汽车制动系统计算
制动系统设计规范
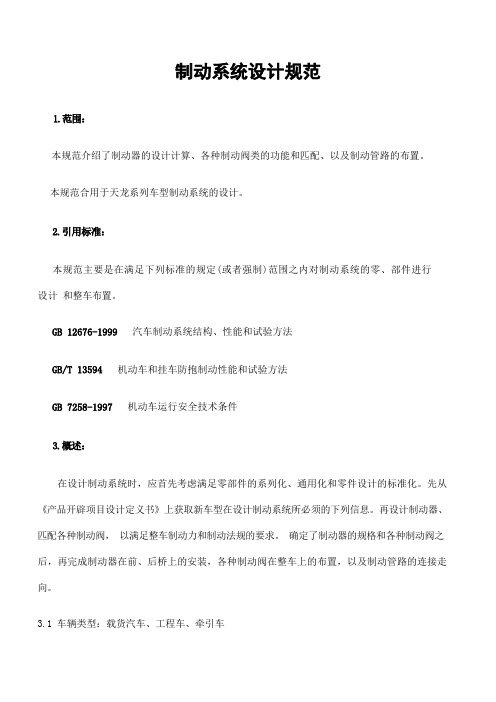
本规范介绍了制动器的设计计算、各种制动阀类的功能和匹配、以及制动管路的布置。
本规范合用于天龙系列车型制动系统的设计。
本规范主要是在满足下列标准的规定(或者强制)范围之内对制动系统的零、部件进行设计和整车布置。
汽车制动系统结构、性能和试验方法机动车和挂车防抱制动性能和试验方法机动车运行安全技术条件在设计制动系统时,应首先考虑满足零部件的系列化、通用化和零件设计的标准化。
先从《产品开辟项目设计定义书》上获取新车型在设计制动系统所必须的下列信息。
再设计制动器、匹配各种制动阀,以满足整车制动力和制动法规的要求。
确定了制动器的规格和各种制动阀之后,再完成制动器在前、后桥上的安装,各种制动阀在整车上的布置,以及制动管路的连接走向。
3.1 车辆类型:载货汽车、工程车、牵引车3.2 驱动形式:4×2、6×4、8×43.3 主要技术及性能参数:长×宽×高、轴距、空/满载整车重心高坐标、轮距、整备质量、额定载质量、总质量、前/后桥承载吨位、 (前/后)桥空载轴荷、 (前/后)桥满载轴荷、最高车速、最大爬坡度等。
3.4 制动系统的配置:双回路气/液压制动、弹簧制动、鼓/盘式制动器、防抱制动系统、手动/自动调整臂、无石棉磨擦衬片、感载阀调节后桥制动力、缓速器、排气制动。
本规范仅对鼓式制动器的各主要元件和设计计算加以阐述,盘式制动器的选型和计算将暂不列入本规范的讨论范围之内。
4.1 鼓式制动器主要元件:4.1.1 制动鼓:由于铸铁耐磨,易于加工,且单位体积的热容量大,所以,重型货车制动鼓的材料多用灰铸铁。
不少轻型货车和轿车的制动鼓为组合式,其圆柱部份用铸铁,腹板则用钢压制件。
制动鼓在工作载荷下将变形,使蹄、鼓间单位压力不均,带来少许踏板行程损失。
制动鼓变形后的不圆柱度过大,容易引起制动时的自锁或者踏板振动。
所以,在制动鼓上增加肋条,以提高刚度和散热性能。
中型以上货车,普通铸造的制动鼓壁厚为 13~18㎜。
汽车制动系统~毕业设计论文(论文)
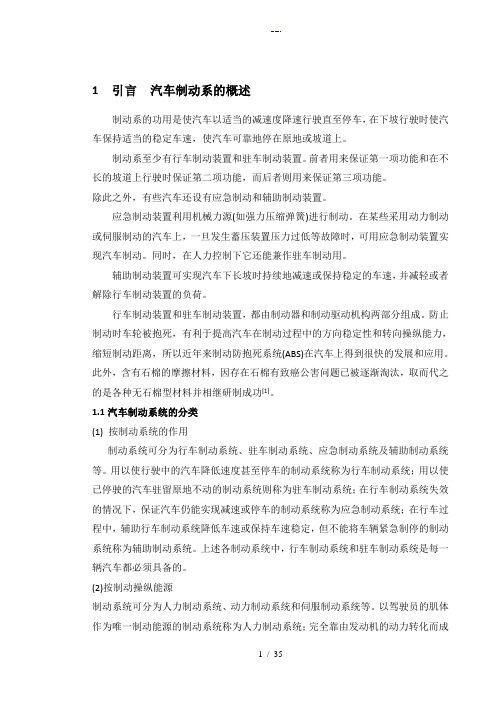
1 引言汽车制动系的概述制动系的功用是使汽车以适当的减速度降速行驶直至停车,在下坡行驶时使汽车保持适当的稳定车速,使汽车可靠地停在原地或坡道上。
制动系至少有行车制动装置和驻车制动装置。
前者用来保证第一项功能和在不长的坡道上行驶时保证第二项功能,而后者则用来保证第三项功能。
除此之外,有些汽车还设有应急制动和辅助制动装置。
应急制动装置利用机械力源(如强力压缩弹簧)进行制动。
在某些采用动力制动或伺服制动的汽车上,一旦发生蓄压装置压力过低等故障时,可用应急制动装置实现汽车制动。
同时,在人力控制下它还能兼作驻车制动用。
辅助制动装置可实现汽车下长坡时持续地减速或保持稳定的车速,并减轻或者解除行车制动装置的负荷。
行车制动装置和驻车制动装置,都由制动器和制动驱动机构两部分组成。
