刀具产品检测方法
NPT螺纹以及检测方法详解
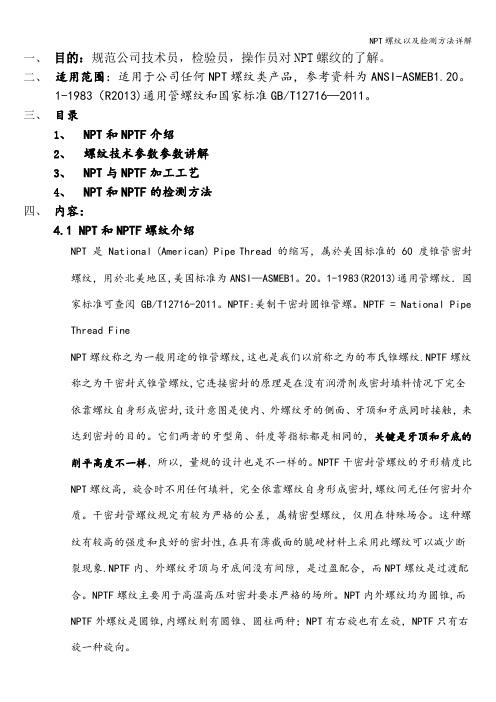
一、目的:规范公司技术员,检验员,操作员对NPT螺纹的了解。
二、适用范围:适用于公司任何NPT螺纹类产品,参考资料为ANSI-ASMEB1.20。
1-1983(R2013)通用管螺纹和国家标准GB/T12716—2011。
三、目录1、NPT和NPTF介绍2、螺纹技术参数参数讲解3、NPT与NPTF加工工艺4、NPT和NPTF的检测方法四、内容:4.1 NPT和NPTF螺纹介绍NPT 是 National (American) Pipe Thread 的缩写,属於美国标准的 60 度锥管密封螺纹,用於北美地区,美国标准为ANSI—ASMEB1。
20。
1-1983(R2013)通用管螺纹.国家标准可查阅 GB/T12716-2011。
NPTF:美制干密封圆锥管螺。
NPTF = National PipeThread FineNPT螺纹称之为一般用途的锥管螺纹,这也是我们以前称之为的布氏锥螺纹.NPTF螺纹称之为干密封式锥管螺纹,它连接密封的原理是在没有润滑剂或密封填料情况下完全依靠螺纹自身形成密封,设计意图是使内、外螺纹牙的侧面、牙顶和牙底同时接触,来达到密封的目的。
它们两者的牙型角、斜度等指标都是相同的,关键是牙顶和牙底的削平高度不一样,所以,量规的设计也是不一样的。
NPTF干密封管螺纹的牙形精度比NPT螺纹高,旋合时不用任何填料,完全依靠螺纹自身形成密封,螺纹间无任何密封介质。
干密封管螺纹规定有较为严格的公差,属精密型螺纹,仅用在特殊场合。
这种螺纹有较高的强度和良好的密封性,在具有薄截面的脆硬材料上采用此螺纹可以减少断裂现象.NPTF内、外螺纹牙顶与牙底间没有间隙,是过盈配合,而NPT螺纹是过渡配合。
NPTF螺纹主要用于高温高压对密封要求严格的场所。
NPT内外螺纹均为圆锥,而NPTF外螺纹是圆锥,内螺纹则有圆锥、圆柱两种;NPT有右旋也有左旋,NPTF只有右旋一种旋向。
用NPTF丝锥在攻NPT螺纹是可以接受的,但是NPT丝锥不能用于NPTF螺纹,因为它生产的螺纹会漏气。
钨钢鉴别方法

钨钢鉴别方法
针对目前公司所用刀具W18Cr4V(简称W18)、W6Mo5Cr4V2(简称W6或6542),W18价格低廉,使用寿命短;6542为通用型刀具用钢,具有优异的性能和性价比。
为对其材质成分进行区分,分类总结如下鉴别方法,以供参考。
表1 HSS W18和6542的鉴别方法
光谱法(看谱镜)物质的原子或离子被激发时,发射出不同波长的
光。
依据反射光不同的波长和强度,对合金中元
素的成分和含量进行定性和半定量分析。
可快速鉴别,适于
现场批量检测和单
个产品检测,需借
助于专业检测设
备。
根据不同鉴别方法的特点,结合公司需求,推荐采用化学法和光谱法,也可采用两种或多种方法配合使用。
以上。
2014 / 1 / 6。
TBM盘形滚刀的质量控制及其检测维修技术

般都达到 4 %.高者达到 6 %。提高 T M 的利用率 ,也 多 .对掘 进 的影响 也就 会大 。 0 0 B 就是要提高 TBM 施工 的技术水平 .减少各施 工工序对 要减 少这种掘进进 行中产 生的刀具故 障 .必须严格
B 8 E型 掘 进 机 的 1 ”盘 形 滚 刀 检 测 和 维 修 技 术 的 7 其 技 术 性 能 的 优 劣是 扩 大 TBM 施 工 适 用 范 围和 降 低 施 对 T 8 0 工造价 的关键 技术 之一 .国外各 著名 TBM 生产 厂家对 总 结 可 供 借 鉴 。 刀具 都 进 行 了长 期 的研 究 .不 断 改 进 T 刀 具 的 性 能 BM 使 产 品 具 有 竞 争 力 。 但 刀 具 性 能 必 须 在 施 工 中 正 确 使
