真空自耗电弧炉(VAR)的工作原理与特点
几种熔炼炉对比

1. 镍基合金熔炼工艺国内外镍基高温合金、镍基耐蚀合金、精密合金的熔炼设备主要有真空感应炉、真空自耗炉、电渣炉、电子束炉和等离子电弧炉等。
1)真空感应炉(VIM)真空感应熔炼是一种成熟的真空熔炼方法,是镍基高温合金、耐蚀合金等的重要生产工艺,特别是对于含有铝、钛等活泼元素较多的合金,必须采用真空感应熔炼。
VIM可提供对化学成分最大程度的控制,防止了溶液与大气中氢、氧、氮的接触。
真空下反应的进行和完成比在大气下要快。
除了使溶液均匀外,感应搅拌能持续将反应物带到熔体和真空界面,从而使精炼反应顺利进行。
气体夹杂和痕量元素的蒸发能改善大多数高温合金的力学性能。
VIM缺点在于大多数最终产品都必须进行重熔,主要是为了减少偏析和控制凝固组织以及耐火材料的侵蚀,采用CaO耐火材料坩埚、电磁搅拌、陶瓷过滤等技术均可以有效提高合金的纯净度。
新建3座12 tVIM,熔炼周期14 h/炉,平均每炉产量12 t,年产能18000 t,可满足规划生产真空感应炉锭17685.8 t/a的要求。
2)电渣重熔炉(ESR)电渣冶金是目前生产高品质材料的重要方法,具有纯度高、含硫量低、非金属夹杂物少、钢锭表面光滑、结晶均匀致密、金相组织和化学成分均匀的优点,广泛应用于航天航空、军工、能源、船舶、电子、石化、重型机械和交通等国民经济的重要领域。
电渣重熔的目的是通过将化学精炼和控制凝固结合起来生产高质量铸锭。
电渣重熔过程中,金属材料能够被熔渣有效地精炼,合金中的非金属夹杂物、气体和硫含量显著减少,合金的纯净度提高,因而合金的力学性能得到改善。
电渣熔炼过程中,始终有液态渣的保护,使金属不与空气接触,合金元素烧损低,成分容易控制;避免了熔炼过程中耐火材料的污染;铸锭组织致密,缩孔较小,没有疏松及皮下气泡等缺陷,提高了材料的塑性;设备简单,易于操作。
然而ESR也存在许多不足之处,如熔炼和凝固速率偏低、熔渣吸收气体、活泼元素不易控制以及电极重熔过程经受高温氧化等。
真空感应熔炼炉(VIM)的工作原理与结构简图

书山有路勤为径,学海无涯苦作舟真空感应熔炼炉(VIM)的工作原理与结构简图世界上第一台真空感应炉是于1917 年在德国诞生的,用于熔炼飞机和火箭发动机的引擎。
真空感应熔炼炉是真空冶金领域中应用最广的设备之一。
事实证明:宇航、导弹、火箭、原子能设备和电子工业所需要的合金和特殊钢,占有相当比例的产品是采用真空感应熔炼炉生产出来的,例如,镍基、钴基、铁基高温合金采用真空感应熔炼炉工艺熔炼时,其热加工性能和机械性能明显提高。
像不锈钢、耐热钢、超高强度钢、工具钢、轴承钢,以及磁性材料、弹性合金、膨胀合金等几乎均采用真空感应熔炼炉来熔炼,以保证材料性能和质量。
此外,真空技术网(chvacuum/)认为随着二次重熔工艺的发展,真空感应熔炼炉的另一用途是为真空自耗电弧炉或电渣重熔炉提供高质量的自耗电极,以及生产母合金供精密铸造用。
众所周知,真空感应熔炼炉工艺,对金属的熔化、精炼和合金化的整个过程均是在真空状态下进行的,因而避免了相同气相的相互作用而污染。
