连续重整原始开工方案简介
重整方案范本

重整方案范本1. 引言在项目或业务运作中,经常会遇到需要对现有的方案进行重整的情况。
重整方案的目的是为了提高效率、降低风险或满足新的需求。
本文档旨在提供一个重整方案的范本,帮助读者了解重整方案的结构和要点,以便能够更好地在实际工作中应用。
2. 概述重整方案是一个系统性的工作,需要对现有方案进行全面的评估和整合,然后提出改进的方案。
重整方案通常包括以下几个步骤:1.方案评估:对现有方案进行评估,包括分析其优点和缺点,以及存在的问题和风险。
2.需求分析:明确重整方案的目标和需求,包括要解决的问题和达到的效果。
3.方案设计:基于现有方案和需求分析的结果,设计出新的方案。
4.方案实施:按照设计的方案进行实施,包括制定详细的实施计划和时间表。
5.方案评估:对实施的方案进行评估,看是否达到了预期的效果,并对方案进行调整和改进。
本文档将依次介绍每个步骤的详细内容和要点。
3. 方案评估在方案评估阶段,需要对现有方案进行全面的评估,包括以下几个方面:1.优点和缺点:分析现有方案的优点和缺点,明确其存在的问题和风险。
2.需求分析:根据现有方案的问题和需求,明确重整方案的目标和需求。
3.资源评估:评估实施重整方案所需要的资源(人力、物力、时间等)。
4.风险评估:评估实施重整方案所面临的风险,并制定相应的应对措施。
4. 需求分析在需求分析阶段,需要明确重整方案的目标和需求,包括以下几个方面:1.目标定义:明确重整方案的目标,即要解决的问题和达到的效果。
2.需求分析:分析现有方案的问题和需求,明确需要改进的方面和需求。
3.目标设定:根据问题和需求,设定重整方案的具体目标,制定明确的指标和标准。
5. 方案设计在方案设计阶段,需要根据现有方案和需求分析的结果,设计出新的方案,包括以下几个方面:1.方案原则:制定方案设计的原则和准则,确保新方案能够满足需求并解决问题。
2.方案内容:具体设计新方案的内容,包括具体的步骤、流程和方法。
连续重整装置简介

2、重整反应部分
重整过程是一个化学反应过程,存在着 多种化学反应。原料油在一定的操作条 件下,由于催化剂的作用使其分子结构 发生重新组合,从而最大限度地促进芳 烃生成和分子异构化达到制取芳烃或提 高辛烷值的目的。
2、重整反应部分
(1)催化重整过程主要有下面六类反应: 六元环烷烃脱氢反应 五元环烷烃异构化脱氢反应 烷烃脱氢环化反应 烷烃异构化反应 加氢裂化反应 缩合反应
中国石油哈尔滨石化公司 60万吨/年连续重整-80万吨/年中 压加氢装置
60万吨/年连续重整装置 简介
一、装置概况 二、工艺原理 三、工艺流程
一、装置概况
1、装置简介 2、装置特点 3、装置组成 4、装置原料 5、主要产品
1、装置简介
(1)60万吨/年连续重整装置是中国石油哈尔滨石化 公司“十一五”期间重点建设项目,由中国石化工程 建设公司设计、中国石油第七工程建设公司施工完成。 (2)重整反应采用UOP开发的超低压重整工艺,由于 采用了较苛刻的反应条件(低压、高温、低氢油比), 使催化剂的活性、选择性得到更充分的发挥,从而能 得到更高辛烷值与收率的产品。重整反应催化剂采用 石科院的PS-Ⅵ铂锡双功能金属催化剂。催化剂连续再 生部分采用UOP新开发的第三代(CYCLEMAX)催化剂 连续再生专利技术。 (3)装置的运行时间为每年8400小时,装置运转周期 为3年1修。
2、装置特点