机 器 正 常 运 转 的 影 响 ,是 当 前在 我 国扩 大 T BM 施 工 使 控制上机掘进 的刀具质量 .通 过在洞外对 刀具 进行严格 用范围降低 T BM 施 工 造 价 的 关键 。
检测并仔细地维修 ,使运进 洞内上机掘进 的刀 具在刀 圈
西康铁路秦 岭隧道 出 1 TBM 施 工中 ,由于刀具原 磨 损 到极 限 尺寸 前发 生 因检测 维修 不 当造成 的 密封 漏 : 3 因造成 的停机时间 占施工时间的比率 为 1 . % ,也就是 油 、轴承损坏 、连接与配合失效 等故 障 占所有检测维修 3 6 每天 1 h的掘进施工 ( 8 每天安排 6 h为 T M施工做 整各 , 刀 具 总 数 的 比 率 小 于 5% 这 就 会 大 为 减 少 掘 进 中 发 生 B 1 h进行掘进施工 )时间 内平均有近 3 8 h的时间是因刀 的被 动性换刀 。减少 了因换刀停机 的时 间 .提 高机器 的
刀具检测报告

刀具检测报告(经典版)编制人:__________________审核人:__________________审批人:__________________编制单位:__________________编制时间:____年____月____日序言下载提示:该文档是本店铺精心编制而成的,希望大家下载后,能够帮助大家解决实际问题。
文档下载后可定制修改,请根据实际需要进行调整和使用,谢谢!并且,本店铺为大家提供各种类型的经典范文,如职场文书、公文写作、党团资料、总结报告、演讲致辞、合同协议、条据书信、心得体会、教学资料、其他范文等等,想了解不同范文格式和写法,敬请关注!Download tips: This document is carefully compiled by this editor. I hope that after you download it, it can help you solve practical problems. The document can be customized and modified after downloading, please adjust and use it according to actual needs, thank you!Moreover, this store provides various types of classic sample essays for everyone, such as workplace documents, official document writing, party and youth information, summary reports, speeches, contract agreements, documentary letters, experiences, teaching materials, other sample essays, etc. If you want to learn about different sample formats and writing methods, please pay attention!刀具检测报告在现在社会,报告的用途越来越大,要注意报告在写作时具有一定的格式。
基于深度学习的刀具磨损状态检测综述
