纳米结构陶瓷涂层磨削表面残余应力的研究
工程陶瓷磨削表面残余应力与磨削条件及零件性能的关系研究
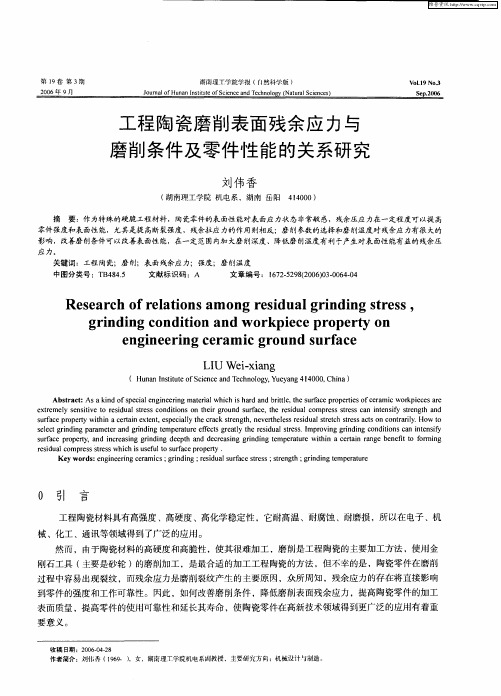
(Hu a n t ueo ce c n e h oo y Yu y n 0 0 Chn n n Isi t f in ea dT c n lg , e a g41 0 . ia) t S 4
Ab t a t Asa k n f p c a e g n e i g mae i 1 ih i h r n rt e t e s ra e p o e t so e a c wo k ic sa e sr c : ido e iI n ie r tr s n a wh c s a d a d b i l. h u f c r p ri f r mi r p e e r t e c
—
口
工程陶瓷材料具有高强度 、高硬度 、高化学稳定性 ,它耐高温 、耐腐蚀 、耐磨损 ,所以在电子 、机
械 、化工 、通讯等领域得到了广泛 的应用。 然而 ,由于陶瓷材料的高硬度和高脆性 ,使其很难加工 ,磨削是工程陶瓷的主要加工方法 ,使用金 刚石工具 ( 主要是砂轮 ) 的磨削加工 ,是最合适的加工工程陶瓷 的方法 ,但不幸的是 ,陶瓷零件在磨削
维普资讯
第 1 9卷 第 3期
20 0 6年 9月
湖南 理工 学 院学报 (f然科 学 版 ) {
J un l f n nIsiueo in ea dT c n lg Naua S in e ) o ra a nt t f e c n e h oo y( t rl ce c s o Hu t Sc
VO .9 No 3 I . 1 S n2 0 e .O 6
工程 陶瓷磨削表面 残余应 力与
磨削条件 及零件性 能 的关系研 究
刘伟香
( 湖南 理工学院 机 电系,湖南 岳 阳 4 4 0 10 0) 摘 要:作 为特殊 的硬脆 工程 材料 ,陶瓷零 件的表 面性能对表面应力状 态非常敏感 ,残余压应力在一定程度可以提 高 零件强度和表 面性能,尤 其是提 高断裂强度 ,残余拉应 力的作 用则相反;磨 削参数的选择和磨 削温度对残余应 力有很 大的 影响 ,改善磨 削条件可 以改善表 面性 能,在一 定范围内加 大磨 削深度 、降低磨 削温度有利于产生对表面性能有益的残余压
结构陶瓷磨削表面损伤的研究

结构陶瓷磨削表面损伤的研究
王西彬;任敬心
【期刊名称】《硅酸盐学报》
【年(卷),期】1997(25)1
【摘要】分析陶瓷磨削过程并通过对Al2O3,Si3N4+ZrO2,PSZ等陶瓷磨削表面及次表面的SEM观察,研究了磨削损伤的形成机理和特征。
结果表明:磨削损伤的主要形式有显微塑性变形磨痕、断裂剥落坑、磨削微裂纹和材料疏松区的塌坑;磨削损伤的特征取决于陶瓷力学性能。
【总页数】5页(P101-105)
【关键词】结构陶瓷;磨削;表面损伤;陶瓷
【作者】王西彬;任敬心
【作者单位】华中理工大学;西北工业大学
【正文语种】中文
【中图分类】TQ174.758
【相关文献】
1.工程陶瓷磨削表面/亚表面损伤的产生及其控制 [J], 孔令志;赵波
2.陶瓷磨削机理及其对表面/亚表面损伤的影响 [J], 朱洪涛;林滨;吴辉;于思远;王志峰
3.工程陶瓷磨削表面/亚表面损伤的产生及其控制 [J], 孔令志;赵波
4.纳米结构陶瓷涂层的外圆磨削力以及磨削表面精度的实验研究 [J], 孟鉴;谢万刚;
张璧
5.ZrO2陶瓷切向超声辅助磨削表面及亚表面损伤机制 [J], 闫艳燕;张亚飞;张兆顷因版权原因,仅展示原文概要,查看原文内容请购买。
工程陶瓷磨削表面残余应力的测量新方法

工程陶瓷磨削表面残余应力的测量新方法工程陶瓷材料由于具有高硬度、高强度、高温耐受性、抗腐蚀等优良性能,在航空航天、电子、医疗等领域得到广泛应用。
然而,在加工过程中,由于工艺参数、机器精度等因素的影响,会导致材料表面产生不同程度的残余应力,进而影响其使用寿命和性能。
传统的残余应力测试方法,如X射线衍射、中子衍射等,存在着测量时间长、需要专业人员、设备昂贵等缺点。
因此,本文提出了一种新的工程陶瓷磨削表面残余应力的测量方法——基于表面变形的
红外热像测量法。
该方法基于工程陶瓷表面的热导率和热膨胀系数与实际表面变
