加氢装置常见腐蚀
加氢装置设备常见腐蚀分析及防护措施

加氢装置设备常见腐蚀分析及防护措施摘要:本文简要介绍了对于高硫油的加氢装置中设备常见的腐蚀,初步分析了腐蚀产生的机理并介绍了一些防腐措施。
关键词:加氢装置腐蚀防护措施1、前言加氢是当今石油化工领域中处理高硫油的主要途径和方式。
随着国内炼油企业炼制进口高硫油的比例越来越大,新建的加氢装置也随之增多。
各类加氢装置中尤以加氢裂化和渣油加氢装置的操作条件最为苛刻,反应器操作压力近20MPa,反应温度也在400℃以上。
因此要搞好设备管理,必须对加氢的腐蚀状况及相应防护措施有一个全面的了解,对腐蚀做到早认识、早管理、早防护,不应有因腐蚀引起影响安全生产的事故发生。
现就加氢装置中一些常见的设备腐蚀原因及防护措施作一浅析。
2、加氢装置常见的腐蚀形态2.1、氢的腐蚀加氢装置中设备不可避免地要处于氢的环境中,氢分子既小又活波,再加上高温高压的操作条件,因此氢很容易渗入缸中并于钢种的成分发生反应。
氢的腐蚀可以分为两类:高温氢腐蚀和氢脆。
(1)高温氢腐蚀。
表现为两种形式:一是表面脱碳,二是内部脱碳和开裂。
以后一种的影响较大。
内部脱碳是由于氢扩散到钢中发生反应生产甲烷,即:Fe3C+2H2→CH4+3Fe。
甲烷在钢中的扩散能力很小,聚集于晶界空隙附近,形成局部高压,造成应力集中,使刚才产生龟裂、裂纹或鼓泡,导致刚才的强度和韧性显著下降。
这种腐蚀是不可逆现象,也称永久脆化现象。
(2)氢脆。
所谓氢脆是由于氢残留于钢中所引起的脆化现象,即原子氢在高温高压状态下侵入钢中,使钢材晶体的原子结合力变弱,或者成为氢分子在晶界或夹杂物周边析出。
产生氢脆的钢材其延伸率和断面收缩率都显著下降。
氢脆的发生一般是在发生氢渗入后恢复到150℃以下时发生。
如果在此温度上某一温度区间恒温一段时间析氢,则可以使氢较彻底的释放出来,钢材的力学性能仍可恢复,因此,氢脆是可逆的。
2.2、硫化氢的腐蚀在加氢装置中,由于原料中含有大量的硫,因此会有很多的H2S腐蚀介质生产。
加氢装置设备的腐蚀与选材
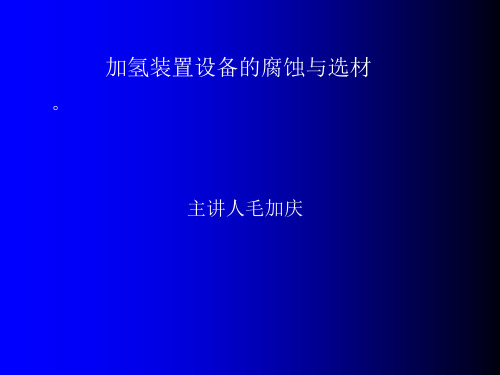
4、应力腐蚀 金属的应力腐蚀是指在静拉伸应力和 腐蚀介质的共同作用下导致腐蚀开裂的现象。特点是 这种应力腐蚀破坏没有先兆,进展迅速的突然断裂。 容易造成严重事故。 金属材料发生应力腐蚀的特征可 用几个方面来说明: 1)应力 可以是外加载荷和装配应力,也可以是加 工、焊接等过程的内应力。 2)腐蚀介质 产生应力腐蚀的材料和介质有一定的 关系,只有二者的某种组合时才发生应力腐蚀。如 普 通碳钢和低合金钢在氢氧化物溶液、含有硝酸盐、碳 酸盐、硫化氢的水溶液、液氨等介质中;奥氏体钢在 酸性和中性的氯化物溶液、海水、热的氢氧化物等溶 液中会发生应力腐蚀。
微观电池 是指金属表面存在着许多肉眼无法分辨 的、微小的电极构成的腐蚀电池。这主要 是由于工 业用金属材料表面存在着电化学不均一性造成的。 常见的有以下几种。一是金属的化学成分不纯或合 金化学成分不均匀。二是组织结构的不均一性。例 如金属结晶的各向异性、位错、晶格空位以及存在 着晶粒的晶界等。三是受力上的不均匀。金属材料 变形较大的部位及存在应力集中的部位电极电位较 低,易腐蚀。例如材料的弯曲变形处、焊缝热影响 区和胀接处等较易发生腐蚀。四是金属表面膜的不 完整性
