价值流程图(Chinese)..
价值流程图

=22 CT = 117s 节拍时间:10S 等待3天 可用时间:11H Quality 97% 360只/H 3天 确定精益生产改善机会 38天 制造时间=23.08+13+42+3+38=119.08天 I 等待31天
IQC检验
CT = 1243s 节拍时间:12S 等待13天 可用时间:11H Quality 90% 300只/H 13天
.
定拍生产循环
出货
裁剪
= 6 7天库存 CT =148s 节拍时间:12S 可用时间:22H Quality98%
=78
=52 CT = 1064s 节拍时间:12S 可用时间:11H Quality95 %
=26 CT = 117s 节拍时间:12S 可用时间:11H Quality 97%
FIFO
注意!
产品多样性可能成为限制性因素
23
形成愿景
我们想让它成为何种工厂? 什么可以确保客户满意? 我们想得到客户何种评价? 我们的愿景和组织商业目标是否一致?
24
在现状图上标注改进点
确定合理的排期点
明确系统中哪个点是节拍时间最长的,并将其单
独列出 确定哪些工序可以合并进单元(创造生产流)
30
项目完成了?
当未来形态成为现实,它就成为现在形态 现在我们只是站在持续改善提高旅程的起点 为完美而努力!
31
什么是精益生产-三个层次
32
什么是精益生产-价值流层五个原则
Value 价值
Perfect 完美
站在客户 的立场上
Value Stream 价值流
在价值流图绘出从左至右的时间轴,按事件先
后顺序标出
绘制价值流程图

27,600 sec/shift
I
1200 L 640 R
ASSEMBLY #2
1
C/T = 40 seconds C/O = 0
Uptime = 100% 2 Shifts
27,600 sec/shift
I
2700 L 1440 R
SHIPPING Staging
1x Daily
I
1600 L 850 R
ASSEMBLY #1 1
I
1200 L 640 R
C/T = 62 seconds C/O = 0
Uptime = 100% 2 Shifts
27,600 sec/shift
ASSEMBLY #2
I
1
2700 L 1440 R
C/T = 40 seconds C/O = 0
Uptime = 100% 2 Shifts
27,600 sec/shift
SHIPPING Staging
31
ACME 冲压加工
#1组装
2 个部件号 1 个操作者 2 班制 没有设置
62 秒操作时间 100%正常运行使用 2次休息–每次 10 分钟 库存:
- 1600 LH
- 850 RH
供方
过程1 上游
过程 2
顾客
过程3 下游
12
价值流图
以笔纸为工具,让你看到 和理解材料和信息的流, 产品是如何通过价值流形 成的
信息
生产流动
材料
价值流图-要点
通常在巡视时收集信息
先快速浏览门对门情况
从发货点和工作上游开始
自己计算 (回避系统里的数字)
什么是价值流程图

什么是价值流程图?定义价值流程图(Value Stream Mapping,VSM)是丰田精实制造(Learn Manufacturi ng)生产系统框架下的一种用来描述物流和信息流的形象化工具。
它运用精实制造的工具和技术来帮助企业理解和精简生产流程。
价值流程图的目的是为了辨识和减少生产过程中的浪费。
浪费在这里被定义为不能够为终端产品提供增值的任何活动,并经常用于说明生产过程中所减少的“浪费”总量。
VSM可以作为管理人员、工程师、生产制造人员、流程规划人员、供应商以及顾客发现浪费、寻找浪费根源的起点。
从这点来说,VSM还是一项沟通工具。
但是,VSM往往被用作战略工具、变革管理工具。
