汽车制动系统的结构设计
EQ1041汽车制动系统的设计-任务书

并通过设计,锻炼了理论联系实际的能力和工程应用的能力,同时培养了学生开拓创新的能力和与人交往的能力。
二、设计(论文)内容、技术要求(研究方法)
1.主要研究内容
(9)毕业设计答辩准备及答辩第17周(6月20日~6月24日)
五、主要参考资料
[1]刘惟信 . 汽车设计 . 清华大学出版社
[2]制动系统的发展现状及趋势 .汽车研究与开发2005.1
[3]周志立 . 汽车ABS原理与结构 ,机械工业出版社
[4]陈家瑞 . 汽车构造 ,机械工业出版社
[5]王国林 . 汽车底盘构造及维修 ,高等教育出版社
[6]齐晓杰 . 汽车液压、液力与气压传动技术,化学工业出版社
[7]王世刚 . 机械设计实践 . 哈尔滨工程大学出版社
[8]戴枝荣 . 工程材料 . 高等教育出版社
[9]王宝玺 . 汽车拖拉机制造工艺学,机械工业出版社
[10]王望予 . 汽车设计,机械工业出版社
六、备注
指导教师签字:
年 月 日
教研室主任签字:
在调查研究的基础上,分析轻型汽车的结构特点和使用条件,设计一套完整的汽车制动系统,包括制动系统的类型的选择、制动系统的总体布置形式,制动器的类型选择和结构设计,及ABS结构型式及工作原理设计。
2.研究方法
1)在调研和搜集资料的基础上,认真分析制动系统的结构特点,确定合理的设计参数;
2)确定制动系统的结构类型和工作原理,完成制动系统的总布置设计;
2)设计有一定创新性。
三、设计(论文)完成后应提交的成果
制动系统设计规范
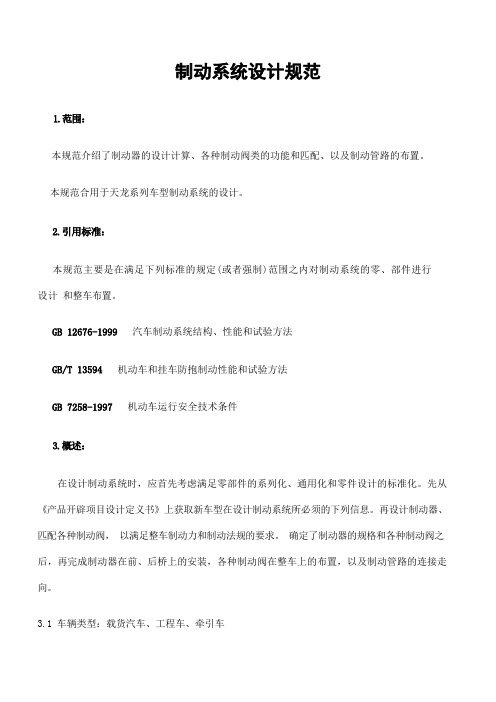
本规范介绍了制动器的设计计算、各种制动阀类的功能和匹配、以及制动管路的布置。
本规范合用于天龙系列车型制动系统的设计。
本规范主要是在满足下列标准的规定(或者强制)范围之内对制动系统的零、部件进行设计和整车布置。
汽车制动系统结构、性能和试验方法机动车和挂车防抱制动性能和试验方法机动车运行安全技术条件在设计制动系统时,应首先考虑满足零部件的系列化、通用化和零件设计的标准化。
先从《产品开辟项目设计定义书》上获取新车型在设计制动系统所必须的下列信息。
再设计制动器、匹配各种制动阀,以满足整车制动力和制动法规的要求。
确定了制动器的规格和各种制动阀之后,再完成制动器在前、后桥上的安装,各种制动阀在整车上的布置,以及制动管路的连接走向。
3.1 车辆类型:载货汽车、工程车、牵引车3.2 驱动形式:4×2、6×4、8×43.3 主要技术及性能参数:长×宽×高、轴距、空/满载整车重心高坐标、轮距、整备质量、额定载质量、总质量、前/后桥承载吨位、 (前/后)桥空载轴荷、 (前/后)桥满载轴荷、最高车速、最大爬坡度等。
3.4 制动系统的配置:双回路气/液压制动、弹簧制动、鼓/盘式制动器、防抱制动系统、手动/自动调整臂、无石棉磨擦衬片、感载阀调节后桥制动力、缓速器、排气制动。
本规范仅对鼓式制动器的各主要元件和设计计算加以阐述,盘式制动器的选型和计算将暂不列入本规范的讨论范围之内。
4.1 鼓式制动器主要元件:4.1.1 制动鼓:由于铸铁耐磨,易于加工,且单位体积的热容量大,所以,重型货车制动鼓的材料多用灰铸铁。
不少轻型货车和轿车的制动鼓为组合式,其圆柱部份用铸铁,腹板则用钢压制件。
制动鼓在工作载荷下将变形,使蹄、鼓间单位压力不均,带来少许踏板行程损失。
制动鼓变形后的不圆柱度过大,容易引起制动时的自锁或者踏板振动。
所以,在制动鼓上增加肋条,以提高刚度和散热性能。
中型以上货车,普通铸造的制动鼓壁厚为 13~18㎜。
