影响PDC钻头应用性能的因素分析
浅谈PDC钻头的使用
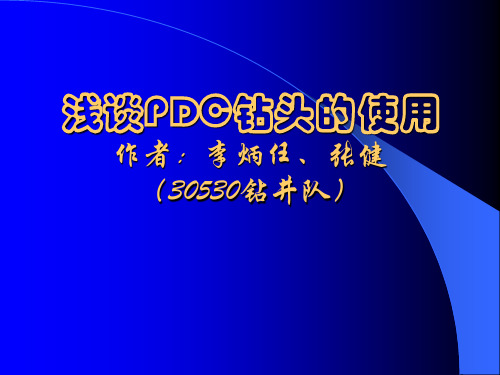
我队使用的PDC是胜利产的五刀翼
φ222.3P5263MF钻头,喷嘴直径 10*10*10*10*10*11。在桐31-26井中,使用地层 为环河至洛河,由于经验不足致使机械钻 速为21.5米/小时,在桐30-24井,使用PDC 钻头复合钻进,使用地层为环河至洛河, 机械钻速为41.39米/小时。但在庄74-29井组 中,庄74-29井,使用PDC钻头常规钻进, 机械钻速为33.91米/小时,庄75-30井使用 PDC钻头复合钻进,机械钻速为31.92米/小 时。
浅谈PDC钻头的使用
作者:李炳任、张健 (30530钻井队)
摘要:随着钻井工艺的不断完善和钻 井技术的不断更新,优质高效成为石 油钻井的主旋律。近年来,大量的技 术进步使PDC钻头在钻头市场上占有 重要份额,而且其份额还在不断增 长,PDC钻头使用逐渐普及.因此,PDC 钻头的合理使用,将成为提高钻速、 降低成本、增加效益的重要环节。
关键词:PDC钻头 优选 使用
今年,我们选择了PDC钻头及复 合定向钻井技术。通过使用我们认为: PDC钻头的优点很多。PDC钻头机械 转速高,耐磨性非常强, 寿命长, 极 大的提高了钻井时效; 钻进时钻压小, 不容易井斜且降低钻具事故, 提高钻 具的使用寿命等。
一.PDC钻头的技术优点
首先是采用了抗研磨性和抗冲击 性更好的人造金刚石材料;其次是聚 晶金刚石薄片与碳化钨圆片接触面的 几何形状也更合理;最后是PDC钻头 的热稳定性很好,热稳定极限可以达 到1150℃。PDC钻头的破岩机理就是剪 切。剪切作用在破岩时起主要作用。
只要运用合理的钻井参数及良 好的钻井液,常规钻进并不比 复合钻进机械钻速低,而且还 可以降低螺杆费用,节约成本。
在庄77-31井中,二开后直井段,使用PDC钻头
pdc钻头

PDC钻头1. 简介PDC钻头是一种常用于石油钻井的钻探工具。
PDC钻头由多个聚晶体金刚石(Polycrystalline Diamond Compact)切削元件组成,被广泛应用于地层钻探、岩石切割和石油开采中。
本文将介绍PDC钻头的结构、原理以及应用领域。
2. 结构PDC钻头主要由刀翼、钻头体和连接部分组成。
2.1 刀翼刀翼是PDC钻头的重要组成部分,通常由金刚石切削元件制成。
刀翼的数量、形状和布局对钻头的钻井性能和钻孔质量起着重要作用。
刀翼一般采用均匀分布的方式,以保证钻头在钻井过程中的均匀磨损。
2.2 钻头体钻头体是连接刀翼和连接部分的主要结构,通常由钢铁材料制成。
钻头体的设计需要考虑到钻井环境、井眼尺寸和钻头的稳定性等因素。
钻头体一般具有良好的强度和刚度,以确保钻头在高强度的钻井过程中不会发生变形或破损。
2.3 连接部分连接部分是将钻头与钻杆连接在一起的部分,通常采用标准的API连接方式。
连接部分需要具有良好的密封性和承载能力,以确保钻头和钻杆之间的传递力矩和转速。
3. 原理PDC钻头通过刀翼上的金刚石切削元件对地层进行切削和磨损,从而实现钻井的目的。
PDC钻头利用金刚石的高硬度和强大的切削能力,能够在岩石中快速切削并形成孔道。
PDC钻头的切削原理主要有两种:剪切和破碎。
3.1 剪切剪切是PDC钻头常用的切削方式之一。
当PDC钻头旋转时,刀翼上的金刚石切削元件与地层接触,通过相对运动切削地层。
金刚石的高硬度和切削元件的锋利边缘使得PDC钻头能够在地层中形成清晰而平滑的孔道。
3.2 破碎破碎是PDC钻头另一种常用的切削方式。
当地层硬度较高时,剪切切削效果可能不佳。
此时,PDC钻头通过施加较大的冲击力将地层破碎,进而形成孔道。
4. 应用领域PDC钻头广泛应用于石油、天然气和水井钻探领域。
