亚磷酸体系镍磷合金电镀工艺及影响镀层耐蚀性的主因素资料
化学镀沉积镍磷合金:耐腐蚀机理
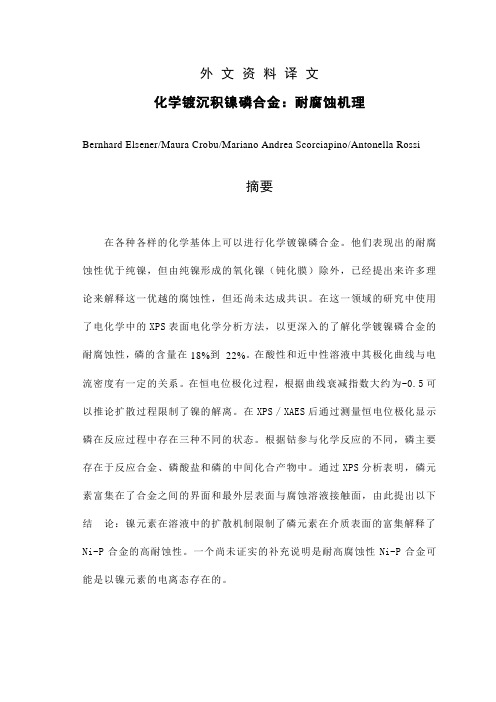
外文资料译文化学镀沉积镍磷合金:耐腐蚀机理Bernhard Elsener/Maura Crobu/Mariano Andrea Scorciapino/Antonella Rossi摘要在各种各样的化学基体上可以进行化学镀镍磷合金。
他们表现出的耐腐蚀性优于纯镍,但由纯镍形成的氧化镍(钝化膜)除外,已经提出来许多理论来解释这一优越的腐蚀性,但还尚未达成共识。
在这一领域的研究中使用了电化学中的XPS表面电化学分析方法,以更深入的了解化学镀镍磷合金的耐腐蚀性,磷的含量在18%到22%。
在酸性和近中性溶液中其极化曲线与电流密度有一定的关系。
在恒电位极化过程,根据曲线衰减指数大约为-0.5可以推论扩散过程限制了镍的解离。
在XPS / XAES后通过测量恒电位极化显示磷在反应过程中存在三种不同的状态。
根据钴参与化学反应的不同,磷主要存在于反应合金、磷酸盐和磷的中间化合产物中。
通过XPS分析表明,磷元素富集在了合金之间的界面和最外层表面与腐蚀溶液接触面,由此提出以下结论:镍元素在溶液中的扩散机制限制了磷元素在介质表面的富集解释了Ni-P合金的高耐蚀性。
一个尚未证实的补充说明是耐高腐蚀性Ni-P合金可能是以镍元素的电离态存在的。
关键词:电位极化扩散,磷,富集, XPS图,衍射参数§1 简介对纳米晶体材料的关注增加使人们对于镍磷合金研究加深,尤其是在具有挑战性的技术应用方面[1,2]。
这些过去主要用作防腐涂料的合金构成了最早的工业应用是在x射线的非晶和纳米晶体材料上,这项技术可以追溯到1946年[3-5]。
现在产生了对三元系镍磷合金的研究[6,7]和共沉积金刚石[8]或聚四氟乙烯颗粒[9],以获得为生产量身定制的功能化表面。
镍磷合金中P元素大约是20%(接近共晶组合)时表现出了比镍更好的耐腐蚀性,同时得到的纯镍在阳极溶液附近镍酸的溶解更加容易[10-22]。
这一现象在化学镀[13-16]或电沉积[17-21]镍磷合金的金属熔体[10-12]时常见到。
化学镀镍磷合金工艺的研究文献综述(二)
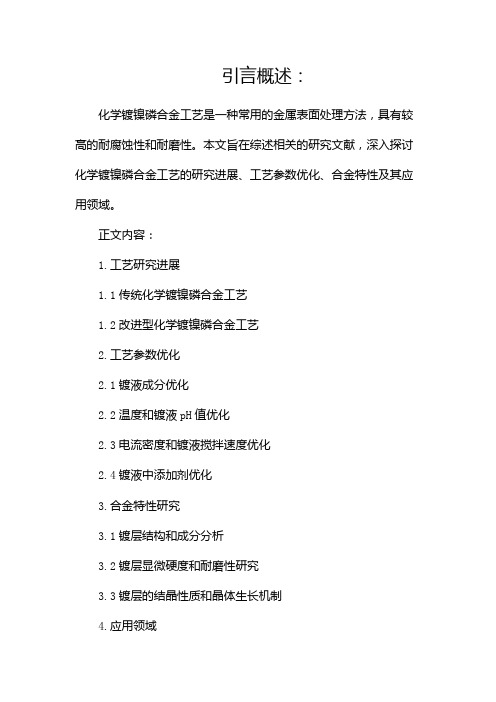
引言概述:
化学镀镍磷合金工艺是一种常用的金属表面处理方法,具有较高的耐腐蚀性和耐磨性。
本文旨在综述相关的研究文献,深入探讨化学镀镍磷合金工艺的研究进展、工艺参数优化、合金特性及其应用领域。
正文内容:
1.工艺研究进展
1.1传统化学镀镍磷合金工艺
1.2改进型化学镀镍磷合金工艺
2.工艺参数优化
2.1镀液成分优化
2.2温度和镀液pH值优化
2.3电流密度和镀液搅拌速度优化
2.4镀液中添加剂优化
3.合金特性研究
3.1镀层结构和成分分析
3.2镀层显微硬度和耐磨性研究
3.3镀层的结晶性质和晶体生长机制
4.应用领域
4.1电子电镀应用
4.2汽车工业应用
4.3航空航天应用
4.4冶金工业应用
4.5其他领域应用
5.工艺优缺点及未来发展趋势
5.1工艺优点
5.2工艺缺点
5.3未来发展趋势
总结:
综合上述研究文献,化学镀镍磷合金工艺在金属表面处理中具有广泛的应用前景。
