新型冷连轧机支承辊的制造
冷轧轧机支承辊辊面剥落原因与应对策略

世界有色金属 2020年 7月上52机械加工与制造M achining and manufacturing冷轧轧机支承辊辊面剥落原因与应对策略龙再祥(西南铝业集团有限责任公司冷轧厂,重庆 400000)摘 要:本文对我厂1#轧机支承辊剥落原因进行了分析,结果表明,疲劳是导致支承辊剥落的主要原因。
由于接触点应力集中导致辊面疲劳裂纹,疲劳裂纹持续发展最终导致剥落。
关键词:冷轧;支承辊剥落;疲劳裂纹中图分类号:TG333.17 文献标识码:A 文章编号:1002-5065(2020)13-0052-2Spalling Failure Analysis and Countermeasure of Back-up Roll for Cold MillLONG Zai-xiang(Cold rolling mill of Southwest Aluminum Group Co. LTD,Chongqing 400000,China)Abstract: Spalling failure had taken place on back up roll for no.1 mill in our factory.Through spalling fracture analysis,it was proved that main causes for roll’s spalling were contact fatigue.The spalling fracture of the back-up roll is caused by the fatigue crack in the surface layer due to the stress concentration at the contact point.Keywords: Cold mill; Spalling of back-up roll; Fatigue crack1 背景西南铝业集团高精板带事业部冷轧板带生产线,有两台1850mm 进口冷轧高速轧机,轧制过程中支承辊除了要承受巨大的轧制力,还要承受由于高速轧制下的转矩,AGC 辊缝调节,弯辊调节,厚差波动,断带挤料,辊型变化等因素均会造成支承辊辊面局部应力集中、与工作辊不同支承辊不具备频繁更换的条件,更换周期可长达一至两个月,易造成辊面疲劳和裂纹导致脱落,严重的情况下无法修复最终造成报废。
新型LG550三辊冷轧管机的研究
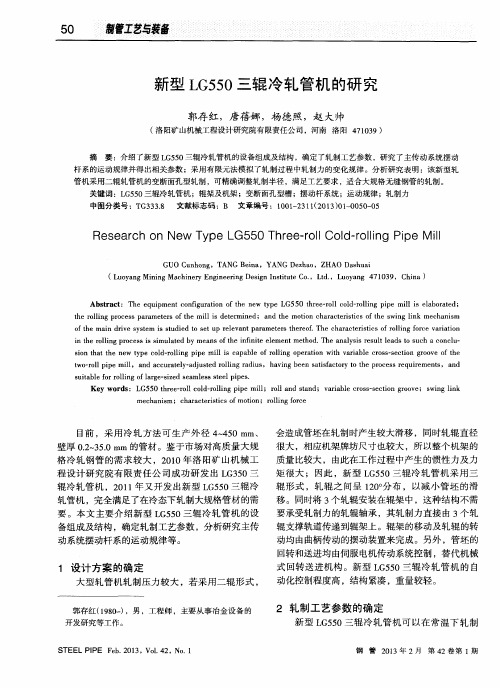
杆 系的运动规律并 得出相关参数 ;采用有 限元法模拟 了轧制过程 中轧制力 的变化规律 。分析研究表 明:该新型轧
管机采用二辊轧管机的变断面孔型轧制 ,可精确调整轧制半径 ,满足工艺要求 ,适合大规格无缝钢管 的轧制 。
关键词 :L G 5 5 0三辊冷轧管机 ;辊架及机架 ;变断面孔型槽 ;摆动杆 系统 ;运动规律 ;轧制力
s u i t a b l e f o r r o l l i n g o f l a r g t e e l p i p e s .
