油井的腐蚀及防护
油田地面管线腐蚀穿孔原因分析与处理方法

油田地面管线腐蚀穿孔原因分析与处理方法摘要:由于我国石油产业的迅速发展,地下油气管道已被越来越多地用于贮存运输。
但是,由于长期的服役以及外部环境的腐蚀,导致了地下管道存在着许多问题,在这些情况下,管道的腐蚀、穿孔尤为严重。
这些现象不但会给油田的正常开采带来很大的影响,也会给周围的环境带来很大的负面影响。
为此,从腐蚀、穿孔等角度,对管道故障产生的原因进行了分析,并提出了切实可行的解决方案。
关键词:油田地面管线;腐蚀穿孔原因分析;处理方法引言腐蚀是一种物质由于受到环境的影响而引起的破坏。
对于石油工程来说,管线腐蚀是一个由来已久的问题,会影响到其的正常运行,如果对机电安装项目的管理与控制工作不重视,这将导致巨大的资源浪费,带来巨大的经济损失。
在油田生产中,如何降低地表管道的穿孔腐蚀是一个十分重要的课题。
在实际操作中,为了有效地降低腐蚀时间,必须增强对这一问题成因的认识,并据此制订出相应的预防措施,因此,应加强对引起地下管线腐蚀的主控因素的把握,研究出降低地下管线腐蚀的对策,以提高油田的经济效益。
一、油田地面管线穿孔腐蚀类型(一)电化学腐蚀这种腐蚀现象多发生在地面管道中,具有腐蚀性,由此造成的管线腐蚀,在油田开采过程中,会产生大量的废水,每天的废水量很大,占到了油田中的85%,因此,油田废水是管道中共同的组成成分。
而且,污水的成分比较复杂,里面包含了很多的化学物质和溶解性气体,此外,还会出现具有强烈腐蚀性的硫化物,从而加剧了输油管线的内部腐蚀问题。
(二)微生物腐蚀油井中的氯离子含量很高,特别是在靠近海洋的近海油田,使土壤含盐量很高,含盐量很高,主要是氯化物,将会造成地面管道的腐蚀状况。
在一些油气田中,管道电阻率很低,在海岸附近的油气田中,每一套电阻率仅为25欧姆,可以看出,相对于一些陆上油田,由于土壤具有极强的腐蚀性,所以这种管道在土壤中会受到更大的腐蚀。
(三)流体冲刷腐蚀石油管线中的污水具有高流速,且含有从油田开采出来的流体,流体具有盐分难溶性、含大量泥沙等特点,在输送过程中会对管线产生一定的破坏。
油井的腐蚀原因与防护措施研究

油井的腐蚀原因与防护措施研究摘要:随着油田的持续开发,油井综合含水逐年上升,目前采油厂处于高含水开发生产阶段,综合含水达到94.3%。
由于后期含水上升,同时受高矿化度、管杆材质等综合因素影响,油井腐蚀现象日趋严重。
油井腐蚀是指井下金属设备与产出液直接接触形成腐蚀电池而产生的腐蚀现象,能够造成管漏、杆断、泵漏而躺井。
随着油管配套的完善,井筒腐蚀问题逐步向抽油杆与抽油泵上转移,其中腐蚀杆断的井数和比例都逐年升高。
油井腐蚀现象是多因素交互作用下的结果,因此,对其形成的原因、腐蚀的程度及防腐的措施进行全方位的把控相当困难。
因此加强油井的腐蚀原因与防护措施研究至关重要。
关键词:油井;腐蚀;机理分析;防腐措施1油井腐蚀研究现状腐蚀是材料与环境反应引起的材料破坏与变质,它存在于各行各业,引起经济损失也是引人注目的。