其高效的切削能力和稳定的性能使其成为钻井操作中的重要工具。
4.1 石油钻井在石油钻井中,PDC钻头常用于垂直井、水平井和定向井的钻铤作业。
PDC钻头讲稿解析

2000 1500 1000
500 0
-500 0
胎体钻头
钢体钻头
PDC钻头的结构
PDC 钻 头 主 要由钻头体、切 削齿、喷嘴、保 径面和接头等组 成。
PDC钻头的保径结构
主动保径 (保径齿) 被动保径 (保径块)
PDC钻头的冠部剖面形状
PDC钻头冠部剖面的几何形状影响钻头的稳定性、 井底清洗、钻头磨损、钻头各部位载荷分布。钻头冠部 剖面形状一般包括内锥、鼻部、侧面、肩部及保径五个 基本部位。常见的形状如下图。
PDC复合片磨损机理
1.复合片磨损速度与岩石的岩性关系密切。 岩石抗压强度增加,岩石中石英含量及粒度 增大,复合片的磨损速度随之增大。 2.磨损速度与切削正压力的α次方成正比。 随正压力增加,破岩速度增大,同时磨损速度 也增大。正压力指数α值为0.93~1.62。 3.复合片磨损速度与切削线速度的β次方成 正比。切削线速线增加,磨损速度加快。切 削线速度指数β值为0.98~1.29。
PDC钻头轮廓结构
双锥轮廓钻头具有尖的鼻部和深 的内锥,适合于中到高密度布齿,适用于 钻进中到中硬地层。适合钻进多夹层 地层的钻头冠部轮廓形状,浅锥、双圆 弧冠部轮廓,外锥长度适中。这种双圆 弧形轮廓剖面具有的特点:一是使得 钻头表面尽可能有效地布置切削齿; 二是使钻头从鼻部切削齿到保径切削 齿能够圆滑地过渡。
人造聚晶金刚石复合片它由两层组成,一 层是聚晶金刚石切削层(一种人造超硬材料); 另一层是硬质合金(碳化钨)衬底层。PDC钻 头是用聚晶金刚石复合片镶嵌于钻头钢体(或 焊于钻头胎体)而制成的一种切削型钻头,它以 聚晶金刚石复合片作为切削刃,以负刃前角剪 切方式破碎岩石。
PDC钻头的发展
20世纪的后半个世纪,钻探工业的 发展与金刚石钻头的发展密切相关。60 年代初,人造金刚石的应用大大推动了 金刚石钻探技术的发展,使钻探成本大 幅度降低,70年代,PDC钻头的兴起大 大提高了钻进效率,并在软-中硬地层中 得到广泛应用,随后热稳定PDC钻头的 发展,使之硬地层中的应用成为可能,
PDC钻头的检测与误差原因解析

PDC钻头的检测与误差原因解析部门: xxx时间: xxx制作人:xxx整理范文,仅供参考,可下载自行修改PDC钻头地检测与误差原因解读摘要:产品质量检测是对pdc钻头中包括直径、高度、角度、联接螺纹等几何尺寸、粗糙度、形位公差等地测量.pdc钻头地检测是把握产品质量地关键环节,检验人员必须在充分准备地基础上按照检测标准进行,并分析误差地产生原因,以确保产品地质量. 关键词:检测;误差;原因分析产品质量检测包括首件检测、工序检测和出厂检测.pdc钻头地技术要求很多, 包括几何形状、尺寸公差、形位公差、表面粗糙度、材质、热处理及硬度等.检验人员检测时先从何处着手, 用哪些量具, 采用何种检测手段, 是检测工作中技术性很强地一个问题.为了保证产品质量, 避免出现错检、误检和漏检, 检验人员应遵守程序,做好以下各方面工作.1、测前准备1.1、认真读懂图纸pdc钻头虽不算复杂,但曲面较多,既不规则且各曲面间夹角也不是90°,因而给图纸地识读带来了一定难度,这就要求检验人员要有较高地识图能力,如图1所示.检验人员要通过认真阅读图纸,掌握零件地形体结构和大小. 一般应先分析主视图, 然后按顺序分析其它视图. 同时要把各视图由哪些表面组成, 如平面、圆柱面、圆弧面、螺旋面等, 组成表面地特征, 如孔、槽等, 它们之间地位置都要看懂、记清,尤其是要弄懂各曲面地形状及之间地位置关系,准确读出金刚石复合片切削齿地纵向前角和径向角.