转炉除尘灰地高附加值利用)
炼钢除尘泥(灰)资源化利用分析

炼钢除尘泥(灰)资源化利用分析吾塔;臧疆文;丁国东;王新成;宋维兆【摘要】低碳循环经济是当今国际社会推进的可持续发展的一种新型实践模式,它强调最有效利用资源和保护环境.钢铁企业炼钢过程产生大量除尘产物,这些除尘产物是很好的二次资源.仅2009年,八钢公司转炉炼钢过程产生除尘干污泥约5.8万t,平均含铁量在50%以上;电炉炼钢过程产生的除尘灰1.4万t以上,平均含铁量在42%以上,科学合理地利用这些资源,既可创造经济效益又能减轻环境负担.目前转炉除尘污泥的利用途径是加人烧结混合料,烧结后进入炼铁高炉进行循环.这种做法虽然解决了污泥给环境造成的污染,但极不科学.实践证明,各种含铁尘泥不经预处理,直接加入烧结混合料中进行烧结并非经济科学的利用途径,其主要危害是转炉尘泥中含有害杂质,如ZnO、PbO、Na2O、K2O等,随烧结矿加入高炉,将影响高炉顺行和寿命.其次化学成分、粒度、水分均存在较大差异,污泥的含铁量低(与精矿粉相比),配人烧结后降低了烧结矿的质量和品位,增加高炉能耗,使炼铁产率降低.经分析将这些转炉炼钢除尘污泥和电炉炼钢除尘灰加工成炼钢造渣剂,加入转炉循环使用,有利于降低炼钢成本和环境保护,是科学利用这些资源的最佳途径,将为企业带来巨大的经济效益和社会效益.【期刊名称】《新疆钢铁》【年(卷),期】2010(000)004【总页数】3页(P14-16)【关键词】转炉除尘泥;电炉除尘灰;科学利用【作者】吾塔;臧疆文;丁国东;王新成;宋维兆【作者单位】宝钢集团八钢公司制造管理部;宝钢集团八钢公司制造管理部;宝钢集团八钢公司制造管理部;宝钢集团八钢公司制造管理部;宝钢集团八钢公司制造管理部【正文语种】中文【中图分类】X756低碳循环经济是当今国际社会推进的可持续发展的一种新型实践模式,它强调最有效利用资源和保护环境,表现为“资源——产品——再生资源”的经济增长方式,做到生产和消费“污染排放最小化”,以最小成本获得最大的经济效益和环境效益。
干熄焦除尘灰的利用现状分析
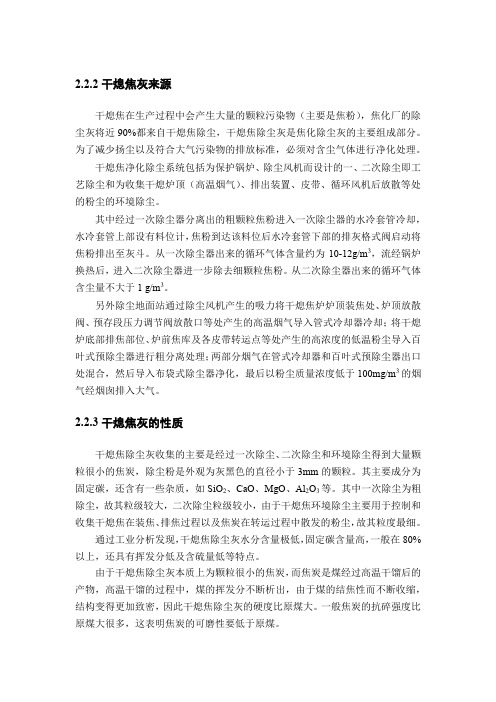
2.2.2干熄焦灰来源干熄焦在生产过程中会产生大量的颗粒污染物(主要是焦粉),焦化厂的除尘灰将近90%都来自干熄焦除尘,干熄焦除尘灰是焦化除尘灰的主要组成部分。
为了减少扬尘以及符合大气污染物的排放标准,必须对含尘气体进行净化处理。
干熄焦净化除尘系统包括为保护锅炉、除尘风机而设计的一、二次除尘即工艺除尘和为收集干熄炉顶(高温烟气)、排出装置、皮带、循环风机后放散等处的粉尘的环境除尘。
其中经过一次除尘器分离出的粗颗粒焦粉进入一次除尘器的水冷套管冷却,水冷套管上部设有料位计,焦粉到达该料位后水冷套管下部的排灰格式阀启动将焦粉排出至灰斗。
从一次除尘器出来的循环气体含量约为10-12g/m3,流经锅炉换热后,进入二次除尘器进一步除去细颗粒焦粉。
从二次除尘器出来的循环气体含尘量不大于1 g/m3。
另外除尘地面站通过除尘风机产生的吸力将干熄焦炉炉顶装焦处、炉顶放散阀、预存段压力调节阀放散口等处产生的高温烟气导入管式冷却器冷却;将干熄炉底部排焦部位、炉前焦库及各皮带转运点等处产生的高浓度的低温粉尘导入百叶式预除尘器进行粗分离处理;两部分烟气在管式冷却器和百叶式预除尘器出口处混合,然后导入布袋式除尘器净化,最后以粉尘质量浓度低于100mg/m3的烟气经烟囱排入大气。