?VSM通过形象化地描述生产过程中的物流和信息流,来达到上述工具目的。
从原材料购进的那一刻起,VSM就开始工作了,它贯穿于生产制造的所有流程、步骤,直到终端产品离开仓储。
对生产制造过程中的周期时间、当机时间、在制品库存、原材料流动、信息流动等情况进行描摹和记录,有助于形象化当前流程的活动状态,并有利于对生产流程进行指导,朝向理想化方向发展。
VSM通常包括对“当前状态”和“未来状态”两个状态的描摹,从而作为精实制造战略的基础。
?价值流程图的历史1980年代,丰田公司的首席工程师Taiichi Ohno与sensei Shigeo Shingo率先运用去处生产浪费的方法来获取竞争优势,他们的主要出发点是提高生产效率,而非提高产品质量。
之所以这么做,是因为他们认为生产效率的提高将有助于精实制造,从而能够暴露出系统中的深层的浪费问题和质量问题。
因此,对浪费问题发起的系统性攻击也就是对质量问题的深层原因展开攻击,对根本性的管理问题展开攻击。
丰田生产系统中认定的七种常见浪费(括号中内容为Jones的表述):1. 生产过剩(快于必要的速度);2. 等待;3. 运输(搬运);4. 不当流程;5. 不必要的库存(超出的库存);6. 不必要的行动;7. 次品(改正错误)。
价值流程图
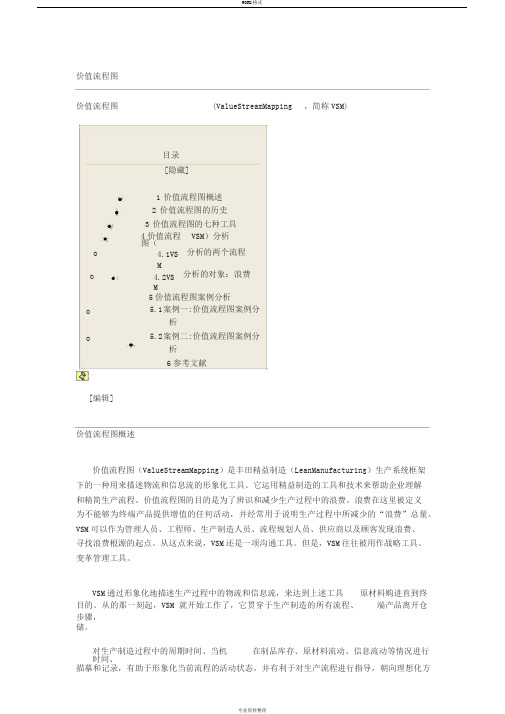
价值流程图价值流程图(ValueStreamMapping ,简称VSM)目录[隐藏]1价值流程图概述2价值流程图的历史3价值流程图的七种工具4价值流程图(VSM)分析o 4.1VSM分析的两个流程o 4.2VSM分析的对象:浪费5价值流程图案例分析o 5.1 案例一:价值流程图案例分析o 5.2 案例二:价值流程图案例分析6参考文献[编辑]价值流程图概述价值流程图(ValueStreamMapping)是丰田精益制造(LeanManufacturing)生产系统框架下的一种用来描述物流和信息流的形象化工具。
它运用精益制造的工具和技术来帮助企业理解和精简生产流程。
价值流程图的目的是为了辨识和减少生产过程中的浪费。
浪费在这里被定义为不能够为终端产品提供增值的任何活动,并经常用于说明生产过程中所减少的“浪费”总量。
VSM可以作为管理人员、工程师、生产制造人员、流程规划人员、供应商以及顾客发现浪费、寻找浪费根源的起点。
从这点来说,VSM还是一项沟通工具。
但是,VSM往往被用作战略工具、变革管理工具。
VSM通过形象化地描述生产过程中的物流和信息流,来达到上述工具目的。
从的那一刻起,VSM就开始工作了,它贯穿于生产制造的所有流程、步骤,原材料购进直到终端产品离开仓储。
对生产制造过程中的周期时间、当机时间、在制品库存、原材料流动、信息流动等情况进行描摹和记录,有助于形象化当前流程的活动状态,并有利于对生产流程进行指导,朝向理想化方向发展。
VSM通常包括对“当前状态”和“未来状态”两个状态的描摹,从而作为精益制造战略的基础。
价值流程图(VSM)分析的是两个流程:第一个是信息(情报)流程,即从市场部接到客户订单或市场部预测客户的需求开始,到使之变成采购计划和生产计划的过程;第二个是实物流程,即从供应商供应原材料入库开始,随后出库制造、成品入库、产品出库,直至产品送达客户手中的过程。
此外,实物流程中还包括产品的检验、停放等环节。
价值流程图课件

10
一些常见的价值流绘图符号
客户/供应商
机器
=6
CT = 1500” C/O = n/a
Uptime 100% Quality 95%
流程 人力 流程基线数据
“推动”系 统
90/60/30 预测
电子信号 (传真)
一个月
运输
I
库存
加工速率 增值时间
1.9 天
1.8 天
150 秒
800 秒
典型的数据 (基线)
节拍时间 =总的产品生产时间/客户需求
的数量
13
现时价值流图应如何表示?