防止制动时车轮被抱死,有利于提高汽车在制动过程中的方向稳定性和转向操纵能力,缩短制动距离,所以近年来制动防抱死系统(ABS)在汽车上得到很快的发展和应用。
此外,含有石棉的摩擦材料,因存在石棉有致癌公害问题已被逐渐淘汰,取而代之的是各种无石棉型材料并相继研制成功[1]。
1.1汽车制动系统的分类(1) 按制动系统的作用制动系统可分为行车制动系统、驻车制动系统、应急制动系统及辅助制动系统等。
用以使行驶中的汽车降低速度甚至停车的制动系统称为行车制动系统;用以使已停驶的汽车驻留原地不动的制动系统则称为驻车制动系统;在行车制动系统失效的情况下,保证汽车仍能实现减速或停车的制动系统称为应急制动系统;在行车过程中,辅助行车制动系统降低车速或保持车速稳定,但不能将车辆紧急制停的制动系统称为辅助制动系统。
上述各制动系统中,行车制动系统和驻车制动系统是每一辆汽车都必须具备的。
(2)按制动操纵能源制动系统可分为人力制动系统、动力制动系统和伺服制动系统等。
以驾驶员的肌体作为唯一制动能源的制动系统称为人力制动系统;完全靠由发动机的动力转化而成图 2 双回路液压系统中的串联式双腔制动主缸 1-套;2-密封套;3-第一活塞;4-盖;5-防动圈;6、13-密封圈 7-垫片;8-挡片;9-第二活塞;10-弹簧;11-缸体;12-第二工作室 14、15-进油孔;16-定位圈;17-第一工作室;18-补偿孔;19-回油孔 图1 制动系统的组成示意图 1-前轮盘制动器;2-制动总泵;3-真空助力器;4-制动踏板机构;5-后轮鼓式制动;6-制动组合阀;7-制动警的气压或液压形式的势能进行制动的系统称为动力制动系统;兼用人力和发动机动力进行制动的制动系统称为伺服制动系统或助力制动系统[2]。
车辆工程毕业设计(论文)ca1041轻型商用车制动系统设计【全套图纸】
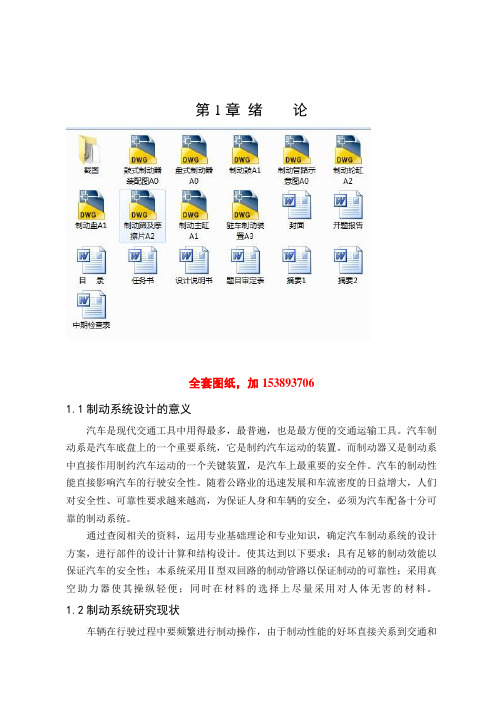
第1章绪论全套图纸,加1538937061.1制动系统设计的意义汽车是现代交通工具中用得最多,最普遍,也是最方便的交通运输工具。
汽车制动系是汽车底盘上的一个重要系统,它是制约汽车运动的装置。
而制动器又是制动系中直接作用制约汽车运动的一个关键装置,是汽车上最重要的安全件。
汽车的制动性能直接影响汽车的行驶安全性。
随着公路业的迅速发展和车流密度的日益增大,人们对安全性、可靠性要求越来越高,为保证人身和车辆的安全,必须为汽车配备十分可靠的制动系统。
通过查阅相关的资料,运用专业基础理论和专业知识,确定汽车制动系统的设计方案,进行部件的设计计算和结构设计。
使其达到以下要求:具有足够的制动效能以保证汽车的安全性;本系统采用Ⅱ型双回路的制动管路以保证制动的可靠性;采用真空助力器使其操纵轻便;同时在材料的选择上尽量采用对人体无害的材料。
1.2制动系统研究现状车辆在行驶过程中要频繁进行制动操作,由于制动性能的好坏直接关系到交通和人身安全,因此制动性能是车辆非常重要的性能之一,改善汽车的制动性能始终是汽车设计制造和使用部门的重要任务。