腐蚀是造成石油工业中金属设备的主要原因之一,它加剧了设备及管道的损坏和人员伤亡,造成了石油生产中停工、停产和跑、冒、滴、漏等事故;并且污染环境,损害人民健康;导致产品流失,增加了石油产品的成本,有的已影响正常的石油生产。
我国很早便开始着手对油气田井下油管的腐蚀展开研究,主要包括腐蚀的环境、影响因素及防腐措施等几个方面。
王明辉等人通过室内实验,针对某油井中的套管在H2S与CO2共存条件下的腐蚀情况开展了研究,精确评估了管材的使用寿命。
贺海军等人结合灰色关联法,对油井套管开展了防腐模拟评价室内实验,通过定量分析管材的安全服役寿命对其进行了优选。
赵健等人提出了深层油井管材阴极保护计算公式,通过计算和推导得出,在一定的误差范围内,这种计算方法能够为深层油井管材保护提供可靠的数据,具有一定的实用性和可靠性。
当前,我国对不同储层物性油田的腐蚀问题进行了大量的研究,在防腐技术方面已相当成熟,当然,这只是油井防腐万里长征的第一步,要想真正意义上把油井防腐工作搞扎实,必须对其腐蚀的影响因素、腐蚀环境、形成原因及腐蚀监控等相关工艺技术进行更深人的分析和研究。
油气田气田腐蚀与防腐技术
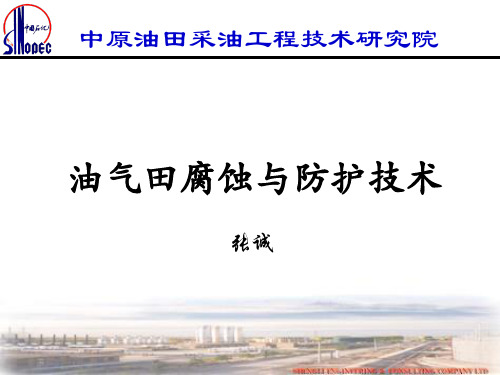
中原油田采油院
二、油气田腐蚀腐蚀机理、现象及分类
(5)氧腐蚀 • 在注入水或者注入的其他工作液中,不可避免的要混 入氧。发生吸氧腐蚀。
2Fe+2H2O+O2=2Fe(OH)2
4Fe(OH)2+O2+2H2O=4Fe(OH)3 Fe(OH)3 Fe2O3· xH2O
钢铁的吸氧腐蚀示意图 中原油田采油院
中原油田采油院
二、油气田腐蚀腐蚀机理、现象及分类 (7)腐蚀性组分相互作用及对腐蚀的影响
(a)硫化氢和二氧化碳共存对腐蚀的影响 • H2S和CO2共同存在下具有协同作用,CO2的存 在可以降低pH值,提高硫化物应力腐蚀的敏感性; H2S可以破坏CO2腐蚀产生的保护膜,使得腐蚀速 度持续增加,并作为毒化剂,加速CO2腐蚀过程中 产生的氢原子进入钢材基体。 同时具有H2S和CO2腐蚀的特点,也包括一些 共同作用下的特点。但最重要的还是需要防止H2S 引起的脆性开裂。
中原油田采油院
一、腐蚀简介 氢与腐蚀:
金属基体 氢进入
表面能降低
原子键合力降低 晶格膨胀
更易断裂 更易腐蚀
浅析化工设备腐蚀的原因及防护
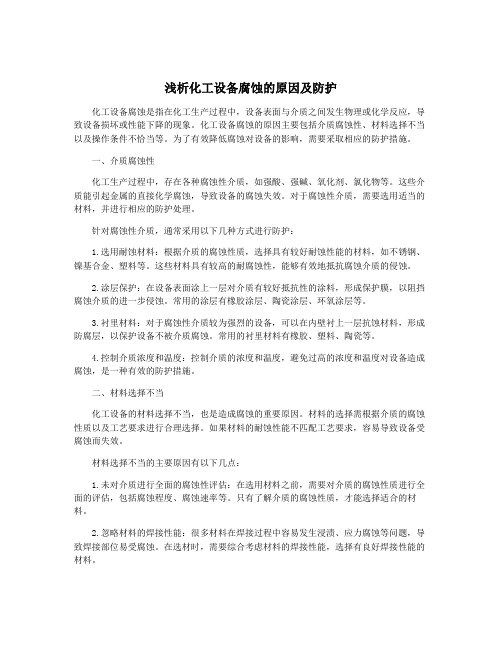
浅析化工设备腐蚀的原因及防护化工设备腐蚀是指在化工生产过程中,设备表面与介质之间发生物理或化学反应,导致设备损坏或性能下降的现象。
化工设备腐蚀的原因主要包括介质腐蚀性、材料选择不当以及操作条件不恰当等。
为了有效降低腐蚀对设备的影响,需要采取相应的防护措施。
一、介质腐蚀性化工生产过程中,存在各种腐蚀性介质,如强酸、强碱、氧化剂、氯化物等。
这些介质能引起金属的直接化学腐蚀,导致设备的腐蚀失效。
对于腐蚀性介质,需要选用适当的材料,并进行相应的防护处理。
针对腐蚀性介质,通常采用以下几种方式进行防护:1.选用耐蚀材料:根据介质的腐蚀性质,选择具有较好耐蚀性能的材料,如不锈钢、镍基合金、塑料等。
这些材料具有较高的耐腐蚀性,能够有效地抵抗腐蚀介质的侵蚀。
