焊缝超声波探伤操作步骤
钢焊缝手工超声波探伤方法及质量分级法

钢焊缝手工超声波探伤方法及质量分级法(最新版5篇)《钢焊缝手工超声波探伤方法及质量分级法》篇1钢焊缝手工超声波探伤方法主要分为预扫查、正式扫查和结束扫查三个阶段。
预扫查阶段主要是为了选择最佳扫查面,确定最佳扫查角度,选择灵敏度最高的探头和适宜的仪器。
正式扫查阶段是超声探伤的关键,其操作方法随工件形状、焊缝形式、探头种类及探伤操作部位的不同而不同。
结束扫查阶段主要是对工件进行局部处理。
质量分级法包括如下内容:1. 对未焊透的评级:当缺陷尺寸小于等于评定标准规定的值时,不论其多少,只做合格品评定;当缺陷尺寸大于评定标准规定的值时,则不合格。
2. 对咬边深度评级:若咬边深度不超过评定标准规定的值,则只做合格品评定;若超过评定标准规定的值,则不合格。
3. 对声影评级:当声影不影响焊缝有效长度内的射线胶片时,只做合格品评定;当声影妨碍射线透入焊缝或妨碍焊缝射线胶片的读出时,则不合格。
4. 对波幅评级:根据缺陷回声最高波的波幅与该焊工、该焊道、该焊缝超声检测的评定标准所规定的要求相比,判定其合格或不合格。
《钢焊缝手工超声波探伤方法及质量分级法》篇2钢焊缝手工超声波探伤方法主要分为4个步骤:1. 表面处理:在探伤前,应将焊缝表面及附近区域彻底清理,以便于检测。
2. 操作人员:操作人员必须经过专业培训,熟悉操作规程,严格按工艺要求进行操作。
3. 探伤灵敏度:应根据母材钢材等级、焊接材料、工艺等因素确定探伤灵敏度。
4. 探伤操作:在探伤操作中,应按照标准规定的操作方法进行,注意检测角度、距离、斜率等参数的选择和调整。
对于手工超声波探伤结果的判定,一般采用《超声检测质量分级指南》(GB11345-89)中规定的标准进行质量分级。
该指南将焊缝质量分为5级,分别是A级、B级、C级、D级和E级。
其中,A级和B 级为合格级别,C级为基本合格级别,D级为不合格级别,E级为严重不合格级别。
《钢焊缝手工超声波探伤方法及质量分级法》篇3钢焊缝手工超声波探伤方法主要分为四个步骤:1. 准备工作:探头校直、探头零点调节、耦合剂的涂敷。
超声波探伤仪操作步骤完整版

超声波探伤仪操作步骤标准化管理处编码[BBX968T-XBB8968-NNJ668-MM9N]步骤一:校准(显示区只显示A扫图像)(1)声速校准(可同时计算出楔块延时和前沿距离)1 、直探头(以厚度校准为例)①范围:根据工件的厚度确定。
将一起检测范围调节到大于工件厚度的2倍。
②声速:5950m/s。
③探头角度:0度。
④增益:调节选择适当的增益。
⑤输入参考点1和参考点2的值。
(如下图,参考点1的值为100,参考点2的值为200)⑥移动闸门A,套住第一次底波,按压校准键,则回波1已校准。
⑦移动闸门A,套住第二次底波,按压校准键,则回波2已校准。
(计算公式:v=(s2−s1)t)同时可计算出楔块延时:t delay=s2v −2(s2−s1)v2、斜探头(以半径校准为例)①范围:根据工件的厚度确定。
如上图,将扫描范围调节到大于100mm。
②声速:5950m/s。
