VSM价值流程图,精益生产工具
价值流程图-VSM

3 Level of Lean 精益生产的三个层次
Principles Of Lean 精益生产5原则
Lean Capability
5 Pursue
CIduesnttoifmy ethredVefAinLeUsEVSATLRUEE4AM(Panedrfeelimctinioatne
8
wastes)
价值流图改善的步骤 Step1: Mapping Current VSM。 绘制当前价值流图 C1.u1r:rUenndterSsttaantdecustomer demand 理解客户的需求
Future
State
1. 2: Process flow and data box 工序流数据箱
- Quick identify main process (in order)
45 Days
Op 1
1
Day
Op 2
2
Days
Op 3
2
Days
Op 4
1
Day
Op 5
5 Op 6 1
Days
Day
S/U = 1 hr CT = 1.6 min
S/U = 0.08 hr CT = 0.9 min
S/U = 0.08 hr CT = 0.9 min
S/U = 0 CT = 60 min
Map
价值流图的5大板块
Supplier
30 Days
Supplier
Loop
Bi-Monthly
MRP
Monthly Orders
880
Customer
Information
Customer Loop Takt Time = 440 min/44
VSM 价值流图
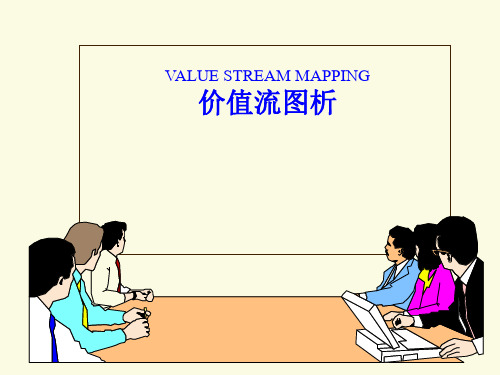
SHIPPING
F
Staging
P
2 days
Production = 4.5 days lead time Value added = 211.5 sec
time
我们怎样才能实现未来状态
精益三要素
1.
节拍Takt
2.
流动Flow
3.
拉动Pull
五、 透过价值流的分析,制订改善步骤
• Helps identify the sources of waste 帮助发现浪费源
• Shows the linkage between information flow and the material flow 展示了信息流与物流之间的联系
• Provides a communication tool for all levels 广泛沟通的 工具
时间的增值分析画在下段;
2)把代表顾客的记号画在纸的右上端,用
代表;
3)把代表供应商的记号画在纸的左上端,用
代表;
4)TAKT的计算,TAKT(客户需求节拍)=某产品客户的每天平均需求量/每
天的作业加工时间,
三、 价值流的制作步骤
供应商
客户
第二步:画信息流(信息流或分为电子信息流和手工传递信息流)
STEP 2
抽出问题点:
1)发现问题,排除过加工过程中不增值的时间; --- 消除停滞? --- 减少临时库存量? --- 减少搬运的次数? --- 减少搬运的距离? --- 消除瓶颈工序? --- 均衡生产 ? ……
2)用爆炸符号把问题标出来? 3)组织大家对问题点进行讨论?
SUCCESS
THANK YOU
beyondsingleprocesslevel建立超越单个工艺过程层次而看到宏观生产流程的能力helpsidentifywaste帮助发现浪费源linkagebetweeninformationflowmaterialflow展示了信息流与物流之间的联系communicationtoolalllevels广泛沟通的工具helpsestablishprioritiesbasedflow确定优先次序tiestogetherleanconceptstechniqueshelpsavoidcherrypicking结合精益的概念与技术?避免只挑容易的来改进implementationplan形成实施计划的基础scrapmanufacturingprocesskaizen闪光点爆炸点外部资源客户数据盒库存卡车运输成品至客户推动箭头超市缓冲区安全库存手工的信息流electronicinformationflowproductionkanbanwithdrawalkanbansignalkanbankanbanpostvsmtools绘制价值流分析图所需工具valuestreammappingsteps价值流图析步骤productfamily产品族工作计划及实施currentstatus当前状态图futurestatus未来状态图物流图标assembly内部工艺过程weekl45sec30minsshifts2scrap数据筐库存300piecesday推动式物料流动物流来自外部资源最多20fifo先进先出顺序流超市拉动通用图标缓冲区或安全库存换型强调改进信息图标手工信息流电子信息流补充看板生产看板分批地看板到达每周计信息oxo载荷均衡看板信号看板收集盒现场了解进度安排外部资源xyzcorporation操作工valuestreammappingicons绘价值流分析图价值流的制作步骤供应商第一步
