轴流压气机叶片优化设计_伊卫林
轴流压气机多叶片排的气动优化设计

收稿日期:2005-03-03; 修订日期:2005-08-08作者简介:尉 涵(1979-),女,山西永济人,清华大学硕士研究生.文章编号:1001-2060(2005)06-0603-04轴流压气机多叶片排的气动优化设计尉 涵,袁 新(清华大学热能工程系,北京100084)摘 要:对某多级轴流压气机前三排叶片径向积叠方案进行了气动优化。
该方案以商用软件iSIGHT作为平台,利用试验设计方法对整个搜索空间进行初步探索,采用逐次序列二次规划算法进行局部寻优,利用商业软件NUMECA进行粘性流场数值评估。
对压气机全工况性能的计算表明,在流量和压比不减少的情况下,优化后的叶型设计工况和非设计工况性能均得到了改善。
关键词:轴流压气机;叶片;DOE;SQP;优化中图分类号:TK263.3 文献标识码:A1 引 言为了提高燃气轮机气动效率、做功能力以及扩大稳定工作范围,要求压气机具有更高的压比和效率。
这就需要不断提高压气机叶型的设计水平,研究压气机新叶型成型技术,以满足压气机气动设计的需要。
随着计算技术的飞速发展,应用计算流体动力学(CFD)已经可以深刻了解、分析流体机械内部的流动状况。
在使用C FD方法对流体机械内部流场进行数值模拟的基础上,人们提出数值设计方法,将数值优化技术与正问题流场计算相结合,由数学过程替代设计人员经验来控制设计参数的修改方向,就构成了叶型气动优化设计方法[1~3]。
一个完整的气动优化设计系统通常包括3个部分:参数化造型系统、评价系统和优化策略。
参数化造型是优化设计系统的基础,需要对优化的对象(即叶轮机械的通流部分)进行建模,并且为优化设计提供设计变量;评价系统的任务是通过某种方法对设计方案的性能做出评估,目前通常是由CFD方法精确求解正问题,获得通流部分的流场数据;优化策略的作用是用尽可能少的计算时间,找到最优的设计方案。
叶轮机械的设计问题即围绕这3个部分进行展开。
2 叶片参数化造型技术叶轮机械叶片弯扭联合设计是现代动力机械行业常用的叶片造型方法[4],它通过叶片的弯曲、扭转来控制叶片积叠线的形状。
高负荷跨音速轴流压气机的叶型优化设计

能。
压气机的全三维数值优化技 术集三维 流场求解 、 优化 技
术 为 一 体 , 过 对 原 型 机 进 行 参 数 化 而 扰 动 几 何 构 型 , 从 通 以
中寻优。 目前较常用 的方法是结合神 经网络 ( 响应面模 型的
一
种) 与遗传算法 的优 化方法。众多国外学者 已在该领域 进
第2 卷 第7 9 期
文 章 编 号 :06 94 (0 2 0 - 0 5 0 1 0 - 3 8 2 1 )7 07 - 5
计
算
机
仿
真
21年7 02 月
荷 跨 音 速 轴 流压 气 机 的 叶型 优 化 设 计
李相 君 , 武利 , 皓光 , 楚 张 米 攀
( 西北工业大学 动力与 能源学 院, 陕西 西安 7 07 102)
定 范 围 内扰 动 , 可 以 得 到 一 系 列 新 的 叶 型 , 就 以此 构 建 叶 型
面处则使用 周向平 均法进 行数 值传 递。计算 区域 包括进 口
导 叶、 转子及静子 排 。另外 为提 高计 算效 率 , 采用 了多重 网
格 法 、 部 时 间 步 长 和 隐 式 残 差 光 顺 三 种 措 施 加 速 计 算 收 局
一
7 — 5
表 1 计 算 网格 数 量分 布
轴流式涡轮增压器涡轮叶片的优化设计

采用 iSIGHT 提供的 多 岛 遗 传 算 法 (multi2island genetic algorithm , MIGA) 及 二 次 序 列 规 划 法 (sequential quadratic programming ,SQP) 相结合 , 先对 求解域进行全局寻优 ,再进行局部深层次寻优 ,以得到 最优解 。
