长庆油田井筒腐蚀机理与防护
油气井腐蚀防护与材质选择指南

油气井腐蚀防护与材质选择指南油气井腐蚀防护与材质选择指南1. 引言腐蚀问题一直是油气开采行业必须面对的挑战之一。
不仅会对设备和管道造成损害,还可能影响沉积物的生成,对环境产生负面影响。
油气井腐蚀防护和正确的材质选择是确保油气生产安全和可持续性的重要措施。
2. 了解油气井腐蚀2.1 腐蚀的原因油气井腐蚀主要是由于地下环境中存在的氧气、水分、硫化物、氯化物以及其他腐蚀性成分对管道和设备的作用。
这些成分与金属相互作用,形成电化学反应造成腐蚀。
2.2 类型和特点油气井腐蚀可分为两种主要类型:一是均匀腐蚀,即金属表面受到均匀的腐蚀,导致金属材质逐渐减薄;二是局部腐蚀,即金属表面受到局部的腐蚀,出现蚀坑和裂纹。
均匀腐蚀通常是由化学环境引起的,而局部腐蚀则与电化学因素有关,如局部阳极和阴极反应的差异。
3. 油气井腐蚀防护措施3.1 涂层保护对于油气井设备和管道,涂层是最常见和有效的腐蚀防护措施之一。
常用的涂层材料包括环氧树脂、聚脲、聚氨酯等。
这些涂层能够提供物理障壁,阻止金属与腐蚀性成分接触,从而减缓腐蚀的发生。
3.2 电化学防护电化学防护是一种通过外加电流,使金属表面保持阳极或阴极状态,从而减少腐蚀的方法。
常用的电化学防护技术包括阴极保护和阳极保护。
阴极保护通过向金属表面供应自由电子,使其成为阴极,从而阻止腐蚀反应发生。
阳极保护则是通过向金属表面提供阳极,将腐蚀反应引导到阳极上,从而保护金属。
3.3 材质选择正确的材质选择在油气井腐蚀防护方面至关重要。
应根据油气井地下环境的特点和腐蚀性成分来选择合适的金属材质。
常见的耐蚀材料包括不锈钢、镍基合金和钛合金等。
这些材料具有良好的耐腐蚀性能和机械性能,能够在恶劣的环境下保持良好的稳定性。
4. 深度探讨油气井腐蚀防护与材质选择4.1 腐蚀机制研究对于油气井腐蚀问题,了解腐蚀机制的研究非常重要。
通过实验和模拟,可以深入了解腐蚀反应的动力学和机理,以及腐蚀性成分与材料之间的相互作用。
油田余热换热装置腐蚀结垢机理及防护措施

油田余热换热装置腐蚀结垢机理及防护措施油田余热换热装置腐蚀结垢机理及防护措施摘要:油田余热换热装置在油田生产中起着至关重要的作用。
然而,腐蚀和结垢问题给其运行带来了极大的困扰。
本文对油田余热换热装置的腐蚀和结垢机理进行了探讨,并提出了相应的防护措施,以期能够降低装置运行中的损失,提高其使用寿命。
一、引言在油田生产中,油田余热换热装置扮演着至关重要的角色。
该装置可以通过回收和利用油田产生的余热,以提高能源利用效率。
然而,由于油田产生的热能和介质本身的特性,油田余热换热装置容易出现腐蚀和结垢问题,严重影响其正常运行和使用寿命。
因此,了解其腐蚀和结垢机理,并采取有效的防护措施,对于提高设备的使用寿命和经济效益具有重要意义。
二、腐蚀机理1. 化学腐蚀:油田余热换热装置经常与含有酸性成分的介质接触,容易发生化学腐蚀。
酸性介质会与金属产生化学反应,形成金属离子或金属化合物,进而腐蚀设备。
另外,介质中的氧和水也能加速金属的腐蚀速度。
2. 电化学腐蚀:油田介质的电导率较高,容易形成腐蚀电池,加剧设备的腐蚀。
