基于EDEM数值模拟的搅拌叶片优化设计
基于SolidWorks的搅拌器结构优化设计

基于SolidWorks的搅拌器结构优化设计预览说明:预览图片所展示的格式为文档的源格式展示,下载源文件没有水印,内容可编辑和复制基于SolidWorks的搅拌器结构优化设计搅拌器的设计一直采用经验设计方法,本文通过SolidWorks对其进行了建模和参数化设计,并运用Simulation仿真分析功能对其所建立的模型进行了有限元分析。
最后通过SolidWorks的优化功能对半搅拌器模型进行了优化设计,得到了搅拌板的最优厚度。
该方法为半搅拌器结构分析和优化设计提供了一种新思路。
全自动液压制砖机简称液压砖机,液压制砖机是采用液压动力制砖的免烧砖机。
蒸压粉煤灰砖是以粉煤灰、石灰或水泥为主要原料,掺加适量石膏、外加剂、颜料和集料等,经坯料制备、坯体成型和高压蒸汽养护等工序制成的实心粉煤灰砖。
蒸压粉煤灰砖是国家建设部推荐的新型墙体材料品种之一。
搅拌器是全自动液压制砖机布料的主要工作装置,其主要功能是保证粉煤灰混合料均匀性的前提下,当粉煤灰混合料从上料斗落到下料斗时,在振动装置和下料斗内搅拌器共同作用下,使粉煤灰混合料在下料斗内均匀分布,在布料小车的运动过程中,行走到制砖模具上方时,使其均匀落到模具模腔内,让每个砖腔都有足够的料,才能保证各块砖重量一致。
搅拌器结构如图1所示,由两个半搅拌器组成一个搅拌器,下料斗内有两个搅拌器,当粉煤灰混合料从上料斗落入下料斗时,两个搅拌器相互运动,同时振动机构使下料斗做往复运动,让物料在下料斗内均匀分布。
实际粉煤灰砖生产中发现,搅拌器在工作过程中,搅拌板向外侧弯曲。
分析认为,搅拌器轴带动搅拌器做旋转运动,搅拌粉煤灰混合料,并使其分布均匀,粉煤灰混合料高度高于搅拌器,也就是说,搅拌器整个埋在粉煤灰混合料里,在搅拌的过程中,不断与粉煤灰混合料相摩擦。
可能由于搅拌器结构强度不够,使得搅拌器的搅拌板产生弯曲。
图1 搅拌器结构图本文以全自动液压制砖机搅拌器为例,基于SolidWorks产品设计平台,对搅拌器进行仿真设计和优化设计,通过分析结果和优化方案,缩短设计周期,增加产品的可靠性,降低材料消耗和成本;并模拟各种试验方案,提前发现潜在的问题,减少试验时间和生产经费。
混流泵叶轮流动性能数值模拟和叶型优化设计

v re e n l fo s p r t n a e r mo e n h a s g o e n e st n n u n i g r n e o x s a d wall w e a a i s c n b e v d a d t e p sa e v r x i tn iy a d if e cn a g t o t l
La nn 10 4 hn ) io ig l6 2 ,C ia
Ab ta t s r c :A u rc lc lu a in wa a re utt i l t h e — i nso a u b l n o i i h n me i a ac l to s c rid o o smu ae tr e d me in lt r u e tf w n a h g l
/ 排灌机械工程学报
I o r a fDr i a e a d lr g to a h n r n i e rn J u n lo a n g n r i a i n M c i e y E g n e i g
_. N _ I1 第 _ 2 4I 、 o- 卷 .■ 8 4
弯曲度 可以有 效控 制叶 片进 1处 的马蹄 涡 , 除近壁 面流 动分 离和 漩涡 , 小流动 中的通 道 涡强 7 : 消 减 度和 影响 范 围 , 改进后 叶轮 流道 内存在 的 涡 团和 流动 脱 离现 象基本 消失 , 叶轮 水 力效率相 对提 高
47 % , .4 单位 功耗 的扬 程 增加 1 .% . 5 叶轮 性能 参数 的计 算数 据 与试 验数 据 吻合 较 好 , 1 验证 了所 采 用的计 算方 法及模 型 的 准确性 和 可靠性 .
