抱轴箱加工工艺分析与胎具的改进
HXN5型机车抱轴箱机加工工艺
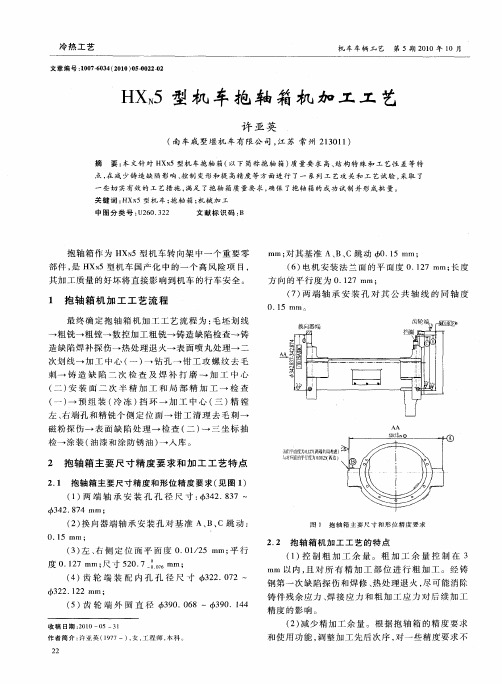
m 对 其 基 准 A、 、 m; B C跳 动 西 . 5mm; 0 1 ( ) 机 安 装 法 兰 面 的 平 面 度 0 17 m 长 度 6 电 .2 m;
方 向的平行 度为 0 17 m .2 m; () 7 两端 轴 承 安 装 孔 对 其 公 共 轴 线 的 同 轴 度
磁 粉探 伤一 表 面缺 陷 处 理 一 检查 ( ) 三 坐 标 抽 二 一 检 一涂装 ( 漆和涂 防锈 油 ) 入库 。 油 一
孩 平面 为0 7N 面 度 . ( ̄ 1 2 与 应 平 度为 ./( 对 面的 行 015 02 两边
2 抱 轴 箱主 要 尺 寸精 度 要 求和 加 工 工艺 特点
+ 2 . 2 n 3 2 1 2 lm;
2 2 抱轴箱 机加 工 工艺 的特点 .
( ) 制粗 加工余 量。粗加 工余 量控 制在 3 1控
m 以内 , 对 所 有 精加 工 部 位 进 行 粗 加 工 。经 铸 m 且
钢第一 次缺 陷探 伤 和焊修 、 热处 理退 火 , 可能 消除 尽 铸件残 余应 力 、 焊接 应 力 和 粗加 工应 力 对 后 续加 工
0. 5 m m 。 1
1 抱 轴 箱 机 加 工 工 艺 流 程
最终 确定 抱 轴 箱机 加 工 工艺 流 程 为 : 毛坯 划 线
一
粗铣一 粗 镗一数 控加 工粗 铣一铸 造缺 陷检查一 铸
造缺 陷焊补 探伤一 热处 理退 火一 表面 喷丸处 理一 二
次 划 线 一 加 工 中 心 ( ) 钻 孔 一 钳 工 攻 螺 纹 去 毛 一 一
摘 要 : 文 针 对 H N 本 X 5型 机 车 抱 轴 箱 ( 下 简 称 抱 轴 箱 ) 量 要 求 高 、 构 特 殊 和 工 艺 性 差 等 特 以 质 结 点 , 减 少铸 造 缺 陷 影 响 、 制 变形 和 提 高精 度 等 方 面进 行 了一 系列 工 艺 攻 关 和 工 艺试 验 , 取 了 在 控 采
某型机车轴箱体加工工艺优化改进
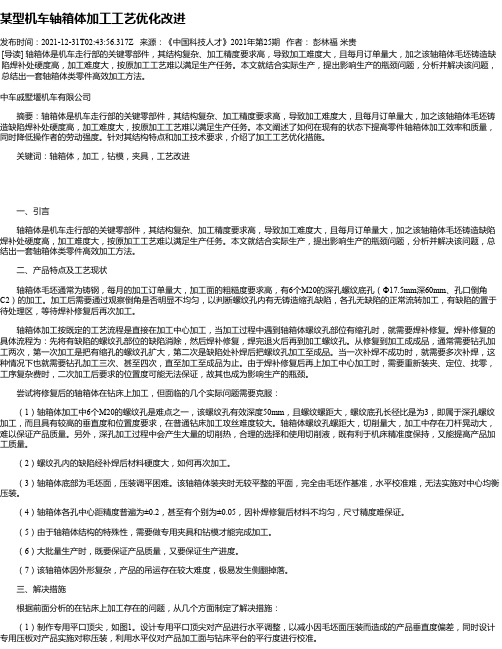
某型机车轴箱体加工工艺优化改进发布时间:2021-12-31T02:43:56.317Z 来源:《中国科技人才》2021年第25期作者:彭林福米贵[导读] 轴箱体是机车走行部的关键零部件,其结构复杂、加工精度要求高,导致加工难度大,且每月订单量大,加之该轴箱体毛坯铸造缺陷焊补处硬度高,加工难度大,按原加工工艺难以满足生产任务。
本文就结合实际生产,提出影响生产的瓶颈问题,分析并解决该问题,总结出一套轴箱体类零件高效加工方法。
中车戚墅堰机车有限公司摘要:轴箱体是机车走行部的关键零部件,其结构复杂、加工精度要求高,导致加工难度大,且每月订单量大,加之该轴箱体毛坯铸造缺陷焊补处硬度高,加工难度大,按原加工工艺难以满足生产任务。
本文阐述了如何在现有的状态下提高零件轴箱体加工效率和质量,同时降低操作者的劳动强度。
针对其结构特点和加工技术要求,介绍了加工工艺优化措施。
关键词:轴箱体,加工,钻模,夹具,工艺改进一、引言轴箱体是机车走行部的关键零部件,其结构复杂、加工精度要求高,导致加工难度大,且每月订单量大,加之该轴箱体毛坯铸造缺陷焊补处硬度高,加工难度大,按原加工工艺难以满足生产任务。
本文就结合实际生产,提出影响生产的瓶颈问题,分析并解决该问题,总结出一套轴箱体类零件高效加工方法。
二、产品特点及工艺现状轴箱体毛坯通常为铸钢,每月的加工订单量大,加工面的粗糙度要求高,有6个M20的深孔螺纹底孔(Ф17.5mm深60mm、孔口倒角C2)的加工。