例如,当金属表面存在阳极和阴极区域时,阳极会发生氧化反应,阴极则会发生还原反应,从而产生电流,加速金属的腐蚀速度。
三、结垢机理1. 水垢:水中存在的溶解固体物质在高温下会析出形成水垢。
这些水垢可以来自水中溶解的钙、镁、硫酸盐等物质。
水垢的形成会减弱热传导能力,降低换热效率,从而影响装置的运行。
2. 油垢:油田介质中含有大量的油脂和胶体颗粒,这些物质容易附着在管道表面上形成油垢。
油垢的形成不仅减缓了热传导速度,还降低了换热效率,增加了设备的能耗。
四、防护措施1. 物理防护:合理设计和安装防护设备,如沉淀器、过滤器、过滤网等,能够有效阻止颗粒物质进入装置内部,减少结垢发生的可能性。
2. 化学防护:采用化学处理剂或添加剂,例如缓蚀剂、抑制剂等,将其添加到介质中,能够减缓金属的腐蚀速度。
但需要注意选择合适的添加剂,避免对油田生产造成其他不良影响。
石油钻井机械设备腐蚀因素及防治技术

石油钻井机械设备腐蚀因素及防治技术摘要:油钻井机械设备是石油勘探和开采的重要工具,其正常运行和安全性直接关系到油田的生产效率和经济效益。
然而,在恶劣的工作环境下,这些设备容易受到腐蚀的影响,导致性能下降、寿命缩短,甚至引发事故。
为了保证设备的可靠性和安全性,必须采取有效的腐蚀防治技术来减少腐蚀的发生和进一步损坏。
本文结合实际,对石油钻井机械设备防腐控制的作用于控制技术进行分析。
关键词:石油工程;钻井机械;设备腐蚀;防治技术引言石油钻井机械设备在作业过程中容易受到腐蚀的影响,导致设备性能下降、寿命缩短甚至发生事故。
因此需要结合实际情况,采取有效的防治技术对存在的问题处理,保证机械设备不受到影响。
1石油钻井机械设备防腐控制的作用石油钻井机械设备在恶劣的工作环境中经常接触到腐蚀性物质,如盐水、酸性溶液和高温高压气体等,因此进行防腐控制对于设备的正常运行和寿命的延长至关重要。
首先,防腐控制有效阻止腐蚀物质对机械设备表面的侵蚀。
选择适合的防腐涂层或涂料,在机械设备表面形成一层保护膜,防止腐蚀物质直接接触金属表面,减少腐蚀的发生。
其次,防腐控制减少设备的损耗和损坏。
腐蚀会导致设备表面的金属材料逐渐腐蚀、磨损甚至破裂,从而影响设备的性能和可靠性。
有效的防腐控制,降低设备的维修频率和维修成本,延长设备的使用寿命。
其三,防腐控制还能提高工作安全性。
腐蚀会导致设备的结构强度下降,从而增加事故发生的风险。
对机械设备进行防腐处理,保证设备的结构完整性和稳定性,减少事故的发生,保障工作人员的安全。
2石油钻井机械设备腐蚀因素石油钻井机械设备在工作过程中会面临多种腐蚀因素,这些因素会导致设备的腐蚀和损坏,以下是一些常见的腐蚀因素。
2.1盐水腐蚀石油钻井过程中使用的钻井液中含有盐分,当盐水与机械设备表面接触时,会引起盐水腐蚀,导致设备表面的金属材料受损。
在钻井过程中,钻井液中的盐分成分是一个重要的腐蚀因素。
当钻井液中的盐水与机械设备表面接触时,会引发盐水腐蚀问题。
采油厂注水井腐蚀原因分析与防护

能源环保与安全一、前言在注水井注水过程中,注水水质复杂、环境多变,造成注水井腐蚀结垢严重。
每年作业井更换油管长度高居不下,主要原因为腐蚀、结垢严重造成,结合油田注水水质及环境变化情况,分析注水井腐蚀原因,实施有效的腐蚀、结垢防护措施具有重要的意义。