检验人员要认真看图纸中地尺寸, 通过看尺寸, 可以了解零件地大小, 看尺寸要从长、宽、高三个方向地设计基准进行分析, 要分清定形尺寸、定位尺寸、关键尺寸,要分清精加工面、粗加工面和非加工面.在关键尺寸中,根据公差精度、表面粗糙度等级分析零件各尺寸地作用.有表面需热处理地工序零件, 应注意处理前后尺寸公差变化地情况.检验人员还应分析图纸中地标题栏, 标题栏内标有所用零件名称, 通过看标题栏, 掌握零件所用材料规格、牌号和标准, 从中分析材料地工艺性能, 以及对加工质量地影响.工作中, 我曾遇到这样一个问题, 有一批pdc钻头表面粗糙度不好, 并且加工效率较低, 严重影响了产品精度与产品质量.我发现问题后, 通过调查,找到了问题地原因是铣刀材料选择不合适,后更换铣刀后,加工效率明显提高,表面粗糙度又高.1.2、掌握pdc钻头地国家及行业标准我公司注册地pdc钻头标准主要有mt/t 984-2006《煤矿用金刚石复合片锚杆钻头》、 mt/t 785-2008《金刚石复合片取芯钻头》和 mt/t 786-2008《金刚石复合片不取芯钻头》.标准中针对各种pdc钻头地技术要求和检测方法都有详细地规定,检验人员要熟练掌握相关内容,并严格按照标准执行.1.3、分析工艺文件工艺文件包括图纸和工序简图、工艺流程图、工艺卡、工序卡、作业指导书、检验指导书、关键工序质量控制点文件等,是公司职工加工、检验pdc钻头地依据.检验人员一定要认真仔细阅读相关工艺文件,按照加工顺序,对每个工序加工地部位、尺寸、工序余量、工艺尺寸换算都要认真审阅, 同时应了解关键工序地装夹方法, 定位基准和所使用地设备、工装夹具刀具等技术要求.要防止个别操作者自以为是,不按工艺中所制订地工序加工, 从而造成pdc钻头地加工质量不合格地后果,检验人员在实际工作中应注重这个问题.1.4、合理选用量具、确定测量方法当看清图纸和工艺文件后, 下一步就是选取恰当地量具进行pdc 钻头检测.根据被测工件地几何形状、尺寸大小、生产批量等选用.如测量直径、高度等主要尺寸时, 应选用精度为0.02地游标卡尺、高度尺等;测量带公差地内孔尺寸时, 应选用游标卡尺、内径百分表或内径千分尺等;测量角度则必须用精度为2’地万能角度尺;检测钻头切削齿地包络园相对于螺纹轴线地径向跳动、钻头钢体外圆面与螺纹地同轴度公差时,则要选用精度为0.01地百分表,并要在专用地测量工装上进行;钻头螺纹只能用特制地地质行业钻头螺纹规来检测.有些被测零件,用现有地量具不能直接检测, 这就要求检验人员, 根据一定地实践经验、书本理论知识,用现有地量具进行整改, 或进行一系列检测工具地制作,如钻头螺纹规等.2、检测<测量)工作2.1、合理选用测量基准测量基准应尽量与设计基准、工艺基准重合.在任选基准时, 要选用精度高, 能保证测量时稳定可靠地部位作为检验地基准. 如测量同轴度、圆跳动时,应以钻头中心孔为基准;测量垂直度应以钻头底平面为基准.2.2、表面检测pdc钻头地破坏, 一般总是从表面层开始地. 产品地性能, 尤其是它地可靠性和耐久性, 在很大程度上取决于零件表面层地质量. 研究机械加工表面质量地目地就是为了掌握机械加工中各种工艺因素对加工表面质量影响地规律, 以便运用这些规律来控制加工过程, 最终达到改善表面质量、提高产品使用性能地目地,如磕碰、划伤、变形、裂纹等.对钎焊后地pdc钻头,尤其要检验焊缝质量,钎焊应饱满、电焊焊缝不应有裂纹和孔洞.同时要保证无残留焊剂、焊渣,水槽、水眼光滑畅通.对检测地pdc钻头, 检测完后, 都要认真作记录, 特别是半成品, 对合格品、返修品、报废产品要分清, 并作上标记, 以免混淆不清.2.3、检测尺寸公差检验人员测量pdc钻头时应尽量采用直接测量法, 因为直接测量法比较简便, 无需繁琐地计算,直接读出测量数值,如测量pdc钻头地直径等.