形之间的关系,通过红外热像仪捕捉工件在加工过程中的热辐射,计算表面变形的大小及其分布,进而得到工件表面的残余应力。
该方法具有测量时间短、精度高、无接触、不破坏等优点,适用于各类工程陶瓷材料的表面残余应力测试。
据实验结果表明,该方法能够准确测量工程陶瓷表面的残余应力,并能反映出加工参数对表面残余应力的影响,为工程陶瓷及其制品的加工提供了一种新的残余应力测试手段。
- 1 -。
Al_2O_3_SiC纳米复合陶瓷中的残余应力分析
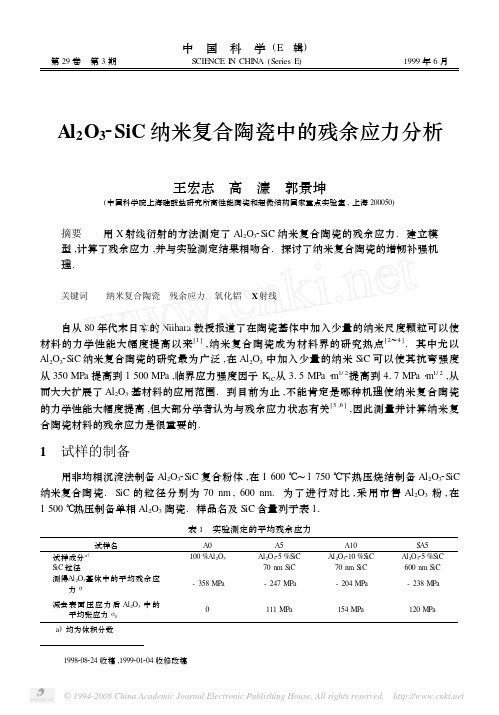
Al 2O 32SiC 纳米复合陶瓷中的残余应力分析王宏志 高 濂 郭景坤(中国科学院上海硅酸盐研究所高性能陶瓷和超微结构国家重点实验室,上海200050)摘要 用X 射线衍射的方法测定了Al 2O 32SiC 纳米复合陶瓷的残余应力.建立模型,计算了残余应力,并与实验测定结果相吻合.探讨了纳米复合陶瓷的增韧补强机理.关键词 纳米复合陶瓷 残余应力 氧化铝 X 射线自从80年代末日本的Niihara 教授报道了在陶瓷基体中加入少量的纳米尺度颗粒可以使材料的力学性能大幅度提高以来[1],纳米复合陶瓷成为材料界的研究热点[2~4].其中尤以Al 2O 32SiC 纳米复合陶瓷的研究最为广泛,在Al 2O 3中加入少量的纳米SiC 可以使其抗弯强度从350MPa 提高到1500MPa ,临界应力强度因子K 1C 从3.5MPa ・m 1/2提高到4.7MPa ・m 1/2,从而大大扩展了Al 2O 3基材料的应用范围.到目前为止,不能肯定是哪种机理使纳米复合陶瓷的力学性能大幅度提高,但大部分学者认为与残余应力状态有关[5,6],因此测量并计算纳米复合陶瓷材料的残余应力是很重要的.1 试样的制备用非均相沉淀法制备Al 2O 32SiC 复合粉体,在1600℃~1750℃下热压烧结制备Al 2O 32SiC 纳米复合陶瓷.SiC 的粒径分别为70nm ,600nm.为了进行对比,采用市售Al 2O 3粉,在1500℃热压制备单相Al 2O 3陶瓷.样品名及SiC 含量列于表1.表1 实验测定的平均残余应力试样名A0A5A10S A5试样成分a (100%Al 2O 3Al 2O 325%S iC Al 2O 3210%S iC Al 2O 325%S iC S iC 粒径70nm S iC 70nm S iC 600nm S iC 测得Al 2O 3基体中的平均残余应力σ-358MPa -247MPa -204MPa -238MPa 减去表面压应力后Al 2O 3中的平均张应力σμ0111MPa 154MPa 120MPa a )均为体积分数 1998208224收稿,1999201204收修改稿中 国 科 学 (E 辑) 第29卷 第3期SCIE NCE I N CHI NA (Series E ) 1999年6月2 残余应力的测定211 X 射线测定应力的基本原理[7]多晶材料中平衡着残余应力时,不同晶粒中同族晶面间距随晶面方位发生规则的变化,平行于应力方位的晶面间距为最小,垂直于应力方向的晶面间距为最大.所以,只要设法测出不同方位上的同族晶面的间距,引用弹性力学中的一些基本关系,可以求得多晶体中所平衡着的残余应力.试样表面某一方向的平均残余应力σx ,可以根据σx =K ・Δ2θΔsin 2ψ(MPa ),(1)通过测定不同方位的同族衍射晶面的2θ值,算得Δ2θ/Δsin 2ψ值,进而求得σx .其中K 为常数,ψ取0°和45°.212 X 射线测定平均残余应力本实验是在Rigaku 公司生产的D/Max 2III A 型衍射仪上进行的,试样与探测器同时以1∶2速度旋转.用Cr 靶,对Al 2O 3的(1010)晶面进行慢扫描,此时d =0.1239nm.取E =402G Pa ,α=8.4×10-6℃-1,ν=0.23,得到结果列于表1.从表1中可以看出,所有试样测得的残余应力都为压应力,并且随着SiC 含量的增加,压应力变小.然而根据Selsing 的关系式(参见(3)式),由于αAl 2O 3大于αSiC ,在Al 2O 3基体中存在的应当是张应力.之所以测得的是压应力,是因为在材料的机械加工过程和冷却过程中都会在表面产生压应力.Chou 等[8]研究了单相Al 2O 3陶瓷和Al 2O 32SiC 纳米复相陶瓷中因机械加工而产生的压应力层的厚度问题,发现压应力层的厚度都在10μm 左右,而这一厚度正是X 射线的探测范围.