乙烯胺工艺就
聚苯乙烯胺的原料

聚苯乙烯胺的原料全文共四篇示例,供读者参考第一篇示例:聚苯乙烯胺(polystyreneamine,简称PSA)是一种重要的热固性树脂,广泛应用于涂料、胶粘剂、包装材料等领域。
PSA的制备过程中所需的原料涉及多种化学物质,以下将就PSA的原料进行详细介绍。
PSA的主要原料是苯乙烯和氨水。
苯乙烯是一种常见的有机化合物,为一种无色液体,在工业中广泛用于合成各类聚合物。
氨水则是氨和水的混合液,是化工生产中一种重要的碱性试剂。
这两种原料在PSA的合成中发挥了重要作用,通过一系列的化学反应,可以得到PSA聚合物。
除了苯乙烯和氨水外,制备PSA所需的一些辅助原料还包括过氧化苯乙烯、磺酸、醇化剂等。
过氧化苯乙烯是一种引发聚合反应的活性氧化剂,能够促进PSA的聚合反应进行。
磺酸则是一种常见的反应催化剂,可以加速聚合反应的进行,提高反应速率和产率。
醇化剂则是一种用于调节PSA分子结构和性能的添加剂,通过其作用可以改善PSA的耐热性和耐化学性。
为了提高PSA的性能,制备过程中还可以添加一些改性剂和增塑剂。
改性剂可以改善PSA的粘结性能和机械性能,提高其耐热性和耐化学性。
增塑剂则可以提高PSA的柔韧性和延展性,使其更适合在不同应用领域中使用。
制备PSA所需的原料种类繁多,包括主要原料苯乙烯和氨水,辅助原料过氧化苯乙烯、磺酸、醇化剂等,以及改性剂和增塑剂等。
这些原料通过一系列精密的化学反应,共同作用于PSA的合成过程中,最终得到具有良好性能和广泛应用前景的PSA聚合物。
希望本文对PSA的原料有所了解,为相关领域的研究和应用提供帮助。
第二篇示例:聚苯乙烯胺是一种重要的合成树脂,广泛应用于包装、建筑、电子等领域。
它的原料主要包括苯乙烯和胺类化合物,下面我们详细介绍一下关于聚苯乙烯胺的原料。
一、苯乙烯苯乙烯是聚苯乙烯胺的主要原料之一。
苯乙烯是一种有机化合物,化学式为C8H8,是苯的一个共轭双键饱和衍生物。
它是一种无色液体,有芳香味,是一种重要的工业化学品,被广泛用于合成聚合物。
乙烯生产技术和工艺流程介绍

乙烯生产技术和工艺流程介绍乙烯(Ethylene)是一种重要的化工原料,广泛应用于塑料、橡胶、纺织品、涂料等多个工业领域。
乙烯的生产技术和工艺流程对于高效和可持续生产乙烯至关重要。
本文将介绍乙烯生产的常见技术和工艺流程。
乙烯生产技术乙烯生产的关键技术主要包括石油和煤炭的裂解、催化剂的选择、热传导控制以及工艺条件的优化等。
石油和煤炭的裂解石油和煤炭是乙烯的重要原料,它们通过热裂解的方式生产乙烯。
热裂解是在高温和缺氧的条件下使原料分解为乙烯和其他碳氢化合物的过程。
石油和煤炭的裂解需要合适的反应器和操作条件,以确保高产率和良好的产品质量。
催化剂的选择催化剂在乙烯生产中起到至关重要的作用。
常用的乙烯生产催化剂包括铝烯烃催化剂、杂环胂催化剂和氧化钇系催化剂等。
选择合适的催化剂可以提高乙烯的产率和选择性,并减少其他副产物的生成。
热传导控制热传导控制是乙烯生产中的关键技术之一。
通过控制反应器壁面的温度分布,可以改善乙烯的产率和收率。
合理设计反应器结构和提高换热效率是实现良好热传导控制的重要手段。