2.涂层保护:在设备表面涂上一层对介质有较好抵抗性的涂料,形成保护膜,以阻挡腐蚀介质的进一步侵蚀。
常用的涂层有橡胶涂层、陶瓷涂层、环氧涂层等。
3.衬里材料:对于腐蚀性介质较为强烈的设备,可以在内壁衬上一层抗蚀材料,形成防腐层,以保护设备不被介质腐蚀。
常用的衬里材料有橡胶、塑料、陶瓷等。
4.控制介质浓度和温度:控制介质的浓度和温度,避免过高的浓度和温度对设备造成腐蚀,是一种有效的防护措施。
二、材料选择不当化工设备的材料选择不当,也是造成腐蚀的重要原因。
材料的选择需根据介质的腐蚀性质以及工艺要求进行合理选择。
如果材料的耐蚀性能不匹配工艺要求,容易导致设备受腐蚀而失效。
材料选择不当的主要原因有以下几点:1.未对介质进行全面的腐蚀性评估:在选用材料之前,需要对介质的腐蚀性质进行全面的评估,包括腐蚀程度、腐蚀速率等。
只有了解介质的腐蚀性质,才能选择适合的材料。
2.忽略材料的焊接性能:很多材料在焊接过程中容易发生浸渍、应力腐蚀等问题,导致焊接部位易受腐蚀。
在选材时,需要综合考虑材料的焊接性能,选择有良好焊接性能的材料。
3.忽略材料的可加工性:一些材料的加工性能较差,容易导致处理不当而引起腐蚀问题。
浅谈油田管道腐蚀及防腐应对措施

浅谈油田管道腐蚀及防腐应对措施随着石油工业的迅速发展,埋设在地下的油、气、水管道等日益增多。
地埋管道会因为土壤腐蚀形成管线设备穿孔,从而造成油、气、水的跑、冒、滴、露。
这不仅造成直接经济损失,而且可能引起爆炸、起火、环境污染等,产生巨大的经济损失。
本文对管道腐蚀危害做了简要说明,并结合日常生产中管道腐蚀的情况,对其腐蚀机理做了进一步的阐述。
结合腐蚀机理提出防腐应对措施,并进一步介绍了新型防腐技术,为今后油田管道设备防腐工作提供了一定的工作方向。
标签:腐蚀;腐蚀危害;腐蚀机理;防腐措施一、石油管道腐蚀的危害我们把石油生产过程中原油采出液、伴生气等介质在集输过程中对油井油套管、油站内、回注管网等金属管线、设备、容器等形成的内腐蚀以及由于环境,例如土壤、空气、水分等造成的外腐蚀统称为油气集输系统腐蚀。
油气集输系统腐蚀中的内腐蚀一般占据腐蚀伤害的主要地位。
针对腐蚀研究,在整个生产系统中,不同的位置及生产环节其所发生的的腐蚀也有所不同,并且腐蚀特征及腐蚀影响因素也有所不同。
因此防腐工作是油田生产中的重要措施。
据不完全统计截止目前,我国输油管道在近20年的时间里,共发生大小事故628起,其中包括线上辅助设备故障190 起,其它自然灾害70 起,有368 起属管体本身的事故。
根据近年的调查发现:影响管线寿命和安全性的因素中,腐蚀占36.4%,机械和焊缝损伤占14.4%,操作失误占35.0%,第三方破坏占14.2%.因此,腐蝕是事故的主要原因。
[1]二、管道腐蚀的机理理论(1)土壤腐蚀土壤腐蚀是电化学腐蚀的一种,土壤的组成比较复杂,其多为复杂混合物组成。
并且土壤颗粒中充满了空气、水及各类盐从而使土壤具有电解质的特征,根据土壤腐蚀机理,我们将土壤腐蚀电池大致分为两类:第一种为微电池腐蚀,也就是我们常说的均匀腐蚀。
均匀腐蚀是因为微阳极与微阴极十分接近,这样的距离在腐蚀过程中不依赖土壤的电阻率,只是由微阳极与微阴极决定电极过程。