应特性越好 。
4 优化设计的仿真流程
采用 iSIGHT多学科设计优化平台 ,将流场计算软 件 NUMECA 及有限元软件 ANSYS 进行集成 。优化中以 增压器涡轮叶片的等熵效率 、涡轮的扭矩以及离心应 力为目标函数 ,以第一阶振动频率以及前 5 阶固有频 率的约束值为约束函数 ; 以叶尖和叶根两个截面的型 面参数为设计变量 ;iSIGHT 的集成过程如图 6 。
Ξ 20060111 收到初稿 , 20060531 收到修改稿 。 ΞΞ 侯乃先 ,男 ,1982 年 6 月生 ,山东郯城人 ,汉族 。硕士研究生 ,主要从事结构设计与优化方面工作 。
938
机 械 强 度
2007 年
进行 MDO 的研究 ,发表了大量研究论文和报告 。本文 对轴流式涡轮增压器的涡轮叶片进行全三维的优化设 计 ,对涡轮叶片进行参数化建模 ,在气动 、结构及振动 三个学科间对涡轮叶片进行优化设计 ,将 MDO 的设计 方法引入到增压器部件的设计中 ,为进一步对涡轮增 压器进行优化打下基础 。
曲应力和热应力 。通常情况下 ,离心力的作用是主
要的 ,为了简化起见 ,本文只考虑离心力的影响。
Dundas 曾证明 ,叶根 ( 最高应力点) 的离心应力可由
下式计算[4]
σc max
=
ρω2
r2m
(1 2
叶片结构优化设计会议纪要
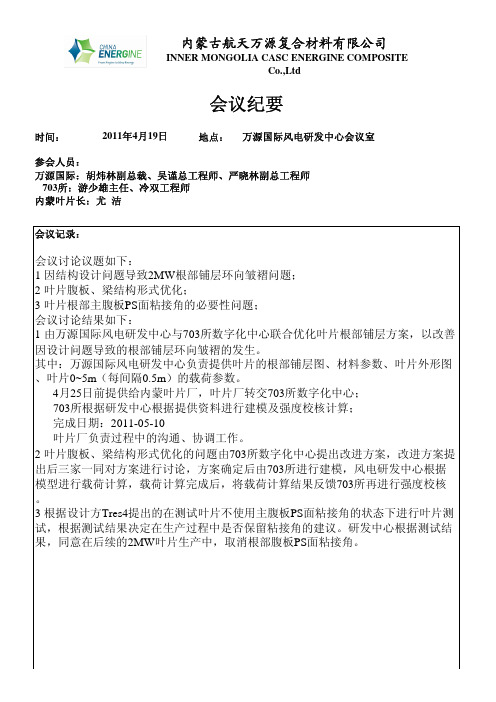
时间:地点:参会人员:会议记录:
会议纪要内蒙古航天万源复合材料有限公司
INNER MONGOLIA CASC ENERGINE COMPOSITE
Co.,Ltd
会议讨论议题如下:
1 因结构设计问题导致2MW 根部铺层环向皱褶问题;
2 叶片腹板、梁结构形式优化;
3 叶片根部主腹板PS 面粘接角的必要性问题;
会议讨论结果如下:
1 由万源国际风电研发中心与703所数字化中心联合优化叶片根部铺层方案,以改善因设计问题导致的根部铺层环向皱褶的发生。
其中:万源国际风电研发中心负责提供叶片的根部铺层图、材料参数、叶片外形图、叶片0~5m (每间隔0.5m )的载荷参数。
4月25日前提供给内蒙叶片厂,叶片厂转交703所数字化中心;
703所根据研发中心根据提供资料进行建模及强度校核计算;
完成日期:2011-05-10
叶片厂负责过程中的沟通、协调工作。
2 叶片腹板、梁结构形式优化的问题由703所数字化中心提出改进方案,改进方案提出后三家一同对方案进行讨论,方案确定后由703所进行建模,风电研发中心根据模型进行载荷计算,载荷计算完成后,将载荷计算结果反馈703所再进行强度校核。
3 根据设计方Tres4提出的在测试叶片不使用主腹板PS 面粘接角的状态下进行叶片测试,根据测试结果决定在生产过程中是否保留粘接角的建议。
研发中心根据测试结果,同意在后续的2MW 叶片生产中,取消根部腹板PS 面粘接角。
2011年4月19日万源国际风电研发中心会议室
万源国际:胡炜林副总裁、吴谨总工程师、严晓林副总工程师
703所:游少雄主任、冷双工程师
内蒙叶片长:尤 洁。
轴流压气机叶片准三维自动优化设计

轴流压气机叶片准三维自动优化设计
安志强;周正贵;张益豪
【期刊名称】《推进技术》
【年(卷),期】2014(0)4
【摘要】为提高轴流压气机叶片气动设计效果,将叶片准三维设计方法与叶型自动优化技术相结合,构建轴流压气机叶片准三维自动优化设计平台。