(是否按横波和纵波)③探头角度:先输入角度参考值,稍后在校正,角度在这里没有影响。
④增益:调节选择适当的增益。
⑤移动探头,找到R100圆弧面的最高反射波,输入参考点1和参考点2的值。
(如上图,参考点1的值为50,参考点2的值为100)。
平移探头到试块带R50圆弧面的一侧,使得R50圆弧面的反射波具有一定高度。
移动闸门A,选中R50圆弧面回波,按压校准键,则回波1已校准。
移动闸门A,选中R100圆弧面回波,按压校准键,则回波2已校准。
(计算公式:v=(s2−s1)t)同时可计算出楔块延时:t delay=s2v −2(s2−s1)v找到R100圆弧面的最高反射波,则前沿距离x=100-L。
(2)斜探头角度(K值)校准现在范围已调整好,声速及楔块延时已校准。
①进入K值校准菜单②输入孔深:(如下图,30mm)③输入孔径:(如下图,50mm)④增益:调节选择适当的增益。
⑤移动探头,找到50mm圆孔最高反射波。
⑥输入试块上入射点与试块上对齐的K值,按校准键确认。
超声波探伤作业指导书

1.仪器连接,开机1.1连接探头,探头线。
1.2按住“电源”键一秒种后,仪器显示有关仪器的信息。
此时按超声探伤即进入探伤画面。
如下图:2.调校仪器2.1按探伤调节对应的箭头。
选择通道选择,再选择“通道号”,输入想保存的某个通道号;选择“打开通道”2.2按探伤调节对应的箭头,选择探头参数,根据探头型号依次将探头类型、晶片尺寸、探头频率、探头K值设置正确(如下图),设置完成后按“返回”键。
2.3选择声速设定,检查当前声速是否正确,按“调节声速”键,可输入正确的声速值,斜探头的声速设置为3240。
设置完成后按“返回”键。
2.4选择零点偏移,选择“零点调节”,通过手动调节将标准试块的R100的最高反射波对准到仪器屏幕的100刻度值。
如偏移通过键盘上面得“+”“-”号调节。
设置完成后按“返回”键。
探头在试块上的位置屏幕显示波形2.5选择测试K值,依次将当前声速、标称K值、孔中心距、反射直径设置正确;进入“K值测试”后,即为仪器自动测试,请按照仪器提示操作。
K值大于等于2时将探头放在试块上端面找最高波;K值小于2时将试块翻转过来(使用试块的下端面)找最高波。
探头在试块上的位置屏幕显示波形3.制作DAC曲线3.1返回到主菜单(最上一级菜单)后,按“曲线”:选择DAC曲线,依次将DAC补偿、判废偏移、定量偏移、测长偏移按照探伤标准设置正确;3.2进入“开始制作”后,按照仪器提示操作,首先输入最浅点(第一点)的孔的深度后,按“回车”键,仪器将该点深度的最高波自动降至80%,请注意波形下降的过程中稳住探头,波形稳定后再前后小幅度移动探头,寻找是否还有更高的波形,确认最高波后,按“回车”键,即形成了DAC 曲线的第一个连接点;探头在试块上的位置屏幕显示波形3.3继续按照仪器提示,再分别输入某一个孔的深度,按“回车”键,再前后小幅度移动探头,寻找是否还有更高的波形,并确认最高波后,按“回车”键,即形成了DAC曲线的后面的连接点;仪器显示波形3.4 当所选择的所有DAC曲线点全部完成后,按“返回”键即完成了DAC曲线的制作并自动退出。
焊缝超声检测实操讲解