汽车制动系统~毕业设计论文(论文)
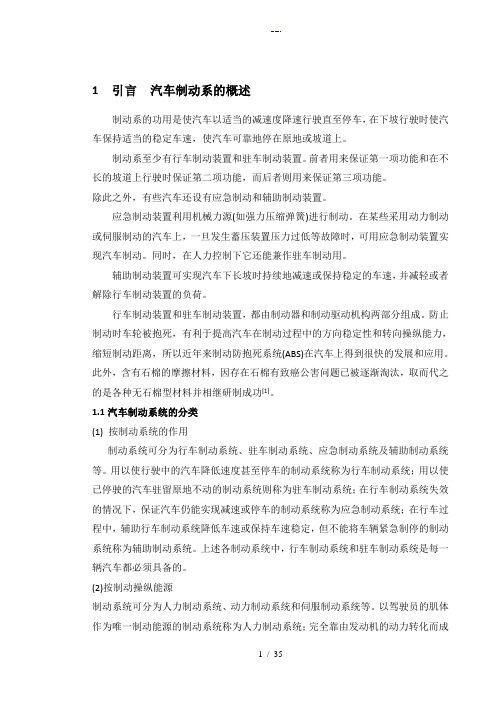
1 引言汽车制动系的概述制动系的功用是使汽车以适当的减速度降速行驶直至停车,在下坡行驶时使汽车保持适当的稳定车速,使汽车可靠地停在原地或坡道上。
制动系至少有行车制动装置和驻车制动装置。
前者用来保证第一项功能和在不长的坡道上行驶时保证第二项功能,而后者则用来保证第三项功能。
除此之外,有些汽车还设有应急制动和辅助制动装置。
应急制动装置利用机械力源(如强力压缩弹簧)进行制动。
在某些采用动力制动或伺服制动的汽车上,一旦发生蓄压装置压力过低等故障时,可用应急制动装置实现汽车制动。
同时,在人力控制下它还能兼作驻车制动用。
辅助制动装置可实现汽车下长坡时持续地减速或保持稳定的车速,并减轻或者解除行车制动装置的负荷。
行车制动装置和驻车制动装置,都由制动器和制动驱动机构两部分组成。
防止制动时车轮被抱死,有利于提高汽车在制动过程中的方向稳定性和转向操纵能力,缩短制动距离,所以近年来制动防抱死系统(ABS)在汽车上得到很快的发展和应用。
此外,含有石棉的摩擦材料,因存在石棉有致癌公害问题已被逐渐淘汰,取而代之的是各种无石棉型材料并相继研制成功[1]。
1.1汽车制动系统的分类(1) 按制动系统的作用制动系统可分为行车制动系统、驻车制动系统、应急制动系统及辅助制动系统等。
用以使行驶中的汽车降低速度甚至停车的制动系统称为行车制动系统;用以使已停驶的汽车驻留原地不动的制动系统则称为驻车制动系统;在行车制动系统失效的情况下,保证汽车仍能实现减速或停车的制动系统称为应急制动系统;在行车过程中,辅助行车制动系统降低车速或保持车速稳定,但不能将车辆紧急制停的制动系统称为辅助制动系统。
上述各制动系统中,行车制动系统和驻车制动系统是每一辆汽车都必须具备的。
(2)按制动操纵能源制动系统可分为人力制动系统、动力制动系统和伺服制动系统等。
以驾驶员的肌体作为唯一制动能源的制动系统称为人力制动系统;完全靠由发动机的动力转化而成图 2 双回路液压系统中的串联式双腔制动主缸 1-套;2-密封套;3-第一活塞;4-盖;5-防动圈;6、13-密封圈 7-垫片;8-挡片;9-第二活塞;10-弹簧;11-缸体;12-第二工作室 14、15-进油孔;16-定位圈;17-第一工作室;18-补偿孔;19-回油孔 图1 制动系统的组成示意图 1-前轮盘制动器;2-制动总泵;3-真空助力器;4-制动踏板机构;5-后轮鼓式制动;6-制动组合阀;7-制动警的气压或液压形式的势能进行制动的系统称为动力制动系统;兼用人力和发动机动力进行制动的制动系统称为伺服制动系统或助力制动系统[2]。
载货汽车底盘总体及制动器的设计毕业设计说明书

1绪论1.1制动器介绍制动器是汽车制动系的主要部件,其功用是使汽车以适当的减速度行驶至直停车;在下坡时,使汽车保持稳定车速;使汽车可靠地停在原地或坡道上。
汽车制动系至少应有两套独立的制动装置,即行车制动装置和驻车制动装置。
前者用来保证前两项功能,后者用来保证第三项功能。
汽车制动性能主要由三方面面来评价:制动效能、制动效能的恒定性、制动时汽车的方向稳定性。
制动器主要有摩擦式、液力式和电磁式等几种形式。
电磁式制动器虽有作用滞后性好,易于连接而且接头可靠等优点,但因成本高,只在一部分总质量较大的商用车上用作车轮制动器或缓速器;液力式制动器一般只用做缓速器。
目前广泛应用的仍为摩擦式制动器。
摩擦式制动器按摩擦副结构形式不同,可分为鼓式和盘式两大类。
前者的摩擦副中的旋转元件为制动鼓,其工作面为圆柱面;后者的旋转元件则为圆盘状制动盘以端面为工作面。