工艺条件的优化乙烯生产工艺条件的优化对于提高乙烯生产效率和产品质量至关重要。
工艺条件的优化包括反应温度、反应时间、料液比等的选择。
合理的工艺条件可以提高乙烯的选择性和稳定性,降低副产物的生成。
乙烯生产工艺流程乙烯生产的工艺流程主要包括原料处理、预处理、裂解、分离和后处理等步骤。
原料处理石油和煤炭作为乙烯的原料需要进行处理。
处理包括去除杂质和调整成分,以保证原料的质量和稳定性。
通常的处理方法包括精制和脱硫等步骤。
预处理预处理是为了提高乙烯生产过程中的效果和稳定性。
预处理包括原料预热、混合和加压等步骤。
预热可以提高裂解反应的温度和速率,混合可以均匀分布原料,加压可以保持正常操作条件。
裂解裂解是将原料通过热裂解反应产生乙烯的过程。
裂解的方法有很多种,常见的有热裂解、催化裂解和电解裂解等。
裂解过程需要合适的反应器和温度控制,以确保高产率和良好的产品质量。
乙烯装置工艺

乙烯装置工艺乙烯是一种重要的有机化工原料,广泛应用于塑料、橡胶、合成纤维等行业。
乙烯装置工艺是指通过一系列工艺步骤将乙烯原料转化为乙烯产品的过程。
本文将介绍乙烯装置工艺的主要步骤及相关技术。
乙烯装置工艺的主要步骤包括乙烷裂解、分离、净化和乙烯制取等环节。
首先是乙烷裂解,乙烯装置的原料是乙烷,通过高温和催化剂的作用,将乙烷分解为乙烯和其他副产物。
在这个过程中,需要控制温度、压力和催化剂的选择,以提高乙烯产率和质量。
乙烯产物还包括少量的丙烷、丙烯和芳烃等。
分离是乙烯装置工艺的第二个步骤,通过一系列的分离操作,将乙烯与其他产物进行分离。
常用的分离方法包括精馏、萃取和吸附等。
精馏是一种常用的分离方法,通过不同组分的沸点差异,将乙烯与其他产物进行分离。
萃取是利用溶剂的选择性溶解性,将乙烯与其他产物进行分离。
吸附是通过在吸附剂上吸附乙烯,再通过升温、减压等操作将吸附的乙烯释放出来。
净化是乙烯装置工艺的第三个步骤,通过一系列的净化操作,去除乙烯中的杂质。
常见的净化方法包括吸附、洗涤和脱硫等。
吸附是将乙烯通过吸附剂,去除其中的杂质。
洗涤是通过溶剂或水的选择性溶解性,将乙烯中的杂质进行洗涤。
脱硫是将乙烯中的硫化物进行去除,以防止催化剂中毒。
乙烯制取是乙烯装置工艺的最后一个步骤,通过一系列的加工操作,将净化后的乙烯产品进行制取。
常见的制取方法包括压缩、冷凝和储存等。
压缩是将乙烯气体进行压缩,以提高乙烯的密度和储存能力。
冷凝是将乙烯气体通过冷却,使其变为液态,方便运输和储存。
储存是将乙烯液体储存在合适的容器中,以备后续使用。
乙烯装置工艺中还涉及到一些辅助设备和控制系统,如加热炉、冷却器、压力控制装置和自动化控制系统等。
这些设备和系统的选择和设计,对乙烯装置的性能和效率有着重要影响。
总结起来,乙烯装置工艺是将乙烷裂解为乙烯,并经过分离、净化和制取等步骤,最终得到乙烯产品的过程。
乙烯装置工艺涉及到多个工艺步骤和技术,需要合理选择和控制,以提高乙烯的产率和质量。
探析聚乙烯亚胺微球(PEI)制备的影响因素
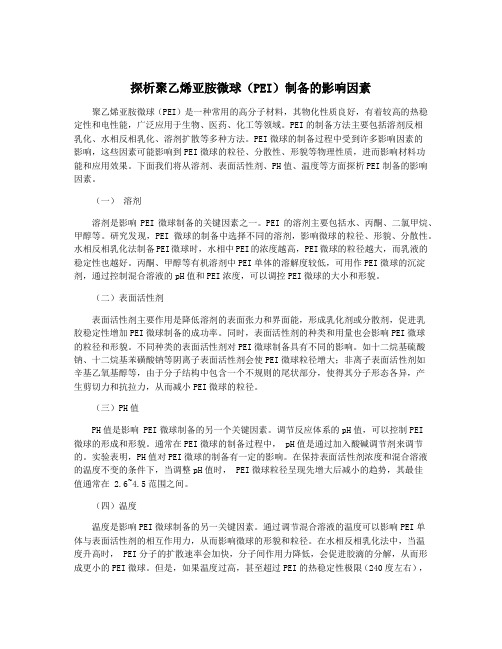
