Ni-NTA superflow cartridge手册 中文版
印度斯坦流动控制系统用户手册说明书

INDUSTRIAL FLUID CONTROLSManufacturers of liquid level controls for overfill prevention.Liquid terminal operationsSpecifically designed Intrinsically safe Rugged Phase-Shift scale,up to 60"long.1/2"NPT connection.armor probe cable.open or shorted cable Tank Trucks,Marine Barges,Open and Close DomeSpillguard A-210Automatic High Level ShutdownOptional ground varification and tilt interlocksGRADUATED SCALESpillguard A-200Automatic High Level ShutdownOptional ground varification and tilt interlocksModel A-100self-contained Battery operatedalarm.Up to 2500Hour battery life,high intensity visual and Outalarm TMINDUSTRIAL FLUID CONTROLSCINCINNATI, OHIO 45246 ModelManufacturers of liquid levelprevention.automationSLIDING 3"1/2"OD SHAFT 316SS,1/4"GRADUATIONSGLAND 1/2"NPT5/8"OD TIPTEFLON1/4"SLIDING 3"1/2"OD SHAFT 316SS,1/4"GRADUATIONSGLAND 1/2"NPT5/8"OD TIPTEFLON1/4"A100-HT325or firm flash.If the tight is Again,finger prevent ring has bumped to Test unit the battery is ok.flashes red..1.Note:monitor.In the threshold off.flash red.FEATURES:MODELA-100CTotally self contained 3"D D SDESIGN SERVICESONTESTOFFOUTALARM6059SLIDING GLAND 1/2"NPT-WARNING-ALARM SELFCONTAINED use in loading tank cars,tank exposure,overloading.Suitable for open conductive fluids.HAS BEEN DESIGNED INANSI/UL913GUIDELINES FOR IS SUITABLE FOR USE IN A,B,C,AND D HAZARDOUS OR REPLACE BATTERY IN REPLACE WITH TYPE U9V,EQUIVALENT 9V RECTANGULAR ANY SUBSTITUTION OF IMPAIR INTRINSIC SAFETYFEATURES:MODELA-100 CSSTotally self contained 3"D D SDESIGN SERVICESONTESTOFFOUTALARM6059DESIGNED INGUIDELINES SUIITABLE FOR AND D BATTERY WITH 9V ANY COMPONENTS MAYIMPAIR HAS BEEN WITHANSI/UL913SAFETYAND IS GROUPS A,B,C,-WARNING-OR REPLACE LOCATION.REPLACE 1604,OR EQUIVALENT ALKALINE BATTERY .ALARM SELFCONTAINED use in loading tank cars,tank exposure,overloading.Suitable for closed SLIDING GLAND 316SS 1/2"NPTliquid flash.9Vrectangular Again,has to Test battery is light.1.red.MODEL A-100C/CSSFEATURES:1990Automated Design Services,Inc.Printed in U.S.A.ADS,the ADS design,and OUTALARM are trademarks of AutomatedDesign Services,Inc.U.S.patent no.5,065,139.All rights reserved.Totally self contained c 9/02SELF CONTAINED use in loading HCl into tank exposure,overloading.Suitable for closed 3"GLAND TEFLON OD SHAFT HAST C-276,LASER ENGR.MODEL A-100HMODEL A-100HCLliquid flash.9Vrectangular Again,prevent has bumped to Test battery is light.1.red.MODELA100PRSHy-Lodome loading SELFCONT AINEDpressurizing or unloading of.FEA TURES:T otally self contained3"5"2.5"4"A100PRS Hy-LoHand tight protective ring accidently bumped to Test the battery is ok.red.1.Note:monitor .In the threshold off.flash red.R1R2LOCATION OF CALIBRATIONPOTS,TOP VIEW5"3"5/8"OD TIPTEFLONPRESS. SENSING PORT1/2"OD SHAFT 316SS,1/4"GRADUATIONSSLIDING GLAND 1/2"NPTA-100 MONITORSELFCONTAINED use in loadingtank cars,tank overloading,overpressure.FEATURES:1990Automated Design Services,Inc.Printed in U.S.A.ADS,theADS design,and OUTALARM are trademarks ofAutomatedDesign Services,Inc.U.S.patent no.5,065,139.All rights reserved.MODELA-110Totally self contained c 1/4"INDUSTRIAL FLUID CONTROLSCINCINNATI, OHIO 45246 (513) 874-8499LOCATION OF CALIBRATION TRIM POTS,TOP VIEWThe electronic pressure switch can be calibrated either as a direct acting or reverse acting single point switch, or as a dual set-point switch that can alarm within or outside of a gap via the two calibration trim The calibration procedures are as follow:(Output goes from low to high at the set-point on increasing pressure)Trim pots are multi-turn (11 turns) with slip clutch at each end. When Setting to full CW or full CCW turn screw a minimum of 15 full turns in the appropriate direction.The trim pots are located in the top of the transducer electronic module labeled R-1R1R2INDUSTRIAL FLUID CONTROLSTESTOUTALARMAUTOMATED DESIGN SUIITABLE COMPONENTS APPARATUS HAS BEEN WITHANSI/UL913INTRINSIC SAFETYAND IS I,DIV 1GROUPS HAZARDOUSAREAS.-WARNING-CASE OR REPLACE HAZARDOUS LOCATION.REPLACE 522,1604,OR EQUIVALENT RECTANGULAR ALKALINE BATTERY SUBSTITUTION OFI N D U S T R I A L F L U I D C O N T R O L SIndustrial Fluid Controls Cincinnati, OH 45246 (513) 874-8499 A-210SPILLGUARD SYSTEM Manufacturers of liquid levelINDUSTRIAL FLUID CONTROLSINDUSTRIAL FLUID CONTROLSJOSEPH MODEL SENSORMODEL A200-PRB-316SS-XX(XX =PROBE LENGTH IN INCHES)INDUSTRIAL FLUID CONTROLSCINCINNATI, OHIO 45246INDUSTRIAL FLUID CONTROLS CINCINNATI, OHIO 45246STAINLESS STEEL ARMORED CABLE STANDARD LENGTHS15,20,25FT. LENGTHS UP TO100FEET AVALIABLEOUTER SHEATH WIRE TYPECABLE ENDS 304SS SPIRAL INTERLOCKING ARMOR3/C SILVER PLATED COPPER,22AWG STRANDED PTFE INSULATION,36AWG SILVER PLATED COPPER BRAID,EXTRUDED JACKETLATCHING XLR FEMALE GOLD PINS WITH CAPTIVE DUSTCAPSINDUSTRIAL FLUID CONTROLS 45246 (513) 874-8499OPTIONS ANDACCESSORIESNUTLOCKINGWASHERPACKINGFOLLOWERCOLLETNUTWASHERINDUSTRIAL FLUID CONTROLS 45246 (513) 874-8499NUT WASHERNUTLOCKINGCOLLETWASHERPACKINGFOLLOWERINDUSTRIAL CONTROLS INDUSTRIAL FLUID CONTROLS 45246 (513) 874-8499EXISTING WIRING TO PLCEXISTING WIRING TO LEVEL SENSOR CABLE RECEPTACLEEXISTING LEVEL MODULENEW PB REMOVE THE PROTECTIVE BACKING FROM THE DOUBLE SIDED TAPE ON THE TIMING MODULE (ORANGE)AND FIRMLY PRESS ONTO THE LEFT SIDE OF THELEVEL MODULE (GRAY)SO THAT THE TOP OF THE TIMING MODULE IS EVEN WITH THE TOP OF THE LEVEL MODULE.ATTACH TIMING MODULE-CAUTION -WHEN SCREWING THE RESET SWITCH INTO THE HOUSING TAKE CARE NOT TO TWIST THE SWITCH WIRES.BLK BLK#18,8"LONGJOSEPH MODEL A-200HIGH PRESSURE FITTING)HEAVY DUTY 300LB.FITTING,3/4"NPTSENSOR WITH STANDARD FITTING,½”NPTINDUSTRIAL FLUID CONTROLSCINCINNATI, OHIO 45246A-200SPILLGUARD SYSTEM Manufacturers of liquid level controls for overfill prevention.SPECIFICATIONS:FEATURES:ModelA-200high levelshutdown system for tank cars,tank trucks -Stainless steel armored cable,standard length 25ft.Other lengths available.Cable connectors are designed for repeated mating and meet IP-65environmental specs.--Tip sensitive proximity sensor.Works on all liquids with a dielectric constant >1.9Insertion length 4"-60"adjustable via 1/2"NPT packing gland.Longer lengths available.Wetted materials 316SS,Teflon.Other materials available.Sensor intrinsically safe for Class I,Div 1,Gr.A,B,C,&D hazardous areas Probe temperature range -40to +212Deg F.-----NEMA 4X enclosure with factory sealed switches and relays suitable for Class I,Div.2hazardous areas TMSpillguard in conjunction with supplied controller.-Fail safe design.Trips in the event of open or shorted cable conductors,or loss of power.barges,ships ....Prevent spills,personnel exposure,overloading.Suitable for open and closed dome loadingthe simple and economical solution.Single stage fail safe level control.Operator panel provides easy and friendly operation via heavy duty illuminated push button switches.NEMA 4X enclosure with hermetically sealed switches and relays suitable for Class I,Div 2Hazardous areas.Single point tip sensitive capacitance level probe,intrinsically safe for Class I,Div 1hazardous areas in conjunction with supplied controller.Adjustable probe insertion length via 1/2"NPT sliding fitting.Probe diameter 1/2"features a laser engraved graduated scale with 1/4"graduations.Rugged corrosion and solvent resistant cable protected by a stainless steel interlocking armor sheath with heavy duty latching connectors at each end.Fail safe design trips in the event of a open or shorted cable or loss of power.Powered output for single stage valve control plus outputs for external horn and strobe light,and contact outputs for pump control.Built in annunciator with silence/acknowledge via the stop button.Setup mode allows system setup and testing prior to loading.Optional ground detector interlock prevents system from being reset if the vessel in not properly bonded to earth.Probe max pressure 50psig standard fitting,300psig heavy duty fitting.Open/close lighted pushbuttons,long life LED lamps.---without purge.Optional ground interlock prevents system from being reset if vessel is not properly bonded to ground (resistance from vessel to ground is 10ohms or less.Green "Ground OK"light provided with this option.INDUSTRIAL FLUID CONTROLS CINCINNATI, OHIO 45246(513)874-8499JOSEPH SENSORMODEL A200-PRB-316SS-XX(XX =PROBE LENGTH IN INCHES)MODEL (MUST BE USED WITH GROUND VERIFICATION OPTION)HEAVY DUTY FITTING,3/4"NPTINDUSTRIAL FLUID CONTROLSCINCINNATI, OHIO 45246LEVEL/PRESSUREREV7/11/03I N D U S T R I A L F L U I D C O N T R O L S2001Automated Design Services,Inc.Printed in U.S.A.ADS,theADS design,and OUTALARM are trademarks ofAutomated Design Services,Inc.All rights reserved.c 0903-1LOCATING TABCAPACITANCE SENSOR TIPTANK TRUCK SWIVEL MOUNT1-1/4"NPT VENT CONNECTIONPRESSURE SWITCHA -300-S P -1000AB A TC H G U A RD S Y S TE ML O C A T I N G T A BC A P A C I T A N C E S E N S O R T I PT A N K T R U C K S W I V E L M O U N T1-1/4"N P T V E N T C O N N E C T I O NP R E S S U R E S W I T C HC O N N E C T O R H E A DL A S E R E N G R A V E D P R O B E R O DC O N T R O L L E RP R O B E -T O -C O N T R O L L E R C A B L EC A B L E I N T E R F A C E J U N C T I O N B O XP R E S S U R E S W I T C H C A B L E。
Invitrogen Platinum SuperFi II DNA Polymerase 用户手册

Steps
Action
Procedure details
1
Thaw reagents
Thaw, mix, and briefly centrifuge each component before use.