二.仪器的调整
3)探头前沿校准
M l0
R100
二.仪器的调整
3)探头前沿校准 校准时反射波不仅在圆弧面产生,在两个棱
数字式超声仪测试完一组不同深度的横孔 后,可输入判废线、定量线、评定线与基准线 的差值,自动生成距离-波幅曲线。
二.仪器的调整
(3)制作距离-波幅曲线
二.仪器的调整
(4)确定检测范围
调节仪器检测范围,将检测的最大距离 调整到屏幕横坐标的80%左右。
二.仪器的调整
(5)确定探伤灵敏度
探伤时以评定线灵敏度作为扫查灵敏度。 探测的最大距离处的评定线调至满屏20% , 探伤灵敏度调整完毕。
①将检测范围调整到检测使用的最大检测范 围,并调整好时基线扫描比例; ②根据工件厚度选择试块,选取试块上孔深 不小于检测深度的横孔为第一基准孔,将探 头置于试块探伤面声束指向该孔,调节探头 位置找到横孔的最高反射波;
二.仪器的调整
(3)制作距离-波幅曲线
③调节“增益”使该反射波幅为荧光屏上某一 高度(例如满幅的60%)该波高即为“基准波 高”,此时,探伤系统的有效灵敏度余量应不 小于10dB; ④调节增益,依次探测其它横孔,并找到最大 反射波,分别记录各反射波的相对波幅值( dB);
一.检测准备
⑶检测设备与材料: 仪器型号、探头规格参 数、试块种类、耦合剂等; ⑷检测工艺参数: 检测方法、仪器时基线比 例、检测灵敏度、检测面、表面补偿等; ⑸检测环境: 安全、检测空间、亮度等。
二.仪器的调整
超声波焊缝探伤操作简述
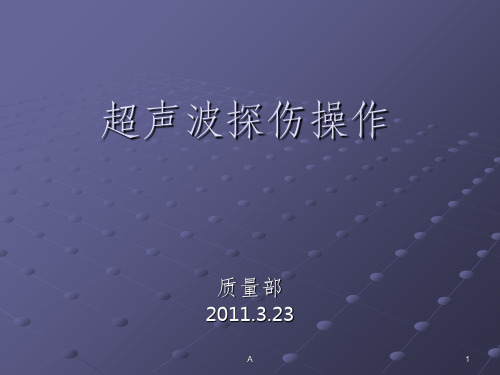
返回13
仪器的调校
5、遇有下述情况应对仪器进行重新核查:
1)、校准后的探头、耦合剂和仪器调节旋钮发生改 变时;
2)、开路电压波动或者检测者怀疑灵敏度有变化 时;
3)、连续工作4h以上时; 4)、工作结束时。
返回
A
14
其他辅助工具
1、卷尺(测量焊缝纵向距离尺寸) 2、直尺(测量水平距离尺寸) 3、耦合剂(机油、浆糊、水。。。) 4、刷子(在探测处涂抹耦合剂) 5、抹布(探伤后清理耦合剂) 6、文件夹及记录表格(记录探伤情况)
线、判废线分别设定为:“DAC-16dB”、“DAC-10dB”、
“DAC-4dB”。
5)、在DAC主菜单“曲线选择”设为“定量线”,另外工件表
面补偿一般要3、4dB,所以“增益校正”应设置为“3、
4dB”。
6)、在保存主菜单保存当前仪器状态设定及DAC曲线到空白的
数据集内,记录好该曲线的储存号。
A
超声波探伤操作
质量部
2011.3.23
A
1
前言
探伤目的:检查焊缝是否存在气孔、裂纹、 未焊透、未熔合等内部缺陷 使用标准:GB11345-89(适用于钢焊缝手 工超声波探伤) 使用仪器:CTS-2020汕头数字超声探伤仪
A
2
目录
1、工作原理 2、熟悉仪器面板 3、准备工作 4、探伤操作及缺陷的判定 5、整理工作
A
3
工作原理
脉冲反射法探伤原理
超声波具有方向性好、能量高、 能在界面上产生反射、穿透能 力强等特性,利用这些特性, 通过超声波探头发射脉冲波到 被检工件内,根据反射波的情 况来检测工件是否存在缺陷及 测量缺陷的大小!