VSM -- 价值流程图--Value Stream Mapping
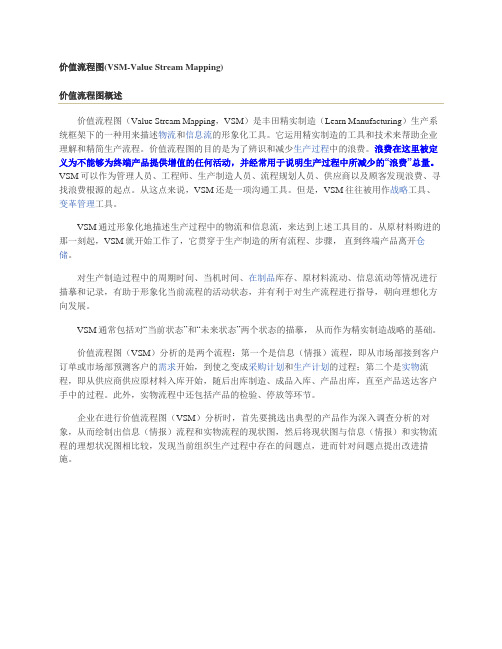
价值流程图(VSM-Value Stream Mapping)价值流程图概述价值流程图(Value Stream Mapping,VSM)是丰田精实制造(Learn Manufacturing)生产系统框架下的一种用来描述物流和信息流的形象化工具。
它运用精实制造的工具和技术来帮助企业理解和精简生产流程。
价值流程图的目的是为了辨识和减少生产过程中的浪费。
浪费在这里被定义为不能够为终端产品提供增值的任何活动,并经常用于说明生产过程中所减少的“浪费”总量。
VSM可以作为管理人员、工程师、生产制造人员、流程规划人员、供应商以及顾客发现浪费、寻找浪费根源的起点。
从这点来说,VSM还是一项沟通工具。
但是,VSM往往被用作战略工具、变革管理工具。
VSM通过形象化地描述生产过程中的物流和信息流,来达到上述工具目的。
从原材料购进的那一刻起,VSM就开始工作了,它贯穿于生产制造的所有流程、步骤,直到终端产品离开仓储。
对生产制造过程中的周期时间、当机时间、在制品库存、原材料流动、信息流动等情况进行描摹和记录,有助于形象化当前流程的活动状态,并有利于对生产流程进行指导,朝向理想化方向发展。
VSM通常包括对“当前状态”和“未来状态”两个状态的描摹,从而作为精实制造战略的基础。
价值流程图(VSM)分析的是两个流程:第一个是信息(情报)流程,即从市场部接到客户订单或市场部预测客户的需求开始,到使之变成采购计划和生产计划的过程;第二个是实物流程,即从供应商供应原材料入库开始,随后出库制造、成品入库、产品出库,直至产品送达客户手中的过程。
此外,实物流程中还包括产品的检验、停放等环节。
企业在进行价值流程图(VSM)分析时,首先要挑选出典型的产品作为深入调查分析的对象,从而绘制出信息(情报)流程和实物流程的现状图,然后将现状图与信息(情报)和实物流程的理想状况图相比较,发现当前组织生产过程中存在的问题点,进而针对问题点提出改进措施。
VSM价值流程图

供应商
信息控制
工序B 工序A
客户
工序C
理解流程…看到价值…憧憬未来状态
价值流程图的发展
起源于1980s的TOYOTA, “物与情报流程图”
大野耐一(Taiichi Ohno )
新乡重夫(Shigeo Shingo)
随着1998年美国Mike Rother & John Shook的著作《学习如何看:价值 流程图创造价值和消除浪费》而风靡全球。
谢谢!1来自2002年11月某企业在推进JIT 改善活动,总经理发出指示,要求在全公司内开展 全员参与的改善活动,以对市场变化做出快速反应。在改善过程中选择了一种销 售金额大、生产数量多、生产周期长的零件进行分析典型产品进行分析。对这种 零件进行详细的调查后发现,这种零件的基本资料为:订单每月4 次,订单量每 月约14000件,每月进行3 次生产,日产量约3600件,每周送货两次。相关人员 据此画出了企业的信息流程和实物流程的现状图,如图所示。从现状图中粗虚线 以上部分可以看到:客户向香港的分公司发出订单,香港分公司再以E-mail 或传 真的形式传到深圳的这家工厂。工厂接到订单后花了两天时间制定生产计划,又 花了两天分别向两家供应商发送原材料采购订单。整个信息流L/T 是8 天时间, 海外材料到货L/T 则是60 天。现状图中粗虚线以下部分为实物流:提前3~5 天 把原料领好后,在工厂的二栋二楼中开始组织生产。生产完成后由品质管理科开 始检验,停留1 天后更换场地进行包装,在包装区域内停留十几个小时。包装完 成后,品质管理科每隔6 小时抽检一次,然后进行组装。组装完成后再由品质管 理科进行确定,确定后的成品在库房中放置14 天后开始出货。整个实物流L/T 折 算下来需要23~28 天的时间。工厂设想的信息(情报)流和实物流的理想状况 如第下图所示。从理想状况图中可以看到:接到紧急订单后,只需要花费2 天时 间就可形成生产计划;在最紧急的状态下,只需要花费6 天的时间即可完成实物 流。因此,从领料开始算起,这家工厂设计的理想的信息流L/T 为2 天,理想的 实物流L/T 为6.05 天。