油气田腐蚀防护技术综述

[收稿日期]2008208205 [作者简介]吕瑞典(19562),男,1982年大学毕业,教授,现从事石油矿场机械的教学和科研工作。
油气田腐蚀防护技术综述 吕瑞典,薛有祥 (西南石油大学,四川成都610500)[摘要]通过查阅大量油气田腐蚀防护相关文献,总结归纳了油气田经常使用的腐蚀防护技术,简要介绍了一些防腐新技术,并对油气田的腐蚀防护提出了些许建议,旨在提高油田腐蚀防护水平,加强腐蚀防护研究与应用,为安全生产提供一个强有力的支撑。
[关键词]油气田;腐蚀防护;防腐技术;技术研究;井下设备[中图分类号]TE980[文献标识码]A [文章编号]100029752(2008)05203672031 油气田腐蚀防护油气田腐蚀往往造成重大的经济损失、人员伤亡和环境污染等灾难性后果,1969年英国Hoar 报告报道,英国每年因腐蚀造成的经济损失估计不少于23165亿英镑[1]。
我国对腐蚀损失统计表明,腐蚀造成的损失占国民经济的3%,对石油石化行业约在6%左右[2]。
据国外权威机构估计,如果腐蚀技术能够得到充分应用,腐蚀损失的30%~40%是可以挽回的[1]。
由此可见,提高腐蚀防护技术,加强腐蚀防护的研究与应用,不仅为安全生产提供一个强有力的支撑,而且给石油工业带来巨大的经济效益。
笔者通过总结,归纳出了目前油气田应用的7种主要腐蚀防护技术,并对油气田如何采用腐蚀防护措施提出拙见。
2 腐蚀防护技术在油气田的应用油气田腐蚀类型众多,腐蚀状况严峻。
其腐蚀有3个显著的特点:气、水、烃、固共存的多相流腐蚀介质;高温或高压环境;H 2S 、CO 2、O 2、Cl -和水为最主要的腐蚀介质。
现场一般采用如下7种腐蚀防护措施。
211 正确选材根据油气田实际腐蚀因素,正确选材对降低事故发生,提高工作效率意义重大。
如长庆油田[3]针对油井油管腐蚀穿孔断裂十分严重的状况,选用了高Cr 、Mo 低S 、P 耐腐蚀合金油套管,以提高井下管柱的抗蚀能力。
油区腐蚀及防护技术进展

Value Engineering 在Kuhn-Tucker 最优性条件下,拉格朗日乘子为1,则个人理性约束的等号成立。
因此个人理性约束可以改写成(4):代理人的激励相容约束是指代理人执行此合约的收益要大于此种情况下采取任何策略的收益,符合其收益最大化的预期目标。
激励相容约束可以表示为:max a∏L =S (r )(1-R a )(1-P ′)-R a vVk-(1-R a )P ′v[Vk-(1-b )V ′]-C (a )(6)对(6)求一阶、二阶导数,因为二阶导数小于零,因此,(6)可以改写为(5):由(4)和(5)得到:R a C ,X=-μ(1-P ′)-vVk (1+r )(1-P ′)-(1-b )P ′vV ′<0(7)a=S (r )(1-P ′)-P ′v[Vk-(1-b )V ′]C (1+r 0)lnP ′+1(1+r 0)lnR (8)将(8)带入(3)并化简得到:max a ,S (r )∏B =[Vk (1+r )-S (r )]1-C ∏∏(1-P ′)+C vVk+1-C ∏∏P ′{(1-b )V ′+v[Vk-(1-b )V ′]}(9)2不同合约下模型的求解当前银行提供三种合约供物流企业选择,三种合约对应了三种合作方式:一是雇佣关系,提供固定费用合约;二是合作关系,提供分成合约;三是授信关系,提供固定租金合约。