Ke y wo r d s :L G5 5 0 t h r e e — r o l l c o l d — r o l l i n g p i p e mi l l ;r o l l a n d s t a n d ;v a r i a b l e c r o s s 。 s e c t i o n g r o o v e ;s wi n g l i n k
me c h a n i s m; c h a r a c t e r i s t i c s o f mo t i o n ;r o l l i n g f o r c e
GUO Cu n h o n g ,TA NG Be i n a ,YANG De z h a o ,Z HAO Da s h u a i
( L u o y a n g Mi n i n g Ma c h i n e r y E n g i n e e r i n g D e s i g n I n s t i t u t e C o . ,L t d . ,L u o y a n g 4 7 1 0 3 9 ,C h i n a)
i n t h e r o l l i n g p r o c e s s i s s i mu l a t e d b y me a n s o f t h e i n f i n i t e e l e me n t me t h o d . T h e a n a l y s i s r e s u l t l e a d s t o s u c h a c o n c l u - s i o n t h a t t h e n e w t y p e c o l d — r o l l i n g p i p e mi l l i s c a p a b l e o f r o l l i n g o p e r a t i o n wi t h v a r i a b l e c r o s s — s e c t i o n g r o o v e o f t h e
一种新型大直径多辊冷轧管机的简要介绍

一种新型大直径多辊冷轧管机的简要介绍冷轧钢管在生产中广泛应用周期式冷轧管机。
根据轧辊的特点及个数,冷轧管机可以分为多辊式、二辊变断面及多辊变断面三种冷轧管机。
目前,国内轧机大部分为多辊式冷轧管机与二辊变断面孔型冷轧管机。
由于多辊变断面孔型冷轧管机所具有的特殊优点,已是二辊变断面冷轧管机的有力竞争对手,可能取代多辊冷轧管机。
标签:冷轧钢管;多辊变断面;冷轧管机前言在众多的管材产品中,冷轧管具有一系列优点。
第一,经过冷轧的管材组织晶粒细密,管材机械性能和物理性能均较优越;第二,冷轧管机对于原始管坯璧厚偏差的纠偏能力较大,几何尺寸精确,表面光洁度高;第三,冷轧过程中道次变形量较大,可达70~85%,生产效率高;第四,采用冷轧法生产管材可大量减少中间工序,减少了金属材料、燃料、电能和其它辅助材料及人力的消耗;第五,用冷轧方法可生产薄壁和极薄壁,内、外表面无划痕的优质管材;第六,可有效地轧制高合金、塑性差的各种金属管材。
鉴于以上诸多优点,冷轧管材的使用范围不断扩大,需要量大幅度增加,带动冷轧管机的需求也不断增加。
目前,国外轧机普遍采用了圆形孔型块,不仅提高了轧辊的强度,还加长了机架的行程近80~100%,改善了轧制过程中管坯变形条件。
轧机驱动采用有效的惯性力和惯性力矩的平衡机构,实现高速轧制,轧制工作制采用高速、超长行程轧制和双回转双送进,轧机的轧制过程实现了不停机连续上料和连续轧制,轧机采用电脑控制,实现自动化操作。