2.2.3干熄焦灰的性质干熄焦除尘灰收集的主要是经过一次除尘、二次除尘和环境除尘得到大量颗粒很小的焦炭,除尘粉是外观为灰黑色的直径小于3mm的颗粒。
其主要成分为固定碳,还含有一些杂质,如SiO2、CaO、MgO、Al2O3等。
其中一次除尘为粗除尘,故其粒级较大,二次除尘粒级较小,由于干熄焦环境除尘主要用于控制和收集干熄焦在装焦、排焦过程以及焦炭在转运过程中散发的粉尘,故其粒度最细。
通过工业分析发现,干熄焦除尘灰水分含量极低,固定碳含量高,一般在80%以上,还具有挥发分低及含硫量低等特点。
由于干熄焦除尘灰本质上为颗粒很小的焦炭,而焦炭是煤经过高温干馏后的产物,高温干馏的过程中,煤的挥发分不断析出,由于煤的结焦性而不断收缩,结构变得更加致密,因此干熄焦除尘灰的硬度比原煤大。
转炉除尘灰的循环利用技术和应用

转炉除尘灰的循环利用技术和应用
张沅;徐铁;陈高亮
【期刊名称】《包钢科技》
【年(卷),期】2017(043)006
【摘要】转炉炼钢过程中会产生大量有害烟尘,经现代化的环保除尘设备处理回收后,可以得到粒度细小且含铁料高的除尘灰.通过采取一定的技术措施,成功开发出符合转炉使用的除尘灰压块.经炼钢转炉现场使用证明除尘灰压块具有良好的冷却和化渣效果,可以替代铁皮球、渣钢和铁矿石,实现了转炉除尘灰的"全闭路"综合利用.【总页数】3页(P17-19)
【作者】张沅;徐铁;陈高亮
【作者单位】内蒙古科技大学材料与冶金工程学院,内蒙古包头 014010;内蒙古包钢钢联股份有限公司稀土钢板材厂,内蒙古包头 014010;内蒙古包钢钢联股份有限公司稀土钢板材厂,内蒙古包头 014010;内蒙古包钢钢联股份有限公司稀土钢板材厂,内蒙古包头 014010
【正文语种】中文
【中图分类】TF805.3
【相关文献】
1.天津荣钢转炉干法除尘灰压球应用实践 [J], 利强;金鑫;房兴华
2.转炉喷溅渣循环利用技术的开发与应用 [J], 颜景春;邢东方;赵景泉;孙惠玲
3.太钢转炉除尘灰冷固球团技术及应用 [J], 王鹏
4.酒钢集团榆钢公司干法除尘灰冷压球转炉应用实践 [J], 亢神周;高勇
5.酒钢集团榆钢公司干法除尘灰冷压球转炉应用实践 [J], 亢神周;高勇
因版权原因,仅展示原文概要,查看原文内容请购买。
粉煤灰高附加值利用

粉煤灰可行性研究报告我国电能大部分由燃煤电厂提供。
全国燃煤电厂废弃的粉煤灰约有30亿吨,挤占了大片土地,对环境造成极大污染。
粉煤灰是一种细粒的复合矿物原料,对它进行整体开发利用不仅减免了对原材料的投入,也是减少固体废物污染的治本之道。
目前,热电粉煤灰主要用于道路工程、回填、改良土壤、灰场复土、水泥和其他建筑材料制造,或是从中提取特定物质,并没有大幅度提升再生产品的附加值,也没有充分利用废弃的粉煤灰,这是因为一般仅从各自行业的需求出发,只对粉煤灰的特殊用途或特定物质做了单向选择利用,并没有全面考虑粉煤灰的综合利用价值,有较大的局限性。
粉煤灰是一种复杂的、主要由无机和少量有机组分组成的混合物。