下面将针对三种不同合约的参数关系求解出银行最优激励函数,并且计算出最优激励合约下的物流企业努力水平。
2.1固定费用合约下的求解结果固定费用合约下,银行支付给物流企业固定费用而拥有剩余,物流企业只负责质押货物的仓储,收取固定仓储费用。
此时μ≠0,v=0,X=-μ(1-P ′)max μ∏B =Vk (1+r )-(1-P ′)+P ′(1-b)V ′-C -μ(1-P ′)+Vk (1+r C +C P ′(1-b )V ≠′1(10)对收益函数求一阶、二阶导数,因为二阶导数小于零,使目标函数存在最大值的条件是一阶导数等于零,解得μ*=姨,a *=μ*(1-P ′)0+10 2.2分成合约下的求解结果分成合约下,银行和物流企业之间对收益与风险按比例分享,物流企业除仓储职能外还需要提供信息服务等监管职能,按比例提成并承担相应风险。
试论钻井工程对油井套管腐蚀损坏原因及预防措施

钻井液的pH值
钻井液的pH值是影响套管腐蚀 的重要因素之一。一般情况下, 酸性钻井液比碱性钻井液更容易
导致套管腐蚀。
钻井液中的微生物
某些微生物在钻井液中繁殖,可 能对套管造成腐蚀损害。
钻井过程中的物理化学因素对套管腐蚀的影响
压力与温度
钻井过程中,地层压力和钻井液的压力变化可能导致套管 内外产生压力差,从而加速套管腐蚀。同时,温度也是影 响套管腐蚀的重要因素之一。
套管材质
不同材质的套管对腐蚀的抵抗 力不同。
井液成分
井液中的酸、碱、盐等成分对 套管腐蚀有重要影响。
流速和冲刷
流速快、冲刷力强的区域更容 易导致套管腐蚀。
防腐措施
采取有效的防腐措施可以降低 套管的腐蚀速度。
01
钻井工程对油井套管腐蚀 损坏的影响
钻井液对套管腐蚀的影响
钻井液的化学性质
钻井液中通常含有多种化学成分 ,如无机盐、有机溶剂等,这些 成分可能对套管产生腐蚀作用。
工程实例三:采用缓蚀剂防护的套管防护
缓蚀剂防护是一种绿色、高效的防护方法。
缓蚀剂防护通过向油井中注入缓蚀剂,减缓或阻止套 管的腐蚀。该方法具有成本低、操作简便、环保等优 点。在实际应用中,需要根据油气田的实际情况选择 合适的缓蚀剂。
01
结论与展望
研究结论
套管材质的影响
不同材质的套管对腐蚀的敏感性不同。
摩擦与磨损
钻井过程中,钻头与套管壁之间的摩擦和磨损可能导致套 管表面损伤和腐蚀。
电化学腐蚀
在某些情况下,钻井液中的电解质可能引起电化学腐蚀, 导致套管损坏。
钻井过程中的微生物对套管腐蚀的影响
硫酸盐还原菌
这类微生物在缺氧条件下能将钻井液中的硫酸盐还原为硫化 氢,从而加速套管的腐蚀。
- 1、下载文档前请自行甄别文档内容的完整性,平台不提供额外的编辑、内容补充、找答案等附加服务。
- 2、"仅部分预览"的文档,不可在线预览部分如存在完整性等问题,可反馈申请退款(可完整预览的文档不适用该条件!)。
