渗碳工件的变形
主轴整体渗碳淬火后的变形量-概述说明以及解释

主轴整体渗碳淬火后的变形量-概述说明以及解释1.引言1.1 概述概述部分的内容如下:概述主轴整体渗碳淬火是一种广泛运用于工程领域的热处理技术。
在制造领域中,主轴承担着关键的作用,因此对主轴进行热处理以提高其硬度和强度具有重要意义。
本文将重点探讨主轴整体渗碳淬火后的变形量。
研究主轴淬火后的变形量对于提高主轴零件加工精度、减小后续加工工序中的修正量以及提高整体产品质量具有重要意义。
在研究过程中,我们将首先介绍主轴整体渗碳淬火的原理,探讨渗碳淬火是如何通过物质渗透和淬火过程改善主轴的硬度和强度。
然后,我们将深入探讨主轴整体渗碳淬火后的变形机制,分析淬火过程中主轴发生形变的原因和特点。
在结论部分,我们将重点讨论影响主轴整体渗碳淬火后变形量的因素,并提出一些有效的控制变形量的方法。
通过对这些影响因素的分析和相应的控制方法,我们可以更好地掌握主轴整体渗碳淬火后的变形规律,从而提高主轴的加工精度和整体产品的质量。
本文旨在为相关研究者和工程师提供一些有益的信息和指导,以便更好地理解和应用主轴整体渗碳淬火技术。
通过深入研究和有效控制变形量,我们可以有效提高主轴的性能和使用寿命,为相关工程领域的发展做出贡献。
1.2文章结构1.2 文章结构本文将分为三个主要部分,即引言、正文和结论。
下面将详细介绍每个部分的内容:- 引言部分将提供对本文研究主题的概述,包括主轴整体渗碳淬火后的变形量。
这一部分将描述该研究领域的背景和研究意义,并引出本文的目的与内容。
- 正文部分将分为两个小节。
首先,2.1节将介绍主轴整体渗碳淬火的原理,包括渗碳和淬火过程的基本原理以及其对材料性能的影响。
其次,2.2节将深入探讨主轴整体渗碳淬火后的变形机制,分析变形的主要原因、形式和程度,并探讨不同变形机制之间的关系。
- 结论部分将总结文章的主要研究结果,并提供对主轴整体渗碳淬火后变形量的影响因素和控制方法的讨论。
在3.1节中,将列举影响主轴整体渗碳淬火后变形量的因素,并对它们的作用进行分析。
风电齿轮渗碳淬火变形分析与改善

零件号 H1 H2 H3 H4
图10 H3零件左右齿面变形
图11 炉和热处理工艺对齿轮变形的影响
渗碳装炉 平装4块蜂窝板 平装8块蜂窝板
淬火装炉 挂放无阻尼工装 挂放有阻尼工装
挂放有阻尼工装
渗碳淬火工艺 原工艺 改进工艺
改进工艺
椭圆/mm 0.18 0.14 0.14 0.15
4)将左右齿面的磨齿对中数据进行平均,如图 6所示,发现零件节圆存在明显的椭圆,椭圆趋势呈 梨状分布,椭圆量约0.18mm。
根据对H1零件磨齿对中数据的分析,暂无法判 定零件齿向变形是由端面翘曲或齿部畸变造成的。 零件的椭圆趋势呈梨状分布,虽无法确定具体位置 是否与挂装有关,但根据单点挂装的情况推测,梨 柄位置(148号齿附近)应是与工装接触的位置, 此处凸起最大;左右齿面变形量最大位置无显著规 律,但在椭圆的梨状尾部附近(即挂装下部)变形 趋势最大。
要求 实测
2.9~3.9 3.39、3.46
58~64 60.26、59.62
≥30 38
ISO 6336:5 MQ级 细针状
弥散
细针状
≤30 15
无块状铁素体 ≤0.05 无块状铁素体 0.025
4.4 优化验证 在序列号为H3和H4的零件生产时,同时采用图
8的渗碳工艺、渗碳时底部蜂窝板满铺的平放装炉方 式(见图9),在挂装淬火装炉时,在底盘上增加网 孔阻尼工装,零件渗碳淬火后,变形得到大幅度改
图8 H2零件渗碳后轴向圆跳动
图9 改善后的渗碳装炉 4.3 淬火装炉改善
综上所述,齿轮下部约1/4位置冷速较快是齿轮
热加工
63 2021年 第3期
热处理
Heat Treatment
变形的影响因素之一[6],故对淬火的装炉形式进行 调整。