加工后需要通过观察倒角是否明显不均匀,以判断螺纹孔内有无铸造缩孔缺陷,各孔无缺陷的正常流转加工,有缺陷的置于待处理区,等待焊补修复后再次加工。
轴箱体加工按既定的工艺流程是直接在加工中心加工,当加工过程中遇到轴箱体螺纹孔部位有缩孔时,就需要焊补修复。
焊补修复的具体流程为:先将有缺陷的螺纹孔部位的缺陷消除,然后焊补修复,焊完退火后再到加工螺纹孔。
从修复到加工成成品,通常需要钻孔加工两次,第一次加工是把有缩孔的螺纹孔扩大,第二次是缺陷处补焊后把螺纹孔加工至成品。
DJ4型机车抱轴箱加工难点及解决方法

现 场 经 验
铁道机车 车辆 工人 第 4 20 年 4月 期 07
文 章 编 号 :0 7— 0 2 2 0 ) 4— 0 1— 5 10 6 4 (0 7 0 0 0 0
D 型 机 车抱 轴 箱 加 工 难点 及 解 决 方 法 J
则 , 电机 安 装 面 上 分 布 有 8个  ̄3 7的 电机 安 装 孔 和 4个 M3 在 3H 0的 拆 卸
孔 . 别 距 抱 轴 箱 中心 2 0、9 l 这些 孔 的精 加 工 , 要 加 工 中心 采 用 分 0 10 im, l 需
一
'
一
维普资讯
心 B轴正 确 旋转 外 , 要 轴 同 时偏 移定 位 才能 加 工 。 需
2 工 艺 装 备 分 析
为 了 满 足 抱 轴 箱 的 加 工 达 到 尺 寸 精 度 和 形 位 公 差 要 求 , 用 选
T K 60 H 4 1 0卧式 加工 中心 , 以及相 配 套 的立 式 夹具 装夹 工 件 对 其 进 行 加工 。 T 4 1 0卧式 加 工 中心 其 数 控 系 统 为 F NU MC, 作 行 程 : : 0 HK 6 O A CO 工 X 200 mm, Y:12 0 mm, :13 0 mm; 位 精 度 : . 0 / 0 0 Z 5 定 0 0 13 0 mm; 作 台 规 格 工 1 0 0 0 mm×1 0 mm, 行 程 范 围和定 位 精 度 均 能 很 好地 满 足 D 抱 轴 箱 的 O0 其 J
图 1 D 抱 轴 箱 J
寸精 度 及形位 公 差要 求 。
1 抱轴 箱 加工 分析
D 抱轴 箱 与 s 抱 轴 箱外 形相 差 很 大 , 圆筒 状 。两 端 轴 承 安 装孑 J s 呈 L、 螺纹 孔等 位 置精 度要 求 较高 , 外形 的 不规 则使 其 在加 工 过程 中 , 装夹 具 的 工 定位 基 准 比较 复杂 。 轴箱 电机安 装座 结 合平 面 的平 面度 要求 为 0 0 l , .5f i m 电机 安装 止 口相 对该 平 面垂 直度 要 求为 0 0 . 3 mm 。安 装 面 上 圆 柱 孑 3 H L ̄ 3 7位 置度 要 求 为
轴箱体加工工艺分析及质量改进
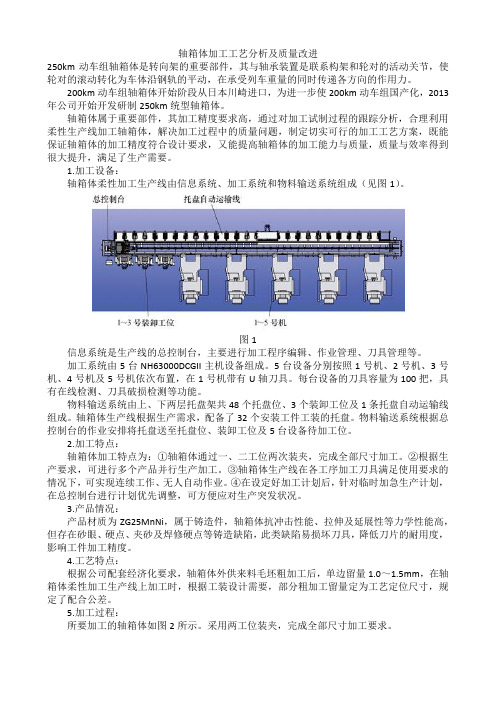
轴箱体加工工艺分析及质量改进250km动车组轴箱体是转向架的重要部件,其与轴承装置是联系构架和轮对的活动关节,使轮对的滚动转化为车体沿钢轨的平动,在承受列车重量的同时传递各方向的作用力。
200km动车组轴箱体开始阶段从日本川崎进口,为进一步使200km动车组国产化,2013年公司开始开发研制250km统型轴箱体。
轴箱体属于重要部件,其加工精度要求高,通过对加工试制过程的跟踪分析,合理利用柔性生产线加工轴箱体,解决加工过程中的质量问题,制定切实可行的加工工艺方案,既能保证轴箱体的加工精度符合设计要求,又能提高轴箱体的加工能力与质量,质量与效率得到很大提升,满足了生产需要。
1.加工设备:轴箱体柔性加工生产线由信息系统、加工系统和物料输送系统组成(见图1)。