不论是传统工艺还是改进工艺,都可以通过优化工艺参数来提高镀层的性能。
相关的合金特性研究有助于深入了解镀层的显微硬度、耐磨性等性能指标。
不同领域都可以找到该工艺的应用,例如电子电镀、汽车工业和航空航天等。
该工艺也存在一些缺点,如镀层中可能含有杂质等。
未来的发展趋势应该在提高工艺的经济性、环境友好性和镀层性能方面进行进一步的研究与改进。
《Ni-Co-P合金脉冲镀工艺及性能研究》

《Ni-Co-P合金脉冲镀工艺及性能研究》一、引言随着现代工业的快速发展,对材料性能的要求越来越高。
Ni-Co-P合金因其优异的物理、化学及机械性能,被广泛应用于各种工业领域。
其中,Ni-Co-P合金的镀层技术,特别是脉冲镀工艺,对提高材料性能具有重要作用。
本文旨在研究Ni-Co-P合金的脉冲镀工艺及其性能,以期为实际应用提供理论支持。
二、Ni-Co-P合金脉冲镀工艺(一)材料准备本文选取纯度较高的镍、钴和磷作为原料,采用电镀法进行Ni-Co-P合金的制备。
在镀液中,需加入适量的添加剂以改善镀层的性能。
(二)脉冲镀工艺脉冲镀是一种电镀技术,通过在电镀过程中施加脉冲电流,使镀层具有更好的致密性和均匀性。
本文采用脉冲电流进行Ni-Co-P合金的电镀,并研究不同脉冲参数对镀层性能的影响。
(三)实验过程1. 配置镀液:按照一定比例将镍、钴、磷等原料溶解在去离子水中,加入添加剂后搅拌均匀。
2. 预处理:对基材进行除油、除锈等预处理,以提高镀层的附着力。
3. 脉冲电镀:将预处理后的基材浸入镀液中,施加脉冲电流进行电镀。
4. 后处理:电镀完成后,对镀层进行清洗、烘干等后处理。
三、性能研究(一)表面形貌分析采用扫描电子显微镜(SEM)对Ni-Co-P合金镀层的表面形貌进行观察,分析不同脉冲参数对镀层表面形貌的影响。
(二)硬度测试通过维氏硬度计对Ni-Co-P合金镀层的硬度进行测试,分析脉冲镀工艺对镀层硬度的影响。
(三)耐腐蚀性测试采用盐雾试验和电化学腐蚀试验等方法,对Ni-Co-P合金镀层的耐腐蚀性能进行测试。
通过对比不同脉冲参数下的耐腐蚀性能,分析脉冲镀工艺对耐腐蚀性的影响。
四、结果与讨论(一)表面形貌分析结果SEM结果显示,Ni-Co-P合金镀层具有致密、均匀的表面形貌。
不同脉冲参数下,镀层的表面形貌有所差异,适当调整脉冲参数可获得更优的表面形貌。
(二)硬度测试结果维氏硬度计测试结果表明,Ni-Co-P合金镀层具有较高的硬度。
化学镀镍磷镀层及其耐蚀性研究
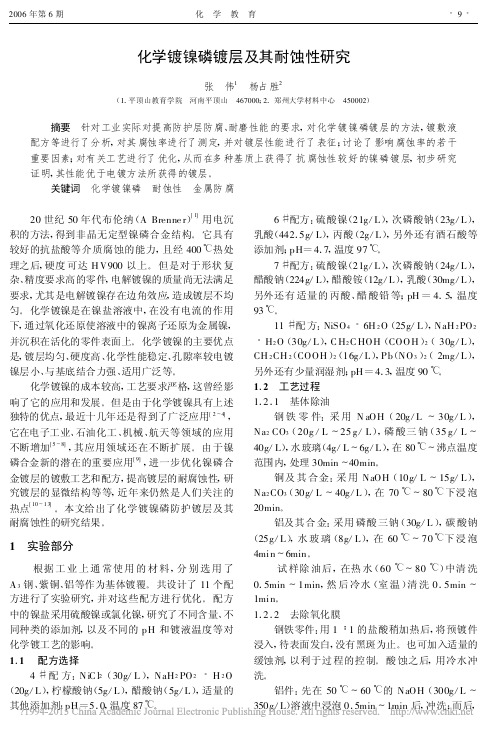
化学镀镍磷镀层及其耐蚀性研究张 伟1 杨占胜2(1.平顶山教育学院 河南平顶山 467000;2.郑州大学材料中心 450002) 摘要 针对工业实际对提高防护层防腐、耐磨性能的要求,对化学镀镍磷镀层的方法,镀敷液配方等进行了分析,对其腐蚀率进行了测定,并对镀层性能进行了表征;讨论了影响腐蚀率的若干重要因素;对有关工艺进行了优化,从而在多种基质上获得了抗腐蚀性较好的镍磷镀层,初步研究证明,其性能优于电镀方法所获得的镀层。
关键词 化学镀镍磷 耐蚀性 金属防腐 20世纪50年代布伦纳(A Brenne r)[1]用电沉积的方法,得到非晶无定型镍磷合金结构。