渗碳钢的热处理知识点总结

一、渗碳钢的热处理工序用于制造渗碳零件的钢称为渗碳钢。
渗碳钢的主要热处理工序一般是在渗碳之后再进行淬火和低温回火。
处理后零件的心部为具有足够强度和韧性的低碳马氏体组织,表层为硬而耐磨的回火马氏体和一定量的细小碳化物组织。
有些结构零件,是在承受较强烈的冲击作用和受磨损的条件下进行工作的,例如汽车、拖拉机上的变速箱齿轮,内燃机上的凸轮、活塞销等。
根据工作条件,要求这些零件具有高的表面硬度和耐磨性,而心部则要求有较高的强度和适当的韧性,即要求工件“表硬里韧”的性能。
为了兼顾上述双重性能,可以采用低碳钢通过渗碳淬火及低温回火来达到,此时零件心部是低碳钢淬火组织,保证了高韧性和足够的强度,而表层(在一定的深度)则具有高碳量(0.85%~1.05%),经淬火后有很高的硬度(HRC>60),并可获得良好的耐磨性。
二、渗碳钢的成分特点渗碳钢的含碳量一般都很低(在 0.15%~0.25%之间),属于低碳钢,这样的碳含量保证了渗碳零件的心部具有良好的韧性和塑性。
为了提高钢的心部的强度,可在钢中加入一定数量的合金元素,如Cr、Ni、Mn、Mo、W、Ti、B等。
其中 Cr、Mn、Ni 等合金元素所起的主要作用是增加钢的淬透性,使其在淬火和低温回火后表层和心部组织得到强化。
另外,少量的Mo、W、Ti等碳化物形成元素,可形成稳定的合金碳化物,起到细化晶粒、抑制钢件在渗碳时发生过热的作用。
微量的B(0.001%~0.004%)能强烈地增加合金渗碳钢的淬透性。
渗碳钢的分类根据淬透性或强度等级的不同,合金渗碳钢分为三类。
低淬透性合金渗碳钢即低强度渗碳钢(抗拉强度≤800MPa),如15Cr、20Cr、15Mn2、20Mn2等。
这类钢淬透性低,经渗碳、淬火与低温回火后心部强度较低且强度与韧性配合较差。
主要用于制造受力较小,强度要求不高的耐磨零件,如柴油机的凸轮轴、活塞销、滑块、小齿轮等。
这类钢渗碳时心部晶粒易于长大,特别是锰钢。
齿轮渗碳淬火变形原因及控制措施_柳晓鹏

收稿日期:2009-03-01作者简介:柳晓鹏(1981—),男,山东莱阳人,主要从事舰船动力学研究.齿轮渗碳淬火变形原因及控制措施柳晓鹏,雷建波(海军驻重庆舰船动力军事代表室,重庆 400000)摘要:介绍了渗碳淬火齿轮的变形规律,分析了渗碳淬火齿轮变形的原因,提出了减小和控制渗碳淬火齿轮变形的措施,主要可通过采用优化零件结构、完善机加工与热处理工序配合、优化热处理工艺等方法减小零件内部应力,改善热处理变形.关键词:齿轮;热处理;变形;控制中图分类号:F407.61文献标识码:A文章编号:1006-0707(2009)05-0058-03 热处理变形会使齿轮零件前期加工获得的精度受到严重损失,这些损失有时甚至通过复杂、先进的修形技术(磨齿、校直等)也难以恢复.对于渗碳淬火的齿轮特别是大型齿轮,其变形量很大且难以控制.较大的变形不仅使磨削量增加、成本提高,而且影响齿轮制造精度,降低承载能力,最终将使寿命大大下降[1].热处理变形主要由零件在机加工时产生的残余应力、热处理过程中产生的热应力和组织应力以及零件自重变形等共同作用产生.影响齿轮渗碳淬火变形的因素很多,包括齿轮的几何形状、原材料及冶金质量、锻造和机加工的残余应力、装料方式和热处理工艺及设备等[2].1 渗碳淬火齿轮变形规律 对大型齿轮质量和寿命影响最大的变形因素来自齿轮外径、公法线长度和螺旋角等.1.1 大型齿轮变形规律大型齿轮渗碳淬火后齿顶圆外径呈明显胀大趋势,且上下不均匀呈锥形;径长比(齿轮外径/齿宽)越大,外径胀大量越大.碳浓度失控偏高时,齿轮外径呈收缩趋势.1.2 大型齿轮轴变形规律齿顶圆外径呈明显收缩趋势,但一根齿轴的齿宽方向上,中间呈缩小、两端略呈胀大趋势.1.3 齿圈变形规律大型齿圈经渗碳淬火后,其外径均胀大,齿宽大小不同时,齿宽方向呈锥形或腰鼓形胀大.2 渗碳淬火齿轮变形原因2.1 渗碳件变形的实质渗碳的低碳钢,原始相结构由铁素体和少量珠光体组成,铁素体量约占整个体积的80%.