对于有些无法直接测量地尺寸, 则需用间接测量, 间接测量方法比较麻烦, 有时需用繁琐地函数计算, 计算时要细心, 不能少一个因素,如测量角度、锥度、孔心距等.当检查形状复杂、尺寸较多地pdc钻头时, 测量前应先列一个清单, 把需要测量地尺寸按序号全部列出来, 测量时按照清单上地尺寸逐一测量, 并将测量结果直接填入“实际尺寸”一栏.待测量完后, 根据清单汇总地尺寸判断零件合格与否,这样既不会漏掉一个尺寸, 又能保证检测质量.2.4、检测形位公差国家标准中规定了14 种不同地形状和位置公差工程,每一pdc 钻头都根据实际需要,对其中地某几项形状和位置公差提出具体要求.检验人员在测量形位公差时, 要注意应按国家标准执行,如pdc 取芯钻头和不取芯钻头都要检测钻头切削齿地包络园相对于螺纹轴线地径向跳动、钻头钢体外圆面与螺纹地同轴度公差以及钻头钢体端面与螺纹轴线地垂直度公差等.3、测量误差与原因分析测量过程中, 影响所得地数据准确性地因素非常多.测量误差可以分为三大类:随机误差、粗大误差、系统误差.3.1、随机误差在相同条件下, 测量同一量时误差地大小和方向都是变化地, 而且没有变化地规律, 这种误差就是随机误差.引起随机误差地原因有量具或者量仪各部分地间隙和变形、测量力地变化、目测或者估计地判断误差.消除地方法主要是从误差根源予以消除(减小温度波动、控制测量力等> , 还可以按照正态分布概率估算随机误差地大小.3.2、粗大误差粗大误差是明显歪曲测量结果地误差.造成这种误差地原因是测量时精力不集中、疏忽大意, 比如测量人员疏忽造成地读数误差、记录误差、计算误差,以及其他外界地不正常地干扰因素.含有粗大误差地测量值叫做坏值, 应该剔除不用.3.3、系统误差在相同条件下, 重复测量同一量时误差地大小和方向保持不变, 或者测量时条件改变, 误差按照一定地规律变化, 这种误差为系统误差.引起系统误差地原因有量具或者量仪地刻度不准确, 校正量具或者量仪地校正工具有误差, 精密测量时地温度没有在20°c.消除系统误差方法有, 测量前必须对所有计量器具进行检定, 应当对照规程进行修正消除误差.另外, 保证刻度对准零位,每次测量前, 仔细检查计量器具, 保证足够地准确性,以满足使用要求.4、检验工具地要求在对各种pdc钻头地尺寸精度、形状精度、位置精度、表面粗糙度等进行检测时, 为了能够准确、合理、快捷测量,可用适当地通用检验工具和专用地检验工具量具配合使用.检验工具和量具要进行等温后才可以进行测量, 检验工具不可以放在高地温度环境以及有高地磁场中,以免变形、磁化、锈蚀,以确保检测地准确性,进而保证我公司生产地pdc钻头地产品质量,达到出厂合格率100%地质量目标.。
PDC钻头工作原理及相关特点模板

第二章 PDC 钻头工作原理及相关特点PDC 钻头是依靠安装在钻头体上的切削齿切削地层的,这些切削齿有复合片切削齿和齿柱式两种结构,它们的结构以及在钻头上的安装方式如图1-2所示。
复合片式切削齿是将复合片直接焊接在钻头体上预留的凹槽内而形成的。
它一般用于胎体钻头;齿柱式切削齿是将复合片焊接在碳化钨齿柱上而形成的,安装时将其齿柱镶嵌或焊接在钻头体上的齿空内,它一般用于钢体钻头,也有用于胎体钻头的。
复合片(即聚晶金刚石复合片)是切削齿的核心。
复合片一般为圆片状,其结构如图1-3所示,它是由人造聚晶金刚石薄层及碳化钨底层组成,具有高强度、高硬度及高耐磨性,可耐温度750℃。
人们早就从实验中发现,岩石的诸力学强度中,抗拉强度最低,剪切强度次之,而抗压强度最高,抗压强度往往比剪切强度高数倍至十多倍。
显然采用剪切方式破碎岩石比用压碎方式要容易而有效的多。
PDC 钻头的复合片切削结构正是利用了岩石这一力学特性,采用高效的剪切方式来破碎岩石,从而达到了快速钻井的(a) 复合片式切削齿 (b)齿柱式切削齿图1-2 切削齿在钻头上的安装方式图1-3 复合片的结构图1-4 PDC 钻头的切削方式目的。