探析聚乙烯亚胺微球(PEI)制备的影响因素聚乙烯亚胺微球(PEI)是一种常用的高分子材料,其物化性质良好,有着较高的热稳定性和电性能,广泛应用于生物、医药、化工等领域。
PEI的制备方法主要包括溶剂反相乳化、水相反相乳化、溶剂扩散等多种方法。
PEI微球的制备过程中受到许多影响因素的影响,这些因素可能影响到PEI微球的粒径、分散性、形貌等物理性质,进而影响材料功能和应用效果。
下面我们将从溶剂、表面活性剂、PH值、温度等方面探析PEI制备的影响因素。
(一)溶剂溶剂是影响PEI微球制备的关键因素之一。
PEI的溶剂主要包括水、丙酮、二氯甲烷、甲醇等。
研究发现,PEI微球的制备中选择不同的溶剂,影响微球的粒径、形貌、分散性。
水相反相乳化法制备PEI微球时,水相中PEI的浓度越高,PEI微球的粒径越大,而乳液的稳定性也越好。
丙酮、甲醇等有机溶剂中PEI单体的溶解度较低,可用作PEI微球的沉淀剂,通过控制混合溶液的pH值和PEI浓度,可以调控PEI微球的大小和形貌。
(二)表面活性剂表面活性剂主要作用是降低溶剂的表面张力和界面能,形成乳化剂或分散剂,促进乳胶稳定性增加PEI微球制备的成功率。
同时,表面活性剂的种类和用量也会影响PEI微球的粒径和形貌。
不同种类的表面活性剂对PEI微球制备具有不同的影响。
如十二烷基硫酸钠、十二烷基苯磺酸钠等阴离子表面活性剂会使PEI微球粒径增大;非离子表面活性剂如辛基乙氧基醇等,由于分子结构中包含一个不规则的尾状部分,使得其分子形态各异,产生剪切力和抗拉力,从而减小PEI微球的粒径。
(三)PH值PH值是影响 PEI微球制备的另一个关键因素。
调节反应体系的pH值,可以控制PEI微球的形成和形貌。
通常在PEI微球的制备过程中, pH值是通过加入酸碱调节剂来调节的。
实验表明,PH值对PEI微球的制备有一定的影响。
在保持表面活性剂浓度和混合溶液的温度不变的条件下,当调整pH值时, PEI微球粒径呈现先增大后减小的趋势,其最佳值通常在 2.6~4.5范围之间。
30万吨乙烯工艺流程

30万吨乙烯工艺流程乙烯是化工工业中最常见的重要有机化学品之一、它广泛应用于塑料工业、橡胶工业、纺织工业、涂料工业等众多领域。
本文将介绍一种生产30万吨乙烯的工艺流程。
一、原料准备乙烯的主要原料是石油原油或天然气。
在加工过程中,原料通过分离和精炼,去除其中的杂质和硫化物,并得到纯净的石脑油或天然气。
二、裂解反应裂解反应是乙烯生产的关键步骤。
现代乙烯生产工艺主要采用热解技术,即通过在高温和高压下将石脑油或天然气裂解成乙烯和丙烯。
常用的方法有石油蒸气裂解(Petrochemical Steam Cracking)、重油裂解(Residual Oil Cracking)和循环流化床催化裂解(Cyclic Fluid Bed Catalytic Cracking)等。
裂解反应通常在反应器中进行,通过加热,将原料加热至高温,和催化剂一起进行反应。
催化剂通常是金属或金属氧化物。
三、分离和净化裂解反应产生的混合气体中除了乙烯和丙烯外,还有其他杂质气体,如氢气、一氧化碳、甲烷等。
在分离和净化过程中,需要通过各种分离技术,如冷凝、吸附、吸收、凝结等将目标产品分离出来,并去除其他杂质。