它具有较好的抗盐酸等介质腐蚀的能力,且经400℃热处理之后,硬度可达H V900以上。
但是对于形状复杂、精度要求高的零件,电解镀镍的质量尚无法满足要求,尤其是电解镀镍存在边角效应,造成镀层不均匀。
化学镀镍是在镍盐溶液中,在没有电流的作用下,通过氧化还原使溶液中的镍离子还原为金属镍,并沉积在活化的零件表面上。
化学镀镍的主要优点是,镀层均匀、硬度高、化学性能稳定、孔隙率较电镀镍层小、与基底结合力强、适用广泛等。
化学镀镍的成本较高,工艺要求严格,这曾经影响了它的应用和发展。
但是由于化学镀镍具有上述独特的优点,最近十几年还是得到了广泛应用[2~4],它在电子工业、石油化工、机械、航天等领域的应用不断增加[5~8],其应用领域还在不断扩展。
由于镍磷合金新的潜在的重要应用[9],进一步优化镍磷合金镀层的镀敷工艺和配方,提高镀层的耐腐蚀性,研究镀层的显微结构等等,近年来仍然是人们关注的热点[10~13]。
本文给出了化学镀镍磷防护镀层及其耐腐蚀性的研究结果。
1 实验部分 根据工业上通常使用的材料,分别选用了A3钢、紫铜、铝等作为基体镀覆。
共设计了11个配方进行了实验研究,并对这些配方进行优化。
配方中的镍盐采用硫酸镍或氯化镍,研究了不同含量、不同种类的添加剂,以及不同的pH和镀液温度等对化学镀工艺的影响。
化学镀镍磷合金过程中磷的析出及其对镀层性能的影响

化学镀镍磷合金过程中磷的析出及其对镀层性能的影响一、本文概述本文旨在深入探讨化学镀镍磷合金过程中磷的析出行为及其对镀层性能的影响。
化学镀镍磷合金作为一种重要的表面处理技术,广泛应用于电子、航空、汽车等领域,以提高材料的耐腐蚀性、耐磨性和电磁性能。
其中,磷的析出是影响镀层性能的关键因素之一。
因此,对磷析出行为的研究具有重要的理论和实践意义。
本文首先简要介绍了化学镀镍磷合金的基本原理和工艺过程,重点阐述了磷在镀层中的析出机制,包括磷的来源、析出条件以及析出动力学等方面。
随后,通过对比分析不同磷含量镀层的性能差异,探讨了磷析出对镀层耐腐蚀性、硬度、电导率等性能的影响规律。
在此基础上,本文还进一步分析了磷析出行为的影响因素,如镀液成分、温度、pH值等,以及这些因素如何调控磷的析出过程。
本文总结了磷析出行为对化学镀镍磷合金镀层性能的影响,并提出了优化镀层性能的策略和建议。
通过本文的研究,不仅有助于深入理解化学镀镍磷合金过程中的磷析出行为,还为实际生产中的工艺优化和性能提升提供了有益的理论指导和实践依据。
二、化学镀镍磷合金过程中磷的析出在化学镀镍磷合金的过程中,磷的析出是一个关键且复杂的化学反应过程。
这一过程中,磷元素从镀液中以一定的方式被还原并沉积到镍基体上,与镍元素共同形成镍磷合金镀层。
我们需要了解化学镀镍磷合金的基本原理。
在适当的条件下,镀液中的镍离子和磷离子通过还原剂的作用被还原成金属镍和磷,并在基体表面形成一层均匀的合金镀层。
这一过程涉及到多个化学反应步骤,包括还原剂的选择、反应条件的控制以及磷析出机制的研究。
在磷的析出过程中,反应动力学和热力学因素起着重要作用。
反应动力学影响磷的析出速率和分布,而热力学则决定了磷在镀层中的存在形式和稳定性。
镀液中的磷浓度、pH值、温度以及搅拌速度等因素也会对磷的析出产生显著影响。