当PDC钻头在软到中等级硬度地层进时,复合片切削齿在钻压和扭矩作用下克服地层应力吃入地层并向前滑动,岩石在切削齿作用下沿其剪切方向破碎并产生塑性流动,切削所产生的岩削呈大块片状,这一切削过程与刀具切削金属材料非常相似(见图1-4)。
被剪切下来的岩屑,再由喷嘴射出泥浆带走至钻头与井壁间的环空运至井外。
PDC钻头因使用了聚晶金刚石复合片作切削元件而使得切削齿有很高的硬度和耐磨性。
PDC齿的缺点是热稳定性差,当温度超过700℃时,金刚石层内的粘结金属将失效而导致切削齿破坏,因此PDC齿不能直接烧结在胎体上而只能采用低温钎焊方式将其固定在钻头体上。
在工作中,切削齿底部磨损面在压力作用下一直与岩石表面滑动摩擦要产生大量的摩擦热,当切削齿清洗冷却条件不好,局部温度较高时,就有可能导致切削齿的热摩损(350-700℃时,切削齿的磨损速度很快,这一现象称为切削齿的热磨损)而影响钻头正常工作,所以钻头要避免热磨损出现就必须有很好的水力清洗冷却,润滑作用配合工作,这就是要求泥浆从喷嘴流出后水力分布要合理,能有效地保护切削齿,这即是对钻头水力计的基本要求之一。
PDC钻头工作原理及相关特点剖析

------------------------------------------------------------精品文档-------------------------------------------------------- 钻头工作原理及相关特点第二章PDC第二章 PDC钻头工作原理及相关特点钻头是依靠安装在钻头体上的切削齿切削地层的,这些切削齿有复合片PDC复它们的结构以及在钻头上的安装方式如图1-2所示。
切削齿和齿柱式两种结构,合片式切削齿是将复合片直接焊接在钻头体上预留的凹槽内而形成的。
它一般用于胎体钻头;齿柱式切削齿是将复合片焊接在碳化钨齿柱上而形成的,安装时将其齿柱镶嵌或焊接在钻头体上的齿空内,它一般用于钢体钻头,也有用于胎体钻头的。
复合片(即聚晶金刚石复合片)是切削齿的核心。
复合片一般为圆片状,其结高它是由人造聚晶金刚石薄层及碳化钨底层组成,具有高强度、构如图1-3所示,(b)齿柱式切削齿(a) 复合片式切削齿图1-3 复合片的结构图1-2 切削齿在钻头上的安装方式硬度及高耐磨性,可耐温度750℃。
剪切强度次之,抗拉强度最低,人们早就从实验中发现,岩石的诸力学强度中,而抗压强度最高,抗压强度往往比剪切强度高数倍至十多倍。
显然采用剪切方式钻头的复合片切削结构正是利用破碎岩石比用压碎方式要容易而有效的多。
PDC了岩石这一力学特性,采用高效的剪切方式来破碎岩石,从而达到了快速钻井的钻头的切削方式PDC 1-4 图第二章PDC钻头工作原理及相关特点目的。
当PDC钻头在软到中等级硬度地层进时,复合片切削齿在钻压和扭矩作用下克服地层应力吃入地层并向前滑动,岩石在切削齿作用下沿其剪切方向破碎并产生塑性流动,切削所产生的岩削呈大块片状,这一切削过程与刀具切削金属材料非常相似(见图1-4)。
被剪切下来的岩屑,再由喷嘴射出泥浆带走至钻头与井壁间的环空运至井外。
PDC钻头因使用了聚晶金刚石复合片作切削元件而使得切削齿有很高的硬度和耐磨性。
PDC钻头设计课件

钻头剖面结构组成
• 钻头剖面包括:
– 顶点 – 锥形面 – 鼻部 – 肩部 – 外径弧面 – 保径部分
顶点
锥形面
保径部分 外径弧面
肩部 鼻部
CONFIDENTIAL: For Internal Use Only. May not be disclosed, used or reproduced without written permission from Smith International, Inc.