一旦收集到基线数据并计算出TAKT,我们就可以制作现时价值流图.
14
供应商 等待21天 原料入仓
等待2H
女雪狗价值流现状图
采购
PMC
业务
HallMark 出货
等待24H FIC验货
货仓
I 等待24H
IQC检验
I 述
q 产品系列内的产品数量
q 每种产品需求
q 数量
q 需求频率
9
步骤2: 制作现时状态图
建议如下:
q 在 “工厂内部”开始 q 计算节拍时间 q 尽可能地使用实际观察到的数据 (搜集的基线数据) q 由流程末端开始反向绘制 q 记录数据之前要走遍整个生产流程 q 每个成员制作出一张价值流图 q 以秒为计算时间单位 q 使用铅笔与纸张 q 在价值流图绘出从左至右的时间轴,按事件先
7
绘制价值流图的步骤
1. 从PR分析中选取产品系列 2. 制作现时状态图 3. 制作未来状态图 4. 设计行动计划
8
步骤1: 选取产品系列 (回顾PQ/PR分析)
什么是产品系列?
价值流程图
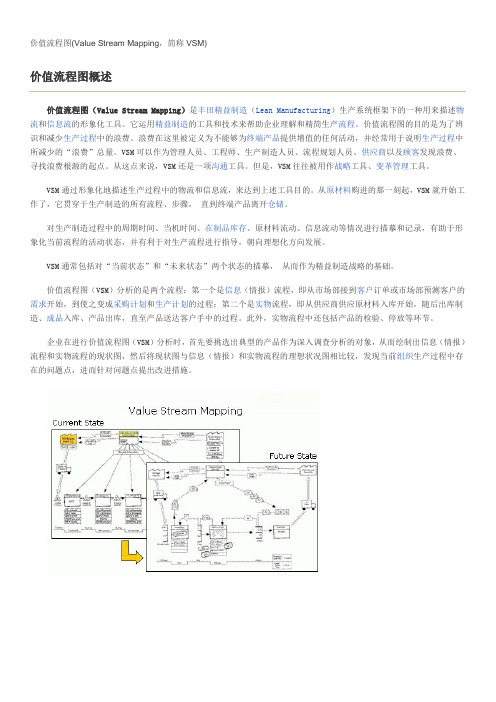
价值流程图(Value Stream Mapping,简称VSM)价值流程图概述价值流程图(Value Stream Mapping)是丰田精益制造(Lean Manufacturing)生产系统框架下的一种用来描述物流和信息流的形象化工具。
它运用精益制造的工具和技术来帮助企业理解和精简生产流程。
价值流程图的目的是为了辨识和减少生产过程中的浪费。
浪费在这里被定义为不能够为终端产品提供增值的任何活动,并经常用于说明生产过程中所减少的“浪费”总量。
VSM可以作为管理人员、工程师、生产制造人员、流程规划人员、供应商以及顾客发现浪费、寻找浪费根源的起点。
从这点来说,VSM还是一项沟通工具。
但是,VSM往往被用作战略工具、变革管理工具。
VSM通过形象化地描述生产过程中的物流和信息流,来达到上述工具目的。
从原材料购进的那一刻起,VSM就开始工作了,它贯穿于生产制造的所有流程、步骤,直到终端产品离开仓储。
对生产制造过程中的周期时间、当机时间、在制品库存、原材料流动、信息流动等情况进行描摹和记录,有助于形象化当前流程的活动状态,并有利于对生产流程进行指导,朝向理想化方向发展。
VSM通常包括对“当前状态”和“未来状态”两个状态的描摹,从而作为精益制造战略的基础。
价值流程图(VSM)分析的是两个流程:第一个是信息(情报)流程,即从市场部接到客户订单或市场部预测客户的需求开始,到使之变成采购计划和生产计划的过程;第二个是实物流程,即从供应商供应原材料入库开始,随后出库制造、成品入库、产品出库,直至产品送达客户手中的过程。
此外,实物流程中还包括产品的检验、停放等环节。
企业在进行价值流程图(VSM)分析时,首先要挑选出典型的产品作为深入调查分析的对象,从而绘制出信息(情报)流程和实物流程的现状图,然后将现状图与信息(情报)和实物流程的理想状况图相比较,发现当前组织生产过程中存在的问题点,进而针对问题点提出改进措施。
价值流程图的历史1980年代,丰田公司的首席工程师Taiichi Ohno与sensei Shigeo Shingo率先运用去除生产浪费的方法来获取竞争优势,他们的主要出发点是提高生产效率,而非提高产品质量。
价值流程图绘制
价值流程图(Value Stream Mapping,简称 VSM)