二、注水井腐蚀现状我采油厂自2011年以来共实施水井有效作业48井次,更换修复油管7万米,使用新油管5963米,防腐油管4210米,新油管和防腐油管使用比例严重偏低,酸化井5口,1000-2000m底部腐蚀结垢严重,结垢物质多为硬质结核;15年平均置换量为1871m/井,16年平均置换量为1482m/井,17年平均置换量为1317m/井,18年平均置换量为1917m/井。
其中夏52-209井和夏52-27井出现油管落井现象,腐蚀结垢趋势加剧。
三、注水井柱结构腐蚀原因1.洗井方式适应性评价。
(1)一种回水管路洗井方式,具有时间充足、成本低、灵活性且能保证洗井水量,但该洗井方式最大的缺点是洗井排量仅为13-16m3/H,对井筒的冲刷能力不足,主要是因为大部分洗井回水管道被油井生产管道取代,位移大时压力过高,容易造成管道破裂;其次,当洗井出口污水进入混输管道时,它会引起混输管道干压升高,容易造成混输穿孔。
(2)洗井车洗井,洗井方式理论排量为30m3/H,洗井冲洗能力理论上是好的,洗井水质足以随时观察。
洗井车数量有限,受道路、天气、工农关系等因素影响较大。
它有很大的局限性;其次,自吸井、严重溢流井不能完全循环,洗井效果不好。
针对以上问题,采油厂制定了详细的洗井方案,确保道路畅通。
由专人全程监督,提高洗涤人员的业务素质。
(3)槽车洗井流量可达30m3/H以上,洗井流量较大且井筒内污水可完全置换,无污水循环,洗井效果最好,主要用于注泥井。
为避免井筒内的污泥再次沉降,每次保证至少2-3辆槽车。
井底只能看到8次以上的返清水,同时,受天气和道路影响严重。
另外,注泥浆井套管往往不光滑,洗井过程中压力容易被抑制。
油气田的腐蚀与防护 ppt课件

(a)
(b)
图2.1 P110试样表面腐蚀产物膜结构和特征。(a)呈现蜂窝状腐 蚀,(b)口小底大烧瓶型
ppt课件
16
5. 温度对二氧化碳腐蚀机理的影响
低温,腐蚀产物膜 中 温 , 100oC 左 右 ,高 温 , 约 大 于
少,均匀腐蚀
膜局部破裂,局部 150oC , 膜 致 密 ,
ppt课件
13
3.二氧化碳腐蚀常见形态
– 国际研究普遍认为:
CO2局部腐蚀有以下三种典型机理 – 台地状腐蚀 – 蜗旋状腐蚀 – 点状腐蚀 – 我们研究发现,腐蚀后试样表面呈现为图2.1所示的蜂窝状和 底 大口小的烧瓶型点状腐蚀
ppt课件
14
ppt课件
15
4.微观腐蚀形态
(a)
闭塞电池效应很强:外大阴极,
(1-1)
ppt课件
10
几种典型腐蚀介质的腐蚀速率对比图
ppt课件
11
三 二氧化碳腐蚀简介
1. 反应机理: 阳极反应机理 Fe=Fe2+ +2e
Fe + HCO3-=FeCO3 +2e+H+ Fe+CO32-=FeCO3 +2e 也有认为初始腐蚀产物为Fe(OH)2,或Fe(HCO3)2 Cr+ 3OH- =Cr(OH)3+ 3e
» —— 高温和/或高压环境
» —— H2S、CO2、O2、Cl-和水分是主要腐蚀物质
» H2S、CO2、O2 是 腐蚀剂
» 水
是 载体
» Cl-
是 催化剂
– 就H2S、CO2和O2三种腐蚀剂来说,其腐蚀速率相对
分析油田注水采油设备的腐蚀与防护

