汽车零件常用制造工艺基础知识
《汽车制造工艺》课件

发展历程
汽车制造工艺从传统手工生产转向现代自动化、信息化生产,并不断引进新技术、新工艺, 形成了高质量、高效率、低成本、多样化的生产体系。
汽车车身制造工艺
车身结构
包括整车车身、门、发动机 舱盖、行李箱盖及车门内饰 件等。
车身结构材料选择
随着汽车工业的发展,车身 材料逐渐由铁制品向铝、玻 璃钢及高聚合物材料转变。
电控系统中的器件制造 工艺
包括各种电子元器件、集成 电路和软件的制造和加工。
电控系统总成制造工艺
包括为实现汽车功能而综合 起来的微控制器的总成制造 工艺。
汽车装配制造工艺
1
汽车主要部件装配工艺
2
包括车身装配、发动机变速器、燃
油供应系统装配、电气系统装配等
过程。
3
汽车装配流水线
将汽车各部件在流水线上逐步安装、 调试直至整车组装完成。
汽车整车装配工艺
包括整车总装和质量检测等过程。
汽车制造工艺质量保证
1 汽车制造工艺质量控制要点
最终达成的质量水平来自于该过程的各个关键流程控制和关键零部件的质量控制。
2 汽车制造过程中的检测
包括原材料、零部件、总装品质量检测、过程检验、终检、试运转和冲洗等。
3 汽车制造质量问题的解决方法
充分的自我审视机制、持续的质量改进和完善的质量保证体系。
汽车制造工艺
本课程将带您了解汽车制造工艺的定义、分类、发展历程以及车身、发动机、 悬挂、电子控制、整车装配等方面的制造工艺流程。
汽车制造工艺概述
定义
是生产汽车所需的各种工艺、方法和操作的总体称谓。它包括产品设计、工艺设计、零件制 造、总装和产品检验等一系列的过程。
分类
按功能分类有五类如下:1.车身制造工艺;2.发动机制造工艺;3.悬挂制造工艺;4.电子控制 制造工艺;5.整车装配制造工艺。
汽车车身制造工艺的基本知识
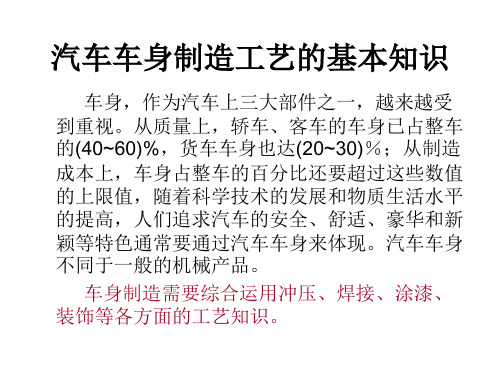
3.3 汽车车身制造工艺的基本知 识
3.3.1 汽车车身制造工艺
3.3 汽车车身制造工艺的基本知 识
3.3 汽车车身制造工艺的基本知 识
• 在车身冲压方面,实现了大型覆盖件的冲压生产机械化 或自动化、坯料准备即卷料的开卷、校平、剪切和落料 等的自动化以及冲压废料处理的自动化。现在正向着 CAD/CAM(车身设计、冲模设计、冲模制造和车身制造) 一体化系统的方向发展。 在车身装焊方面,从现在大量使用悬挂式点焊钳的装焊 生产线向以多点焊机为主的自动生产线过渡,并向着机 器人自动化装焊生产线的方向发展。 在车身涂饰方面,一方面通过开发低污染涂料——粉基 底漆及洁净面漆来降低车身生产对环境的污染,另一方 面,从漆前处理和涂漆自动生产线向着通过应用机器人、 传感嚣和微电子技术而实现整个涂饰车间自动化的方向 发展。
在负压气氛或真空中进行的热处理称为真空热处理它不仅能使工件不氧化不脱碳保持处理后工件表面光洁提高工件的性能还可以通入渗剂进行化学热处342表面热处理表面热处理是只加热工件表层以改变其表层力学性能的金属热处理工艺
汽车车身制造工艺的基本知识