图1信息系统是生产线的总控制台,主要进行加工程序编辑、作业管理、刀具管理等。
加工系统由5台NH63000DCGII主机设备组成。
5台设备分别按照1号机、2号机、3号机、4号机及5号机依次布置,在1号机带有U轴刀具。
每台设备的刀具容量为100把,具有在线检测、刀具破损检测等功能。
物料输送系统由上、下两层托盘架共48个托盘位、3个装卸工位及1条托盘自动运输线组成。
轴箱体生产线根据生产需求,配备了32个安装工件工装的托盘。
物料输送系统根据总控制台的作业安排将托盘送至托盘位、装卸工位及5台设备待加工位。
2.加工特点:轴箱体加工特点为:①轴箱体通过一、二工位两次装夹,完成全部尺寸加工。
②根据生产要求,可进行多个产品并行生产加工。
③轴箱体生产线在各工序加工刀具满足使用要求的情况下,可实现连续工作、无人自动作业。
④在设定好加工计划后,针对临时加急生产计划,在总控制台进行计划优先调整,可方便应对生产突发状况。
3.产品情况:产品材质为ZG25MnNi,属于铸造件,轴箱体抗冲击性能、拉伸及延展性等力学性能高,但存在砂眼、硬点、夹砂及焊修硬点等铸造缺陷,此类缺陷易损坏刀具,降低刀片的耐用度,影响工件加工精度。
HXD3型电力机车滚动抱轴箱体组装工艺改进提升

HXD3型电力机车滚动抱轴箱体组装工艺改进提升摘要:HXD3型电力机车是单轴功率1200kW、六轴、交流传动干线货运电力机车,该型机车持续功率7200kW,轴式C0-C0,轴重23t(或25t),最高运行速度120km/h,前后两个转向架结构相同,电机采用滚动抱轴式半悬挂方式。
本文主要是针对HXD3型电力机车驱动轴承组装工艺进行研究,旨在通过对现有组装工艺进行优化和提升,提高组装质量和组装效率。
关键词:滚动抱轴箱体平面度游隙周期专用套筒一、引言HXD3型电力机车的前后两个转向架结构相同,电机采用滚动抱轴式半悬挂方式。
滚动抱轴箱体在与牵引电机连接中起着至关重要的作用,其重要作用主要体现于连接轮对与牵引电机,支撑牵引电机。
机车在高速运行中牵引电机与滚动抱轴箱相对不变,滚动抱轴箱相对于轮对高速运转,主要是通过齿端和非齿端的驱动轴承来实现相对转动,而驱动轴承的游隙的大小在机车运行过程中起着至关重要的作用。
本文以笔者在实际工作中遇到的实际问题出发,通过对现有工艺进行优化调整,来保证轴承工作游隙以达到提升组装效率和减少使用起重机使用率。
二、现有技术现状HXD3型机车轮对主要由车轴、车轮装配、从动齿轮、抱轴箱体等部件组成。
现有HXD3型电力机车轮对和滚抱轴箱组装在组装台位采用立式组装方式进行组装。
在组装的过程中常常出现以下两种情况:一是轴承工作游隙较大,在高速运转时,会使振动较大,降低轴承的使用寿命;二是轴承工作游隙较小,在高速运转时,将增大轴承的摩擦力矩,从而产生大量的热,容易导致轴承发热损坏,这是因为轴承工作游隙较小时,将导致轴承的滚动体与轴承内外圈润滑不良,因干摩擦产生大量的热,产生磨损、胶结、轴承内外圈胀烈等现象,导致轴承损坏。
目前组装工艺简述如下:1.组装驱动轴承外圈,轴承外圈采用冷装法,先将轴承外圈置于工业冰箱中冷冻至规定的温度和时间,待轴承外圈冷冻合格后,将驱动轴承外圈组装至预先检修合格立式放置的滚抱轴箱体的轴承座中,翻转滚抱轴箱体后组装另外一端驱动轴承外圈,检查驱动轴承外圈与滚抱轴箱体轴承座的间隙合格后待组装,在整个作业过程中需注意防护,做好清洁度管控;2.组装齿端驱动轴承内圈,驱动轴承内圈采用热装法,齿端驱动轴承内圈加热至规定温度后热装至车轴,冷却后检查驱动轴承内圈与齿轮端面间隙,符合要求后进行下道工序;3.组装滚抱轴箱体,将滚抱轴箱体用起重机竖直吊起,套在车轴相应位置,组装时注意不得对车轴及驱动轴承造成磕碰伤;4.