真空自耗电弧炉熔炼钛铸锭的质量控制
铸造生产过程的质量控制
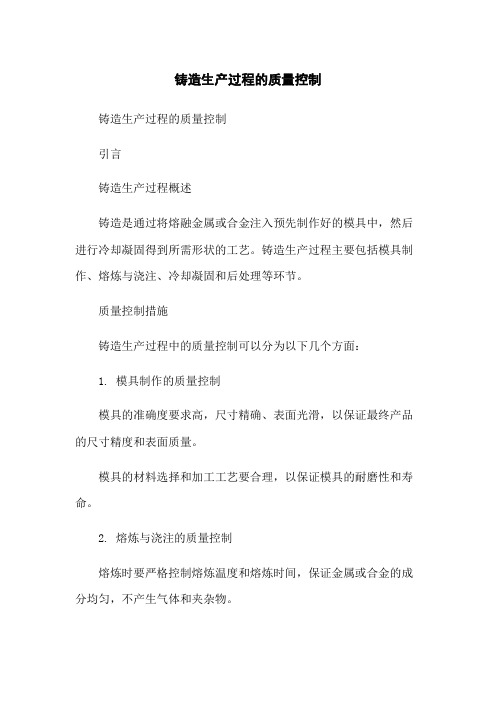
铸造生产过程的质量控制铸造生产过程的质量控制引言铸造生产过程概述铸造是通过将熔融金属或合金注入预先制作好的模具中,然后进行冷却凝固得到所需形状的工艺。
铸造生产过程主要包括模具制作、熔炼与浇注、冷却凝固和后处理等环节。
质量控制措施铸造生产过程中的质量控制可以分为以下几个方面:1. 模具制作的质量控制模具的准确度要求高,尺寸精确、表面光滑,以保证最终产品的尺寸精度和表面质量。
模具的材料选择和加工工艺要合理,以保证模具的耐磨性和寿命。
2. 熔炼与浇注的质量控制熔炼时要严格控制熔炼温度和熔炼时间,保证金属或合金的成分均匀,不产生气体和夹杂物。
浇注时要控制浇注温度和速度,避免产生气孔、夹渣和缩松等缺陷。
3. 冷却凝固的质量控制控制冷却速度和冷却方式,以避免产生组织缺陷,如晶粒过大、晶界不清晰等。
控制凝固过程中的温度变化,以避免产生应力和变形。
4. 后处理的质量控制清理杂质和缺陷,如夹渣、气孔等。
进行热处理、表面处理或机械加工,以改善产品的性能和表面质量。
质量控制方法为了有效控制铸造生产过程中的质量,可以采取以下几种方法:1. 设计质量控制在产品设计阶段,就应考虑产品的铸造性,合理设计产品的几何形状和壁厚,减少可能出现的缺陷和变形。
2. 工艺参数控制对每个工艺环节中的关键参数进行严格控制,如熔炼温度、浇注温度和速度等。
在铸造过程中,通过实时监测温度、压力和流速等参数,进行及时调整和控制。
3. 检测和检验使用各种检测设备和仪器,如X射线探伤仪、超声波检测仪等,对产品进行无损检测,以发现和排除可能存在的缺陷。
进行物理和化学性能的检验,如拉伸试验、硬度测试和成分分析等。
4. 信息化管理建立完善的质量管理体系,进行全过程的质量记录和数据分析,发现问题并采取措施进行改进。
运用信息化技术,实现数据的实时监控和追溯,提高生产过程的透明度和可控性。
结论铸造生产过程的质量控制是确保最终产品质量的重要环节。
通过合理的质量控制措施和方法,可以有效避免铸造过程中可能出现的缺陷和变形,提高产品的质量和性能。
钛合金的熔炼工艺-电子束冷床熔炼法(EBCHR)

钛合金的熔炼工艺-电子束冷床熔炼法(EBCHR)真空自耗电弧熔炼一直是钛合金的主要熔炼方法。
为了提高航空发动机用钛合金铸锭成分的均匀性和尽可能消除偏析等缺陷,一般采用三次真空电弧熔炼。
但研究证明,真空电弧熔炼消除钛合金中的高密度夹杂(HDI)和低密度夹杂(LDI)的能力有限。
而这两种缺陷是钛合金零部件的疲劳裂纹源,降低了零部件的使用寿命。
若用于航空发动机,可能引起重大事故。
因此美国在20世纪80年代开始研究开发一种熔炼钛合金的新工艺———冷床熔炼(Cold Hearth Melting,简称CHM)技术。
根据热源的不同,冷床熔炼可以分为电子束冷床熔炼(Electron Beam Hearth Melting,简称EBCM 或Electron Beam Cold-Hearth Remelting,简称EBCHR)和等离子束冷床熔炼(Plasma Arc Cold Hearth Melting,简称PACHM)两种熔炼方式。
冷床炉熔炼技术独特的熔炼方式,可以有效消除钛合金中的各种夹杂物,解决了长期困扰钛工业界的一大难题,因此,冷床熔炼技术可以认为是钛合金熔炼技术发展史上的一次飞跃。