磷的析出机制主要包括两种:一种是磷原子直接替代镍原子进入镍的晶格中,形成固溶体;另一种是磷原子聚集成磷颗粒,分布在镍基体上。
亚磷酸体系镍磷合金电镀工艺及影响镀层耐蚀性的主因素资料

亚磷酸体系镍磷合金电镀工艺及影响镀层耐蚀性的主因素[摘要]为了弄清影响亚磷酸体系电镀镍磷合金层耐蚀性能的主因素,用极差法分析了各工艺参数的影响,采用SEM/EDAX考察了镍磷镀层的形貌、成分,采用电化学测试考察了镀层的耐蚀性,测定了镀层与基体的结合强度,并确定了最佳工艺条件。
结果表明:亚磷酸含量是影响镀层耐蚀性的主要因素,在240 g/L硫酸镍,45 g/L 氯化镍,30 g/L硼酸,30 g/L亚磷酸,电流密度5 A/dm2,温度40℃条件下所得镀层均匀,耐蚀性和结合力好。
[关键词]电沉积;镍磷合金;亚磷酸体系;耐蚀性能;影响因素[中图分类号]TQ153.2[文献标识码]A[文章编号]1001-1560(2011)07-0064-030·前言镍磷合金镀层耐腐蚀、耐高温、耐磨,导电性和导磁性高,原料成本低,环保性能好,在汽车、航空航天、电子、通讯等行业得到了广泛应用。
获得镍磷合金镀层的主要途径包括化学镀和电镀。
其中在沉积速率、镀液稳定性、成本、最大厚度等诸多方面,电镀法具有化学镀法不具备的优点[1~7]。
目前,电镀镍磷合金工艺和性能的报道较化学镀少,进一步了解电镀工艺参数对镀层耐蚀性的影响对于扩大电镀镍磷的应用范围很有意义。
次磷酸盐体系镍磷合金电镀层质量不稳定,温度及电流稍有变化就容易引起镀层发黑[8,9]。
本工作采用电镀方法,在亚磷酸镍盐体系中获取了镍磷合金镀层;通过正交试验优选了可获得耐蚀性好的镀层的工艺参数,并探讨了各参数对镀层耐蚀性的影响。
1·试验1.1基材前处理以纯铜片为基材,尺寸10 mm×10 mm×1 mm,用环氧树脂封装,留出施镀的面积为1 cm2。
镀前处理流程:基材磨光→水洗→除油→水洗→酸洗→水洗。
用800号水砂纸打磨基材试样至平整光滑后除油。
除油60~100 g/L Na2CO3,5~10 g/L Na3PO4·12H2O,5~15 g/L Na2SiO3,1~3 g/L OP-10乳化剂,温度80~90℃,至将油除净为止。
磷元素对Ni-W-P镀层硬度和磨损性的影响

磷 元素对 N i — W— P镀 层 硬 度 和 磨 损 性 的 影 响
成 威, 廖秋 慧
2 0 1 6 0 0 ) ( 上 海 工程技 术 大 学 材料 工程 学院 , 上海
摘
要: 为研 究磷 的质量分数 大小对 N i . W— P镀层 的硬 度和磨损性 的影响 , 采 用化 学沉积 的方法制备 N i — W— P合金 镀层 。
第3 3卷 第 2期 2 0 1 5年 4月
轻 工 机械
Li e ,  ̄tI ndu s t r y M ae /  ̄ ne r y
V0 1 . 3 3 No . 2 Ap r . 2 01 5
[ 研究 ・ 设 计]
D O I : 1 0 . 3 9 6 9 / j . i s s n . 1 0 0 5 - 2 8 9 5 . 2 0 1 5 . 0 2 . 0 0 6
C HE N G We i . L I A 0 Q i u h u i