当车辆制动时,由于车辆受到与行驶方向相反的外力,所以才导致汽车的速度逐渐减小至零,对这一过程中车辆受力情况的分析有助于制动系统的分析和设计,因此制动过程受力情况分析是车辆试验和设计的基础,由于这一过程较为复杂,因此一般在实际中只能建立简化模型分析,通常人们主要从三个方面来对制动过程进行分析和评价:(1)制动效能:即制动距离与制动减速度;(2)制动效能的恒定性:即抗热衰退性;(3)制动时汽车的方向稳定性;目前,对于整车制动系统的研究主要通过路试或台架进行,由于在汽车道路试验中车轮扭矩不易测量,因此,多数有关传动系!制动系的试验均通过间接测量来进行汽车在道路上行驶,其车轮与地面的作用力是汽车运动变化的根据,在汽车道路试验中,如果能够方便地测量出车轮上扭矩的变化,则可为汽车整车制动系统性能研究提供更全面的试验数据和性能评价。
面积承受力计算公式

面积承受力计算公式一、引言在物理学中,面积承受力是一个重要的概念。
它指的是一个物体上单位面积所承受的力的大小。
在工程学和力学设计中,了解和计算面积承受力是至关重要的,因为它可以帮助我们确定材料的强度和结构的稳定性。
本文将介绍面积承受力的计算公式以及其在实际应用中的意义。
二、面积承受力的计算公式面积承受力的计算公式为:F = P/A其中,F表示面积承受力,P表示作用于物体上的力的大小,A表示物体的面积。
该公式表明,面积承受力与作用力的大小成正比,与物体的面积成反比。
三、面积承受力的意义1. 材料的强度评估根据面积承受力的计算公式,我们可以评估材料的强度。
当一个物体上的面积较大时,在相同的力作用下,面积承受力就会较小,这意味着该材料具有较高的强度。
而当面积较小时,面积承受力就会较大,这表明材料的强度较低。
通过计算面积承受力,我们可以选择合适的材料来满足工程设计的要求。
2. 结构的稳定性在建筑和工程设计中,面积承受力的计算也有助于评估结构的稳定性。
当一个建筑物或桥梁承受外力时,我们需要确定结构上各个部分的面积承受力是否均衡,以确保结构的稳定性。
通过计算面积承受力,我们可以发现并解决结构中可能存在的问题,从而提高建筑物或桥梁的安全性。
四、面积承受力的应用举例1. 汽车制动系统在汽车制动系统中,面积承受力的计算非常重要。
制动器通过施加力来减速汽车,而制动器与车轮之间的接触面积会影响制动效果。
如果接触面积较小,那么面积承受力就会较大,制动效果可能不理想。
因此,在设计制动系统时,需要考虑接触面积的大小,以确保制动效果的稳定和可靠。
2. 建筑物结构设计在建筑物结构设计中,面积承受力的计算也是必不可少的。
例如,在设计一个大型屋顶时,需要考虑屋顶的承重能力,以确保它能够承受雨水、风力以及其他外部压力。
通过计算面积承受力,我们可以确定需要使用的材料和结构的大小,从而保证屋顶的稳定性和安全性。
五、总结面积承受力的计算公式为F = P/A,它可以帮助我们评估材料的强度和结构的稳定性。
毕业设计论文—汽车制动系统的设计