另外,由于Al 2O 3为各向异性,在不同的晶向上热膨胀系数不同,在冷却的过程中就会在材料中产生压应力;再加上冷却时试样表面和内部存在温度差而在表面产生的压应力,这样实验中测得的应力可以表示为σ=σm +σμ,(2)式中σm 代表因机械加工和快速冷却而在表面产生的压应力,σμ代表因Al 2O 3和SiC 热膨胀失配而产生的残余应力.如果认为在单相Al 2O 3中不存在因两相热膨胀系数不同而导致的残余应力,即σμ=0,则所测得的压应力值为σm 值,即σ=σm =-358MPa.把表1中的σ代入(2)式中,并认为σm =-358MPa ,则得到各个样品的σμ值:A5为111MPa ,A10为154MPa ,S A5为120MPa.可见随着SiC 含量的增加,Al 2O 3中的平均张应力增加.但随着SiC 粒径的变化不大.3 Al 2O 32SiC 纳米复合陶瓷材料中残余应力分析311 复相材料的残余应力理论残余应力影响陶瓷体的微观结构和性能,是非常重要的,因而研究者提出了许多模型和公式进行计算.其中最著名的是由Jorgen Selsing 提出的连续均匀无限大基体中存在单个异相颗粒模型[9]P =Δα・ΔT [(1+ν1)/2E 1]+[(1-2ν2)/E 2],(3)第3期王宏志等:Al 2O 32S iC 纳米复合陶瓷中的残余应力分析201 σr =-2σt =-P ・R 3r 3,(4)其中P 为基体与球形颗粒间因热膨胀系数不同而在界面上产生的应力,Δα为两相的热膨胀系数差,ν为P oiss on 比,E 为弹性模量,下标分别代表基体和颗粒.σr 和σt 分别为在基体中某一点因应力P 的存在而产生的径向应力和切向应力,其中R 为球形颗粒的半径,r 为从颗粒中心到这一点的距离.由(3)式可以预测材料内部不同相颗粒的应力状态,即由材料不同结晶相的热膨胀系数差可判断材料是受张应力还是压应力,对于Al 2O 32SiC 纳米复合陶瓷来说,P =-1300MPa ,SiC 颗粒受压应力,Al 2O 3基体受张应力.但是Selsing 的模型毕竟是一个比较简单的模型,在复合材料中单个分散相颗粒是不会独立存在的,必须考虑到复合材料中的分散相是以一定的尺寸和一定数量引入到基体中的.基体颗粒也不是无限大的,分散相可能分布在基体晶粒内也可能分散在基体晶界上.因而有必要对残余应力进一步分析.312 Al 2O 32SiC 纳米复合陶瓷中残余应力分布残余应力的分布同分散相颗粒之间的距离有关,而分散颗粒的间距又同其数量有关,因此需首先计算每个Al 2O 3晶粒中含有的分散相颗粒(SiC )数目n ・V p V m =f v ,(5)其中n 为每个Al 2O 3晶粒中所含SiC 颗粒数,V p 为单个SiC 颗粒的体积,V m 为单个Al 2O 3晶粒的体积,f v 为SiC 的体积含量.知道了SiC 的粒径以及Al 2O 3晶粒体积(Al 2O 3的晶粒尺寸可以通过电子显微镜观察得到),就可算得n .知道SiC 颗粒的数量,可以进一步求得颗粒之间的距离.SiC 颗粒在Al 2O 3晶粒中的分布是随机的,为了计算颗粒间距的方便,假设SiC 颗粒是以面心堆积的形式排布于Al 2O 3晶粒内.因为单位面心堆积格子中含有4个SiC 颗粒(3颗面心颗粒,1颗顶角颗粒),所以每个Al 2O 3晶粒内含有n /4个单位SiC 面心堆积格子.每个面心格子的体积可以通过(6)式得到.V g =V m n/4.(6)由面心格子的体积可算得面心格子的边长((7)式),即为SiC 颗粒间的平均间距,a =316π3f v ・R.(7)几个样品的SiC 颗粒间距列于表2.尽管(3),(4)式是假设基体无限大的情况下得到的,但相对于Al 2O 3晶粒尺寸,SiC 颗粒间的距离还是很小的,可以近似的认为基体是无限的.Selsing 模型可以计算单个颗粒的应力分布,通过多个颗粒的叠加可以用来计算残余应力的分布.计算一维情况下,Al 2O 3基体中两颗SiC 颗粒O 1,O 2间某一点的残余应力(如图1所示).以A5试样为例,SiC 的含量为5v ol %,SiC 的半径为35nm.