无机组分大部分为硅酸铝盐类物质,伴有少量碱性元素和微量的贵重金属元素;有机物主要为未燃烧碳粒和游离碳。
粉煤灰粒径小,是一种含有大量高附加值的可再利用的资源。
1、粉煤灰的资源特性分析1.1粉煤灰的化学成分、颗粒组成及物理性能粉煤灰是火力发电厂排出的一种工业固体废弃物, 它是由磨成一定细度的煤粉在煤粉炉中经过1100~1500℃的高温悬浮燃烧之后, 由原煤中粘土质矿物发生分解、氧化、熔融等变化, 在表面张力的作用下形成细小的液滴, 在排出炉外时, 经急速冷却形成粒径为0.1~380μm的玻璃质微细球形颗粒,然后, 同未被燃烧的可燃物一起由除尘器所收集,或者由水流管道排放到储灰厂。
粉煤灰的化学组成取决于原煤的无机物组成和燃烧条件,粉煤灰中70%以上都是由二氧化硅、三氧化二铝和三氧化二铁组成, 我国大中型电厂粉煤灰的化学组成和物理性能分别见表1和表2.粉煤灰是由各种颗粒机械混合而成的颗粒群体,主要颗粒为圆球形, 其中视密度大于1的微珠含量通常为50%~70%, 最大可达85%.主要颗粒形式有:①漂珠:在粉煤灰中含有0.5%-1%,, 形成空心的主要原因是矿物质转变过程中产生的CO2、CO、等气体, 被包裹于熔融的灰滴中心, 成为圆球型薄壁空心球体,含SiO2量较高, 达60%左右, Al2O3约30%, 其最大特点为质轻壁薄, 视密度小于1;②微珠:粉煤灰中含有50%~70%的空心微珠, 厚壁, 视密度大于1, 强度很高;③富铁微珠:以富集氧化铁而命名, 颜色黑, 有磁性;④海绵状多孔体:是粉煤灰中含量较多的一种颗粒成分, 其形貌特点为多孔不规则, 以海绵状为最典型, 粒径差别较大, 视密度较小, 比表面积则较大;⑤碳粒:碳粒在粉煤灰中大致有3种, 即多孔碳、碎屑碳和碎片碳。
高炉渣与转炉渣综合利用汇总
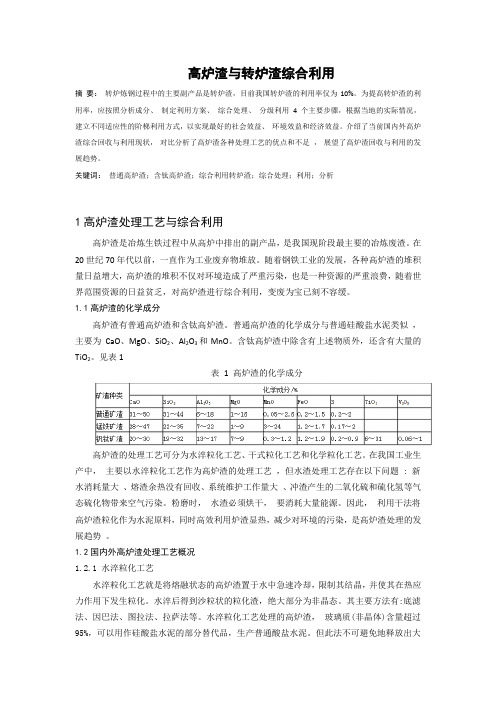
高炉渣与转炉渣综合利用摘要:转炉炼钢过程中的主要副产品是转炉渣,目前我国转炉渣的利用率仅为10%。
为提高转炉渣的利用率,应按照分析成分、制定利用方案、综合处理、分级利用 4 个主要步骤,根据当地的实际情况,建立不同适应性的阶梯利用方式,以实现最好的社会效益、环境效益和经济效益。
介绍了当前国内外高炉渣综合回收与利用现状,对比分析了高炉渣各种处理工艺的优点和不足,展望了高炉渣回收与利用的发展趋势。
关键词:普通高炉渣;含钛高炉渣;综合利用转炉渣;综合处理;利用;分析1高炉渣处理工艺与综合利用高炉渣是冶炼生铁过程中从高炉中排出的副产品,是我国现阶段最主要的冶炼废渣。
在20世纪70年代以前,一直作为工业废弃物堆放。
随着钢铁工业的发展,各种高炉渣的堆积量日益增大,高炉渣的堆积不仅对环境造成了严重污染,也是一种资源的严重浪费,随着世界范围资源的日益贫乏,对高炉渣进行综合利用,变废为宝已刻不容缓。
1.1高炉渣的化学成分高炉渣有普通高炉渣和含钛高炉渣。
普通高炉渣的化学成分与普通硅酸盐水泥类似,主要为CaO、MgO、SiO2、Al2O3和MnO。
含钛高炉渣中除含有上述物质外,还含有大量的TiO2。
见表1表 1 高炉渣的化学成分高炉渣的处理工艺可分为水淬粒化工艺、干式粒化工艺和化学粒化工艺。