价值流程图VSM管理

价值流程图VSM管理什么是价值流程图?定义价值流程图(Value Stream Mapping,VSM)是丰田精实制造(Learn Manufacturing)生产系统框架下的一种用来描述物流和信息流的形象化工具。
它运用精实制造的工具和技术来帮助企业理解和精简生产流程。
价值流程图的目的是为了辨识和减少生产过程中的浪费。
浪费在这里被定义为不能够为终端产品提供增值的任何活动,并经常用于说明生产过程中所减少的“浪费”总量。
VSM可以作为管理人员、工程师、生产制造人员、流程规划人员、供应商以及顾客发现浪费、寻找浪费根源的起点。
从这点来说,VSM还是一项沟通工具。
但是,VSM往往被用作战略工具、变革管理工具。
VSM通过形象化地描述生产过程中的物流和信息流,来达到上述工具目的。
从原材料购进的那一刻起,VSM就开始工作了,它贯穿于生产制造的所有流程、步骤,直到终端产品离开仓储。
对生产制造过程中的周期时间、当机时间、在制品库存、原材料流动、信息流动等情况进行描摹和记录,有助于形象化当前流程的活动状态,并有利于对生产流程进行指导,朝向理想化方向发展。
VSM通常包括对“当前状态”和“未来状态”两个状态的描摹,从而作为精实制造战略的基础。
价值流程图的历史1980年代,丰田公司的首席工程师Taiichi Ohno与sensei Shigeo Shingo率先运用去处生产浪费的方法来获取竞争优势,他们的主要出发点是提高生产效率,而非提高产品质量。
之所以这么做,是因为他们认为生产效率的提高将有助于精实制造,从而能够暴露出系统中的深层的浪费问题和质量问题。
因此,对浪费问题发起的系统性攻击也就是对质量问题的深层原因展开攻击,对根本性的管理问题展开攻击。
丰田生产系统中认定的七种常见浪费(括号中内容为Jones的表述):1。
生产过剩(快于必要的速度);2。
等待;3。
运输(搬运);4。
不当流程;5。
不必要的库存(超出的库存);6。
不必要的行动;7。
精益工具

二、精益工具在以上的精益改善活动中提到很多精益工具,以下将对一些常用的精益工具作一简单介绍。
(1)价值流程图VSM:价值流程图(Value Stream Mapping)是丰田精益制造(Lean Manufacturing)生产系统框架下的一种用来描述物流和信息流的形象化工具。
它运用精益制造的工具和技术来帮助企业理解和精简生产流程。
VSM可以作为管理人员、工程师、生产制造人员、流程规划人员、供应商以及顾客发现浪费、寻找浪费根源的起点。
价值流分析就是通过价值流程图来辨识和减少生产过程中的浪费,浪费在这里被定义为不能够为终端产品提供增值的任何活动,并经常用于说明生产过程中所减少的“浪费”总量。
(2)特性要因图(鱼骨图):1953年,日本管理大师石川馨先生所提出的一种把握结果(特性)与原因(要因)的极方便而有效的方法,因其形状很像鱼骨,是一种发现问题“根本原因”的方法,是一种透过现象看本质的分析方法,因此也被称作鱼骨图或者鱼刺图。
(3)SIPOC模型:SIPOC模型是一代质量大师戴明提出来的组织系统模型,是一门最有用而且最常用的,用于流程管理和改进的技术。
是过程管理和改进的常用技术,作为识别核心过程的首选方法。
SIPOC其中每个字母各代表:Supplier 供应者;Input 输入;Process 流程;Output 输出;Client 客户。
戴明认为任何一个组织都是一个由供应者、输入、流程、输出、还有客户这样相互关联、互动的5个部分组成的系统。
这5个部分的英文单词的第一字母就组成SIPOC,因而把此称作SIPOC组织系统模型。
其优点是:1)能展示出一组跨越职能部门界限的活动;2)不论一个组织的规模有多大,SIPOC图都可以用一个框架来勾勒其业务流程;3)有助于保持“全景”视角。
(4)潜在失效模式分析(FMEA):FMEA(Potential Failure Mode and Effects Analysis)是在产品设计阶段和过程设计阶段,对构成产品的子系统、零件,对构成过程的各个工序逐一进行分析,找出所有潜在的失效模式,并进行分析其可能的后果,从而预先采取必要的措施,以提高产品的质量和可靠性的一种系统化的活动。
精益工具之价值流程图
客户订单 采购原材料
生产制造
成品入库
发货
二、价值流