首先考虑只受两颗SiC 颗粒的影响,根据(4)式,σt =P2・6ni =1R 3r 3i ,R =35nm ,n =2,r 1=r 2=243/2=122nm ,P 可由(3)式算得为P =-1300MPa ,算得O 1O 2间202 中 国 科 学 (E 辑)第29卷图1 S iC颗粒间距示意图图2 A5试样在一维方向上残余张应力的变化中心点的张应力为31MPa.在一维的尺度上计算O 1O 2间各点的张应力,其张应力的变化如图2所示,最大张应力为650MPa ,最小张应力为31MPa.由此可见,在Al 2O 32SiC 纳米复合陶瓷中,Al 2O 3基体中存在的是张应力,根据应力平衡的条件,SiC 颗粒受压应力.由于张应力的存在,使得基体晶粒强度降低,有利于形成穿晶断裂.由于应力分布并不均匀,张应力在两相的界面附近最大,裂纹进入晶粒以后,将向SiC 颗粒偏转,SiC 的加入起到了裂纹偏转和钉扎的作用.313 一维平均残余应力为了和X 射线测定的应力值进行比较,需要计算一维情况下纳米复合陶瓷中Al 2O 3基体的平均残余应力,计算一维(Y 轴方向)O 1O 2间的平均张应力〈σt 〉为〈σt 〉=∫l +R R 6n i =1σtid r l=∫l +R R 6n i =1P 2R r i 3d r l ,(8)其中l 为两颗SiC 颗粒表面间的距离,l =a -2R ,a 为两颗SiC 颗粒中心距离.把(7)式代入(8)式积分〈σt 〉=P 26n i =011+i 316π3f v 2316π3f v -2-1316π3f v -1+i 316π3f v-42316π3f v -2,(9)从(9)式可以看出,Al 2O 3基体中的平均张应力与SiC 的体积含量f v 有关,随着f v 的增加而增加.把计算所得的数据和试样所测的数据进行对比,列于表2,可见计算值与实测值符合得较好.表2 残余应力实验测定值和计算值样品名A5A10S A5X 射线测定张应力值/MPa 111154120计算所得一维平均张应力/MPa 129177128计算S iC 颗粒间的平均间距/nm2431922084第3期王宏志等:Al 2O 32S iC 纳米复合陶瓷中的残余应力分析203314 二维残余应力图3 二维应力示意图前面的计算过程只考虑了一维的情况,在二维示意图中(图3)可以看到,O 5,O 6颗粒在O 1O 2间所产生的径向压应力的垂直分量(F 1)与O 1,O 2所产生的切向张应力(F 2)方向相反,而O 5,O 6颗粒在O 1O 2间所产生的切向张应力的垂直分量(F 3)与O 1,O 2所产生的切向张应力(F 2)方向相同,因而都可能对O 1O 2间的平均张应力产生影响.以A5为例,F 1在O 1O 2间的平均值〈F 1〉为〈F 1〉=-∫θ-θP R cos θ/(R +l/2)3cos θd θl .(10)F 3在O 1O 2间的平均值〈F 3〉为〈F 3〉=∫θ-θP 2R cos θ/(R +l/2)3sin θd θl .(11)〈F 1〉=-1.91MPa ,〈F 3〉=0.02MPa ,可见O 1O 2垂直方向的SiC 颗粒对X 轴方向上的平均张应力影响是很小的.但是对于X 轴上的某一点影响有可能是很大的.例如在O 1O 2的中点A 处,O 1O 2对其产生的张应力为31MPa ,O 5,O 6在此处产生的径向压应力的垂直分量和切向张应力垂直分量之和为-61MPa ,则此处总的残余应力为-30MPa.由此可以看出尽管从总体上看,SiC 颗粒受压应力,而Al 2O 3基体受平均张应力,但在Al 2O 3晶粒内同时存在着张应力区和压应力区,裂纹在压应力区受阻,而在张应力区扩展,因而裂纹扩展的路径曲折.张应力最大的区域在SiC 颗粒周围,裂纹扩展到此,SiC 颗粒可以起到颗粒钉扎的作用,有利于提高力学性能.315 SiC 颗粒的位置对晶界残余应力的影响图4 晶界应力示意图在基体晶界附近,如果SiC 颗粒位于基体晶内,SiC 颗粒与Al 2O 3基体间因热膨胀系数不同产生的径向压应力传导到晶界上,加强了晶界,有利于抵抗裂纹的扩展.压应力的大小同SiC 到晶界的距离有关,进而同SiC 的含量有关.以A5样品为例,根据表2,SiC 的平均颗粒间距为243nm ,单个SiC 颗粒在晶界上某一点所产生的压应力为-31MPa.但如果SiC 颗粒位于晶界上,因热膨胀系数不同造成的径向压应力促使基体晶界张开,如图4所示,有利于裂纹的扩展,弱化了晶界,在晶界SiC 颗粒某一点上的张应力即为(4)式中的σr =-P =-1300MPa.