其次,在真空条件下,碳具有很强的脱氧能力,其脱氧产物CO 不断被抽至系统之外,克服了采用金属脱氧剂脱氧的污染问题。
真空感应熔炼炉工艺可精确地控制合金的化学成分,对于含有和氧、氮亲和力强的活性元素Al、Ti、B、Zr 等,可控制在很少的范围内。
对低熔点易挥发的金属杂质,如Pb、Bi、Sn、Sb 等能蒸发去除,这对提高材料性能起到重要作用。
强烈的感应搅拌作用,能加速其反应速度,这对于熔池温度均匀、化学成分均匀等方面很有效果。
真空感应熔炼工艺之因此得到迅速发展是和航空航天工业所需高温合金材料有密切关系,如宇航、导弹、火箭、原子能等设备所需的高温合金。
在未采用真空熔炼方法生产的高温合金,其最高工作温度通常只有750-810 ℃;而。
电炉、AOD炉、LF炉、VD真空炉的原理与作用
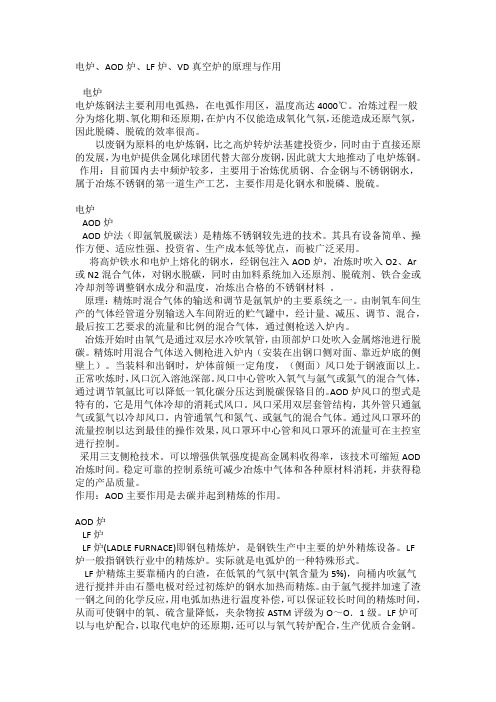
电炉、AOD炉、LF炉、VD真空炉的原理与作用电炉电炉炼钢法主要利用电弧热,在电弧作用区,温度高达4000℃。
冶炼过程一般分为熔化期、氧化期和还原期,在炉内不仅能造成氧化气氛,还能造成还原气氛,因此脱磷、脱硫的效率很高。
以废钢为原料的电炉炼钢,比之高炉转炉法基建投资少,同时由于直接还原的发展,为电炉提供金属化球团代替大部分废钢,因此就大大地推动了电炉炼钢。
作用:目前国内去中频炉较多,主要用于冶炼优质钢、合金钢与不锈钢钢水,属于冶炼不锈钢的第一道生产工艺,主要作用是化钢水和脱磷、脱硫。
电炉AOD炉AOD炉法(即氩氧脱碳法)是精炼不锈钢较先进的技术。
其具有设备简单、操作方便、适应性强、投资省、生产成本低等优点,而被广泛采用。
将高炉铁水和电炉上熔化的钢水,经钢包注入AOD炉,冶炼时吹入O2、Ar 或N2混合气体,对钢水脱碳,同时由加料系统加入还原剂、脱硫剂、铁合金或冷却剂等调整钢水成分和温度,冶炼出合格的不锈钢材料。
原理:精炼时混合气体的输送和调节是氩氧炉的主要系统之一。
由制氧车间生产的气体经管道分别输送入车间附近的贮气罐中,经计量、减压、调节、混合,最后按工艺要求的流量和比例的混合气体,通过侧枪送入炉内。
冶炼开始时由氧气是通过双层水冷吹氧管,由顶部炉口处吹入金属熔池进行脱碳。
精炼时用混合气体送入侧枪进入炉内(安装在出钢口侧对面、靠近炉底的侧壁上)。
当装料和出钢时,炉体前倾一定角度,(侧面)风口处于钢液面以上。
正常吹炼时,风口沉入溶池深部。
风口中心管吹入氧气与氩气或氮气的混合气体,通过调节氧氩比可以降低一氧化碳分压达到脱碳保铬目的。
AOD炉风口的型式是特有的,它是用气体冷却的消耗式风口。
风口采用双层套管结构,其外管只通氩气或氮气以冷却风口,内管通氧气和氮气、或氩气的混合气体。
通过风口罩环的流量控制以达到最佳的操作效果,风口罩环中心管和风口罩环的流量可在主控室进行控制。
采用三支侧枪技术。
可以增强供氧强度提高金属料收得率,该技术可缩短AOD 冶炼时间。
真空自耗电弧炉控制系统及控制策略研究

文章编号:0 1 9 42 0 )40 3—4 10 - 4 (0 80 —0 60 9