其中,乙烯和丙烯通过分馏和冷凝技术得到液态乙烯和丙烯。
此外,通过吸附技术可以去除其他杂质气体,如碳氢化合物、硫化氢等。
四、脱碳和再生脱碳是乙烯生产过程中的一项重要技术。
在裂解反应中产生的催化剂中会含有沉积的碳物质,会降低催化剂的活性,因此需要进行脱碳处理。
脱碳一般分为浮选脱碳和气流脱碳两种方法。
浮选脱碳是利用催化剂颗粒的密度差异,通过空气悬浮将含碳颗粒从催化剂中分离出来。
气流脱碳是通过高温空气在流化床中吹拂催化剂,将含碳颗粒氧化成CO2和CO,然后再用空气吹扫,将CO和CO2脱去。
脱碳后的催化剂可以再生利用。
五、乙烯加氢乙烯加氢是为了提高乙烯的纯度。
乙烯在加热或长时间存储过程中容易聚合,这会影响产品质量。
因此需要将乙烯加氢,将其中的不饱和键饱和掉。
乙烯的生产工艺介绍

乙烯的生产工艺介绍生产乙烯的重要核心过程就是分离过程,目前世界乙烯装置分离技术主要分为3大类,即顺序分离技术、前脱乙烷前加氢技术和前脱丙烷前加氢技术。
经过几十年的发展乙烯装置的分离流程,通过不断改进,已发展出几种不同的分离路线[3]。
1顺序分离技术深冷分离技术中,顺序分离技术应用的最早也最广泛。
在顺序分离技术中,是把关键组分的相对挥发度最接近1的乙烯和乙烷、丙烯和丙烷的分离放到流程的最后,首先按照从轻到重的顺序,将裂解气中的各个组分进行分离。
其典型流程主要包括:裂解气急冷、裂解气压缩、裂解气分离及制冷系统等几个主要部分[3],见图1-2。
图1-2典型的顺序分离流程示意(1)裂解气急冷重裂解汽油组分分离出来后,一部分作为急冷油塔的回流,一部分送至汽油汽提塔。
急冷油塔底部采出裂解燃料油,经燃料油汽提塔汽提,来控制闪点,并且冷却。
裂解气急冷部分还包括稀释蒸汽发生系统,它的作用是为裂解炉提供稀释蒸汽。
(2)裂解气压缩裂解气从急冷水塔中出来后进入裂解气压缩机一段吸入罐,压缩后经一段后冷器冷却进入压缩机二段吸入罐,然后分别进入压缩机三、四、五段吸入罐(3)裂解气分离裂解气经过干燥后依次经过脱乙烷塔进料、乙烯精馏塔、中间再沸器和丙烯冷剂冷却,进入脱甲烷塔,塔顶要控制乙烯损失在0.3%一下。
塔釜再沸器用丙烯冷剂回收冷量作为热源,塔釜液送进脱乙烷塔,塔釜控制乙烷含量在0.04%以下,塔顶控制丙烯含量在0.25%以下,乙炔选择加氢生成乙烯和乙烷,塔顶气相经乙烯干燥器后进乙烯精馏塔。
世界上乙烯装置采用最为广泛的一种乙烯分离技术就是顺序分离技术,随着技术进步以及节能减排的要求不断提高,各个行业也在传统的顺序流程的基础上开发了不少新的分离技术,为乙烯分离技术做了很大的改进。
2前脱乙烷分离技术图1-3前脱乙烷前加氢技术前脱乙烷技术的主要特点就是指分离流程的第一个塔为脱乙烷塔[4]。
见图1-3裂解气经急冷、压缩后预冷,首先进人脱乙烷塔系统,C2组分和C3以上组分先分开。
乙烯工艺流程分析

乙烯工艺流程分析
《乙烯工艺流程分析》
乙烯是一种重要的化工原料,在很多行业中都有广泛的应用。
乙烯的生产工艺是一个复杂的过程,需要经过多道工序来完成。
下面将针对乙烯生产的工艺流程进行分析。
乙烯的生产通常以石油或天然气作为原料。