Add the following components to each PCR tube.
Note: Consider the volumes for all components listed in steps 2 and 3 to determine the correct amount of water required to reach your final reaction volume.
Cap each tube, mix, and then briefly centrifuge the contents.
-2-
Run PCR Steps
4
5
Action
Incubate reactions in a thermal cycler
Add gel loading buffer and analyze with gel electrophoresis
Optimization strategies and troubleshooting
Click here for guidelines to optimize your PCR experiment. Click here for guidelines to troubleshoot your PCR experiment.
Invitrogen™ Platinum™ SuperFi™ II DNA Polymerase
Print Options
Parker Hannifin NX系列恒温拓展阀说明书
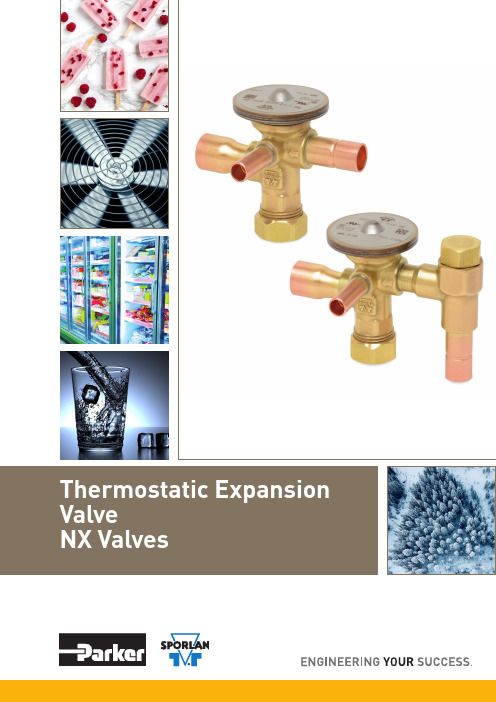
▲WARNING - USER RESPONSIBILITYFailure or improper selection or improper use of the products described herein or related items can cause death, personal injury and property damage.This document and other information from Parker Hannifin Corporation, its subsidiaries and authorized distributors provide product or system options for further investigation by users having technical expertise.The user, through its own analysis and testing, is solely responsible for making the final selection of the system and components and assuring that all performance, endurance, maintenance, safety and warning requirements of the application are met. The user must analyze all aspects of the application, follow applicable industry standards, and follow the information concerning the product in the current product catalog and in any other materials provided from Parker or its subsidiaries or authorized distributors.To the extent that Parker or its subsidiaries or authorized distributors provide component or system options based upon data or specifications provided by the user, the user is responsible for determining that such data and specifications are suitable and sufficient for all applications and reasonably foreseeable uses of the components or systems.For safety information see the Safety Guide at /safetyOFFER OF SALEPlease, contact your Paker representation for a detailed "Offer of Sale"FOR USE ON REFRIGERATION and/or AIR CONDITIONING SYSTEMS ONLYType NX Valves THERMOSTATIC EXPANSION VALVEType NXEType SNXE Sporlan built the Type NX valve with a stainless steel capillary tube laser welded to the sensing bulb and element housing to withstand the repeated bending during installation and improve endurance to vibrations while in service. The forged brass NX valve body is available with a straight-through flow configuration and ODF (sweat) copper connections. The valve can be supplied with either an internal or external equalizer and features a field adjustable superheat stem. Valves with fittings in metric sizes are available upon special request. Sporlan constructed the NX valve with a single, balance-ported pushrod which is specifically designed to help flush out any solid debris build-up. The bleed port feature allows the system refrigerant to bypass the pin and port. System designers can utilize this feature to alter system p erformance f or a v ariety o f r easons. B leed port options are available upon special request. SpecificationsThe Type NX valves offer a wide range of type W thermostatic charges with or without the MOP feature. You can use the thermostatic charges with the MOP (maximum operating pressure) feature to help protect the compressor from overloading at startup or under high load conditions. S ee the MOP temperature in the table below.The small and compact design of S porlan’s Type NX Thermostatic Expansion Valves makes this product ideal for foodservice and food retail applications such as display cases, ice machines, frozen drink dispensers and commercial kitchen refrigerators and freezers. The Type NX valves feature a laser-welded stainless steel element, capillary tube, and sensing bulb assembly optimized for reliability and long life. The single pushrod balanced port design ensures precise pin and port alignment, enabling the valve to maintain superior superheat control at all load conditions. Features and Benefits• Long-lasting and durable stainless steeldiaphragm and weld design• Single pushrod balanced port construction• Suitable for all common refrigerants includingR-290• Internal or external equalizer• Easily adjustable superheat setting• High strength silver soldered joints with solid copper connections.The design ensures enabling the valve to main-tain a superior superheat control from 15% to 100% load conditions therefore fully compat-ible to work with inverter driven compressors.MOP Temperature TableS tandard static superheat settings vary based on the system refrigerant selected, but the valves are set to approximately 4K static superheat based on the newer refrigerants such as R448A, etc. S pecial settings are available upon special request. The seal cap utilizes a mechanical knife-edge seal. The torque required for proper sealing is 10,8 to 14,9 Nm. S porlan offers 2 optional inlet strainers for use with NX valves; an insert strainer and an integral strainer. The insert type strainer is placed into the inlet fitting prior to brazing and can only be serviced by disconnecting the liquid line.Valve ModelsNXInternallyEqualizedNXEExternallyEqualizedValves, its item number completely defines thetype NX valve. The standard NX item number has 7 positions; however, item numbers can be up to 14 positions in length. Positions 8-14 are reserved for special OEM configurations.Refer to the following example of a standard NX item number and the position descriptions when ordering.Nomenclature and Item Numbering SystemLike other Sporlan Thermostatic Expansion Valves, the Type NX valves follow the nomenclature example and ordering instructions below.Item NumberPosition DescriptionsItem Number and PositionsPackagingAll valves are packaged in clear plastic bags for protection.Standard NX valves are individually boxed with a bulb strap kit and are packed 24 pieces per case. Egg crate style production packaging is available upon special request and valves come packed 36 pieces per case.AccessoriesIdentification and Markings Several valve identifications are laser marked onthe element, as shown. The 5 digit date code indicates the day and year. The first 3 digits repre-sent the day of the year. The last 2 digits are the year. The PTS Number is a Parker Sporlan serial number. Additional markings are on the forged brass body, including a flow direction arrow and the Sporlan trademark.DescriptionRefrigerantCompatibility Parker SporlanItem NumberDate CodePTS Number2D DataMatrix ElementThermostatic expansion valve capacity ratings are based on vapor free 38°C (100°F) liquid refrigerant entering the expansion valve; a maximum open-ing superheat of 7K (4°F); and a standard fac-tory air test superheat setting. A discussion of the relationship between valve capacity and super-heat setting (along with other important applica-tion information) can be found in Bulletin 10-9. The valves are tested in accordance with ANSI/ ASHRAE 17. The ratings in the capacity tables are in accordance with ANSI/AHRI Standard 750. It is possible to correct for both liquid temperature and pressure drop using the factors in the tables following the capacity tables. The liquid temperature correction factors are refrigerant dependent, and tables are pro-vided for each refrigerant. The pressure drop correc-tion factor is affected by the valve and is indepen-dent of the refrigerant. The correction calculation is shown below, followed by an example calculation.TEV Capacity = TEV Rating x CF Liquid Temperature x CF Pressure DropExample Calculation: The actual capacity of a Type NX valve with a C38 capacity code on R448A at 20°F evaporator temperature, 100 psi pressure drop across the TEV, and 90°F liquid temperature entering the TEV is:Actual Capacity = 2.07 (from rating chart) x 1.08 (CF liquid temperature) x 0.89 (CF pressure drop) = 1.99 tonskW ■ bar ■ °CkW ■ bar ■ °CkW ■ bar ■ °CCapacity Ratings and SelectionLiquid Temperature kW ■ bar ■ °CDimensions - Inches (mm)Type NX(E)Front ViewTop ViewExternal 1/4” ODF Equalizer FittingNotesParker Hannifin RACE Instrumentation GroupRefrigeration and Air Conditioning Europe Via Enrico Fermi,520060 Gessate - Milano - ItalyTel. +39 (0) 2 95125.1 - /raceEU.RE1.C.9T2.NX.EN.1.2021.04© 2021 Parker Hannifin Corporation. All rights reserved.Parker WorldwideUnited Arab Emirates Middle EastSarkis OHANNESSIAN Tel +961 3334622***********************Germany, Austria and German speaking part of Switzerland Francesco GALANTE Tel +49 (0)175 5756 032****************************Spain and Portugal Alberto PEÑATel +34 609 153 154***********************France, Belgium,French speaking part of Switzerland Goska WARNECKTel + 33 (0)6 73 89 36 08*******************Italy, Greece, Malta, Cyprus Italian speaking part of Switzerland Andrea BRAGATel +39 334 6944386 *****************Baltic Countries,Eastern and Central Europe, AfricaEliane EMERIT-BONNOT Tel +33 (0)6 73 89 36 01 ******************Turkey************************UK andNorthern Europe Kenny ADAMSON Tel +44 77853 71229*******************Customer Service: Parker Hannifin Ltd Instrumentation Group Refrigeration andAir Conditioning Europe Manvers House Office 21Pioneer CloseWath Upon Dearne Rotherham S63 7JZ United KingdomTel +44 (0) 1709 774600 Fax +44 (0) 1709 774601******************************/raceYour local authorized Parker distributor。
尼德曼 Wallcart 墙上过滤器说明书

Low ceiling height? Turn Wallcart around and choose a 4-metre horizontal Nederman Original arm. The fan can be upside-down.