A
返回 4
CTS-9006超声波探伤仪操作规程
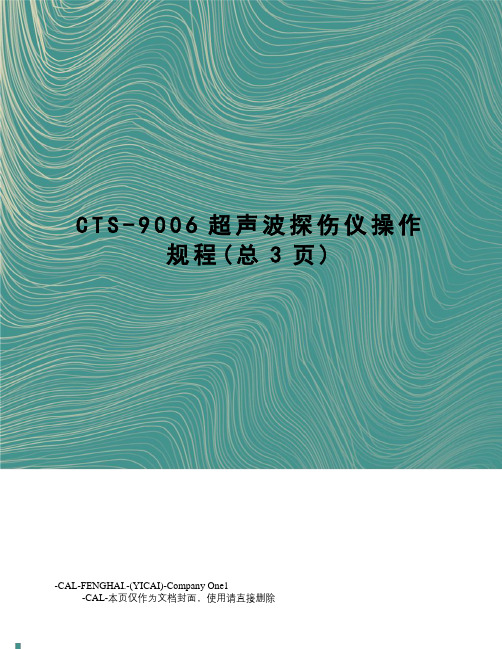
C T S-9006超声波探伤仪操作规程(总3页)-CAL-FENGHAI.-(YICAI)-Company One1-CAL-本页仅作为文档封面,使用请直接删除CTS-9006超声波探伤仪操作规程适用范围适用于母材厚度不小于8mm的铁素体类钢全焊透溶化焊对接焊缝脉冲反射法手工超声波检验。
一、主要技术指标:A型脉冲扫描,工作频率0.5~10MHz,总衰减量:110dB ,扫描范围:5~13000mm ,电源:DC-92)和充电/适配器(CD-92);二、操作方法1、斜探头检测1 )打开电源开关。
2 )设置仪器的初始参数:探测范围、声速、延迟、重复频率、频带、发射方式、阻尼、厚度(“基本”菜单中“)。
3)校正仪器零点及声速。
①按下“校正”键,切换到“自动校正”主菜单;②选择“选项”子菜单,调节为“声速”或“声速+零点”(校正声速将“选项”子菜单单设为“声速”;校正声速和零点将“选项”子菜单设为“声速+零点”);③选择“参照物1”子菜单,调节为参照物1的实际声程;④选择“参照物2”子菜单,调节为参照物2的实际声程;⑤选择“闸门起位”子菜单,调节闸门起位试闸门套住参照物1所对应回波,并调节增益或按“AGC”键,使回波幅度在80%左右,按“←”键,屏幕提示“请套住参照物2对应回波”。
⑥按⑤的调节方法使闸门套住参照物2所对应回波,并调节增益,使回波幅度在80%左右,按“←”键,屏幕提示“校正完成”。
此时对应显示的声速和零点为测量出的当前材料声速和探头零点。
4 )测量探头前沿长度:将探头置于标准CSK-IA试块,斜探头:利用R100圆弧测定探头的前沿,分别测定三次取平均值并输入到仪器中(“设置”菜单中)。
5)角度测量①按“校正”键,然后选择“角度测量”子菜单,再按“←”键切换到“角度测量”的扩展子菜单;②选择“孔深”扩展子菜单,调节为实际使用试块反射孔的深度;③选择“孔径”扩展子菜单,调节为实际使用试块反射孔的孔径;④选择“闸门起位”扩展子菜单,调节闸门起位试闸门套住反射孔回波,并来回移动探头是反射孔回波幅度最高;⑤调节增益或按“AGC”键。
超声波探伤30mm厚板对接焊缝实例
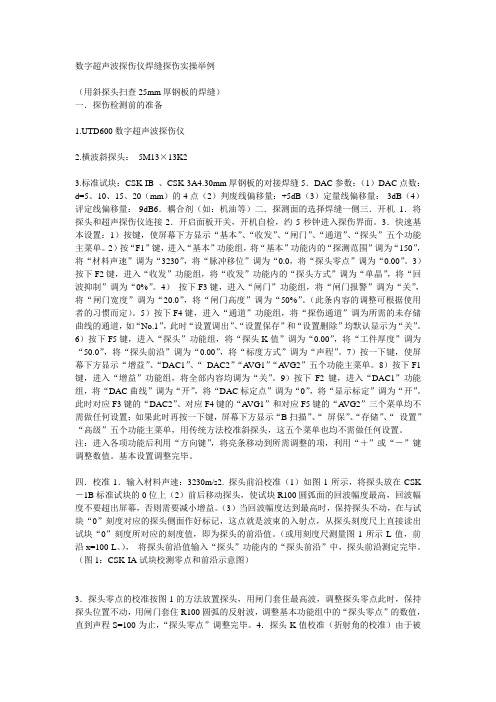
数字超声波探伤仪焊缝探伤实操举例(用斜探头扫查25mm厚钢板的焊缝)一.探伤检测前的准备1.UTD600数字超声波探伤仪2.横波斜探头:5M13×13K23.标准试块:CSK-IB 、CSK-3A4.30mm厚钢板的对接焊缝5.DAC参数:(1)DAC点数:d=5、10、15、20(mm)的4点(2)判废线偏移量:+5dB(3)定量线偏移量:-3dB(4)评定线偏移量:-9dB6.耦合剂(如:机油等)二.探测面的选择焊缝一侧三.开机1.将探头和超声探伤仪连接2.开启面板开关,开机自检,约5秒钟进入探伤界面。