(1)预处理部分采用先加氢后分馏的技术路 线,以降低轻石脑油的硫含量,正常情况下原 料的预处理仅考虑处理直馏石脑油。 (2)预加氢反应部分采用氢气循环流程。 (3)重整部分采用UOP超低压连续重整工艺, 可得到较高的液体产率、较高的芳烃产率和氢 气产率。重整汽油苛刻度为RONC102。 (4)重整反应器采用四台叠置式,物流为上 进上出(中心管上流式),以减少反应器中催化 剂的“死区”。
连续重整装置工艺流程简介 ppt课件
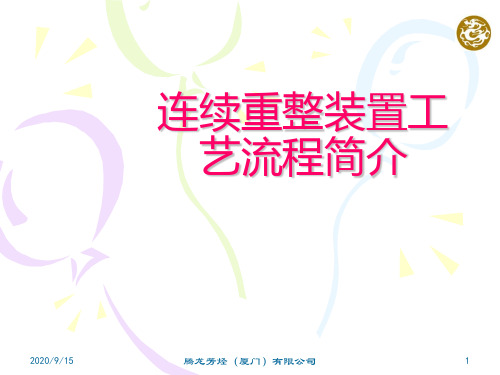
2020/9/15
腾龙芳烃(厦门)有限公司
6
反应产物经反应器进出料换热器冷却后,与 HP除氧水混合洗涤在低温下沉积的氯化物,硫化 物和铵盐。接着经过反应产物空冷器和水冷器冷 却进入反应产物分离罐,气液混合相通过分离罐 进行分离。
气相被用作循环气,并与来自重整反应部分 的补充氢混合。混合物通过循环压缩机入口分液 罐除去携带的液体,送至循环压缩机升压并循环 至反应系统。
液相的烃类产物经过汽提塔进料/塔底换热 器进入汽提塔。
2020/9/15
腾龙芳烃(厦门)有限公司
7
进料缓冲罐
石脑油加氢反应部分
加热炉
冷却
分
反
液
应
罐
器 分离罐
汽提塔
泵 进料
2020/9/15
循环机
腾龙芳烃(厦门)有限公司
8
2 .汽提塔部分
在汽提塔部分,加氢预处理直馏石脑油经汽 提塔进料/塔底换热器预加热后,进入汽提塔。
• 催化剂连续再生是将碳含量高的催化剂,经过烧焦、 氧氯化、干燥(或焙烧)、还原等工艺使之恢复活性。
• 连续重整采用Axens(原IFP)工艺包设计,采用超低 压连续重整工艺。
2020/9/15
腾龙芳烃(厦门)有限公司
2
主要技术特点:
• 重整四台反应器为并列布置,加热炉采用四合一 炉,炉管为倒“U”型布置。
催化剂再生
重整单元
PSA单元 异构化单元
歧化单元
LPG去罐区 抽提单元 吸附分离单元
2020/9/15
腾龙芳烃(厦门)有限公司
4
装置工艺流程介绍
第1部分 石脑油加氢
一、工艺流程描述
直馏石脑油自界区外进入单元,经过流量液 位控制引入单元,通过进料缓冲罐的液位来控制 石脑油加氢的进料。
连续重整装置开工总结

连续重整装置开工总结一、概况1.1装置简介330 万吨/年连续重整装置是某炼化 150 万吨/年芳烃联合装置的主要装置之一。
装置由中石化洛阳工程进展工程设计,四台重整反响器两两重叠布置。
设计年开工时间为 8400 小时,装置操作弹性为 60~110%。
330 万吨/年连续重整装置由预加氢、重整、催化剂连续再生三个单元组成。
装置以轻烃回收装置直馏石脑油和加氢裂扮装置重石脑油为原料生产芳烃,重整生成油送往二甲苯分馏单元,同时生产预加氢轻石脑油、戊烷、液化气、含氢气体等产品;预加氢轻石脑油和戊烷送至轻石脑油异构扮装置;液化气送至气体分馏装置;含氢气体除供芳烃联合装置自用外,其余送至 PSA 经提纯后供加氢装置使用;连续重整装置相对应的各单元设计规模见表 1-1:表1-1 连续重整装置各单元设计规模单元名称设计规模预加氢 260 万吨/年重整 330 万吨/年催化剂再生 3175 公斤/小时(7000 磅/小时)1.2装置的主要技术特点1.预加氢单元:预加氢承受先加氢、再汽提后分馏的工艺流程。
预加氢催化剂承受美国 UOP 公司的 HYT-1119 催化剂,反响器入口压力为 3.19MPa。
设置补充氢压缩机,将重整产氢由 2.6MPa 升压至 2.85MPa 后为预加氢反响供给补充氢气。
2.重整单元:重整承受美国 UOP 最的超低压连续重整工艺技术及 UOP 公司的R-264 催化剂,四台反响器两两重叠布置。