在我国工业生产中,主要以水淬粒化工艺作为高炉渣的处理工艺,但水渣处理工艺存在以下问题 : 新水消耗量大、熔渣余热没有回收、系统维护工作量大、冲渣产生的二氧化硫和硫化氢等气态硫化物带来空气污染。
粉磨时,水渣必须烘干,要消耗大量能源。
因此,利用干法将高炉渣粒化作为水泥原料,同时高效利用炉渣显热,减少对环境的污染,是高炉渣处理的发展趋势。
1.2国内外高炉渣处理工艺概况1.2.1 水淬粒化工艺水淬粒化工艺就是将熔融状态的高炉渣置于水中急速冷却,限制其结晶,并使其在热应力作用下发生粒化。
水淬后得到沙粒状的粒化渣,绝大部分为非晶态。
其主要方法有:底滤法、因巴法、图拉法、拉萨法等。
转炉LT法除尘技术
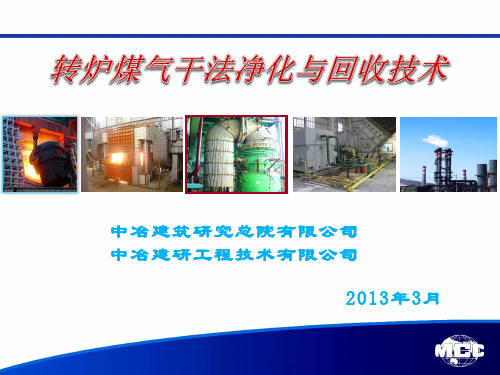
工程实例照片
-安装在汽化冷却烟道上的喷枪
工程实例照片
-汽化冷却烟道上的喷枪布置
工程实例照片
静电除尘器
工程实例照片
-放散烟囱
工程实例照片
-轴流风机
工程实例照片
-切换阀(杯阀)
工程实例照片
-排放效果
操作画面
Hale Waihona Puke -主画面操作画面-蒸发冷却器系统
操作画面
-轴流风机系统
操作画面
-静电除尘系统
对煤气回收及放散进行快速切换。当氧含量≥1%和煤气不符合回
收要求时,煤气经烟囱点火后放散,烟尘排放浓度小于 15mg/Nm3, 当氧含量<1%且煤气符合回收要求时,煤气进入喷淋冷却器,温
度降至70℃以下直接送入煤气柜,煤气含尘浓度小于10mg/Nm3 。
电除尘器收集下的粉尘通过输灰装置排出,可送至烧结直接利用。
中冶建筑研究总院有限公司 中冶建研工程技术有限公司 2013 年 3 月
转炉煤气干法净化与回收技术
工艺流程介绍
能耗排放指标对比
工程实例照片 操作界面 工艺系统优势
转炉干法一次除尘[整理]
![转炉干法一次除尘[整理]](https://img.taocdn.com/s3/m/c2b2b07226d3240c844769eae009581b6bd9bd8e.png)
转炉已一次干法除尘技术1 转炉干法除尘技术背景转炉煤气干法除尘是鲁奇(Lurgi)和蒂森(Thyssen)公司20世纪60年代末合作开发的。
转炉干法除尘的基本原理是对经汽化烟道后的高温煤气进行喷水冷却,将煤气温度由900℃~1000℃降低到200℃左右,采用电除尘器进行处理。
转炉干法除尘系统主要包括:蒸发冷却器、静电除尘器、煤气切换、煤气冷却器、放散烟囱、除灰系统等。
与湿法除尘(OG)法比较,干法除尘有以下优点:.除尘效率高。
净化后烟气含尘量为10mg/Nm3~20mg/Nm3,如有特殊要求可降至5mg/Nm3。
.系统阻力小,耗能低,风机运行费低,寿命长,维修工作少。
.在水、电消耗方面具有明显的优越性。
.不需要泥浆沉淀池及污泥处理设施。
.含铁干粉灰压块后可直接供转炉利用。
2 首钢京唐干法除尘设施的技术特点及实施情况首钢京唐炼钢厂采用2+3的“全三脱”两步法冶炼生产模式。
配置2座300t脱磷转炉和3座300t脱碳转炉。
脱磷转炉平均冶炼周期25min ,脱碳转炉平均冶炼周期28min。
正常情况下,实行2+3转炉全量脱磷、脱碳处理,转炉与板坯连铸机采用3对3的高效快节奏的生产模式。