由于残余应力随距离的增长迅速的减弱,作用距离比较短,因而在晶内型纳米复合材料中晶界附近的SiC 颗粒对晶界的加强作用比较强.总体上看,SiC 的作用可以概括为在基体204 中 国 科 学 (E 辑)第29卷晶粒内部的SiC 颗粒在Al 2O 3中产生平均张应力,使基体晶粒弱化,有利于穿晶断裂,同时压应力区和张应力区并存,使裂纹扩展的路径曲折.而位于基体晶界附近的SiC 颗粒在晶界上产生压应力,强化晶界,有利于造成穿晶断裂,提高力学性能.4 结论通过残余应力分析可知,在Al 2O 32SiC 纳米复合陶瓷中,SiC 颗粒受到压应力,Al 2O 3基体晶粒受到的总的应力为张应力.应力的结果是基体弱化和晶界强化.在Al 2O 3基体晶粒内既存在压应力区也存在张应力区,裂纹通过这些区域时,路线曲折,增韧补强.基体中的张应力随着SiC 含量的增加而增加,基体强度降低,因而SiC 的含量有一最佳值,既可以引起穿晶断裂又不致使基体强度降低太多.参 考 文 献1 Niihara K.New design concept of structural ceramics 2ceramic nanocom posites.J Ceram S oc Jpn ,1991,99:974~9822 S tearns L C ,Zhao J ,Harmer M P.Processing and microstructure development in Al 2O 32S iC nanocom posites.J Eur Ceram S oc ,1992,100:448~4533 王宏志,高 濂,郭景坤,等.晶内型Al 2O 32S iC 纳米复合陶瓷的制备.无机材料学报,1997,12(5):671~6744 王宏志,高 濂,郭景坤,等.Al 2O 3基复合材料中纳米S iC 对微观结构的影响.无机材料学报,1998,13(4):603~6075 Levin I ,K aplan W D ,Brandon D G,et al.E ffect of S iC submicrometer particle size and content on fracture toughness of alumina 2S iC nanocom posites.J Am Ceram S oc ,1995,78:254~2566 Li Z ,Bradt R C.M icromechanical stresses in S iC 2rein forced Al 2O 3com posites.J Am Ceram S oc ,1989,72(1):70~777 杨于兴,漆 睿.X 射线衍射分析.上海:上海交通大学出版社,19948 Chou I A ,Chan H M ,Harmer M P.M aching 2induced surface residual stress behavior in Al 2O 32S iC nanocom posites.J Am Ceram S oc ,1996,79(9):2403~24099 Selsing J.Internal stresses in ceramics.J Am Ceram S oc ,1961,44(8):419第3期王宏志等:Al 2O 32S iC 纳米复合陶瓷中的残余应力分析205 。
一种多陶瓷热障涂层的残余应力检测方法

一种多陶瓷热障涂层的残余应力检测方法在航空航天领域,热障涂层是一种常用的技术,用于保护航空发动机等部件免受高温、高压和腐蚀等环境的影响。
其中,多陶瓷热障涂层是一种性能优异的新型涂层材料,具有高温抗氧化性能和优良的隔热性能。
然而,热障涂层在使用过程中会受到各种力的作用,从而产生残余应力,若残余应力过大会影响其使用寿命和性能。
因此,残余应力的检测对于热障涂层的可靠性至关重要。
目前,常用的残余应力检测方法包括X射线衍射法、中子衍射法、全场光学法等。
然而,这些方法存在一定的局限性,如X射线衍射法需要昂贵的设备和专业的操作人员,中子衍射法对试样尺寸和形状要求较高,全场光学法对试样表面质量要求高。
因此,有必要探索一种简便、快速、准确的多陶瓷热障涂层残余应力检测方法。
近年来,基于声波谐振技术的残余应力检测方法逐渐受到关注。
该方法通过分析多陶瓷热障涂层在声波作用下的谐振频率变化,来间接获取残余应力的大小和分布情况。