冷床熔炼就是在冷坩埚(水冷坩埚)熔炼技术的基础上,再加上电子束或等离子束的高温外加热源作用的结合。
所谓冷床实际就是凝壳熔炼的坩埚,冷床熔炼就是凝壳熔炼的新发展。
1905年,德国的西门子(Siemens)公司和Haisko用电子束熔炼钽首次获得成功,但由于当时世界的真空技术发展水平还很有限,从而阻碍了电子束熔炼技术的发展。
真正将电子束熔炼技术推向商业化是在1957年,Temescal冶金公司利用电子束熔炼钛锭。
之后Temescal冶金公司大力发展电子束熔炼技术,在20世纪60年代初期,该公司利用横向电子枪熔炼炉制备了直径80mm的钽锭和钨锭以及直径127mm、重数百公斤的钛锭。
20世纪80年代,现代轴向电子枪取代了早期的横向电子枪,使得电子束熔炼炉的产能得到真正意义上的大幅提高。
铸造工艺流程的质量控制方法
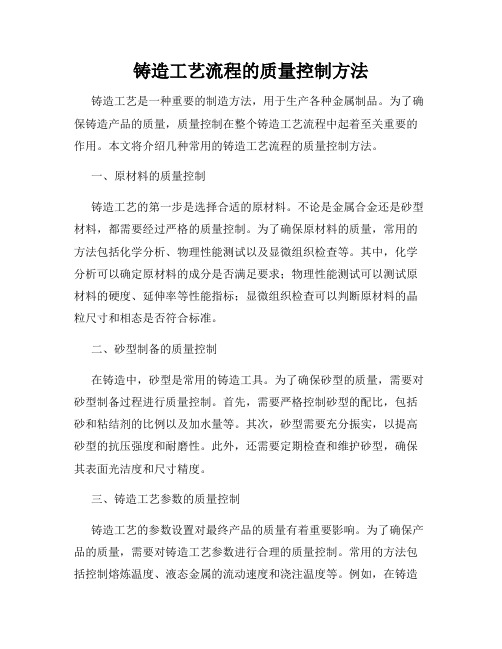
铸造工艺流程的质量控制方法铸造工艺是一种重要的制造方法,用于生产各种金属制品。
为了确保铸造产品的质量,质量控制在整个铸造工艺流程中起着至关重要的作用。
本文将介绍几种常用的铸造工艺流程的质量控制方法。
一、原材料的质量控制铸造工艺的第一步是选择合适的原材料。
不论是金属合金还是砂型材料,都需要经过严格的质量控制。
为了确保原材料的质量,常用的方法包括化学分析、物理性能测试以及显微组织检查等。
其中,化学分析可以确定原材料的成分是否满足要求;物理性能测试可以测试原材料的硬度、延伸率等性能指标;显微组织检查可以判断原材料的晶粒尺寸和相态是否符合标准。
二、砂型制备的质量控制在铸造中,砂型是常用的铸造工具。
为了确保砂型的质量,需要对砂型制备过程进行质量控制。
首先,需要严格控制砂型的配比,包括砂和粘结剂的比例以及加水量等。
其次,砂型需要充分振实,以提高砂型的抗压强度和耐磨性。
此外,还需要定期检查和维护砂型,确保其表面光洁度和尺寸精度。
三、铸造工艺参数的质量控制铸造工艺的参数设置对最终产品的质量有着重要影响。
为了确保产品的质量,需要对铸造工艺参数进行合理的质量控制。
常用的方法包括控制熔炼温度、液态金属的流动速度和浇注温度等。
例如,在铸造过程中,如果熔炼温度过高,易导致铸件内部存在气孔和夹杂物;如果浇注温度过低,易导致铸件的收缩缺陷。
因此,合理控制这些参数可以有效提高铸件的质量。
四、铸造产品的检测与测试在铸造工艺流程中,对铸造产品进行质量检测和测试是不可或缺的环节。
常用的方法包括无损检测、机械性能测试以及尺寸测量等。
其中,无损检测可以通过X射线、超声波等方法检测产品是否存在缺陷;机械性能测试可以测试产品的抗拉强度、硬度等力学性能;尺寸测量则可以验证产品的尺寸精度是否符合要求。
五、质量记录与反馈为了总结经验并改进铸造工艺流程,需要对质量进行记录和反馈。
对于每个铸造批次,应该记录原材料、砂型、工艺参数以及产品质量等关键信息。
大规格纯钛铸锭化学成分均匀性控制技术

4 2 8 0 mm 纯 钛 铸 锭 主 要 生 产 工 艺 流 程
如下 :
海绵 钛
( 部 分 返 回 炉 料 ) 一 配 料 一 布 加
其 中 纯 钛 铸 锭 化 学 成 分 及 其 均 匀 性 的 控 制 技 术 水 平 较 高 , 尤 其 是 添 加 返 回 炉 料 的 纯 钛 铸 锭 生 产 技 术 比较 高 。 宝 鸡 有 色 金 属 加 工 厂 新 建 的 一 台 6t真
衰 1
