原油加 工35% 中国催化 裂化加工 重油60% 中国催化 裂化掺渣 40%
②
③
总计
占原油比例
4002
24
1879
30
1037
22
3889
15
5801
19
16609
20
100
9
1.1 重质油加工技术现状
劣质重油加工过程收率
产率 减粘 裂化 临氢 减粘 加氢 裂化 焦化 延迟 10.7 13.9 42.6 56.5 32.8 灵活 10.0 13.7 54.4 68.1 22.0 加氢裂 沸腾 化/脱沥 床 青 3.0 3.7 67.3 71.0 26.0 4 13 66 79 17 催化 裂化 10.4 41.5 23.3 64.8 23.0
1.1 重质油加工技术现状
国内原油供求趋势Βιβλιοθήκη ① 2011年8月对 外依存度 55.2%,美国 53.5%; ② 2020年6亿吨,
我国原料油进口依存度不断增加,而进口原料油重质
2030依存度 80%
7
、劣质化日益严重,重油的高效转化成为炼化企业面
临的重要课题。
1.1 重质油加工技术现状
重油分子特点
11
1.2 催化裂化工艺发展史
国外主要专利商催化裂化技术发展历程
专利商 UOP 类型 叠置式; 高低并列式; 高效再生式; 逆流两段再生式 改进型 PetroFCC、LOCC多产烯烃技术 正流A型 B型 C型 F型 改进型 HOC型 Maxofin、Superflex多产烯烃技术 同高并列Ⅳ型 管式反应器型 灵活裂化型 高低并列式 渣油FCCU RFCC 改进型 首套投产时间 1947 1952 1974 1980 1990年以后 1951 1953 1960 1976 1979 1961 1990年以后 1952 1958 1974 1974 1981 1990年以后
4
第一部分
催化裂化工艺简介
5
1.1 重质油加工技术现状
世界原油供求趋势
P.O.Connor,SSSC169, 2007, P231
2003年现有供需持平
,原油需求持续增加 ,但是现有油田产量 降低,供需矛盾突出 ,超重原油和油砂沥 青等非常规原油开采 加大。
油田开采预测(ExxonMobil)
6
3.0 3.7 53.3 57.0 40.0
残渣 形态
焦油
液态 沥青
固体 沥青
焦炭 块
焦粉
固体沥 青
减渣
焦炭与 减渣
FFB反应:焦化原 料,低活性催化 剂,C/O 10.6,温 度450℃
1.2 催化裂化工艺发展史
全球第一套商业流化催化装置 (1942年,埃克森公司)
目前全球最大的一套催化装置 (2009年,印度信诚650万吨/年)
③
P.O.Connor,SSSC169, 2007, P336
① ②
减粘裂化属 于浅度裂化 灵活焦化与 加氢裂化/ 脱沥青的馏 分油收率高 沸腾床加氢 的馏分油收 率可以达到 80%
气体 石脑油 瓦斯油 馏分油 残渣
1.7 6.1 10.4 16.5 81.8
2.5 3.0 34.5 37.5 60.0
催化裂化工艺及催化剂概述
从事领域-催化裂化
原油一次加工
催化剂与工艺技术
常减压
是其最关键技术
原油二次加工
重整
焦化
催化裂化
加工重油60%
加氢
其它
国内现状
柴油35%
汽油75%
丙烯40%
2
催化裂化过程像什么?催化剂是什么?
催化裂化过程就像给重油分子做手术 催化裂化催化剂就是手术中的剪刀 催化裂化过程与手术对比
稠环芳烃多与分子尺寸大
1.16 nm
973项目研发成果
2.58 nm
1.93 nm
分子结构随石油流程的变化(AM-02-53) 定义:重油是指常规原油中的渣油和API 重度小于20(密度大于0.934),2.5-15nm
8
1.1 重质油加工技术现状
世界渣油加工能力(千桶/天,2003)
转化技术 热裂化/减粘 焦化 脱沥青 加氢 固定床 沸腾床 浆态床 渣油FCC 102 831 244 4 281 23 318 79 681 49 1832 497 4 3942 3 0 24 美国 44 2245 283 499 加拿大/墨西 哥/委内瑞拉 331 951 39 30 日本 24 66 16 591 欧洲 2260 673 46 149 其他 1635 1169 75 1042 总计 4293 5104 458 2312 百分数 25 31 3 14