重整反响设计条件如下:平均反响压力0.35MPa、反响器入口温度 536℃,体积空速 1.82h-1,轻烃分子比 2.3,C5+辛烷值为 105.7(RON)。
再接触系统设置两台重整氢增压机将重整产氢压力上升至2.6MPa,设置三台丙烷冷冻压缩机提高重整增压氢的纯度同时提高重整产物的液体收率。
3.催化剂再生单元:催化剂再生局部承受美国 UOP 的CycleMax 二代工艺技术。
待生催化剂和再生催化剂分别设置除尘系统,再生烧焦放空气脱氯承受Chlorsorb 工艺技术回收其中的氯化氢。
连续重整装置工艺流程简介

的稳定性和效率。
自动化与智能化
03
引入自动化设备和智能化控制系统,降低人工干预,提高生产
效率。
绿色生产与可持续发展
降低能耗
优化工艺流程,降低装 置的能耗,减少碳排放。
环保材料
采用环保材料和绿色催 化剂,降低对环境的污 染。
资源回收
实现废气、废水和固废 的资源化利用,降低生 产成本。
市场前景与挑战
空速
空速反映了装置的处理能力 ,是衡量装置生产效率的重 要指标。
设备维护与保养
定期检查设备运行状况
检查设备的运行参数、振动、声音等,确保设 备正常运行。
定期清洗和更换易损件
对设备的易损件进行定期更换,对设备进行定 期清洗,确保设备的清洁度和稳定性。
定期进行大修
根据设备的运行状况和维修记录,制定合理的维修计划,确保设备的稳定性和 使用寿命。
去除原料油中的水分和盐分,防止催化剂失活和 设备腐蚀。
原料油预热
将原料油预热至一定温度,为后续反应提供适宜 的温度条件。
杂质脱除
通过加氢等方法脱除原料油中的硫、氮、氧等杂 质,提高产品质量和减少对催化剂的毒害。
反应部分
催化剂装填
将催化剂装填到反应器中,确保催化剂与原料油充分接触。
反应温度控制
通过加热和冷却等方法控制反应温度,使反应在适宜的温度下进 行。
催化剂再生
催化剂失活
催化剂在反应过程中会逐渐失活,需要定期再生或更 换。
催化剂烧焦
通过控制烧焦温度和时间,除去催化剂表面的积碳和 杂质。
催化剂还原
在还原气氛下,使催化剂恢复活性,提高其催化性能。
连续重整装置的设备
03
与操作
主要设备介绍
连续重整工艺原理

连续重整工艺原理连续重整工艺原理是一种工业生产过程中常用的技术,其通过对原始材料进行连续分离、净化和重组等操作,最终得到高纯度的产品。
本文将从连续重整工艺的原理、应用以及优势等方面进行阐述。
连续重整工艺是基于物理、化学等原理进行的一种工艺过程。
其核心原理是利用物质在不同条件下的物理和化学性质的差异,通过一系列的操作步骤将原始材料中的杂质、杂质组分和有害物质等分离出来,从而得到所需的高纯度产品。
连续重整工艺一般包括以下几个步骤:预处理、分离、净化和重组。
预处理是连续重整工艺的第一步,其目的是对原始材料进行初步的处理,例如去除杂质、调整温度和压力等。
预处理的主要目的是为了提高后续分离和净化的效果,确保最终产品的质量。
接下来,分离是连续重整工艺的关键步骤之一。
在这一步骤中,通过利用物质在不同条件下的物理性质的差异,将原始材料中的各个组分分离出来。
常用的分离方法包括蒸馏、萃取、吸附和膜分离等。
这些方法的选择取决于原始材料的性质和所需产品的要求。
净化是连续重整工艺的另一个重要步骤。
在这一步骤中,通过进一步的处理和过滤,将分离得到的组分中的杂质和有害物质进一步去除,以确保最终产品的纯度。
净化方法包括溶剂萃取、吸附剂过滤和膜过滤等。
重组是连续重整工艺的最后一步。
在这一步骤中,通过将经过分离和净化的组分按照一定的比例和顺序重新组合,得到所需的最终产品。
重组的目的是获得高纯度的产品,并满足不同应用领域的要求。