当加热至AC1以上温度时,珠光体转变为奥氏体,900℃时铁素体全部转变为奥氏体.920~940℃渗碳时,零件表面奥氏体区碳浓度增加至0.6%~1.2%,这部分碳浓度高的奥氏体冷至600~650℃才开始向珠光体、索氏体转变,而心部区的低碳奥氏体在900℃即开始分解为铁素体,冷至550℃左右全部转变完成.心部奥氏体向铁素体转变是比容增大的过程,表层奥氏体冷却是热收缩量增加的变化过程.在整个冷却过程中,心部铁素体生成时总是受到表层高碳奥氏体区的压应力.此外,大型齿轮由于模数大、渗层深,渗碳时间较长,同时由于自重影响,也会增加变形.2.2 淬火变形的原因零件淬火时,淬火应力越大,相变越不均匀;比容差越大,则淬火变形越严重.此外淬火变形还与钢的屈服强度有关,塑性变形抗力越大,其变形程度就越小.对齿轮和齿轮轴渗碳淬火冷却时各部位的冷却速度、组织及硬度状态比较分析,可以发现上中下各部位冷却速度的差别,以及表面、过渡区、心部冷却速度的差别与其组织转变的不同时性是造成齿轮变形的主要原因.因此,减小变形也可以通过提高各环节的均匀性来实现.3 减小和控制渗碳淬火齿轮变形的措施3.1 控制原材料减小变形我国高速重载齿轮行业目前普遍使用的钢种有20CrMn Mo 、20CrNi 2Mo 、17CrNi Mo 6、42CrMo 、30CrMoA 等,由于受到冶炼水平等影响,原材料质量状况不尽人意.同时由于进货渠道不同,质量也有较大波动,给变形控制带来很大难度.总体来说,原材料对变形的影响如下:1)材料淬透性是影响热处理变形的主要因素之一,淬透性带宽较小变形较小;反之则变形较大.第30卷 第5期四川兵工学报2009年5月2)钢的冶金质量.钢材经过真空脱气处理后,材料纯净度高、杂质含量少、晶粒度均匀,以氧化物为主的夹杂物大幅度减少.钢材晶粒度对变形有着明显的影响,随着晶粒度尺寸增加,变形加大.因而要严格控制晶粒度尺寸及混晶.大型齿轮通常要求晶粒度在5级以上.同时,随着钢材淬透性的增加,变形率增大.因而在齿轮选材时,只要淬透性能满足要求即可.但应尽可能控制好淬透性带,以利于变形规律的统计和摸索.此外,马氏体相变点M s对变形的影响是随着Ms点的降低,变形增大.一般C、Mn含量较高的钢材具有较低的Ms点,因而从变形的角度考虑,钢材中C、Mn含量应尽可能控制在较低的范围内.3)锻件质量.要求合理的锻造流线和锻造比,严格控制锻件利用率,加强锻后热处理控制等措施均能提高锻件质量,从而减小热处理变形.3.2 设计和机加工的预先控制3.2.1 合理的设计零件的结构、用材、技术要求对其热处理工艺性能有很大影响.处理好它们之间的关系,对减少淬火变形大有益处.1)合理的零件结构.合理结构即零件在设计时其形状应尽可能简单,分布均匀、对称,力求在零件上无盲孔、尖棱等.由于零件设计不合理,往往在淬火时应力分布不均匀,从而产生不规则变形.因此,在满足使用性能的条件下,零件设计时要尽可能兼顾热处理变形.2)选材.零件在选材时,首先应保证使用性能的要求,同时还要考虑热处理工艺性能及经济性能.既不能为降低成本采用热处理工艺性能较差的材料,又不能盲目提高成本,一般应遵循以下原则:①依据材料热处理性能选材,一般选材原则是要以较缓和的冷却方法来达到淬硬零件的目的;②将材料和热处理方法结合起来选材,在使用性能允许的情况下,可通过改变热处理方法来达到设计要求,即将选材与热处理方法有机的结合起来;③合理的力学性能要求,设计者除在材料与力学性能之间进行合理搭配外,还应考虑某些零件局部的特殊要求,以免降低热处理工艺性能,造成不必要的变形,甚至产生不合格品.3.2.2 适当的机加工机加工由于进给量、零件各部位加工余量及加工差异,可导致零件各部位应力性质不同和应力分部不均衡,致使零件在淬火时发生变形.