首先,原料通过蒸馏或裂解的方式得到乙烯的预生产物——乙烷。
接着,乙烷要经过脱氢反应来制得乙烯。
这个脱氢反应通常在高温、高压下进行,需要通过催化剂来加速反应速度。
脱氢反应后的乙烯会含有杂质,需要进行蒸馏和净化处理,以去除其中的杂质成分。
随后,乙烯要经过合成反应来制得乙烯聚合物,也就是聚乙烯。
这个合成反应通常需要使用催化剂,而且反应条件也相当苛刻。
一旦制得乙烯聚合物,就需要进行后续的加工和处理,最终形成乙烯产品。
整个乙烯生产的工艺流程中,不仅需要各种化工反应工序,还需要配套的设备和管道来保证生产的顺利进行。
而且在整个生产过程中,要保证生产设备的安全和稳定运行,并且要防止化工品的泄漏和污染。
总的来看,乙烯的生产工艺流程是一个复杂的系统工程,需要多个环节的紧密配合,以确保乙烯的高效生产和产品质量。
同时,要加强安全管理和环境保护,以确保生产过程中对环境和人员的安全不会造成影响。
十八烯胺 合成工艺

十八烯胺合成工艺
会议烯胺是一种有机化合物,其化学式为C18H37NH2。
以下是一种合成会议烯胺的工艺:
1. 制备底物:将油酸(C18H36O2)与过量的氨水反应,生成油酸胺(C18H37NH2)底物。
2. 催化氢化:将油酸胺底物与催化剂一起加入催化氢化反应器中,进行反应。
常用的催化剂包括铁、镍等。
反应条件一般为高压高温下进行,使底物发生氢化反应。
这个反应可以在氢气存在下进行。
3. 蒸馏分离:在氢气氢化反应后,需要对反应混合物进行蒸馏分离。
通过调控温度和压力,使得油酸胺与产物分离开来。
蒸馏可以将产物分离出来并得到高纯度的会议烯胺。
以上是一种常用的合成会议烯胺的工艺流程,具体情况还需要根据实际条件进行调整。
合成工艺的选用也会受到成本、废物处理等因素的影响。
- 1、下载文档前请自行甄别文档内容的完整性,平台不提供额外的编辑、内容补充、找答案等附加服务。
- 2、"仅部分预览"的文档,不可在线预览部分如存在完整性等问题,可反馈申请退款(可完整预览的文档不适用该条件!)。
- 3、如文档侵犯您的权益,请联系客服反馈,我们会尽快为您处理(人工客服工作时间:9:00-18:30)。
《乙烯胺工艺》乙二胺(EDA)又称二胺基乙烯、乙烯二胺,是重要的化工原料和精细化工中间体,可用作农药杀菌剂和活性染料中间体,也可用于医药、纺织整理剂原料,还用于环氧树脂固化剂、乳化稳定剂和抗电剂等,用途十分广泛。
近年来,EDA在我国的应用发展较快,其进口量年增长率达到了20%以上,成为我国亟待发展的精细石油化工中间体之一。
乙二胺的合成方法主妻有二氯乙烷法(EDC)、乙醇胺法(MEA)、乙烯氨化法、甲醛-氢氰酸法、二甘醇氨化法、氯乙酰氯氨化法和氨基乙腈加氢法等。
工业生产乙二胺的方法主要是EDC法和MEA法,其他方法由于原料来源和成本等原因尚未实现工业化生产。
美国UCC公司于1936年将EDC-法工业化,MEA-法于20世纪60年代初由联邦德国BASF公司开发并实现工业化。
现在世界上EDA的生产装置中,约61%为EDC路线,由于二氯乙烷原料价廉,来源广泛,早期乙二胺装置主要采用EDC法。
以单乙醇胺(MEA)为原料与氨反应生成乙二胺。