真空 自耗 电弧 炉控制 系统及 控制策略研 究
葛 国秋 , 陈今 润 , 张绪 兵
( 重庆 大 学 自动 化 学 院 , 重庆 4 0 3 ) 0 0 0
GE Gu . i CHEN Jn 1 n Z o qu, i.l , HANG Xu bn q - ig
( c o lo tmain, o g ig Unv ri , h n qn 0 0 0, ia S h o fAuo t o Ch n qn iest C o g ig 4 0 3 Chn ) y
关键 词 : 空 自耗 电弧 炉 ; 速 率 控制 ; 馈控 制 真 熔 前
中 图分 类 号 : 2 35 TP 7 . 文献 标 志 码 : B
Re e r h o Co t o se n Co r l Te h i ue o sa c n n r l Sy t m a d nt o c n q f VAR Fur c na e
的优点 是能源利 用率 高 , 由于等 离子体 的流 向是从
阴极流 向 阳极 区 的 , 以传 热效率 很高 。尽 管如此 , 所 非 自耗 电弧炉也 存在一 些 缺陷 ,其非 自耗 电极 的挥 发 损失会 对钢锭 造成 污染 , 其性 能下 降 。 空 自耗 使 真
电弧熔炼 ,就 是把要 熔炼 的钢及 合金 原料制 作成 标
晶 , 而实现 了钢 的提纯 和结构均 匀 化[ 从 2 1 。非 自耗 炉
准形 状 的电极 , 过 电弧 的高温熔 化 , 通 再在 铜坩 埚 内 冷却 结 晶形 成 均匀 、 密 的合金 钢 , 致 同时 电弧 的超 高 温还 可 以去除 原料 中的气 体和 其他 杂质 。 因此 , 空 真 自耗 熔炼 方法 主要应 用 于难熔 高活 性金 属和超 高温 金属 的熔炼 。 空 自耗 电弧熔炼 一般 采用 短弧熔 炼 , 真
真空自耗电弧炉铜坩埚的受热与冷却计算

真空自耗电弧炉铜坩埚的受热与冷却计算自耗电弧炉是一种使用电能将电能转化为热能的设备,其主要应用于熔化金属材料。
在电弧炉的操作过程中,铜坩埚在高温环境下进行受热和冷却,因此需要进行相应的计算。
首先,需要计算铜坩埚的受热过程。
在电弧炉工作时,电能将通过电弧传导到铜坩埚上,使其达到高温。
可以通过下述公式计算铜坩埚的受热速率:Q=m*Cp*(T2-T1)其中,Q为受热速率,m为铜坩埚的质量,Cp为铜的比热容,T2为铜坩埚的最终温度,T1为铜坩埚的初始温度。
接下来,需要计算铜坩埚的冷却过程。
在停止供电后,铜坩埚会通过自然冷却失去热能。
一般情况下,可以使用牛顿冷却定律计算铜坩埚的冷却速率:Q=-h*A*(T2-T1)其中,Q为冷却速率,h为热传导系数,A为铜坩埚的表面积,T2为初始温度,T1为环境温度。
以上是计算铜坩埚的受热和冷却的基本原理,下面将对具体计算过程进行详细说明。
1.计算铜坩埚的质量:铜坩埚的质量可以通过称重或从产品规格中获取。
2.计算铜的比热容:铜的比热容为0.386J/(g·℃)。
3.计算受热过程的能量:根据上述公式,计算铜坩埚的受热速率。