调整驱动轴承游隙,用两个顶尖顶在滚抱轴箱体下方,顶起滚抱轴箱体约0.5~2mm;5.组装非齿端驱动轴承内圈,驱动轴承内圈采用热装法,非齿端驱动轴承内圈加热至规定温度后热装至车轴;6.用起重机吊起压实胎具放置车轴端面,使压实胎具紧贴在非齿端轴承内圈处,用液压油泵加压使压实胎具及非齿端轴承内圈受轴向推力,用塞尺检查轴承内圈与压实胎具之间间隙,通过检查一圈的间隙后计算加垫量,计算后在对应位置处加垫,加垫后液压油泵加压使压实胎具压实;7.在滚动抱轴箱体上方沿180°方向放置两个百分表,人工推动滚动抱轴箱体,检查转动是否灵活,同时测量非齿端驱动轴承内圈端面的平面度,使平面度≤0.1mm;8.游隙测量,用起重机吊滚动抱轴箱体测量轴承游隙,在达到规定的吨位,游隙符合要求后则进行下一步工序,不合格则按上述第6)条重新进行调整,具体组装见图一。
箱体加工方案改进革新
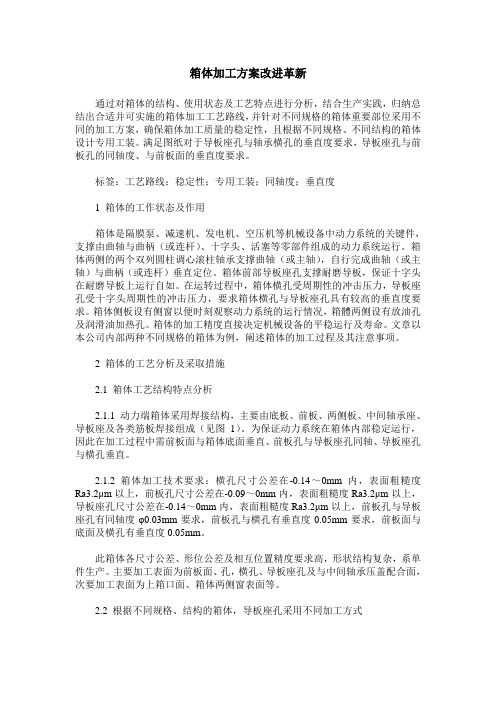
箱体加工方案改进革新通过对箱体的结构、使用状态及工艺特点进行分析,结合生产实践,归纳总结出合适并可实施的箱体加工工艺路线,并针对不同规格的箱体重要部位采用不同的加工方案,确保箱体加工质量的稳定性,且根据不同规格、不同结构的箱体设计专用工装。
满足图纸对于导板座孔与轴承横孔的垂直度要求,导板座孔与前板孔的同轴度、与前板面的垂直度要求。
标签:工艺路线;稳定性;专用工装;同轴度;垂直度1 箱体的工作状态及作用箱体是隔膜泵、减速机、发电机、空压机等机械设备中动力系统的关键件,支撑由曲轴与曲柄(或连杆)、十字头、活塞等零部件组成的动力系统运行。
箱体两侧的两个双列圆柱调心滚柱轴承支撑曲轴(或主轴),自行完成曲轴(或主轴)与曲柄(或连杆)垂直定位。
箱体前部导板座孔支撑耐磨导板,保证十字头在耐磨导板上运行自如。
在运转过程中,箱体横孔受周期性的冲击压力,导板座孔受十字头周期性的冲击压力,要求箱体横孔与导板座孔具有较高的垂直度要求。
箱体侧板设有侧窗以便时刻观察动力系统的运行情况,箱體两侧设有放油孔及润滑油加热孔。
箱体的加工精度直接决定机械设备的平稳运行及寿命。
文章以本公司内部两种不同规格的箱体为例,阐述箱体的加工过程及其注意事项。
2 箱体的工艺分析及采取措施2.1 箱体工艺结构特点分析2.1.1 动力端箱体采用焊接结构,主要由底板、前板、两侧板、中间轴承座、导板座及各类筋板焊接组成(见图1)。
为保证动力系统在箱体内部稳定运行,因此在加工过程中需前板面与箱体底面垂直、前板孔与导板座孔同轴、导板座孔与横孔垂直。
2.1.2 箱体加工技术要求:横孔尺寸公差在-0.14~0mm内,表面粗糙度Ra3.2μm以上,前板孔尺寸公差在-0.09~0mm内,表面粗糙度Ra3.2μm以上,导板座孔尺寸公差在-0.14~0mm内,表面粗糙度Ra3.2μm以上,前板孔与导板座孔有同轴度φ0.03mm要求,前板孔与横孔有垂直度0.05mm要求,前板面与底面及横孔有垂直度0.05mm。
提升机车抱轴箱精加工效率的解决方案

1 序言重载型内燃机车走行部的牵引电动机组装为轴悬式:一端通过滚动抱轴箱与车轴相连,另一端通过吊杆和橡胶垫悬挂在构架的横梁和后端梁上,该类型组装结构被广泛应用于国内重载货运系列机车,因此,抱轴箱是重载型内燃机车走行部的重要零件。
抱轴箱为整体铸钢、外形呈半圆筒形结构(见图1),属薄壁异形件。
图1 机车抱轴箱抱轴箱正反安装面在工艺流程中均需作为安装基准面,正反安装面的平面度≤A、平行度≤B且表面粗糙度值Ra=3.2μm等要求较高,因此一直以来是由龙门式五面体加工中心承担抱轴箱这些部位的精加工(见图2)。