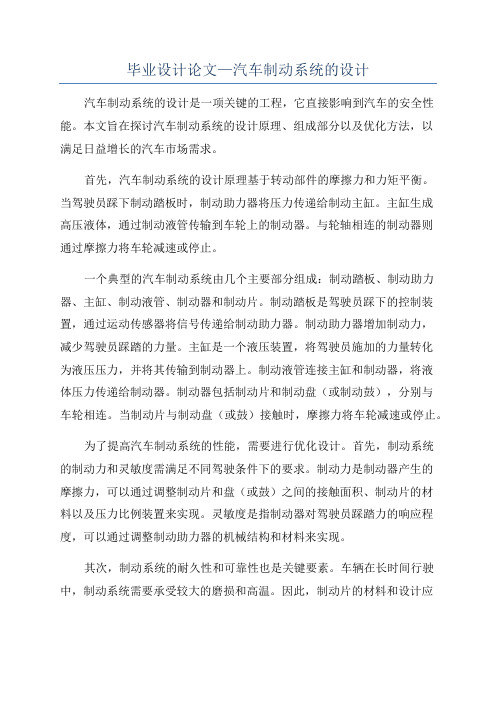
毕业设计论文—汽车制动系统的设计汽车制动系统的设计是一项关键的工程,它直接影响到汽车的安全性能。
本文旨在探讨汽车制动系统的设计原理、组成部分以及优化方法,以满足日益增长的汽车市场需求。
首先,汽车制动系统的设计原理基于转动部件的摩擦力和力矩平衡。
当驾驶员踩下制动踏板时,制动助力器将压力传递给制动主缸。
主缸生成高压液体,通过制动液管传输到车轮上的制动器。
与轮轴相连的制动器则通过摩擦力将车轮减速或停止。
一个典型的汽车制动系统由几个主要部分组成:制动踏板、制动助力器、主缸、制动液管、制动器和制动片。
制动踏板是驾驶员踩下的控制装置,通过运动传感器将信号传递给制动助力器。
制动助力器增加制动力,减少驾驶员踩踏的力量。
主缸是一个液压装置,将驾驶员施加的力量转化为液压压力,并将其传输到制动器上。
制动液管连接主缸和制动器,将液体压力传递给制动器。
制动器包括制动片和制动盘(或制动鼓),分别与车轮相连。
当制动片与制动盘(或鼓)接触时,摩擦力将车轮减速或停止。
为了提高汽车制动系统的性能,需要进行优化设计。
首先,制动系统的制动力和灵敏度需满足不同驾驶条件下的要求。
制动力是制动器产生的摩擦力,可以通过调整制动片和盘(或鼓)之间的接触面积、制动片的材料以及压力比例装置来实现。
灵敏度是指制动器对驾驶员踩踏力的响应程度,可以通过调整制动助力器的机械结构和材料来实现。
其次,制动系统的耐久性和可靠性也是关键要素。
车辆在长时间行驶中,制动系统需要承受较大的磨损和高温。
因此,制动片的材料和设计应具有良好的耐磨和耐高温性能。
此外,制动液管和连接件应具有高强度和密封性,以防止液压泄漏和系统失效。
最后,制动系统的安全性是设计的重要目标。
为了提高系统的安全性,制动系统应具有防抱死制动系统(ABS)和电子制动力分配系统(EBD)。
ABS系统能够避免车轮因制动过度而导致车辆失控,而EBD系统能够根据不同车轮的情况分配适当的制动力,以实现最佳制动性能。
2章汽车制动系统

三、制动主缸
1、单腔制动主缸
四、制动轮缸
双活塞式制动轮缸:
说明:
各类汽车为了使前后车轮的制动力矩能与其实际载荷及附着 力相适应,以获得最大的制动效果,多采用不同活塞直径的轮 缸或不同型式、不同尺寸的制动器。货车制动时前轮实际载荷 及附着力仍小于后轮,所以后轮缸直径大于前轮缸直径。轿车 制动时,因质量转移较大,前轮实际载荷大于后轮,故前轮缸 直径大于后轮缸直径,且装用高制动性能的制动器。
制动踏板机构 15、16-制动轮缸
真空式
这种伺服制动系比人力液压制动系多一套真空伺服系统, 供能装置包括:由发动机进气管8(真空源)、真空单向阀9、 真空罐10组成。 控制装置:真空增压器控制阀6; 传动装置:伺服气室7; 中间传动液压缸:辅助缸4。。 真空增压器:辅助缸、真空伺服气室和控制阀通常组合装配 成一个部件。 工作原理