Complete units
Wallcart, a complete filter unit placed on the wall. A package consists of: • Fan N24 • Arm Original 2m alt. Arm 4mH • Light package • Control box incl. transformer and
Mount Wallcart on walls in combination with Nederman’s range of extractor arms/fans.
Supplement your existing plant
Wallcart can be easily attached to existing extractor systems regardless of manufacturer.
The majority of Nederman’s products are manufactured within SS-EN ISO 9001 and ISO 14001-certified Quality- and Environmental system. For more detailed information please contact us.
Net weight: Basic filter 22,6 kg, Gas/Micro filter 30,4 kg Recyclability: 68%, for Basic filter
迈尼-克路特移动测试设备编程手册说明书
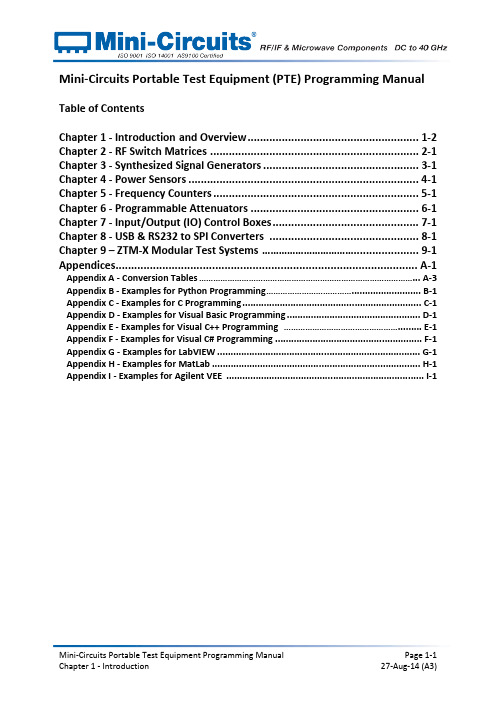
Mini-Circuits Portable Test Equipment (PTE) Programming Manual Table of ContentsChapter 1 - Introduction and Overview ....................................................... 1-2 Chapter 2 - RF Switch Matrices ................................................................... 2-1 Chapter 3 - Synthesized Signal Generators .................................................. 3-1 Chapter 4 - Power Sensors .......................................................................... 4-1 Chapter 5 - Frequency Counters .................................................................. 5-1 Chapter 6 - Programmable Attenuators ...................................................... 6-1 Chapter 7 - Input/Output (IO) Control Boxes ............................................... 7-1 Chapter 8 - USB & RS232 to SPI Converters ................................................ 8-1 Chapter 9 – ZTM-X Modular Test Systems ……………………………..................... 9-1 Appendices ................................................................................................. A-1 Appendix A - Conversion Tables ………………………………………………………………………………... A-3 Appendix B - Examples for Python Programming ……………………………….......................... B-1 Appendix C - Examples for C Programming ................................................................... C-1 Appendix D - Examples for Visual Basic Programming .................................................. D-1 Appendix E - Examples for Visual C++ Programming …………………………………………......... E-1 Appendix F - Examples for Visual C# Programming ....................................................... F-1 Appendix G - Examples for LabVIEW ............................................................................ G-1 Appendix H - Examples for MatLab .............................................................................. H-1 Appendix I - Examples for Agilent VEE .......................................................................... I-1Chapter 1 -Introduction and OverviewChapter 1 - Introduction and Overview ....................................................... 1-2 1.1 - Overview ............................................................................................................ 1-3 1.2 - Operating in a Windows Environment ................................................................ 1-41.2.1 - The DLL (Dynamic Link Library) Concept .......................................................................... 1-41.2.2 - Summary of DLL Files for the Mini-Circuits PTE Range .................................................... 1-51.2.3 - ActiveX COM Object ......................................................................................................... 1-61.2.4 - Class Library .............................................................................................. 1-8 1.3 - Operating in a Linux Environment ....................................................................... 1-9 1.4 - Notices ............................................................................................................. 1-101.4.1 - Registered Trademarks ................................................................................................... 1-101.4.2 - Copyright Information .................................................................................................... 1-101.1 -OverviewThis Programming Manual is intended for customers wishing to create their own interface for Mini-Circuits' USB controlled Portable Test Equipment (PTE). For instructions on using thesupplied GUI program, or connecting the PTE hardware, please see the User Guide of therelevant model.Mini-Circuits offers support over a variety of operating systems, programming environments and third party applications.Support for Windows® operating systems is provided through the Microsoft®.NET® andActiveX® frameworks to allow the user to develop customized control applications. Support for Linux® operating systems is accomplished using the standard libhid and libusb libraries.Mini-Circuits has experience with a wide variety of environments including (but not limitedto):∙Visual Basic®, Visual C#®, Visual C++®∙Delphi®∙Borland C++®∙CVI®∙LabVIEW®∙MATLAB®∙Python®∙Agilent VEE®The Mini-Circuits PTE CD package includes a GUI program installation, DLL Objects (32/64bit), Linux support, project examples for third party software, and detailed user manuals.The latest CD version is available for download at:/support/software_download.htmlFor details on individual models, application notes, GUI installation instructions and userguides please see:/products/PortableTestEquipment.shtmlFiles made available for download from the Mini-Circuits website are subject to Mini-Circuits’terms of use which are available on the website.1.2 -Operating in a Windows Environment1.2.1 -The DLL (Dynamic Link Library) ConceptThe Dynamic Link Library concept is Microsoft's implementation of the shared libraryconcept in the Windows environment.DLLs provide a mechanism for shared code and data, intended to allow a developer todistribute applications without requiring code to be re-linked or recompiled.Mini-Circuits' CD package provides DLL Objects designed to allow your own softwareapplication to interface with the functions of Mini-Circuits' PTE, see Figure 1.Figure 1: DLL Interface ConceptMini-Circuits’ CD package provides two DLL files, the choice of which file to use is dictated by the user’s operating system:1.ActiveX com objectDesigned to be used in any programming environment that supports third partyActiveX COM (Component Object Model) compliant applications.The ActiveX file should be registered using RegSvr32 (see following sections fordetails). Class LibraryDesigned to be a logical unit of functionality that runs under the control of the system.1.2.2 -Summary of DLL Files for the Mini-Circuits PTE RangeActiveX Com objects and class libraries can be downloaded from the Mini-Circuits website at:/support/software_download.html1.2.3 -ActiveX COM ObjectActiveX COM object DLL files are designed to be used with both 32 bit and 64 bit Windowsoperating systems. A 32 bit programming environment that is compatible with ActiveX isrequired. To develop 64 bit applications, the Class library should be usedinstead.Supported Programming EnvironmentsMini-Circuits’ PTE devices have been tested in the following programming environments.This is not an exhaustive list and the DLL file is designed to operate in most environmentsthat support ActiveX functionality. Please contact Mini-Circuits for support.∙Visual Studio® 6 (Visual C++ and Visual Basic)∙LabVIEW 8.0 or newer∙MATLAB 7 or newer∙Delphi∙Borland C++∙Agilent VEE∙PythonInstallation1.Copy the DLL file to the correct directory:a.For 32 bit Windows operating systems this is C:\WINDOWS\System32b.For 64 bit Windows operating systems this is C:\WINDOWS\SysWOW642.Open the Command Prompt:a.For Windows XP® (see Fig 1.1.2a):i.Select “All Programs” and then “Accessories” from the Start Menuii.Click on “Command Prompt” to openb.For later versions of the Windows operating system you will need to haveAdministrator privileges in order to run the Command Prompt in “Elevated”mode (see Fig 1.1.2b for Windows 7 example and Fig 1.1.2c for Windows 8):i.Open the Start Menu/Start Screen and t ype “Command Prompt”ii.Right-click on the shortcut for the Command Promptiii.S elect “Run as Administrator”iv.You may be prompted to enter the log in details for an Administratoraccount if the current user does not have Administrator privileges on thelocal PCe regsvr32 to register the DLL:a.For 32 bit Windows operating systems type (see Fig 1.1.2d):\WINDOWS\System32\Regsvr32 \WINDOWS\System32\mcl_pm.dll(where mcl_pm.dll is the name of the relevant DLL)b.For 64 bit Windows operating systems type (see Fig 1.1.2e):\WINDOWS\SysWOW64\Regsvr32 \WINDOWS\SysWOW64\mcl_pm.dll(where mcl_pm.dll is the name of the relevant DLL)4.Hit enter to confirm and a message box will appear to advise of successful registration.Fig 1.1.2a: Opening the Command Prompt in Windows XP Fig 1.1.2b: Opening the Command Prompt in Windows 7Fig 1.1.2c: Opening the Command Prompt in Windows 8Fig 1.1.2d: Registering the DLL in a 32 bit environmentFig 1.1.2e: Registering the DLL in a 64 bit environment1.2.4 Class Library class libraries are designed to be used with both 32 bit and 64 bit Windowsoperating systems. To develop 64 bit applications the user must have both a 64 bit operating system and 64 bit programming environment. However, the class library isalso compatible with 32 bit programming environments.Supported Programming EnvironmentsMini-Circuits’ PTE devices have been tested in the following programming environments.This is not an exhaustive list and the DLL file is designed to operate in most environmentsthat support functionality. Please contact Mini-Circuits for support.