连续重整工艺在许多工业领域都有广泛的应用。
例如,在石油化工行业,连续重整工艺被用于原油的分馏和石化产品的生产;在制药工业中,连续重整工艺常用于药物的提纯和制备;在食品行业,连续重整工艺被用于食品的加工和提纯等。
这些应用都表明了连续重整工艺的重要性和广泛性。
连续重整工艺相比传统的离散操作具有许多优势。
首先,连续重整工艺可以实现高效、连续的生产,提高生产效率和产能。
其次,连续重整工艺可以减少能源和原材料的消耗,降低生产成本。
企业重整方案

(1)遵循国家法律法规,保障员工合法权益,确保员工待遇不受影响;
(2)开展员工培训和技能提升,提高员工综合素质,增强企业凝聚力;
(3)加强与客户、供应商等合作伙伴的沟通协调,维护良好合作关系。
四、实施步骤
1.成立企业重整工作小组,负责方案的具体实施;
2.对企业进行全面评估,制定详细的重整计划;
(2)优化董事会、监事会及高级管理人员构成,提高决策科学性和执行力;
(3)加强内部监督,防范经营风险,保障企业合规经营。
3.业务优化与转型升级
(1)深入分析市场需求,调整产品结构,提高产品附加值;
(2)加大研发投入,推动技术创新,培育企业核心竞争力;
(3)拓展市场渠道,提高市场占有率,实现业务规模扩大。
4.做好员工稳定工作,维护企业和谐稳定。
六、总结
本重整方案旨在帮助企业摆脱当前经营困境,实现可持续发展。在实施过程中,需密切关注各项措施的落实情况,及时调整优化,确保企业重整目标的实现。同时,要充分发挥企业、员工、客户及供应商等相关方的积极作用,共同为企业的美好未来努力。
企业重整是一项系统工程,需要各方共同努力。在重整过程中,我们要坚定信心,锐意进取,以严谨的态度和务实的作风,确保重整工作的顺利进行。相信通过全体人员的共同努力,企业必将迎来崭新的发展局面。
企业重整方案
第1篇
企业重整方案
一、背景分析
鉴于当前企业面临的经营困境,为保障企业持续稳定发展,维护员工、客户及供应商等相关方的合法权益,现依据我国相关法律法规,结合企业实际情况,制定本重整方案。
二、目标定位
1.优化企业资产结构,提高资产使用效率;
2.完善企业治理结构,提升企业运营管理水平;
连续重整再生系统开工遇到的问题及解决措施

连续重整再生系统开工遇到的问题及解决措施林德溪【摘要】The regeneration system of catalyst is an important part of the platforming unit. Problems in continuous catalyst regeneration ( CCR ) of 2000 kt/a platforming unit of Sinochem Quanzhou Petrochemical Co. , Ltd. were discussed, including large deviation between calibration and design of nuclear level, the lifting of inter-reactor transfer system being not smooth, and no catalyst flow during cool down mode test. Solutions were also proposed.%催化剂再生系统是连续重整装置的重要组成部分。
本文针对中化泉州石化有限公司200万吨/年连续重整装置再生系统在开工过程中遇到的问题,包括核料位计标定与设置值偏差大,催化剂器间提升不畅,以及冷态循环模式提升试验时没有催化剂流动等进行分析,并提出相应的解决措施。