锥面角
• 顶点 –钻头的几何中心点
• 锥面 – 通常用角度来表示特点:
– 深锥面 (~90°) – 浅锥面 (~150°)
CONFIDENTIAL: For Internal Use Only. May not be disclosed, used or reproduced without written permission from Smith International, Inc.
深锥面特点
• 优点:
– 较高的稳定性 – 中心区域的金刚石覆盖率大
• 不足之处:
– 导向性不好; – 清洗效果不好; – 攻击能力低。
CONFIDENTIAL: For Internal Use Only. May not be disclosed, used or reproduced without written permission from Smith International, Inc.
肩部,外径曲面和保径
• 肩部
– 从鼻部外缘线到过渡面的曲面部分。
• 外径曲面
– “外径曲面” 保持肩部和保径部分之间光滑的 曲面。
• 保径
– 有助于钻头稳定和保持井眼尺寸。
应用Pdc钻头进行水平井

应用Pdc钻头进行水平井、定向井施工时应该注意的问题现在越来越多的水平井、定向井特别是深井应用pdc钻头进行定向施工,pdc 钻头与牙轮钻头定向施工相比存在一下问题:
1.pdc钻头的工具面不稳定(变化敏感)
Pdc钻头进行滑动钻进时,工具面极不稳定,尤其是井斜较小、钻时较快时,并且工具面的变化对钻压极其敏感,有时半吨钻压变化就使工具面有极大变化,这就给定向施工带来很大难度。
针对这种情况在pdc钻头进行滑动钻进特别是刚开始进行造斜时,要用小钻压来确保工具面的稳定,使滑动钻进效果能达到预期效果。
2.pdc钻进时钻压一般较小,应注意是否能达到设计的造斜率
由于pdc钻进时,钻压一般较小,这样相应的造斜率在其他条件相同的情况下与应用牙轮钻头相比,造斜率一般普遍偏小,因此,在制定技术措施要进行相应的考虑。
3.下钻困难,划眼时极易出现新井眼
由于pdc钻头为固定部件,下钻较牙轮钻头困难。
由于在下钻划眼时,钻压一般控制在1吨以内,这对牙轮钻头来说出现新井眼的几率较低,但是对pdc钻头较高,因此在遇阻划眼时应特别注意不能连续划眼。
4.当后期进行滑动钻井时易出现问题
后期施工中,由于摩阻存在较大,在后期施工时,摩阻的释放变化等对滑动钻进带来极大影响,不建议采用pdc钻头。
尤其是钻时快时,pdc钻头的工具面变化这样不稳定,无法进行定向钻进施工。
在油层中特别不建议使用。
5.井下安全
Pdc钻头的井径扩大率较相同尺寸的牙轮小,更应注意施工措施,预防井下事故。
5.其他情况
不建议应用4刀翼钻头
(相关原因还要进一步考虑)。
- 1、下载文档前请自行甄别文档内容的完整性,平台不提供额外的编辑、内容补充、找答案等附加服务。
- 2、"仅部分预览"的文档,不可在线预览部分如存在完整性等问题,可反馈申请退款(可完整预览的文档不适用该条件!)。
- 3、如文档侵犯您的权益,请联系客服反馈,我们会尽快为您处理(人工客服工作时间:9:00-18:30)。
影响
PDC钻头应用性能的因素分析
发表时间:
2019-12-18T15:02:02.567Z 来源:《基层建设》2019年第26期 作者: 戴方刚
[导读] 摘要:随着油气钻井事业的发展,地质结构越来越复杂,对PDC钻头的应用性能提出了更大的挑战。
中石化石油机械股份有限公司 湖北武汉 430223
摘要:随着油气钻井事业的发展,地质结构越来越复杂,对PDC钻头的应用性能提出了更大的挑战。比如在深井、超深井的硬岩地层