∙National Instruments CVI∙ (Visual C++, Visual , Visual C# 2003 or newer)∙LabVIEW 2009 or newer∙MATLAB 2008 or newer∙Delphi∙Borland C++Installation1.Copy the DLL file to the correct directorya.For 32 bit Windows operating systems this is C:\WINDOWS\System32b.For 64 bit Windows operating systems this is C:\WINDOWS\SysWOW642.No registration is required1.3 -Operating in a Linux EnvironmentTo open a connection to Mini-Circuits PTE devices, the Vendor ID and Product ID arerequired:∙Mini-Circuits Vendor ID: 0x20CE∙Mini-Circuits Product IDs:▪Switch Matrices: 0x22▪Signal Generators: 0x12▪Power Meters: 0x11▪Frequency Counters: 0x10▪Digital Step Attenuators: 0x23▪Input/Output Control Boxes: 0x21▪USB/RS232/SPI Converters: 0x25▪ZTM-X Modular Test Systems: 0x22Communication with each PTE device is carried out by way of USB Interrupt. The transmitted and received buffer sizes are 64 Bytes each:∙Transmit Array = [Byte 0][Byte1][Byte2]…[Byte 63]∙Returned Array = [Byte 0][Byte1][Byte2]…[Byte 63]In most cases, the full 64 byte buffer si ze is not needed so any unused bytes become “don’t care” bytes; they can take on any value without affecting the operation of the PTE.1.4 -Notices1.4.1 -Registered TrademarksMicrosoft, Windows, Windows XP, Windows 7, ActiveX, , Visual Basic, Visual C#, and Visual C++ are registered trademarks of Microsoft Corporation.Linux is a registered trademark of Linus Torvalds.LabVIEW is a registered trademark of National Instruments Corporation.Delphi is a registered trademark of Codegear LLC.MATLAB is a registered trademark of MathWorks, Inc.Agilent VEE is a registered trademark of Agilent.The above trademarks and all other trademarks cited within the Programming Manual are the property of their respective owners.Neither Mini-Circuits nor the Mini-Circuits Portable Test Equipment are affiliated with orendorsed or sponsored by the owners of the above referenced trademarks set forth in this manual.Mini-Circuits and the Mini-Circuits logo are registered trademarks of Scientific Components Corporation.1.4.2 -Copyright InformationThis Programming Manual is owned by Mini-Circuits and is protected by copyright,trademark and other intellectual property laws.© Copyright 2013 Scientific Components Corporation.。
铭 mining 移动连续带运送器槽对ipedia抬升器操作 mantenance 手册说明书

USA 1-323-310-5474**********************************************************OPERATIONS & MAINTENANCE MANUAL PORTABLE HYDRAULIC TROUGH CONVEYOR BELT LIFTERTABLE OF CONTENTS1.GENERAL INFORMATION (4)1.1General Safety Precautions (4)2. KEY ITEMS OF IMPORTANCE (5)2.1 Summarised Essentials Pocket Slip (5)2.2Summarised Essentials List (6)3.DESIGN INFORMATION (7)3.1Portable Belt Lifter- Fixed Beam Lifter (7)3.2Hydraulic Power Pack (8)4.GENERAL LIFTER OPERATIONAL PROCEDURES (9)4.1Pre-start Equipment Inspection (9)4.1.1Telescope Beams (9)4.1.2Hydraulic Hose (10)4.1.3Hydraulic Pump (11)4.1.4Lifting Beams (11)4.1.5Converter Pack (If using alternative pumps) (13)5.FIXED BEAM LIFTER- FIELD SET-UP AND OPERATION (15)5.1Fixed Beam Belt Lifter- Detailed Set-up Instructions (17)6.ADVANCED COMPONENTRY SET-UP AND OPERATION (18)6.1 Hydraulic Pump – Safety Features (18)6.2 Hydraulic Pump – Operation (19)6.3 Techmine Converter Pack (19)7.EQUIPMENT STORAGE AND AFTERCARE (21)7.1Disassembly and Demobilization (21)7.2Aftercare, Inspection and Storage (22)7.3Equipment Clean-down Procedure (23)8.MAINTENANCE (24)8.1Bleeding Air from System (24)8.2Rigging and Lifting Componentry- Quarterly Inspection (25)8.3Hydraulic Telescope Contamination- Cleaning Procedure (25)8.4Maintenance Records and Summary (26)8.5Additional Maintenance, Repairs and Modifications of Components (26)9.WARRANTY (27)9.1Ongoing responsibility (27)9.2Warranty (27)10.SPARE PARTS (28)10.1Recommended Spare Parts Table (28)11.TROUBLESHOOTING GUIDE (29)12.MAINTENANCE REGIME (31)12.1Portable Hydraulic Belt Lifter (31)12.2Hydraulic Pump (32)PONENT IDENTIFICATION GENERAL DRAWINGS (33)13.1Specially Profiled Bent Beam Lifter (33)1. GENERAL INFORMATION1.1 General Safety PrecautionsPlease read this Operations and Maintenance Manual prior to installing, operating and maintaining your Techmine Hydraulic Belt Lifter. This document should be included as a reference in the work permit, safe work procedure or equivalent documentation used at your facilities.i. The Portable Hydraulic Belt Lifter is only to be operated with a Techmine Hydraulic PowerPack. The Techmine Power Pack has been carefully designed to ensure equipmentoverload is prevented and to automatically synchronize the hydraulic cylinders, ensuringan even lift by compensating for uneven loading.ii. The Portable Belt Lifter is intended for use on a STATIONARY and DE-ENERGISED belt conveyor. Prior to installing and operating the Lifter, please ensure that the conveyordrives are ISOLATED and that the belt and/or brakes are CLAMPED/LOCKED to preventmovement.iii. Visually inspect all equipment prior to use. If damage is evident, do not use the lifter and tag “Out of Service”. Never attempt to repair the lifter yourself, always contact Techmineor approved agent for repair, replacement or assistance.iv. All lifting equipment should be thoroughly inspected on a quarterly basis by a qualified and competent rigger. It is recommended to tag the inspected and approved equipmentusing a colour coded tagging system or similar.v. The belt lifter is rated to safely lift a load of certain tonnage. The rated capacity is indicated on the products identification plates and also clearly marked as a rated Working Load Limit(WLL).vi. Never adjust the pressure relief settings on the Hydraulic Power Pack. Exceeding the specified maximum pressure as indicated on the products identification plates may causeinjury and/or equipment damage.vii. Ensure all components are stored, assembled, tightened and operated as specified within this document.2. KEY ITEMS OF IMPORTANCE2.1 Summarised Essentials Pocket SlipThis pocket slip contains a dot point summary of some of the most important operationalrequirements and helpful tips. The card can be printed out and used as a guide when operating the lifter. This card is to be used as a prompt tool only and does not replace the need to read and understand the Operations and Maintenance Manual.2.2 Summarised Essentials ListThis list below is identical to the wording on the printable pocket slip in section 2.1.∙Do not use the lifting equipment if any part of the equipment appears damaged.∙Only operate equipment if competent and authorised to do so.∙Conveyor system must be isolated with belt restrained.∙Mounting areas on the conveyor stringers must be relatively clean with large debris wiped away prior to set-up.∙Only use the Techmine hydraulic pump to operate the lifter.∙Lifter hydraulic telescopes sections must be assembled tightly together by hand.∙Hydraulic telescopes must be positioned with the retaining lip toe-in on the stringers (Allowable gap is 0-10mm between the lip and stringer).∙Flanged M24 nuts must be done up hand tight plus a ¼ turn extra using a mechanical aid.∙Adjustable rigging assemblies or solid lifting beams should be set in position as centrally under the belt as possible.∙Rigging chain assemblies may be used when secured no more than 2 links higher or lower to the opposing side.∙Monitor system pressure during operation and never exceed the equipment’s maximum rated working load limit.∙If an uneven lift is experienced, the system will synchronise at ¼ creep speed when holding the raise button down.∙//OR//∙Alternately, operating the power pack repeatedly using 1 second on / 4 seconds off will fully extend the lagging cylinder.∙Always install, secure and lower the lifter onto the locking pins before commencing belt maintenance.3. DESIGN INFORMATION3.1 Portable Belt Lifter- Fixed Beam LifterThe typical features for a standard 1T,1.5T and 2T belt lifting system for an 1800mm conveyor are listed below;3.2 Hydraulic Power PackThe typical features for a standard 1T, 1.5T and 2T hydraulic pump are listed below;4. GENERAL LIFTER OPERATIONAL PROCEDURESThe following section contains the methodology on the general lifter set-up in a step by step format referencing photographs.4.1 Pre-start Equipment InspectionBefore heading out to commence any maintenance activities using the belt lifting equipment. It is recommended to check that all equipment is in place, clean and tagged with the correct quarterly equipment colour identification tags. (If this system is used at your site)4.1.1 Telescope BeamsI. Check typical equipment list to ensure all equipment is present.Typical Equipment List:I. 2 x Hydraulic Telescopic LegsII. 2 x Return Belt Lifting Chain AssembliesIII. 2 x Locking PinsIV. 2 x M24 Flanged Nuts4.1.2 Hydraulic HoseI. Inspect hydraulic hoses for leaks.II. Check overall condition of hose.III. Check hydraulic hose connectors for cleanliness. Ensure that hose connections are clean before connecting them to the hydraulic pump. See picture below.4.1.3 Hydraulic PumpI. Check oil level in hydraulic pump using dipstick. If extra oil is required, top up with HYD 32.Maximum capacity of tank is 2L.II. Ensure battery pack is fully charged by connecting charger into charging point. Charger should show green when battery pack is fully charged.III. Ensure hydraulic connectors are clean before attaching hydraulic hoses.4.1.4 Lifting BeamsI. Visually inspect beams for any structural defects and ensure overall condition is satisfactory. II.Check for name plates. Name plates are attached to the sides of the beams. See picture above for location.Location of name platesIII. Typical name plate should show following information. See picture below for details.4.1.5 Converter Pack (If using alternative pumps)Techmine equipment can be used with alternative pumps. However, alternative pumps must be used in conjunction with Techmine Converter Pack. The converter pack must be detuned to a pressure that is suitable for the certified lifting equipment.I. Ensure Techmine name tag is present. The presence of the name tag ensures that theequipment has been detuned. If no name tag is present, do not use it with Techmine Converter Pack. See above picture for location of name tag.Techmine Name TagII. Typical name tag should show following information. See picture below for more details.III. Inspect hydraulic hoses for leaks.IV. Check overall condition of hose.V. Check hydraulic hose connectors for cleanliness. Ensure that hose connections are clean before connecting them to the hydraulic pump. See picture below.5. FIXED BEAM LIFTER- FIELD SET-UP AND OPERATIONThe following photos details the set-up of the profiled beam lifter onto at typical 1800mm wide conveyor. It is recommended for two personnel to assemble the lifter during use.Wipe down stringer.Stand up left and right telescope.Pass