- 3、如文档侵犯您的权益,请联系客服反馈,我们会尽快为您处理(人工客服工作时间:9:00-18:30)。
2H+ + 2e→H2
溶解氧的作用:
H2
阴极去极 化作用
+
1 2 O2
H2O
2 Fe(O H )3
2 Fe(O H )2
HO O +1 2 2 + 2
在碱性介质中
阴极去极 化作用
H2O + 2 O2 + 2 e 2 OH 1 H2O + 22+ O2 + 2e 2 OH Fe + 2 OH Fe(O H )2 2+ Fe + 2 OH Fe(O H )2 1 2 Fe(O H 2 Fe(O H )2 + 2 O2 + H2O 2 Fe(O H )3 HO 2 Fe(O H O )2 + 1 2 2 + 2
增加,对晶格界面的压力不断增高,最后导致界面开 裂,形成氢鼓泡,其分布平行于钢板表面。氢鼓泡的 发生并不需要外加应力。 氢致开裂(HIC)是由于在钢的内部发生氢鼓泡区 域,当氢的压力继续增高时,小的鼓泡裂纹趋向于相 互连接,形成阶梯状特征的氢致开裂。氢致开裂的发 生也无需外加应力。 硫化物应力腐蚀开裂(SSCC) 也叫电化学失重腐蚀, 是湿硫化氢环境中产生的氢原子渗透到钢的内部,溶解 于晶格中,导致氢脆,在外加应力或残余应力作用下形 成开裂。它通常发生在焊道与热影响区等高硬度区。 应力导向氢致开裂(SOHIC)是在应力引导下, 在夹杂物与缺陷处因氢聚集而形成成排的小裂纹沿着 垂直于应力的方向发展。它通常发生在焊接接头的
油井的腐蚀及防护技术
目 录
第一部分:腐蚀的危害
第二部分:腐蚀的类型和基本原理 第三部分:金属腐蚀的防护
一、 腐蚀的危害 金属腐蚀是指金属表面与周围介质发生化学 或电化学反应而遭到破坏的现象(被氧化) 工业发达国家由于腐蚀造成的损失约占国民 经济生产总值的2%-4%。目前美国每年的腐 蚀经济损失已高达3000亿美元。 在我国的管道事故中,腐蚀造成破坏约占 30%;我国东部油田管线腐蚀穿孔2万次/年, 更换管线400km/年。
腐蚀----在油气井开发中,从地下管柱到地面管
道和储罐以及各种工艺设备都会遭到腐蚀,严重影响 注水开发效果,造成巨大的经济损失。
研究应用针对性的工艺方法预防和治理腐蚀,
对于保证油田正常生产具有重要意义。
二、金属腐蚀的基本原理 1、关于腐蚀:
金属在使用过程中,与环境发生 氧化还原作用,而损坏的过程
2、金属腐蚀的原理 根据与环境作用不同,金属腐蚀的因素有:(1) 溶解氧的存在:主要是金属表面与水接触时而 在溶解氧作用下产生的电化学腐蚀。
硫酸盐还原 菌
阳极部位
8 H + SO2 4
S2- + 4 H2O + Q FeS Fe(OH )2
8 H+ -+ 6 OH 2OH
+8 e 8H2O
阴极部 位
2+ 4 Fe 4 Fe 8e
FeS Fe(OH )2
2SO 4 Fe + 4 + 4 H2O
腐蚀反应
Fe S + Fe(OH)2 + 2 OH-
危害:一方面生成硫化铁引起堵塞;另一方面,成菌 落式的附着在管壁上出现坑穴,甚至引起穿孔。 ②铁细菌的习性、作用和危害:是好氧菌,但在 1/10ppm的少量氧的条件下也能生长,数量增到一定 程度时,可造成危害。其作用是:Fe2+→Fe3+ 把可溶 的二价铁盐转变成蜂窝团胶状的氢氧化铁沉淀