在叶片三维数值计算结果中提取总压损失系数径向分布,反馈到S_2流面计算程序,替代原有的基于试验数据的损失模型,重新进行通流设计,提高S_2流面流场计算精度;S_1流面叶型设计采用并行遗传算法与叶轮机CFD方法相结合的叶型自动优化方法,以数值寻优代替叶型气动外形的人工调整,减小对设计经验的依赖。
运用设计平台,对一设计流量6.3kg/s,设计压比2.07的轴流压气机第一级转子进行气动设计,得到径向三维叶片,设计点流量、总压比均接近设计目标,等熵效率接近90%,失速裕度达15.5%,结果令人满意。
采用三维优化方法进一步进行叶片积叠线弯、掠设计,在失速点到设计点的稳定工作范围内效率均得到了1%的提升。
【总页数】7页(P485-491)
【作者】安志强;周正贵;张益豪
【作者单位】南京航空航天大学能源与动力学院;中国航空动力机械研究所
【正文语种】中文
【中图分类】TH453
【相关文献】
1.优化方法在轴流压气机转子叶片气动设计中的应用
2.轴流压气机三维叶片周向积叠的多目标优化
3.基于数值优化方法的轴流压气机叶片设计与分析
4.轴流压气机串列静子叶片弯掠设计优化
5.基于NURBS的三维轴流压气机叶片的几何型面优化研究
因版权原因,仅展示原文概要,查看原文内容请购买。
简述轴流式压气机从第一级到最后一级叶片的变化规律_概述及解释说明

简述轴流式压气机从第一级到最后一级叶片的变化规律概述及解释说明1. 引言1.1 概述轴流式压气机是一种常见的热能转换设备,广泛应用于航空、发电和工业领域。
它通过叶片的旋转运动将气体进行压缩,提高了气体的静压力和动能。
然而,叶片在压缩过程中不断受到气体的冲击和离心力的作用,这就要求叶片在设计和制造过程中具备一定的性能优化和结构改善。
本文旨在简要描述轴流式压气机从第一级到最后一级叶片的变化规律,包括影响叶片设计参数、叶片剖面及角度变化规律以及叶片材料和制造工艺的发展与改进等方面。
同时还涵盖了中间级叶片变化规律和最后一级叶片变化规律,并分析了气动特性、效率以及振动特性等关键问题。
通过对这些内容进行阐述,我们可以更好地理解轴流式压气机中各个级别叶片变化背后的原因与机制。
1.2 文章结构本文共分为五个部分:引言、轴流式压气机第一级叶片变化规律、轴流式压气机中间级叶片变化规律、轴流式压气机最后一级叶片变化规律以及结论。
引言部分将对文章的主要内容进行概述,为读者提供整体框架。
接下来的各个部分将详细描述轴流式压气机各级别叶片的变化规律,并解释背后的原因和机制。
最后的结论部分将总结本文主要观点,并展望未来发展趋势。
1.3 目的本文旨在探讨轴流式压气机从第一级到最后一级叶片的变化规律,从而增进对该设备工作原理和性能优化方面的理解。
通过深入研究叶片设计参数、叶片剖面及角度变化规律、叶片材料和制造工艺的发展与改进,我们可以更好地了解轴流式压气机在实际应用中遇到的挑战与解决方案。
此外,通过对气动特性、效率以及振动特性等关键问题进行分析,我们可以为未来轴流式压气机设计与制造提供参考意见,并预测其可能的发展趋势。
通过本文的撰写,我们希望能够促进轴流式压气机领域的研究与发展,推动该设备在不同领域应用的创新与进步。
2. 轴流式压气机第一级叶片变化规律:2.1 叶片设计参数的影响:在轴流式压气机中,第一级叶片是整个压气机系统中起始压缩空气的关键部分。
轴流压气机叶片优化仿真系统的开发
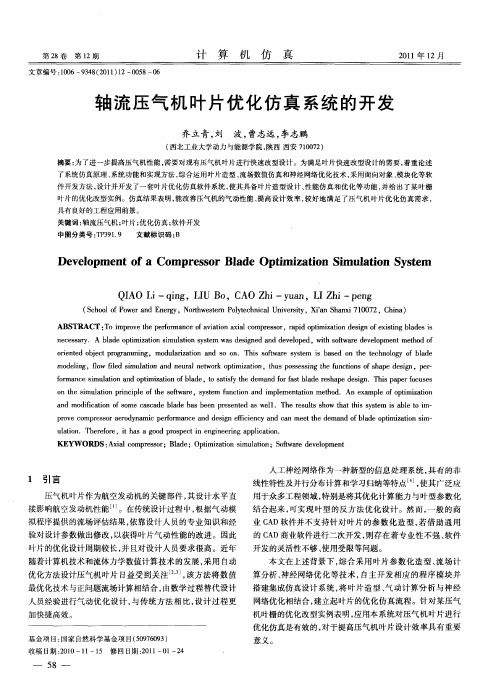
叶片的优化设计周期较长 , 且对设计人 员要 求很高 。近年 并 随着计算机技术 和流体力学数值计算 技术 的发展 , 采用 自动 优化方法设计压 气机 叶片 日益受到关 注 , 该方法将 数值
最优化技术 与正 问题 流场计算相结合 , 由数学 过程替代设计
开发 的灵 活性不够 、 使用受限等问题 。 本 文在上述背 景下 , 综合 采用 叶片参数 化造 型 、 场计 流