而我国轧机生产控制水平与国外轧机水平相比还有很大的差距。
现今使用的冷轧管机分为如下二种:(1)多辊式冷轧管机,统称LD型。
(2)二辊变断面孔型冷轧管机,统称LG型。
截止2010年底,我国冷轧成品管最大直径规格为450mm。
随着科学技术的发展,我国对更大直径,如直径为520、610、720及920毫米,壁厚为20-60毫米的冷轧管材提出了强烈的需求,同时对小直径钢管的表面质量及尺寸精度也提出了更高的要求。
一种新型抗辊印轧辊的研制

在轧辊接触区 ,接触应 力超过一定值 时 ,也会在 支承辊 或工作辊表 面造成 辊印 ( 压痕 ) :这 说明产生辊 印 的概
率也 与 轧制力 的分配 、工作辊 与中间辊 ( 支承辊 )之 间
磊 工热 工 处 铸 21年 2期 ■ 加 热 般 造 0 第 3 雀 0
w w w. et w or i g 7 0. om m a1 k n 95 c
印缺 陷传递到钢板表面 ,不但影 响冷轧钢板 质量 ,而且 导致非计划换辊的增J ,轧辊 消耗增多 ,轧机 作业率降 J l 1
低。因此急需抗辊印性 能好 的冷轧 [ 作辊 ,以提 高冷轧
硬度的合理匹配 ,以及各机架轧制 力的合理分 配等。而 开发研制新型的抗辊 印轧辊 ,提高 轧辊 的抗 压人 性能 , 则是轧辊制造 厂要做 的工作 。
8 rM V材质 )辊 面经常出现的辊 印 轧辊 辊面 l的辊 C3 o
的硬度匹配密切相关 。
因此 ,降低辊 印发生率必须从轧辊 的设计制造 和使
用维护两个方面人手 :在使用维护方 面要 注意减少 杂质 ( 氧化皮 、焊渣 、铁屑 、砂粒等 )进人轧机 ,提高轧辊 、
带钢和乳化液的清 洁度 ;注意工作辊 、中间辊和支 承辊
硬度…般在 6 HR 3 C左右
图 1 某 冷轧厂轧辊上的辊印
一
、
辊印成因及对策
辊印可简单地描述 为:由于杂质 进入轧制 区域 ,轧 辊辊身的抗压 人性 能又较差 ,辊身表 面局 鄙出现永久 性
变形而形成的随机 分布的小 凹痕 辊 印形 状 一 为圆形 般 压痕 ,最大直 径约 3 mm,最 大深度约 0 0 I] 在接 下 .8 1 nl 来的轧制过程中 ,辊 印会转移到钢带 表 由造成缺 陷。轧
1580mm热连轧机精轧支承辊新材料研制

近 十年来 一重 在 国 内推 广 应 用 5 r 5 %C 和 % c 改 进 型锻 钢 支 承 辊 , 得 了较 好 效 果 , 国 内 r 取 在
e an e a xad( C + )crie r b i db t nteigcoig rcs o qe cig etra e t r ii )m t n M7 3 MC a d eot n yseghnn ol oes f unhn a t t n b t i r b a ae r np h e m
1 试 验 阶段
居 同行业 领先 地位 。但 随着 钢铁 行业 产 品技术 的 发展 , 现代 化大 型 冷 、 带钢 连轧 机 出于提 高轧 机 热 作 业 率和 实现 无头 、 半无 头轧 制等 目的 , 出 了延 提 长 支 承辊换 辊周 期 的要求 。一 重公 司的支 承辊 与
JF C C的支 承辊 相 比仍 有 一 定 的差 距 。 一 重公 司
11 8 r 钢支 承辊 化学成 分设 计 . %C 锻 在 8 C 锻 钢 支 承辊 的 化学 成 分 设 计 中 , % r 合
理 的合 金元 素配 比和加 入量 是保证 支承 辊各项 性
能要 求 的关 键 。依 据各 种 元 素 在 钢 中 的作 用 , 设