关键 词 :混 流泵 ;叶轮 ;数值模 拟 ;叶型优 化 ; 能 性
基于CFD仿真的风力发电机组叶片优化设计

基于CFD仿真的风力发电机组叶片优化设计随着对可再生能源需求的增加,风力发电在现代能源产业中占据着重要地位。
而风力发电机组的叶片作为转动能量的主要组成部分,其设计对于风力发电效率的提高至关重要。
因此,基于CFD (Computational Fluid Dynamics,计算流体动力学)仿真的风力发电机组叶片优化设计成为了当前研究和工程实践的热点之一。
1.概述风力发电机组通过将风能转化为机械能,再经由发电机转化为电能的过程,实现了清洁、可再生能源的利用。
在风力发电机组中,叶片作为风能转化的关键组件,其设计直接影响到发电机组的发电效率和性能。
优化叶片设计可以有效提高风能的转化效率,增加风力发电机组的发电量。
2.风力发电机组叶片设计的挑战风力发电机组叶片设计面临诸多挑战。
首先,由于风能是不稳定的,叶片需要具备良好的自适应能力以适应不同条件下的风能变化。
其次,由于风力发电机组的结构复杂、工作环境恶劣,叶片需要具备较高的强度和耐久性。
同时,为了提高叶片的发电效率,叶片的气动特性也需要得到充分的考虑。
3.CFD在叶片设计中的应用CFD是一种基于数值方法的仿真技术,通过对流动领域中各项物理方程的求解,可以较为准确地预测流场的分布和特性。
在风力发电机组叶片优化设计中,CFD技术的应用可以快速、有效地评估不同叶片设计方案的性能,并指导优化设计过程。
首先,利用CFD技术可以对叶片在不同风速下的气动特性进行模拟和分析。
通过计算流场中的风速、压力等参数,可以获得叶片的气动力,并对叶片设计进行评估和调整。
其次,CFD技术还可以模拟叶片与周围环境的相互作用。
在风力发电机组叶片设计中,考虑叶片与塔筒、浆轮等部件的相互作用对于提高效率和减少振动非常重要。
通过CFD仿真,可以定量分析叶片与周围环境的相互影响,并针对性地进行叶片结构和布置的优化设计。
最后,CFD技术还可以辅助优化叶片的材料选择和制造工艺。
通过模拟和分析叶片在不同材料和工艺条件下的性能,可以选择最佳的材料和工艺参数,提高叶片的强度和耐久性。
基于流固耦合的搅拌桨叶数值模拟研究

基于流固耦合的搅拌桨叶数值模拟研究
陈福华;张晨阳;张雷;刘庆钊;孟令璋;韦嘉明
【期刊名称】《机械工程师》
【年(卷),期】2024()5
【摘要】为探究三角形桨叶、格子式桨叶、八字形桨叶在不同工况时的性能,基于ANSYS Workbench平台,采用k─ε标准流场模型,对不同水流冲击和不同转速的3种桨叶进行流固耦合数值模拟研究。
仿真结果表明,格子式桨叶性能和结构稳定性最差,相同工况其变形和应力最大,随着工况的变化变形与应力的大小变化最为明显;八字形桨叶性能和结构稳定性最好,载荷冲击下其变形和应力最小,随着工况的变化变形和应力的大小变化最小;桨叶转速对变形和应力的影响比水流速明显,转速越高则变形和应力越大;高变形区域发生在桨叶边缘,高应力区域则发生在桨叶中心旋转轴及其附近。
研究结果为卧式搅拌设备桨叶选型与优化设计提供理论依据。
【总页数】5页(P66-70)
【作者】陈福华;张晨阳;张雷;刘庆钊;孟令璋;韦嘉明
【作者单位】天津商业大学机械工程学院;天津大学化工学院
【正文语种】中文
【中图分类】U661.1
【相关文献】
1.基于流固耦合效应的岩层渗透系数演化规律与断层活化突水数值模拟研究
2.基于流固耦合的钢筋混凝土板抗爆性的数值模拟研究
3.基于流-热-固耦合的水冷壁应力
场数值模拟研究4.基于流固耦合的煤系气排采数值模拟研究5.基于流固耦合的立式轴流泵站振动特性数值模拟研究
因版权原因,仅展示原文概要,查看原文内容请购买。
重型燃机叶片锻造过程数值模拟与工艺优化