What is The Function Of Value Steam Function? 价值流的作用? ①一个交流或改善的公共基础平台; ②一个贯穿“产-供-销”的实物流和信息流的流程汇集; ③一个现状描述、发现问题及未来展示的工具; ④一个串联精益概念和技术的纽带或桥梁; ⑤一个优秀的精益生产改善工具;
1.CT: 2.ACT: A: 4.OEE: 5.FTQ: 6.C/O: 7.Avail. Time: 8.Shift:
⑴ 生产过程:
定义生产流程(冲压、焊接、机加、装配等),每班配备
人数,流程设备台数等;
①与②协
⑵数据盒子:
同使用
1.CT:Cycle Time,节拍;
2.ACT:Actual Cycle Time,实际节拍=CT ÷ OEE;
FTQ=First Time Good Parts ÷ Total Parts
6.C/O:Changeover Time (Good Part To Good Part);
7.Avail. Time:用于生产的总时间(Non OEE);
8.Shift:班次,即开班次数.
三、价值流绘制及分析
⑶ 外部资源(Out side Sources):
机:11
1.8
1.2
K
K
C/T:245S
C/O:15M
Shift:3
TVA:1715S
OEE:0.85
245S
产品 日需求量 A 300 B 200
客户
C 100
装配
人:15 机:2
检查
人:1 机:1
《VSM价值流图中》课件
数字化转型
随着数字化转型的加速,VSM价 值流图将更加依赖于大数据和人 工智能技术,实现更精准的分析 和预测。
可持续性发展
未来,VSM价值流图将更加关注 可持续性发展目标,通过减少资 源浪费和环境污染,实现经济、 环境和社会综合效益的提升。
感谢您的观看
THANKS
细致、专业、精准
04
VSM价值流图的优化策略
优化生产流程
减少生产浪费
通过消除生产过程中的浪费,如等待 时间、过量生产等,提高生产效率。
优化生产线布局
引入自动化和智能化技术
利用自动化设备和智能化技术,提高 生产过程的自动化和智能化水平,降 低人工干预和错误率。
合理安排生产线布局,降低物料搬运 距离,提高生产线的协同效率。
05
VSM价值流图的未来发展
VSM价值流图与其他管理工具的结合
VSM与精益生产结合
通过VSM价值流图与精益生产管理 工具的结合,企业可以更好地识别和 消除浪费,提高生产效率和产品质量 。
VSM与六西格玛结合
VSM价值流图可以与六西格玛管理方 法结合,通过数据分析和流程改进, 降低变异和缺陷,提升流程稳定性和 效率。
VSM价值流图在智能制造中的应用
实现生产透明化
VSM价值流图可以帮助智能制造企业 实现生产过程的可视化,实时监控生 产数据,提高生产透明度和可预测性 。
优化资源配置
通过VSM价值流图的分析,智能制造 企业可以更好地了解生产过程中的瓶 颈和浪费,优化资源配置,提高生产 效率和设备利用率。
VSM价值流图的发展趋势和展望
降低库存成本
通过合理的库存管理和优 化库存结构,降低库存成 本。
提高生产效率
通过优化生产流程和提高 生产效率,降低生产成本 。
(免费资料)精益生产必胜宝典之价值流程图VSMVisio图标总览.doc
精益生产必胜宝典之价值流程图VSM Visio图标总览价值流程图是干啥用的?要实施精益生产首先要绘制价值流程图(Value Steam Map),否则就是做精益生产就是瞎做。
有人不服,问道为什么非要做价值流程图不可呢?别急,请先回答我四个问题。
1 •你了解公司的现状吗?(客户需求,生产,物流,供应商,设备状态,定单响应时间等)2你认为公司现状有哪些地方急需改进吗?(各个环节中的浪费)3•你知道整个公司怎样改进,才能满足未来客户需求吗?(关键改进项目)4•最后一点最重要,你们公司其他人对上述三个问题有统一的回答,还是从各自的部门出发有不同的见解?要做精益生产,首先要对以上几个问题有科学明晰的答案。
而价值流程图VSM 就是帮你澄清上述的问题。
什么是价值流?价值只有在流动中才能够升值。
举个例子,你有一万块钱,藏在你家橱柜里,放一年,到年底还是一万块钱。
如果你把它存进银行,假设年利率2%,年底连本带息一万零二百元。
如果你将其投入到股市,假设收益率是8%,年底收益一万零八百元。
银行和股市是实现金钱流动的场所,只要参与流动,钱就有可能生钱。
流动的越快,增值就越快。
公司经营也是一样的道理。
价值在流动中获利。
但地球人都知道,股市有风险,入市须谨慎,弄得不好,有可能连老本都赔光了。
怎么办呢?只有靠自己掌握足够的知识、技能再加上努力工作去管理风险、控制风险、最终消除风险。