( S c h o o l o f Ma t e i r a l s E n g i n e e r i n g , S h a n g h a i U n i v e r s i t y o f E n g i n e e i r n g S c i e n c e , S h a n g h a i 2 0 1 6 0 0 , C h i n a )
c o n t e n t o f p h o s p h o us r e l e me n t c r u c i a l l y i l u f n e n c e t he h a r d n e s s ,a n d t h e ma i n or f m o f t h e we a r i s a d h e s i v e we r. a Ke y wo r d s: El e c t r o l e s s; Ni - W— P; he a t t r e a t me n t ; a b r a s i o n r e s i s t a n c e
电镀镍

摘要:对电沉积镍-磷合金的工艺与性能进行了综述,包括镀液成分、镀覆条件、阳极组成等工艺条件的研究现状,并介绍了合金镀层的物相结构、非晶态与晶态之间的转化和不同成分的镀层的硬度、耐磨性、耐蚀性及影响这些性质的因素。
引言当镀层中磷的质量分数超过8%时,镍-磷镀层是一种非晶态合金,具有高耐蚀、耐磨、可焊性、磁性屏蔽、高硬度、高强度、高导电性等优异的性能,已广泛应用于汽车、航空、计算机、电子、化工和石油等领域。
近年来,由于环保的要求,以其它镀层代替铬镀层的技术越来越受到重视。
镍-磷合金镀层经热处理后的硬度接近或超过硬铬镀层,并且电镀镍-磷合金镀层具有很多优点,在成本和性能方面代替硬铬镀层是可行的。
目前用于制备镍-磷合金的方法有化学镀和电镀两种,电镀法与化学镀法相比具有很多优点,例如沉积速度快、镀液工作温度相对较低、镀液稳定性高、可制得更厚的镀层、成本较低等。
本文综述了电镀镍-磷合金的研究进展。
1 镍-磷合金的制备工艺目前,用于制备镍-磷合金的电镀一般有氨基磺酸盐、次磷酸盐和亚磷酸盐体系。
总体来说,这些镀液通常是由镍源(硫酸镍、氯化镍、氨基磺酸镍等)、磷源(亚磷酸或次磷酸)、缓冲剂、络合剂及添加剂等组成。
1.1 镍源的影响研究表明,镀液中镍离子浓度低会导致沉积速度变慢,析氢严重。
随着镍离子浓度的增加,一般阴极电流效率会随之增高,镀层质量得到改善。
但镍离子浓度过高,镀层的沉积速度过快将导致镀层粗糙,镀层中磷的含量也会下降。
所以镀液中的镍离子要保持在一合适的浓度范围内。
对于不同的镍源,其阴离子也会对电镀产生影响。
BrennerA[1]的研究表明,硫酸镍的加入将有利于提高阴极电流效率。
余维平[2]等认为,硫酸根可能会在阴极还原,使镀层中夹杂少量硫。
1.2 磷源的影响次磷酸盐和亚磷酸是目前研究最多的两种磷源。
有研究认为以次磷酸为磷源的镀液制得的镀层有更好的光亮度[3],张春丽等[4]认为采用次磷酸为磷源的镀液有更高的镀速以及镀层硬度。
- 1、下载文档前请自行甄别文档内容的完整性,平台不提供额外的编辑、内容补充、找答案等附加服务。
- 2、"仅部分预览"的文档,不可在线预览部分如存在完整性等问题,可反馈申请退款(可完整预览的文档不适用该条件!)。