重型燃机叶片锻造过程数值模拟与工艺优化传统的叶片制造方法主要采用铸造或切削加工,但这样会造成叶片的形状、内部结构和物理性质方面的不均匀性,从而限制了燃机的性能和寿命。
为了克服这些问题,人们开始采用锻造工艺生产叶片,以确保叶片的均匀性和一致性。
本文主要研究了重型燃机叶片的锻造工艺过程与质量控制,采用数值模拟方法,优化了叶片的锻造工艺,提高了叶片的性能和寿命。
具体如下:1. 叶片材料的选择叶片一般采用高温合金材料,如铸造合金、钴基合金等。
这些材料具有高温强度、耐热疲劳和抗腐蚀性等优点,但材料价格昂贵,对工艺要求较高。
2. 叶片锻造的工艺流程重型燃机叶片的锻造工艺主要分为以下几个步骤:① 预加热:在锻造前,将叶片材料加热到适当的温度,以提高其塑性和可锻性。
② 下料:根据叶片的图纸,将材料切割成合适大小的坯料,以便进行下一步的模具成型。
③ 模具成型:将坯料放入模具中,通过锤击或压力使其变形成为叶片的形状。
此过程需要考虑叶片的内部结构、空心率、表面光洁度等因素。
④ 热处理:将锻造后的叶片进行高温处理,以消除内部应力,并改善其力学性能和寿命。
⑤ 表面处理:对锻造后的叶片进行表面处理,以增加其耐磨性和防腐蚀性。
1. 模型建立与网格划分本研究采用了有限元方法建立了叶片的三维模型,并通过网格划分,将叶片分为不同的单元,以便进行数值模拟计算。
2. 材料力学性能模型这里使用的是工程模型,基于人们对材料的逐步认识而不断发展的热塑性塑性本构模型。
膜式流变表达式,考虑到铸造/锻造过程的高应变率,被选择且较合理。
这个模型主要用于模拟材料在高温和强应变下的变形和塑性行为。
3. 数值模拟求解和结果分析模拟过程中采用了ABAQUS软件,首先对叶片的锻造过程进行了模拟,对叶片在锻造过程中的变形、应力和应变等参数进行了分析,从而确定了叶片锻造的最佳工艺流程。
通过数值模拟,我们获得了更准确的叶片变形和力学性能数据,有利于优化设备和工艺流程。
混流泵叶片优化设计
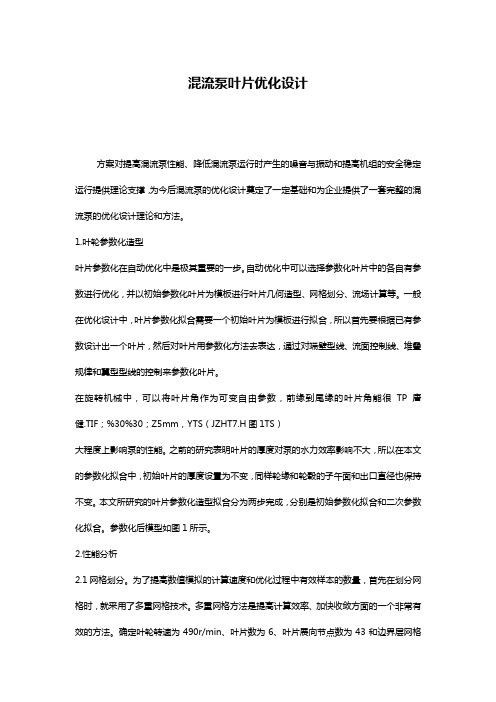
混流泵叶片优化设计方案对提高混流泵性能、降低混流泵运行时产生的噪音与振动和提高机组的安全稳定运行提供理论支撑,为今后混流泵的优化设计奠定了一定基础和为企业提供了一套完整的混流泵的优化设计理论和方法。
1.叶轮参数化造型叶片参数化在自动优化中是极其重要的一步。
自动优化中可以选择参数化叶片中的各自有参数进行优化,并以初始参数化叶片为模板进行叶片几何造型、网格划分、流场计算等。
一般在优化设计中,叶片参数化拟合需要一个初始叶片为模板进行拟合,所以首先要根据已有参数设计出一个叶片,然后对叶片用参数化方法去表达,通过对端壁型线、流面控制线、堆叠规律和翼型型线的控制来参数化叶片。
在旋转机械中,可以将叶片角作为可变自由参数,前缘到尾缘的叶片角能很TP唐健.TIF;%30%30;Z5mm,YTS(JZHT7.H图1TS)大程度上影响泵的性能。
之前的研究表明叶片的厚度对泵的水力效率影响不大,所以在本文的参数化拟合中,初始叶片的厚度设置为不变,同样轮缘和轮毂的子午面和出口直径也保持不变。
本文所研究的叶片参数化造型拟合分为两步完成,分别是初始参数化拟合和二次参数化拟合。
参数化后模型如图1所示。
2.性能分析2.1网格划分。
为了提高数值模拟的计算速度和优化过程中有效样本的数量,首先在划分网格时,就采用了多重网格技术。
多重网格方法是提高计算效率、加快收敛方面的一个非常有效的方法。
确定叶轮转速为490r/min、叶片数为6、叶片展向节点数为43和边界层网格单元大小,完成网格的制作,划分得到的叶片网格数为607469。
2.2边界条件设定。
边界条件是指流体在运动或静止的边界条件上给予的确定性条件,所以边界条件的参数直接影响了求解过程和得到的结果。