车身,作为汽车上三大部件之一,越来越受 到重视。从质量上,轿车、客车的车身已占整车 的(40~60)%,货车车身也达(20~30)%;从制造 成本上,车身占整车的百分比还要超过这些数值 的上限值,随着科学技术的发展和物质生活水平 的提高,人们追求汽车的安全、舒适、豪华和新 颖等特色通常要通过汽车车身来体现。汽车车身 不同于一般的机械产品。 车身制造需要综合运用冲压、焊接、涂漆、 装饰等各方面的工艺知识。
• •
3.4 汽车制造过程中其它工艺基本知 识
3.4.1 热处理
1.金属热处理的概念 金属热处理是对固态金属或合金采用 适当方式加热、保温和冷却,以获得所需 要的组织结程中其它工艺基本知 识
汽车零部件专业知识
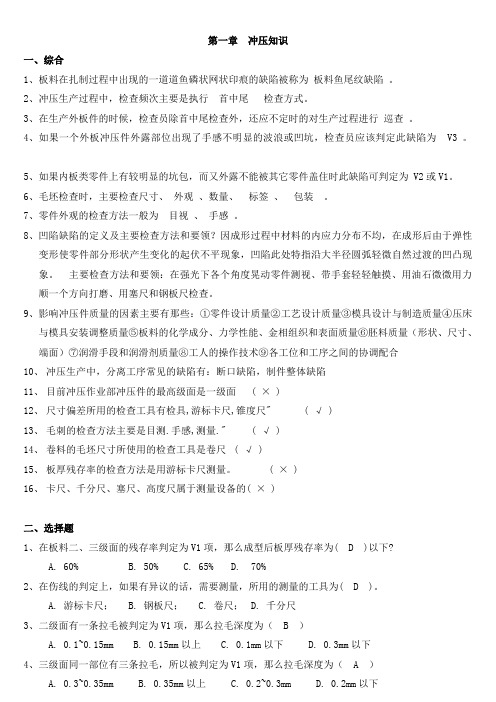
第一章冲压知识一、综合1、板料在扎制过程中出现的一道道鱼磷状网状印痕的缺陷被称为板料鱼尾纹缺陷。
2、冲压生产过程中,检查频次主要是执行首中尾检查方式。
3、在生产外板件的时候,检查员除首中尾检查外,还应不定时的对生产过程进行巡查。
4、如果一个外板冲压件外露部位出现了手感不明显的波浪或凹坑,检查员应该判定此缺陷为 V3 。
5、如果内板类零件上有较明显的坑包,而又外露不能被其它零件盖住时此缺陷可判定为 V2或V1。
6、毛坯检查时,主要检查尺寸、外观、数量、标签、包装。
7、零件外观的检查方法一般为目视、手感。
8、凹陷缺陷的定义及主要检查方法和要领?因成形过程中材料的内应力分布不均,在成形后由于弹性变形使零件部分形状产生变化的起伏不平现象,凹陷此处特指沿大半径圆弧轻微自然过渡的凹凸现象。
主要检查方法和要领:在强光下各个角度晃动零件测视、带手套轻轻触摸、用油石微微用力顺一个方向打磨、用塞尺和钢板尺检查。
9、影响冲压件质量的因素主要有那些:①零件设计质量②工艺设计质量③模具设计与制造质量④压床与模具安装调整质量⑤板料的化学成分、力学性能、金相组织和表面质量⑥胚料质量(形状、尺寸、端面)⑦润滑手段和润滑剂质量⑧工人的操作技术⑨各工位和工序之间的协调配合10、冲压生产中,分离工序常见的缺陷有:断口缺陷,制件整体缺陷11、目前冲压作业部冲压件的最高级面是一级面( × )12、尺寸偏差所用的检查工具有检具,游标卡尺,锥度尺" ( √ )13、毛刺的检查方法主要是目测.手感,测量." ( √ )14、卷料的毛坯尺寸所使用的检查工具是卷尺( √ )15、板厚残存率的检查方法是用游标卡尺测量。
( × )16、卡尺、千分尺、塞尺、高度尺属于测量设备的( × )二、选择题1、在板料二、三级面的残存率判定为V1项,那么成型后板厚残存率为( D )以下?A. 60%B. 50%C. 65%D. 70%2、在伤线的判定上,如果有异议的话,需要测量,所用的测量的工具为( D )。
汽车制造技术基础
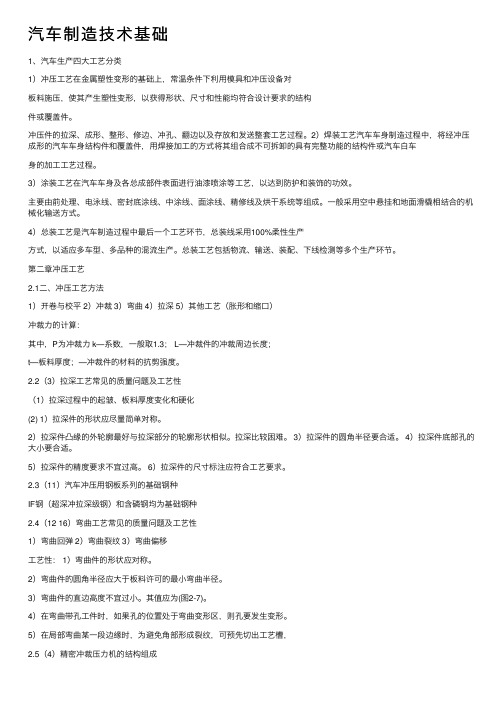
汽车制造技术基础1、汽车⽣产四⼤⼯艺分类1)冲压⼯艺在⾦属塑性变形的基础上,常温条件下利⽤模具和冲压设备对板料施压,使其产⽣塑性变形,以获得形状、尺⼨和性能均符合设计要求的结构件或覆盖件。
冲压件的拉深、成形、整形、修边、冲孔、翻边以及存放和发送整套⼯艺过程。
2)焊装⼯艺汽车车⾝制造过程中,将经冲压成形的汽车车⾝结构件和覆盖件,⽤焊接加⼯的⽅式将其组合成不可拆卸的具有完整功能的结构件或汽车⽩车⾝的加⼯⼯艺过程。