分析油田注水采油设备的腐蚀与防护针对油田注水采油设备腐蚀原因进行科学的分析,并简要介绍了油田注水采油设备的特点,如作业风险比较大、成本高、系统复杂等,提出油田注水采油设备的腐蚀类型与防护措施,能够有效延长注水采油设备的使用寿命,希望可以给相关人员提供良好的借鉴与参考。
标签:油田注水采油设备;腐蚀;防护伴随油田开发力度的不断加大,原油含水量逐渐提升,地面输水与输油管线,包括井下油管与注水管线出现了严重的腐蚀现象。
通过对油田注水采油设备腐蚀状况进行全面的调查得知,水当中的溶解氧与硫化氢,会对油田注水采油设备产生严重腐蚀。
为了有效延长油田注水采油设备的使用寿命,本文重点研究油田注水采油设备腐蚀原因与防护措施。
1油田注水采油设备的特点分析油田注水采油技术难度比较大,操作流程较为复杂,通常集中在较大面积的平台上,一座采油平台类似复杂工厂。
油田注水采油设备具有以下特点:第一,作业风险比较大,成本较高,因为油田注水采油设备操作难度较大,具备较大的风险性。
第二,油田注水采油系统复杂,特别容易发生腐蚀,受大气中水蒸气的影响,增加油田注水采油设备发生腐蚀现象的概率。
2油田注水采油设备的腐蚀与防护措施2.1油田注水采油设备腐蚀原因2.1.1缝隙腐蚀油田注水采油设备内部金属部件比较多,不同的金属部件之间存在比较小的缝隙,而缝隙之中的介质呈现滞留态,使得缝隙内部的金属部件发生腐蚀,此种腐蚀经常被人们称作缝隙腐蚀。
因为油田注水管道内部结构特别复杂,管道内部的金属表层经常出现砂泥与积垢,容易引发缝隙腐蚀现象[1]。
2.1.2孔蚀在油田注水采油设备表面,经常会出现向深入发展的腐蚀孔,这些腐蚀孔比较小,又常被人们称为孔蚀或者点蚀。
一般来讲,孔腐蚀通常发生在表面较为钝化的金属部件上,碳钢表层出现孔隙,在含氯离子的水之中,也会发生孔腐蚀现象。
孔腐蚀现象特别常见,对油田注水采油设备的安全运行产生较大影响。
孔腐蚀现象的发生与发展共分成两阶段,分别是腐蚀孔的成核与腐蚀孔生长,若金属部件位于腐蚀介质当中,因为介质内部的活性阴离子能够有选择性的直接吸附于金属钝化膜之上,和钝化膜阳离子有效结合,会形成可溶性的氯化物质,在新露出基底金属表层形成较小的腐蚀坑,这些腐蚀坑被人们称作腐蚀核。
油气田的腐蚀与防护技术

(二) H2S环境导致的输送管损伤
2.1 SSC (Sulfide Stress Cracking)—(硫化物应力腐蚀开裂)
2.1.2 材料因素 (4)冷变形——增大硬度,引入残余拉应力
(二) H2S环境导致的输送管损伤
2.1 SSC (Sulfide Stress Cracking)—(硫化物应力腐蚀开裂) 2.1.2 材料因素 (5)焊缝SSC的控制(适用于510MPa管线焊缝) ① 合理选择焊接材料与工艺: 焊丝、焊剂匹配保证焊缝与母材等强度;
硫化物环境中输送管的主要腐蚀 类型
(一)钢在H2S环境中的腐蚀机理:
(1)H2S的性质
① 摩尔质量:34.08g/mol
② 密度:1.539g/L(25℃);相对空气密度:1.1906(空气=1) ③ 在水中的溶解度大:3480mg/L(25℃,0.1MPa),大于CO2和O2
④ 腐蚀性:干H2S无腐蚀性;溶于水后有强的腐蚀性
(二) H2S环境导致的输送管损伤