2) 氢腐蚀 钢受到高温高压氢的作用后,钢中的碳与渗入钢中 的氢原子反应生成甲烷,使其强度韧性明显降低。这 种现象叫氢腐蚀。(1937年Numann提出) Fe3C+4H C + 2H2 3Fe+CH4 CH4,,C +4H 或者是 CH4,
这种腐蚀是不可逆的。大多数氢腐蚀常伴有脱碳现 象。氢腐蚀过程生成的甲烷气体,在晶界会形成较大 的压力使钢形成裂纹,又由于渗碳体分解、脱碳,钢 的强度降低性能变坏。 氢腐蚀有三个阶段。孕育阶段、性能变化阶段和最 后阶段。
c 操作温度 介质温度对钢材的影响很大,在大多数 情况下,它比氢分压的影响大。大约以200℃为界, 介质温度低于此值时,钢材一般不发生明显的腐蚀现 象。高于此值钢材的腐蚀程度随介质温度的升高而逐 渐加重。所以在选材时要合理的确定设备的操作温度。 d 钢材的化学成分的影响 从腐蚀机理来看氢腐蚀是 由于扩散入钢中的氢与钢的碳元素作用形成甲烷所致。 为此为了提高抗腐蚀能力应该添加一些能与碳形成 稳定碳化物的元素,如Cr、M、W、V、Ti、Nb。这些 元素能与碳形成稳定的碳化物,而不会生成甲烷气体。
加氢裂化装置的腐蚀与防护

加氢裂化装置的腐蚀与防护加氢裂化是炼油厂重要的二次加工手段,可以获得高质量的轻质燃料油。
其特点是对原料适应性强,可加工直镭重柴油、催化裂化循环油、焦化镭出油,甚至可以用脱沥青重残油生产汽油、航煤、和低凝点柴油。
其次,生产方案灵活,可根据不同的季节改变生产方案,并且产品质量好,产品收率高。
加氢裂化操作条件:温度380-450°C,操作压力8-20Mpa,采用的催化剂含有Pt、Pd、W、Mo、Ni、Co等金属氧化物作为加氢组分,以硅酸铝、氟化氧化铝或结晶硅铝酸盐为载体。
原料油经加氢、裂化、异构化等反应转化为轻油产品,收率一般可达100%(体积),可以获得优质重整原料、高辛烷值汽油、航煤、和低凝点柴油,同时产品含硫、氮、烯坯低,安定性好。
加工含酸、高酸原油主要对原料油进料系统有严重影响,加氢反应器也应选择防护措施。
6.1腐蚀形态6.1.1氢损伤高温高压条件下扩散在钢中的氢与钢中不稳定的碳反应生成甲烷,可引起钢的内部脱碳,甲烷不能从钢中逸出,聚集在晶界及其附近的空隙、夹杂物等不连续处,压力不断升高,形成微小裂纹和鼓泡,钢材的延展性、韧性等显著降低,随之变成较大的裂纹,致使钢最终破坏。
因为路铝钢具有良好的高温力学性能和抗氢损伤性能,近年来加氢反应器大多选用2.25CrlMo 钢制造。
6.1.2堆焊层氢致开裂在高温高压的氢气氛中,氢气扩散侵入钢材,当反应器停工冷却过程中,温度降至150°C以下时,由于氢气来不及向外释放,钢中吸藏了一定量的氢,这样在一定条件下就有可能发生开裂。
裂纹的产生和钢中的氢气含量有很大关系,曾经有实验证明,停工7个月后的加氢反应器,堆焊层仍有29ppm的氢含量,在堆焊层上取样进行弯曲实验,弯曲角度在19-750范围内试样就发生了开裂,取试样进行脱氢处理后,试样中氢含量降到1.2ppm,试样弯曲到1800也没有发生开裂。
实验证明了氢脆的危害性,同时也证明了氢脆是可逆的。
加氢装置腐蚀类型及选材要点

加氢装置腐蚀类型及选材要点加氢裂化装置存在的主要腐蚀类型主要有:氢损伤(包括高温氢腐蚀、氢脆、氢致剥离)、高温H2+H2S腐蚀、连多硫酸腐蚀、Cr-Mo钢的回火脆性、高温S腐蚀、低温部位的H2S+H2O腐蚀、H2S+NH3 +H2O腐蚀。
1.氢损伤【定义】由于氢原子扩散进入金属本体或与金属反应引起金属材料性能的破坏称为氢损伤。
【部位】氢损伤发生的主要部位在:高温、高压氢气环境下的反应系统设备和管线。
【分类】氢损伤主要可以分为:氢脆、高温氢腐蚀和氢致剥离。