序 号
为 生 产 大 规 格 铸 锭 奠 定 了 设 备 基 础 。 同 时 可
参 考 6 0lm、质 量 为 3t的 纯 钛 铸 锭 熔 铸 2 l l
技 术 制 定 4 2 m 、 质 量 为 6t的 大 规 格 纯 8 0m 钛 铸 锭 的 工 艺参 数 。但 是 根 据结 晶偏 析 理 论 和 VAR 熔 炼 的 特 征 ,随 着 铸 锭 尺 寸 的 增 加 , 铸 锭 的 化 学 成 分 偏 析 可 能 性 和 成 分 波 动 范 围 也 相 应 增 大 , 另 外 , 生 产 这 样 大 的 纯 钛 铸 锭 还 需 要 添 加 大 量 残 钛 返 回 炉 料 , 因 此 就 大 大 增 加 了铸 锭 化 学 成 分 控 制 的 工 艺 难 度 。 本 项 研 究 主 要 通 过 对 原 料 配 料 技 术 、返 回 料 添 加 比例 、 原 料 布 料 工 艺 、 铸 锭 熔 炼 参
工 业 纯 钍 的 化 学 成 分
化学 成 分 / ( 大 于) 不
H O
Fe
C
N
李 藏 军 ,男 , 高 级 工 程 师 , 陕 西 省 宝 鸡 市 7 1信 箱 科 技 部 , 宝 鸡
钛及钛合金铸锭氧化和预防

钛及钛合金铸锭氧化和预防摘要:本文详细介绍了钛合金铸锭熔炼过程中头部氧化、侧身氧化、底部氧化、整锭氧化的特征、产生原因的判断、以及钛合金铸锭氧化带来的风险和处理方式。
通过对不同类型钛及钛合金氧化的处理,可以最大限度的降低铸锭增氧的风险,从而满足钛及钛合金氧元素控制要求。
关键词:钛及钛合金;铸锭;氧化分类;电弧炉熔炼前言钛是地壳中分布最广的元素之一,约占地壳总质量的0.6%,仅次于铝、铁、镁,位居于第四位。
钛及钛合金由于比强度高、耐蚀性能好、高温性能优良,广泛用于航空、航天、航海以及医疗等领域。
但钛由于化学性质性质活泼,很容易与空气中的碳、氮、氧、氢等元素发生化学反应。
钛在室温下就与氧发生反应形成一层致密的氧化膜,可以阻止氧进一步向基体扩散。
随着温度的升高,钛与钛合金氧化逐步加快,当温度达到500℃时,钛的氧化膜变得疏松且容易脱落,甚至变硬变脆。
钛合金铸锭目前最长见的熔炼方式是真空自耗电弧炉熔炼,简称VAR熔炼。
为了满足化学成分均匀性的要求,经常需要经过三次真空自耗电弧炉熔炼。
在三次熔炼过程中钛合金头部氧化、端面氧化、侧身氧化和底部氧化,都是最常见的钛及钛合金氧化现象。
严重时,可能发生整锭氧化,导致铸锭氧元素过高,产品不合而报废。
1. 钛及钛合金铸锭氧化的分类。
钛及钛合金目前最常见的熔炼方式为真空自耗电弧炉熔炼,真空自耗熔炼过程中跟钛合金氧化相关的设备及工模具有:真空泵组、闭锁阀及其密封、坩埚系统、充氩系统等。
若设备及工模具漏气,则钛及钛合金铸锭熔炼出炉后,会明显观察到钛合金氧化的现象,主要分为以下四类:头部氧化、侧身氧化、底部氧化、整锭氧化。
头部氧化,即钛及钛合金铸锭头部位置氧化,包含铸锭头部端面和头部侧面。
当只有头部端面氧化时,一般影响相对较小。
当端面和头部侧面均有氧化时,一般相对氧化较为严重。
头部氧化一般发生在熔炼结束以后,闭锁阀、充氩管道和炉室等均与头部氧化存在一定关系。
侧身氧化,即钛及钛合金铸锭侧身位置氧化,一般指仅侧身氧化,其他部位未氧化。
真空自耗电弧炉熔滴控制研究
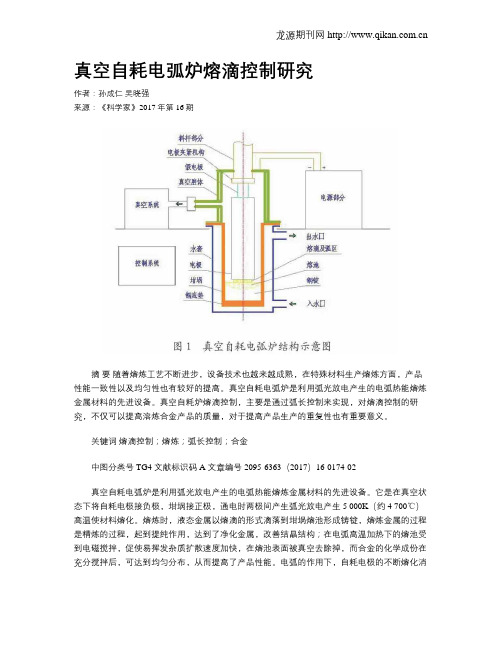