2.1 SSC (Sulfide Stress Cracking)—(硫化物应力腐蚀开裂)
2.1.1 环境因素 (1)H2S浓度:酸性天然气—总压0.4MPa,H2S气压>0.0003MPa 在满足上述条件的环境中敏感材料易产生SSC破坏。
酸性天然气系统 (天然气体积是在0℃, 0.101325MPa状态下) H2S/CO2>1/500时, H2S腐蚀为主
油田注水系统管线历年穿孔柱状图
穿孔次数
4500 4000 3500 3000 2500
4072
2632
1801
2000 1500 1000 500 0
1321
1122 841
油井偏磨腐蚀的机理分析及防治对策
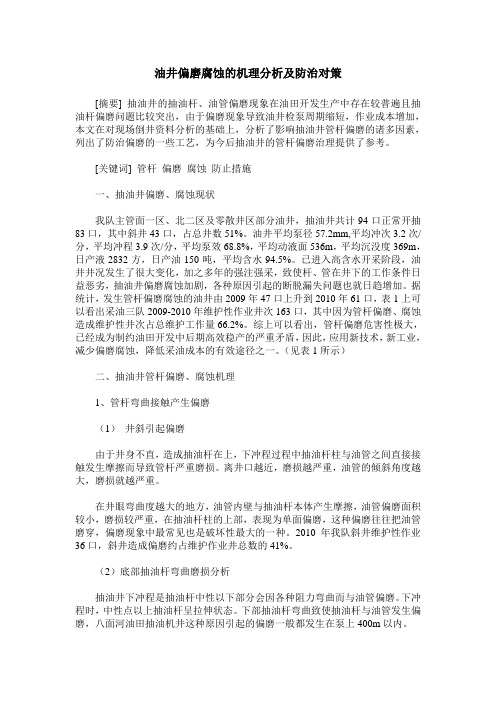
油井偏磨腐蚀的机理分析及防治对策[摘要] 抽油井的抽油杆、油管偏磨现象在油田开发生产中存在较普遍且抽油杆偏磨问题比较突出,由于偏磨现象导致油井检泵周期缩短,作业成本增加,本文在对现场倒井资料分析的基础上,分析了影响抽油井管杆偏磨的诸多因素,列出了防治偏磨的一些工艺,为今后抽油井的管杆偏磨治理提供了参考。
[关键词] 管杆偏磨腐蚀防止措施一、抽油井偏磨、腐蚀现状我队主管面一区、北二区及零散井区部分油井,抽油井共计94口正常开抽83口,其中斜井43口,占总井数51%。
油井平均泵径57.2mm,平均冲次3.2次/分,平均冲程3.9次/分,平均泵效68.8%,平均动液面536m,平均沉没度369m,日产液2832方,日产油150吨,平均含水94.5%。
已进入高含水开采阶段,油井井况发生了很大变化,加之多年的强注强采,致使杆、管在井下的工作条件日益恶劣,抽油井偏磨腐蚀加剧,各种原因引起的断脱漏失问题也就日趋增加。
据统计,发生管杆偏磨腐蚀的油井由2009年47口上升到2010年61口,表1上可以看出采油三队2009-2010年维护性作业井次163口,其中因为管杆偏磨、腐蚀造成维护性井次占总维护工作量66.2%。
综上可以看出,管杆偏磨危害性极大,已经成为制约油田开发中后期高效稳产的严重矛盾,因此,应用新技术,新工业,减少偏磨腐蚀,降低采油成本的有效途径之一。
(见表1所示)二、抽油井管杆偏磨、腐蚀机理1、管杆弯曲接触产生偏磨(1)井斜引起偏磨由于井身不直,造成抽油杆在上,下冲程过程中抽油杆柱与油管之间直接接触发生摩擦而导致管杆严重磨损。
离井口越近,磨损越严重,油管的倾斜角度越大,磨损就越严重。
在井眼弯曲度越大的地方,油管内壁与抽油杆本体产生摩擦,油管偏磨面积较小,磨损较严重,在抽油杆柱的上部,表现为单面偏磨,这种偏磨往往把油管磨穿,偏磨现象中最常见也是破坏性最大的一种。
2010年我队斜井维护性作业36口,斜井造成偏磨约占维护作业井总数的41%。
- 1、下载文档前请自行甄别文档内容的完整性,平台不提供额外的编辑、内容补充、找答案等附加服务。
- 2、"仅部分预览"的文档,不可在线预览部分如存在完整性等问题,可反馈申请退款(可完整预览的文档不适用该条件!)。
- 3、如文档侵犯您的权益,请联系客服反馈,我们会尽快为您处理(人工客服工作时间:9:00-18:30)。
总反应为: 4F e + SO4 + 4 H 2O