的若干截 面轮廓线来 表示 三维叶片实体 , 当截 面数取得 足够 多且分布合 理时它们 所构成的空 间将 逼近 叶片实体 。同时 , 这也符合所依据 的压 气机叶片设计理论 , 即先 进行基元 叶型 设计 , 再将不 同半 径上 的叶型 叠加 起 来形 成 一个 完整 的叶
片 J如图 1 示。 , 所
—
5 一 8
以叶型马赫数分 布作 为 网络 输入 , 中弧线 的 N R S 以 U B
2 叶片建 模 问题
2 1 叶片建模及参数化造型 . 为使 叶片能够被计 算 机识别 、 理和 显示 , 处 需要 建 立三
维 叶片 的几何模 型。本文应用离散化 的思想 , 用沿径 向分布
控制点坐标作 为输 出 , 这样就使几何控制点 与气 动性能相关 联 , 马赫数分布 一曲线控制点 ” 以“ 数值对 的形式创建大量 的 训练样本 , 以便对人工 神经 网络进行 训练 , 而建立 起叶 片 从 几何型面控制点与气动性能 的非线性 映射关系 , 3显示 了 图 优化样本库 的建立流程 。
o et b c porm ig oua ztn adS n hssf aess m i bsd o h eho g f l e i e r n doj t rga m n ,m l a o n Oo.T i ow r yt s ae ntetcnl o a e d r i i t e o y bd
轴流压气机叶片的优化设计方法和系统[发明专利]
![轴流压气机叶片的优化设计方法和系统[发明专利]](https://img.taocdn.com/s3/m/69aefde1581b6bd97e19ea29.png)
专利名称:轴流压气机叶片的优化设计方法和系统专利类型:发明专利
发明人:杨波,朱国明,周蕊
申请号:CN202011286421.7
申请日:20201117
公开号:CN112395702A
公开日:
20210223
专利内容由知识产权出版社提供
摘要:本发明提供了一种轴流压气机叶片的优化设计方法和系统,该方法包括:根据轴流压气机的流动特点,将描述流动过程的偏微分方程转换为常微分方程;建立轴流压气机的状态方程;根据预设的约束条件,基于所述状态方程,确定轴流压气机的最优扩压因子分布;以出口角作为控制变量,根据叶片三维空间的几何造型所对应的参数和所述常微分方程,迭代运算,得到满足所述轴流压气机的最优扩压因子分布的叶片型线。
采用该方法设计的轴流压气机叶片具有高效率、大失速裕度的特性,适用于各种设计工况和变工况。
申请人:上海交通大学
地址:200240 上海市闵行区东川路800号
国籍:CN
代理机构:上海汉声知识产权代理有限公司
代理人:胡晶
更多信息请下载全文后查看。
- 1、下载文档前请自行甄别文档内容的完整性,平台不提供额外的编辑、内容补充、找答案等附加服务。
- 2、"仅部分预览"的文档,不可在线预览部分如存在完整性等问题,可反馈申请退款(可完整预览的文档不适用该条件!)。
- 3、如文档侵犯您的权益,请联系客服反馈,我们会尽快为您处理(人工客服工作时间:9:00-18:30)。
收稿日期:2005-06-09;修订日期:2005-12-22作者简介:伊卫林(1978-),男,满族,黑龙江宁安人,哈尔滨工业大学博士生.文章编号:1001-2060(2006)02-0140-05轴流压气机叶片优化设计伊卫林,黄鸿雁,韩万金(哈尔滨工业大学能源科学与工程学院,黑龙江哈尔滨150001)摘要:开发了基于梯度法的数值优化程序,并与三维粘性流场求解程序相结合对跨音压气机动叶片进行了以绝热效率最大为目标的三维气动优化设计。
先对其进行了沿弦长方向掠设计,绝热效率可提高约0.65%。