3.快速基本设置:1)按键,使屏幕下方显示“基本”、“收发”、“闸门”、“通道”、“探头”五个功能主菜单。
2)按“F1”键,进入“基本”功能组,将“基本”功能内的“探测范围”调为“150”,将“材料声速”调为“3230”,将“脉冲移位”调为“0.0,将“探头零点”调为“0.00”。
3)按下F2键,进入“收发”功能组,将“收发”功能内的“探头方式”调为“单晶”,将“回波抑制”调为“0%”。
4)按下F3键,进入“闸门”功能组,将“闸门报警”调为“关”,将“闸门宽度”调为“20.0”,将“闸门高度”调为“50%”。
(此条内容的调整可根据使用者的习惯而定)。
5)按下F4键,进入“通道”功能组,将“探伤通道”调为所需的未存储曲线的通道,如“No.1”,此时“设置调出”、“设置保存”和“设置删除”均默认显示为“关”。
6)按下F5键,进入“探头”功能组,将“探头K值”调为“0.00”,将“工件厚度”调为“50.0”,将“探头前沿”调为“0.00”,将“标度方式”调为“声程”。
7)按一下键,使屏幕下方显示“增益”、“DAC1”、“DAC2”“A VG1”“A VG2”五个功能主菜单。
8)按下F1键,进入“增益”功能组,将全部内容均调为“关”。
9)按下F2键,进入“DAC1”功能组,将“DAC曲线”调为“开”,将“DAC标定点”调为“0”,将“显示标定”调为“开”。
超声波焊点检测设备使用方法

超声波焊点检测设备使用方法
超声波焊点检测设备的使用方法主要包括以下步骤:
1. 接通电源开关,打开主机开关按钮。
2. 调节水平旋钮,使探头中心线与水平面垂直。
3. 将探头和被检工件放在平板上。
4. 按“开始”键,当屏幕显示“请等待...”,说明系统正在自检。
5. 当屏幕上出现“请继续”,说明系统进入自动探伤状态。
6. 根据屏幕提示按相应键盘键。
7. 待屏幕显示正常后即可开始工作。
8. 若需打印报告单可按打印键。
此外,使用超声波焊点检测设备时,需要注意以下事项:
1. 使用前要认真阅读说明书并按要求正确操作。
2. 每次开机必须用清洁液把机器擦拭干净。
3. 严禁用手触摸探头。
4. 发现异常立即切断电源并停止使用。
5. 本设备属高压电器产品,应严格遵守国家有关安全条例。
6. 本设备为非标准产品,不能作为生产依据。
如果在使用过程中遇到问题,建议联系专业人员或厂家进行维修和保养。
- 1、下载文档前请自行甄别文档内容的完整性,平台不提供额外的编辑、内容补充、找答案等附加服务。
- 2、"仅部分预览"的文档,不可在线预览部分如存在完整性等问题,可反馈申请退款(可完整预览的文档不适用该条件!)。
- 3、如文档侵犯您的权益,请联系客服反馈,我们会尽快为您处理(人工客服工作时间:9:00-18:30)。
焊缝超声波探伤操作步骤
一、探头前沿长度的测量。