+ 2-
SR B
3Fe( OH ) 2 + F eS + 2OH
22+
-
此外采出液中常溶有少量 的 H 2 S , H 2 S 在水溶液 中会电离出 H 、 H S 和 S , 也能够与 F e 作用生成 F eS , 电离出的 H 则在钢铁表面使铁发生氢去极化腐 蚀。同时, H 也是参与硫酸盐还原菌作用的物质, 大 大促进了 SRB 的作用, 细菌、 化学腐蚀互相促进 , 使钢 铁腐蚀进一步加剧
2-
与金属 F e反应后生成 FeCO 3 和 F e3 O4。同时 , 溶液中 的 CO3 和 HCO 3 还可与 Ca 、 M g 发生反应 , 生成 CaCO3、 M gCO3 沉淀, 或悬浮在介质中或覆盖在金属表 面成为腐蚀产物的一部分。由于 CaCO3、 M gCO3 属于 同构类质晶体 , 因 此膜层中可夹杂复盐 ( C a , M g ) CO 3
井筒腐蚀导致的井下管柱穿孔、 挤扁、 断落, 不仅 给试修作业带来很多复杂情况, 也严重影响油井正常 生产 。因此 , 井筒腐蚀问题已成为制约油田经济效 益的瓶颈技术之一。
[ 1]
非常严重。现场腐蚀严重的生产井具有以下特点: ( 1) 采出液呈弱酸性 , 硫酸盐还原菌 ( SRB) 、 矿化 度和 C l 浓度高, 且含有少量溶解 氧。表 1 为 该油田 部分油井采出液分析数据。 ( 2) 产液量不高、 含水率高。从表 2 可以看出 , 腐 蚀严重的油井产液量不是很高 , 但含水率都较高, 单井 平均液量 15 t /d , 含水率在 90 % 左右。
超过 65 % (w )以上。
表 3 部分油井井筒腐蚀产物 XRD 分析结果 井号 X - 1 井 66. 77 15. 78 X - 3 井 80. 77 7. 54 腐 蚀产物及含量 , w , % , M g ) CO3 F eCO3 FeS F e2 O 3 FeO ( OH ) Fe3 O4 ( Ca 4. 56 2. 34 3. 21 1. 40 7. 34 4. 57 2 . 34 3 . 38
-
1 井筒腐蚀情况调查
所调查油田属于长庆油田的一个主产油田, 已开 采近 30 年, 为低 压低渗透油藏。随着开采时 间的延 长 , 采收率下降, 油井含液量逐年上升 , 井筒腐蚀穿孔
表 1 部分 油井采出液分析数据 井号 X - 1井 X - 2井 X - 3井 X - 4井 X - 5井 离子含量 , m g /L N a+ + K+ 15 159 4 697 21 187 5 487 24 159 Ca2+ 655 705 913 187 875 M g2+ 507 126 654 94 516 C l15 668 5 323 30 012 5 711 32 528 SO 24 12 368 4 305 7 441 3 867 9 314 HCO 3 2 074 583 1 132 844 1 517 F e2+ 0. 78 0. 51 0. 60 1. 01 0. 20 矿化 度 g /L 46. 43 15. 74 61. 34 16. 19 68. 91 溶解氧 mg /L 1. 54 0. 46 0. 23 0. 67 1. 12 pH 值 6. 21 6. 42 6. 02 6. 73 6. 42 SRB 个 /mL 128 210 167 58 274