(1)氢脆【定义】钢在临氢条件下使用,氢以原子状态扩散浸入晶格内、又以分子状态聚集于晶界或非金属夹渣物周围。
【特征】物理过程,可逆的,称为一次脆化现象。
材料的抗拉强度或硬度没有特别大的变化,但是在常温条件下材料的缺口强度或韧性降低,有时还产生裂纹。
受到氢脆的材料经过脱氢处理后,如果没有产生裂纹,其延性和韧性都能得到恢复。
(2)高温氢腐蚀【定义】氢在高温(T>220℃)高压下与合金中的夹杂物(碳合物F3C或固溶碳C)或合金添加物(如Si)发生化学反应,生成高压气体。
从而导致钢材产生脱碳和结晶界裂纹。
受到高温氢腐蚀的材料的抗拉强度和延性、韧性显著降低。
【特征】高温氢腐蚀与氢脆性质完全不同,它是化学反应过程,具有不可逆性,称为永久脆化现象。
高温氢腐蚀主要有2种形式:一是表面脱碳;一是内部脱碳。
钢材与氢接触后可产生表面脱碳。
表面脱碳不会产生裂纹,但材料的强度和硬度稍有下降,而延伸率增加。
发生的主要反应有:Fe3C+2H2→CH4+3Fe。
这一反应一般从钢的表面开始,逐渐向内部推进,生成的甲烷气体不易逸出,他们聚集在晶界或杂质周围,形成的局部压力可高达几千大气压以上,因此,不仅钢的表面和里层脱碳脆化,而且还发展为严重的鼓泡开裂。
钢中的固溶的碳也会与钢中溶解的氢反应:C+4H→CH4;Si+4H→SiH4。
高温氢腐蚀的特点是要经过一个潜伏期,根据材料和环境条件的不同,潜伏期短可几个小时,长则数年。
设备腐蚀类型
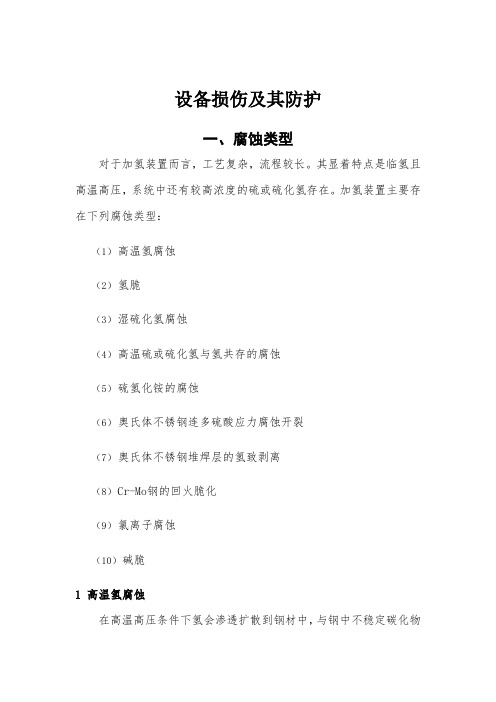
设备损伤及其防护一、腐蚀类型对于加氢装置而言,工艺复杂,流程较长。
其显着特点是临氢且高温高压,系统中还有较高浓度的硫或硫化氢存在。
加氢装置主要存在下列腐蚀类型:(1)高温氢腐蚀(2)氢脆(3)湿硫化氢腐蚀(4)高温硫或硫化氢与氢共存的腐蚀(5)硫氢化铵的腐蚀(6)奥氏体不锈钢连多硫酸应力腐蚀开裂(7)奥氏体不锈钢堆焊层的氢致剥离(8)Cr-Mo钢的回火脆化(9)氯离子腐蚀(10)碱脆1 高温氢腐蚀在高温高压条件下氢会渗透扩散到钢材中,与钢中不稳定碳化物的碳发生化学反应生成甲烷,甲烷不能逸出钢外,而是在晶间空穴和非金属夹杂物部位聚集,使钢材鼓泡、裂纹,并引起钢的强度、延伸性和韧性下降与劣化,还伴有晶间断裂。
一旦发生破坏,后果严重,这是加氢装置首先要考虑的问题。
反应部分包括加热炉、反应器、热低分、反应物流换热器及管道都有发生高温氢腐蚀的可能,必须选用能抵抗相应使用条件下高温氢腐蚀的材料。
通常是根据美国石油学会推荐惯例(API941)“炼油厂和石油化工厂高温高压临氢作业用钢”(亦称纳尔逊曲线)来选择。
且可根据使用情况与经验考虑一定的安全裕量。
根据本装置工艺过程的最高氢分压,其钢的使用极限温度不应超过 454℃;钢不应超过330℃。
操作中应严防异常超温,另外,使用过程的维修中,如果有补焊时,必须进行焊后热处理。
2 氢脆氢脆是由氢本身引起的钢材脆化现象,氢原子渗入钢材之后,使钢材中的原子结合里降低,因而造成钢材的延伸率、断面收缩率、冲击韧性显着下降。
但这种脆性是可逆的,一旦将氢从钢中脱出,钢材的力学性能就能恢复。
低温氢开裂的敏感和钢的强度值,氢含量以及容器内所处部位的应力有关。
决定钢抗氢脆最重要的因素是钢的强度值,钢材开裂敏感性随着强度的增加而提高。
高强度钢的氢脆开裂可能在大约150℃以下出现。
氢与钢材直接接触时被钢材吸附,并以原子状态向钢材内部扩散,溶解在铁素体中形成固溶体,使钢材边脆,塑性减小,这种脆性与氢在钢中的溶解度成正比。