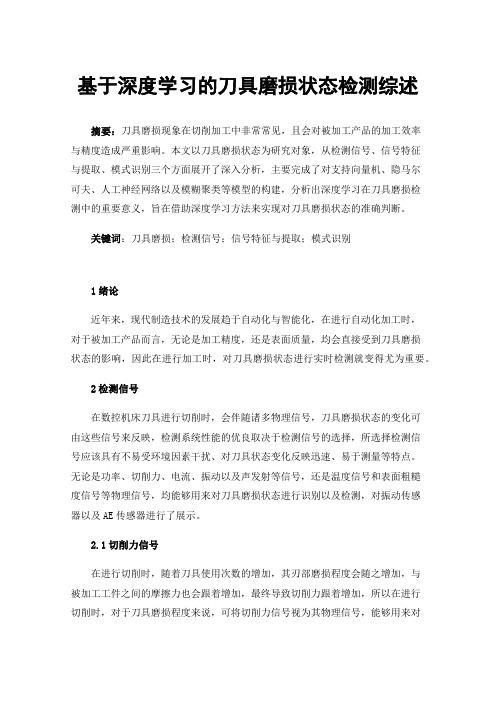
基于深度学习的刀具磨损状态检测综述摘要:刀具磨损现象在切削加工中非常常见,且会对被加工产品的加工效率与精度造成严重影响。
本文以刀具磨损状态为研究对象,从检测信号、信号特征与提取、模式识别三个方面展开了深入分析,主要完成了对支持向量机、隐马尔可夫、人工神经网络以及模糊聚类等模型的构建,分析出深度学习在刀具磨损检测中的重要意义,旨在借助深度学习方法来实现对刀具磨损状态的准确判断。
关键词:刀具磨损;检测信号;信号特征与提取;模式识别1绪论近年来,现代制造技术的发展趋于自动化与智能化,在进行自动化加工时,对于被加工产品而言,无论是加工精度,还是表面质量,均会直接受到刀具磨损状态的影响,因此在进行加工时,对刀具磨损状态进行实时检测就变得尤为重要。
2检测信号在数控机床刀具进行切削时,会伴随诸多物理信号,刀具磨损状态的变化可由这些信号来反映,检测系统性能的优良取决于检测信号的选择,所选择检测信号应该具有不易受环境因素干扰、对刀具状态变化反映迅速、易于测量等特点。
无论是功率、切削力、电流、振动以及声发射等信号,还是温度信号和表面粗糙度信号等物理信号,均能够用来对刀具磨损状态进行识别以及检测,对振动传感器以及AE传感器进行了展示。
2.1切削力信号在进行切削时,随着刀具使用次数的增加,其刃部磨损程度会随之增加,与被加工工件之间的摩擦力也会跟着增加,最终导致切削力跟着增加,所以在进行切削时,对于刀具磨损程度来说,可将切削力信号视为其物理信号,能够用来对前者进行反映。
大部分研究人员以刀具磨损以及切削力为研究对象,通过对其的研究来完成对两者映射关系的建立。
2.2振动信号振动信号是由于切削过程中被加工产品与刀具刃部之间相互接触碰撞而产生的一种信号。
无论是刀具和被加工部件间所存在的动态相互作用,还是机器部件所存在的周期性运动,均能够导致机床振动的出现。
机床振动能够对加工性能带来不利影响,同时降低了刀具的使用寿命以及加工工件的表面质量,使刀具更易出现磨损。
PCD质量检测方法

复合片的性能检测方法1、耐磨性复合片的耐磨性一般是通过磨耗比这个指标来衡量的,但迄今为止国际上也没有制定统一的测试标准,几个主要的PDC生产国均有其自己的测试方法。
美国的GE公司采用的方法是用PDC来车削一种结构均匀的花岗岩棒,切削速度为180 m/min,切深为1 mm,进给量为0. 28 mm/r。
车削时用测力计测PDC的受力大小。
车削一定数量的花岗岩后,观察PDC 的磨损量。
磨损量是用投影显微镜测量被磨损部位的长宽尺寸,然后用计算机算出其体积,进行比较。
英国De Beers公司的方法与GE公司类似。
前苏联对PDC耐磨性的测定是用PDC 来刨削指定地区采来的石英砂岩。
石英砂岩采自顿涅茨地区托列兹露采厂,尺寸为500 mm×300 mm×250 mm。
PDC固定在牛头刨床的刀具上,测试时,切削速度为0. 55m/s,切深为0. 5mm,横向进给量为2. 8m/行程,每片PDC样品检测的切削长度为501 m。
PDC磨耗值为其金刚石层磨损面中心部分的线高度(用工具显微镜测量,误差为0.03mm)。
这2种方法各有优点:用砂轮可统一规范标准,即使不能完全规范标准,也相差不大,且能通过计算求出较准确的磨削值。
用花岗岩更加符合应用范畴。
但它们的缺点也是很明显的:只对复合片局部测试,不能判断整个复合片的质量;只能判断复合片的耐磨性能优劣,不能找到磨耗比大小的原因,是一种破坏性实验。
国内通过6面顶合成出来的复合片一开始是采用工具磨床进行磨耗比测定,但误差甚大。