为此应考虑:1)加工方法与变形的关系.在零件的成形加工过程中,可能会采用车、滚、镗、磨等不同的加工方法,从而使零件的各部位应力分布不均衡,淬火时产生较大变形.反过来,则可通过改变局部加工方法,使该部分残留的应力对减少变形有利,从而达到减少变形的目的.2)加工量与变形.零件各部分加工量不同或人为造成加工量的不同,均会给零件热处理后的变形造成不良影响.3)机加工工序与变形.合理地安排机加工工序,协调好机加工与热处理之间的关系,对减少淬火变形大有益处.特别是那些形状不对称或带有长槽类零件,这点尤为重要.例如在易变形的齿圈淬火前增加一道去应力工序,磨齿后再进行一次低温回火.3.2.3 变形的预补偿对大型齿圈,可针对渗碳淬火后齿顶圆涨大规律,预先车小齿顶圆;对大型齿轴的螺旋角,可采取滚齿时预补偿办法达到减小螺旋角变形的目的.3.3 热处理工艺操作与变形关系3.3.1 预先热处理采用适当的预先热处理方法,可有效减小后续热处理的变形.对齿轮和齿轮轴,由于退火周期长、成本高,目前一般采用正火回火处理,而大型齿圈则采用调质作为预先热处理.3.3.2 渗碳与淬火温度通常采用的渗碳温度为920~930℃.采用稀土催渗技术时,加入稀土元素后,在渗碳周期相当的前提下,可使渗碳温度由930℃降为860~880℃.在改善渗层组织、节能、延长设备寿命的同时,还可以明显减少渗碳件的变形.但目前催渗技术在大型齿轮深层渗碳变形控制方面还有待进一步研究.淬火温度对零件的淬火变形影响很大,淬火变形趋势一般规律如图1所示.根据此规律,可以通过调整淬火温度来达到减少变形的目的,或经热处理试验后再根据试验结果合理选择预留机加工量与淬火温度.一般情况下,淬火温度越高则零件变形越大.这是由于增加了零件截面上的温差,使热应力增加,同时由于过高的加热温度,使奥氏体晶粒长大,降低了塑性变形的抗力,从而增大了淬火变形.为此从减少变形出发,应尽量选择淬火下限温度.3.3.3 加热速度当零件内部存在较大的机加工残余应力,而零件截面差别又较大时,升温速度对变形影响更大.零件快速加热会产生较大的热应力,与零件内部残余应力和相变组织应力相互作用,如应力方向一致,产生迭加或合成的应力很容易使零件在高温状态下产生变形.3.3.4 淬火保温时间保温时间的选择除应保证零件透烧、淬火后达到要求的硬度或其它力学性能外,还要考虑它对淬火变形的影响.延长淬火保温时间,实际上也就相应提高了淬火温度.3.3.5 装炉方法零件在加热时摆放形式不合理,会因零件自重而引起变形,或因零件之间相互挤压产生变形,或因零件堆放过密造成加热及冷却不均而产生变形.因此装炉要均匀,各种齿轮轴渗碳淬火时可设计相应的工装进行压紧,以减少变形.齿轮要根据形状分别采用平放或垂直放置的方法,特别地,在某些大型齿圈热处理时,可设计专用的工装夹具对其进行装炉,从而减小变形.3.3.6 渗碳淬火设备选用良好的渗碳淬火设备是减小齿轮变形的重要手段,对大型齿轮尤为重要.大型齿轮采用井式气体渗碳炉进行渗碳淬火时,应满足控温精度±1℃,炉温均匀度±7℃,碳势均匀度±0.05%.59柳晓鹏,等:齿轮渗碳淬火变形原因及控制措施3.3.7 淬火介质与设备[3]在保证零件淬火硬度的前提下,一般选用冷却较缓和的介质,同时还要控制好介质的温度.目前常用的淬火介质为普通淬火油,通过添加剂对其进行改性处理后,其冷却性能较好,能满足硬度要求.对于淬火冷却设备,要保证零件淬火时冷却均匀,避免使淬火油温有较大温差,因而要求安装加热装置和搅拌装置.热处理车间两个淬火油槽,旧油槽只有搅拌循环,新油槽既有搅拌循环,又有热交换器循环.通过对比,在保证硬度前提下,热油淬火变形要比冷油淬火变形小.