与传统方法相比,声波谐振技术具有简单易行、高效准确等优点,适用于多样化的试样形状和尺寸。
具体而言,该方法首先利用压电传感器在试样表面激发声波信号,然后通过信号处理系统测量谐振频率的变化。
根据声波在多陶瓷热障涂层中传播的方式,可以间接推导出残余应力的大小和类型。
通过数学模型的建立和优化算法的应用,可以更准确地分析残余应力的分布情况,为工程师提供可靠的数据支持。
此外,声波谐振技术还可以结合有限元分析等数值模拟方法,对残余应力的影响因素进行深入研究。
通过对多种工况下残余应力的变化规律进行探究,可以为优化设计和改进工艺提供重要参考。
同时,该方法还可以实现在线、实时监测,帮助及时发现和解决问题,提高生产效率和产品质量。
综上所述,基于声波谐振技术的多陶瓷热障涂层残余应力检测方法具有广阔的应用前景和研究价值。
通过不断深入探索和创新,相信这一方法将为航空航天领域的发展和进步做出重要贡献。
纳米结构陶瓷涂层精密磨削的初步分析
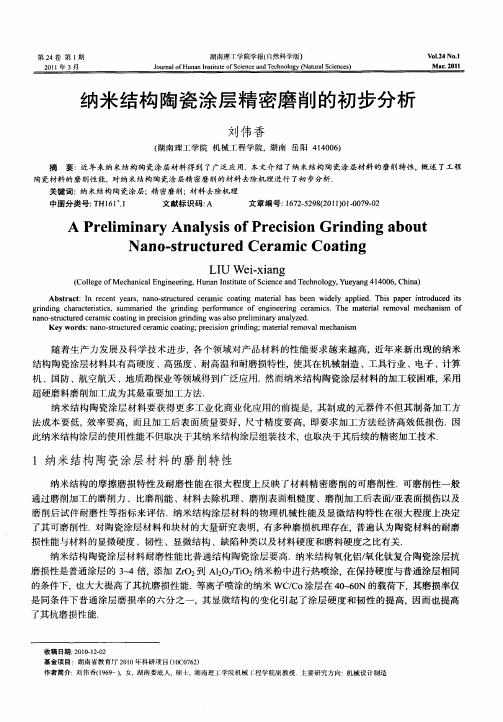
Vb .4 No 1 1 . 2 M a. 0 1 t 2 1
纳米结构 陶瓷涂层精密磨 削 的初步分析
刘伟 香
( 南理 工学 院 机 械工 程学 院,湖南 岳 阳 4 4 0 ) 湖 10 6
摘 要 :近 年 来 纳 米 结 构 陶 瓷 涂 层 材 料 得 到 了广 泛 应 用 .本 文 介 绍 了 纳 米 结构 陶 瓷 涂 层 材 料 的 磨 削特 性 ,概 述 了工 程
陶瓷 材 料 的 磨 削性 能,对 纳 米结 构 陶瓷 涂 层 精 密磨 削的 材 料 去 除 机 理 进 行 了初 步 分 析 . 关 键 词 :纳 米 结 构 陶 瓷 涂层 ; 密磨 削 ; 料 去 除机 理 精 材
中图分类号 : H1 1. T 6 1
文献标识码: A
文章编号 :6 25 9(0 1 1 0 90 17 .2 82 1) . 7-2 0 0
纳米结构 陶瓷涂层材料要获得更多工业化商业化应用的前提是, 其制成 的元器件不但其制备加工方
法成 本要 低 , 率 要高 ,而且 加 工后 表 面质 量要 好 ,尺寸 精度 要 高,即要求 加 工方 法 经济 高效 低 损伤 .因 效 此 纳米结 构涂 层 的使用 性能 不但 取决 于其 纳米 结构涂 层组 装技 术 , 取决 于其 后续 的精 密加工 技 术. 也
纳米结构陶瓷涂层材料耐磨性能比普通结构 陶瓷涂层要高. 纳米结构氧化铝/ 氧化钛复合陶瓷涂层抗 磨损性是普通涂层 的 3 4倍,  ̄ 添加 ZO 到 A 2 3 i2 r2 l / O 纳米粉中进行热喷涂, OT 在保持硬度与普通涂层相同 的条件下, 也大大提高了其抗磨损性能. 等离子喷涂的纳米 WCC 涂层在 4~ 0 /o 0 6N的载荷下, 其磨损率仅 是 同条件 下普 通 涂 层磨 损率 的六 分之 一 ,其显 微 结构 的变化 引起 了涂 层 硬度 和 韧性 的提 高,因而也 提 高
纳米结构陶瓷涂层磨削表面残余应力的研究
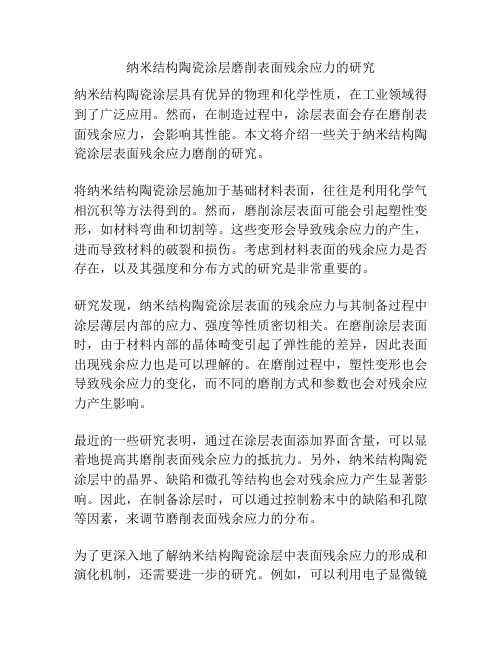
纳米结构陶瓷涂层磨削表面残余应力的研究纳米结构陶瓷涂层具有优异的物理和化学性质,在工业领域得到了广泛应用。
然而,在制造过程中,涂层表面会存在磨削表面残余应力,会影响其性能。
本文将介绍一些关于纳米结构陶瓷涂层表面残余应力磨削的研究。
将纳米结构陶瓷涂层施加于基础材料表面,往往是利用化学气相沉积等方法得到的。
然而,磨削涂层表面可能会引起塑性变形,如材料弯曲和切割等。
这些变形会导致残余应力的产生,进而导致材料的破裂和损伤。
考虑到材料表面的残余应力是否存在,以及其强度和分布方式的研究是非常重要的。
研究发现,纳米结构陶瓷涂层表面的残余应力与其制备过程中涂层薄层内部的应力、强度等性质密切相关。
在磨削涂层表面时,由于材料内部的晶体畸变引起了弹性能的差异,因此表面出现残余应力也是可以理解的。
在磨削过程中,塑性变形也会导致残余应力的变化,而不同的磨削方式和参数也会对残余应力产生影响。
最近的一些研究表明,通过在涂层表面添加界面含量,可以显着地提高其磨削表面残余应力的抵抗力。
另外,纳米结构陶瓷涂层中的晶界、缺陷和微孔等结构也会对残余应力产生显著影响。