郑州磨料所和桂林金刚石厂首先提出要研制专用仪器,后由桂林金刚石厂陈朝华和彭为云等研制设备,郑州磨料所汪荣华、黄祥芬,桂林金刚石厂方啸虎等进行测试方法和标准的研究,得到了现在普遍使用的磨耗比测定仪和测定方法。
这种检测方法自动化程度高、检测效率高,且可大大降低劳动强度。
目前还有一种测试方法,主要是通过XRD、Raman光谱法及SEM等对复合片进行综合测试,这几种方法综合使用可对复合片金刚石层的耐磨性能做出准确的判断,不仅可判断复合片质量的优劣,还能给出复合片金刚石层耐磨性能优劣的原因及改进方法,这种方法还未普遍使用。
CNC加工检验标准

1目的为了规范CNC加工产品的加工标准及检验标准,给判定者提供可靠的依据2范围适用于本公司以及外协厂的CNC加工工件的可靠性验证和外观检验3检验项目及定义3.1刀纹:由于刀具磨损或摆动产生的纹路,通常有触感,呈浪状;3.2碰伤:由于操作不当产生碰撞或跌落行程塌陷状;3.3气孔、砂眼:由于铸造密度不够,形成不规则孔状缺陷或蜂窝状黑点;3.4擦伤:由于操作不当产品发生摩擦形成条状缺陷,或由于刀具附有残留切削废料形成螺旋线状缺陷;3.5段差(台阶):由于刀路斜接不顺畅,形成台阶状缺陷;3.6毛刺:由于刀具径向作用力导致局部切削废料未脱离工件形成锯齿状或条状缺陷;3.7缺料:由于刀具磨损后切削作用力过大导致产品薄弱处崩边或缺肉;3.8烂牙:由于攻丝底径偏小或偏大、底孔歪斜、丝锥磨损导致螺纹局部紊乱、无螺纹、牙型不符3.9压伤:由于加工治具存有切削残渣或受外力影响,将杂质压入产品内部呈凹陷状缺陷;3.10裂纹:由于铸造致密度不够或刀具磨损导致切削作用力过大造成薄弱处呈撕裂状缺陷;3.11切削不良:由于产品在治具固定位置发生偏移或刀具相对坐标发生变化造成切削量过大或偏小;包括过切或少切,其中少切也叫多料;3.12孔偏:由于定位不当或加强柱歪斜,甚至压铸产品缩水不均导致孔位与该孔所在加强柱中心发生偏离;3.13倒角不良:由于装配或安全因素对产品锐边进行工艺倒角,若图面无特殊要求按照C0.2±0.1管控,螺纹倒角须保证攻丝披锋不高出螺丝柱顶面(即披锋高度要低于倒角高度),倒角不良分两种状况:a、倒角过大,由于刀具或程序控制存有吃刀过深,造成倒角偏大或倒角偏小;倒角后存有锐边或翻边披锋;b、倒角不均(倒角大小边),由于产品变形,或治具装夹存有松动,导致倒角宽度存有不规则形状,治具装夹松动常伴随振刀纹路出现。
3.14牙平(牙浅):由于螺纹底孔偏大导致螺纹滑牙或扭力不够,目视时螺纹呈锥形平台;3.15结构不符:产品与3D存有不相符,常有多料、少料、孔(轴、柱)圆度不符;3.16变形:由于工件材质影响,工件加工后厚薄度及韧性产生变化,改变了工件原本的形态,从而导致产品外形不平整或扭曲;4判断方法4.1A级面:产品经过组装后直接外露的表面,通常讲外观面4.2B级面:产品经过组装后不直接外露的表面,但旋转一定角度后能直接观察的表面;4.3C级面:产品经过组装后不直接外露的表面,且需要拆除某些部件后才能观察到的表面;4.4线性类缺陷判断法长度*宽度*深度*个数L *W *H *N4.5孔状类缺陷判断法面积*深度*个数A *H *N5CNC加工工件检验标准。
CNC刀具设计规范
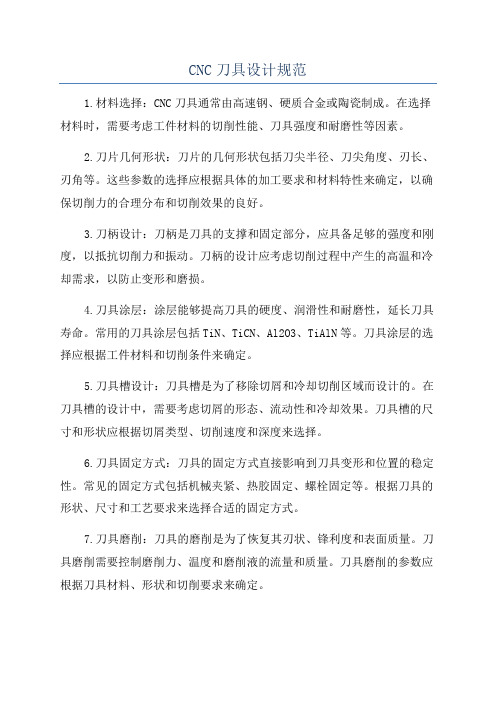
CNC刀具设计规范1.材料选择:CNC刀具通常由高速钢、硬质合金或陶瓷制成。
在选择材料时,需要考虑工件材料的切削性能、刀具强度和耐磨性等因素。
2.刀片几何形状:刀片的几何形状包括刀尖半径、刀尖角度、刃长、刃角等。
这些参数的选择应根据具体的加工要求和材料特性来确定,以确保切削力的合理分布和切削效果的良好。