计 了三种 化学 成分 进行选 择 , 体 见表 1 具 。 1 2 冶炼 和锻 造试 验 . 根据设 计 的化学 成分 , 用 10 k 工 频 感 应 采 5 g 电炉熔 炼 3钢水 , 大气 浇 注 3支 7 g 钢 锭 , 5k 小 并
大型锻钢支承辊的机加工工艺

大型锻钢支承辊的机加工工艺摘要:大型锻钢支承辊凭借着自身独特的内部结构和广泛的使用范围,具有对生产制造的高标准要求,对其加工的任一环节若出现误差,就会使整体的机械性能产生不良影响,因此对于该机器的加工技术和方法的选用就变得非常关键。
为保证大型锻钢支承辊的质量和生产效率,本文根据对其结构特点、加工工序的分析,将支承辊制作过程中的工艺难点、要点进行了研究。
关键词:支承辊;机加工;工艺要点由于对从国外引进的机器加工设备使用技术的提高,使得大型锻钢支承辊的生产实现国产化。
所谓支承辊,即是一种轧机内的重要组成零件,其起到了支撑工作辊、防止工作辊变形的作用,并且其生产的质量对于轧机的组装和轧制钢板的性能、精确度具有重要影响。
所以有关人员要加强对于支承辊加工技艺的深入研究。
1.支承辊的结构特点和加工工艺路线1.1支承辊的结构特点支承辊内部的构造特点包括:①器械中能够旋转的零件直径相比于其他要更大,其重量最小为50t,最大能够达到214t。
同时,辊的同轴度一般在φ0.8mm范围内,粗糙度最大为R a0.8;②支承辊左右两边的部分均具有复合倒角和圆弧,其倾斜程度为20°,粗糙程度不能超过R a0.8,由于这一部分被用来安装迷宫环,所以对其加工精确度就会有相对较高的要求;③为了使得机器轴承拆卸和安装工作可以更加便利,因此支承辊在制造过程中使用是油膜式轴承,并且左右两端轴颈带的锥度在加工时被制成了1:5.647的比例,同轴度在φ0.01mm范围内,粗糙程度在R a0.4之内;④在机械的辊颈位置设有相对称的两个凹槽,对称程度最大在0.05mm左右,由于精确程度较高,所以在进行零件制作时很难控制,检测的难度也较大。
1.2支承辊的加工工艺路线在实际生产支承辊的过程中,其具体的工艺程序为:焙烧→提炼→溶解、溶化→浇铸→锻造→去除应力→热加工处理→粗车(为调质工作预留加工零件的余量)→高温回火热加工处理→半精车(为后续工作预留零件余量)→差温淬火加工→精车→对于支承辊颈进行毛坯部分余量的去除(预留精细制作的余量)→精磨→制作零件的内部孔洞→铣削→钻→零件产品检验→包装。
《5000mm轧机支承辊辊型曲线的研究》范文

《5000mm轧机支承辊辊型曲线的研究》篇一一、引言在轧机生产线上,支承辊作为轧机的重要部件之一,其性能直接影响着轧制产品的质量和生产效率。
随着现代轧机技术的不断发展,对支承辊的性能要求也越来越高。
其中,辊型曲线作为支承辊的重要技术参数之一,对于其在实际生产中的使用效果有着决定性的影响。
本文将对5000mm轧机支承辊的辊型曲线进行深入的研究和分析,以期为相关领域的研发和应用提供参考。
二、支承辊的基本结构与工作原理支承辊是轧机的重要组成部分,其基本结构包括辊身、辊颈、法兰等部分。
在轧制过程中,支承辊与工作辊协同工作,为轧制材料提供支撑和驱动力。
同时,由于受到工作时的热和力等复杂因素的作用,支承辊的形状会发生变化,这就需要其具备稳定的辊型曲线来保持其性能的稳定。
三、5000mm轧机支承辊的辊型曲线研究(一)研究目的本研究旨在通过对5000mm轧机支承辊的辊型曲线进行深入研究和分析,探索其变化规律及其对轧制产品性能和质量的影响,以期优化其设计和生产过程,提高产品的质量和生产效率。
(二)研究方法本研究所采用的方法包括理论分析、仿真模拟和实验研究。