3)涂装⼯艺在汽车车⾝及各总成部件表⾯进⾏油漆喷涂等⼯艺,以达到防护和装饰的功效。
主要由前处理、电泳线、密封底涂线、中涂线、⾯涂线、精修线及烘⼲系统等组成。
⼀般采⽤空中悬挂和地⾯滑橇相结合的机械化输送⽅式。
4)总装⼯艺是汽车制造过程中最后⼀个⼯艺环节,总装线采⽤100%柔性⽣产⽅式,以适应多车型、多品种的混流⽣产。
总装⼯艺包括物流、输送、装配、下线检测等多个⽣产环节。
第⼆章冲压⼯艺2.1⼆、冲压⼯艺⽅法1)开卷与校平 2)冲裁 3)弯曲 4)拉深 5)其他⼯艺(胀形和缩⼝)冲裁⼒的计算:其中,P为冲裁⼒ k—系数,⼀般取1.3; L—冲裁件的冲裁周边长度;t—板料厚度;—冲裁件的材料的抗剪强度。
2.2(3)拉深⼯艺常见的质量问题及⼯艺性(1)拉深过程中的起皱、板料厚度变化和硬化(2) 1)拉深件的形状应尽量简单对称。
2)拉深件凸缘的外轮廓最好与拉深部分的轮廓形状相似。
拉深⽐较困难。
3)拉深件的圆⾓半径要合适。
4)拉深件底部孔的⼤⼩要合适。
5)拉深件的精度要求不宜过⾼。
6)拉深件的尺⼨标注应符合⼯艺要求。
2.3(11)汽车冲压⽤钢板系列的基础钢种IF钢(超深冲拉深级钢)和含磷钢均为基础钢种2.4(12 16)弯曲⼯艺常见的质量问题及⼯艺性1)弯曲回弹 2)弯曲裂纹 3)弯曲偏移⼯艺性: 1)弯曲件的形状应对称。
2)弯曲件的圆⾓半径应⼤于板料许可的最⼩弯曲半径。
3)弯曲件的直边⾼度不宜过⼩。
汽车制造工艺学复习资料 (1)
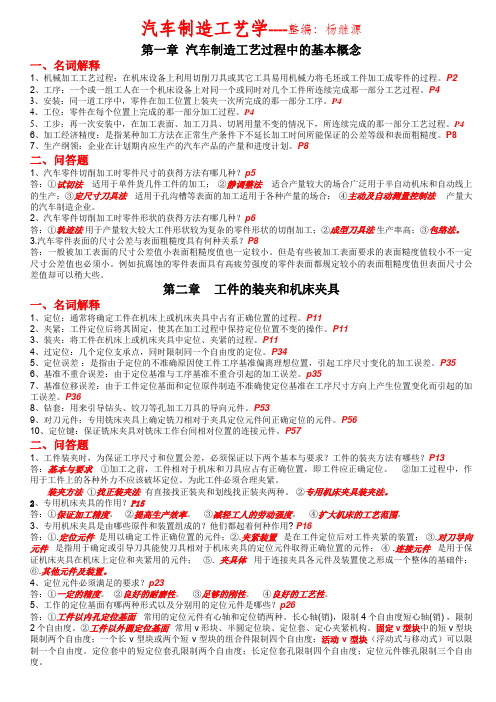
汽车制造工艺学----整编:杨继源第一章汽车制造工艺过程中的基本概念一、名词解释1、机械加工工艺过程:在机床设备上利用切削刀具或其它工具易用机械力将毛坯或工件加工成零件的过程。
P22、工序:一个或一组工人在一个机床设备上对同一个或同时对几个工件所连续完成那一部分工艺过程。
P43、安装:同一道工序中,零件在加工位置上装夹一次所完成的那一部分工序。
P44、工位:零件在每个位置上完成的那一部分加工过程。
P45、工步:再一次安装中,在加工表面、加工刀具、切屑用量不变的情况下,所连续完成的那一部分工艺过程。
P46、加工经济精度:是指某种加工方法在正常生产条件下不延长加工时间所能保证的公差等级和表面粗糙度。
P87、生产纲领:企业在计划期内应生产的汽车产品的产量和进度计划。
P8二、问答题1、汽车零件切削加工时零件尺寸的获得方法有哪几种?p5答:①试切法适用于单件货几件工件的加工;②静调整法适合产量较大的场合广泛用于半自动机床和自动线上的生产;③定尺寸刀具法适用于孔沟槽等表面的加工适用于各种产量的场合;④主动及自动测量控制法产量大的汽车制造企业。
2、汽车零件切削加工时零件形状的获得方法有哪几种?p6答:①轨迹法用于产量较大较大工件形状较为复杂的零件形状的切削加工;②成型刀具法生产率高;③包络法。
3.汽车零件表面的尺寸公差与表面粗糙度具有何种关系?P8答:一般被加工表面的尺寸公差值小表面粗糙度值也一定较小。
但是有些被加工表面要求的表面糙度值较小不一定尺寸公差值也必须小。