图2 龙门式五面体加工中心加工轴箱体抱轴箱在该设备上精加工工序集中,加工时间长,公司龙门式五面体加工中心已成为抱轴箱制造的加工瓶颈,需要对抱轴箱精加工工艺流程和工艺装备(以下简称工装)进行专题分析和研究,采取应对措施,缓解龙门式五面体加工中心的加工瓶颈,提升抱轴箱精加工效率和加工质量,满足制造需求。
2 精加工过程分析2.1 原精加工工艺流程分析原精加工的工艺流程为:精铣安装面(反)→精铣安装面(正)→划线→钻孔。
需多次将抱轴箱放置于水平位置,用龙门式五面体加工中心进行加工,需正、反两个工位装夹,同时针对抱轴箱背面两端轴承孔处有两只注油孔和传感器安装孔的加工,又需进行一次划线、装夹和加工(该部位若在摇臂钻床加工,质量难以保证;若在龙门式五面体加工中心加工,刀架角度需人工调整),因此,抱轴箱精加工工序加工效率低,有必要对其进行优化。
2.2 对原龙门式五面体加工中心上精加工工装分析对上述工艺流程进行分析可以得出,抱轴箱在龙门式五面体加工中心加工时,工装存在的问题为抱轴箱被反复定位夹紧次数多,作业使用的工装多达3个,费工费时,即工步一为抱轴箱卧放加工(反向),加工内容是加工抱轴箱的螺栓固定平面和悬臂的平面及孔;工步二为抱轴箱仰放加工(正向),应用抱轴箱仰放加工工装,加工内容是加工抱轴箱的主安装平面和两端的外圆及内孔;工步三为抱轴箱在龙门式五面体加工中心利用立式工装,加工抱轴箱的传感器安装孔等。
抱轴箱体精加工工艺的改进
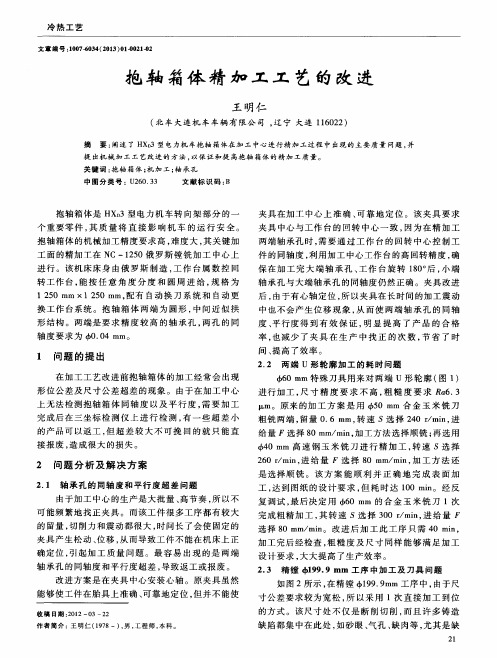
进行 。该 机 床床 身 由俄 罗斯 制 造 , 工 作 台属 数 控 回
转工作台, 能 按 任 意 角 度 分 度 和 圆周 进 给 , 规 格 为 1 2 5 0 m m X 1 2 5 0 m m, 配 有 自动换 刀 系统 和 自动 更
换工 作 台系 统 。抱 轴箱 体 两 端 为 圆形 , 中 间近 似 拱 形结 构 。两端 是 要求 精 度 较 高 的轴 承 孔 , 两 孔 的 同 轴度 要求 为 0 . 0 4 mm。
冷 热 工 艺
文章 编 号 : 1 0 0 7 - 6 0 3 4 ( 2 0 1抱 轴 箱 体 精 加 工 工 艺 的 改 进
王 明 仁
( 北 车大 连机 车车 辆有 限公 司 , 辽 宁 大连 1 1 6 0 2 2 )
摘 要: 阐述 了 H X D 3型 电 力 机 车 抱 轴 箱体 在 加 工 中 心进 行 精 加 工 过 程 中 出现 的主 要 质 量 问题 , 并
工, 达 到 图纸 的设 计 要 求 , 但耗时达 1 0 0 m i n 。经 反 复 调试 , 最 后决 定 用 6 6 0 m m 的合 金 玉 米 铣 刀 1次 完 成粗 精 加工 , 其转速 . s选 择 3 0 0 r / m i n , 进给量 ,
选择 8 0 m m / mi n 。改 进 后 加 工 此 工 序 只需 4 0 mi n , 加 工完 后经 检查 , 粗 糙 度 及 尺 寸 同样 能够 满 足 加 工
工 面 的精 加 工在 N C一1 2 5 0俄 罗斯 镗 铣 加 工 中心 上
夹具 在加 工 中心 上 准 确 、 可 靠 地 定 位 。该 夹具 要 求 夹具 中心与工 作 台 的 回转 中心 一 致 , 因为 在精 加 工 两端 轴 承孔 时 , 需 要 通 过 工作 台 的 回转 中心控 制 工 件 的 同轴 度 , 利用 加工 中心 工作 台 的高 回转 精度 , 确 保在加工完大端轴承孔、 工 作 台旋 转 1 8 0 。 后, 小 端 轴 承 孔与 大端 轴承 孔 的 同轴 度仍 然正 确 。夹具 改进 后, 由于有 心轴 定 位 , 所 以夹 具在 长 时间 的加工 震动