3.刀柄设计:刀柄是刀具的支撑和固定部分,应具备足够的强度和刚度,以抵抗切削力和振动。
刀柄的设计应考虑切削过程中产生的高温和冷却需求,以防止变形和磨损。
4.刀具涂层:涂层能够提高刀具的硬度、润滑性和耐磨性,延长刀具寿命。
常用的刀具涂层包括TiN、TiCN、Al2O3、TiAlN等。
刀具涂层的选择应根据工件材料和切削条件来确定。
5.刀具槽设计:刀具槽是为了移除切屑和冷却切削区域而设计的。
在刀具槽的设计中,需要考虑切屑的形态、流动性和冷却效果。
刀具槽的尺寸和形状应根据切屑类型、切削速度和深度来选择。
6.刀具固定方式:刀具的固定方式直接影响到刀具变形和位置的稳定性。
常见的固定方式包括机械夹紧、热胶固定、螺栓固定等。
根据刀具的形状、尺寸和工艺要求来选择合适的固定方式。
7.刀具磨削:刀具的磨削是为了恢复其刃状、锋利度和表面质量。
刀具磨削需要控制磨削力、温度和磨削液的流量和质量。
刀具磨削的参数应根据刀具材料、形状和切削要求来确定。
8.刀具检测:刀具在使用前和使用过程中需要进行检测,以确保其性能和质量。
常用的检测方法包括外径测量、刃磨深度测量、焊接性能检测等。
刀具检测结果应符合相关标准和要求。
9.刀具保养:刀具在使用过程中需要进行保养和维护,以延长其寿命和保持良好的切削性能。
保养包括刀具清洁、润滑、涂层修复等。
保养周期和方法应根据刀具类型和使用情况来确定。
10.刀具标识:刀具的标识应清晰、准确、耐久,并包含相关的信息,如刀具型号、材料、涂层等。
刀具标识有助于追溯和管理刀具,并提供了刀具使用和维护的参考。
以上是CNC刀具设计规范的一些重要内容,设计和制造CNC刀具时应遵循这些规范,以确保刀具的性能和质量,提高加工效率和产品质量。
- 1、下载文档前请自行甄别文档内容的完整性,平台不提供额外的编辑、内容补充、找答案等附加服务。
- 2、"仅部分预览"的文档,不可在线预览部分如存在完整性等问题,可反馈申请退款(可完整预览的文档不适用该条件!)。
- 3、如文档侵犯您的权益,请联系客服反馈,我们会尽快为您处理(人工客服工作时间:9:00-18:30)。
处理。其计算步骤如下:
1)将螺距实测值依次填入表 1 中第Ⅱ列;
2)将第Ⅱ列数分别减去理论螺距,误差列入第Ⅲ列;
3)将第Ⅲ列的第一个数、第一至第二个数、第一至第三个数……,分别取其代数和列入第Ⅳ列;
分度值为 0.01mm的千分尺、1 级三针或五针;螺纹千分尺、奇数槽比较仪、标准螺纹样柱;万能 工具显微镜。 12. 2 检测方法
丝锥中径的测量部位在校准部分起点处。若手用丝锥的校准部分起点距前端不足 4 牙时,在距前端 4 牙处检测。螺母丝锥在切削部分中点向校准部分移动 1~2 牙处检测。锥度螺纹丝锥在规定的基面位置 上测量。此项检测方法有三种:
值。见图 5,通过测量,找出牙厚的实测值等于半个理论螺距(即中径线)所在位置的横向读数 y。再
将镜头米字线的水平虚线转ϕ/2
分别压线测出牙顶和牙底的横向读数
y
1
和
y ,则牙顶高 2
h 1
和牙底高
h 2
的计算式按式(11)~式(13)。
h1 = y1 − y ································(11)
当容屑槽为右旋时:
θ = 360°[P /(H − P)]·····························(7)
Pnp = PH /(H − P) ······························(8)
当容屑槽为左旋时:
θ = 360°[P /(H + P)]·····························(9)