例如抗腐蚀的零件表面具有高疲劳强度的零件表面都规定较小的表面粗糙度值但表面尺寸公差值却可以稍大些。
第二章工件的装夹和机床夹具一、名词解释1、定位:通常将确定工件在机床上或机床夹具中占有正确位置的过程。
P112、夹紧:工件定位后将其固定,使其在加工过程中保持定位位置不变的操作。
P113、装夹:将工件在机床上或机床夹具中定位、夹紧的过程。
P114、过定位:几个定位支承点,同时限制同一个自由度的定位。
《汽车制造工艺》课件

PART 03
汽车发动机制造工艺
铸造工艺
总结词
通过将熔融的金属倒入模具中,待其冷却凝固后形成发动机零部件的过程。
详细描述
铸造工艺是发动机制造过程中常见的工艺之一,主要用于生产发动机缸体、缸 盖等大型零部件。铸造过程中,需要确保模具的精度和质量,以获得合格的发 动机零部件。
锻造工艺
总结词
通过施加外力使金属坯料变形,从而得到所需形状和大小的发动机零部件的过程 。
02
03
早期汽车制造
19世纪末至20世纪初,汽 车制造开始起步,主要采 用手工制作,结构简单。
流水线生产
20世纪初,福特汽车公司 引入流水线生产方式,大 大提高了生产效率。
现代化制造
随着科技的发展,汽车制 造逐渐实现自动化、数字 化和智能化。
汽车制造的工艺流程
冲压工艺
焊接工艺
涂装工艺
总装工艺
利用冲压机将钢板冲压 成各种形状的零件。
详细描述:涂装工艺所使用的材料主要包括油漆、清漆 、色漆和底漆等,这些材料具有防腐、耐磨、耐候和美 观等特点。
详细描述:涂装工艺具有防腐性能强、装饰效果好、高 耐磨性和高耐候性的特点,能够满足汽车制造的高要求 。
总装工艺
在此添加您的文本17字
总结词:最后一道工序
在此添加您的文16字
详细描述:总装工艺是汽车制造中的最后一道工序,主要 是将各个零部件组装成一个完整的汽车。
在此添加您的文本16字
总结词:主要设备
在此添加您的文本16字
详细描述:总装工艺的主要设备是装配线和装配台,它们 能够实现高效、高精度和高自动化的装配。
在此添加您的文本16字
总结词:工艺特点
在此添加您的文本16字
汽车机械制造的机械加工工艺

汽车机械制造的机械加工工艺汽车作为现代社会交通工具的代表,其机械制造过程中的机械加工工艺至关重要。
机械加工工艺是指通过各种机械手段对汽车零部件进行形状、尺寸或者性能的加工和变换。
本文将从汽车机械制造的角度,探讨几种常见的机械加工工艺。
1.车削加工车削加工是最常见的机械加工工艺之一。
它利用车床或车床加工中心等设备,将旋转的工件固定在主轴上,然后通过刀具对工件进行切削,从而改变工件的外形和尺寸。
在汽车制造中,车削加工常用于发动机缸套、凸轮轴等部件的制造。
2.铣削加工铣削加工是通过铣床等设备对工件进行切削的一种机械加工工艺。
铣床上的铣刀旋转,将工件锁定在工作台上,然后通过刀具在工件上进行切削,从而获得所需的形状和尺寸。
在汽车制造中,铣削加工常用于制造曲轴、齿轮等精密部件。
3.钻削加工钻削加工是利用钻床等设备对工件进行孔加工的一种机械加工工艺。
钻床上的钻头旋转,通过对工件施加下压力,使钻头在工件上转动和前进,从而形成孔洞。
在汽车制造中,钻削加工常用于车身和底盘等部位的孔加工。