对导叶式混流泵进行数值模拟,流体介质为清水,密度为997kg/m3,边界条件设置如下:(1)进口边界条件:静态温度为293K,湍流粘度为1e-6m2/s,叶轮进口采用速度进口,速度方向垂直于叶轮进口。
基于数值模拟的汽轮机叶片锻模设计

高质量 1016 mm 大叶片。 另外,利用 CAE 软件模拟 的结果远比利用经验值更科学, 可以次去优选模具 结构和毛坯。 Bariani[2]将物理模拟和数值模拟技术 有效应用到不锈钢叶片热锻工艺设计过程, 取得理 想的效果。国内也有许多学者进行了这方面的研究, 文 献 [3-7] 利 用 数 值 模 拟 技 术 分 别 对 叶 片 成 形 过 程 、 叶片锻造余量选择、坯料形状尺寸选择进行了研究。 本 文 拟 提 出 一 个 基 于 Deform-3D 模 拟 的 汽 轮 机 叶 片锻造工艺和模具设计方法, 以求对一般锻件锻造 工艺和模具设计具有普遍参考意义。
及设计具有一定参考价值
关键词: 锻造模具设计;数值模拟;优化设计;锻造工艺
中 图 分 类 号 :TG315.2
文 献 标 识 码 :A
文 章 编 号 :1001-3814(2011)21-0194-04
Design of Turbine Blade Forging Die Based on Numerical Simulation
叶片锻模自动设计系统
只要输入必要的参数, 如图
4 所示, 系统利用内置专家
系统自动确定截面修型、工
艺余面加放等, 自动生成叶
片的锻模及其锻坯, 如图 5
所示。
3 实例分析
3.1 锻件坯料类型选择
图 4 叶片模具自动 设计参数输入
Fig.4 Parameters input of blade die in automated
求,内、背弧面保留完整流线,分型飞边选择在进、出 汽边位置。最后通过余量加放及工艺余面、飞边体设 计,就可以形成锻件截面。对叶根叶冠加放加工余量 后和锻件叶身连接, 考虑飞边过渡的需要加工艺余 块,合并实体生成锻件实体。经冷热转换生成热锻件 实体。 拉飞边体,设计桥部和仓部。 选择模座模块, 经布尔运算即可生成上、下模具。根据叶片锻件设计 选择锻坯, 确定锻坯在模具中的定位, 设计定位结 构。 这样就完成了叶片模锻模具的设计。 这个过程 在我们开发的叶片模具 CAD 系统中已经实现了自 动化。
叶片泵设计数值模拟基础与应用

叶片泵设计数值模拟基础与应用叶片泵是一种常见的离心泵,其结构简单、工作可靠,被广泛应用于各种行业中。
而泵的设计过程中需要依靠数值模拟来对其性能进行预测和优化。
叶片泵的设计数值模拟基础主要包括流场模拟、网格划分、流体模型、边界条件等。
流场模拟是泵设计的基础,它通过数值计算得到叶轮和泵腔内的流场状态,以便分析泵的性能和进行优化。
网格划分是模拟过程中的重要环节,其决定了计算精度和计算速度。
合理的网格划分可以使模拟结果更加准确,同时也可以缩短计算所需的时间。
流体模型是指将流体看作连续介质,采用一定的宏观理论和微观数学描述其运动规律的方法。
流体模型的选择取决于流体种类和运动状态,例如,真实流体可以采用雷诺平均应力模型,而高速稀薄气体可以采用理想气体模型。
边界条件是指对流场进行约束的条件,包括进口边界条件,出口边界条件,墙面边界条件等。
合理的边界条件可以保证数值模拟的可靠性和准确性。
泵的设计数值模拟应用主要包括流量、压力、效率、扬程等性能参数的预测与优化。
其中,最主要的是效率的预测和优化。
泵的效率是泵性能的重要指标,它直接影响到能源的消耗和泵的使用寿命。
因此,泵的设计数值模拟应该从提高泵的效率入手,同时也要合理控制泵的流量、压力等参数,保证泵的正常工作。
在实际应用中,泵的设计数值模拟可用于方案比较、优化设计、工艺分析等。