鼓式制动器有内张型和外束型两种。
根据促动蹄促动装置的不同可分为轮缸式制动器、楔式制动器和凸轮制动器。
轮缸式制动器因采用液压式促动装置使其结构复杂,密封性能要求提高,增加了造成本。
凸轮式制动器结构简单,易加工,刚性好,并且质量轻,操纵力低,有良好的防污染和防潮能力,成本相对低廉,比较经济。
加上我国现有的基本国情,鼓式制动器仍具有很大的应用空间。
尤其是在大中型、需要较大制动力的车辆,使用鼓式制动器较能满足其要求。
1.2汽车制动系概论汽车制动系是用于行驶中的汽车减速或停车,使下坡行驶的汽车的车速保持稳定以及使已停驶的汽车在原地驻留不动的机构。
汽车制动系直接影响着汽车行驶的安全性和停车的可靠性。
随着高速公路的迅速发展和车速的提高以及车流密度的日益增大,为了保证行车安全,停车可靠,汽车制动系的工作可靠性显得日益重要。
也只有制动性能良好,制动系工作可靠的汽车,才能充分发挥其动力性能。
汽车制动系至少应有两套独立的制动装置,即行车制动装置和驻车制动装置;重型汽车或经常在山区行驶的汽车要增设应急制动装置;牵引汽车还应有自动制动装置。
汽车制动系统动力学特性分析与优化设计
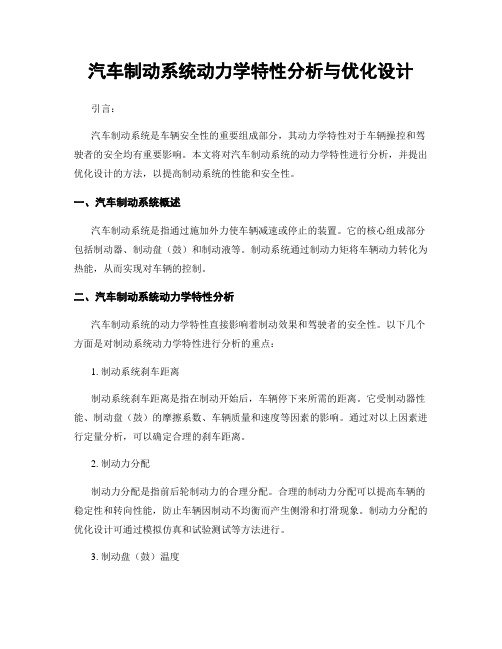
汽车制动系统动力学特性分析与优化设计引言:汽车制动系统是车辆安全性的重要组成部分,其动力学特性对于车辆操控和驾驶者的安全均有重要影响。
本文将对汽车制动系统的动力学特性进行分析,并提出优化设计的方法,以提高制动系统的性能和安全性。
一、汽车制动系统概述汽车制动系统是指通过施加外力使车辆减速或停止的装置。
它的核心组成部分包括制动器、制动盘(鼓)和制动液等。
制动系统通过制动力矩将车辆动力转化为热能,从而实现对车辆的控制。
二、汽车制动系统动力学特性分析汽车制动系统的动力学特性直接影响着制动效果和驾驶者的安全性。
以下几个方面是对制动系统动力学特性进行分析的重点:1. 制动系统刹车距离制动系统刹车距离是指在制动开始后,车辆停下来所需的距离。
它受制动器性能、制动盘(鼓)的摩擦系数、车辆质量和速度等因素的影响。
通过对以上因素进行定量分析,可以确定合理的刹车距离。
2. 制动力分配制动力分配是指前后轮制动力的合理分配。
合理的制动力分配可以提高车辆的稳定性和转向性能,防止车辆因制动不均衡而产生侧滑和打滑现象。
制动力分配的优化设计可通过模拟仿真和试验测试等方法进行。
3. 制动盘(鼓)温度制动盘(鼓)温度是制动系统动力学特性中的一个重要参数。
当制动盘(鼓)温度过高时,会导致制动渐缓现象,减少制动效果和安全性。
因此,对制动盘(鼓)温度进行分析,并通过散热设计降低温度是提高制动系统性能的重要手段。
三、汽车制动系统优化设计基于对汽车制动系统动力学特性的分析,我们可以通过以下几个方面的优化设计来提高制动系统的性能和安全性:1. 制动器材料的优化选择制动器材料的选择直接影响制动盘(鼓)的摩擦系数和热导率等性能。
对于高速行驶的车辆,选择摩擦系数和热导率较高的制动器材料能够提高制动效果和降低制动盘(鼓)温度。
2. 制动系统结构的优化设计制动系统结构的优化设计包括对制动器、制动盘(鼓)和制动液等的布置和参数的优化。
通过合理的结构设计,可以实现制动力的均衡分配和散热能力的提高,进而提高制动系统的性能和安全性。
汽车制动系统的设计-开题报告

三、技术路线(研究方法)
收集资料,进行调研 完成开题报告
确定总体设计方案
制动系统的主要参 数确定及计算
制动系统主要 参数的确定
制动力与制动 力分配系数
同步附着系数
制动强度和附 着率利用率