绘制价值流程图用来了解价值在公司中流动的状况,在此基础上分析如何改进从而实现快速获利。
而从某种意义上讲,精益生产的有效实施就是公司控制价值流动风险的最有力的保障。
价值流程图中包括哪些流动?价值流程图内的流动信息包括:工作流,物料流,信息流等。
作为一名精益生产的推广者,要首先了解这些流动信息和要素。
后续介绍的相关图例说明能够帮助人家了解这吐要素。
绘制价值流程图常用的软件是什么?早期的价值流程图是手绘的,现在有些五百强的公司还强调用铅笔手绘价值流程图,为的是大家边绘制边讨论,增加理解和认识,但改来改去效率很低O现在多数公司都用计算机软件来做VSM,最常用的软件是Microsoft Visio绘图软件。
价值流程图-VSM
人工讯息流 电子讯息流
讯号广告牌
广告牌搜集点
生产广告牌
取用广告牌
拉动指定单元
周排程计划 排程
查看生产计划
负荷平准化 电子邮件讯息
质量检测点
Q
质量问题 50 PPM
IN PROCESS ASSEMBLY LINE INSPECTION
质量问题的测量结果 量测流程与量测方式
-9-
资讯前置时间
1-2 Days
前置时间变异 单位
注计 V = Variable,变动 M = Manual Activity,人工作业 A = Automated Activity,自动作业
人员
VSM的图示 –其它
重工循环
2人, 1天 执行重工所需的人数和时间
改善 机会点
-10-
步骤一:辨识产品族
首先要选定你的产品,也就是研究的对象。
3. 定义资讯流及作业,并加上资讯方块 4. 完成资料方块,并描述重要的活动状态 5出质量检核点及返修闭环,包括质量绩效、返修资源等 7. 给定前置作业时间,并了解时间变异的程度
-14-
价值流图绘制要点
使用铅笔、橡皮擦和便条纸绘制 直接绘制在大白报纸上,避免使用电脑软体绘制 可以使用下列颜色,使价值流图更容易阅读
资讯
VSM
物料
非增加价值活动 (non valueadded)
增加价值的活动 (value added)
-4-
价值流图四大步骤
1.选定范围
选定产品族,及价值流图范围
2.绘制现况图
绘制现况图了解目前流程如何运作,现况 图是未来图的基础
标
准
化 未
3.绘制未来图
运用精益原则,设计未来方案, 并绘制成未来图
- 1、下载文档前请自行甄别文档内容的完整性,平台不提供额外的编辑、内容补充、找答案等附加服务。
- 2、"仅部分预览"的文档,不可在线预览部分如存在完整性等问题,可反馈申请退款(可完整预览的文档不适用该条件!)。
- 3、如文档侵犯您的权益,请联系客服反馈,我们会尽快为您处理(人工客服工作时间:9:00-18:30)。
信号看板 Signal Kanban
信号看板 Signal Kanban
信号看板 Signal Kanban
信号看板 Signal Kanban
信号看板 Signal Kanban
Milk-run
Milk-run
Milk-run
Milk-run
Milk-run
Milk-run
Milk-run
Milk-run
Shifts= 班次
Quality=
%
合格率
# Operator= 员工数
工序Process
数据框Data
P/T= 加工时间
C/T= 周期时间
C/O= 换模时间
U/T= 开机时间
Shifts= 班次
Quality=
%
合格率
# Operator= 员工数
工序Process
数据框Data
P/T= 加工时间
推动Push
推动Push
推动Push
推动Push
推动Push
推动Push
推动Push
推动Push
推动Push
推动Push
推动Push
推动Push
先进先出FIFO FIFO
先进先出FIFO FIFO
先进先出FIFO FIFO
先进先出FIFO FIFO
先进先出FIFO FIFO
先进先出FIFO FIFO
Problem Problem
Improvement Idea Idea
Example Value Stream
Customer
MRP
20 ton
Excess Inventory
Pencil Lead Forming
3500 pcs
800 pcs
Pencil Wood Cutting
230 pcs
Implement Pull
Pencil Assembly
FiFo
Pencil Varnishing
FiFo
Pencil Package
Customer
生产看板 Production Kanban
生产看板 Production Kanban
生产看板 Production Kanban