例如,在对泵进行微调或者更换关键零部件的情况下,可以通过数值模拟来预测泵的性能变化,并进行优化设计。
此外,泵在实际使用中还需要面对不同的工况,因此数值模拟也可以用于分析泵在不同工况下的性能,以便优化泵的设计和使用。
总之,叶片泵的设计数值模拟是一项重要的任务,它可以帮助工程师和科研人员更加深入地了解泵的运作原理和性能特点,并进行优化设计和工艺分析。
在今后的应用中,泵的设计数值模拟还将发挥越来越重要的作用,以提高泵的效率和性能,并适应不同领域的需求。
- 1、下载文档前请自行甄别文档内容的完整性,平台不提供额外的编辑、内容补充、找答案等附加服务。
- 2、"仅部分预览"的文档,不可在线预览部分如存在完整性等问题,可反馈申请退款(可完整预览的文档不适用该条件!)。
- 3、如文档侵犯您的权益,请联系客服反馈,我们会尽快为您处理(人工客服工作时间:9:00-18:30)。
基于EDEM 数值模拟的搅拌叶片优化设计聂超超1,韩振南1,赵远1,2,刘邱祖1(1.太原理工大学机械工程学院,山西太原030024;2.山西天地煤机装备有限公司,山西太原030006)来稿日期:2018-10-27基金项目:山西省基础研究计划项目(2015011061)作者简介:聂超超,(1991-),男,河南人,硕士研究生,主要研究方向:混凝土搅拌问题研究;韩振南,(1958-),男,山西壶关人,博士生导师,教授,主要研究方向:车辆故障诊断1引言混凝土作为建筑及工程所需基本材料用量巨大,搅拌机作为生产混凝土所必须的装备,其性能对工程建设质量和效率有着重要的影响。
双卧轴强制式搅拌机是目前搅拌设备中的主要机型,但由于该设备搅拌轴附近物料得不到搅拌,形成了搅拌低效区。
而且由于低效区内物料流动性差,物料容易与搅拌轴粘附,产生抱轴现象,造成搅拌质量和效率的低下[1-2]。
众多学者专家对此问题进行了研究。
文献[3]研究设计了双排叶片结构,分析了其搅拌机理,并对其合理参数进行了确定和匹配,通过样机实验证明该结构可以有效改良搅拌低效区。
文献[4]设计了双螺旋轴搅拌机,其特殊的“无轴”结构和内螺旋叶片的存在,使螺旋轴中心附近物料的运动得到了加强,减弱了混凝土抱轴结块和搅拌低效区现象。
文献[5]对双螺旋轴搅拌机的搅拌筒长宽比、螺旋轴螺旋形式、螺旋轴螺旋升角等参数进行了优化,提高了搅拌性能和效率。
文献[6]设计了双卧轴振动搅拌机,在筒侧安装振动电机,增强了物料在宏观上的对流剪切运动和微观上的扩散运动,改善了低效区。
但该结构需要在搅拌筒一侧安装振动电机,使搅拌功率和成本过度增加。
重点研究分析了双卧轴搅拌机的低效区问题,在普通双卧轴摘要:为了解决双卧轴搅拌机的搅拌低效区问题,可旋转搅拌臂与叶片重合,利用搅拌臂来搅拌低效区物料,增强其物料流动性。
通过对建立的单搅拌叶片模型进行非线性规划计算,得出其叶片最优参数。
为证明该优化结构的准确性,同时建立普通叶片、双排叶片与该优化叶片进行对比,将三种叶片分别装配在同一搅拌筒内导入EDEM 模拟搅拌过程。
颗粒接触模型采用为Hertz-Mindlin with JKR Cohesion ,相关参数通过塌落度数值模拟进行校核。
结果发现新型叶片可增大低效区物料速度,改善低效区物料流动性;两轴速度差较小,筒端物料堆积较少从而使物料运转更流畅;可从宏观上增加物料剪切对流运动,微观上增大颗粒动能,使颗粒碰撞更剧烈,物料能够快速达到均匀状态,提高整盘物料搅拌效率。