货车制动时前轮实际载荷及附着力仍小于后轮,所以后轮缸 直径大于前轮缸直径。
轿车制动时,因质量转移较大,前轮实际载荷大于后轮,故 前轮缸直径大于后轮缸直径,且装用高制动性能的制动器。
真空式
红旗CA7220型轿车真空助力伺服制动系示意图 动画演示 真空助力器结构
气压助力伺服制动系统
为了兼取气压制动和液压制动两者的优点,不少重型汽车采 用了空气液压制动传动装置。
4.制动平顺性好
5.散热性好。连续制动时,制动鼓的温度高达400 ° C,摩 擦片的抗“热衰退”能力要高(摩擦片抵抗因高温分解变质引起 的摩擦系数降低);水湿后恢复能力快。
6.对有挂车的制动系,还要求挂车的制动作用应略早于主车; 挂车自行脱挂时能自动进行应急制动。
第二节 制动器
按旋转元件的形状的不同,汽车制动器可分为鼓-蹄式和盘 式两大类。
汽车制动系统设计说明书
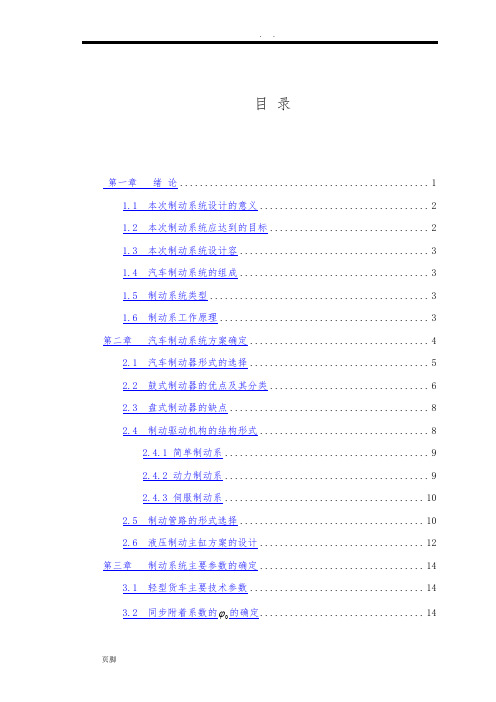
目录第一章绪论 (1)1.1 本次制动系统设计的意义 (2)1.2 本次制动系统应达到的目标 (2)1.3 本次制动系统设计容 (3)1.4 汽车制动系统的组成 (3)1.5 制动系统类型 (3)1.6 制动系工作原理 (3)第二章汽车制动系统方案确定 (4)2.1 汽车制动器形式的选择 (5)2.2 鼓式制动器的优点及其分类 (6)2.3 盘式制动器的缺点 (8)2.4 制动驱动机构的结构形式 (8)2.4.1 简单制动系 (9)2.4.2 动力制动系 (9)2.4.3 伺服制动系 (10)2.5 制动管路的形式选择 (10)2.6 液压制动主缸方案的设计 (12)第三章制动系统主要参数的确定 (14)3.1 轻型货车主要技术参数 (14)的确定 (14)3.2 同步附着系数的3.3 前、后轮制动力分配系数 的确定 (15)3.4 鼓式制动器主要参数的确定 (16)3.5 制动器制动力矩的确定 (18)3.6 制动器制动因数计算 (19)3.6.1 制动器制动因数计算 (19)3.6.1 制动器制动因数计算 (20)3.7 鼓式制动器零部件的结构设计 (21)第四章液压制动驱动机构的设计计算 (24)4.1 制动轮缸直径d的确定 (24)的计算 (25)4.2 制动主缸直径d4.3 制动踏板力F (26)P4.4 制动踏板工作行程Sp (26)第五章制动性能分析 (27)5.1 制动性能评价指标 (27)5.2 制动效能 (27)5.3 制动效能的恒定性 (27)5.4 制动时汽车的方向稳定性 (28)5.5 前、后制动器制动力分配 (28)5.5.1 地面对前、后车轮的法向反作用力 (29)5.6 制动减速度j (29)5.7 制动距离S (29)5.8 摩擦衬片(衬块)的磨损特性计算 (30)5.9 汽车能够停留在极限上下坡角度计算 (32)第六章总结 (33)参考文献 (34)一.绪论汽车工业是一个综合性产业,汽车工业的生产水平,能够代表一个国家的整个工业水平,汽车工业的发展,能够带动各行各业的发展,进而促进我国工业生产的总体水品。