生产看板 Production Kanban
生产看板 Production Kanban
信号看板 Signal Kanban
信号看板 Signal Kanban
信号看板 Signal Kanban
安全库存 Safety Stock
安全库存 Safety Stock
安全库存 Safety Stock
安全库存 Safety Stock
超市 Supermarket
超市 Supermarket
超市 Supermarket
超市 Supermarket
超市 Supermarket
超市 Supermarket
超市 Supermarket
超市 Supermarket
卡车 Truck
卡车 Truck
卡车 Truck
卡车 Truck
卡车 Truck
卡车 Truck
卡车 Truck
卡车 Truck
生产看板 Production Kanban
生产看板 Production Kanban
生产看板 Production Kanban
先进先出FIFO FIFO
先进先出FIFO
先进先出FIFO FIFO
先进先出FIFO FIFO
先进先出FIFO FIFO
先进先出FIFO FIFO
先进先出FIFO FIFO
先进先出FIFO FIFO
Withdraw Withdraw
Withdraw Withdraw
客户Customer
客户Customer
客户Customer
客户Customer
客户Customer
客户Customer
客户Customer
客户Customer
供应商 Supplier
供应商 Supplier
供应商 Supplier
供应商 Supplier
供应商 Supplier
供应商 Supplier
Withdraw Withdraw
Withdraw Withdraw
Withdraw
Withdraw
Withdraw
Withdraw
Withdraw
Withdraw
Withdraw
Withdraw
工序Process
数据框Data
P/T= 加工时间
C/T= 周期时间
C/O= 换模时间
U/T= 开机时间
Levelling
Manual Information Flow
Digital Information Flow
Sequenced Pull Ball (and alternative)
Other Symbols
Document
Leveling Board
Kanban Post
Database
Manual Observation
•C/T: 12s •C/O: 15 min •1 Worker •3 Processes parallel
Customer
Customer
Data Process Box (and Alternative)
Customer
Customer
MRP
Work Cell Worker
Inventory
FIFO Lane (and alternatives)
(Production) Kanban (and alternative)
PI
P
Batch (Production) Triangle/Signal Kanban
Kanban
(and alternative)
S
Withdrawal Kanban (and alternative)
PW
W
Batch Withdrawal Kanban
FiFo Max 25
Supermarket
Cross Dock
Cross Dock
Material Flow
Push Arrow
Transport Finished Goods
Withdrawal
Sequenced Pull Ball
Milk Run
Fork Lift
Truck
Information Flow
供应商 Supplier
供应商 Supplier
库存 Stock
库存 Stock
库存 Stock
库存 Stock
库存 Stock
库存 Stock
库存 Stock
库存 Stock
安全库存 Safety Stock
安全库存 Safety Stock
安全库存 Safety Stock
安全库存 Safety Stock
C/T= 周期时间
C/O= 换模时间
U/T= 开机时间
Shifts= 班次
Quality=
%
合格率
# Operator= 员工数
Process Box
Milling
Process Box (shared with other value streams)
Milling
Process Box
Milling