关键词:低效区;优化设计;EDEM 数值模拟;JKR 接触模型;搅拌效率中图分类号:TH16;TU642+.2文献标识码:A文章编号:1001-3997(2019)04-0017-04Optimal Design of Mixing Blade Based on EDEM Numerical SimulationNIE Chao-chao 1,HAN Zhen-nan 1,ZHAO Yuan 1,2,LIU Qiu-zu 1(1.School of Mechanical Engineering ,Taiyuan University of Technology ,Shanxi Taiyuan 030024,China ;2.Shanxi Tiandi Coal Machine Equipment Co.,Ltd.,Shanxi Taiyuan 030006,China )粤遭泽贼则葬糟贼:In order to solve the problem of inefficient zone of twin shaft mixer ,themixing arm can be rotated to coincide with the blade to participate in the stirring inefficient material and enhance the material flow.The optimal parameters of the blade were obtained by nonlinear programming of the established single mixed blade model.To prove the accuracy of the optimized structure ,the ordinary blade and double row blade were build to compared with the optimized blade.And the three blade were assembled in the same mixing barrel to imported into EDEM to simulate the mixing process.Particle contact model wasadopted as Hertz-Mindlin with JKR Cohesion ,and the relevant parameters were checked by slump simulation.The results showed that the new blade can effectively increase the velocity of the material in the inefficient area and improve the material flow in the inefficient zone.The two axisvelocity difference is smaller ,and the cylinder end of the material accumulation is less so that the material running smoothly.The new blade can increase the material convection shear movement from the macroscopic view and the particle kinetic energy from the microscopic view to the collision of particles more intense.The material can reach a uniform state quickly so that improve the whole plate material the mixing efficiency.Key Words :Inefficient Zone ;Optimal Design ;EDEM Numerical Simulation ;JKR Cohesion ;Mixing EfficiencyMachinery Design &Manufacture机械设计与制造第4期2019年4月17搅拌机的基础上,将原本与搅拌轴垂直的搅拌臂旋转至与叶片重合,利用搅拌臂来搅拌低效区物料,增强低效区内物料的流动性,并利用离散元分析软件EDEM模拟其搅拌过程,验证了其确实可以达到改善低效区,提高搅拌效率的目的,对今后搅拌叶片的优化设计具有一定的指导意义。