综合驻车式卡钳的驻车制动系统校核计算

综合驻车式卡钳的驻车制动系统校核计算应卓凡【摘要】为提升使用后盘式制动器汽车的驻车制动性能,叙述了球盘式综合驻车制动钳的工作原理,分析了汽车驻车性能的影响因素.利用驻车操纵手柄每齿提供的拉丝行程计算制动钳驻车力,再由此反推驻车手柄操纵力,得到汽车驻车手柄的转动齿数、操纵力与制动钳驻车力的对应关系.通过与实车驻车性能试验结果对比,验证了计算方法的正确性.该方法适用于开发前期驻车制动系统的校核计算与调整优化.【期刊名称】《汽车工程师》【年(卷),期】2014(000)006【总页数】4页(P31-33,36)【关键词】IPB卡钳;球盘式;驻车;校核计算【作者】应卓凡【作者单位】江淮汽车股份有限公司技术中心【正文语种】中文因盘式制动器相对于鼓式制动器有众多优点,目前乘用车后轮制动器广泛采用盘式制动器[1]。
但由于驻车功能的需要,须加装驻车制动机构,主要有盘中鼓和综合驻车式卡钳(Integral Parking Brake,简称IPB 卡钳)2 种方案,前者原理与鼓式制动器相同,后者通过集成在制动钳内的特殊驻车机构,将输入轴驻车驱动杆的旋转运动转变为活塞的直线运动,从而夹紧制动盘实现驻车。
IPB 卡钳不需要独立的驻车制动器,因此更为紧凑和经济[2-3]。
文章针对IPB 卡钳的特点,在整车开发前期计算校核汽车驻车制动性能,并进行了实车验证。
1 法规要求制动性能是汽车的重要使用性能之一,包括行车制动性能和驻车制动性能。
汽车驻车制动系统可使已停驶的汽车长时间可靠地停驻在原地或一定坡道上,并具备帮助汽车在坡路上起步和必要时辅助制动的功能[4]。
GB 7258—2012,GB 21670—2008,GB 12676—1999 等标准均对车辆驻坡度和驻车手柄操纵力提出明确要求[5-7],如表 1所示。
表1 乘用车驻车性能的国标要求性能评价项目标准操纵力(手刹)/N GB 21670≤400 GB 12676≤400操纵行程(有足够储备行程)images/BZ_33_1576_2642_1939_2759.png驻坡度(上/下坡)/%images/BZ_33_1576_2804_1939_2922.pngGB 7258≤400≤2/3 操纵装置全行程(一般要求)20(空载)20(满载)20(满载)2 驻车原理2.1 IPB卡钳驻车工作原理IPB 卡钳兼具行车制动和驻车制动双重功能,前者通过液压传动机构实现制动,而后者则采用机械杠杆机构实现制动。
- 1、下载文档前请自行甄别文档内容的完整性,平台不提供额外的编辑、内容补充、找答案等附加服务。
- 2、"仅部分预览"的文档,不可在线预览部分如存在完整性等问题,可反馈申请退款(可完整预览的文档不适用该条件!)。
- 3、如文档侵犯您的权益,请联系客服反馈,我们会尽快为您处理(人工客服工作时间:9:00-18:30)。
制动系统方案设计计算说明书P201-NAM-SD-DP-G3-22、2
.2
.