再对所得掠叶片进行叶型中弧线优化设计得到最终叶片,与初始叶片相比绝热效率提高达1.05%。
优化结果表明,动叶片的单纯掠型叶片改进气动性能有限,而弦向掠与中弧线的联合优化设计可以显著改善叶片排内流动状况,并具有良好的变工况性能。
关键词:压气机;掠动叶;中弧线;N-S方程;优化设计中图分类号:TK474.8文献标识码:A1引言叶轮机械内部流动包含有边界层分离、二次流、旋涡以及激波与边界层相互干扰等复杂现象。
跨音压气机中的三维激波结构是流动损失的主要根源,因此如何控制激波的位置与强度是提高压气机性能的主要因素之一。
Wadia和Denton等人都曾对掠叶片进行过深入研究[1~2],并证明采用掠叶片可以改变跨音压气机动叶中的三维激波结构。
叶型中弧线对压气机叶片气动性能也有显著影响,与叶片流道内激波产生的强度与分布以及附面层的分离状态都密切相关。
可以推测,积叠线形状的空间变化只能在一定程度上改善内部流动状况,再配以合适的叶型必定能进一步提高压气机工作性能。
随着计算速度的提高及CFD三维流场求解精度的完善,基于N-S方程的全三维流场数值模拟用于叶轮机械气动设计成为可能。
近年来,梯度法、遗传算法、模拟退火算法和响应面法等数值优化算法广泛应用于叶轮机械优化[3~6]。
但是由于遗传算法和模拟退火算法的耗时性,使其无法应用于工程实际,响应面方法虽然简单、省时,但需要较多的人工操作,尤其是前期的样本如果选取不好,将在很大程度上破坏其寻优能力。
因此,在叶轮机械优化设计中梯度法的应用仍最为广泛。
为了研究掠及相应叶型变化对压气机气动性能的影响,本文采用常规H型网格生成程序、基于雷诺平均N-S方程的全三维流场模拟程序和基于梯度法的数值优化程序,对某跨音压气机动叶进行优化设计。
2控制方程及数值方法采用有限体积法求解圆柱坐标系下的雷诺平均N-S方程。
空间求解采用二阶精度的中心差分格式加二阶、四阶人工粘性项,时间方向求解采用四步Ronger-Kutta格式。
湍流模型为壁面函数修正的B -L模型,采用隐式残差光顺、局部时间步及多重网格等加速收敛技术,计算中采用两重网格,使程序具有较快的收敛速度,尤其适用于数值优化设计。
网格采用常规H型网格,网格数为41@145@41。
此种网格生成方法简单,在数值优化过程中,由于其参数为随机选择过程,如果网格生成质量不高,极易出现畸形网格,从而导致优化过程无法继续。
本文采用的网格生成程序则没有出现这一情况。
3叶型参数化表达在叶型的气动优化设计中,需要对其进行参数化表达,以便采用尽可能少的设计变量来控制叶片形状。
另外还必须保证叶片型线曲率的光滑分布。
控制点类曲线可以很好地解决这些问题。
本文采用5个控制点的3次B样条曲线分别对25%、50%、75%叶高的叶型中弧线进行参数化表达,图1为25%叶高示意图。
对于每个叶型以中弧线的首末端点为两控制点,并保证其在设计过程中不变,其余3个控制点为设计变量沿叶型型线垂直方向变化,这样既可以有第21卷第2期2006年3月热能动力工程JOURNAL OF ENGINEERING FOR THERMAL ENERGY AND POWERVol.21,No.2Mar.,2006效地减少设计变量的数量,还能保证其寻优范围。
图1 中弧线和控制点示意图4 优化方法及设计尽管遗传算法、模拟退火算法等在叶轮机械优化设计中有所应用,但由于其理论尚待完善及气动设计本身的长时间性,其在现阶段仍无法应用于工程实际。
如Ernesto 对跨音压气机动叶选取3个截面叶型[4],考虑叶型及积叠线变化,共23个设计变量,采用遗传算法进行优化设计,需要高达2000h 的工作时间,显然这是不可行的。
为了降低优化设计时间,本文开发了可在单机上运行的基于梯度法的优化程序。