4.磨削加工磨削加工是通过磨床等设备对工件进行磨削的一种机械加工工艺。
磨床上的磨轮旋转,通过对工件施加切割力和磨削液的冷却,使磨轮与工件之间发生相对运动,从而实现工件的表面精密加工。
在汽车制造中,磨削加工常用于发动机曲轴、凸轮轴等高精度部件的制造。
5.螺纹加工螺纹加工是通过车床等设备对工件进行螺纹加工的一种机械加工工艺。
车床上的刀具按特定的螺旋轨迹与工件表面接触,从而形成螺纹。
在汽车制造中,螺纹加工常用于制造紧固件、传动装置等部件。
除了以上提到的几种常见的机械加工工艺,汽车机械制造还涉及到其他多种加工方式,如冲压、焊接、铸造等。
这些机械加工工艺之间互相配合,共同为汽车的制造提供保障,确保汽车零部件的尺寸精度、表面质量和性能要求。
总结起来,汽车机械制造的机械加工工艺包括车削加工、铣削加工、钻削加工、磨削加工和螺纹加工等多种方式。
这些加工工艺的运用,不仅能够满足汽车零部件的形状、尺寸和性能要求,还能够提高生产效率和产品质量,为汽车行业的发展做出贡献。
汽车制造中的汽车底盘部件的组装工艺

汽车制造中的汽车底盘部件的组装工艺在汽车制造过程中,汽车底盘部件的组装工艺是至关重要的一环。
汽车底盘作为整车的基础骨架,承载着车身负荷和车辆的动力系统,其质量和装配精度直接影响着整车的性能和安全性。
本文将深入探讨汽车底盘部件的组装工艺,包括工艺流程、工艺方法和质量控制等方面。
一、工艺流程汽车底盘部件的组装工艺流程通常包括以下几个关键步骤:1. 零部件准备:在组装之前,各个底盘部件需要进行清洗、涂漆、标记等预处理。
同时,需要根据设计图纸和工艺要求对零部件进行检查和测量,以确保其质量和尺寸的准确性。
2. 部件装配:根据装配图纸和工艺要求,将各个底盘部件按照顺序装配起来。
在这个过程中,需要严格控制装配顺序、装配方法和装配力度,以确保零部件的正确配合和装配质量。
3. 熔接工艺:对于一些需要进行熔接的底盘部件,如车架和悬挂系统等,需要采用适当的熔接方法,如气体焊接、电弧焊接或摩擦焊接等。
在熔接过程中,需要注意焊接参数的选择和控制,以确保焊接接头的强度和密封性。
4. 螺栓连接:在底盘部件的组装中,常常使用螺栓连接来固定零部件。
螺栓连接需要根据设计要求进行预紧力的控制,以确保连接的紧固度和可靠性。
5. 质检和调试:在底盘组装完成后,需要对整车进行质量检验和调试。
质检包括外观检查、尺寸检测和功能检测等,以确保底盘部件装配的质量和性能符合要求。
同时,还需要对底盘进行调试,包括悬挂系统的调整和刹车系统的校准等,以确保底盘的平稳性和操控性。
二、工艺方法在汽车底盘部件的组装过程中,可以采用多种工艺方法来提高装配效率和质量。
1. 自动化装配:借助机器人和自动化设备,可以实现对底盘部件的自动装配。
自动化装配可以提高装配速度和精度,减少人为因素对装配质量的影响。
2. 模块化设计:将底盘部件划分为多个模块,各个模块之间采用标准接口进行连接。
这样可以简化装配过程,提高模块的通用性和可维护性,同时也方便后期的维修和更换。
3. 先进的装配工具:采用先进的装配工具,如扭矩扳手、液压千斤顶和气动工具等,可以提高装配精度和效率。