加氢裂化装置腐蚀分析和防腐对策

化工设备中,由于原油含量的增加,加氢裂化装置的腐蚀加剧,给安全生产带来了很大的隐患,必须对其进行根本的分析,并采取相应的防护措施。
对加氢裂化装置的氢损伤,硫化氢腐蚀,碳钢的回火脆性,铵盐腐蚀,奥氏体不锈钢的磨蚀和过多硫酸应力腐蚀进行了分析。
一、氢损伤及其防护氢的损失主要是高温氢损、氢脆和奥氏体不锈钢堆焊层的脱氢。
高温度氢气腐蚀是指钢中晶间碳化物中的氢气进入高温反应生成甲烷的内部脱碳。
也就是说:Fe3C+2H2=CH4+3 Fe。
具体表现为非金属夹杂位置和晶间空间,产生局部高压,形成应力集中,导致钢件开裂等,使钢件强度、韧性下降,导致晶件断裂。
为了防止高温氢气腐蚀,工艺必须严格按要求进行,不能出现“飞温”,操作平稳,反应器停机温度不低于135 C。
氢的脆性主要是由于钢中氢的释放,一般低于150°C是由于氢的渗入所致,如果在一定的温度范围内恒温一段时间,氢就会释放出来,使钢的力学性能逐渐恢复。
增大法兰密封槽底接半径,可实现氢脆防护,并可避免法兰密封槽底面开裂。
FCC的反应器在启动运行时,首先要把温度提高到一定程度再升压,如果工作停止,则应先降低压力,再降低温度,杜绝直接停机运行和异常升温。
锚杆的上紧力应严格控制,避免因上紧力分布不均而造成法兰和锚杆过压。
氢气在高温条件下会进入奥氏体不锈钢堆焊层,从正常状态到停堆,反应器过热时,母材的氢气溶解性和扩散速度与堆焊层不同,由于氢气温度下降,分压降低,过热形成的氢分子的压力大于过热生成的氢,导致剥离。
保护堆焊层的主要措施是选择碳-碳-钛合金加焊材料,以提高堆焊抗剥落能力。
采用大电流高速焊接,同时进行焊接,避免产生粗晶。
在生产实践中要保证生产的平稳性,避免过热现象,避免紧急泄压和快速冷却。
二、硫化氢腐蚀及其防腐H2S和H2是硫化氢的两种主要腐蚀类型,高温H2S和高温H2是两种不同类型。
湿态H2S腐蚀主要是硫化氢与液相水共存时产生的腐蚀,对其防护主要是从材料上,湿态H2S环境下的管道和设备优先选用镇静钢,如无CN系统可进行中和处理操作,使其PH值呈碱性,还可将缓蚀剂注入低温系统。
柴油加氢装置的腐蚀与防护分析

柴油加氢装置的腐蚀与防护分析摘要:我国社会经济不断发展,也不断增加了能源消耗情况,因为能源劣质化问题,不断提高了原油中硫、酸的成本含量,导致柴油加氢装置发生腐蚀问题。
本文分析了柴油加氢装置的腐蚀问题,提出针对性的防护措施。
关键词:柴油;加氢装置;腐蚀问题;防护措施当前我国能源劣质化问题比较严重,不断提升原油中的硫、酸成分,引发腐蚀问题。
柴油加氢装置在工作过程中存在高温高压特征,因此很容易发生物质腐蚀问题。
柴油加氢装置反应阶段会产生H2S,危害柴油加氢装置的安全性。
为了维持柴油加氢装置运行安全性,需要利用针对性措施解决腐蚀问题。
一、概述柴油加氢装置的腐蚀介质H2S属于已自动酸性气体,H2S发生腐蚀问题包括高温腐蚀和低温腐蚀,高温腐蚀的温度在240℃以上,H2S通过分解会形成单质硫,和设备金属发生反应之后,会破坏柴油加氢装置。
在低温腐蚀过程中,H2S在溶解过程中产生氢离子,从而腐蚀金属。
柴油加氢装置经常会发生低温腐蚀问题,导致设备氢脆开裂问题。
【1】O通常无法和水溶解,因此O分布范围比较广泛,在常温下O并不是活跃度,高温状态下,O比较活跃,和各种元素发生化学反应。
在高温条件下,O和金属之间发生反应从而引发氧化腐蚀问题。