profile beam under conveyor.Lift beam onto telescope using handles.Position beams as centrally as possible.Install and tighten M24 securing nuts.The following photos detail the lifting and securing procedure when raising the belt using the fixed beam lifter.Connect hydraulic hoses. Ensure connections areclean before connecting.Attach hoses to hydraulic pump. Ensure connections are clean before connecting.Use pendant to operate lifter.Slide in locking pin.Lower lifter onto locking pins.Hydraulic pressure gauge on pump should read0. Lifter is now secure for safe roller removal.5.1 Fixed Beam Belt Lifter- Detailed Set-up InstructionsThe following section shows in detail how to assemble some of the more complicated componentry.Lift and pass the specially profiled beam using the purpose-built grab handles.Note: If needed, a tag line can be secured to these handles to make passing the beam under the conveyor belt easier.Secure the profiled beams with the flanged M24 nuts.Note: Nuts must be done up hand tight plus 1/8 - 1/4 turn extra using a mechanical aid.6. ADVANCED COMPONENTRY SET-UP AND OPERATION6.1 Hydraulic Pump – Safety FeaturesThe hydraulic power pack has the following safety features included in the equipment design.The battery charger has thermistor protection to prevent a hot battery receivingcharge. This feature is in addition to the battery’s inbuilt protection circuit module.The hydraulic pressure gauge indicates the lifted weight in tonnes.6.2 Hydraulic Pump – OperationSee Techmine Hydraulic Pump Instruction Manual for more details.6.3 Techmine Converter PackHydraulic hose to pumpHydraulic hoses to cylindersHydraulicpressure gaugeInstructions on how to connect pumps to the Techmine Converter Pack are detailed below in a step-by-step format referencing photographs.Ensure Techmine name tag is present. If name tag is not present, do not use it with TechmineConverter Pack.Converter Pack comes with 3 connection points. Connect hose on right of converter (labelled above) to pump. Ensure hose connections areclean before attaching them to pump.Connect bottom 2 hoses to each of the hydraulic cylinders. Ensure hose connections are cleanbefore attaching them to the cylinders. Completed setup should look like picture above.While operating pump, ensure hydraulic pressure does not exceed the safe working limit of liftinggear.7. EQUIPMENT STORAGE AND AFTERCARE7.1 Disassembly and DemobilizationAt the end of any maintenance job, the lifter equipment should be disassembled and placed back into its protective carry case, for transport back to the workshop or stores for an aftercare inspection and storage, until the next time the equipment is required for use.7.2 Aftercare, Inspection and StorageThe following tasks are recommended as part of the aftercare inspection of the equipment after use around site.∙Visually inspect the flexible hydraulic hoses for cuts or exposed, damaged wire braiding whilst coiling all hoses neatly and securely around the hydraulic power pack hose stays.Protective end caps should be in place. Ensure connectors are clean before attaching end caps.∙Visually inspect power pack for signs of abnormal hydraulic oil leakage. Pay attention to all hoses and fitting comings from the hydraulic pump as well as directly under these parts,i.e. reservoir fittings, flow divider manifold including pressure gauge and hydraulic hoseconnections. It is normal for the quick release hydraulic coupling to leak a few drips of oil onto the cradle. However, if parts of the cradle appear to be coated or smeared with oil,a leak test may be required.∙If needed, wipe excess dust off the power pack cradle. If required, the entire power pack cradle can be washed down using soapy water at residential tap pressure. (Do not use high pressure plant water or pressure cleaners to wash down the equipment) ∙Visually inspect the hydraulic cylinder telescope assemblies for signs of abnormal hydraulic oil leakage. Pay attention to fittings and quick connect couplings at the base of the cylinders. It is normal for the quick release hydraulic coupling to leak a few drips of oil when released. However, if feet or telescope assemblies appear to be coated or smeared with oil, a leak test may be required.∙If needed, wipe excess dust off the belt lifter parts. If required, all parts can be washed down using soapy water at residential tap pressure. (Do not use industrial solvents, thinners, high pressure plant water or pressure cleaners to wash down the equipment.) ∙Visually inspect the hydraulic cylinder outer telescopes piping. Minor damage such as paint chipping with an area no larger than size of a 10-cent piece is acceptable if the exposed aluminium is not cracked, feels dented or exposed at the weld area on a lifting point. Unlimited superficial scratches to the painted surfaces are acceptable if the parent metal has not been damaged or the scratches are on the weld area of a lifting point. If a scratch damages the parent metal for a length longer than 50mm or is more than 1mm deep further analysis is required. If any items of concern are found, tag the equipment out of service for further inspection. Refer to the equipment maintenance section for further information or contact the equipment supplier if required.If the equipment passes the above post use inspection, the equipment can be placed into its storage casing and stored until required.7.3 Equipment Clean-down ProcedureAfter use the equipment generally only ever requires and brush down or gentle wash to remove dirt and some hydraulic fluid residue from the parts. In some occasions such as inclement weather, abnormally dirty work area or high use, the equipment may become overly dirty. Some problems may include;∙Dirt and/or water ingress into the hydraulic power pack battery enclosure.∙Dirt and/or water ingress into the hydraulic pump 24V DC motor∙Dirt and/or water ingress into hydraulic telescopes under the bushes and internal to the outer cover.Note: If any of the above problems are experience during use or picked-up in the aftercare inspections, please refer to the maintenance section of the manual.8. MAINTENANCEIt is essential that a regular maintenance and inspection program be implemented for all lifting equipment. Such a program will result in more reliable operation, longer equipment life and ensure the equipment operates safely during every maintenance activity. Equipment that is properly maintained will operate dependably, providing the longest possible duration in trouble free service.The maintenance recommended in this document is presented as a guide and should be considered as a minimum requirement. However, the maintenance of the equipment should be modified and/or added to in the light of experience with the plant involved and the changing operating conditions.8.1 Bleeding Air from SystemAir within the hydraulic system is the cause of numerous problems with the lifter operation. Air ingress must be rectified by bleeding the air from the system at the soonest opportunity. The effects of air ingress on the systems performance can be viewed in Section 11- Troubleshooting.With both the cylinder telescope connected to the hydraulic power pack, cycle the cylinders 3 times up and down to remove any air trapped internally. As the cylinders retract, any fugitive air venting from the system will cause an audible gurgling noise within the oil reservoir. If air can still be heard venting on the 3rd. cycle, keep cycling the cylinders until no more audible air is present in the system. If air still can be heard on the 5th cycle, leave the hydraulic pump still for30 minutes allowing any emulsion in the oil reservoir to dissipate. After the rest period, thesystem should only take a maximum of 3 cycles to complete the bleeding operation.8.2 Rigging and Lifting Componentry- Quarterly InspectionThoroughly inspect all lifting equipment on a quarterly basis using a qualified and competent rigger. It is recommended to tag the inspected and approved equipment using a colour coded tagging system or similar.8.3 Hydraulic Telescope Contamination- Cleaning ProcedureIf excessive dirt, oily scum or other foreign matter has entered the void between the hydraulic cylinder and outer telescope, and is affecting the lifters raise and retraction performance, the following steps may be required to remove the contamination;∙Both telescope assemblies must be cleaned, even if only one of the hydraulic telescopes is suffering from contamination.∙Connect both cylinders to the hydraulic pump and fully extend cylinders.∙Wipe dirt or contaminants off the cylinder tube.∙Wipe dirt or contaminants off the painted outer telescope tubes.If required, the cylinder telescope and tube can be washed down externally and internally using warm soapy water at residential tap pressure.∙Retract the cylinders.∙Fill the telescope/cylinder cavity with soapy water through the locking pin holes. Shake the cylinder telescope assembly for 30 seconds allowing the warm soapy water time to react with any residual dirt and/or oil trapped on the inside surfaces of the telescope assembly.∙Slowly extend the cylinders once again, allowing the soapy water to escape and drain.∙Whilst the cylinders are extended gently flush the inside cavity by squirting water down one of the locking pin holes for 20-30 seconds.∙Wipe down the cylinder and painted outer telescope tubes with a rag if needed.