制动器最大力 矩
盘式制动器的设计 及计算
制动器零部件的结 构设计与强度计算
摩擦衬块的磨损 特性计算
制动器主要零部 件的结构设计
制动器是制动系统的主要组成部分,目前汽车制动器基本都是摩擦式制动器,按照摩擦副中 旋转元件的不同,分为鼓式和盘式两大类制动器。鼓式制动器又有领从蹄式、双领蹄式、双向双 领蹄式、双从蹄式、单向自增力式、双向自增力式制动器等结构型式。盘式制动器有固定钳式, 浮动钳式,浮动钳式包括滑动钳式和摆动钳盘式两种型式。滑动钳式是目前使用广泛的一种盘式 制动器。由于盘式制动器热和水稳定性以及抗衰减性能较鼓式制动器好,可靠性和安全性也好, 而得到广泛应用。但是盘式制动器效能低,无法完全防止尘污和锈蚀,兼做驻车制动时需要较为 复杂的手驱动机构,因而在后轮上的应用受到限制,很多车是采用前盘后鼓的制动系统组成。电 动汽车和混合动力汽车上具有再生制动能力的电机,在回收制动能量时起制动作用,它引入了新
签字:
年月日
三技术路线研究方法收集资料进行调研完成开题报告确定总体设计方案盘式制动器的设计及计算制动器零部件的结构设计与强度计算液压制动驱动机构的设计及计算制动系统的主要参数确定及计算完成课题设计研究绘制设计图制动系统主要参数的确定制动力与制动力分配系数同步附着系数制动强度和附着率利用率制动器最大力矩摩擦衬块的磨损特性计算制动器热容量和温升特性的核算盘式制动器制动力矩的计算制动器主要零部件的结构设计制动器主要零部件的强度计算制动器轮缸直径与工作容积制动主缸的直径与工作容积完成说明书四进度安排1收集资料调研撰写开题报告第一周2周四交开题报告实习了解制动系统的构造第二周3完成各参数的设计计算和校核工作至少应有装配图的草图第三周第七周4中期检查画装配图和零件图第八周5画装配图和零件图编写说明书第九周第十一周6交毕业设计说明书和装配图零件图修改第十二周7毕业设计指导教师审核第十三周8毕业设计修改第十四周9毕业设计评阅教师评阅或预审第十五周10毕业设计修改第十六周11毕业设计答辩第十七周五参考文献1陈家瑞
汽车制动主缸的设计论文

汽车制动主缸的设计论文标题:汽车制动主缸的设计一、引言汽车制动主缸是液压制动系统的重要组成部分,负责将驾驶员施加在制动踏板上的力量转化为制动液的压力,进而传递到车轮制动器,产生制动作用。
制动主缸的性能直接影响到汽车的制动效果。
因此,设计一款性能优良的制动主缸对于提高汽车的安全性能具有重要意义。
二、制动主缸的设计1.结构设计汽车制动主缸主要由缸体、活塞和回位弹簧等组成。
缸体是制动主缸的主体,用于存储制动液。
活塞在缸体内运动,将制动液推出,产生制动压力。
回位弹簧用于保证活塞在松开制动踏板后恢复到原始位置。
2.材料选择制动主缸的材料选择对其性能有着重要影响。
缸体通常采用耐高压、耐腐蚀的铝合金或铸铁材料。
活塞则通常采用耐磨、耐高温的材料,如聚酯树脂或不锈钢。
3.性能设计制动主缸的性能设计包括以下几个方面:(1)制动压力:制动主缸产生的制动压力应与驾驶员施加在制动踏板上的力量成线性关系,且压力值应能在短时间内达到最大。
(2)响应时间:制动主缸应在驾驶员踩下制动踏板后迅速产生制动压力,响应时间越短,制动效果越好。
(3)稳定性:制动主缸应能在各种行驶状态下保持稳定的制动压力,避免出现突增或突减的情况。
三、制动主缸的设计优化1.结构设计优化为了提高制动主缸的性能,可以对结构进行优化。
例如,增加活塞的直径可以增加输出压力;缩短活塞与缸体之间的间隙可以减少制动液的泄漏;优化回位弹簧的弹力可以改善活塞的复位速度。
2.材料选择优化针对不同的使用环境和使用要求,可以选择更合适的材料来提高制动主缸的性能。