式中:D——仪器光圈直径; K——系数;
3
JB/T 10231.4- 2001
d2 —— 螺纹中 径。 式中:P——螺距。
tanψ = P /(πd 2 ) ································(4)
用上述方法所测的半角为法向牙型半角值,当ψ>2°30′时,应按式(5)进行修正:
方法一:对偶数槽丝锥用三针、外径千分尺测量。对奇数槽丝锥用五针、三沟千分尺或五沟千分尺。 见图 8 a),将三针放在规定部位的牙槽处,千分尺测量面应使三针同时接触,转动丝锥测出 M 最大值, 它与 M 理论值之差为丝锥中径实际偏差。M 值计算按式(14)、式(15)。
60°牙型角螺纹: M = d 2 + (3d m − 0.866P) ···························(14)
h2 = y 2 − y ································(12)
B = [Ptan(ϕ / 2)]/ 2 ···························(13)
式中:ϕ/2——锥度斜角。
图5
图6
10 大径的检测
10. 1 检测器具 分度值为 0.01 mm 的千分尺、万能工具显微镜。
55°圆锥管螺纹丝锥 刀具产品检测方法 第 1 部分:通则
相关标准和产品图样。
4 通用项目的检测
下列项目的检测方法和检测器具均按 JB/T 10231.1 中对应项目的有关规定: a) 标志、包装; b) 外观、表面粗糙度; c) 材料、硬度、表面处理。
5 主偏角Κr 的检测
5. 1 检测器具 万能工具显微镜。
I
中华人民共和国机械行业标准
刀具产品检测方法 第 4 部分:丝锥
Tool inspaction methods part4:taps
JB/T 10231.4-2001
1 范围
本标准规定了成品丝锥检测时的检测项目、检测器具和检测方法。这些方法并非唯一的。 本标准适用于按 GB/T 967~969、GB/T 3464.1~3464.3、GB/T 3506、JB/T 8364.2、JB/T 8364.3、 JB/T 8786、JB/T 8824.1~8824.4、JB/T 8825.1~8825.4、JB/T 9994~9996 生产的丝锥作质量判定检测。 其他成品丝锥可参照采用。
0.000 +0.002 +0.003
最大 螺距偏 差 (Ⅴ )
3 4 5 6 7 4
1.499 1.496 1.500 1.498 1.499
–0.001 –0.004 0.000 –0.002 –0.001
+0.002 –0.002 –0.002 –0.004 –0.005
–0.008
JB/T 10231.4- 2001
同 9.1。 11. 2 检测方法 11. 2. 1 圆柱螺纹丝锥
按图 7 所示,测出两处的牙侧直线与牙底圆弧交界点的横向读数值,两值之差为小径实测值。
图7 11. 2. 2 锥度螺纹丝锥
锥度螺纹丝锥的小径在给定基面位置上,测量出沿垂直于轴线方向截得螺纹牙底所形成的圆锥上的 直径。 12 中径的检测 12. 1 检测器具
JB/T 8825.4—1998 惠氏螺纹螺母丝锥
JB/T 9994—1999
55°圆柱管螺纹丝锥
JB/T 9995—1999
55°圆柱管螺纹丝锥 螺纹公差
中国机械工业联合会 2001-03-29 批准
2001-07-01 实施
1
JB/T 10231.4- 2001
JB/T 9996—1999 JB/T 10231.1—2001 3 检测依据
图3