【期刊名称】《广州化工》【年(卷),期】2015(000)001【总页数】3页(P147-149)【关键词】核料位计标定;催化剂器间提升;冷态循环模式【作者】林德溪【作者单位】中化泉州石化有限公司,福建泉州 362103【正文语种】中文【中图分类】TE624中化泉州石化有限公司连续重整装置选用的是美国环球油品公司(UOP)超低压连续重整和第三代催化剂再生工艺技术(CycleMax),设计规模为200 万吨/年,催化剂再生能力为4500 磅/时,选用的催化剂为R-234,并同时采用氯吸附(Chlorbsorb)工艺技术,反应器采用“2+2”并列式布置方案,器间提升设计有连续提升模式和批量提升模式。
- 1、下载文档前请自行甄别文档内容的完整性,平台不提供额外的编辑、内容补充、找答案等附加服务。
- 2、"仅部分预览"的文档,不可在线预览部分如存在完整性等问题,可反馈申请退款(可完整预览的文档不适用该条件!)。
- 3、如文档侵犯您的权益,请联系客服反馈,我们会尽快为您处理(人工客服工作时间:9:00-18:30)。
按催化剂装填方案装填催化剂。
CCR重整催化剂装填
1、催化剂装填应在CCR重整装置干燥完成 之后进行。
2、重整反应器催化剂从R-201顶还原区上部 装填,以UOP重整催化剂装填要求依次按 R-204、R-203、R-202、R-201的顺序装填。
3、再生部分催化剂从分离料斗D-303顶部 装料口装填。
全面检查是装置试车前的一项重要工作。细 致周到的检查准备工作是装置能否顺利开工的 前提,通过对装置的全面检查,可以及早发现 和处理问题,为装置试运打好坚实的基础。
全 面 检 查 包 括
1、公用工程系统检查 2、工艺管线检查 3、静设备检查 4、动设备检查 5、仪表检查
二、装置吹扫试压
f、重整进料(反应器入口温度达到370℃,重整与 预处理联动,C101底油改进重整) g、启动K202,停管网H2 ,向预加氢、C6加氢 供氢,控制系统压力正常。 h、再接触丙烷系统投运 i、建立正常操作(调整各工艺指标至正常,控 制产品质量合格。 ) j、引精制油对C6加氢催化剂硫化4~6h ,停精制 油,化验分析C203回流罐油合格后,改进C6 加氢反应器,苯抽提进料,停油路循环。
四、装置水冲洗及水联运
一、水冲洗: 1. 冲洗管线和设备内的脏物、泥土、沙子等。 2. 考验设备、管线施工质量及安装情况。 二、水联运: 1. 进一步清洗管线及设备,清除管线、设备内的铁锈、 碎屑、泥沙等杂物。 2. 考察系统在装水条件下的严密性及强度,贯通工艺 流程,以保证装置能顺利运行。 3. 考核机泵、设备的性能及可靠性。 4. 考察仪表控制系统的控制性能,摸索仪表控制参数, 检验流量、液位、压力等检测仪表的准确性。 5. 以水代油进行操作模拟和事故演习,使岗位人员熟 悉和掌握操作技术,提高操作水平。
重整加热炉烘炉及余热锅炉煮炉与重 整部分干燥同时进行。利用加热炉烘 炉的热量,使用除盐水和化学药品, 脱除余热锅炉系统内设备和管线表面 的油脂、铁锈等有害物质,保证余热锅 炉安全长期运行以及蒸汽质量合格。 在系统各部温度达到250℃时,应对 各高温部位做全面检查并联系保运单 位进行热紧。在系统各部降温后,应 对原高温部位再一次做全面检查,防 止泄漏。
六、加热炉烘炉、余热锅炉煮炉及系统干燥 烘炉的目的是脱除新建加热炉耐火材料 中所含的自然水、结晶水,烘结耐火材 料,增加耐火材料的强度和使用寿命。 反应炉烘炉与反应系统干燥同时进行, 采用氮气循环,(控制系统压力3.5MPa) 一方面氮气从炉内带出烘炉热量,保证 炉管不超温而保护炉管,另一方面,借 助这部分热氮在反应系统内循环,可以 带走水分,起到系统干燥的目的。( 圆 筒炉F-102、F-205、F-206通入蒸汽保护