真空自耗电弧炉熔滴控制研究作者:孙成仁吴晓强来源:《科学家》2017年第16期摘要随着熔炼工艺不断进步,设备技术也越来越成熟,在特殊材料生产熔炼方面,产品性能一致性以及均匀性也有较好的提高。
真空自耗电弧炉是利用弧光放电产生的电弧热能熔炼金属材料的先进设备。
真空自耗炉熔滴控制,主要是通过弧长控制来实现,对熔滴控制的研究,不仅可以提高溶炼合金产品的质量,对于提高产品生产的重复性也有重要意义。
关键词熔滴控制;熔炼;弧长控制;合金中图分类号 TG4 文献标识码 A 文章编号 2095-6363(2017)16-0174-02真空自耗电弧炉是利用弧光放电产生的电弧热能熔炼金属材料的先进设备。
它是在真空状态下将自耗电极接负极,坩埚接正极,通电时两极间产生弧光放电产生5 000K(约4 700℃)高温使材料熔化。
熔炼时,液态金属以熔滴的形式滴落到坩埚熔池形成铸锭,熔炼金属的过程是精炼的过程,起到提纯作用,达到了净化金属,改善结晶结构;在电弧高温加热下的熔池受到电磁搅拌,促使易挥发杂质扩散速度加快,在熔池表面被真空去除掉,而合金的化学成份在充分搅拌后,可达到均匀分布,从而提高了产品性能。
电弧的作用下,自耗电极的不断熔化消耗,熔池不断上升,熔融金属被水冷坩埚逐渐冷凝。
这种炉子主要用于钛、锆、钼活泼金属,以及特铁金属的熔铸。
1 真空自耗电电弧炉工作原理真空自耗电弧炉主要由炉体(融化站)、电极杆及其传动系统、电极杆对中调节、观察摄像装置、炉体升降液压系统、炉体框架(真空室、立柱导向联接体)及其旋转或熔炼室平移机构、坩埚及稳弧线圈、冷却水套(下炉室)、真空系统、冷却系统、压缩空气系统、直流整流电源、电气控制系统,防爆墙等组成。
其工作特点:炉体融化站相对坩埚提升和旋转(或者炉体融化站提升和坩埚平移),电极装入和铸锭卸出均由吊装工具完成。
真空自耗电弧炉结构示意图示见图1。
熔滴形成于电极下端部位,在熔滴滴落过程中,会有物理化学反应产生,在这个过程中,去除掉一部分气体杂质。
铸造生产过程的质量控制
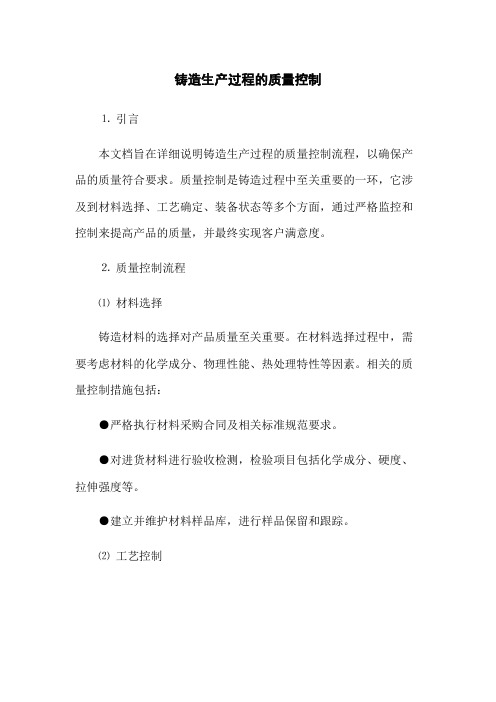
铸造生产过程的质量控制⒈引言本文档旨在详细说明铸造生产过程的质量控制流程,以确保产品的质量符合要求。
质量控制是铸造过程中至关重要的一环,它涉及到材料选择、工艺确定、装备状态等多个方面,通过严格监控和控制来提高产品的质量,并最终实现客户满意度。
⒉质量控制流程⑴材料选择铸造材料的选择对产品质量至关重要。
在材料选择过程中,需要考虑材料的化学成分、物理性能、热处理特性等因素。
相关的质量控制措施包括:●严格执行材料采购合同及相关标准规范要求。
●对进货材料进行验收检测,检验项目包括化学成分、硬度、拉伸强度等。
●建立并维护材料样品库,进行样品保留和跟踪。
⑵工艺控制铸造工艺的控制对产品质量的影响巨大。
在工艺控制过程中,需要考虑熔炼、浇注、冷却、固化等阶段的控制要点。
相关的质量控制措施包括:●制定详细的工艺规程,并严格执行。
●设置合理的熔炼温度、浇注温度和冷却速率。
●使用合适的浇注工艺和设备,确保铸件结构紧密、无夹杂、无缩孔等缺陷。
⑶设备维护铸造设备的状态对产品质量有直接影响。
定期维护和检修设备是保证生产工艺可靠性的重要措施。
相关的质量控制措施包括:●制定设备维护计划,并按计划进行设备巡检、保养和维修。
●建立设备使用记录,包括设备维修记录、故障记录等。
●定期进行设备性能验证,确保设备在正常工作状态。