- 1、下载文档前请自行甄别文档内容的完整性,平台不提供额外的编辑、内容补充、找答案等附加服务。
- 2、"仅部分预览"的文档,不可在线预览部分如存在完整性等问题,可反馈申请退款(可完整预览的文档不适用该条件!)。
- 3、如文档侵犯您的权益,请联系客服反馈,我们会尽快为您处理(人工客服工作时间:9:00-18:30)。
抱轴箱加工工艺分析与胎具的改进姓名:宋继勇大连机车车辆有限公司机二车间2011年6月30日滚动抱轴箱体加工工艺与胎具的改进[摘要]一个完整的工件从毛坯加工为成品,需要各个方面的准备,包括:性能良好的机床,完整科学的加工工艺,定位精准的工装胎具,简便实用的刀具。
身为一名机械加工操作者,对待产品加工的时候,要尽量的在保证工件的公差尺寸要求的前提下通过各种有效的手段去提高生产效率,降低生产成本,减少工人的劳动强度,尽可能的去扩大利润,降低成本。
[关键字] :滚动抱轴箱体、一体式工装、销孔定位、加工工艺[前言]:滚动抱轴箱体(以下简称抱轴箱)是属于机车走行部的工件,安装在轮对中间的车轴上,属于转向架组装中的高精度要求部件,其质量的好坏对机车质量有非常重要的影响,其中又以抱轴箱的孔与孔之间公差要求最为严格,因为重点加工部位多为孔径,所以其加工部位的特殊性以及图纸技术要求决定了对其加工必须一步到位,不能够反复对其进行返修处理,否则必然无法保证各个孔的公差要求。
具体外型形状与内部尺寸要求以及技术要求如下:检测发现平行度、对称度、同轴度、表面粗糙度、跳动量普遍存在超差现象,通过分析得出以下几条影响产品质量的主要原因。
1.机床—车间用来加工抱轴箱的机床经过多年使用,精度已经有所下降。
2.工装—目前使用工装为钢件焊接结构,刚性差,为最大影响因素。
针对以上两条主要原因,如果从第一条机床入手解决,会耗费相当大的时间和成本;所以应该从工装上入手解决。
工装胎具一般有两种,一种为钢板焊接胎具:另一种为铸造一体式胎具。
钢板焊接胎具在生产加工中为最常用的工装组合方式,是通过将板件简单的通过焊接方式连接在一起,然后对需要加工的基准面进行加工处理。
钢板焊接胎具具有结构简单,制造方便以及制造工期短的优点,但是相应的也有很多的缺点:1、由于是钢板焊接,胎具底面即基准面容易发生变形;2、胎具上的几个定位基准由于是焊接组合在一起的,时间长了会产生变形,各个定位基准也就不平行和垂直,进而影响了加工工件的精度要求;3、在生产加工中,由于胎具是板件焊接,各个支撑点都比较单薄容易产生震动,这样加工出来的工件容易在吃刀量稍大的时候对表面粗糙度造成影响,容易因为工装的震动而使加工面产生缺陷;由于以上不足,加工出来的工件,平行度、对称度、同轴度、表面粗糙度、跳动量都互相产生了影响,所以产品的合格率必将受到影响,进而影响生产效率。
铸造一体胎具则是先用铸造方式铸造出毛坯,整个工装为一个整体,胎具在加工前,先回火处理,最后进行时效处理,去除它的内部应力,这样处理后的胎具不会因为内部应力的影响而再次变形,然后到数控加工中心进行加工,一次性完成所有的加工尺寸。
铸造一体的胎具缺点在于加工工艺复杂,加工周期长,并且比较沉重,不利于重复安装实用。
但是铸造一体的胎具在加工中心加工后的平行度、垂直度都可以得到保证。
为了便于两种工装胎具使用效果的对比,我们对两个工件分别用两种胎具加工199±0.05、162.5Error!尺寸进行测量的结果如下:X=199±0.05(钢板焊接)Y=162.5Error!X=199±0.05(铸造一体)Y=162.5Error!199.0843162.6087199.0320162.5207 199.0800162.5889199.0293162.5192 199.0924165.5904199.0376162.5184 199.0926162.5695199.0501162.5301 199.1105162.5645199.0174162.5096 199.1081162.5547199.0228162.5001 199.0979162.5616199.0307162.5173 199.0962162.5932199.0428162.5191以上两组数据可以清晰表明铸造一体式胎具加工出的工件的公差要求要远远优于钢板焊接式胎具。