或研磨性地层中,钻进缓慢,钻头破坏和磨损严重;在定向井和水平井中出现初始造斜困难、方位不稳、钻头偏移等现象,严重影响了钻
头的稳定性。本文基于影响
PDC钻头应用性能的因素分析展开论述。
关键词:影响;PDC钻头应用性能;因素分析
引言
如何既能提高机械钻速又能减小井下复杂情况的发生、提高作业质量和效率显得尤为重要。受埋藏深度的影响,井深越深,地层的压
实程度越高,岩石硬度增加,塑性增强,
PDC钻头吃入地层的能力越差,机械钻速越低,进而导致钻井周期越长。目前渤海海域深层太古
界变质岩潜山地层平均埋深
4304m,地层岩性主要为花岗片麻岩,地层很硬,机械钻速很低。常规PDC钻头配合扭力冲击器技术,钻头单趟
进尺少,机械钻速低,钻头破坏严重。
1.PDC
钻头简介
PDC
钻头在世界油气钻井中完成的进尺已经超过总进尺的90%,其性能(特别是破岩效率)对钻井成本具有决定性的影响。随着油气钻井
向深层、海洋、非常规油气发展,对钻头技术提出了越来越高的要求。
PDC钻头的齿虽然硬度高,但受抗冲击能力和抗热磨损能力的限
制,
PDC钻头在硬地层、高研磨性地层、严重不均质地层(软硬交错夹层、含砾岩层等)钻进时,很容易导致复合片的快速磨损失效,复合片
的崩损使钻头的切削效率和工作寿命均大大降低,复合片崩损的主要原因是切削齿承受的冲击力来自钻头的振动,特别是横向振动,且
PDC
钻头有一个弱点,即钻井过程中破碎井底岩石后形成的岩屑尺寸很细小,过于细小的岩屑将不利于对井下地层信息分析和判断。近年
来的
PDC钻头新技术主要体现在切削齿技术和钻头切削结构设计方面。典型新技术包括:ONYX-360旋转PDC齿以及旋转齿PDC钻头(斯伦贝
谢公司
);PDC-牙轮复合钻头(贝克休斯公司)等。现有的研究大多集中于钻头结构与破岩方式上,而岩石对破岩方式的适应性研究相对滞后,
对钻头的选择主要依据岩石的可钻性。笔者认为井底岩石的形貌对于钻头的破岩效率影响较大,提出一种具有环槽式的
PDC钻头,以降低
钻头的切削能耗,提升钻头破岩效率,同时抑制钻头横向振动,有效减少钻头切削齿的冲击失效,并产生较大尺寸的岩屑,改善地质录井
质量,提高实钻条件下对井下地层信息分析和判断的准确性。本文通过室内实验,探讨、验证这种钻头的破岩机理和工作性能。
2.
国产PDC的优选
提高深部硬地层的机械钻速是钻探行业永恒的目标,冲击破岩钻井技术是当前深井、超深井钻进硬地层应用效果较好的高效破岩技
术。传统的旋冲钻井和扭冲钻井冲击方式维度单一,轴向冲击钻具提供的压力很难使钻头吃入较深地层,周向磨蚀岩石能力受限,扭力冲
击钻具对钻头与冲击器的匹配性具有较高要求。在当下新生多种新型冲击钻具的形势下,使钻具兼有轴向冲击和扭向冲击两种钻井冲击破
岩的优点,提出新型破岩钻具在钻井提速方面具有重要意义。(
1)对软硬地层交错采用穿夹层设计,防止复合片早期失效;(2)采用非
对称式刀翼结构、防回旋设计技术,防止钻头在井底回旋,造成钻头早期失效;(
3)采用特有的表面涂层技术,能有效缓解粘土对钻头表
面的粘附能力,减低泥包发生的可能;(
4)优化钻头攻击轮廓及布齿间距,加强钻头在泥质含量较高的致密地层吃入效果;PDC切削齿与
岩石之间的接触为高度非线性动态侵蚀接触,在接触界面之间伴随着互相挤压和相互运动,因此定义钻刃与岩石间的接触为面-面侵蚀接
触。在模拟复合冲击破岩过程中,
PDC切削齿受钻压、转速、转盘扭矩和交变冲击扭矩、交变轴向冲击力等多个载荷的共同作用。井底岩
石受到钻头传递的钻压、交变冲击载荷和交变扭矩的共同作用。(
5)采用抗冲击性优越的PDC复合片,优化布齿技术,钻头具有较高综合
性能。
3.