[ 2] + +
。黑色的硫化亚铁 ( FeS) 稳定性
较好, 与其它垢物结合常附着于泵筒和管壁上 , 使其与 管壁之间形成更适合于 SRB 生长的封闭区, 进一步加 剧井筒管壁的腐蚀, 在管壁形成严重的坑蚀或局部腐 蚀。虽然在采出液中未检测出 H 2 S , 但并不表示在井 下就不存在 H 2 S , 可能由于 H 2 S 含量少而未检测出。 ( 2) 溶解氧腐蚀。油层水中少量的溶解氧可引起 腐蚀, 其腐蚀 产物 主要 为铁 锈 F e2 O3 或 针铁 矿 FeO ( OH ) , 在腐蚀产物内部, F eOOH 还可以与 F e 结合, 生成 Fe3O 4。由此可推测在 X- 1 和 X- 3 两口井的井 筒垢样中存在的少量 Fe2 O3、 F eO ( OH ) 以及 Fe3 O4 是 采出液中溶解氧的腐蚀产物。 ( 3 ) CO2 腐 蚀。 采出 液 中溶 解 的 少量 CO2 与 Ca 、 F e 等离子 , 在一定条件下可生成 C aCO3 和 F e CO3, 形成腐蚀垢物 , 导致垢下腐蚀。溶液中的 H CO 3
22+ 2+ 2+ 2+ 2+
3 井筒腐蚀机理分析
通过对现场油井腐蚀情况的调查及室内高温高压 腐蚀模拟试验, 得出该油田井筒腐蚀机理如下 : ( 1) 细菌腐蚀。该油田油井采出液中含有大量的 SRB、 铁细菌 ( IB )、 硫细菌等菌种 , 这些菌种潜伏在地 层水和岩石中, 当开采生成的新环境有利于细菌生长 时 , 这些菌种就会大量繁殖。在这些菌种的影响中以 SRB 腐蚀最具代表性。硫酸盐中的 SO4 常存在于地 层水中 , 通常情况下, 地层水中的 SRB 含量较低 , 这主 要是因为地层高温、 高压和高矿化度等因素限制了它 们的生长, 同时在地层中因缺少有机营养 , SRB 菌很难 大量繁殖。随着采出液被提升, 由于温度、 压力、 流速 的变化 , SRB 生长环境发生了变化 , 使得 SRB 迅速繁 殖 , 含量激剧升高。在 SRB 作用下 , 井 筒产生严重腐
针对长庆油田油井油管腐蚀穿孔断裂十分严重的现状, 通过现场调研和室内试验 , 对影响
腐蚀的各因素进行了分析并探讨井筒腐蚀机理 。结果表明 , 硫酸盐还原菌引起的细菌腐蚀和垢下腐蚀 是油井腐蚀结垢的根本原因, 其次是溶解氧、 二氧化碳及高矿化度采出液的电化学腐蚀 , 此外部分油井 井口结蜡, 上述因素的共同作用导致井筒腐蚀 。据此提出了预防井筒腐蚀的综合治理方案 , 可为油田井 筒防腐提供指导和借鉴作用。 关键词 井筒腐蚀 油井 油管 硫酸盐还原菌 防腐 细菌腐蚀 缓蚀剂
石 油 与 天 然 气 化 工
第 35 卷 第 4期 CHEM I C AL ENG INEER ING OF O IL & GAS
313
成分。 ( 4) 结垢。在采出液中, 当 Ca 、 Mg 、 Ba 的浓 度达 到 [ M
22+ 2+ 2+ 2+