在欧洲转炉干法除尘技术应用非常普遍,但是欧洲钢厂均没有采用“全三脱”转炉两步法冶炼技术。
在日本“三脱”转炉两步法冶炼技术应用很多,却没有采用转炉干法除尘的实例。
首钢京唐钢铁公司是世界上第一个在“全三脱”两步法冶炼的大型快节奏转炉上采用干法除尘技术的钢厂。
该工艺特点是:“三脱”处理后的铁水,已基本不含Si,C、Mn 含量也有较大的降低。
但是在工业化生产中仍需解决以下两个问题,对“三脱”处理后铁水进行吹炼,开吹后的炉气量和炉气中的CO含量是否会显著增加?如采用干法除尘是否会增加卸爆发生频率?为了实现在“全三脱”冶炼的转炉上应用煤气干法电除尘技术,技术团队对国外进行了考察调研和认真分析研究。
分析结论认为:与常规吹炼相比,“三脱”铁水吹炼前期炉气中CO比率不会增加,这对减少卸爆有利。
转炉一次干法除尘技术的应用与改进
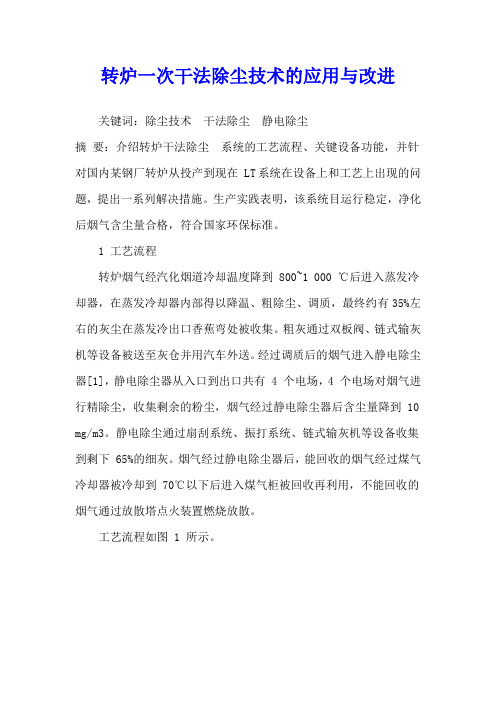
转炉一次干法除尘技术的应用与改进关键词:除尘技术干法除尘静电除尘摘要:介绍转炉干法除尘系统的工艺流程、关键设备功能,并针对国内某钢厂转炉从投产到现在 LT系统在设备上和工艺上出现的问题,提出一系列解决措施。
生产实践表明,该系统目运行稳定,净化后烟气含尘量合格,符合国家环保标准。
1 工艺流程转炉烟气经汽化烟道冷却温度降到800~1 000 ℃后进入蒸发冷却器,在蒸发冷却器内部得以降温、粗除尘、调质,最终约有35%左右的灰尘在蒸发冷出口香蕉弯处被收集。
粗灰通过双板阀、链式输灰机等设备被送至灰仓并用汽车外送。
经过调质后的烟气进入静电除尘器[1],静电除尘器从入口到出口共有 4 个电场,4 个电场对烟气进行精除尘,收集剩余的粉尘,烟气经过静电除尘器后含尘量降到 10 mg/m3。
静电除尘通过扇刮系统、振打系统、链式输灰机等设备收集到剩下 65%的细灰。
烟气经过静电除尘器后,能回收的烟气经过煤气冷却器被冷却到70℃以下后进入煤气柜被回收再利用,不能回收的烟气通过放散塔点火装置燃烧放散。
工艺流程如图 1 所示。
2 关键设备功能介绍2.1 蒸发冷却器在转炉 LT 干法除尘系统中,蒸发冷却器起着关键性的作用,可以对烟气进行冷却、调质、粗除尘。
在蒸发冷却器上部均匀布置16个双介质雾化冷却喷枪[2],喷枪喷射出来的雾化水蒸气对烟气进行降温,使烟气在蒸发冷凝出口达到合适的温度,确保电除尘进口温度在140~160℃。
在降温的同时也对烟气湿度进行调质,使粉尘的比电阻达到更有利于静电除尘器捕捉的值。
约有35%的灰尘在蒸发冷却器香蕉弯处被收集后通过输灰系统运送到储灰罐。
2.2 静电除尘器静电除尘器主要由进口气流分布板、放电极、收尘极、振打系统、扇形刮灰系统、泄爆装置等部分组成。
静电除尘器的工作原理是:在阳极和阴极上通以高压(20~80kV)直流电流,其间产生一定强度的电场,使空气电离,产生大量的电子和正负离子,正离子向负极靠近被中和,负离子和电子在电场力作用下向收尘极运动,当含灰烟气通过电场后,固体尘粒与这些电子、负离子碰撞被荷电(粉尘获得电荷),荷电尘粒在电场力作用下向收尘极运动,被吸附在阳极板上。
- 1、下载文档前请自行甄别文档内容的完整性,平台不提供额外的编辑、内容补充、找答案等附加服务。