∙Retract the cylinders and allow them to dry. Once dry, the lifter parts can be placed back into its protective case for storage.Note: In lieu of soap, a biodegradable and non-toxic degreasing fluid can be used to clean down the entire cylinder assembly.DO NOT USE INDUSTRIAL SOLVENTS SUCH AS THINNERS, EMULSIFIERS, ACIDS, ALKALIES OR OTHER CHEMICALS THAT MAY REMOVE OR DAMAGE EPOXY or POLYETHYLENE PAINTS.8.4 Maintenance Records and SummaryA record should be maintained to log the work carried out on each maintenance inspection. This can be achieved by registering the belt lifter as an asset in your plant maintenance planning software such as SAP.Maintenance work on individual components or the supplied equipment must be carried out in accordance of this Manufacturer’s instructi on manual. Please contact the Techmine team at any time if any further information is required.8.5 Additional Maintenance, Repairs and Modifications of ComponentsIt is recommended that the complete equipment assembly is returned to the original equipment m anufacturer for maintenance above what’s listed in this manual; i.e. repairs, modification or upgrades. Please note that some parts are recommended for complete replacement in lieu of carrying out regular maintenance or repair works. Details of such parts can be found in the spare parts inventory tables.9. WARRANTY9.1 Ongoing responsibilityThis operations and maintenance manual provide sufficient information to efficiently manage the generic operational and maintenance requirements for the belt lifting equipment provided by Techmine Solution Pty Ltd. The Portable Belt Lifter shall only be used per the equipment’s manufacturer’s original intent and following the procedures and practices outlined within this document. The end user assumes full responsibility for any equipment damage, personal injury or conveyor belt damage if the equipment is modified, altered or operated outside of the normal operating guidelines.9.2 WarrantyTechmine guarantees all equipment supplied is of the highest quality and offers a 12-month warranty on the quality of workmanship for all fabricated items and supplied parts. Warranty commences upon receipt of all equipment where proof of delivery is available. Otherwise the warranty will commence from the date of dispatch.Minor cosmetic damage to the products surface finish including fading, discoloration, small marks and abrasions caused during normal use and operation are not covered by warranty.Due to the operational environment and tasks the equipment has been designed to undertake; it is expected that minor cosmetic damage will be experienced during normal use. Visual damage that occurs to surfaces that have been painted, powder coated or anodised generally poses no performance degradation and/or safety threats during future use.During the warranty period, Techmine will repair or replace any components and products that are proven defective due improper material supply or workmanship. A replacement component or part will be covered by the above-mentioned warranty clause.10. SPARE PARTS 10.1 Recommended Spare Parts Table11. TROUBLESHOOTING GUIDETMS_RQ_002_Rev_1 Page 29TMS_RQ_002_Rev_1 Page 30OPERATIONS & MAINTENANCE MANUAL 12. MAINTENANCE REGIME12.1 Portable Hydraulic Belt LifterOPERATIONS & MAINTENANCE MANUAL 12.2 Hydraulic PumpOPERATIONS & MAINTENANCE MANUALTMS_RQ_002_rev_0Page 3313. COMPONENT IDENTIFICATION GENERAL DRAWINGS13.1 Specially Profiled Bent Beam Lifter。
ARTISAN技术组的产品说明说明书

USER GUIDENI SMA-2164/2165 Test Fixture Differential Digital I/O AccessoryThe NI SMA-2164/2165 test fixture is a breakout box for National Instruments differential digital waveform generator/analyzer modules, arbitrary waveform generators, andNI FlexRIO™ adapter modules. This fixture provides an easy way to connect to other devices for testing and debugging.The NI SMA-2164 is intended for use with devices with a matching Infiniband connector such as NI6561/6562 modules, NI6583 adapter modules, and NI6587 adapter modules.The NI SMA-2165 is intended for use with devices with matching VHDCI connectors such as NI5421 modules and NI6585 adapter modules. The NI SMA-2164/2165 may be compatible with other NI modules depending on the connector type and pinout.This guide explains how to set up and use the NI SMA-2164/2165 test fixture. Contents Conventions (2)What You Need to Get Started (3)Related Documentation (3)Parts Locator (4)Installing Cables (6)Connecting Signals (7)Using SMA Connectors (12)Making a Solder Connection (13)Terminating Signals (15)Minimizing the Effects of Stubs (15)Differentially Terminating DIO and Control Signals (15)Using the Prototyping Area (15)Prototyping Circuits (16)Cleaning the Accessory (16)Specifications (17)Where to Go for Support (18)NI SMA-2164/2165 User Guide ConventionsThe following conventions are used in this manual:<>Angle brackets that contain numbers separated by an ellipsis represent a range of values associated with a bit or signal name—for example, DIO <0..3>.»The » symbol leads you through nested menu items and dialog box options to a final action. The sequence Options»Settings»General directs you to pull down the Options menu, select the Settings item, and select General from the last dialog box.This icon denotes a note, which alerts you to important information.This icon denotes a caution, which advises you of precautions to take to avoid injury, data loss, or a system crash. When this symbol is marked on a product, refer to the Specifications section for information about precautions to take.boldBold text denotes items that you must select or click in the software, such as menu items and dialog box options. Bold text also denotes parameter names.italicItalic text denotes variables, emphasis, a cross-reference, or an introduction to a key concept. Italic text also denotes text that is a placeholder for a word or value that you must supply.monospaceText in this font denotes text or characters that you should enter from the keyboard, sections of code, programming examples, and syntax examples. This font is also used for the proper names of disk drives, paths, directories, programs, subprograms, subroutines, device names,functions, operations, variables, filenames, and extensions.What You Need to Get StartedTo set up and use the NI SMA-2164/2165, you need the following items:❑(NI SMA-2164 only) NI SHB12X-B12X LVDS cable assembly❑(NI SMA-2165 only) NI SHC68-C68-D3 cable assembly❑Compatible NI digital waveform generator/analyzer, NI FlexRIO adapter module, or other NI device installed in a PXI or CompactPCI chassisYou also may need the following optional items:❑SMA cables❑Resistors for termination or characterization. The NI SMA-2164/2165 ships populated with 0Ω resistors.❑The documentation included with the digital waveform generator/analyzer and driver softwareRelated DocumentationRefer to the documentation set for the device that you are connecting to the NI SMA-2164/2165 for more information. Documentation is available at /manuals and in your hardware kit.© National Instruments Corporation3NI SMA-2164/2165 User GuideNI SMA-2164/2165 User Guide Parts LocatorRefer to Figure 1 to locate connectors and components on the NI SMA-2164.Figure 1. NI SMA-2164 Parts Locator Diagram173-Pin Infiniband Connector 2SMA Connector 3Solder Pads4Resistor Network5Area Enlarged in Figure 86Solder Pads 7Labeling Strips© National Instruments Corporation 5NI SMA-2164/2165 User GuideRefer to Figure 2 to locate connectors and components on the NI SMA-2165.Figure 2. NI SMA-2165 Parts Locator Diagram168-Pin VHDCI Connector 2SMA Connector 3Solder Pads4Resistor Network 5Solder Pads 6Labeling StripsNI SMA-2164/2165 User Guide 6Installing CablesThe NI SHB12X-B12X LVDS cable is designed for use with the NI SMA-2164 and the NI SHC68-C68-D3 cable is designed for use with the NI SMA-2165. Figure 3 shows how to connect either of these cables to another NI device.Figure 3. Connecting a Device to the NI SMA-2164/2165Refer to Figure 3 as you complete the following steps to install the NI SHB12X-B12X LVDS or the NI SHC68-C68-D3 cable.CautionDisconnect power from the device, accessory, and any other connectedhardware before connecting the cable to prevent damage to the hardware and personal injury. NI is not liable for damage resulting from improper connections.1.Install the driver software for your device using the installation instructions available with your device.NoteAlways install the module in a computer or PXI/CompactPCI chassis before attaching any cables or accessories. Refer to your device documentation for instructions on installing the module.1An NI Device Installed in a PXI Chassis2NI SHB12X-B12X LVDS or NI SHC68-C68-D3 Cable3NI SMA-2164/2165© National Instruments Corporation 7NI SMA-2164/2165 User Guide2.Attach either end of the NI SHB12X-B12X LVDS or the NI SHC68-C68-D3 cable to the appropriate connector on your other NI device and secure the cable with the captive screws on the cable connector.NotesDo not use cables other than the NI SHB12X-B12X LVDS cable with theNI SMA-2164, and do not use cables other than the NI SCH68-C68-D3 cable with the NI SMA-2165. NI is not liable for any damage resulting from improper cable connections.3.Attach and secure the other end of the NI SHB12X-B12X LVDS or the NI SHC68-C68-D3 cable to the connector on the NI SMA-2164 or NI SMA-2165, respectively, and secure them together with the captive screws on the cable connector, as shown in Figure 3.Connecting SignalsEach DIO, PFI, and clock channel on your connected NI device corresponds to a specific pin on the NI SMA-2164/2165. Most channels are routed differentially to high-bandwidth SMA connectors, but some channels may be used for other purposes depending on your NI device. Refer to you device documentation for more information.You can make connections to the DIO, PFI, or clock channels on the NI SMA-2164/2165 using an SMA coaxial cable or by soldering directly to the inline circuits. Examples of how to make these connections are provided in the following sections.CautionBefore powering down the chassis, remove power from the prototyping areaof the NI SMA-2164/2165. NI is not liable for any damage resulting from improper signal connections.CautionConnections that exceed any of the maximum ratings for theNI SMA-2164/2165 or the connected NI device can damage the module and the computer. Maximum input ratings are provided in the Specifications section and in the specifications document that shipped with the other NI device. NI is not liable forany damage resulting from such signal connections.NI SMA-2164/2165 User Guide8Figure 4 shows the pinout of the NI SMA-2164 connector. Table 1 describes the pinout signals.Figure 4. NI SMA-2164 Connector PinoutNoteIf you are designing a custom cabling solution with the NI SMA-2164 connector (779157-01) and the NI SHB12X-B12X LVDS cable (192344-01), the pinout is reversed at the end connector. Refer to your connected device documentation for more information.Table 1. NI SMA-2164 Signal DescriptionsSignal Name Signal DescriptionCLK_LVDS+Positive terminal for the LVDS exported Sample clock.CLK_LVDS–Negative terminal for the LVDS exported Sample clock.CLK_LVPECL+Positive terminal for the LVPECL exported Sample clock.CLK_LVPECL–Negative terminal for the LVPECL exported Sample clock. STROBE+Positive external Sample clock source, which can be used fordynamic acquisition.STROBE–Negative external Sample clock source, which can be used fordynamic acquisition.IO_<0..15>+Positive bidirectional digital I/O data channels 0through15.IO_<0..15>–Negative bidirectional digital I/O data channels 0through15.PFI_<1..3>+Positive input terminals to the connected device for external triggers,or positive output terminals from the connected device for events. PFI_<1..3>–Negative input terminals to the connected device for externaltriggers, or negative output terminals from the connected device forevents.GND Ground reference for signals.RESERVED These terminals are reserved for future use. Do not connect tothese pins.Refer to your device documentation for more information about the signals on your connected device. For information about how the signals on your connected device map to the SMA connectors on the NI SMA-2164/2165, visit /info and enter 216xpinmap.