V)氯离子 :由于Cl-存在:介质的导电能力增加、阻碍 硫化物膜的生成以及始膜脱落, 从而加速金属腐蚀;但若 Cl- 浓度很高, 由于Cl- 吸附能力强, 大量吸附在金属表面, 完全取代了吸附在金属表面的H2S、HS- , 因而金属腐蚀 反而减缓。 可见, Cl- 对于低合金钢材的抗H2S 腐蚀性有一定影 响。随着Cl- 浓度增加, 抗H2S 腐蚀性减弱。但是, 在过 高的Cl-浓度范围内, 抗H2S 腐蚀性得到改善。
II)CO2的分压:在中低温时,pCO2增大,腐蚀速度加 快;在高温时, pCO2增大,腐蚀速度减小。 III)流速的影响:流速增大,去极化速度加快,且阻碍 着保护膜的生成,从而腐蚀加剧,甚至导致严重的局 部腐蚀。 IV)pH值和介质成分的影响:pH值的增大,降低了原 子氢还原反应速度,从而腐蚀速率降低。 钢铁在3%NaC1的盐水溶液中腐蚀最为严重。 Ca2+ 、Mg2+的存在,通过影响钢铁表面腐蚀产 物膜的形成和性质来影响腐蚀特性,具体降低CO2的全 面腐蚀,加剧局部腐蚀;另外,溶解氧的存在也会引 发严重的局部腐蚀。 另外,金属材料本身的组成、处理工艺不同,对 CO2腐蚀的敏感性也有较大的差异(13Cr)
(3)CO2的存在 二氧化碳溶于水后对部分金属材料有极强的腐蚀性。 由此而引起的材料破坏统称为CO2 腐蚀。 CO2 在水介 质中能引起钢铁迅速的全面腐蚀和严重的局部腐蚀。 CO2 腐蚀典型的特征是呈现局部的点蚀、癣状腐蚀和台 面状腐蚀。随着油气井含水量的增加、深层含CO2 油气 层的开发日益增多,注CO2 强化采油工艺的推广,我国 埋地管道80%以上是1978年以前建成的。目前已进入 老龄期,漏油事故就日益增多。 CO2腐蚀问题越来越突 出。已成急待解决的重要课题 ①CO2的腐蚀机理: 二氧化碳腐蚀遵循以下机理:阳极反应
临盘采油厂临南油田油水井的腐蚀严重影响了油
田的正常生产和集输,造成大量原油损失,同时也造 成了大批资金的被迫投入。
埕岛油田目前共有平台65座,其中有20余座投产5a以
上。CB25A,CB25C,CB22A,CB11D和CB11G等平台甲板、 导管架锈蚀严重。利用CYGNUS-1型测厚仪,在CB11B平 台对平台潮溅区、全浸区进行了水下腐蚀情况检测。 结果表明:腐蚀速率为0.45mm/a左右,有的甚至高达 0.51mm/a 。
式中ad,sol,ab分别为吸附、溶液和吸收:Had表示 吸附在钢铁表面的氢原子,Hab 表示渗入钢铁内即钢铁 所吸收的氢原子,H+sol表示溶液介质体系中的H+。其 中,吸附在钢铁表面的氢原子既可能结合成 H2脱附,也 可能被金属吸收,从而导致产生氢脆。二氧化碳分子 也可以直接被吸附在钢铁表面.从而对钢铁表面产生 作用。总的腐蚀反应方程式为: Fe + 2CO2 + 2H2O → Fe + 2H2C03 2+ Fe + 2H2C03 →Fe + H2 + 2HC03 ②二氧化碳腐蚀的影响因素:I)温度:由于随温度升 高CO2在钢铁表面形成的FeCO3晶粒的形态、致密性 以及与本体结合由松软、粗大变为细小、致密和强的 附着力,因而随温度升高(60℃→100℃→150℃)特 点是全慢、快点、到钝化膜形成腐蚀速度减小。