- 2、"仅部分预览"的文档,不可在线预览部分如存在完整性等问题,可反馈申请退款(可完整预览的文档不适用该条件!)。
- 3、如文档侵犯您的权益,请联系客服反馈,我们会尽快为您处理(人工客服工作时间:9:00-18:30)。
实用文案 文案大全 核心提示:摘要:随着转炉炼钢生产的发展,炼钢工艺的日趋完善,相应的除尘技术也在不断地发展完善。炼钢烟气的净化回收方法主要有两种,一种是湿法(OG 法),一种是干法(LT 法)。LT 法(干法)为德国Lurgi 公司与Thyssen 钢铁厂研制成功的一种转炉烟气净化及煤气回收干式系统,该除尘方式不用大量浊环水洗涤烟气,而是采用蒸发冷却器+静电除尘器+煤气冷却器系统。它以净化效率高、能耗低、干粉尘可设置压块系统,粉尘经压块后直接供转炉利用等特点,得到广泛应用。 转炉除尘灰的高附加值利用 卜二军 耿丽君 刘红艳 随着转炉炼钢生产的发展,炼钢工艺的日趋完善,相应的除尘技术也在不断地发展完善。炼钢烟气的净化回收方法主要有两种,一种是湿法(OG 法),一种是干法(LT 法)。LT 法(干法)为德国Lurgi 公司与Thyssen 钢铁厂研制成功的一种转炉烟气净化及煤气回收干式系统,该除尘方式不用大量浊环水洗涤烟气,而是采用蒸发冷却器+静电除尘器+煤气冷却器系统。它以净化效率高、能耗低、干粉尘可设置压块系统,粉尘经压块后直接供转炉利用等特点,得到广泛应用。 邯钢转炉烟气采用干法除尘技术,与湿法相比,分别节电、节水约1/3,减少建设用地1/2,烟尘含量由50mg/Nm3 降到10mg/Nm3,同时烟尘可被全部回收再利用,实现节能4.5kgce/t 钢。现一炼钢厂的煤气回收量已稳定达到140Nm3/t 钢,回收煤气热值稳定在1500kcal/Nm3 以上。这对我国转炉炼钢节能减排、实现负能炼钢起到了积极的推动作用。但是转炉除尘灰具有温度高、金属化程度高、易自燃、粒度细、扬尘二次污染大等特性,造成其处理及综合利用难度大,亟待开发一种适合干法粉尘特性的新型处理工艺。 1 国内转炉除尘灰的利用现状及合理性 1.1 热压块 热压块工艺是利用粉尘的自燃特性将粉尘加热,利用其在高温下的塑性,经高压压球机压制成块,然后在氮气密封状态下冷却后输送到转炉,代替废钢或矿石。该方法不需要另外添加黏结剂,粉尘团块的强度也很高,可直接用于转炉作冷却材料使用,是现在LT 粉尘处理应用最多的一种方法。但是,热压块生产需在高温和隔绝空气的条件下进行,对设备和工艺控制要求很高,一次性投资大、工艺条件苛刻、设备故障率很高,难以长期顺利生产。 1.2 冷压块 有企业在除尘灰及污泥中加入部分添加剂,通过冷固工艺制成转炉造渣剂压块,用于转炉造渣,强化了造渣,改善了脱磷效果,脱磷率提高;化渣效果好,能够起到防喷溅的作用。 1.3 返回烧结 邯钢西区转炉除尘灰的利用途径是加入烧结混合料中,经烧结后进入炼铁高炉进行循环。虽然该方法不需要增加设备,但粒度过细且能够自燃的干法除尘灰不利于烧结矿质量的实用文案 文案大全 控制和热量的平衡。除尘灰含有有害杂质,而烧结难以有效地去除这些杂质,使得烧结配加和稳定操作困难,入高炉后将影响高炉正常操作和炉衬寿命;其化学成分、粒度、水分均存在较大差异,不利于烧结矿生产和质量的提高;该方法仅能回收部分含铁粉尘,从某利意义上讲,对这些宝贵的二次资源没有起到真正意义上的回收。