2双卧轴搅拌低效区分析在双卧轴搅拌筒内,装在两根轴上的搅拌叶片将物料刮向拌筒的中央主搅拌区内。
位于叶片下端到搅拌轴的半圆形区域内的物料却无法受到叶片的直接搅拌,只能够靠物料间摩擦挤压及粘滞阻力来带动,这些作用力从叶片下端至搅拌轴逐渐减弱,物料的线速度也逐渐降低,流动性变得愈差,形成了搅拌低效区。
随着搅拌机容量的增大,低效区现象愈严重,严重影响搅拌效率和质量。
V max中央主搅拌区低效区低效区图1双卧轴搅拌机低效区示意图Fig.1Schematic Diagram of Twin Shaft Mixer Inefficient Zone 3叶片优化过程3.1叶片结构初步改进双卧轴搅拌机普通叶片的搅拌臂原本与搅拌轴垂直,轴附近的物料得不到搅拌,因此形成了搅拌低效区。
为了改善低效区问题,笔者经研究发现可将搅拌臂旋转至与搅拌叶片重合,如图2所示。
利用搅拌臂来搅拌低效区物料,促使其产生强烈的剪切对流运动,提高搅拌效率。
图2叶片对比Fig.2Comparison of Blades3.2叶片参数优化新型叶片的搅拌臂参与物料搅拌,搅拌面积势必增大。
然而只有在叶片的搅拌面积、个数和拌筒容积利用系数之间匹配合理时,才能保证既推动一定比例的物料,又留有必需的空间使物料流畅地运动,达到拌和快、又节能的目的。
为了评判设计的准确性,并为参数选择时提供参考,根据文献[7],可用指标ψ来进行综合评判,ψ表示搅拌轴转动1周时,叶片推动的物料量Q与出料容积V1之间的比值,即:ψ=Q/V1(1)当ψ值为(1.05~1.10)时,说明叶片面积,数量和容积利用系数三者匹配较为合理。
新型叶片几何模型,如图3所示。
因叶片与衬板的间隙非常小,可忽略不计,叶片高度可近似等于拌筒半径R,设叶片长度为w,宽度为b,搅拌臂底边长度为L,底角为β,叶片与搅拌臂连接处宽度为L′,叶片总面积为S,则:S=wb+L(R-b)-((R-b))2/2tanβ(2)wLβL′图3新型叶片Fig.3New Blade叶片安装角为α,设叶片由刚开始推料到从物料中转出来,如图4所示。
搅拌轴需要转过的角度为θ,即图1中央主搅拌区的顶角,叶片转动1周,所推动的物料量p等于叶片在x-y面投影面积绕搅拌轴转动θ后排出的体积。
xyzOX′yxw cosαL cosαβα图4叶片在x-y平面的投影Fig.4Projection of Blade in X-Y Planep=π[R2-(R-b)2]w cosα+π(R-b)2L cosα-π(R-b)3cosα3tanβ⎧⎩⏐⏐⏐⏐⎨⏐⏐⏐⏐⎫⎭⏐⏐⏐⏐⎬⏐⏐⏐⏐θ2π(3)化简为:p=wb(2R-b)+(R-b)2-(R-b)33tanβ[]θcosα2(4)搅拌轴搅拌1周,所有叶片推动的物料总量Q(单位:m3)为:Q=4p0+10p1(5)式中:p0—单个侧叶片推动物料量;p1—单个主叶片推动物料量。
设进料容积为V2,搅拌筒几何容积为V3,出料系数为δ,容积利用系数为γ:γ=V2/V3(6)δ=V1/V2(7)则出料容积:V1=δγV3(8)根据相关技术参数,一般为(0.60~0.70),可取为0.65,当搅拌筒为宽短型,γ为0.25时,θ为125°,V3(单位:m3)可由模型测量得到。