需要输入初始温度和最终温度,以及铜坩埚的质量。
4.计算冷却过程的能量:根据上述公式,计算铜坩埚的冷却速率。
需要输入初始温度、环境温度,以及铜坩埚的表面积和热传导系数。
5.根据受热速率和冷却速率的差值,可以得到铜坩埚在操作过程中的热能损失。
需要注意的是,以上计算仅为基本的理论计算,实际计算过程需要考虑其他因素的影响,例如电弧炉的具体工作情况、炉温的稳定性等。
此外,铜坩埚的材料和结构也会对受热和冷却过程产生影响,因此在实际运行中需要进行更为详细的计算和试验。
总之,铜坩埚的受热和冷却计算是电弧炉操作过程中的重要环节,可以通过理论计算和实验验证相结合的方法来得到更准确的结果。
这些计算结果对于保证电弧炉的正常运行和提高生产效率具有重要意义。
ZHTF01型1.5T真空自耗电弧炉的研制
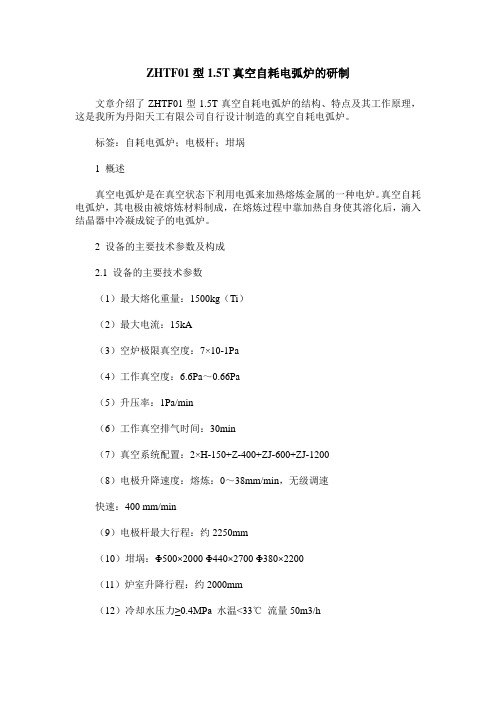
ZHTF01型1.5T真空自耗电弧炉的研制文章介绍了ZHTF01型1.5T真空自耗电弧炉的结构、特点及其工作原理,这是我所为丹阳天工有限公司自行设计制造的真空自耗电弧炉。
标签:自耗电弧炉;电极杆;坩埚1 概述真空电弧炉是在真空状态下利用电弧来加热熔炼金属的一种电炉。
真空自耗电弧炉,其电极由被熔炼材料制成,在熔炼过程中靠加热自身使其溶化后,滴入结晶器中冷凝成锭子的电弧炉。
2 设备的主要技术参数及构成2.1 设备的主要技术参数(1)最大熔化重量:1500kg(Ti)(2)最大电流:15kA(3)空炉极限真空度:7×10-1Pa(4)工作真空度:6.6Pa~0.66Pa(5)升压率:1Pa/min(6)工作真空排气时间:30min(7)真空系统配置:2×H-150+Z-400+ZJ-600+ZJ-1200(8)电极升降速度:熔炼:0~38mm/min,无级调速快速:400 mm/min(9)电极杆最大行程:约2250mm(10)坩埚:Φ500×2000 Φ440×2700 Φ380×2200(11)炉室升降行程:约2000mm(12)冷却水压力≥0.4MPa 水温<33℃流量50m3/h(13)应急水压力:0.1MPa 水温<33℃流量30m3/h(14)压缩空气压力:0.3~0.5MPa 用量150l/min 空压储气罐0.6m3 压力0.7MPa2.2 设备的构成该设备主要由以下几部分构成:(1)主传动系统;(2)真空炉室及动密封;(3)坩埚及稳弧系统;(4)真空系统;(5)炉室升降装置;(6)观察摄像系统;(7)压缩空气系统;(8)冷却水系统;(9)自动熔炼控制系统。
3 设备主要部分工作过程和结构特点3.1 主传动系统主传动系统包括电极杆、传动系统。
电极杆为双层水冷结构,传动采用数字控制交流伺服电机,驱动滚珠丝杠,以满足熔炼时的快速反应;电极杆的运行速度及电极杆的位置可在操作室进行数字显示。
5--10公斤自耗炉
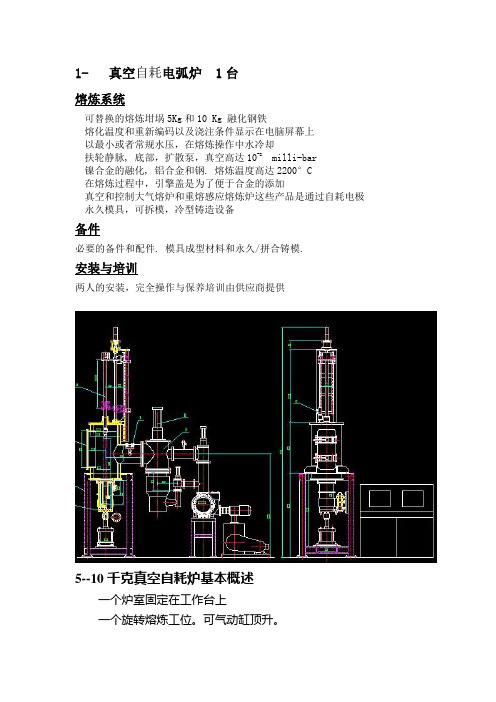