© National Instruments Corporation9NI SMA-2164/2165 User GuideFigure5 shows the pinout of the NI SMA-2165 connector. Table2 describes the pinout signals.Figure 5. NI SMA-2165 Connector PinoutNI SMA-2164/2165 User Table 2. NI SMA-2165 Signal DescriptionsSignal Name Signal DescriptionGLCK+Positive terminal for the global clock.GLCK–Negative terminal for the global clock.P0_DIO<0..7>+Positive bidirectional digital I/O data channels 0through7 on port 0. P0_DIO<0..7>–Negative bidirectional digital I/O data channels 0through7 on port 0. P1_DIO<0..7>+Positive bidirectional digital I/O data channels 0through7 on port 1. P1_DIO<0..7>–Negative bidirectional digital I/O data channels 0through7 on port 1. P2_PFI<0..4>+Positive input terminals to the connected device for external triggers,or positive output terminals from the connected device for events.P2_PFI<0..4>–Negative input terminals to the connected device for external triggers,or negative output terminals from the connected device for events. GND Ground reference for signals.Refer to your device documentation for more information about the signals on your connected device. For information about how the signals on your connected device map to the SMA connectors on the NI SMA-2164/2165, visit /info and enter 216xpinmap.© National Instruments Corporation11NI SMA-2164/2165 User GuideNI SMA-2164/2165 User Guide Using SMA ConnectorsEach signal pair is labeled on the NI SMA-2164/2165. These connectors are arranged so that you can make quick connections to each polarity using a standard SMA coaxial cable assembly. Connectivity is made by inserting the cable receptacle onto the appropriate connector and tightening the receptacle sufficiently.NoteRefer to the receptacle documentation to assure that proper connections are made to signal and ground.Figure 6 shows how to make an SMA coaxial cable assembly connection.Figure 6. SMA Coaxial Cable Connection1SMA Cable 2SMA ConnectorMaking a Solder ConnectionEach signal pair is routed through a simple circuit to provide solder and probe access to the signals. Signal pairs are routed to a symmetric circuit, as shown in Figure7.Figure 7. Symmetric Circuit© National Instruments Corporation13NI SMA-2164/2165 User GuideNI SMA-2164/2165 User Guide Figure 8 is an enlarged portion of Figure 1. Figure 8 shows the routing of the signal pairs and the placement of the resistors shown in Figure 7.Figure 8. Solder ConnectionNoteThis figure shows channels IO_0 and IO_1 on the NI SMA-2164. This circuit is copied on the NI SMA-2164/2165 on each pair of channels, though the reference designators vary. Figure 7 is the schematic representation of the PCB shown in Figure 8.The resistors in the locations of R3, R4, R11, R12, R101, R377, R80, R67, R84, R105, and R345 above are unpopulated and discussed further in the Cleaning the Accessory and Prototyping Circuits sections. These pads are available for probing and for soldering.© National Instruments Corporation 15NI SMA-2164/2165 User GuideTerminating SignalsTermination of high-speed digital signals is necessary to prevent signal reflections and force signal channels to a known state when no signal is present. Pads for terminating resistors are connected to all DIO and control channels on the NI SMA-2164/2165. These pads are labeled in Figures 1 and 2 and are shown in more detail in Figure 8.NoteProper termination needs are application-specific. For some special considerations for choosing resistor values, refer to the Cleaning the Accessory section.Minimizing the Effects of StubsStubs are unterminated tributaries from the original signal path. Stubs decrease the signal quality of the system by adding reflections to the transmission channels. To minimize the effect of stubs, termination is placed at the end of the signal path.NoteRefer to your connected device documentation for more information about proper signal termination.If your signal transmission line ends on the NI SMA-2164/2165, you can use the provided resistor pads to solder termination resistors. If your signal terminates somewhere other than the NI SMA-2164/2165, NI recommends terminating the transmission line at the final signal destination. Each signal pair is routed through a symmetric circuit, shown in Figure 7.Differentially Terminating DIO and Control SignalsUnpopulated resistors like R80, R63, R67, and R84 in Figure 8 can be populated with 0402-sized resistors to provide termination. It is recommended that these resistors are each populated with 50Ω resistors to provide the expected 100Ω of differential termination.Using the Prototyping AreaThe NI SMA-2164/2165 prototyping area is designed to aid you in the following tasks:•Prototyping and testing circuits—Use the NI SMA-2164/2165 in conjunction with other NI devices for prototyping, evaluating, and testing custom circuits and/or components.•Creating custom interfaces—Use the NI SMA-2164/2165 for creating custom interfaces to other cables or devices. You can use the prototyping area to mount and interface the integrated circuits (ICs) or connectors required for your application.•Prototyping a DUT load board—Use the NI SMA-2164/2165 as a simple DUT interface board or as a prototype of a custom DUT load board.The prototyping area is labeled in Figure 1.Also labeled in that diagram are the erasable labelingstrips for your notes as you use the prototyping area.Prototyping CircuitsEach signal pair is routed to a simple debug and prototyping circuitry illustrated in Figure7. By placing or removing components, each circuit can be configured to accomplish one of the following tasks, which are described in more detail in the following sections.•Differentially terminate the signals—For more information about differential termination, refer to the Differentially Terminating DIO and Control Signals section.•Externally provide a common mode or offset voltage to a differential signal—If an application requires an externally provided offset voltage, you may populate the R3, R4, R11, and R12 resistor locations with 0603-sized resistors to provide a connection point. For balanced application to a differential signal, it is recommended that R0 and R1 each be populated with a 3.74 kΩ resistor.The node shared by the resistors in the R3, R4, R11, and R12 location is electricallyconnected between all DIO circuits.•Externally probe or measure the common mode or offset of a differential signal—If an application requires that the offset voltage be measured on a differential signal, you can populate the R80 and R63 resistor locations. R80 and R63 are connected at a node which is connected to an SMA pad through a 0Ω jumper. This SMA can be populated for coaxial connectivity to the offset voltage of the signal. The R80 and R63 resistor locations should each be 50Ω if termination is required, else, larger values of 3.74kΩ are more appropriate.•Channel-to-channel connectivity—If it is required that two channels be connected to one another (for round-trip delay elimination for example), you can connect neighboringchannels by populating a size 1206 0 jumper on resistor locations R345 and R377 inFigure8. By populating these resistors, IO_0 connects to IO_1, IO_2 connects to IO_3, and so on, and CLKOUT_LVDS connects to STROBE.Cleaning the AccessoryDisconnect all cables to the NI SMB-2164/2165 before cleaning. To remove light dust, use a soft, nonmetallic brush. To remove other contaminants, use alcohol wipes. The unit must be completely dry and free from contaminants before returning to service.NI SMA-2164/2165 User SpecificationsDigital I/ODIO channels....................................................16, differentialControl I/O channels.........................................6, differentialResistors Number (44)VoltageMaximum voltage.............................................5 VPrototyping Area Dimensions.......................................................4 cm × 9 cm(1.57 in. × 3.54 in.)Solder pads.......................................................154, unconnectedTraces Type..................................................................Matched length to 100 milsAC impedance...................................................100 Ω differentialPhysical Dimensions.......................................................17.55 cm × 2.07 cm × 20.32 cm(6.91 in. × 0.816 in. × 8 in.)I/O connectors...................................................One 73-pin Infiniband connector or one 68-pinVHDCI connector, and 44SMA connectors Weight...............................................................216 g (7.6 oz)CE ComplianceRefer to the regulatory statement for this product for additional compliance information. To obtain this information for this product, visit /certification, search by model number or product line, and click the appropriate link in the Certification column.interference. In a residential environment, the user may be required to take adequatemeasures to reduce the radio interference.