污染小,原料易得,是当前研究的重点。
EDC法存在产品质量差、设备腐蚀严重和三废排放量大等缺点,现正逐步被MEA法取代。
基于此。
本文对EDC法和MEA法合成乙二胺的研究进展作一综述,希望能为合成乙二胺的研究工作提供有益的借鉴。
1.二氯乙烷法(EDC)二氯乙烷法通常在高压下由二氯乙烷和氨水液相直接反应制得,无需使用催化剂,乙二胺的单程收率在40%-70%之间。
主要反应如下:① ClCH2CH2Cl + 2NH3 → NH2CH2CH2NH2·2HCl ② Cl CH2CH2Cl + NH2CH2CH2NH2·2HCl + 2NH3 → NH4Cl + NH2CH2CH2NHCH2CH2NH2·3HCl ③ ClCH2CH2Cl + NH3 → ClCH=CH2 + NH4Cl二氯乙烷氨化反应属于快速、放热反应,主产物乙二胺为连串反应的中间产品,反应生成的乙二胺碱性要强于无机氨,所以会继续与二氯乙烷反应生成二乙烯三胺(DETA)、三乙烯四胺(TETA)以及其他多乙烯多胺。
研究表明改变反应压力、温度、酸度、以及产物的循环比可改变产物分布状况,提高此反应的氨烷比可以提高乙二胺的选择性,但是为了提高氨烷比就需要采用高浓度氨水,因此反应压力也随之上升,这就加大了对反应器结构耐压性的要求。
反应的产品分布不仅与反应的动力学特征有关,还与反应器的类型有关。
因此合适反应器的选取是影响产品分布的重要因素之一。
反应器可以分为釜式反应器和管式反应器。
张海江对反应器的类型和特点进行了总结,认为二氯乙烷氨化反应产品是连串反应的中间产物,采用管道化反应器的反应选择性较高。
张海江对在管道化反应器中以二氯乙烷法合成乙二胺的工艺进行研究,结果表明变温反应工艺与等温反应工艺相比,在相同的管道长度下提高了产品收率。
他将一段式等温管道化反应器改进为两段式变温管道化反应器,在内径4mm,总长度27m的反应器中,较适宜工艺条件为:第一段管道反应温度为160℃,反应时间1.5min,第二段管道温度130℃,反应时间8.5min,其它工艺条件(物料配比、体积流量和体系压力等)与等温反应工艺一致。
在此工况下,二氯乙烷的单程转化率可达98.6%,乙二胺收率60.1%。
传统的二氯乙烷法制乙二胺直接得到的是乙撑胺盐酸盐和氯化铵的混合物,需用氢氧化钠中和后才能得到乙撑胺的水溶液,乙撑胺中的乙二胺组分与水形成共沸物,给分离带来困难,副产氯化钠有效利用困难。
刘聪在醇介质中氨解二氯乙烷直接制得乙二胺,将乙醇或正丙醇、二氯乙烷、氨混合为溶掖,控制氨醇溶液中的氨质量浓度为15%-60%、氨与二氯乙烷的摩尔比为4-40,反应直接制得乙二胺。
这样分离容易,能耗低,降低原材料成本。
刘聪研究还发现氨的质量浓度高有利于降低热能消耗,氨与二氯乙烷摩尔比高有利于乙撑胺中伯胺组分的生成,氨解的时间与氨解时物料流动状态、温度、压力有关,即与氨解时反应物间的有效碰撞有关。
二氯乙烷法的优点是原料易得,无需催化剂,而且副产物多乙烯多胺和哌嗪26等是高附加值物质,国Dow化学公司、瑞典AKZO公司、荷兰Delamine公司以及日本Tosoh等公司采用该法进行生产。