首先通过理论分析了解轧制过程中的基本原理和规律,然后利用仿真软件进行模拟实验,以进一步探究支承辊的辊型曲线变化情况,最后通过实际生产中的实验验证理论分析和仿真模拟的结果。
(三)研究结果1. 辊型曲线的变化规律:通过对支承辊的长期观察和实验研究,我们发现其辊型曲线随着使用时间的增长会发生一定的变化。
在初始阶段,由于新辊的使用,其形状相对稳定;但随着使用时间的延长,受到热和力的作用,其形状会逐渐发生变形。
因此,我们需要对支承辊的形状进行定期的检测和调整。
2. 辊型曲线对产品质量的影响:研究发现在一定范围内调整支承辊的辊型曲线可以影响轧制产品的厚度、宽度等性能参数。
当辊型曲线合理时,产品的性能和质量会得到显著提高;反之,如果辊型曲线不合理或出现变形,则会影响产品的性能和质量。
探究冷轧支撑辊和工作辊剥落机理及有效预防措施(全文)

探究冷轧支撑辊和工作辊剥落机理及有效预防措施引言轧辊是轧钢生产的重要工具,价格非常昂贵,尤其是冷轧板带用的锻钢支撑辊及工作辊。
近年来,各轧钢厂为提高产量和减少换辊周期, 广泛使用价格更贵、硬度更高及淬硬层更深的高合金辊。
因此,减少轧辊的早期失效及降低生产成本显得日益重要。
在冷轧板带生产过程中,轧辊处于复杂且不断变化的应力状态。
轧制负荷引起的支撑辊与工作辊间的接触应力、带钢跑偏断带以及肋浪粘钢造成的机械及热冲击容易使轧辊损坏。
轧辊损坏的形式主要为剥落,因此,探究轧辊剥落机理以便早期发现裂纹和预防剥落是延长轧辊使用寿命的有效途径。
1、冷轧技术概述钢材是国民经济的各个领域中的十分重要的材料,它被广泛应用于机械工程、电机工程、建筑、金属制品、汽车、运输、家用器具等各个行业。
20XX年以来,全球对钢材的需求量除了在经受金融危机时出现负增长以外均保持持续增长状态。
20XX年全球范围内粗钢产量11.65亿吨,ZG达到5.68吨,ZG在全球钢材市场上的产量及消费量表现出强劲的态势。
冷轧是指金属进行礼制变形时的温度在再结晶温度以下,实际一般是指带钢在室温下进行轧制加工而不加热。
利用冷轧技术生产的带材和钢板精确度高,而且性能优良,其主要特点为轧制温度低,可以获得精确的尺寸和均匀的厚度,可以获得很薄的带材,这是热轧技术无法做到的;冷轧产品具有很好的力学性能和工艺性能,可以获得优越的表面质量,可以幸免热轧生产的带钢具有的缺陷,并且可以操纵带钢的表面粗糙度,以满足不同的用户需求,也可以满足下一道工序的加工需求;并且可实现高速轧制,具有很高的生产效率。
2、冷轧支撑辊轴承的力学分析2.1、轴承的失效形式轴承的常火效形式命内的疲破坏命期外的失效,其中寿命内的疲劳点蚀、剥落、塑性变形、磨损与胶合。
轴承的非常失效形式发生在寿命期内,可能会出现在滚子、内圈、外圈滚道或保持架上具体表现形式为破裂、取性变形或烧独等。
(此处需要修改,语句不顺)2.2、轴承的失效机理图1 轴承的运动及受力从运动学原理上分析,轴承的失效可能源于内倒随捉轴的高速旋转,或滚子高速自转和公转。
- 1、下载文档前请自行甄别文档内容的完整性,平台不提供额外的编辑、内容补充、找答案等附加服务。
- 2、"仅部分预览"的文档,不可在线预览部分如存在完整性等问题,可反馈申请退款(可完整预览的文档不适用该条件!)。
- 3、如文档侵犯您的权益,请联系客服反馈,我们会尽快为您处理(人工客服工作时间:9:00-18:30)。
新型冷连轧机支承辊的制造
摘要:在新型冷连轧机上增加工作辊刚度,直接或间接承受轧制载荷的轧辊称
为支承辊。支承辊是轧机中用来支承工作辊或中间辊以便在轧制时防止工作辊出
现挠曲变形而影响板形质量的重要部件。支撑辊质量的优劣直接影响轧板的产量