本文的基本想法是定义目标函数F (X ),在有限制g j (x )[0情况下使其达到最小化,其中X 为设计变量矢量,其分量X 1i [X i [X ui 具有上下界限制。
优化过程中的梯度信息采用有限差分方法获得。
定义最大绝热效率为目标函数f =1-G ,其中效率的定义为:G =(P 0out /P 0in )C -1C -1/T 0out /T 0in -1初始叶片由五个叶型构成,分别为根部、25%叶高、50%叶高和75%叶高、顶部叶型。
在此基础上进行网格生成并进行计算。
先对初始叶片进行积叠线掠优化设计,以叶片前缘曲线为积叠线,以根部为积叠点并保持不动,其余截面从根部到顶部依次沿前后缘弦向在各自弦长的5%、10%、25%和50%范围内变化,共计4个设计变量。
优化过程中被优化的前缘线采用B 样条曲线连接,以确保其光滑性,得到了最优掠形叶片。
然后再对得出的优化掠叶片进行了中弧线优化设计,以25%、50%、75%叶高的经过参数化的3个叶型的控制点为设计变量,共计9个。
每个叶型的厚度分布不变,在新中弧线上叠加生成新叶型。
结果表明气动性能可进一步提高,具体的性能参数与气动分析将在下文进行。
在优化过程中分别对总压比与质量流量加以限制:0.97@P ori [P opti [1.05@P ori m o pti -m o riginm o rigin<0.5%这是为了尽可能地保证其工作点不变,图2为初始叶片与各优化叶片对比。
在本算例中为了保证优化过程能够自动进行,叶型控制点的变化范围相对较小,以确保不会计算中止,因此最终叶型变化也较小,效率提高较小。
但这并不是说中弧线的变化对流场性能的影响不显著,这需要对其进行专门的分析研究。
图2 初始叶片与各优化叶片5 结果分析初始叶型与优化叶型设计结果的各气动参数对比见表1。
仅做掠型优化设计后效率可提高约0165%,再对其进行中弧线优化设计后效率还可进#141#第2期伊卫林,等:轴流压气机叶片优化设计一步提高,最终绝热效率提高约1.05%。
由于在优化过程中适当地加入了限制,其它的两个重要参数压比与质量流量未发生明显变化。
可以看出,压比基本未变,质量流量随着效率的增大而略有增加,最终优化结果的质量流量已经接近给定限制的上限,这是气动参数之间相互平衡的结果。
表1 初始叶型与优化叶型参数对比初始叶片掠形叶片掠+中弧线优化叶片总压比 2.14104 2.14200 2.14640绝热效率/%86.273386.924087.3279质量流量/kg #s-120.4520.5120.54图3为优化设计后叶片与初始叶片气动参数沿叶高分布的对比图。
从中可以看出,绝热效率在下半叶展有所降低,整体效率提高主要发生在60%以上叶高。
压比沿叶高的分布未减小,而是略有增加,这是由于质量流量增大,通流能力有所增强造成的。
对于绝热效率沿展向有升有降,是各个截面负荷分配的结果,也是由于根部积叠点的限制导致了其附近的性能提高。
因此,积叠点与积叠线的选取是非常重要的。
在掠叶片之后再对中弧线进行优化设计,虽然未能完全抵消此处的流动恶化情况,但仍在一定程度上有所改善,效率有所提高。
优化后叶型更适合于此处的工作状况。
图3 优化与初始型出口参数展向分布图4 不同截面马赫数等值线对比#142# 热能动力工程2006年由不同截面马赫数等值线对比(见图4)也可以看到,绝热效率的提高主要发生在上半叶展。
在90%叶高相对马赫数对比图中,可以看出掠型叶片与原型相比,前缘激波无论在强度还是在波形上都发生了明显变化。
由强正激波变为弱斜激波,因此效率有较明显提高。
由此可见,叶片前掠对前缘激波结构强度的影响是十分明显的。
而再经过中弧线优化之后,前缘激波进一步后掠,激波边界层干扰位置明显移向下游而且强度减弱。