例如,采用高强度铝合金或铸铁材料可以增加缸体的强度和耐压能力;采用耐磨性更好的材料可以增加活塞的使用寿命。
3.性能设计优化通过对制动主缸进行性能测试和调整,可以优化其性能表现。
例如,调整制动主缸的响应时间和压力曲线可以使其更好地适应不同的行驶状态;优化缸体的流体动力学设计可以减少制动液的流动阻力。
四、结论汽车制动主缸的设计直接影响到汽车的制动性能和安全性能。
(完整版)汽车制动系统毕业设计论文

优秀论文审核通过未经允许切勿外传摘要Formula SAE比赛由美国车辆工程师学会(SAE)于1979年创立,每年在世界各地有600余支大学车队参加各个分站赛,2011年将在中国举办第一届中国大学生方程式赛车,本设计将针对中国赛程规定进行设计。
本说明书主要介绍了大学生方程式赛车制动的设计,首先介绍了汽车制动系统的设计意义、研究现状以及设计目标。
然后对制动系统进行方案论证分析与选择,主要包括制动器形式方案分析、制动驱动机构的机构形式选择、液压分路系统的形式选择和液压制动主缸的设计方案,最后确定方案采用简单人力液压制动双回路前后盘式制动器。
除此之外,还根据已知的汽车相关参数,通过计算得到了制动器主要参数、前后制动力矩分配系数、制动力矩和制动力以及液压制动驱动机构相关参数。
最后对制动性能进行了详细分析。
关键字:制动、盘式制动器、液压AbstractFormula SAE race was founded in 1979 by the American cars institute of Engineers every year more than 600 teams participate in various races around the world,China will will be for design of the provisions of the Chinese calendar.This paper mainly introduces the design of breaking system of the Formula Student.First of all,breaking system's development,structure and category are shown,and according to the structures,virtues and weakness of drum brake and disc brake analysis is done. At last, the plan adopting components braking and channel settings and the analysis of brake performance.Key words:braking,braking disc,)的汽车上。
- 1、下载文档前请自行甄别文档内容的完整性,平台不提供额外的编辑、内容补充、找答案等附加服务。
- 2、"仅部分预览"的文档,不可在线预览部分如存在完整性等问题,可反馈申请退款(可完整预览的文档不适用该条件!)。
- 3、如文档侵犯您的权益,请联系客服反馈,我们会尽快为您处理(人工客服工作时间:9:00-18:30)。
课题名称:汽车制动系统的结构设计与计算 第一章:制动器结构型式即选择 一、汽车已知参数: 汽车轴距(mm):3800 车轮滚动半径(mm):407.5 汽车空载时的总质量(kg):3330 汽车满载时的总质量(kg)6330 空载时,前轴负荷G=mg=12348.24N 后轴负荷为38624.52N 满载时,前轴负荷G=mg=9963.53N 后轴负荷为43157.62N 空载时质心高度为750mm 满载时为930mm 质心距离前轴距离空载时为2.36m 满载时为2.62m