2.
序号
3踏板
5驻车系统驻车手柄杠杆比总泵缸径mm第一腔行程mm
4真空助
力器
尺寸助力比总泵类型
制动踏板杠杆比
前制动器
结构制动盘外径mm
驻车拉杆机构杠杆比分泵直径mm行车效能因数
摩擦片有效半径mm
车轮滚动半径Rd(mm)
质心距前轴距离a(mm)质心距后
轴距离b(mm)质心高度hg(mm)质量m(kg)
车型载荷
表2 设计方案参数1标杆分泵直径mm满载方案轴距L(mm)空载项目
第二腔行程mm2后制动器
结构制动鼓内径mm
驻车效能因数
©版权归江淮汽车股份有限公司所有 未经授权禁止复制第 1 页,共 13 页制动系统方案设计计算说明书P201-NAM-SD-DP-G3-22.整
车
2.
2
Z1
—
Z2L
—a
—b
—h
g
—G
—m
—
静态驻坡驻坡度≥18%
制动减速度(m/s2)≥2.2
制动减速度(m/s2)≥2.2满载失效制动
(70km/h)
前失效制动距离(m)≤95.7
后失效制动距离(m)≤95.7
后失效制动距离(m)≤95.7
空载失效制动
(70km/h)
前失效制动距离(m)≤95.7制动减速度(m/s2)≥2.2
满载制动(80km/h)
冷态制动距离-O型(m)≤61.2
制动减速度(m/s2)≥5.0
设计要求空载制动(80km/h)冷态制动距离-O型(m)≤61.2制动减速度(m/s2)≥5.0图1 整车受力简图制动减速度(m/s2)≥2.2项目制动安全性能法规要求
©版权归江淮汽车股份有限公司所有 未经授权禁止复制第 2 页,共 13 页制动系统方案设计计算说明书P201-NAM-SD-DP-G3-2整车
前、
其中 、P1
、—
—d1
、—
——
—r
、—
—B
F1
—
—R—
—制动
整车
其中
L
—b
—h
g
—β
—根
据表4 各附着系数路面下空、满载前、后轴理想制动力
n1、n2
RrBFndpF111211142
gifhLGZFb1
girhaLGZF2
0ghbL
0
211uuuFFF
1F2F
RrBFndpF222222242
©版权归江淮汽车股份有限公司所有 未经授权禁止复制第 3 页,共 13 页制动系统方案设计计算说明书P201-NAM-SD-DP-G3-2根据
此时
车型
标杆名称代号图2 车型的I曲线与β线压强MPa标杆12空载同步附着系数满载同步附着系数表6 制动力分配系数和同步附着系数方案
678
34
9101112
5方案选配方案(四轮盘式)表5 各管路压力下前后制动器制动力irFifF
0'0
irFifFifF
irF
©版权归江淮汽车股份有限公司所有 未经授权禁止复制第 4 页,共 13 页制动系统方案设计计算说明书P201-NAM-SD-DP-G3-2通过
2前
、
式中———
——
——
——
—整
车
图3 利用附着系数与制动强度的关系曲线
2、在满载状态下,地面附着系数为0.8,标杆管路压力达到12MPa,方案管路压力达到10MPa,选配方案管路压力达到11MPa,制动器发生抱死,此时前轴早于后轴抱死,整车保持稳定性。
1、在空载状态下,地面附着系数为0.8,标杆管路压力达到6MPa,管路压力达到5MPa,选配方案管路压力达到5MPa,制动器发生抱死,此时后轴早于前轴抱死,这时整车稳定性非常差。需要ABS进行调节。