及质量。所以本文就新型冷连轧机支承辊制 造的相关问题进行探究。
关键词:冷连轧机;支承辊;制造;重要性
引言
随着轧机向自动化、高精度、优质板形控制等方向的发展,对支承辊的质量要求也不断
提高,不仅要求辊身表面有极高的硬度和硬度均匀性,而且要求有较深的淬硬层深度。由于
合金元素 , 尤其是碳化物形成元素含量低 , 使钢的耐磨性降低 , 因此 , 此类材料不能满足大型
轧机支承辊的要求。冷轧行业为了提高轧制产品的质量, 提高轧制效率, 降低轧制成本, 用户对
国内轧辊制造厂家提出了更高的要求。
一、支承辊在新型冷连轧机制造中的重要性
支承辊是新型冷连轧机中的重要部件,用来支承工作辊或中间辊, 以防工作辊出现挠曲
变形而影响板、带的产量及质量。支承辊的质量特征为辊身表面硬度高、硬度均匀性好、辊
身淬硬层深、辊颈及辊身心部具有良好的强韧性 ; 支承辊的质量特征为耐磨性高、抗剥落性
好和抗事故性强。随着冷、热轧机向高速化、大型化、高精度方向发展, 对支承辊的要求也
在不断提高,从现代化冷、热连轧机组支承辊对材质、 辊身硬度、均匀性、淬硬层深度、残
余应力等方面的要求来看,选用锻钢支承辊更为合适。锻钢支承辊与复合铸钢支承辊相比,
具有材质均匀、耐磨性及抗剥落性更优等特点。大型锻钢支承辊属高附加值产品, 因其技术
要求高,工艺复杂,制造难度大,生产工序多、周期长等原因, 我国只有少数企业能生产,
其产量不能满足市场需求,致使现代化冷、热连轧机企业所用大型锻钢支承辊不得不依赖进
口。
二、新型冷连轧机支承辊的制造
1支承辊工作条件及性能要求
在轧制过程中,支承辊对工作辊起支承作用,保证工作辊工作时刚度高、变形小,因此,
支承辊应具有良好的刚度。在使用过程中, 支承辊始终与工作辊或中间辊滚动接触,极易产
生加工硬化现象,在 过载时局部屈服使硬化层底部产生皮下微裂纹,微裂纹扩展最终造成辊
身剥落,这就要求支承辊具有较高的接触疲劳强度、合理的应力状 态和抗裂纹扩展性能。支
承辊中部会因磨损而形成凹形,辊身两端接 触应力剧增,从而导致剥落,故要求轧辊耐磨性
优良,以延缓和减轻 凹陷辊型的形成。支承辊使用周期长,辊颈长期承受交变弯曲应力, 为
防止辊颈裂断,要求辊颈具有良好的屈服强度、韧性和抗断裂性能。
2大型锻钢支承辊最终热处理工艺
最终热处理是使支承辊达到使用要求的重要环节,随着对支承辊要求的不断提高,其最
终热处理工艺也由过去的整体加热 + 淬火 + 回火改为辊身表淬 + 回火。此工艺中辊身的表淬
尤为重要,它直接影响着辊身硬度及淬硬层深度,对产品的性能影响很大。
辊身表淬工艺应根据其综合使用性能和用户要求选定。大型锻钢支承辊先进的辊身表淬
工艺有差温淬火(差温加热 + 喷雾冷却)和整体感应淬火(整体感应加热 + 喷雾冷却)两种。
两种工艺的最大差异是淬火加热方式不同 ; 相似之处都是将锻件表面快速加热至相变温度以
上而心部保持在相变温度以下,均采用喷雾冷却。喷雾冷却是以一 定压力的水和压缩空气在
喷嘴中混合呈雾状喷向辊件进行冷却,可通过调节风压、水压方便地调整冷却强度。
辊身表淬采用差温淬火工艺,即将半精加工后超声波探伤合格 的支承辊坯先在台车炉中
进行 500 ~ 600℃整体预热,并保证辊身内外温度均匀一致,然后再将支承辊转入差温加热
炉及喷雾淬火设备, 进行辊身的差温加热及淬火处理。差温加热炉的特点是加热速度快,
1.5~ 2h 内即可将支承辊的表面温度由 500℃升到 1000℃以上 ; 加热均匀,工件在炉内
每隔一定时间旋转 90°;加热层深,支承辊在炉内保温 4h 左右加热层深度可达 200mm 左右。
辊身采用差温淬火工艺表淬的优点是,当辊身一定深度的表层达到淬火温度时,心部仍处于