价值流程图概述
价值流程图(Value Stream Mapping)是丰田精益制造(Lean Manufacturing)生产系统框架下的 一种用来描述物流和信息流的形象化工具。它运用精益制造的工具和技术来帮助企业理解和精简生产流 程。价值流程图的目的是为了辨识和减少生产过程中的浪费。浪费在这里被定义为不能够为终端产品提供 增值的任何活动,并经常用于说明生产过程中所减少的“浪费”总量。VSM 可以作为管理人员、工程师、生 产制造人员、流程规划人员、供应商以及顾客发现浪费、寻找浪费根源的起点。从这点来说,VSM 还是 一项沟通工具。但是,VSM 往往被用作战略工具、变革管理工具。 VSM 通过形象化地描述生产过程中的物流和信息流,来达到上述工具目的。从原材料购进的那一刻 起,VSM 就开始工作了,它贯穿于生产制造的所有流程、步骤, 直到终端产品离开仓储。 对生产制造过程中的周期时间、当机时间、在制品库存、原材料流动、信息流动等情况进行描摹和记 录,有助于形象化当前流程的活动状态,并有利于对生产流程进行指导,朝向理想化方向发展。 VSM 通常包括对“当前状态”和“未来状态”两个状态的描摹, 从而作为精益制造战略的基础。 价值流程图(VSM)分析的是两个流程:第一个是信息(情报)流程,即从市场部接到客户订单或市 场部预测客户的需求开始,到使之变成采购计划和生产计划的过程;第二个是实物流程,即从供应商供应 原材料入库开始,随后出库制造、成品入库、产品出库,直至产品送达客户手中的过程。此外,实物流程 中还包括产品的检验、停放等环节。 企业在进行价值流程图(VSM)分析时,首先要挑选出典型的产品作为深入调查分析的对象,从而绘 制出信息(情报)流程和实物流程的现状图,然后将现状图与信息(情报)和实物流程的理想状况图相比 较,发现当前组织生产过程中存在的问题点,进而针对问题点提出改进措施。
价值流程图绘制方法(精益生产)
对工作流程进行优化,消除浪费,提高生产效率。
引入新技术
引入新技术和设备,提高生产过程的自动化和智能化水平。
培养员工的价值流意识与能力
培训员工
对员工进行价值流相关培训,提高其对价值流 的认识和理解。
鼓励员工参与
鼓励员工参与到价值流改进过程中,发挥其主 动性和创造性。
建立激励机制
建立激励机制,对在价值流改进中做出贡献的员工给予奖励和表彰。
05
价值流程图的持续改进
定期审查与更新价值流程图
定期审查
价值流程图绘制完成后,应定期进行审 查,以确保其与实际生产过程保持一致 。
VS
更新价值流程图
随着生产过程的改进和变化,价值流程图 也应随之更新,以反映最新的生产状况。
持续改进的策略与方法
识别瓶颈
通过价值流程图,识别生产过程中的瓶颈,并制定相应的改进措 施。
非价值流
描述生产过程的原材料、组件、 信息和能源的来源。
描述生产过程中的浪费环节,如 等待、库存、搬运、重复作业等。
价值流程图的作用
识别生产过程中的浪费
提高生产效率
通过绘制价值流程图,企业可以清晰地看 到生产过程中的浪费环节,从而有针对性 地采取措施消除浪费。
价值流程图可以帮助企业优化生产流程, 减少不必要的环节和等待时间,提高生产 效率。
增强了企业的竞争力。
THANK YOU
服务流程梳理
利用价值流程图对服务流程进行全面梳理,包括客户需求、服务 提供、售后支持等环节。