实践证明钢板焊接胎具出现的不足,在铸造一体式胎具上都可以得到有效解决。
二、改进抱轴箱与胎具的定位方式传统的工件与胎具的连接方式为通过螺柱联结,然后通过压板定位,这种连接方式的好处为组成简单,操作方便。
但是不足之处也很明显,没有过多的调节手段,只能通过压板的拧紧力来控制各个方这两个键槽在转向架装配中用与安装其他工件,因此对其的表面粗糙度有一定的要求,所以可以在胎具上加工出跟其相互配合的台面,再利用其工件自身的4个螺栓孔,找好相关位置后在胎具上加工相应的螺栓孔,则成功限制了两个方向的自由度,最后把紧螺栓,X、Y、Z三个方向上的移动和转动的自由度全部被限制。
工件处于完全定位状态。
完全可以保证工件的定位精度和加工精度。
根据这种设计的如下:思想所设计的工装简图为节约成本和方便后续工装制作工序,非关键部位采取减重设计。
关键定位件采用45号钢调质处理进行制作,定位面采取磨削加工,以确保其精度。
后续组装过程严格控制尺寸精度,以确保工装对产品的精确定位,提高加工精度。
三、改进抱轴箱胎具与工作台接合方式上面所讲述的方法是抱轴箱与胎具的定位方式,还有一个是改变胎具与工作台面的接合方式。
在批量进行抱轴箱加工时,由于最主要的技术要求就是孔与孔之间的同轴度要求,公差要求为0.02mm,此要求特别严格,所以每次加工抱轴箱的时候,胎具都需要重新装夹,所有的坐标原点(X轴零点、Y轴零点、Z轴零点、W轴零点)都需要重新进行测量,测量完以后还要进行X轴与Y轴的同轴度检测,因为抱轴箱的两端的孔径是利用工作台的旋转加工完成的,这样一来工件两端孔径在X轴方向上的零点有两个,这两个零点保证抱轴箱的同轴度要求,为了达到要求在每次上胎具以后都要用工件先加工一个尺寸到其他车间利用三坐标测量仪进行检测,检测合格才可以再次加工,如若不然则需要重复上述步骤。
因此每次上一次胎具都会浪费将近3天到一个星期甚至更长的时间,需要不断检测,不断调试,浪费了时间、精力、耽误了生产。
但是如果把胎具固定在工作台的某一个位置上不动的话,虽然每次加工抱轴箱时,就不用需要再去进行测量胎具、检测半成品工件的工序,却会出现其他问题,因为这台机床并非专用机床,因此在加工其他工件的时候,由于胎具会占据一部分工作台的空间,那么就会影响到其他工件的加工。
在经过几次试验后我们采取了一种新的定位方式,就是利用工作台上的四个工艺孔,选出在胎具底部的两个,事先将这两个孔的下半部分用铰刀配铰,钉入销子过盈配合,高度不高于工作台面,我们在这次加工完抱轴箱以后,先不要把胎具卸下来,用台钻在胎具与工作台上钻两个直径为10的销孔(计算好胎具与工作台工艺孔的尺寸)然后用销子压进孔内,这样只要把这次加工抱轴箱的坐标尺寸全部记录下来,等下次加工抱轴箱时只需要把胎具直接用销子定位在工作台的位置上,再用压板固定胎具,即可进行加工,然后直接调用上次各轴坐标即可进行加工,虽然由于不可知因素影响,第一个加工出来的工件还是要进行检测,但是这次检测可以说校验意义大于检测,因此可以在精加工,也可以在半精加工后进行,通过加工后的校验反馈来看,基本上第一个工件就可以达到图纸要求的同轴度要求。
在以后几次加工中这种定位方法非常简便实用,节省了大量的胎具调试装夹和找正的时间,为完成生产任务奠定了基础。