游离的H2SXO6缺乏稳定性,在高温状态下,可以分解出硫和二氧化硫等物质,导致柴油加氢装置发生腐蚀问题。
因为氢气具有较小的密度,因此质量比较轻,在高温状态下,氢气会进入到大分子间隙当中,因此引发氢脆问题。
二、柴油加氢装置腐蚀原因调查设备腐蚀问题,根据发生腐蚀问题的设备管道,采取针对性的治理对策,保障防腐蚀效果。
在反应器中操作温度在390℃以上,在操作压力的影响下,可以保障设备整体工作效果,但是在封头部位发生明显的腐蚀问题。
堆焊层出现脱落的问题,分配器和格栅也出现腐蚀问题。
【2】高温腐蚀的问题非常严重,检查脱硫化氢汽提塔和循环氢脱硫塔的腐蚀问题,其中循环氢脱硫塔的操作温度达到50℃以上,发生腐蚀问题的主要原因是因为酸性气体产生腐蚀介质,释放酸性气体会冲蚀设备,引发腐蚀开裂问题。
柴油加氢装置腐蚀与防护对策研究

柴油加氢装置腐蚀与防护对策研究随着我国社会经济的不断向前发展,对能源的消耗量正在不断上升,柴油加氢装置在使用过程中经常会出现各种腐蚀问题,影响到了装置使用的安全性。
基于此,本文重点针对柴油加氢装置的腐蚀问题展开了分析和研究,同时提出了相应的防腐蚀工作对策,有效保证柴油加氢装置的工作质量。
标签:柴油加氢;腐蚀;防护在人们的日常生活当中,对柴油资源的使用量相对较高,柴油质量的高低直接关系到了燃烧性能以及对环境的污染程度,同时柴油当中含有大量的硫元素,经过一系列反应之后,会对加氢装置形成一定的腐蚀问题,造成了装置出现泄漏或者是损坏等。
在柴油的加氢装置反应过程中,需要在高温高压的环境下进行工作,因此这一环境会加剧材料的腐蚀问题。
除此之外,柴油加氢装置在工作过程中会生成一定量的硫化氢,硫化氢会对柴油加氢装置的表壁形成更加严重的腐蚀,影響到了整个设备的运行安全性。
因此,必须要对柴油加氢装置的腐蚀问题加以关注,提出针对性的防控方法来加以保障。
1.柴油加氢中的腐蚀介质1.1低温腐蚀氯化氢气体属于一种无色易燃的酸性气体,硫化氢在低浓度环境下会伴随着恶臭性,并且具有一定的毒性。
硫化氢产生腐蚀问题可以分为高温腐蚀和低温腐蚀两种类型,所谓的高温腐蚀问题主要指的是在240℃以上的状态,硫化氢气体会分解成单质硫,单质硫和加氢装置内部的某些金属发生一系列反应,进而形成了腐蚀破坏问题。
所谓的低温腐蚀问题主要指的是在低温工作状态下,硫化氢直接溶解在水体当中,然后电离反应生成大量的氢离子也会对加氢装置的表面形成一定的腐蚀作用。
通常情况下低温腐蚀的现象非常普遍,对加氢装置的危害更加明显,严重的情况下会直接造成加氢装置出现脆性开裂问题。
柴油加氢装置也会受到氧元素的影响,由于氧气在空气当中分布非常广泛,但是它不易溶于水,在常温的状态下表现不是非常活跃,但是如果氧气在高温高压的环境下则表现非常活跃,可以和很多的元素之间形成一系列化学反应,进而会对加氢装置形成一定的化学腐蚀问题。
- 1、下载文档前请自行甄别文档内容的完整性,平台不提供额外的编辑、内容补充、找答案等附加服务。
- 2、"仅部分预览"的文档,不可在线预览部分如存在完整性等问题,可反馈申请退款(可完整预览的文档不适用该条件!)。
- 3、如文档侵犯您的权益,请联系客服反馈,我们会尽快为您处理(人工客服工作时间:9:00-18:30)。