© National Instruments Corporation17NI SMA-2164/2165 User GuideWhere to Go for SupportThe National Instruments Web site is your complete resource for technical support. At/support you have access to everything from troubleshooting and application development self-help resources to email and phone assistance from NI Application Engineers.A Declaration of Conformity (DoC) is our claim of compliance with the Council of the European Communities using the manufacturer’s declaration of conformity. This system affords the user protection for electromagnetic compatibility (EMC) and product safety. You can obtain the DoC for your product by visiting /certification. If your product supports calibration, you can obtain the calibration certificate for your product at /calibration. National Instruments corporate headquarters is located at 11500North Mopac Expressway, Austin, Texas, 78759-3504. National Instruments also has offices located around the world to help address your support needs. For telephone support in the United States, create your service request at /support and follow the calling instructions or dial 5127958248. For telephone support outside the United States, visit the Worldwide Offices section of / niglobal to access the branch office Web sites, which provide up-to-date contact information, support phone numbers, email addresses, and current events.NI SMA-2164/2165 User LabVIEW, National Instruments, NI, , the National Instruments corporate logo, and the Eagle logo are trademarks of National Instruments Corporation. Refer to the Trademark Information at /trademarks for other National Instruments trademarks. Other product and company names mentioned herein are trademarks or trade names of their respective companies. For patents covering National Instruments products/technology, refer to the appropriate location: Help»Patents in your software, the patents.txt file on your media, or the National Instruments Patents Notice at /patents. Refer to the Export Compliance Information at /legal/export-compliance for the National Instruments global trade compliance policy and how to obtain relevant HTS codes, ECCNs, and other import/export data.© 2005–2011 National Instruments Corporation. All rights reserved.374063B-01Oct11。
Intellian v60 产品数据手册说明书
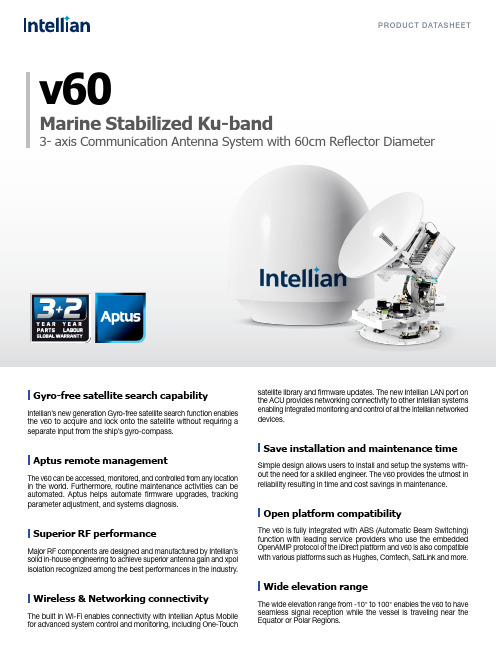
PRODUCT DATASHEE TGyro-free satellite search capability Intellian’s new generation Gyro-free satellite search function enables the v60 to acquire and lock onto the satellite without requiring a separate input from the ship’s gyro-compass.Aptus remote managementThe v60 can be accessed, monitored, and controlled from any location in the world. Furthermore, routine maintenance activities can be automated. Aptus helps automate firmware upgrades, tracking parameter adjustment, and systems diagnosis.Superior RF performanceMajor RF components are designed and manufactured by Intellian’s solid in-house engineering to achieve superior antenna gain and xpol isolation recognized among the best performances in the industry.Wireless & Networking connectivityThe built in Wi-Fi enables connectivity with Intellian Aptus Mobile for advanced system control and monitoring, including One-T ouch satellite library and firmware updates. The new Intellian LAN port on the ACU provides networking connectivity to other Intellian systems enabling integrated monitoring and control of all the Intellian networked devices.Save installation and maintenance timeSimple design allows users to install and setup the systems with-out the need for a skilled engineer. The v60 provides the utmost in reliability resulting in time and cost savings in maintenance.Open platform compatibilityThe v60 is fully integrated with ABS (Automatic Beam Switching) function with leading service providers who use the embedded OpenAMIP protocol of the iDirect platform and v60 is also compatible with various platforms such as Hughes, Comtech, SatLink and more.Wide elevation rangeThe wide elevation range from -10° to 100° enables the v60 to have seamless signal reception while the vessel is traveling near the Equator or Polar Regions.Marine Stabilized Ku-band3- axis Communication Antenna System with 60cm Reflector Diameter v60AmericasIrvineIntellian Technologies USA, Inc.T +1 949 727 4498F +1 949 271 4183Toll Free +1 888-201-9223EMEARotterdam Intellian B.V.T +31 1 0820 8655F +31 1 0820 8656APACSeoulIntellian Technologies, Inc.T +82 2 511 2244F +82 2 511 2235Global HQ Innovation CenterIntellian Technologies, Inc T +82 31 379 1000F +82 31 377 6185• Automatic Diagnosis Encoder, Motor, Tilt/Gyro sensor, LNB pol control, LNB, Antenna & ACU power, Modem connection, I/F• DC Power SeparationRotary joint - TX and RX IF signalSlip ring - Antenna power and 8W BUC power8W BUC Power (48 V DC)Modem InterfaceAntenna RX*Modem is not suppliedSystem Dimensions30.4 c m (12")30.4 cm (12")4.4 cm (1.7")38 c m (15")P a r t N o . 2020N 0-D S 0401-V 5©2020 Intellian Technologies, Inc. All rights reserved. Intellian and the Intellian logo are registered trademarks. v60 and v-Series are trademarks of Intellian Technologies, Inc. in the U.S. and/or various countries. All other trademarks are the property of their respective owners. Information in this document is subject to change without notice. ISO9001 / ISO14001 Certified Intellian has more offices worldwide. Addresses, phone numbers, and fax numbers are listed on the Intellian Website at 。
- 1、下载文档前请自行甄别文档内容的完整性,平台不提供额外的编辑、内容补充、找答案等附加服务。
- 2、"仅部分预览"的文档,不可在线预览部分如存在完整性等问题,可反馈申请退款(可完整预览的文档不适用该条件!)。
- 3、如文档侵犯您的权益,请联系客服反馈,我们会尽快为您处理(人工客服工作时间:9:00-18:30)。
Ni-NTA Superflow Cartridge 手册用于手动或FPLC纯化His-tag蛋白目录:包装内容物(4)储存和稳定性(4)安全措施(4)介绍(7)Ni-NTA Superflow Cartridge说明书(7)QIA表达系统(7)Ni-NTA Cartirdge 接头(14)天然或变性条件下纯化蛋白(15)说明书⏹天然条件下清澈的E.coli菌液的制备(16)⏹变性条件下清澈的E.coli菌液的制备(18)⏹从E.coli细胞制备6XHis-tag的胞质蛋白(19)⏹天然条件下从昆虫细胞中制备细胞菌液(20)⏹使用注射器手动纯化6XHis-tag蛋白(21)⏹使用自动层析系统纯化6XHis-tag蛋白(22)问题的解决(23)附录A:Buffer成分(25)附录B; Ni-NTA Superflow Cartridge的清洁与再生(27)包装包含物Cat no. Ni-NTA Superflow Cartridge(1)Ni-NTA Superflow Cartridge(5)说明书30721 5 1 30725 100 1 30760 1 1 30761 5 1 30765 100 1技术支持在QIAGEN,我们为我们的技术支持的质量和有效性而感到骄傲我们的技术部门是由有广泛实验经验的技术人员和专家组成的,他们都从事分子生物学而且熟练使用QIAGEN的产品。
如果您有任何问题或实验中遇到困难关于Ni-NTA SuperflowCartridge或QIAGEN的产品,请尽快联系我们。
QIAGEN用户是我们改进和专业化产品的主要信息来源。
这些信息对于我们的科研人员与其他的科学家一样重要。
因此您如果有什么关于产品的建议或新的需要和技术等等请尽快联系我们。
对于技术支持和更多的信息请联系QIAGEN的技术服务部或者当地经销商储存和稳定性Ni-NTA Superflow Cartridge应该储存在2-8度。
不要冷冻。
Cartridges在这样的条件下可以储存一年而性能不会发生任何改变。
产品局限性Ni-NTA Superflow Cartridge仅供科研使用。
没有声明或表述是用来为诊断,预防或治疗疾病而提供信息。
所有预料到的麻烦和注意事项东应该使用中注意。
对于重组DNA实验,我们推荐所有用户参照NIH指导方法,或者其他的可用性指导方针。
产品授权和满意的保证QIAGEN保证产品的效果在我们的产品文献中都有描述。
顾客对于产品的特殊用途必须决定它的适用性。
如果不是由于使用造成的产品性能问题,QIAGEN将会免费更换或退货。
我们有权更换、更改或是调整任何产品以增强性能和设计。
如果QIAGEN产品没有达到您的要求,联系我们的当地技术部门或是销售商。
我们将相信您的理由或者交换产品----只要您愿意。
分离条件应用于QIAGEN科学仪器,服务产品,干冰用于产品运输。
请询问更多的信息你还可以要求得到QIAGEN的条款和条件的副本,他会在我们的发票后提供给您。
如果您有什么关于产品说明和性能的问题,请联系QIAGEN技术服务和当地经销商。
安全措施当工作时使用化学药品时,通常要穿实验服装,带一次性手套和护目镜。
更多的信息请咨询MSDSs。
您可以在网站下载PDF或打印QANGE kit 和kit 组成以下危险和安全性用语适用于Ni-NTA Superflow Cartridge。
包含乙醇和镍铵酸。
伤害性的,感光的,易燃的。
危险和安全用语:R10-22-40-42/43。
S13-26-36-4624小时紧急情况紧急医疗信息24小时内可以从Poison Information Center Mainz, Germany得到,有英语、法语和德语三种。
电话:+49-6131-19240介绍QIAGEN Ni-NTA Superflow Cartridge是预先装好Ni-NTA Superflow的1ml和5ml柱子,用来纯化6XHis-tagged蛋白,可以使用注射器、蠕动泵,或者液相层析系统(例如AKTA或FPLC)Ni-NTA Superflow Cartridge高流速可能导致恢复6XHis-tagged蛋白减少蛋白不同吸附能力不同QIA表达系统QIA表达系统以6Xhis tag为基础,这是一个亲和标签由6个连续的His残基组成。
这个亲和标能够被QIAGEN独特的专利产品Ni-NTA金属吸附层析柱显著的选择吸附。
QIA表达系统这个独特的特性提供了大量的显著优势(表一)而并不适合其他亲和标签和层析方法表一:QIA表达系统的特点和优势Ni-NTA SuperflowNi-NTA Superflow由连接Superflow树脂的Ni-NTA组成。
它将出众的机械稳定性和显著的流动特性及高效的动力吸附能力相结合。
吸附6XHis-tagged蛋白的能力是5-20mg/ml。
这种树脂对于效率生产登记和FPLC的要求允许使用一步法纯化6XHis-tag蛋白。
Ni-NTA能力出众,适应试剂范围广泛,例如2M NaCl,10mM DTT,8M尿素,及许多去污剂(表二)局限性Ni-NTA基质不要暴露在高浓度的还原剂中,例如DTT,DTE;高浓度下,这些试剂还原Ni离子还可能阻止吸附6XHIS-Tag蛋白。
Ni-NTA基质在还原剂中会变成棕色。
很多情况下,β-巯基乙醇能够在浓度不高于20mM时使用,DTT兼容性证明浓度可以到10mM。
EDTA,EGTA或其他任何强螯合剂吸附Ni离子并将他们从NTA上夺走。
NTA基质缺乏NI时变白。
使用任何还原剂或螯合剂都要当心,如果不确定,就在小量的Ni-NTA 基质上作检测。
高浓度的Buffer包含强的给电子集团或者氨基酸例如Arg、Glu、Gly、His,菌液中应该尽量避免。
细胞应该被溶解。
不要用强的螯合剂如EDTA,强的还原剂如DTT,或者离子去垢剂如SDS。
虽然有些例子表明这些试剂小剂量的应用没有问题,但是我们还是不推荐使用。
更多的详细信息,见表二Cartridge 连接器Ni-NTA Superflow Cartridge 可以手动纯化蛋白(用注射器),也可以自动纯化(使用层析系统,例如AKAT或FPLC 系统)。
Cartridge 进样口和出样口的尺寸和要求的连接器及手动和自动纯化所需适配器详细情况如下表表三 Ni-NTA Superflow Cartridge 所需连接器天然或变性条件下的纯化在变性还是天然条件下纯化6XHis-tagged蛋白取决于蛋白的位置和可溶性,6XHis-tag的特性,下游技术的要求以及生物活性都必须要保持,因此如果复性过程是可用的,变性纯化和随后的蛋白折叠复性就要考虑周全天然条件下纯化如果纯化首选而且必须在天然条件下,那么6XHis-tagged蛋白必须要溶解。
尽管如此,虽然有许多蛋白出现在包涵体,一般还是有一些可溶物质能够在天然条件下纯化。
潜在的无关的影响Ni-NTA基质的无标签蛋白一般在天然条件下要高于变性条件,这个反映在首次的洗液中会出现大量的蛋白。
可以用含有低浓度咪唑的裂解液(Lysis Buffer)和清洗液(Wash Buffer)冲洗减少非特异性吸附无特异。
有时6XHIs-tag会被天然蛋白的三级结构包埋,因此可溶蛋白要求在能够被Ni-NTA 纯化之前要求变性。
作为对照,在变性条件下的平行试验应该要实行:如果只能在变性条件下纯化,Tag能够容易的移到蛋白相反的另一端。
变性条件下纯化许多表达系统表达出的高水平的重组蛋白都能够形成不溶的集合体;Ecoli中形成众所周知的包涵体。
变性Buffer包含6M尿素或6M盐酸胍,通常用来完全溶解包涵体和6XHis-tag蛋白。
变性条件下,蛋白中的6XHis tag会完全暴露因此Ni-NTA基质吸附效率会提高,而且基质减少了非特异性吸附,纯化效率也会升高。
变性条件下纯化的6XHis-tagged蛋白可以直接用来试验,或者复性再折叠。
蛋白复性和重折叠能够在Ni-NTA cartridge洗脱之前完成,或在溶液中也可以;建议参考QIAexpressionist说明书:天然条件下Ecoli菌液的制备材料和试剂细胞颗粒,Buffer NPI-10,溶菌酶,Benzonase核酸酶(一级纯度,25U/ml,Merck,catno.1.0169.0001),2XSDS-PAGE样品Buffer,可选择仪器:超声仪Buffer组成参见Appendix A步骤:1、冰上解冻细胞颗粒,用Buffer NPI-10重悬细胞,每克湿重用2-5ml需要多少细胞取决于6XHis-tagged蛋白的表达水平和使用的表达系统。
Ni-NTA 基质的吸附能力是蛋白依赖性的,一般为20mg/ml。
Buffer NPI-10包含10mM咪唑用来降低无标签蛋白和污染蛋白的吸附,并用少量Wash步骤后增加纯度。
如果标签蛋白在这些条件下没有被吸附,咪唑的量因该减少到1-5mM。
如果6XHis 蛋白显示出高吸附亲和力,那咪唑的浓度可以增至20mM。
2、加入溶菌酶终浓度1mg/ml(50000units/ml)和Benzonase核酸酶(3U/ml)冰上孵化30Min选择性的,可以加入RNase A(10μ/ml)和DNase I(5μ/ml),冰上10-15分,或用小容量的钝的注射器的针头吸吹数次溶解。
2a、(可选)冰上超声波破碎用200-300W的six 10s的脉冲,每个脉冲间隔10S的冷却期。
3、4度10000Xg离心菌液20-30分,沉淀细胞残基,收集上清可能会有一定比例的细胞蛋白,包括6XHis-tagged蛋白,仍然未溶而存在于细胞沉淀。
为了得到更多的标签蛋白,材料在变性条件下纯化之前必须在变性条件下溶解。
4、加入5μ2X SDS-PAGE样品Buffer于5μ上清中,-20度储存以备SDS-PAGE5、纯化过程见说明书说明书:变性条件下Ecoli菌液的制备材料和试剂细胞颗粒;2X SDS-PAGE样品Buffer;Buffer B;可选择:BufferB/7M尿素和Benzonase 核酸酶(7M尿素不变性,8M尿素变性)Buffer组成参见Appendix A步骤:1、冰上15分溶解细胞颗粒,Buffer B重悬,每克湿重5m l1a、(可选)冰上15分钟溶解细胞颗粒,BufferB/7M尿素中重悬,每克湿重5ml,加入Benzonase核酸酶,室温(20-25度)孵育30分钟需要多少细胞取决于6XHis-tagged蛋白的表达水平和使用的表达系统。
Ni-NTA 基质的吸附能力是蛋白依赖性的,一般为20mg/ml。
2、室温下摇动细胞15-60分钟或者用漩涡振荡器轻轻震荡,注意避免泡沫当溶液为半透明时表明溶解完全。