四、改进抱轴箱体的工艺在加工抱轴箱的试运行工艺中工序安排,依照正常的机械加工原则,首先进行端面加工,先用粗端铣刀对轴箱两端面进行半精加工,留量0.2mm,然后换槽铣刀把各个阶台孔的端面铣出来,留量0.2mm ,再换端面精光刀把两侧端面精铣至要求尺寸,换槽铣刀把孔的各个端面加工出来,保证每个阶台面间的距离。
然后用各种尺寸的双刃镗刀把每个孔留量φ0.6mm加工出来,然后再进行精镗孔,钻两端面的孔,攻丝,最后倒角,整个工件则就加工完毕。
在加工完后在机床上进行测量的时候有几个尺寸,例如:φ358.77 5Error!,805Error!等尺寸,上述尺寸在进行加工以及加工后的校验中都在公差要求内,可是工件卸下之后以后再进行测量有的尺寸就会超差,而且都是在下差,经过仔细观察,毛病出现加工顺序不合理,加工后的热量没有有效进行释放,产生了热胀冷缩的现象,为了避免热胀冷缩的发生,现在把加工工艺的顺序颠倒,在本着先面后孔先粗后精的加工基本原则,首先,铣各个大端面留量,粗镗各孔,钻功两侧端面丝孔,然后再精铣每个端面,再精镗,最后再倒角。
工序经过上述调整后,有效的解决了加工下床后尺寸变形的问题。
五、减少抱轴箱体加工的刀具种类上述的改进后的工艺安排虽然从工艺角度上来看没有任何问题了,但是有一个缺点,就是刀具太多,加工端面粗精铣刀共4把,粗精镗孔共需要12把,钻孔攻丝加上其他刀具一共需要27把刀,才能完成一个完整的抱轴箱加工。
由于刀具太多,换刀,磨刀等辅助时间大大延长,来回换刀也给操作者带来了很大的麻烦,首先每换一把刀需要机床停止,卸刀,然后人工将刀具搬下来,然后安装新的刀具,开动机床……每换一次刀具对操作者的体力就会造成一部分损耗。
这样一天下来就只能加工出2件成品,远远达不到生产需要。
由于加工机床是数控控制,具有其他加工设备不具有的先进性及属性特点,所以经过研究试验改变一下它的加工方法,即把直线进给改成曲线进给,利用一把φ80玉米铣刀,这样一把刀具接合数控机床特性即可完成端面粗精加工以及粗镗各孔径,精铣阶台孔端面则利用一把φ80,75°厚30m m的锯齿铣刀代替以前的槽铣刀,这样就可以减少了9把刀具,经过几次试验加工后发现,一把φ80的玉米铣刀完全可以完成工艺要求。
利用坐标直接跑位加工,因此,现在只需要一把玉米铣刀用圆弧差补的方式可以把端面和半精孔全部一次加工出来,这样大大节省了辅助时间同事也节省了刀具损耗,节约了生产成本,提高了生产效率。
为了直观显示,把工件同一部位前后两种加工的部分程序列表如下:1、刀具减少前部分加工程序列表如下:G0 G54 X0 Y0 S300 M03Z0.2 // 端铣刀G0|F300 X195G0 2 X-195G0 X0Z400M05M00 // 换刀S300 M03 // 槽铣刀G0 X-87.2 // 留量G0 | F300 X79G02 I-79Z-80X0Z-109 // 留量G0 | F300 X67.5G0G0 X0Z400M05M00 // 换刀G0 Z0.2 S200 M0.3 // 双刃镗刀(φ361.7)G0| T-60 Z-32.44G0 Z400M05M00 // 换刀S200 M03 // 双刃镗刀(φ358.775)G0 Z-32G01 F60 Z-87.44G0 Z400M00M05 // 换刀S200 M03G0Z-87.44 // 双刃镗刀(φ335)G0 |F60 Z-109G0 Z400M00M05 // 换刀S200 M03 // 双刃镗刀(φ256.6G0 Z-108G0 |F60 Z-130G0 Z400M05M00……由上述部分程序可以看出,换刀次数相当多,这仅仅是一端加工需要的工作,工人体力是有限的,这么频繁的换刀大大的加剧了工人的体力消耗。