1- 真空自耗电弧炉 1台熔炼系统可替换的熔炼坩埚5Kg和10 Kg 融化钢铁熔化温度和重新编码以及浇注条件显示在电脑屏幕上以最小或者常规水压,在熔炼操作中水冷却扶轮静脉, 底部,扩散泵,真空高达10-8 milli-bar镍合金的融化, 铝合金和钢. 熔炼温度高达2200°C在熔炼过程中,引擎盖是为了便于合金的添加真空和控制大气熔炉和重熔感应熔炼炉这些产品是通过自耗电极永久模具,可拆模,冷型铸造设备备件必要的备件和配件. 模具成型材料和永久/拼合铸模.安装与培训两人的安装,完全操作与保养培训由供应商提供5--10千克真空自耗炉基本概述一个炉室固定在工作台上一个旋转熔炼工位。
可气动缸顶升。
一个KTZJ300.600油增压泵真空系统一个2000安熔炼电源电源满足熔炼4公斤钛及钛合金锭,5.5公斤锆及锆合金锭,7公斤铁及铁合金锭的需要。
环境要求:提供厂房:梁下4000。
设备电源供电电压为:3 相4线AC 380V±7%土木基础施工。
地平处理混凝土浇注厚度大于200mm采购方配合试车工作电网频率:50Hz±1%压缩空气:压力0.6MP a(如有需要)惰性气体(氩气)气体压力:0.4~0.8 MPa(工业冷水机)提供的循环冷却水:进水温度2℃-20℃,进水压力0.25-0.3Mpa,流量8m3/h应急水:压力:0.2-0.3MP a,(由发电机带动冷水机)海绵钛电极密度:3.3 g/cm3(最小)、钛锭4.5海绵锆电极密度:4.7 g/cm3(最小)、锆锭6.5基本技术参数最大熔化重量:≥5.5Kg锆及锆合金(密度6.5g/cm3)海绵钛电极密度:3.4kg/dm3最大熔炼电流:2000A电极杆最大行程:750mm下炉室升降行程: 100mm开路电压:68V工作电压:20-45V真空系统:一台ZL300油增压泵+一台 ZJ-600罗茨泵+一台2H-70滑阀泵泵电极升降速度:0~280mm/min,无级快速速度:500 mm/min极限真空度:≤7×10-2Pa工作真空度: 10-0.67Pa升压率:≤0.1Pa/min)抽空时间从大气压达到0.1Pa ,≤15分钟。
金属冶炼工艺

金属冶炼工艺EAF:电弧炉(electric arc furnace)利用电极电弧产生的高温熔炼矿石和金属的电炉。
气体放电形成电弧时能量很集中,弧区温度在3000℃以上。
对于熔炼金属,电弧炉比其他炼钢炉工艺灵活性大,能有效地除去硫、磷等杂质,炉温容易控制,设备占地面积小,适于优质合金钢的熔炼。
AOD:氩氧脱碳法(argon-oxygen decarburization)AOD吹氧脱碳的原理是:吹入炉内的氧气进入钢液后、与钢液中的碳和铬反应,即:钢液中的碳和氧反应生成气态的一氧化碳[C]+{O}=(CO)↑钢液中的铬与氧反应生成氧化铬进入渣层 2[Cr]+3{O}=(Cr2O3)另外,钢液中的碳与渣中的氧化铬反应,将渣中的 Cr2O3还原为铬,重新回到钢液中。
3[C]+(Cr2O3)=2[Cr]+3(CO)反应平衡常数:K(T)=(aCr2•2PCO3)/(aC3•aCr2O3)式中,acr为钢液中铬的活度;ac为钢液中碳的活度;Pco为CO的分压;acr2O3为渣中Cr2O3 的活度。