⒊附件本文档涉及的附件包括:●材料采购合同及相关标准规范●进货材料检验报告样本●工艺规程范本●设备维护计划范本⒋法律名词及注释在本文档中,涉及到的法律名词及注释如下:●合同:指双方或多方当事人之间订立的具有法律效力的协议。
●标准规范:指由相关行业组织或制定并公布的规定产品设计、生产、质量等方面要求的文件。
●样品保留:指保留材料样品作为日后验证或追溯的依据。
●巡检:指定期巡查设备状态,发现异常及时进行处理。
请根据实际情况对文档进行适当修改和调整,以确保与您的具体需求匹配。
真空自耗

真空自耗电弧炉1 VAR的结构组成及其特点VAR 炉由真空系统、电极驱动机械系统、铜坩埚及冷却循环系统、直流电源、自动和手动控制系统、稳弧搅拌系统、检测和自动记录系统等部分组成。
VAR 炉现已处于较为完善的阶段,在结构上具有同轴性、再现性和灵活性特征,正在向更大容量和远距离精确操作发展。
VAR炉采用先进的计算机自动电控和数据收集系统,能够对给定的合金和铸锭规格建立良好的熔炼模式,并分析熔炼过程中出现的问题,获得良好的铸锭表面质量和内在冶金质量,提高金属成品率。
2 真空自耗炉的工作原理真空自耗炉主要用于钛和钛合金的生产。
图1所示为真空自耗炉原理示意图。
该炉有一个结晶器,结晶器装入水冷的外套里,并与熔炼电源的正极相接。
电源的负极与活塞即“拉杆”连接,该拉杆通过滑动的真空密封进入炉内。
待熔炼的钢材(即电极)夹紧在控制活塞的机座上,并且在炉膛抽空以后,下降电极与在结晶器底部的同样材料的金属垫料触发电弧。
当电极由于输人功率而熔化时,就可通过液压控制系统下降活塞,以便保持电极同由此而形成的熔池之间的距离不变。
当熔炼继续进行时,在结晶器里就逐渐地形成了一支新的锭料。
3 VAR基本的工艺流程:工艺流程:混料一压制电极一电极和残料焊接成自耗电极一熔炼一铸锭处理一检验。
3.1 真空自耗原料由纯料、合金元素、返回料等组成。
3.2 电极制备经过混料后,添加或未添加残料的原料通过压制、焊接,制成自耗电极。
焊接方法为自耗电弧焊或等离子焊,焊接应进行充分的保护或在惰性气氛下的容器里进行,以避免污染和难熔氧化物或氮化物的形成。
应严禁使用钨极氩弧焊。
制备的自耗电极必须具备足够的机械稳定性,即使在熔炼过程中加热时也不会开裂.并确保电流畅通无阻地通过。
3.3 熔炼过程炉子采用真空系统,是为了避免空气污染,同时有效去除氢气和氯化物。
水冷铜坩埚给金属的熔炼提供了适宜的容器,只要冷却适当,熔融金属就在其表面形成一层“渣壳”.既保护坩埚,又不被坩埚污染。
- 1、下载文档前请自行甄别文档内容的完整性,平台不提供额外的编辑、内容补充、找答案等附加服务。
- 2、"仅部分预览"的文档,不可在线预览部分如存在完整性等问题,可反馈申请退款(可完整预览的文档不适用该条件!)。
- 3、如文档侵犯您的权益,请联系客服反馈,我们会尽快为您处理(人工客服工作时间:9:00-18:30)。
真空自耗电弧炉熔炼钛铸锭的质量控制安红刘俊玲范丽颖/AnHongLiuJunlingFanLiyingTechnology&Equipment真空白耗电弧炉熔炼钛铸锭的质量控制Qualitycontrolinsmeltingtitaniumingotsinvacuumarc-meltingfurnace 目前,我国生产钛及钛合金铸锭的基本方法仍为真空白耗电弧炉熔炼法,该方法可满足一般工业的要求,是一种成熟的工业熔炼方法(如下图).