淬火过程中,变形是由于内部残余应力分布不均匀造成的,应力性质与大小受多种因素影响.当单项因素或多项因素同时起作用时,淬火介质温度是重要因素.就目前使用的淬火油来讲,其温度对冷却速度并无明显影响,但对变形影响较大.所以在满足使用性能的前提下,往往采用热油淬火.图1 淬火变形的一般规律4 结束语 总之,齿轮变形是一个复杂的系统工程,是各种因素综合作用的结果.要减小齿轮的变形,其方法可归结为“均匀”二字,只要做到材料均匀、形状均匀、加热和冷却均匀,各个环节都均匀,就不会有变形问题.实际上这是不可能完全满足的,所以变形不可避免.到目前为止,大型齿轮的变形控制依然是一个长期的课题,但只要有针对性的采取措施,就可以使变形量尽可能减小.参考文献:[1] 程里,程方.大型渗碳齿轮圈热处理畸变与控制[J ].金属热处理,2005(3):88-91.[2] 陈仁悟,林建生.化学热处理原理[M ].北京:机械工业出版社,1988.[3] Altena H .Influence of Gas and Oil Quenching Parameterson changes in Shape and Dimension of Gear Wheels [J ].HTM .2001(1):1-8.(上接第57页)4 结束语 本文中结合本人的实际工作,提出了基于FPGA 的测试对象整合方法,利用电路板对应电路的模块化设计思想,对于后续的电路板调试奠定了基础.此方法亦可用于类似的工作中,对于简化电路设计,提高工作效率有一定的参考价值.参考文献:[1] 褚振勇,翁木云.FPGA 设计及应用[M ].西安:西安电子科技大学出版社,2002.[2] 宋万杰,罗丰,吴顺君.CPLD 技术及其应用[M ].西安:西安电子科技大学出版社,1999.[3] 王道宪.CPLD /FPGA 可编程逻辑器件应用与开发[M ].北京:国防工业出版社,2004.60四川兵工学报。
渗碳
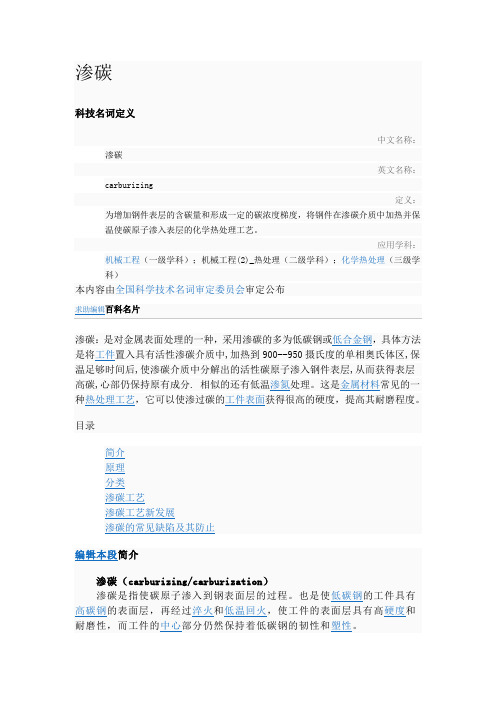
渗碳科技名词定义中文名称:渗碳英文名称:carburizing定义:为增加钢件表层的含碳量和形成一定的碳浓度梯度,将钢件在渗碳介质中加热并保温使碳原子渗入表层的化学热处理工艺。
应用学科:机械工程(一级学科);机械工程(2)_热处理(二级学科);化学热处理(三级学科)本内容由全国科学技术名词审定委员会审定公布编辑本组织及性能特点:不能细化钢的晶粒。
工件淬火变形较大,合金钢渗碳件表面残余奥氏体量较多,表面硬度较低适用范围:操作简单,成本低廉用来处理对变形和承受冲击载荷不大的零件,适用于气体渗碳和液体渗碳工艺。
2 、预冷直接淬火、低温回火,淬火温度800-850℃组织及性能特点:可以减少工件淬火变形,渗层中残余奥氏体量也可稍有降低,表面硬度略有提高,但奥氏体晶粒没有变化。
适用范围:操作简单,工件氧化、脱碳及淬火变形均小,广泛应用于细晶粒钢制造的各种工具。
3、一次加热淬火,低温回火,淬火温度820-850℃或780-810℃组织及性能特点:对心部强度要求较高者,采用820-850℃淬火,心部为低碳M,表面要求硬度高者,采用780-810℃淬火可以细化晶粒。
适用范围:适用于固体渗碳后的碳钢和低合金钢工件、气体、液体渗碳的粗晶粒钢,某些渗碳后不宜直接淬火的工件及渗碳后需机械加工的零件。
4、渗碳高温回火,一次加热淬火,低温回火,淬火温度840-860℃组织及性能特点:高温回火使M和残余A分解,渗层中碳和合金元素以碳化物形式析出,便于切削加工及淬火后残余A减少。
适用范围:主要用于Cr—Ni合金渗碳工件5、二次淬火低温回火组织及性能特点:第一次淬火(或正火),可以消除渗碳层网状碳化物及细化心部组织(850-870℃),第二次淬火主要改善渗层组织,对心部性能要求不高时可在材料的Ac1—Ac3之间淬火,对心部性能要求高时要在Ac3以上淬火。