将探头放置在CSK—ⅠA试块上,将入射点对准R100处,找
出反射波达到最高时探头到R100端部的距离。
然后用其所长
100减去此段距离。
此时所得的数据就是探头的前沿距离。
按
此方法连测三次,求出平均值。
二、测量探头的K值
利用CSK—ⅠA试块上的φ50孔的反射角测出并用反三角函数
计算出K值。
将探头对准试块上φ50横孔,找到最高回波:则有K=tgβ=(L+l-35)/30。
三、扫描速度的调节
1、水平调节法:将探头对准R50、R100,调节仪器使B1、B2分
别对准不平刻度,此时计算出l1、l2。
l1,l2
将计算出的数据在示波屏上将B1和B2调至相对应的位置,此时水平距离扫描速度为1:1。
2、深度调节法
利用CSK-ⅠA试块调节,先计算R50、R100圆弧反射波B1、B2对
应的纵深d1、d2:d1,d2
B1、B2分别对准水平刻度值d1、d2。
如K=2时,经计算d1=22.4mm、d2=44.8mm。
调节仪器使B1、B2分别对准22.4和平共处44.8,这时
深度1:1就调节好了。
四、距离——波幅曲线的绘制
1、将探头置于CSK-ⅢA试块上,衰减48dB,调增益使深度为
10mm的φ1×6孔的最高回波达基准60%,记录此时的衰减器读数和孔深,然后分别探测其它不同深度的φ1×6孔,增益不动,调节衰减器将各孔的最高回波调至60%高,记下相应的dB 值和孔深填入表中。
2、以孔深为横坐标,以分贝值为纵坐标,在坐标纸上描点绘出定
量线、判废线和评定线,标出Ⅰ区、Ⅱ区、Ⅲ区,并注明所用探头的频率、晶片尺寸和K值。
3、现以T=30mm举例说明
五、调节探伤灵敏度
调节探伤灵敏度时,探伤灵敏度不得低于评定线,一般以2倍的壁厚处所对应的评定线dB值,也就是说在工件60mm处评定线所对应的分贝值。
如若还要考虑耦合补偿,补偿根据实际情况而定。
六、探测钢板
1、初扫,找缺陷,怀疑处作好标记。
2、细探,对可疑处进行仔细扫查。
去伪存真,对真缺陷测最大值,一、二次波都要测一下,另一侧也要测一下,然后作比较,取当量最大者。
4、缺陷的定位
(1)按水平调节扫描速度时
一次波探伤时,缺陷在工件中的水平距离lf和深度df为:
lf=nτf df= nτf/K
n——扫描比例τf——实际探伤水平刻度值K=探头的K值二次波探伤时,缺陷在工件中的水平距离lf和深度df为:
lf=nτf df=2T—nτf/K
(2)按深度调节扫描速度时
一次波探伤时,缺陷在工件中的水平距离lf和深度df为:
lf=Knτf df= nτf
二次波探伤时,缺陷在工件中的水平距离lf和深度df为:
lf=Knτf df= 2T—nτf
5、根据最大值,结合dB——距离曲线判定缺陷所处的区域,记录
成φ1×6±X型式。
6、根据6dB法测出缺陷的长度。
7、对Ⅱ区和Ⅲ区的缺陷测定其长度和大小。
并对照JB/T4730-2005
评定级别。