加氢装置常见的腐蚀1. 氢腐蚀氢腐蚀是在高温高压条件下,分子氢发生部分分解而变成原子氢或离子氢,并通过金属晶格和晶界向钢中扩散,扩散侵入钢中的氢与不稳定的碳化物发生化学反应,生成甲烷气泡(它包含甲烷的成核过程和成长),即Fe3C+2H2→CH4+Fe,并在晶间空穴和非金属夹杂部位聚集,而甲烷在钢中的扩散能力很小,聚积在晶界原有的微观孔隙(或亚微观孔隙)内,形成局部高压,造成应力集中,使晶界变宽,并发展成为裂纹,开始时是很微小的,但到后期,无数裂纹相连,引起钢的强度、延性和韧性下降与同时发生晶间断裂。
由于这种脆化现象是发生化学反应的结果,所以他具有不可逆的性质,也称永久脆化现象。
在高温高压氢气中操作的设备所发生的氢腐蚀有两种形式:一是表面脱碳,二是内部脱碳。
表面脱碳不产生裂纹,这点与钢材暴露在空气、氧气或二氧化碳等一些气体所产生的脱碳相似,表面脱碳的影响一般很清,其钢材的强度和硬度局部有所下降而延性有所提高。
内部脱碳是由于氢扩散侵入到钢中发生反应生成甲烷,而甲烷又不能扩散到钢外,就聚集于晶界或夹杂物附近。
形成了很高的局部应力,使钢产生龟裂、裂纹或鼓包,其力学性能发生了显化。
造成氢腐蚀的因素:1 操作温度、氢的分压和接触时间。
温度越高或者压力越大发生高温氢腐蚀的起始时间越早。
氢分压8.0MPa是个分界线,低于此值影响比较缓和,高于此值影响比较明显,操作温度200℃是个临界点,高于此温度钢材氢腐蚀程度随介质的温度升高而逐渐加重。
氢在钢中的话浓度可以用下面公式表示:C=134.9P1/2exp(-3280/T)式中:C-氢浓度P——氢分压,MPaT-温度,K从式中可看出,温度对钢中氢浓度的影响比系统氢分压更显著。
2 钢材中合金元素的添加情况。
在钢中不能形成稳定碳化物的元素(如镍、铜)对改善钢的抗氢腐蚀的性能毫无作用;而在钢中添加形成很稳定碳化物的元素(入铬、钼、钒、钛、钨等),就可以使碳的活性降低,从而提高钢材抗氢腐蚀的能力。
关于杂质的影响,在针对2.25Cr-1Mo刚的研究已发现,锡、锑会增加甲烷气泡的密度、大小和生成速率。
3 加工过程。
钢的抗氢腐蚀性能与钢的显微组织也有密切关系。
回火过程对钢的氢腐蚀性能也有影响。
对于淬火状态,只需很短时间加热就出现了氢腐蚀。
但是一施行回火,且回火温度越高,由于可形成稳定的碳化物,抗氢腐蚀性能就得到改善,另外对于在氢环境下使用的铬钼钢设备,施行焊后热处理同样具有提高抗氢腐蚀能力的效果。
曾有试试验证明,2.25Cr-1Mo钢焊缝若不进行热处理的话,则发生氢腐蚀的温度将比纳尔逊(Nelson)曲线表示的温度低100℃以上。
4 钢材受的热应力。
在高温氢气中蠕变强度会下降,特别是由于二次应力(如热应力或由冷加工所引起的应力)的存在会加速高温氢腐蚀。
当没有变形时,钢材具有较长的“孕育期”,随着冷变形量增大,“孕育期”逐渐缩短,当变形量达到39%时,则在任何试验条件下都无“孕育期”,只要暴露在此条件的氢气中,裂纹立刻就发生。
因此对于临氢压力容器的受压元件,应重视采用热处理消除残余应力;5 不锈钢复合层和堆焊层的影响,由于氢在奥氏体不锈钢以及铁素体钢中的溶解度和扩散系数不同,因此完整冶金结合的奥氏体不锈钢复合层和堆焊层能降低作用在目材中的氢分压。
如何防止氢腐蚀:1 采用内保温、降低筒壁温度;2 采用耐氢腐蚀的钢板做反应器筒体;3 采用抗氢腐蚀的衬里(如0Cr13、1Cr18Ni9Ti等)4 采用多层式结构,可在壁上开排气孔及特殊的集气层,将内筒渗过来的氢气集中起来排走。
5 采用催化剂内衬筒式反应器,新氢走环形空间,使筒壁降温。
6 在实际应用中,对于一台设备来说,焊缝部位的氢腐蚀更不可忽视。
因为通常焊接接头的抗氢腐蚀性能不如目材,特别是热影响区的粗晶区附近更显薄弱应引起重视。