)(111gZXbfzhbLzFF
)(1)1(22gZXbrzhaLzFF
frabz
©版权归江淮汽车股份有限公司所有 未经授权禁止复制第 5 页,共 13 页制动系统方案设计计算说明书P201-NAM-SD-DP-G3-2 2(
1
制动在
车制
动的
情式
中
(2
根据GB 12676-1999制动法规要求: 1)当制动强度z处于0.2~0.8之间时,制动强度z≥0.1+0.85(φ-0.2)。 2)当制动强度z处于0.15~0.3之间时,各轴的附着系数利用曲线位于由φ=z+0.08和φ=z-0.08确定的两条平行于理想附着系数利用曲线之间,其中后轴附着系数利用曲线允许与直线φ=z-0.08相交; 3)当制动强度z处于0.3~0.5和0.5~0.61之间时,分别满足公式φ≤z+0.08和φ≤2×(z-0.21) 由上图可以得出结论:当制动强度z处于0.3~0.5和0.5~0.61之间时,标杆满载前轴利用附着系数不满足法规要求,必须通过ABS电磁阀调节制动力分配,才能满足法规要求。P201方案前制动器对标,也须通过ABS电磁阀调节制动力分配。
路面峰值附着系数的利用,决定于ABS的匹配,且其值大于路面滑动附着系数;在法规要求的最大踏板力作用下,制动器制动力应远大于任何路面附着系数下的地面制动力;所以,可按式 近似计算制动减速度。
在制动稳定性符合法规要求、制动器制动力足够的情况下,车辆的制动减速度主要取决于路面附着系数及利用,装有ABS的制动系统可以很好的利用路面的峰值附着系数,所以可以获得更大的制动减速度。在不考虑滚动阻力、风阻等的情况下车辆可获得的最大减速度可用以下公式表示:
Fu—前后轴总制动力φs—路面滑动附着系数φp—路面峰值附着系数
制动距离,可用以下公式计算:t1—制动机构滞后时间,即踩下制动踏板克服回位弹簧力并消除制动蹄片与制动鼓间的间隙所需的时间式中:
t2—制动器制动力增长过程所需的时间v—制动初速度,km/ht1+t2—制动器作用时间,一般在0.2-0.9s对液压制动系统,GB7258-2004规定,达到规定的制动减速度的75%时的制动协调时间不得超过0.35秒,所以最大值近似取0.35秒。
221
tt
mFju/maxgjsmax
gjpmax
gjsmax
max22192.25)2(6.31j
vvttS
©版权归江淮汽车股份有限公司所有 未经授权禁止复制第 6 页,共 13 页制动系统方案设计计算说明书P201-NAM-SD-DP-G3-2(3对
于a.
后
b.前
制根
4)
施加
式中———
—管路P
=
主缸径开发方案标杆方案
助力器失效时,制动力完全由人力操纵踏板产生,最大踏板力要求:N1类车700N。 各个设计方案均能满足法规对行车制动性能的要求,同时也满足设计要求。 从计算结果可以看出:当真空助力器失效后,前、后制动器制动力均小于附着系数为0.8的地面附着力(空、满载),因此在制动过程中,前、后轮均不抱死。可以计算出制动减速度和制动距离。
踏板比
piFF真
pi
ghLGbF
1
gdhLbgmFj1max1
ghLGaF
2
gdhLagmFj2max2
max22192.25)2(6.31j
vvttS
©版权归江淮汽车股份有限公司所有 未经授权禁止复制第 7 页,共 13 页