第三次升压:升压至2.4MPa并进行恒压 煮炉 保压煮炉 降压至0.8Mpa,排污 冲洗置换
注:煮炉过程中,必须始终保证汽包液面,仔细检查, 确保循环泵不抽空。
系统干燥时,应尽可能使每根流程均 走干燥介质,对不能同时进干燥介质 的流程,可每隔4小时左右切换操作 一次,使系统各部分均得到干燥。 干燥过程中应加强低点脱水,尤其是 低温部分的脱水。 干燥结束后,应尽可能避免湿空气或 水进入系统。
油联运注意事项
(1)、引油时必须“人跟油走”,出现异常事故立 即处理。 (2)、在热油循环时,当热油经过冷换设备时,如 果只有一程走介质,那么另一程必须打开放空。而 空冷器和冷却器则应及时投用。 (3)、随着温度上升,各塔,容器等设备要防止憋 压,及时启用压控。 (4)、加热炉点火必须严格遵守加热炉点火操作规 程,防止正压回火。 (5)、严禁乱排油,严格动火制度,防止出现火灾。 (6)、各罐加强脱水,每小时一次,脱水时要专人 负责防止跑油。
重整进料中杂质含量要求
杂 质 名 称 硫 ppm
总 氮 氧 ppm ppm
氯 氟 化 化 砷 铅 硅 物 ppb ppb ppm 物 ppm ppm
溴 指 数
பைடு நூலகம்
水 ppm
质 量 指 标
0.2~ 0.5
0.5
5
0.5 0.5
1
10
0.1 10
2
4、重整单元开工
a、开车前的准备工作已完成,油联运正常 b、系统气密、置换合格 c、启动K201,建立H2循环 (苯抽提单元 建立溶剂循环、油路循环) d、投用余热锅炉系统(在重整四合一炉点 炉前蒸汽放空) e、重整反应开始升温(10~15 ℃/h 250 ℃ 时联系热紧)
在活化过程中,必须严格控制升温速度。尽量 减少系统的排放或泄漏,以保持最高H2S浓度。 循环氢中H2S浓度每1小时分析一次。
3、预处理进油
活化结束后,以15~20℃/h 速度降温 至反应器入口温度280℃,开始外送活 化油,2小时后开始在高分底部采油样 进行分析,连续2次采样分析D102底 油(硫含量<12PPm)合格,改罐区 进料,停D102底油循环,改进C101。 C101底油改污油。
注意事项:
1、在升温阶段,要定期检查U型管,要确保炉管畅 通,没有局部过热现象。 2、对整个反应部分和再生部分的热膨胀进行详细 检查。 3、当重整进料后,应立即增点主火嘴,以 20~30℃/h的升温速率向460℃升温,温度升到 460℃后在此温度下至少停留12小时进行催化剂的 脱水干燥和操作调整 。 4、当重整进料后,应立即提K201转速,确保氢油 比合适。 5、一旦反应器进料,就应根据循环氢气中水含量, 投用注氯设施,进行水氯平衡的调节。 6、当汽包压力达到3.5MPa、过热段蒸汽出口温度 达到440℃后3.5MPa蒸汽并管网。
油联运目的 : 全面考察装置工艺、设备、机泵、管道、仪表 的施工和制造安装质量。考核工艺流程的合理 性。 对岗位人员进行一次技术练兵,熟悉机泵操作 和温度、流量、液面、压力等控制方法,进一 步提高操作人员利用DCS操作控制的能力。 通过油运,进一步冲洗设备和管线内的残存脏 物,并将残存的水份脱除。 处理油运发现的问题,等待反应系统投料,为 反应部分开车做准备。
气密压力MPa
气密温度℃ 气密介质 压降(MPa/h) 维持时间(h)
1.0
常温 氮气 <0.01 2-4 0.1