杂质含量低的耐腐蚀合金油套管, 可提高井下管柱的 抗蚀能力。因为 Cr 含量增加, 可增加钝化膜 的稳定 性 , M o 含量增加 , 可减少 C l 的破坏作用。如重庆气 矿对部分油管腐蚀原因进行调查发现 , C r 和 M o 含量 高的油管, 其耐蚀能力强, Cr 、 M o 含量低的油管 , 易腐 [ 7] 蚀断裂 。若是 新开发 的高 产油 田, 从长 远角度 出 发 , 可考虑选用耐蚀性好的合金材料 ; 对年平均产量较 低的老油田 , 若采用耐蚀合金钢 , 势必提高其 采油成 本 , 这在实际措施中不可行 , 普遍采用价格便宜的 J55 和 N 80管材, 配合其它防腐措施。针对井筒动液面以 下腐蚀更为严重的情况, 可在油井下部采用涂层油管、 钢塑复合管以及耐蚀合金油管。 ( 2) 添加化学药剂。用化学方法除掉腐蚀介质或 者改变环境性质可以达到防腐目的 , 根据油 ( 气 ) 井腐 蚀环境和生产情况, 有针对性地选用缓蚀剂种类、 用量 及加注制度。这类化学药剂包括缓蚀剂、 杀菌剂、 除硫 剂、 除氧剂、 p H 值调节剂等。 ( 3) 对腐蚀恶劣的油井下永久性封隔器, 并在油 套环空充满含缓蚀剂的液体。采用这种方法既可避免 套管承受高压, 又可避免和防止酸性气体对油管外壁 和套管内壁的腐蚀。 ( 4) 油 ( 气 ) 井在进行酸化等增产作业时 , 应尽量 缩短酸液和油、 套管的接触时间 , 酸化后井内残酸应尽 量排尽 , 防止残酸对油套管的腐蚀; 在气井生产中尽量 防止井下积液, 避免产生井下腐蚀条件。 ( 5) 建立完善的腐 蚀监测系统 , 加强防腐管 理。 建立完善的腐蚀监测系统, 便于及时发现生产中出现 的腐蚀问题 , 及时采取科学的防腐措施。
312 度以 3
长庆油田油井井筒腐蚀机理与防护措施 / 100m 计算 ) , 井底温度不超过 80 , 井底压
2006
蚀 , 其腐 蚀产物 主要为含 硫化合物 垢类物质 ( F eS )。 以 X- 1 井采出液为腐蚀介质 , 腐蚀条件同前 , 取在培 养基中培养 2~ 7 天的 SRB 细菌 , 按 SY5329- 94 标准 计算菌量 , 考查 SRB 对试片腐蚀速率影响, 结果见表 4 。在相同条件下 , SRB 数量越多, 试片腐蚀越严重。
( 3) 腐蚀垢物中含硫化合物含量高。对 X- 1 和 X- 3 两口 井的井筒 内垢样 进行 X - 射线 衍射 分析 ( XRD ), 结果见表 3 , 发现腐蚀产物中 FeS 含量较高,
2 高温高压腐蚀试验
表 1 和表 2 所示的 5 口井资料分析知 : 该区块井 深 1 600~ 1 800 m 左右 ( 设地表温度为 25 X - 1井 X - 2井 X - 3井 X - 4井 X - 5井 井 深, m 1 744 1 792 1 688 1 629 1 613 固井情况 油层段良好 油层段良好 油层段合格 良好 合格 产液量 t/d 14. 82 12. 20 11. 61 21. 57 17. 78 产油量 t/d 0. 41 2. 44 0. 33 1. 78 0. 46 含水率 % 97 . 2 80 . 0 96 . 6 90 . 1 97 . 1
SRB 含量 , 个 /mL 腐蚀速率 , mm /a
8000~ 10000 0. 415
反应机理如下: 4Fe → 4Fe + 8e
+ + 2+ -