服务效率提升
基于价值流程图的分析结果,优化服务提供方式,提高服务效率和 质量。
服务创新
通过价值流程图发现服务中的瓶颈和浪费,实施服务创新,如开发 新的服务项目、优化服务流程等。
价值和价值流程图
— 31 —
如何理解价值流图:
是:
让所有人看见整体情况 根据真实数据 改善的蓝图 持续改善的依据
不是:
流程图 根据工程标准或旧数
据 一年一次的大计划
— 32 —
什么是价值流图分析:
— 33 —
价值流图分析:先对运作过程中的现状进行分析,即对“当前状态图”进行分 析,从顾客一端开始,首先了解顾客的需求情况和节拍,然后研究运作流程中的每 一道工序,从下游追溯到上游,直至供应商。分析每个工序的增值和非增值活动, 包括准备、加工、库存、物料的转移方法等,记录对应的时间,了解分析物流信息 传递的路径和方法,然后根据分析情况来判别和确定出浪费所在及其原因,为消灭 浪费和持续改善提供目标。最后根据企业的实际情况,设计出新的价值流程,为未 来的运作指明方向。
奥通门封供应商
■ 流程信息 ■ 客户/供应商
OXOX
■ 均衡生产
■ 生产计划
单件工时(S):1680 设备数量:1 设备故障率(%):2 换模时间(min): 一次合格率:88% 搬运距离(m):1 转运批量(件):1 在制品(待加工):80 在制品(已加工):1 其它有用信息:
■ 数据表 ■ 操作工
价值简介:
下面的情况那些是增值的?
— 18 —
价值简介:
统计研究发现,企业生产活动中增值和非增值活动的比重如下:
浪不费增值
增值
必要非增值
— 19 —
增值 5%
不增值 35%
必要非增值 60%
目录
— 20 —
1、价值简介 2、价值流及价值流图简介 3、价值流图的绘制 4、价值流图分析
企业如何获取利润:
— 38 —
价值流图符号及意义:物流
价值流程图概述
价值流程图(Value Stream Mapping,简称VSM)价值流程图概述价值流程图(Value Stream Mapping)是()生产系统框架下的一种用来描述和的形象化工具。
它运用的工具和技术来帮助企业理解和精简生产。
价值流程图的目的是为了辨识和减少中的浪费。
浪费在这里被定义为不能够为提供增值的任何活动,并经常用于说明中所减少的“浪费”总量。
VSM可以作为管理人员、工程师、生产制造人员、流程规划人员、以及发现浪费、寻找浪费根源的起点。
从这点来说,VSM还是一项工具。
但是,VSM往往被用作工具、工具。
VSM通过形象化地描述生产过程中的物流和信息流,来达到上述工具目的。
从购进的那一刻起,VSM就开始工作了,它贯穿于生产制造的所有流程、步骤,直到终端产品离开。
对生产制造过程中的周期时间、当机时间、、原材料流动、信息流动等情况进行描摹和记录,有助于形象化当前流程的活动状态,并有利于对生产流程进行指导,朝向理想化方向发展。
VSM通常包括对“当前状态”和“未来状态”两个状态的描摹,从而作为精益制造战略的基础。
价值流程图(VSM)分析的是两个流程:第一个是(情报)流程,即从市场部接到订单或市场部预测客户的开始,到使之变成和的过程;第二个是流程,即从供应商供应原材料入库开始,随后出库制造、入库、产品出库,直至产品送达客户手中的过程。
此外,实物流程中还包括产品的检验、停放等环节。