1.7
常温 氮气 <0.05 2-4 0.1
2.5
常温 氮气 <0.1 2-4 0.1
0.25
常温 氮气 <0.01 2-4 0.1
0.45
常温 氮气 <0.01 2-4 0.1
升降压速度 (MPa/8min)
烘炉曲线
700 600 炉 膛 温 度 ℃ 500 400 300 200 100 0 1 2 3 4 5 6 7 时间,/天
150℃恒温 320℃恒温 500℃恒温
7~8℃/h 14~15℃/h
~7℃/h
烘炉必须严格控制升温曲线,不能超过工艺 指标,由于反应系统干燥需要较高的操作温 度,提温必须在烘炉曲线所示的最高温度恒 温结束后方可进行。烘炉期间,必须每小时 记录一次温度,并绘制实际温度曲线。 烘炉期间应加强对加热炉,余热锅炉、冷换 设备、反应器,再生器、电加热器,鼓风机 等现场设备的检查,发现异常及时处理。 加热炉炉墙在烘炉结束后必须认真检查,发 现裂纹必须仔细测量其长度、宽度和深度, 做好记录,并根据要求及时修复。
装
1 公 用 工 程 系 统 投 用 2 临 氢 系 统 吹 扫 3 非 临 氢 系 统 吹 扫
置
4 苯 抽 提 部 分 吹 扫
吹
扫
5 临 氢 系 统 爆 破 吹 扫 6 中 压 蒸 汽 打 靶 7 再 生 部 分 吹 扫
三、单机试车 单机试车的目的: 对装置的所有动设备(机泵,搅拌器等) 的机械性能通过实际启动运转进行初步 检验,尽早发现设计、制造、安装过程 中存在的缺陷并予以消除,以保证后续 开车程序的顺利进行。 单机试车设备包括: 离心泵、鼓引风机、空冷风机、压缩机 等所有动设备
吹扫目的: 清除装置施工建设中残存于设备,管线内的泥 沙,焊渣,铁锈等脏物,为装置试车贯通流程、 检验装置的施工质量。 试压目的: 1、检查并确认静设备(炉、塔、容器、阀门等) 及所有工艺管线的密封性能是否符合石化总公 司的规范要求。 2、检查施工过程中焊接质量、安装质量及使 用的材质是否符合要求,便于及时发现装置施 工的漏项和缺陷
煮炉各阶段及控制指标
序号 1 2 3 4 5 6 7 8 汽包升压程序 汽包上水 加药、碱率分析 第一次升压:升压至0.5MPa并进行恒压 煮炉并进行热紧工作 所需时间 (小时) 4 7 8 14 15 12 6 10 累计时间(小时) 4 11 25 40 58 70 76 83
第二次升压:升压至1.2MPa并进行恒压 煮炉
其他反应器(R-101、R-102、R-205) 及容器(D-204、D-206、D-211)等 按催化剂装填方案进行装填。
八、装置进油开工方案
1、分馏系统油运
2、预加氢催化剂的干燥
3、预处理进油
4、重整单元开工
5、再生部分开工
6、苯抽提部分开工
1、分馏系统油运及调整操作
油联运合格后,分馏部分操作
1、预处理部分:C-101单塔循环; 2、重整分馏部分:C-201、C-203、C-204、 C-205四塔循环。 3、F-102、F- 205、F-206按10~15 ℃/h升 温至正常指标。 4、采样分析D-102底油合格后改进C-101。 5、采样分析C-101底精制油合格后,具备 与重整联动条件。
2、临氢系统置换
气密合格后,将系统内的氮气在各低点排 放,至系统压力到0.035MPa,然后启用 抽空器对各系统抽真空至600mmHg; 引氮气缓慢破真空,将系统充压至 0.035MPa,然后在各排放点排放,继续 抽真空至600mmHg,再用氮气升压至 0.035MPa,然后在各排放口将压力再泄 掉,如此反复进行,直至系统采样分析氧 含量小于0.5(V)%, 置换合格。