汽车设计课程设计 质心距离后轴距离满载时为1.44m 满载时为1.18m 二、鼓式制动器工作原理 鼓式制动器的工作原理与盘式制动器的工作原理基本相同: 制动蹄压住旋转表面。 这个表面被称作鼓。 许多车的后车轮上装有鼓式制动器,而前车轮上装有盘式制动器。 鼓式制动器具有的元件比盘式制动器的多,而且维修难度更大,但是鼓式制动器的制造成本低,并且易于与紧急制动系统结合。 我们将了解鼓式制动器的工作原理、检查紧急制动器的安装情况并找出鼓式制动器所需的维修类别。 我们将鼓式制动器进行分解,并分别说明各个元件的作用。
图1 鼓式制动器的各个元件 与盘式制动器一样,鼓式制动器也带有两个制动蹄和一个活塞。 但是鼓式制动器还带有一个调节器机构、一个紧急制动机构和大量弹簧。 图2仅显示了提供制动力的元件。 图2. 运行中的鼓式制动器 当您踩下制动踏板时,活塞会推动制动蹄靠紧鼓。 这一点很容易理解,但是为什么需要这些弹簧呢?
这就是鼓式制动器比较复杂的地方。 许多鼓式制动器都是自作用的。 图5中显示,当制动蹄与鼓发生接触时,会出现某种楔入动作,其效果是借助更大的制动力将制动蹄压入鼓中。 楔入动作提供的额外制动力,可让鼓式制动器使用比盘式制动器所用的更小的活塞。 但是,由于存在楔入动作,在松开制动器时,必须使制动蹄脱离鼓。 这就是需要一些弹簧的原因。 其他弹簧有助于将制动蹄固定到位,并在调节臂驱动之后使它返回。 为了让鼓式制动器正常工作,制动蹄必须与鼓靠近,但又不能接触鼓。如果制动蹄与鼓相隔太远(例如,由于制动蹄已磨损),那么活塞需要更多的制动液才能完成这段距离的行程,并且当您使用制动器时,制动踏板会下沉得更靠近地板。 这就是大多数鼓式制动器都带有一个自动调节器的原因。 当衬块磨损时,制动蹄和鼓之间将产生更多的空间。汽车在倒车过程中停止时,会推动制动蹄,使它与鼓靠紧。 当间隙变得足够大时,调节杆会摇动足够的幅度,使调节器齿轮前进一个齿。 调节器上带有像螺栓一样的螺纹,因此它可以在转动时松开一点,并延伸以填充间隙。 每当制动蹄磨损一点时,调节器就会再前进一点,因 此它总是使制动蹄与鼓保持靠近。 一些汽车的调节器在使用紧急制动器时会启动。 如果紧急制动器有很长一段时间没有使用了,则调节器可能无法再进行调整。 因此,如果您的汽车装有这类调节器,一周应至少使用紧急制动器一次。 汽车上的紧急制动器必须使用主制动系统之外的动力源来启动。 鼓式制动器的设计允许简单的线缆启动机构。 鼓式制动器最常见的维修是更换制动蹄。 一些鼓式制动器的背面提供了一个检查孔,可以通过这个孔查看制动蹄上还剩下多少材料。 当摩擦材料已磨损到铆钉只剩下0.8毫米 长时,应更换制动蹄。 如果摩擦材料是与后底板粘合在一起的(不是用铆钉),则当剩余的摩擦材料仅为1.6毫米厚时,应更换制动蹄。
图3. 制动蹄 与盘式制动器中的情况相同,制动鼓中有时会磨损出很深的划痕。 如果磨损完的制动蹄使用时间太长,将摩擦材料固定在后部的铆钉会把鼓磨出凹槽。出现严重划痕的鼓有时可以通过重新打磨来修复。 盘式制动器具有最小允许厚度,而鼓式制动器具有最大允许直径。由于接触面位于鼓内,因此当您从鼓式制动器中去除材料时,直径会变大。
图4. 制动鼓 第二章:制动系的主要参数及其选择 一、制动力及制动力分配系数分析 二、汽车前后车轮同时抱死时的制动力和分配系数
1、制动力(满载) 假设汽车的同步附着系数为0=0.8.