奥 氏体化温度以下温度,经激烈的喷淬后可保证心部具有较小的拉应力,
从而提高支承辊的抗事故能力。
差温淬火工艺在国内大型锻钢支承辊最终热处理工艺中属先进、 成熟的工艺。Cr3 ~
Cr5 钢大型锻钢支承辊采用差温淬火工艺所生产的支承辊辊身表面硬度为 55 ~ 71HSD,淬硬
层深度≤ 100mm,硬度均匀性为±2HSD,淬火组织为贝氏体,韧性、强度较好,适用于钢厂
一般硬度和淬硬层深度要求的锻钢支承辊。但此工艺难以生产辊身硬度
>72HSD 的马氏体组织的高硬度支承辊。
辊身表淬采用整体感应淬火工艺,即将半精加工后、超声波探伤 合格的支承辊辊身进行
整体感应加热然后喷雾淬火,国内有的新建大 型锻钢支承辊生产厂拟采用此工艺。
整体感应淬火工艺在国外大型锻钢支承辊制造业中已经应用,在 国际上属最先进的最终
热处理工艺,日本 JCFC(日本铸锻钢公司)、日立和关东公司均已采用此工艺。我国还没有
这种生产工艺,宝钢2050 热轧机支承辊曾试用过 JCFC 公司用整体感应淬火热处理工艺生产
的大型锻钢支承辊,使用效果非常好。据有关专家介绍,Cr3 ~ Cr5 钢大型锻钢支承辊采用整
体感应淬火工艺所生产的辊身表面硬度为 60 ~ 80HSD,淬硬层深度≥ 100mm,硬度均匀性为
±1.5HSD,淬火组织为马氏体或马氏体+ 贝氏体。
由此可见,大型锻钢支承辊最终热处理工艺的首选应是整体感应淬火处理,经此工艺生
产的大型锻钢支承辊综合使用性能优于差温淬火处理的产品。为了缩小与国外轧辊制造业的
差距,建议轧辊制造厂与有关科研单位、大专院校密切合作,加紧研发整体感应淬火处理技
术, 力争在较短时间内填补这一国内空白,并早日应用于轧辊制造。之所以希望国内大型锻
钢支承辊的最终热处理选用整体感应淬火处理工艺, 还基于以下原因。
1.随着对板型要求的不断提高和板型控制技术 CVC、HC 的应用, 对于冷轧连续退火、热
镀锌四辊平整支承辊,要求马氏体基体组织、辊身硬度 72 ~ 78HSD,必须采用整体感应淬火
处理才能达到。2. 随着热轧机工作辊半高速钢、高速钢材质的广泛应用,支承辊的硬度及耐
磨性要求也不断提高,采用差温淬火处理工艺难以达到要求。3. 随着市场需求量的不断增大,
生产成本的压力愈来愈大,要求支承辊的换 辊周期与检修周期同步、换辊周期更长,要求支
承辊辊身表面的耐磨性及抗事故性能更好,选用整体感应淬火处理工艺更为适合。4. 整体感
应淬火处理在最终热处理工艺中最为先进,定能生产出一流的锻钢 支承辊,使锻钢支承辊在
耐磨性、断裂韧度、抗疲劳剥落等性能方面得到极大的提升,缩小与国外的差距。5. 整体感
应淬火热处理工艺的实施,可填补国内辊身表面淬火工艺的又一空白,属国内首创,属世 界
先进水平
三、结语
我国轧辊制造业要想在激烈的市场竞争中生存、发展,有力支撑 钢铁主业,生产出高技
术含量、高附加值的轧辊,适应国内外现代化 轧机用辊需求,达到与国外企业抗衡的水平,
必须不断增强自主创新 能力,有针对性和有效地进行新材料研究、新产品开发和工艺改进与
创新,同时还须改变我国轧辊制造业所存在的“小而散、多而乱”的 现状,开展战略性重组与
合作,实施强强联合共同发展,充分发挥大 型轧辊制造企业的优势,创自己的品牌,这样才
能对抗外来的竞争, 最终超越世界同行。
参考文献
[1]王文明 , 章大健 , 陈伟 . 新型冷连轧机支承辊的制造 [J]. 金属热处理,2018,43(07):167-
170.
[2]张苗兴 . 八辊五机架冷连轧机组核心工艺参数设定技术的研究[D]. 燕山大学,2018.