适用范围:主要用于对力学性能要求很高的重要渗碳件,特别是对粗晶粒钢。
但在渗碳后需经过两次高温加热,使工件变形和氧化脱碳增加,热处理过程较复杂。
表面渗碳处理工艺

表面渗碳处理工艺渗碳与渗氮一般是指钢的表面化学热处理渗碳必须用低碳钢或低碳合金钢。
可分为固体、液体、气体渗碳三种。
应用较广泛的气体渗碳,加热温度900-950℃。
渗碳深度主要取决于保温时间,一般按每小时0.2-0.25mm估算。
表面含碳量可达百分之0.85-1.05。
渗碳后必须热处理,常用淬火后低温回火。
得到表面高硬度心部高韧性的耐磨抗冲击零件。
渗氮应用最广泛的气体渗氮,加热温度500-600℃。
氮原子与钢的表面中的铝、铬、钼形成氮化物,一般深度为0.1-0.6mm,氮化层不用淬火即可得到很高的硬度,这种性能可维持到600-650℃。
工件变形小,可防止水、蒸气、碱性溶液的腐蚀。
但生产周期长,成本高,氮化层薄而脆,不宜承受集中的重载荷。
主要用来处理重要和复杂的精密零件。
涂层、镀膜是物理的方法。
“渗”是化学变化,本质不同。
钢的渗碳---就是将低碳钢在富碳的介质中加热到高温(一般为900--950℃),使活性碳原子渗入钢的表面,以获得高碳的渗层组织。
随后经淬火和低温回火,使表面具有高的硬度、耐磨性及疲劳抗力,而心部仍保持足够的强度和韧性。
渗碳钢的化学成分特点1)渗碳钢的含碳量一般都在0.15--0.25%范围内,对于重载的渗碳体,可以提高到0.25--0.30%,以使心部在淬火及低温回火后仍具有足够的塑性和韧性。
但含碳量不能太低,否则就不能保证一定的强度。
2)合金元素在渗碳钢中的作用是提高淬透性,细化晶粒,强化固溶体,影响渗层中的含碳量、渗层厚度及组织。
在渗碳钢中通常加入的合金元素有锰、铬、镍、钼、钨、钒、硼等。
常用渗碳钢可以分碳素渗碳钢和合金渗碳钢两大类1)碳素渗碳钢中,用得最多的是15和20钢,它们经渗碳和热处理后表面硬度可达56--62HRC。
但由于淬透性较低,只适用于心部强度要求不高、受力小、承受磨损的小型零件,如轴套、链条等。
2)低合金渗碳钢如20Cr、20Cr2MnVB、20Mn2TiB等,其渗透性和心部强度均较碳素渗碳钢高,可用于制造一般机械中的较为重要的渗碳件,如汽车、拖拉机中的齿轮、活塞销等。
各种渗层比较解读

Fe2B
或FeB+Fe2B
渗后
热处理
淬火+低温回火
无
无
淬火+回火
渗层
硬度
56~64HRC
950~1200HV
500~1000HV
58~67HRC
1300~2300HV
常用
渗剂
固:木炭,碳酸盐,粘结剂
优点
比渗氮工艺的渗层厚,可承受重载荷;工艺时间短;渗前不需要调质处理
常用固体渗剂
50%铬铁+
45%Al2O3+5%NH4Cl
常用硼砂盐浴
5%~10%钒粉+
95%~90%无水硼砂+少量中性盐
固体粉末或颗粒
40%~50%钛粉+
55%~45%Al2O3+3%NaF+2%NH4Cl
硼砂盐浴
4%~8%铌粉+
96%~92%硼砂
渗温
/℃
950~1050
900~1000
900~1000
渗氮层的机械性能比渗碳层的好;渗氮温度低,渗后不进行淬火处理,工件变形小;渗氮温度低
与渗氮相比,氮碳共渗的速度快,渗层韧性更高
与渗碳相比处理温度低,变形小,共渗层的机械性能更好
工艺时间短,渗层机械性能好
缺点
硬度和耐磨性不如渗氮层高;渗碳温度高,工件变形大;渗后往往需要淬火处理
渗氮层较薄、且脆性大,不能承受太大的接触应力和高的冲击载荷;渗氮时间长,生产率低,成本较高
8%~15%V2O5+
60%~70%Na2B4O7+1%~3%NaF+Al
常用固体粉末
渗碳齿轮热处理的变形控制