与仅经过掠优化的叶片相比,相应位置的叶型更适合其工况,因此也具有更高的效率。
图5吸力面附近马赫数等值线对比图6 特性线对比从图5吸力面附近马赫数等值线可以看出,在初始叶片中,激波强度很强且为正激波,这正是高损失的来源。
而前掠叶片明显地改善了三维激波结构,通道内激波形状不再为正激波,而是弱强度的斜激波,因此有效地降低了通道内的流动损失。
而中弧线优化叶片与掠叶片相比,激波结构变化就不明显,可见中弧线对空间三维激波结构的改变影响是较小的。
单一工作点下进行的优化设计,必须考虑其变工况性能。
图6为3套动叶片的变工况特性对比。
从图中可以看出,掠叶片及最终叶片都具有良好的变工况性能,工作范围相对宽些。
最终经过中弧线优化的叶片具有最高的尖峰效率及最大的工作范围,只是在近失速工况附近效率有所降低。
6 结 论本文采用雷诺平均N -S 方程的全三维数值模拟程序及梯度法的数值优化程序对某型跨音压气机动叶进行了叶片掠及中弧线形状的有限制优化设计,得到了最优叶片,并对其进行了详细的流场分析。
从优化结果看,前掠动叶能显著改善叶片前缘激波结构,削弱激波强度,降低激波损失,并能改善其变工况性能。
再对其进行中弧线优化设计,能进一步改善动叶片排内的流动。
由此可见,叶片单纯发生掠型变化以后,相应叶型已不处于最佳工作点,可以通过对中弧线形状的重新设计,得到更加适合的叶型。
掠型叶片的设计可能会造成局部位置流动恶化,最终性能的改进是各部分相互抵消的结果。
相比较而言,最终优化叶片具有最宽的工作范围及最高的尖峰效率,只是在近失速点附近绝热效率有所降低。
三维空间的积叠线形状与二维叶型的中弧线形状如何合理的搭配以提高压气机性能是一个值得深入研究的方向。
参考文献:[1] WADIA A R,SZUCS P N,CRA LL D W.Inner working of aerodynamicsweep[R].ASME Paper,1997-G T-401.[2] D EN TO N J D,XU L.The effects of lean and sweep on transonic fan#143#第2期伊卫林,等:轴流压气机叶片优化设计performance[R].ASME Paper,2002-GT-30327.[3] J U NE C HUNG,LEE K I D.Shape optimiz ati on of trans onic c ompress orblades using quasi-3D flo w physi cs[R].ASME Paper,2000-G T-489.[4] ERNESTO BENINI.Three -dimensional mult-i objective desi gn opti miza -tion of a trans onic compress or rotor [J ].Journal of Propulsion and Power ,2004,20(3):559-565.[5] SHAHROK H SHAHPAR DR.A comparative study of optimi sati onmethods for aerodynamic of turbomachienry blades[R].ASME Paper,2000-G T-523.[6] AHN CHAN SOL,KIM KWA NG YO NG.Aerodyna mic design optimi za -tion of an axial flow co mpressor rotor[R].A SME Paper,2002-G T -30445.(丹 编辑)5热能动力工程6投稿须知5热能动力工程6是学术性与技术性科技期刊。