- 3、如文档侵犯您的权益,请联系客服反馈,我们会尽快为您处理(人工客服工作时间:9:00-18:30)。
亚磷酸体系镍磷合金电镀工艺及影响镀层耐蚀性的
主因素
[摘要]为了弄清影响亚磷酸体系电镀镍磷合金层耐蚀性能的主因素,用极差法分析了各工艺参数的影响,采用SEM/EDAX考察了镍磷镀层的形貌、成分,采用电化学测试考察了镀层的耐蚀性,测定了镀层与基体的结合强度,并确定了最佳工艺条件。
结果表明:亚磷酸含量是影响镀层耐蚀性的主要因素,在240 g/L硫酸镍,45 g/L 氯化镍,30 g/L硼酸,30 g/L亚磷酸,电流密度5 A/dm2,温度40℃条件下所得镀层均匀,耐蚀性和结合力好。
[关键词]电沉积;镍磷合金;亚磷酸体系;耐蚀性能;影响因素[中图分类号]TQ153.2[文献标识码]A[文章编号]1001-1560(2011)07-0064-03
0·前言
镍磷合金镀层耐腐蚀、耐高温、耐磨,导电性和导磁性高,原料成本低,环保性能好,在汽车、航空航天、电子、通讯等行业得到了广泛应用。
获得镍磷合金镀层的主要途径包括化学镀和电镀。
其中在沉积速率、镀液稳定性、成本、最大厚度等诸多方面,电镀法具有化学镀法不具备的优点[1~7]。
目前,电镀镍磷合金工艺和性能的报道较化学镀少,进一步了解电镀工艺参数对镀层耐蚀性的影响对于扩大电镀镍磷的应用范围很有意义。
次磷酸盐体系镍磷合金电镀层质量不稳定,温度及电流稍有变化就容易引起镀层发黑[8,9]。
本工作采用电镀方法,在亚磷酸
镍盐体系中获取了镍磷合金镀层;通过正交试验优选了可获得耐蚀性好的镀层的工艺参数,并探讨了各参数对镀层耐蚀性的影响。
1·试验
1.1基材前处理
以纯铜片为基材,尺寸10 mm×10 mm×1 mm,用环氧树脂封装,留出施镀的面积为1 cm2。
镀前处理流程:基材磨光→水洗→除油→水洗→酸洗→水洗。
用800号水砂纸打磨基材试样至平整光滑后除油。
除油60~100 g/L Na2CO3,5~10 g/L Na3PO4·12H2O,5~15 g/L Na2SiO3,1~3 g/L OP-10乳化剂,温度80~90℃,至将油除净为止。
酸洗10%H2SO4,室温,1 min。
1.2电镀Ni-P合金
以亚磷酸体系作为电镀液的基础配方,其镀液配方及工艺条件见表1。
镀液中亚磷酸含量对镀层的组成有较大影响,镀液温度、电流大小对沉积速率和镀层结构也有比较大的影响。
选取温度,亚磷酸含量,电流密度为试验的3个因素,采用L9(34)正交试验表进行试验(见表2)。
在做正交试验前,先准备好 9组样品(每组3个平行样品),每个电极电镀面积为1 cm2。
电镀后水洗、吹干。
1.3性能测试
(1)使用AUY220型电子天平(精度0.1 mg)称重,测定镀层的
沉积速率:
根据沉积速率数据,通过控制沉积时间获得近似相同厚度的样品,供电化学测试试验使用。
(2)按GB/T 5933-86测定结合力;利用加热法和划痕法试验评价电镀镍磷层与基体的结合力。
(3)镀层的电化学测试在CHI604C综合测试仪上进行:采用三电极体系,参比电极为饱和甘汞电极,辅助电极为铂电极,镀件为工作电极;腐蚀介质为3.5%NaCl溶液(用蒸馏水和分析纯NaCl配制)。
Tafel极化曲线测量时,扫描速度为0.5 mV/s;交流阻抗测量时,频率范围:1.0×(10-2~102)kHz。