在前后车轮均被抱死时,q=0=0.8,这时前后轴车轮的制动器制动力1fF、2fF即是理想最大制动力,此时BF、fF和F相等,所以有:(BF为汽车总的地面制动力,fF为汽车总的制动器制动力,F车轮与路面总的附着力) L=3.8M L1=2.62M L2=1.18M Hg=0.93M
11200()BfgGFFFLhL=
24891.2N
22100()BfgGFFFLhL=24786.628N
2、制动力分配系数与同步附着系数 假设汽车的同步附着系数为0=0.8.
则制动力分配系数0ghbL=0.5 3、制动强度和附着系数利用率 取该车所能遇到的最大附着系数为max=1,从保证汽车制动时的稳定性出发来确定各轴的最大制动力矩。=1时,后轴先抱死,当后轴刚要抱死时,可推出得: 110()Bg
GLFLh
=66.8039KN
110()g
LqLh
=0.9342
110()g
L
Lh=1.871.87(10.8)*0.886=0.9342
4、最大制动力矩 对于选取较大0值的汽车,这类车辆经常行驶在良好道路上,车速较高,后轮制动抱死失去稳定而出现甩尾的危险性较前一类汽车大得多。因此应从保证汽车制动时的稳定性出 发,来确定各轴的最大制动力矩。 2max12800*9.81()*(1.870.9134*0.886)*1*0.352.8fgeGTLqhrL
=10100.5NM 1max2max0.585*5403.08110.585ffTT=10143.2NM
5、制动器因数 领蹄的制动蹄因数
11NfhfBFcPbfb
2.6
从蹄的制动蹄因数为
11NfhfBFcPbfb
2.6
6、鼓式制动器主要结构参数 ○1、车轮的滚动半径为r=407.5mm,通过中华人民共和国国标,载重汽车标准,轮辋直径为d=16in=406.4mm 制动鼓直径D,通过查表得D/Dr=0.787 D=d*78.7%=406.4*0.787=320mm 取D=300mm 制动间隙取0.3mm.
○2、制动蹄摩擦片包角β宽度b和单个制动器摩擦衬片总面积,取β=90°A=400 2cm(前轴制动器) A=4002cm(后轴制动器)
b=AR=16.98cm(前轮制动器摩擦片宽度)
b=AR==16.98cm(后轮制动器摩擦片宽度) ○3、摩擦衬块起始角β。 β。=β/2=45° ○4、制动器中心张开到张开力F。作用线的距离e e=0.8R=0.8*15=12cm ○5、制动器距支撑点位置坐标a与c a=0.8R=0.8*15=12cm 两支承销之间距离k=1.5cm
第三章:鼓式制动器设计计算 一、制动蹄片上的制动力矩
前轴单个制动器应能产生的最大制动力矩: fT1max/2fT
5071NM
单个蹄片上的制动力矩 11111111cossinTfTPfhcffPB
……………○1
12222222cossinTfTPfhcffPB
.....……….○2
arctanarctancos2cos2/2sin2sin2XYNN
…………………………………………………………….…○3
2214coscos/cos2cos22sin2sin2R
…………………………………………………………….….○4 121122fTfTfTTTPBPB…………….……….○5
:对于液压驱动的制动器,由于12PP,故所需要的张开力为 12/fPTBB
…………………………………………….○6
由上图可得参数数据:R=159.65mm,c′=131.4686
0=13.19°,β=90°,= 31.81°,=121.81°,f=0.35
fT7955.64NM
将参数带入○1○2○3○4○5○6计算得: 10.115°,2
0.5°10.22025,20.22025
10.0009268B,20.002693B
带入.○6式得P=2197.8KN