由上式可见,碳-铬平衡是温度和一氧化碳分压的函数。
根据铁碳相图上碳和铬氧化反应吉布斯能曲线的相对位置关系,要达到降碳保铬,就得使碳优先于铬氧化,构成选择性的氧化关系。
通过向钢液中连续不断地吹入N2和Ar来降低CO分压,从而使上述反应向着生成CO的方向进行,将渣中的Cr2O3还原为铬溶入钢液中,从而达到降碳保铬的目的。
正因为AOD具有该功能,使得不锈钢生产采用高碳和高硅含量原材料成为可能,从而改善了整个不锈钢生产线的物料消耗,降低了冶炼成本费用。
VAR:真空电弧重熔(vacuum arc remelting) 一种利用电弧作热源在真空条件下熔炼金属的真空熔炼技术,它包括真空电弧双电极重熔和真空凝壳炉熔炼。
真空电弧重熔的原理是:在无渣及真空条件下,金属电极在直流电弧的高温作用下迅速熔化并在水冷铜结晶器内进行再凝固。
当液态金属以薄层形式形成熔滴通过近5000K的电弧区域向结晶器中过渡以及在结晶器中保持和凝固的过程中,发生一系列的物理化学反应,使金属得到精炼,从而达到净化金属、改善结晶结构、提高性能的目的。
- 1、下载文档前请自行甄别文档内容的完整性,平台不提供额外的编辑、内容补充、找答案等附加服务。
- 2、"仅部分预览"的文档,不可在线预览部分如存在完整性等问题,可反馈申请退款(可完整预览的文档不适用该条件!)。
- 3、如文档侵犯您的权益,请联系客服反馈,我们会尽快为您处理(人工客服工作时间:9:00-18:30)。
书山有路勤为径,学海无涯苦作舟
真空自耗电弧炉(VAR)的工作原理与特点
世界上第一台真空自耗电弧炉是于1950 年在美国诞生的。
真空自耗电弧炉是在真空室中利用电弧的能量来熔炼金属的一种电炉。
真空自耗电弧炉主要用来熔炼钛、锆、钼等活泼金属和难熔金属,也用来熔炼耐热钢、不锈钢、工具钢、轴承钢。
上个世纪五十年代初,用来重熔高温合金,显示出极好的优越性,真空技术网(chvacuum/)认为成为高温合金和特殊钢重熔的重要手段之一。
1、真空自耗电弧炉的工作原理
真空自耗电弧炉结构示意首先,在自耗电极下端部同结晶器之间燃起电弧,自耗电极下端部同熔池之间形成电弧等离子区,该区具有极高的温度,能使自耗电极端部首先在这里被熔化掉。
随着自耗电极中一些非金属夹杂物,如氧化物、氮化物,在真空和高温条件下,发生离解或被碳还原而被去除掉,达到进一步提纯的目的。
由于真空自耗电弧炉工艺能去除气体和非金属夹杂物,以及去除某些低熔点的有害杂质,从而使冷、热加工性能、塑性和力学性能、物理性能得到明显改善。
特别是改善了纵向和横向性能的差异,这对保证材料性能的稳定性、一致性和可靠性有着极其重要的意义。
为了获得高质量锭子,熔炼过程中要求熔炼功率稳定,对供电电源要求具有
恒流特性的直流电流。
真空自耗电弧炉用的硅整流电源主回路示于上述硅整流装置的参数为:
(1)在20-40V 工作电压范围内具有恒流特性,空载电压在70V 左右。
(2)电流调节范围为1:10。
(3)当各整流臂中有10%硅元件损坏时,系统会发出信号,但能在额定电流下继续运行。