(4)用附带能谱仪的HITACHI-S-3400N扫描电镜对样品的表面形貌和成分进行分析。
2·结果与讨论
2.1正交试验结果
9组试样的腐蚀电流密度及交流阻抗数据见表3。
就各因素对腐蚀电流的影响进行极差分析,见表4。
由表4可知,各因素对腐蚀电流这一指标的影响顺序为亚磷酸含量>电流密度>温度,由极差分析得到最佳工艺条件:240 g/L硫酸镍,45 g/L氯化镍,30 g/L硼酸,0.05~0.10 g/L十二烷基硫酸钠,30 g /L亚磷酸,温度40℃,电流密度5 A/dm2。
图1为正交试验9组试样在3.5%NaCl溶液中的极化曲线。
图2为正交试验9组试样在3.5%NaCl溶液中的Nyquist谱和Bode谱,Bode谱测得的低频部分的交流阻抗值也列在表3中,其数值越大,
表明镀层的耐蚀性较好,这和腐蚀电流评价耐蚀性有很好的一致性,即对应样品的腐蚀电流也较小。
2.2镀层的耐蚀性
影响镀层耐蚀性的主要因素是亚磷酸的含量,而镀层中磷含量与亚磷酸有关,一般随亚磷酸含量增加而提高[8]。
试样3,6,9亚磷酸的含量均为30 g/L,其腐蚀电流均较低,并且阳极极化曲线部分具有明显的钝化区间,且钝化电流密度也较小。
从图2a也明显看到:此3种试样都具有较大的容抗弧;在Bode谱(图2b)中,低频下测量初期的交流阻抗值与镍磷镀层表面钝化膜层的耐蚀性密切相关,与腐蚀电流密度的关系具有较好的一致性。
试样3的腐蚀电流密度最
小,交流阻抗值最大,其耐蚀性也最好。
而温度和电流密度对耐蚀性影响较小,随着温度升高和电流密度减小,腐蚀电流略有提高。
由图2可发现:不同亚磷酸含量所得镍磷镀层的电化学阻抗谱非常类似,且温度相同时,随着亚磷酸含量的增加,镀层电化学阻抗逐渐升高;试样4,5,7,8低频部分基本上都出现实部收缩现象,表明低频部分有感抗成分,其原因是镍磷合金为自钝化金属,表面为钝化膜所覆盖,当溶液中存在引起局部破坏的活性Cl-时,发生孔蚀,当孔蚀处于诱导期时,阻抗平面上的低频区即出现了明显的感抗。
这种低频的感抗弧随着时间的延长逐渐萎缩,当真正的蚀孔出现时,感抗完全消失[6];试样在3.5%NaCl溶液中的腐蚀过程在Nyquist 谱上出现了明显的容抗弧,表明该电极过程主要由电子转移步骤控制,容抗弧的大小反映了反应电阻的大小,这和腐蚀电流测试结果一致,也和低频部分的Bode谱的阻抗测试结果一致。
2.3镀层的外观及结合力
划痕法和热震法测试结果,镀层均不剥落,说明镀层与基体的结合力良好。
2.4镀层的形貌及组成
最佳工艺获得的镀层表观细致、光亮,其表面SEM形貌和能谱见图3。
由图3可见,镀层呈现较为细致的胞状结构,没有明显的缺陷;镍磷合金镀层中P含量质量分数为14.81%,属于高磷镀层。
Ni-P合金镀层的耐蚀机理与表面磷化钝化膜的生成和溶解有关[6]。
3·结论
(1)本工艺中对镀层耐蚀性的影响因素主次顺序:亚磷酸含量>电流密度>温度。
(2)亚磷酸体系电镀镍磷合金最佳工艺条件:240g/L硫酸镍,45 g /L氯化镍,30 g/L亚磷酸,30 g/L硼酸,0.05~0.10 g/L 十二烷基硫酸钠,温度40℃,电流密度5 A/dm2。
该工艺下所得镀层均匀,耐蚀性及其与基体的结合力良好。