Fe 2H2O Fe
2e 2+
Fe(O H )2 + 2OH 2H
↓
+
↑
在酸性介质中
Fe Fe H O 2H 2 O 2 2
Fe
2+ 2+ Fe
阳极 反应 阴极 反应
e +22e + + 2O H + 2 H + 2H + 2O H Fe(OH) H) 2 Fe(O 2
Fe
Байду номын сангаас
2+ 2+ Fe
+ +
2 O H 2O H
热影响区及高应力集中区,如接管处、几何突变处、 裂纹状缺陷处或应力腐蚀开裂处等。 危害性大
③影响硫化氢腐蚀 的因素:
I)水的含量:水是造成各种类型的电化学腐蚀的必要 条件。 没有水的存在H2S的腐蚀是轻微的,可以忽略。 II) 温度 :在低温范围内, 钢在硫化氢水溶液中的腐蚀 程度随温度的上升而增加。当温度由55 ℃上升到84 ℃ 时, 其腐蚀速度大约增加20 %; 若温度继续上升, 其腐蚀 速度反而降低; 碳钢在100~200 ℃之间的腐蚀速度最小。 因为,随温度升高, 其具有保护性的腐蚀产物膜也逐渐 由富铁、无规则几何微晶结构转变为富硫、有规则几何 微晶结构的磁黄铁矿或黄铁矿, 温度越高, 转化过程越快。 这种结构转变后的腐蚀产物膜可降低高强度钢对 SSCC 的敏感性。
III)腐蚀体系气体总压力P 及H2S 分压PH2S :对于环境 的腐蚀性有较大的影响 。PH2S 升高, 从而XH2S 升高, 最 终导致pH 值下降。溶液酸性增大, 氢去极化腐蚀加剧。 NACE 用H2S 的临界分压PH2S=0.034 8 MPa 来区分其 腐蚀性强弱, 当PH2S <0.034 8 MPa时, 称为非酸性 气; 而当PH2S>0.034 8 MPa时, 称为酸性气。 IV) pH 值影响 :pH 值不同, 溶解在水中的H2S 离解 成HS- 和S2- 的百分比不同,对腐蚀的影响不同: ( 1) pH<4.5 时,主要是H+的去极化,腐蚀速度随溶液 pH 值升高而降低;( 2) 在4.5<pH<8 , HS-是阴极去极化 剂,腐蚀速度随溶液pH 值的升高而增大; ( 3) pH>8 , H2S 可完全离解并形成较为完整的硫化铁 保护膜。
普通杆腐蚀断
套管腐蚀
泵杆的腐蚀 泵杆腐蚀
同时套管强度降低,引起其他类型的套损。
胜坨油田的坨712井生产80天左右,即发生抽油杆磨
蚀断脱和抽油泵柱塞多处穿孔;36200阀组至坨二站 集油管线仅投产运行89天就出现腐蚀穿孔,235天便 全线报废。
垦西油田采油井井下工具的腐蚀主要表现为油管漏、
泵漏、抽油杆断脱、光杆断。油管腐蚀导致油管螺 纹损坏,现场表现为油管螺纹出现腐蚀沟槽,内壁呈 坑状腐蚀。抽油泵由于缸套始终处于受磨状态,凡尔 受到流体的冲击涡流腐蚀严重。
1
结果:引起点腐蚀,引起管线的穿孔
(2)硫化氢的存在 天然气中含有的硫化氢对管线及设备具有强烈的腐 蚀性, 了解硫化氢腐蚀情况, 采取恰当的防腐措施对天然 气的安全生产及成本降低具有至关重要的意义。