评价钛及钛合金铸锭冶金质量的好坏,主要有以下几点:①化学成分均匀,各合金元素含量不仅达到标准要求,而且要稳定地控制在一个最佳的含量水平.②主要杂质(Fe,O等)控制适当范围,其它杂质符合标准要求.③铸锭内部无杂质,偏析,气孔,裂纹,缩孔和疏松等冶金缺陷.④铸锭表面光滑,无冷隔,折皱等表面缺陷,头部缩孔切除量小,铸锭成品率高.⑤合理的形状和精确的尺寸,适合压力加工的要求,否则会增加工艺废品,降低成本.图1钛及钛合金铸锭生产工艺流程图影响铸锭质量的主要因素Mainfactorsinfluencing价equalityofingots原料,熔炼工艺参数(熔炼电流,电弧电压,真空度,漏气率,冷却速度,搅拌磁场强度)选择的合理性以及工艺过程控制的严密性决定着钛及钛合金铸锭的冶金质量.下面分别进行论述.(1)海绵钛海绵钛中常含有H,MgC1(NaC1),Fe和H,O等杂质.当H含量高时,它将在熔炼过程大量排出,会使电弧不稳;氯化物含量多时,熔炼过程操作困难,并会影响设备的寿命;铁含量高时,会使材料耐腐蚀性能降低;原料潮湿将使钛锭含氧,氢量增高,从而降低其强度.因此,海绵钛必须满足相关标准的要求,如纯度,均匀性和粒度.最为重要的是不能含有高熔点钛的氧化物,氮化物或者其它高熔点颗粒. 这些高熔点颗粒有可能在最终产品中成为裂纹源.据资料,分析高间隙缺陷发现,这些区域含有较高的O,N,C,认为这些颗粒的来源之一就是海绵钛.海绵钛生产过程中漏气或者污染的反应剂,有可能导致N,O与产品反应.迄今为止没有自动方法检验原料,并剔除这些污染的粒子.一般主要是肉眼评价或者工艺参数评定. 因此,除了与原料供应商协议不允许出现有缺陷的原料外,还应100%肉眼检查海绵钛和残料及中间合金. 真空白耗电弧熔炼是一种区域性熔炼,铸锭杂质含量主要靠合理的原料选择来保证.况且,钛及钛合金的熔炼是在密闭的真空室中进行的,熔炼过程中不可能对熔体进行化学成分调整,因此,在焊接成自耗电极之前的各道工序中必须严把质量关,保证准确无误.通过精选海绵钛,按配料要求将不同成分的海绵钛充分搅拌混合,确保海绵钛的成分均匀.同时,配入中间合金后还必须将中间合金与海绵钛混合均匀.(2)中间合金采用中间合金作添加原料,是改善合金化条件,提高合金成分均匀度,克服偏析和不溶金属夹杂,减少金属烧损率的有效方法.使用中间合金,便于加入某些熔点较高且不易溶解或易氧化挥发的合金元素,以便更准确地控制合金成分,其次,使用中间合金作为炉料,可以避免熔体过热,降低烧损.因此,中间合金应尽可能满足下列要求: WORLDNONFERROUSMETALS2007.825技术与装鲁①添加的合金化元素,熔点低于或者接近合金的熔炼温度.无论是纯金属或者中间合金,其熔点一方面不能超过合金的熔点,另一方面,也不能比钛的熔点低450~C~550~C,否则,过早熔化,会造成铸锭成分不均匀.②化学成分均匀一致.③含有尽可能高的合金元素,夹杂物少.④具有足够的脆性,便于破断配料,但在大气下保存时不应碎裂成粉末.⑤比重,比热,熔化潜热与钛相近.⑥生产成本低.(3)电极制备制备单块电极的基本方法有压制和挤压两大类.电极块经过组装和焊接得到一次熔化的电极.焊接方法主要为氩弧焊或等离子焊,焊接应进行充分的保护或者在惰性气氛的焊箱内进行,以避免金属污染或形成难熔氧化物和氮化物.制备的自耗电极必须具备下列特征:①足够的强度,除能承受自重外,应能在运输,吊装及熔炼操作过程中的振动和冲击下不受损坏.②足够的导电性,一般认为,关键在于要求足够的焊接面积.