因此,在烧结配料中加入除尘灰进行循环利用极不科学。 1.4 竖炉球团配加 有企业在竖炉中配加炼钢除尘细灰,经过近20 个月的摸索和改进,实现了生产稳定顺行,并保证了质量稳定。转炉干法除尘灰用于竖炉球团配加生产是可行的,配加量在5%以内,可减少对竖炉生产的影响。但是还存在炼钢除尘灰质量不稳定、成分波动大、倒运过程中二次扬尘太大等问题。 2 邯钢转炉除尘灰基本情况 2.1 转炉除尘灰产量及回收量 邯钢以转炉LT 除尘灰为研究对象,探索转炉除尘灰的高附加值利用途径。 转炉除尘灰分为粗灰、细灰两种。粗灰来自蒸发冷却器底部,细灰是炼钢过程中产生的烟尘经干法除尘、沉降得到的。2014 年12 月邯钢炼钢除尘灰当月产量、累计量及回收量,如表1 所示。
2.2 转炉除尘灰的化学成分 转炉除尘灰的化学成分,见表2。
转炉除尘粗灰为灰黑色,为细颗粒。转炉除尘细灰为红-褐色,颜色与氧化铁红相近,粒度较细,100 目的占70%以上。转炉除尘细灰中氧化铁的含量比较高,含有少量Fe3O4,是制备铁系颜料的理想原料。 3 创新研究 邯钢以转炉除尘细灰为原料,以制备出高附加值产品为目标,提出氧化焙烧制备成高纯氧化铁红的方案。氧化铁红制备试验采用高温氧化培烧法。 3.1 制备氧化铁红的研究 1)烘干除水工艺 对转炉除尘灰进行现场取样,在烘箱中烘干2h 以上,温度控制在100℃左右。 2)混匀物料工艺 实用文案 文案大全 转炉除尘灰质量不稳定,TFe 和CaO 含量波动较大。-应采取质量控制措施,即将其进行初步混匀处理,以降低成分波动。 3)磨样制备工艺 转炉除尘灰为粒度较细的粉尘,为了达到粒度均匀、氧化效果好的目的,采用制样机对转炉除尘灰进行一次粗破,其出料粒度200 目达到92%以上。 4)焙烧氧化工艺 本研究是在碳管炉内进行静态焙烧氧化制备氧化铁红,氧化过程中所需氧气来自空气,工艺温度控制在850-900℃,恒温时间为30mmin。其炉内反应为:
碳管炉升温速率的控制如图1 所示。 焙烧所得物料产生结块,经简单磨细至-200 目占90%以上,可获得纯度较高的氧化铁红产品。氧化铁红的化学成分,如表3 所示。氧化铁红质量与标准对比,如表4 所示。该产品不存在有机着色物,不仅可用作涂料或建材的着色剂或添加剂,更适宜做磁性材料的原料,可直接生产铁氧体预烧料。
3.2 制备磁性材料的研究 以氧化铁红为原料生产高品质铁氧体预烧料,进而生产铁氧体材料已被磁性材料厂广泛采用。其原理及化学方程式如下: 碳酸盐分解反应:(300-0-800℃)
中间反应:(600-800℃) 实用文案
文案大全 通过以上流程制得的铁氧体性能优良,与利用铁鳞作原料制备的铁氧体预烧料性能相当或优于铁鳞。邯钢于2012 年分别建成铁鳞、氧化铁红生产永磁铁氧体预烧料生产线,采用链篦机-回转窑的方法,每年可生产出2 万多吨永磁铁氧体预烧料,现已稳定生产运行两年多。氧化铁红和铁鳞的利用提高了邯钢产品的综合利用程度及科技含量,填补了邯钢磁性材料的空白,发展壮大了其非钢产业。 如果通过转炉除尘灰批量生产氧化铁红,进而再生产铁氧体材料,附加值水平将得到更大提升。针对这种情况,邯钢进行了利用转炉干法除尘细灰制备铁氧体预烧料的试验研究,材料磁性能检测结果如表5 所示。