- 1、下载文档前请自行甄别文档内容的完整性,平台不提供额外的编辑、内容补充、找答案等附加服务。
- 2、"仅部分预览"的文档,不可在线预览部分如存在完整性等问题,可反馈申请退款(可完整预览的文档不适用该条件!)。
- 3、如文档侵犯您的权益,请联系客服反馈,我们会尽快为您处理(人工客服工作时间:9:00-18:30)。
2、 铸件浇注位置和分型面的选择 铸件浇注位置:指铸件在铸型中的位置与姿态
选择铸件浇注位置要考虑以下原则: a. 铸件的重要加工面、主要工作面应朝下或在侧面
(图12、13):保证组织均匀、致密;
b、大平面朝下(图2-14):在上时,由于热上升,型砂膨胀, 易使铸件拱起
c. 铸件薄壁部分应放在下部(图2-15):下部组织均匀、防 热拱起
第二章 汽车零件常用制造工艺基础
第一节 铸造工艺基础 第二节 锻造工艺基础 第三节 焊接工艺基础 第四节 冲压工艺基础 第五节 粉末冶金工艺基础 第七节 毛坯的选择
第一节 铸造工艺基础
一、概述
• 铸造:将熔化的金属液浇注到铸型中,待其凝固 冷却后, 获得一定形状的零件毛坯或零件的成形方
法。铸造的毛坯或零件称为铸件。
• 特点:“一型多铸”,铸件精度和力学性能高。尺寸
精度IT12-IT16,表面粗糙度Ra6.3-12.5
• 应用:用于形状不复杂的中、小铸件的大批量生产中。
如汽车中的铝合金缸盖、进气管及活塞等。 工艺措施:1)排气;2)型腔喷耐火涂料;3)预热 金属型
• 2. 压力铸造(压铸机+金属膜)
• 概念:指将熔融金属在高压下高速充型,并在压力下凝固
2-21); d. 应尽量减少型芯和活块的数量(图2-21)。
方案a:制模(手工)的过程中需要手工翻动 沙箱,取出样模,生产率低, 方案b:需用三箱手工造型 方案c:两箱机器造型
减小错箱误差,保证位置精度(加工基准面为 φ350,内孔与其在一个箱容易保证二者位置 精度和组织的均匀。 若以φ350为分型面,虽可简化型芯,但分型 面处铸造质量难以保证
铸件材质:铸铁、铸钢、铸铝、铸铜 铸铁:白口:C以FeC形式存在
灰口:C以片状自由态存在 球铁:C以球状自由态存在 可锻:C以团絮状存在 蠕墨:灰口铁中添加稀土元素
车用铸件特点与分类:
特点:1、薄壁、形状复杂、尺寸精度高; 2、生产批量大; 3、材质要求高,如强韧、抗压等。
分类:砂型铸造(>90%)和特种铸造
•——排气困难,这可导致铸件表皮下产生含气体的微孔,容 易引起压铸件变形。因此,压力铸造铸件不能进行热处理。
• 结构工艺性:可铸出细小的螺纹、孔、齿、文字等;适用
于薄壁件(铝合金:1.5-5mm,铜合金2-5mm);
•应用: 在汽车压铸造
• 概念:在20-60kPa的压力下,使金
d. 易形成缩孔的铸件,较 厚的部分保证铸件实现定
向凝固(图2-16); e. 尽量减少型芯,利于其 安放、合型、排气(图2-
17)。
分型面:两个半铸型相互接触的表面 选择分型面要考虑以下原则:
a. 分型面应尽量采用平面(图2-19);
b. 分型面数量尽量少(图2-20); c. 尽量使铸件全部或大部分放在同一砂型中(图
(五)铸造工艺图:用工艺符号或文字,将
铸造工艺方案、工艺参数、型芯等绘制在零件图上形成的 图形。