③足够的平直度,保证在整个熔炼过程中的电极与坩埚壁内径之间的最小间隙大于弧长.④合金元素组元成分和杂质含量的分布合理.⑤电极不得污染和受潮.熔炼工艺参数Processpemrne~insmelling(1)电流和电压自耗熔炼中最敏感的工艺参数就是熔炼电流.对于熔炼电流的确定,有不少经验公式,但因为各参数之间相互影响的关系比较复杂而局限性较大.熔炼电流主要取决于电极材料,铸锭规格和坩埚比,此外,电源类型,极性以及炉子结构,熔炼室压力等都影响最佳电流数值.对于钛及钛合金而言,主要是铸锭直径的函数.实际采用的电流可利用经验公式:In=(18~33)Dk(安培)上式中,In一熔炼电流Dk一结晶器内径,毫米由于在整个电弧熔炼过程中,熔区的热平衡条件是变化的,对于直径大的铸锭则更为明显,初期结晶器底座冷却效果特别显着,而电极温度较低,中期逐渐减弱了底座冷却强度的影响,电极温度升至稳定阶段,而在后期,电极温度由于炉内其他部件如夹头,26世界有色金属2OO7年第8期辅助电极温度升高及接受热辐射能量增加而达到最高阶段.为了使熔池深度基本保持恒定,获得化学成分和组织均匀的铸锭,三个阶段中使用的电流应该是递减的.在具体确定熔炼电流值时,还应考虑到原料品位,熔次,合金元素的熔点,比重以及坩埚比的不同而作相应的调整.对于熔炼电压来说,由于钛及钛合金一般采用短弧熔炼,电压一般在28~40伏之间,铸锭规格大,电流大则电压靠上限,铸锭规格小,电流小则电压靠下限. (2)炉内压力炉内压力和原料的气体含量影响电弧行为和产品质量.当电弧区残余压力增大到13Mp~66Mp时就达到辉光放电的临界压力范围,电弧燃烧不稳定,甚至导致电弧熄灭,严重时会产生边弧而击穿设备.虽然真空自耗电弧炉可在常压惰性气体保护下进行,但真空熔炼具有加热温度更均匀,弧柱压降小,热效率高的优点,正常生产中多采用真空熔炼.惰性气体保护下熔炼的El的在于解决一些钛合金严重偏析问题.(3)磁场效应电弧是一种由流动的电子和离子化的粒子组成的电现象,必然受到磁场影响而发生偏转.通常的做法是在水套上缠绕稳弧线圈,以此对电弧和熔池更好地控制.稳弧线圈通常有两种形式,一是永久固定在水套上,基本可以覆盖整个坩埚;另一种则较短并可移动,只用来覆盖弧区及熔池的上部区域,随熔池的升高而不断地升高,对于拉锭系统则保持在某一位置不动.实践证明,流过坩埚的电流不对称,供电线路及附近设备磁场的影响都会引起熔池的瞬时转动,进一步影响铸锭的结晶凝固并降低冶金质量.合理的稳弧线圈布置和参数给定能够使电弧围绕电极平稳缓慢地移动,防止集中在坩埚壁上击穿坩埚.熔池搅拌是获得良好的结晶组织以利于锻造加工的基础.线圈的电流连续不断地沿着一个方向流动,凝固时,晶粒会在某一方向优先长大,对锻造不利.实际生产中,可每隔几秒将直流电极性转换,补偿熔池固有的旋转.(4)热封顶操作热封顶的El的是减少铸锭头部的缩孔和偏析等,减少铸锭的切头量,提高铸锭的成品率.最后一次熔炼,当电极消耗~U9o%以上时,应逐级降低电流,使熔池凝固不形成有害的缺陷.(5)坩埚比也称填充比,是指电极与坩埚直径之比.它是影响铸锭质量和安全生产的重要参数之一.对于钛及其合金,坩埚比一般在0.625~0.88之间.坩埚比大,铸锭表面质量好,致密度高,但易产生边弧.(6)铸锭冷却铸锭一般在真空或者惰性气体保护下冷却后出炉.惰性气体保护会加速冷却.如果还需要进一步的熔炼,应避免铸锭氧化.(7)铸锭规格和铸锭熔化次数铸锭尺寸不仅影响铸锭的质量,而且对生产率也有影响.