3.3 经济性能评价 炼钢除尘灰的价格约100-200 元/t,氧化铁红的价格为1400 元/t,铁氧体预烧料的价格则超过3000 元/t,采用炼钢除尘灰生产氧化铁红,进而再生产高性能永磁铁氧体,昔日炼钢除尘灰作为固体废弃物易污染、难治理的现状将得到根本性的改善,其高附加值、高效的利用得以实现。 4 结语 邯钢西区转炉除尘细灰的处理方式为返回烧结配料,利用档次低,经济效益不明显。除尘细灰返回烧结配加困难,经常造成烧结故障。本工艺可将转炉除尘细灰全部回收利用生产出氧化铁红,不仅有效回收利用了二次资源、减少环境污染,而且提高了除尘细灰的利用水平,对企业的可持续发展有重要意义,以利用促治理,可达到经济效益、环境效益和社会效益协调发展的目的。 1)通过开展转炉除尘灰的二次回收利用试验研究,拓展了思路,验证了可行性,为进一步工业化生产铺平了道路。 2)转炉除尘灰作为氧化铁红生产的原料,资源丰富,可利废为宝,生产中不使用酸、碱及其他化学原料进行处理、无废物排放,可防止环境污染、方法简单快捷、能耗小、生产成本低,成品中氧化铁红含量高达95%以上,具有竞争力。 3)利用制备出来的氧化铁红制备铁氧体预烧料,将会创造更多利润。 实用文案
文案大全 焦粉分布对准颗粒燃烧速度的影响 1 研究背景 由于原料价格大幅度上涨、环保政策更加严格及原料质量变差,导致铁矿烧结生产形势愈发严峻,因此必须改进烧结生产工艺。在烧结过程中,焦粉燃烧速度是影响烧结矿质量和烧结机利用系数最重要的因素之一。为了提高焦粉燃烧效率,开发出新的喷涂制粒方法,如图1所示。在该方法中,将焦粉和石灰石喷涂于准颗粒的表面。 采用喷涂制粒法能够改善焦粉的燃烧性,提高烧结机利用系数,生产出优质烧结矿。日本九州大学研究了焦粉在准颗粒中的分布对焦粉燃烧速度的影响。 2 讨论 2.1 试验试样和步骤 实用文案 文案大全 使用氧化铝粉末和焦粉制备模拟准颗粒的试验试样。为了简化试验条件,制备氧化铝粉末以替代铁矿。在试验过程中,忽略液相生成、铁矿还原和二次氧化对焦粉燃烧的影响。 选取焦粉的粒度小于125μm,氧化铝粉末的粒度小于250μm,按照表1示出的质量比进行混合。制备四种具有不同焦粉分布的试样。全部原料和试样示意图如图2所示。该试样分为内核和涂层。把氧化铝与焦粉进行混合后,用不锈钢冲模将混合料压成直径10mm的圆片,将该圆片作为内核,圆片厚度为10mm,孔隙比为35%。然后对内核进行喷涂,并压成直径15mm的圆片,该圆片厚度为15mm,孔隙比为35%。涂层中焦粉配比的变化范围为33vol%~55vol%。 在本次研究中用热天平测量试样在焦粉燃烧期间的重量损失如图3所示。将该试样放入铂制篮子内。使用立式电阻炉营造等温加热条件,等温区的温度达到1073K、1223K、1373K和1523K。在燃烧试验前,在N2气氛下按照给出的各个温度进行热处理,以便从试样中脱除水分和挥发分。然后,把反应管的里面换成空气,空气流量为4NL/min。当试样的重量损失为零时,表明试验已经结束。 2.2 试验结果 在本次研究中将反应率定义为试样中固定碳的去除率。如果产生的CO气体可以忽略不计,那么碳燃烧反应的化学方程式如(1)式: C(s) O2(g)=CO2(g) (1)