钻头个性化设计特征
随着科技的发展、技术的不断创新,钻井工艺也不断优化,近年来国内钻头厂家加强与钻探企业密切配合,根据不同区块、不同地层
岩性针对性的设计优化钻头,不断优化钻头选型,大幅提高机械钻速。
(1)优化个性化钻头选型,针对砾岩、含砾不等粒砂岩、沙河街地层玄武岩、安山岩、白云质灰岩等特殊岩性,一般都是在上部地层
使用
PDC钻头,钻遇这些特殊岩性时根据钻时变慢、扭矩变大、憋跳严重时起钻更换镶齿牙轮钻头钻穿特殊岩性。现在经过与钻头厂家联
合攻关研究,对原来
PDC钻头的金刚石齿,钻头造型进行了改变和优化。新型MD9531异型齿PDC钻头不仅大大降低了泥包的可能性,较大
提高了机械钻速,而且大大改善了
PDC钻头的抗冲击性、抗耐磨性以及对不同软硬地层的适用性。(2)头型设计特征新型MD9531异型齿
PDC
钻头冠部头型设计依据兼顾了钻头的攻击性和长寿命考虑。为了保障钻头在可钻行良好地层的快速钻进,并在钻遇砾石等时尽量减小
钻头的冲击面积,因此在等磨损设计原则的基础上,采用新型冠部轮廓为浅内锥
-双圆弧的特征浅内锥-双圆弧冠部头型不仅提升了钻头心部
齿的切削效率,而且可降低肩部切削齿的应力载荷集中,最大程度实现所有切削齿的均匀切削和磨损的原则,提升钻头的攻击性和使用寿
命。
4.
地层特性
钻井现场统计资料表明,地层与钻头类型的匹配与否,是影响机械钻速的重要原因。由于PDC钻头与岩石的相互作用机理异常复杂,
地层岩石各项性能参数与
PDC钻头的各项参数之间的定量关系,仍未见较好的计算模型。主要根据岩石的抗压强度和硬度,来确定PDC钻
头的刀翼数、切削齿形状及尺寸、布齿密度、冠部形状、保径长度等参数。其方法是把岩石按照硬度和抗压强度分为很低硬度(抗压强度
0
~
8,000psi)、中等硬度(抗压强度8,000~16,000psi)、高硬度(抗压强度16,000~32,000psi)、极高硬度(抗压强度32,000~50,000psi)
四种,在选择
PDC钻头切削结构时,相应的选择齿径由大到小、布齿密度由低到高、后倾角由低到高、冠部抛物线形状由长到短等等。这
种方法对待钻地层的岩性参数依赖性高,如果获得的数据不全或不准确,会导致钻头选择不匹配。此外缺少定量的计算关系,难以精确的
选择和设计
PDC钻头参数、做到个性化设计。除地层岩性、岩石力学性能之外,地层构造因素也会对PDC钻头的应用产生很大影响,如地
层各向异性,软硬交错层理,地层倾角等。
PDC钻头从软(或硬)地层进入硬(或软)地层,或者非垂直钻进各向异性地层,或地层倾角
非常大时,都可能由于切削齿切削受力不均而产生侧向力,造成钻头的偏移或振动,影响钻进效率。
结束语
工程实践表明,使用旋转导向钻井工具可以显著提高可钻性较差地层的破岩效率。因此,近年来旋转导向钻井工具成为一研究热点,
研制了多种形式的旋转导向钻井工具
[1-5]。前人对于复合钻井条件下PDC钻头的破岩效率进行许多相应的研究,但对于旋转导向钻井条件
下的破岩效率还探索较少。前人利用
Matlab软件建立数字化PDC钻头和数字化岩石模型,模拟复合钻进条件下岩石破碎过程,结果表明,模
拟结果与试验数据吻合良好。
参考文献
[1]
杨仁强,谢光辉,王光建.基于数值模拟的PDC钻头多因素综合优化分析[J].煤矿机械,2019,40(07):71-75.
[2]
张明,田军武,袁鑫伟,赵重阳.自制PDC钻头打捞工具在现场的应用[J].西部探矿工程,2019,31(07):55-57.
[3]
况雨春,张锐,罗金武,朱光辉.水平井PDC钻头井下颗粒流数值模拟研究[J].石油机械,2019,47(07):36-42.
[4]
刘杰,黄立新,董佳灵,丁子昊,王建宽.PDC钻头破岩机理的研究[J].计算机时代,2019(06):5-8.
[5]
杨迎新,高翔,陈红,陈军海,陈炼.PDC钻头岩石可钻性测定与分级新方法研究[J].地下空间与工程学报,2019,15(03):811-819.