作者:魏启武渗碳齿轮的热处理变形热处理变形直接影响到齿轮的精度、强度、噪声和寿命,即使在渗碳热处理后加上磨齿工序,变形仍然要降低齿轮的精度等级。
影响渗碳热处理变形的因素较多,只有控制各方面的因素才能将变形控制到较小程度。
控制齿轮变形也必须在制造齿轮的全过程中设法去解决。
(1)齿轮材料冶金因素对变形的影响试验表明,钢的淬透性越高.变形越大。
当心部硬度高于40HRC时,变形会明显增大。
因此,对钢的淬透性带有一定的要求,淬透性带越窄.则变形越稳定,要钢厂提供“低、稳变形”钢材。
A1/N含量比控制在1~2.5范围内,可使淬进性带变窄、减小变形(日本三菱钢铁株式会设)。
另外,材料的方框偏析及带状组织影响齿轮花键孔的不均匀变形及渗碳不均匀。
(2)预备热处理对齿轮变形的影响正火硬度过高、混晶、大量索氏体或魏氏组织都会使内孔变形增大,所以要用控温正火或等温退火来处理锻件。
(3)渗碳工艺对变形的影响温度的均匀性.碳层的均匀性,冷却介质温度的均匀件都影响齿轮变形,同时渗碳温度越高,渗碳层越厚.油温低、齿轮变形大。
所以要改进设备,优化工艺,提高齿轮热处理质量。
(4)淬火对变形的影响淬火冷却行为是影响齿轮变形最重要的因素,热油淬火比冷油淬火变形小,般控制在100℃±120℃.油的冷却能力对变形也是至关重要的。
搅拌方式和烈度均影响变形,上淬火压床淬火的盘状齿轮,按各种齿轮的变形情况.调整冲火压床参数减小变形,调整内、外压模及胀心块的压力及各段喷油量的大小及上作台面来控制变形。
(5)装夹方式及夹具目的使工件加热冷却均匀,工件各部分渗碳层均匀,以减少热应力不均,组织应力不均,来减小变形,可改变装夹方式,盘类零件与油面垂直,轴类零件立装,使用补偿垫圈,支承垫圈,叠加垫圈等,花键孔零件可用渗碳心轴等。
(6)机械加工方面配合:第一.掌握热处理变形规律、移动公差带位置,提高产品合格率;第二,根据变形规律、施用反变形、收缩端预胀孔,提高淬火后变形合格率,第三,对非对称或厚度不均匀零件采用预留加工量的方法.热处理后再加工。
- 1、下载文档前请自行甄别文档内容的完整性,平台不提供额外的编辑、内容补充、找答案等附加服务。
- 2、"仅部分预览"的文档,不可在线预览部分如存在完整性等问题,可反馈申请退款(可完整预览的文档不适用该条件!)。
- 3、如文档侵犯您的权益,请联系客服反馈,我们会尽快为您处理(人工客服工作时间:9:00-18:30)。
化学热处理工件的变形-渗碳工件的变形
化学热处理工件的表面和心部成分和组织不同,具有不同的比体积和不同的奥氏体等温转变曲线,因此,其热处理变形的特点和规律不同于一般工件。
化学热处理的目的是为了强化零件的表面或改善工件表面的物理性能和化学性能,例如,提高工件的表面硬度、耐磨性和疲劳强度等,改善工件表面的抗氧化性、耐腐蚀性等。
化学热处理层深有限,为了发挥渗层的有利作用,工件经过化学热处理后,只允许进行加工余量不大的磨削加工或不再进行机械加工,相对于一般工件,化学热处理工件的变形要求比较严格,研究和掌握化学热处理工件的变形规律和预防方法是热处理实践中的重要内容。
钢铁材料的化学热处理可以分为两类:一类在高温奥氏体状态下进行,热处理过程中有相变发生,工件变形较大,最常用的高温化学热处理工艺是渗碳;另一类在低温铁素体状态下进行,热处理过程中除因素渗入元素进入渗层形成新相外,不发生相变,工件变形较小,渗氮是最常用的低温化学热处理工艺。
渗碳工件通常用低碳钢和低碳合金钢制造,其原始组织为铁素体和少量珠光体,根据工件的服役要求,工件经过渗碳后需要进行直接淬火、缓冷重新加热淬火或二次淬火。
渗碳工件在渗碳后缓冷和渗碳淬火过程中由于组织应力和热应力的作用而发生变形,其变形的大小和变形规律取决于渗碳钢的化学成分、渗碳层深度、工件的几何形状和尺寸以及渗碳和渗碳后的热处理工艺参数等因素。