2. 氢腐蚀潜伏期在高温高压氢的作用下,钢材的破坏往往不是突出发生的,而是经历一个过程,在这个过程中,钢材的机械性能并无明显变化,这一过程就称为潜伏期或孕育期。
潜伏期的长短与钢材的类型和暴露条件有关.条件苛刻,潜伏期就短,甚至几小时就破坏.在高温压力比较低的条件下,潜伏期可能就长一些.知道钢材的氢腐蚀潜伏期后,对掌握设备的安全运转时间有很重要的意义。
3. 氢致裂纹氢致裂纹也称诱导裂纹。
这是由于反应器在高温高压的氢气中操作时氢气扩散侵入钢中,当反应器在停工冷却过程中,由于冷却速度太快,氢来不及从钢中向外释放,钢内就会吸藏了一定的氢,严重的拉伸延性损失就会导致裂纹引发。
在操作中,当装置停工时,宜采用能使氢较彻底释放出的停工方案。
例如停工时降温速度不能过大,并在较高的温度下(大于350℃)保持一段较长的时间。
4. 氢脆所谓氢脆,就是由于氢残留在钢中所引起的脆化现象。
产生了氢脆的钢材,其延伸率和断面收缩率显著下降。
这是由于侵入钢中的原子氢,使结晶的原子结合力变弱,或者作为分子状态在晶体或杂物周边上析出的结果。
但是,在一定的条件下,若能使氢较彻底释放出来,钢材的力学性能仍可得恢复。
这一特性与氢蚀截然不同,所以氢脆是可逆的,也称作一次性脆化现象。
对于操作在高温高压环境下的时设备,在操作状态下,器壁会吸收一定量的氢。
在停工过程中,冷却速度太快,使在温度低于150℃引起亚临界裂纹扩展,对设备的安全使用带来威胁。
防止氢脆的对策:1 尽量减少应变幅度,这对于改善使用寿命很有帮助。
采取降低热应力和避免应力集中等措施都是有效的。
2 尽量保持堆焊金属有较高的延性。
3 装置在停工时降温速度不宜过快,且停工过程中应有使钢材中吸收的氢尽量释放出来的过程(分阶段恒温脱氢,一般在260~427℃之间),以减少器壁中的残留氢含量。
另外,尽量避免非计划停工(紧急放空)也是非常重要的。
因为此情况下器壁中的残留氢浓度会很高。
5. 应力腐蚀所谓应力就是作用在单位面积上的内力值,垂直于横截面上的应力称为正应力,平行于横截面的应力称为剪应力。
金属材料在静拉应力和腐蚀介质同时作用下,所引起的破坏作用,称为应力腐蚀。
产生腐蚀应力的原因,首先是由于内应力使钢材增加了内能,处于应力状态下的钢材的钢材稳定性必然会下降,从而降低了电极电位,内应力愈大,化学稳定性愈差,电极电位愈低。
所以,应力大的区域成为阳极,其次应力(特别是表示拉应力)破坏了金属表面的保护膜,保护膜破坏后形成裂缝,裂缝就成为阳极,其他无应力区域成为阴极,成为腐蚀电池,加速腐蚀。
奥氏体不锈钢对应力腐蚀是比较敏感的,较易发生,这可能是和他比较容易产生滑移即孪晶有关。
由于滑移带和孪晶界应力集中,易遭受腐蚀破坏,裂纹一般都是穿晶的,也有在晶间发生的,由于这种应力腐蚀所产生的裂纹呈刀口状,所以成为“刀口腐蚀”。
奥氏体不锈钢形成刀口腐蚀的原因,除了焊缝有不均匀的的应力外,还由于焊缝在焊接后的冷却过程中,从奥氏体中析出了铬的碳化物,使晶界贫铬,刀口腐蚀就发生在焊缝区或热影响区里,而热影响区内的某一段的温度很可能就是奥氏体的贫铬的碳化物出的敏化温度(450~850℃),这样就使得晶界贫铬,发生晶界裂纹。
防止应力腐蚀的方法:1 利用热处理消除焊接和冷加工的残余应力,以及进行稳定化和固溶处理;2 采用超低碳(小于0.03%)不锈钢或用含铌、钛稳定的不锈钢,焊接时用超低碳或含铌的焊条进行焊接。
6. 奥氏体不锈钢的连多硫酸腐蚀机理连多硫酸应力腐蚀开裂的特征应力腐蚀开裂是某一金属(钢材)在拉应力和特定的腐蚀介质共同作用下所发生的脆性开裂现象。