国内由于工艺技术等方面的原因仍没有大规模采用该工艺,如能加强对二氯乙烷氨化工艺的研究开发,将有利于扩大二氯乙烷氨化法在国内的应用。
主要问题是反应中氯离子的在国外是一种重要的乙二胺工业生产方法,美产生对设备腐蚀性强,并且中和过程中产生大量的氯化钠,三废问题严重。
如何解决这些问题也有待进一步的研究。
2.乙醇胺法(MEA)乙醇胺法分为还原氨化工艺和缩合工艺,相应的催化剂按其反应机理也分为两类,一类为还原氨。
化催化剂,主要采用ⅧB族和ⅠB族金属或金属氧化物为催化剂活性组分,另一类为固体酸缩合催化剂,主要以Lewis酸、质子酸、杂多酸以及分子筛等为活性组分。
采用固体酸催化剂以乙醇胺和氨为原料生产乙二胺的方法具有反应压力低,产物收率高和污染小等优点,正逐渐成为未来发展的趋势。
2.1 乙醇胺还原胺化合成乙二胺该工艺在氢气氛中,以乙醇胺和氨为原料,以镍、钴、铜等金属为催化剂,反应温度150-230℃,反应压力20.0-30.OMPa,反应生成乙二胺、多乙烯多胺及哌嗪等,乙醇胺转化率为93%,乙二胺收率为74%。
其反应机理大体如下:乙醇胺具有2个活性接近的官能团,其与氨的反应较为复杂,容易发生分子内或分子间的串联反应,生成一系列的链状或环状副产物,导致反应选择性降低。
其中MEA的转化率和产物组成除了与反应条件有关外,还和催化剂的性质密切相关。
2.1.1 温度的影响有研究发现高的反应温度有利于MEA的转化,但高转化率会导致产物的选择性降低,并产生较高的环化副产物和少量的线性胺化副产物。
Renken在Ni-Cu-Cr催化剂的作用下研究了MEA的转化率和EDA的选择性随温度的变化规律,其研究表明低温有利于EDA的合成。
华明月等研究以ZSM-5分子筛为催化剂,从MEA和NH3合成乙撑胺的气固相反应,讨论了不同反应温度对反应物转化率和产物分布的影响,发现在300℃下,MEA的转化率较低,随着反应温度的提高,MEA的转化率迅速升离,EDA的选择性逐渐降低。
华明月等还进一步研究了具有不同酸性的3种改性ZSM-5分子筛催化剂对反应中MEA原料的转化率以及产物的选择性影响,同时讨论温度对反应的影响。
2.1.2 压力的影响Charles M.Barnes等研究发现在反应液含水量相同的条件下,NH3的浓度对NH3:MEA的影响呈正比例关系,加入10%H2O的情况下,NH3:MEA值越大,反应速度越快,EDA收率越高。
Lichtenberger在Ni基催化剂的作用下研究了氨压对MEA胺化反应的影响,发现氨压为13.17MPa时,EDA的选择性达到70%-90%;氨压小于8MPa 时,EDA的选择性只有40%。
白义国等人认为氢气分压对反应的影响较大,因为反应要经过加氢-脱氢两个过程。
Hironaka研究发现,在该反应中氢气分压高有利于环胺的生成,氢气分压低容易引起催化剂的失活。
D.常等认为氢气在胺化反应中并不是非常重要,它的作用只是保证催化剂处于活化状态。
2.1.3 乙醇胺还原胺化催化剂为进一步改善工艺条件,提高乙二胺收率,各国科研人员一直在着力研究还原氨化工艺用新型催化剂,并取得较好成果。