工件按其长度、宽度、高度(厚度)的相对尺寸可以分为细长件、平面件和立方体件。
细长件的长度远大于其横截面尺寸,平面件的长度和宽度远大于其高度(厚度),立方体件三个方向的尺寸相差不大。
最大热处理内应力一般总是产生在最大尺寸方向上。
若将该方向称为主导应力方向,则低碳钢和低碳合金钢制造的工件,渗碳后缓冷或空冷心部形成铁素体和珠光体时,一般沿主导应力方向表现为收缩变形,收缩变形率约为0.08%~0.14%。
钢的合金元素含量增加、工件的截面尺寸减小时,变形率也随之减小,甚至出现胀大变形。
图3-13a为20钢制造的量规,经过气体渗碳后(渗碳层浓度1.0㎜),长度方向收缩0.26㎜;图3-13b为20CrMo钢制造的辅具,经过920~940℃固体渗碳缓冷后(渗碳层深度约1.0㎜),孔距252㎜收缩变形量为0.12~0.14㎜。
截面厚度差别较大形状不对称的细长杆件,渗碳空冷后易产生弯曲变形。
弯曲变形的方向取决于材料。
低碳钢渗碳工件冷却快的薄鞭面一侧多为凹面;而12CrN3A、18CrMnTi等合金元素较高的低碳合金钢渗碳工件,冷却快的薄截面一侧往往为凸面。
例:渗碳的导磨镶条,用15钢制造,经过渗碳空冷后,工件向冷却快的两条薄筋面一侧弯曲,用12CrNi3A 钢制造时,则向相反一侧弯曲。
低碳钢和低碳合金钢制造的工件经过920~940℃温度下渗碳后,渗碳层碳的质量分数增加至0.6%~1.0%,渗碳层的高碳奥氏体在空冷或缓冷时要过冷至Ar1以下温度(600℃左右)才开始向珠光体转变,而心部的低碳奥氏体在900℃左右即开始向珠光体转变,而心部的低碳奥氏体过冷至Ar1温度以下也发生共析成分的渗碳层未发生相变,高碳奥氏体只随着温度的降低而发生热收缩,与此同时,心部低碳奥氏体却因铁素体的析出比体积增大而发生膨胀,结果心部受压缩应力,渗碳层则受拉伸应力。
由于心部发生γ→α转变时,相变应力的作用使其屈服强度降低,导致心部发生压缩塑性变形。
低碳合金钢强度较高,相同条件下心部的压缩塑性变形量较小。
形状不对称的渗碳工件空冷时,冷却快的一侧奥氏体线长度收缩量大于冷却慢的一侧,因而产生弯曲应力,当弯曲内应力,当弯曲内应力大于冷却慢的一侧的屈服强度时,则工件向冷却快的一侧弯曲。
对于合金元素含量较高的低碳合金钢,渗
碳后表层具有较高、组织比体积较大的新相,而另一侧因冷却较慢形成的新相硬度较低,故出现相反的弯曲变形。
渗碳工件的淬火变形规律可以用相同的方法分析。
渗碳件的淬火温度通常为800~820℃,淬火时渗碳层的高碳奥氏体从淬火温度冷却至Ms点温度区间内将发生明显的热收缩;而同时心部低碳奥氏体转变为铁素体和珠光体、低碳贝氏体或低碳马氏体。
不论转变为何种组织,心部都因组织比体积的增大而发生体积膨胀,结果在渗碳层与心部产生较大的内应力。
一般来说,未淬透的情况下,由于心部的相变产物为屈服强度较低的铁素体和珠光体,因而心部在渗碳层热收缩的压缩应力作用下,沿主导应力方向产生收缩变形;当心部的相变产物为强度较高的低碳贝氏体和低碳马氏体时,表层高碳奥氏体则在心部胀应力作用下产生塑性变形,结果沿主导应力方向而胀大。
随着渗碳钢碳含量和合金元素含量的增加,渗碳件淬火后心部硬度升高,主导应力方向胀大倾向增大。
根据渗碳工件主导应力方向的变形率随心部硬度的变化曲线可知,当心部硬度为28~32HRC时,渗碳工件的淬火变形很小。
随着心部硬度的升高,胀大变形倾向增大。
很明显,提高淬火加热温度,选用剧烈的淬火冷却介质,提高渗碳钢的淬透性等凡导致渗碳工件心部硬度升高的因素,都会增大渗碳工件沿主导应力方向的胀大倾向。
殷汉奇研究了20CrMnTi钢和20CrMo钢制造的七种花键孔齿轮经过碳氮共渗淬火回火后的变形规律,发现花键孔产生了收缩变形,收缩的大小与心部硬度和钢的碳含量有关,碳含量偏下限的收缩变形量较小,心部硬度超过40HRC时,变形量显著增大。