四、特种铸造
• 特种铸造:指与砂型铸造不同的其他铸造方法。 • 方法种类:金属型铸造、压力铸造、低压铸造、离心铸造、熔
模铸造、陶瓷型铸造、石膏型铸造等等。
1. 金属型铸造
• 概念:借助重力将熔融金属浇注入金属铸型获得铸件的 方法. 常用的垂直分型式金属型如图2-6所示。
属液自下而上热压入铸型并在压力下 结晶凝固的铸造方法。原理如图2-8。
• 特点:压力可控,压力下凝固,组
织致密,无缺陷。成品率高,金属利 用率高(可达95%)。铸件表面粗糙度 可达IT14-lTl2,最小壁厚为2-5mm。
(四). 工艺参数的选择
铸造工艺方案确定以后,还要选择各种工艺参数。
(1) 加工余量:为进行机械加工,铸件比零件增大的一层
金属称为加工余量 加工余量取决于铸造合金的种类、造型方法、铸件
大小及加工面在铸型中的位置等诸多因素。 一般,各种铸造方法的加工余量可参阅《机械制造手 册》。
(2) 起模斜度:为使模样便于从铸型中取出,垂直于分型
合金的铸造性能
1 流动性: 液态合金的流动能力,影响充型能力。 ——流动性好,则充型能力强,铸造缺陷少 ——影响因素:合金成分、浇注温度\压力和
铸型等
2. 收缩性:液态与凝固收缩是产生缩孔(宏观)、缩
松(微观)的基本原因;固态收缩是产生内应力、 变形和裂纹的基本原因。
影响因素:合金成分,浇注温度、铸型等。
面的立壁要有一定的斜度,称之为起模斜度。 一般取 0.5°~ 4°。
(3) 铸造圆角:防止铸件连接和拐角处产生应力、裂纹,
防止铸型的尖角损坏和产生砂眼。
• (4) 型芯头:保证型芯在铸型中的定位、 固定和排气,型模和型芯都要设计出型 芯头,型芯要有排气孔。
• (5) 收缩余量:为补偿铸件收缩,模样要 比铸件图纸尺寸略大,这个增大的数值 称为收缩余量。一般灰铸铁的收缩余量 为0.8%-1.0%,铸钢为1.8 %-2.2%,铸 造铝合金为1.0%-1.5%。收缩余量大小 通常与合金种类、铸造工艺、铸件在收 缩时的受阻情况等有关。
的铸造方法。压力铸造使用的压铸机如图2-7所示。
• 特点:
•——高压、高速充型(压力:5-150MPa,时间:<0.15s,充 填速度:5-100m/s),无流动性问题,生产率很高,适用于大 批量生产(设备、铸型投资大)。
•——组织细密,精度高:力学性能比砂型铸造提高20%-40%。 精度:IT11-IT13,Ra1.6-6.3
套筒的砂型铸造过程示意图
•(二)造型材料与造型方法
• 造型材料 • 型砂、芯沙:砂、粘结剂(粘土、桐
油、合成脂等)、特殊附加物(如:木屑 增加透气性;煤粉加强防粘性)。 • 芯砂要比型砂具有更好的耐火性、强度、 透气性、退让性(不阻碍收缩)。 • 造型方法:手工造型与机器造型
(三)砂型制造 • 1、砂型的组成
3. 偏析及吸气性:
偏析: 铸件中出现化学成分不均匀的现象称为 偏析,偏析使铸件性能不均匀;
吸气性:熔炼、浇注时吸收气体的性能。冷凝 时如气体不逸出,会在铸件中形成气孔或夹杂物 (如FeO)。
降低吸气性的方法主要有:缩短熔炼时间,炉料 烘干;加保护气;提高铸型和型芯透气性;降低含水 量等。
二、砂型铸造的造型工艺 (一) 砂型铸造的工艺过程