因此,在制备涂层时,可以通过控制粉末中的缺陷和孔隙等因素,来调节磨削表面残余应力的分布。
为了更深入地了解纳米结构陶瓷涂层中表面残余应力的形成和演化机制,还需要进一步的研究。
例如,可以利用电子显微镜和成像技术等手段,对材料结构和变形进行更直接的观察和分析。
同时,也需要引入新的理论和模型,以定量预测和描述纳米结构陶瓷涂层中表面残余应力的分布和演化规律。
总之,磨削表面残余应力是影响纳米结构陶瓷涂层性能和寿命的重要因素之一。
通过加强对材料中残余应力的研究,可以指导材料的制备和加工,提升其性能和应用范围。
由于没有数据提供,因此在此无法进行详细分析。
但是可以提供一些可能与磨削表面残余应力相关的数据。
1. 材料结构数据:纳米结构陶瓷涂层材料的晶体结构、晶粒尺寸、形貌等结构参数都对其残余应力产生显著影响。
纳米陶瓷涂层磨削表面残余应力的研究进展
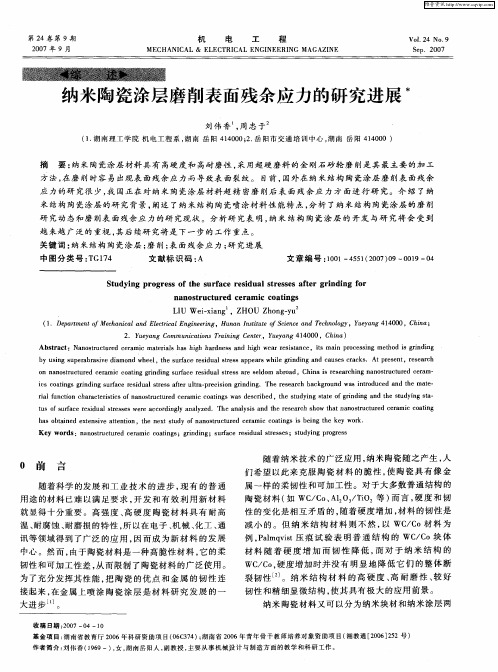
第2 4卷 第 9期
20 0 7年 9 月
机
电
工
程
V0 . 4 NO 9 12 .
S p 20 7 e. 0
M ECHANI CAL & ELECTRI CAL ENGI NEERI NG AGAZI M NE
纳 米 陶瓷 涂 层 磨 削表 面残 余 应 力 的研 究进 展
刘伟 香 ’周 忠 于 ,
( . 南 理 工 学 院 机 电工 程 系 , 南 岳 阳 4 4 0 ; . 阳 市 交通 培训 中 心 , 南 岳 阳 4 4 0 ) 1湖 湖 100 2 岳 湖 100
摘
要: 纳米 陶瓷 涂层材 的金 刚石砂轮 磨 削是其 最主要 的加 工 采
中图分类 号 :G 7 T 14 文献标 识码 : A 文 章 编 号 :01 45 (07 0 — 09 0 10 — 5 120 )9 0 1 — 4
S u i g pr g e s o he s f c e i ua t e s s a t r g i i o t dy n o r s ft ur a e r sd lsr s e fe rnd ng f r
na o t uc u e c r m i o tng n s r t r d e a c c a i s
LI W e — ing U ix a ,ZHOU Zh n — u o gy
( ,D p r e tfMe a i l n l tc l n ie i , u a ntu S i c a d T cn l y uy n 10 0 hn ; 1 eat n o c n a a d Ee r a gne n H n nIs tt o c ne n eh o g ,Y ea g 4 4 0 ,C ia m h c ci E rg i ef e o
- 1、下载文档前请自行甄别文档内容的完整性,平台不提供额外的编辑、内容补充、找答案等附加服务。
- 2、"仅部分预览"的文档,不可在线预览部分如存在完整性等问题,可反馈申请退款(可完整预览的文档不适用该条件!)。
- 3、如文档侵犯您的权益,请联系客服反馈,我们会尽快为您处理(人工客服工作时间:9:00-18:30)。
6 ・ 2
纳米 结构 陶瓷涂层磨 削表面残余应力 的研 究 术
刘 伟香 周 忠 于 ,
(. 1 湖南理 工学院 机械 学院, 南 岳阳 4 40 ;. 阳市交通培训 中心 , 湖 1002 岳 湖南 岳 阳 4 40 100)
摘要 : 用金刚石砂轮对 n WC 1C 涂层精 密磨 削后 , — /2 o 零件表 面存在 残余应 力, 出本 次研 究的 结论 , 出进 一步研 究的 得 提
LI ex a g ,ZH OU o y U W ii n Zh ng u
Ab t a t A trp e ie g i d n — C 1 Co c ai g t imo d w e l,t ee i r sd a t s n t e s r c fp r , e s r c : fe r cs rn i g n W / 2 o t swi d a n h e n h h r s e i u l s e s o h u f e o at t r a s h
纳米结构 WC 1C ( —WC 1C ) /2o n /2 o 涂层材料是近年
磨损性能 、 表面硬度 、 断裂强度 、 疲劳强度 、 腐蚀强度都有
影响。