企业在进行价值流程图(VSM)分析时,首先要挑选出典型的产品作为深入调查分析的对象,从而绘制出信息(情报)流程和实物流程的现状图,然后将现状图与信息(情报)和实物流程的理想状况图相比较,发现当前生产过程中存在的问题点,进而针对问题点提出改进措施。
价值流程图的历史1980年代,的与率先运用去除的方法来获取,他们的主要出发点是提高,而非提高。
之所以这么做,是因为他们认为生产效率的提高将有助于,从而能够暴露出系统中的深层的浪费问题和问题。
- 1、下载文档前请自行甄别文档内容的完整性,平台不提供额外的编辑、内容补充、找答案等附加服务。
- 2、"仅部分预览"的文档,不可在线预览部分如存在完整性等问题,可反馈申请退款(可完整预览的文档不适用该条件!)。
- 3、如文档侵犯您的权益,请联系客服反馈,我们会尽快为您处理(人工客服工作时间:9:00-18:30)。
Source: The Lean Institute
19
ACME 当前的流程图
Source: The Lean Institute
ACME 数据—续
所有的工序都会在下列的订单中发生并且每一个部件都流经所有的工序
1. 冲压
为其他产品制作零件
2. 点焊接工位 1
专注于该产品族
• • • • •
钢卷的200 吨冲压机 周期: 1 秒 转版时间: 1 小时 机器可靠性: 85% 观察到的库存:
– 在冲压前的5 天钢卷量 – 4,600 件左手托盘完成冲 压的半成品 – 2,400件右手托盘完成冲 压的半成品
Source: The Lean Institute
18
ACME 数据—续
5. 组装工位 2
专注于该产品族
6. 货运部
• • • • •
手动工序 1个操作员 周期: 40 秒 转版时间: 无 可靠性: 100% 仓库中观察到的成品库存:
– 2,700 件左手的托盘 – 1,440 件右手的托盘
• 从仓库中取出货品装箱并用 卡车发往客户
4
目的
• 通过开发一个系统来洞察全局避免被局部 的改善“驱动” • 创建一个精益生产的框架使得精益的概念 和技术能用于统一的的行为习惯中 • 提供实施精益价值流的一张蓝图
5
个体
对 系统的效率
高效的个体
高效的系统
Source: The Lean Institute
6
过程 – 总览
确定价值流所处 的水平 选择产品线
Source: The Lean Institute
• 接到客户 90/60/30 天的预计 订单量并输入MRP系统中 • 通过MRP发布 Acme 6 周的预 计量给 MSC (钢铁公司). • 可靠的钢卷量每周以传真的方 式告知 MSC 钢铁公司 • 收到客户的每天订单. • 基于客户订单生成一个MRP系统每周部门的需求量, 半成 品库存水平,成品库存水平, 预 期的报废和停机时间 • 发出每周的生产计划给各个部 门 • 发出每天的发货计划给货运部16
• 客户工厂按两个班生 产 • 用可回收的盒子包装, 每盒20个托盘,每个 卡板10个盒子. 客户 定制了很多盒子. • 每天用卡车发送货物 给客户 . Source: The Lean Institute
• 每月工作 20 天 • 生产部所有部门上两 个班 • 每个班 8 个小时,如 果有需要可以加班 • 每班有两次,每次10 分钟的休息时间. 在 休息时间手工线停线. 不付报酬的午餐.