一般,铸锭尺寸依据半成品尺寸来确定.大规格铸锭具有实用经济性的优点,但是,增大铸锭的尺寸,偏析倾向就增高.铸锭长度的确定必须考虑炉子的生产率.一定电流下,随着铸锭长度的增加,生产率增加较小.应该指出,长度的增加应合理,否则,会给生产带来困难, 实际上起不到提高生产率的作用.为了保证最终产品的均匀性,两次熔炼是必要的.一次熔炼是为了使铸锭初步合金化,均匀化及去除挥发性物质和气体,二次熔炼是为了获得成分分布均匀,表面质量良好的铸锭.铸锭质量控制Qualitycon~oloningots(1)合金化学成分均匀性控制合金化学成分均匀性,是指铸锭各个区域具有均匀的化学成分;同一牌号的铸锭的化学成分波动范围是严格控制的.在钛合金真空自耗电弧熔炼过程中,当合金元素及中间合金的熔点高于被熔炼合金的熔点时,可能出现因合金元素及中间合金熔化不完全而造成的化学成分不均匀.钛合金的结晶遵循树枝状结晶机制,由此也会产生树枝状结晶偏析形式的化学成分不均匀.通常采用以下措施控制合金化学成分均匀性:①海绵钛质量对钛合金铸锭质量有遗传性影响.要控制钛合金铸锭质量,首先应该控制海绵钛的质量.需要制订先进的海绵钛质量标准,采用先进的海绵钛生产,破碎,分选及混合工艺,在海绵钛生产的各个环节提高不同批次的海绵钛化学成分和硬度的一致性,防止海绵钛中混入其它外来杂质.②在真空自耗电弧炉熔炼之前严格检查并挑选炉料,防止炉料中混入气体含量,主要是氮氧含量超标的海绵钛块.③在合金铸锭生产中采用小颗粒海绵钛(通常为0.83~1.72毫米).Technology&Equipment④使用多元中间合金.⑤确保电极焊接质量,防止一次电极在熔化过程中出现掉块.⑥严格控制熔化工艺过程,尽量保持恒速熔炼.(2)防止出现夹杂在熔炼过程中密度和熔点大于基体金属的炉料颗粒,以不熔块的形式存在于铸锭中,叫高密度夹杂.在钛合金零件中出现高密度夹杂的部位,容易产生集中应力,形成裂纹,引发灾难性事故.为了防止高密度夹杂,通常采用以下措施:①100%地仔细地检查所有的炉料,防止夹杂有硬质合金碎粒的颗粒进入炉料.②以连续挤压法生产长电极,少用焊接制造自耗电极.③采用一根电极熔炼一次铸锭,然后,一次铸锭化一支二次铸锭的工艺路线.④采取工艺措施防止难熔金属块掉人液态熔池,并要避免把电极与辅助电极的焊缝区化入铸锭.⑤对于特别重要用途的铸锭,采取二次,甚至三次重熔工艺,提高偶然进入炉料的高熔点料块的熔化概率.(3)偏析缺陷的改进真空自耗电弧炉熔炼和凝固结晶的基本特征是电极不断地熔化,同时,铸锭自下而上地在结晶器中连续凝固增高.在熔化过程中,冷却条件,熔池形状和深度等均不是一成不变的,且合金元素在凝固结晶时的分配系数各异,这样,不可避免地使合金元素或化合物在树枝状晶间富集而形成偏析.偏析程度与合金分配系数,凝固速率,液相的自然和受迫运动,扩散,晶粒尺寸及晶体形成的方式有关,其它因素则与具体操作工艺有关,可通过以下措施进行改进.①对铸锭的前道工序进行严格的质量控制,尤其是电极焊接工序.②可采用反复熔炼.反复熔炼可以减少硬0【缺陷.③提高海绵钛质量.海绵钛生产大多采用镁还原法,对于用镁作为还原剂的海绵钛全部制造工序的质量管理特别重要.近年来,宝鸡有色金属加工厂采用布料一混料生产线计算机控制配置中间合金,单块电极混料,真空等离子焊箱内焊接等先进工艺生产钛合金铸锭,钛锭的冶金质量明显提高. WORLDNONFERROUSMETALS2007.827。