还原氨化工艺用催化剂早期多采用RaneyNi(Co)和改性的RaneyNi(Co)催化剂,后来发展为负载金属催化剂,载体采用Al2O3、SiO2、TiO2、ZrO2、MgO以及硅铝酸盐等多孔材料,催化剂可有效提高催化剂反应活性,降低反应压力。
近年来科研人员对还原氨化工艺用催化剂的研究取得了较好的成果。
如D.常等将Re、Ni、Co、B和Cu和(或)Ru等浸渍在a-氧化铝、氧化硅、氧化硅.氧化铝、硅藻土和氧化硅.氧化钛等载体材料上制得Re、Ni、Co、B和Cu和(或)Ru基催化剂。
弗劳恩克朗等将Ni、Co、Cu、Ru、Re、Rh、Pd或Pt中的2种或多种金属的混合物负载在Al2O3、TiO2、ZrO2和SiO2等氧化物载体上制成胺化催化剂。
Deeba等研究发现在乙醇胺还原氨化反应中低Cu-Ni比有利于生成EDA,高的Cu-Ni比有利于生成二乙烯三胺。
Legoff等研究了镍的负载量对催化剂活性的影响,发现随着镍负载量的增加,原料MEA的转化率不断提高,但是反应对环胺(如哌嗪)具有更高的选择性。
Lif等研究了在氢气和氨气氛围内,Al2O3负载的Ni基催化剂的失活现象,并把其失活的原因归结为活性组分Ni颗粒的迁移而引起的烧结。
赵锋伟、杨建明等研究了丝光沸石脱铝及金属改性等对合成乙二胺反应性能的影响,研究表明,脱铝改性时HCl溶液的最佳浓度为0.2mol·L-1,Cu和Zn改性可极大提高催化剂的活性和选择性。
Yuecheng Zhang等制得Co20/H-ZSM-5(25)[w(Co)=20%,m(Si):m(Al)=25]催化剂,并对其在MEA胺化反应当中的催他作用进行了深入研究。
研究发现Co20/H-ZSM-5(25)酌催化效果要明显好于H-ZSM-5(25)。
他们认为在还原胺化反应当中所采用的金属种类,载体材料酸性质以及金属与载体之间的相互作用等对于MEA还屠弼讹法制备EDA 具有极其重要的影响。
Deeba等采用稀有金属离子或氢来改性丝光沸石增加催化剂的表面酸性,提高催化反应的活性和选择性,其研究结果发现H和La等交换效果最好。
2.1.4 载体的影响载体对催化剂的性能起着重要作用。
催化剂的性能与载体材料的比表面积、孔径、孔容等密切相关,它们影响反应物料的吸附,脱附平衡,从而影响反应的转化率和选择性。
Barthey等研究发现比表面积为50-200m2·g-1,孔容为0.5-1.0mL·g-1的SiO2-Al2O3载体有助于提高反应对EDA的选择性。
Chang dane等认为比表面积在40-200m2·g-1的氧化铝、硅铝分子筛、硅钛分子筛等适合于作为载体材料。
Best等研究在Ni基催化剂中活性炭作为载体的催化活性,研究发现无论活性炭比表面积如何,均无催化活性。
D.常等指出在弘氧化铝、氧化硅、氧化硅.氧化铝、硅藻土和氧化硅,氧化钛等载体当中,最适合的是氧化硅基裁体。
弗劳恩克朗等研究了Al2O3、TiO2、ZrO2、SiO2和沸石等,研究发现其中沸石载体当中的丝光沸石、八面沸石和菱沸石催化效果最好。
载体的处理方法对催化剂性能也有较大的影响。
Juhan用质量分数为18%的HCl预处理载体,结果发现反应的活性和选择性有较大的提高。
2.1.5 助剂的影响助剂可以改善催化胺化反应的转化率和选择性。