来国内外迅速发展的一种新型工程材料 , 良的性能使 其优
其在工程上有着』 泛的应用前景。然而正 由于它的高硬
度和 良好 的耐磨 性使 其很 难加 工 , 采用金 刚石 砂 轮 的磨 削 加工 是纳 米结 构 WC 1C 涂 层 的 主要 加 工 方法 , /2 o 由于磨
如何降低磨削表面残余应力 , 提高零件表面质量 , 提高其 使用可靠性和寿命 , 着重要的意义。 有
面残余应力 的影响最大 , 切削应力对残余应 力的影 响
最小 , 磨削热趋 向于在工件表面产生残余拉应力 , 的影 它
响仅 次于 挤压应 力 。
4 )磨削深度的选择对表面残余应力的影 响很大 , 不 管是在垂直磨削方向还是平行磨削方向, 在小磨削深度范
p p rd a n c n ls n b u hssu y i p itdo tte cne t o r e td ,h iet n o rh rs d spop ce n a e rw o cu i sa o tti td ,t one u h o tns ff t rsu y te drci ff te t ywa rse td i o u h o a u
2 磨削表面残余应力值的大小及性质对零件 的表面 )
1 本 次研 究结 论
本次研究基于 目前国内外普遍采用 的卧式平面磨削 方式 , 在低 碳钢基 体 经趟 音速 火焰 喷 涂纳 米结 构 对
围内, 磨削表面残余压应力随着磨 削深度的增加 而增加 , 但随着磨削深度 的继续 增加, 残余压应力增加 的趋势 变
缓。
WC 1 o / 2 涂层材料 的试件进行 磨 削, C 采用德 国 SM N IE S
t i su y t o h s t d o .
.
Ke r y wo ds: a o tu u e e' ni o tn s;g i i g;S  ̄ie r sd lsr se n n si ctr d c l ' al c c ai g rnd n UF c e i ua te s s;r s a c o p c s e e r h pr s e t
内容 , 4- 的研 究 方 向进 行 展 望 。 对 - , a
关键词 : 纳米结构陶瓷涂层 磨 削 表 面残余应 力 研 究展 望 中图分 类号 :H11 T 6 文献标识码 : 文章编号 :02— 86 2 1 )s一 02— 3 A 10 68 (0 1 o 06 0
Ree r h Pr s e t n Grn i g S fc sd a tes sf r Na o tu t r d Ce a i a ig sa c o p cso id n ura e Re i u lS r se o n sr cu e r m c Co t s n
3 残余应力的产生机理是磨粒刃作用引起 的机械应 )
力( 分为挤压应力 和切 削应力 ) 和热 应力 的综 合作用效
应 , 三种应 力 中 , 压应 力产 生残余 压 应力 , 磨 削 表 在这 挤 对
削过程中引入了残余应 力, 使零件磨削表 面存 在残余应 力, 而残余应力是引起零件表面裂纹的主要原因。因此 ,
D 00型 x射线衍射仪测试磨削后平行 、 50 垂直磨削方向的 残余应力 , 通过实验研究结合理论分析, 对纳米结构 WC /
1C 涂 层材 料磨 削 表 面残 余 应 力 进 行 了 研究 , 出 了 磨 2o 得
5 磨削表 面残余压应力 随着 工件速度 的增加而增 ) 加, 但总的增加速度较缓慢 , 不象磨削深度对残余应力 的
影 响那 么大 。
6 磨削表面残余压应力 随着磨 粒尺寸 的减小而增 )
加 , 变化 不是很 大 。 但 7 树脂 粘结 剂砂 轮 比陶 瓷粘 结 剂对磨削表面残余应力 的影 响规律 , 结合 磨削表面
S M观察 , E 充分揭示了残余应力的产生机理 , 建立 了磨削
参数与磨削表面残余应力的数学模型并进行 了验证。通 过本次研究得出如下结论 : 1磨削表面残余应力 由因喷涂引起 的原始残余应 )
面残余压应力值要大。 8 对同一种砂轮来说 , ) 垂直方 向的残余 压应力 比水
平方向的残余压应力值要大, 但相差不是很悬殊 。
力 c 和磨削过程引起 的磨 削残余应力 A - r n o两部分组成 , 通过实验结果得 出, 原始残余应力相对磨削表面残余应力 来说不是很大。磨削表面残余应力 O全部都是压应力。 -