价值流程图
简要介绍
1
议程
• • • • 简介 精益生产的好处 目的 过程
– – – – 总览 创建当前的流程图 改善机会 创建将来的流程
• 挑战 • 机会
2
简介
• 一个产品生产路径的形象 的表征 • 从原材料到成品所需的信 息流和物料流
3
精益生产的好处
• • • • • 缩短交货期 降低库存 劳动力的交叉培训 浪费变得更容易识别和消除 更好的满足客户需求的反应能力
• • • • •
手动工序 1个操作员 周期: 39 秒 转版时间: 10 分钟 可靠性: 100% 观察到的库存:
– 1,100 件左手的托盘 – 600 件右手的托盘
Source: The Lean Institute
17
ACME 数据—续
3. 点焊接Leabharlann 位 2专注于该产品族4. 组装工位 1
专注于该产品族
• • • • •
手动工序 1个操作员 周期: 46 秒 转版时间: 10 分钟 可靠性: 80% 观察到的库存:
– 1,650 件左手的托盘 – 850 件右手的托盘
• • • • •
手动工序 1个操作员 周期: 62 秒 转版时间: 无 可靠性: 100% 观察到的库存:
– 1,200 件左手的托盘 – 640 件右手的托盘
15
ACME 数据—续
生产过程 生产控制部
• 包括冲压金属部件,然 后焊接和组装. 零部件集 中后每天发往客户工厂. • 在生产左手和右手的托 盘产品转换时,冲压工 位需要 1小时的转版时间 和焊接工位 10 分钟的夹 具更换时间. • 钢卷由密歇根州钢铁公 司 (MSC) 供应,每周二 和周四发货到 Acme 工 厂.
产距时间 =
每班有效的工作时间 每班客户的需求量
12
精益学院的ACME 案例
• 客户给了两种产品的订单
– 左手驾驶盘 – 右手驾驶盘
• 我们从供应商那儿得到钢材 • 在钢材冲压后我们存入仓库 • 从冲压产品到分段运输,然后两个焊接工位(中间有 在制品库存) • 从焊接产品到分段运输,然后有两个组装工位(中间有 在制品库存) • 从组装产品到发货 (中间有在制品库存) • 产品发往客户
• • • • 流程水平 单一产品工厂 多产品工厂 跨公司的 • 相类似的组装步骤/设备 • 不一定要是畅销品系列
当前阶段的流程
确定改善
将来的流程
建立计划 实施 7
流程 – 当前阶段的流程图
• • • • 通常最多花 2 – 4 天 价值流的粗略的简单印象 系统的产距时间 系统的交货时间
8
创建当前阶段的流程图
• 整个的核心团队从头到尾把 流程走一遍,获取总体价值 流的粗略概念和主意
• 团队把总的流程划分为若干 个合乎逻辑的小区域来作流 程图
9
创建当前阶段的流程图—续
• 团队指派每个小片区域给 2-3 人的各小组来收集数 据 • 小组研究自己的区域并拿 到相关数据 • 核心团队组合到一起来完 成总的流程图,确定产距 (客户需求)时间,并确 定系统的供货期
Source: The Lean Institute
13
第1步: 画出基础流程图
• 在走过流程后, 画出一个很基础的流程图 • 把流程图细分为多个小片区,收集详细的数 据
Source: The Lean Institute
14
ACME 数据
客户需求 工作时间
• 每月18,400 件
– 12,400 左手的 – 6,000 右手的
10
流程图符号
FIFO
电子信息流 先进先出流 成品发货给客户
I
生产工序 手工信息流 “去看” 计划表 库存 工序
XOXO
操作员 外部资源 生产看板 负荷水平 次序拉动球
“改善亮区”
看板邮筒
推动
符号看板
超市
缓冲/安全库存
取货看板
取货
卡车货运
批看板
11
需求时间
• 客户需求率 • 精益生产系统的理想的比率