奥氏体不锈钢对于硫化物应力腐蚀开裂是比较敏感的。
连多硫酸(H2SxO6,x=3~6)引起的应力腐蚀开裂也属于硫化物应力腐蚀开裂,一般为晶间裂纹。
当炼油装置停工过程中,系统降温降压后,有水气被冷凝下来或打开设备检修时,设备和管线内部与湿空气接触。
铁/铬硫化物于氺和氧发生化学反应,就有亚硫酸和连多硫酸生产,从而产生腐蚀。
在石化工业装置中,奥氏体不锈钢或管道发生硫化物应力腐蚀开裂多有见到。
连多硫酸应力腐蚀开裂在加氢装置中也都发生过。
防止奥氏体不锈钢产生连多硫酸腐蚀最好采取以下几点措施:1 材质一般采用超低碳型(C≦0.03%)或稳定性的不锈钢(SUS321,SUS347),采用奥氏体+铁素体双相不锈钢也有较好的效果,它对连多硫酸应力发生开裂不敏感。
制造上要尽量消除或减轻由于冷加工或焊接引起的残余应力,并注意加工成不形成应力集中或尽可能小的结构。
2 使奥氏体不锈钢设备或管线的金属表面保持干燥,即不与空气和水基础或处于热状态下。
即装置停工后,对不需检修的奥氏体不锈钢设备或管线用阀门或盲板封闭起来,内充氮气保持正压,使其隔绝空气。
如果温度低于38℃会生产液态水时,则要将无水氨注入系统内,浓度大约5000PPm,特别是加热炉管,在停工检修时,保持其温度在149℃以上,使其干燥。
3 对于需要检修的奥氏体不锈钢设备,管线和不能保持149℃以上的加热炉管,应用1.5~2%的碳酸钠或氢氧化钠溶液进行中和冲洗。
冲洗后,务必用不含氯化物的除盐水冲洗,以防止残留碱留在表面上造成碱脆和在开工时被带到催化剂上,影响活性。
在溶液中增加0.5%的硝酸钠,可以减少不锈钢发生氯化物应力腐蚀开裂的可能性,但必须防止溶液中加入过量的硝酸钠(不大于0.5%),它有引起碳钢应力腐蚀开裂的危险。
4 尽可能减少奥氏体不锈钢金属表面裸露在可能产生应力腐蚀的环境中的时间。
总之每次停工前都要根据停工时间的不同,编制具体的奥氏体不锈钢防护的具体措施,并经设备、工艺、生产和检修审查批准。
7. 奥氏体不锈钢发生的其它类型应力腐蚀奥氏体不锈钢除了在含硫化合物中会产生应力腐蚀外,在含氧化合物和含烧碱的环境中也有产生应力腐蚀的可能性。
应避免由于进行中和清洗而引起的其他应力腐蚀。
奥氏体不锈钢对氯化物的敏感性与氯化物的浓度和温度成正比。
在正常的停工期间,一般不会产生氯化物应力腐蚀裂纹,但在高温状态下,由于氯化物的浓缩,就可能产生腐蚀裂纹,穿晶裂纹和两者都有的裂纹。
8. 氯离子(Cl-)对18-8型奥氏体不锈钢的危害在有“Cl-”存在时,18-8型奥氏体不锈钢对点腐蚀特别敏感。
点腐蚀在在生产中是很危险的,它在一定区域内迅速发展,并往深处穿透,以至造成设备因局部地区破坏而损坏。
或因个别地方穿孔而进行渗漏。
产生点腐蚀的原因,可能是不锈钢表面钝化膜(氧化膜)有个别地方是薄弱的,有可能是局部地方有夹杂或不平整所造成。
当液体中有活性(Cl-)时,也很容易被表面钝化膜所吸附,在钝化膜比较薄弱的局部地区,氯离子在表面排挤氧原子,并取代氧原子的位置,取代之后,在吸附时“Cl-”的点上就产生可溶性的氯化物,这样就在此地方逐渐形成小孔。
形成小孔后,造成了不利的局面,,即小孔为阳极,被钝化表面为的阴极,阴极面积大而阳极面积小,这样构成的腐蚀电池,将大大加速腐蚀速度,点腐蚀的坑穴多了相连起来,则形成裂纹,造成钢材恶性破坏,为了避免氯离子对奥氏体不锈钢的腐蚀,对奥氏体不锈钢设备及管线清洗或试压,所用的水中氯化物含量要求小于30μg/g。