∆α / 2(左) = [α / 2(Ⅰ) + α / 2(Ⅲ)]/ 2 − α / 2 ···············(1) ∆α / 2(右) = [α / 2(Ⅱ) + α / 2(Ⅳ)]/ 2 − α / 2 ···············(2)值偏差; α/2——公称牙型半角。 D = K sin(α / 2) / d 2 ···························(3)
偿角θ /2,θ 的计算按式(7)或式(9)。
8 螺距的检测
8. 1 检测器具
同 7.1。
8. 2 检测方法
8. 2. 1 直槽丝锥
仪器的调整同 7.2。测量时使镜头米字线中心在螺纹中径线附近重合,记下纵向读数。然后按标准
规定牙数,在校准部分任意处依次测完螺距 Pk′(k=1,2,…,n)和 Pk″(k=1,2,…,n)。见图 4a)。取各同名相对的两相邻牙侧的单侧螺距平均值 Pk 为螺距的实际测量值。即P1 = (P1′ + P1″) / 2, Λ , 经
JB/T 8824.2—1998 统一螺纹丝锥 螺纹公差
JB/T 8824.3—1998 统一螺纹丝锥 技术条件
JB/T 8824.4—1998 统一螺纹螺母丝锥
JB/T 8825.1—1998 惠氏螺纹丝锥
JB/T 8825.2—1998 惠氏螺纹丝锥 螺纹公差
JB/T 8825.3—1998 惠氏螺纹丝锥 技术条件
ICS 25.100.01 J41
JB/T 10231.4-2001
www刀具产品检测方法 .b第 4 部分:丝锥 Tool inspactionmethods part4:taps
2001-03-29 发布
中国机械工业联合会 发 布
2001-07-01 实施
JB/T 10231.4-2001
7. 2 检测方法 首先按螺纹中径选择光圈,其值的计算见式(3)。再使主显微镜立柱顺牙面螺旋线方向旋转一个螺
纹升角ψ,ψ的计算见式(4)。此项的检测部位为丝锥校准部分任一个完整牙。调整镜头米字线的垂直 虚线与被测牙廓相切,见图 3,测出牙型半角,然后将丝锥旋转 180°,对同一牙型再次测量,则左右半 角实际偏差的数据处理按式(1)、式(2)。
GB/T 3464.2—1994 长柄机用丝锥
GB/T 3464.3—1994 短柄机用和手用丝锥
GB/T 3506—1993 螺旋槽丝锥
JB/T 8364.2—1996 60°圆锥管螺纹丝锥
JB/T 8364.3—1996 60°圆锥管螺纹丝锥 技术规范
JB/T 8786—1998
长柄螺母丝锥
JB/T 8824.1—1998 统一螺纹丝锥
tanα′ / 2(n) = [tanα / 2(n)]/ cosψ ·······················(5)
式中:α′/2(n)——轴向牙型半角实测值; α /2(n)——法向牙型半角实测值,n=Ⅰ、Ⅱ、Ⅲ、Ⅳ。
检测螺旋槽丝锥的牙型半角时,其他同上所述。但测量牙的另一侧面时,分度头应转动一个对焦补
8. 2. 2 螺旋槽丝锥
检测螺旋槽丝锥时,测量要求和数据处理同 8.2.1,仅在每测一螺距时,分度头需转一个对焦补偿
角θ,如此测得数值为法向螺距 Pn在轴向的投影 Pnp,见图 4b)。则 Pnp 的实测值与 Pnp 的理论值之差为
螺距偏差。各关系式按式(6)~式(10)。 H = 360° l ·································(6) β
Pnp = PH /(H + P) ······························(10)
式中:l——容屑槽轴向实际测量长度;
β——测量 l 长度时分度头转过的角度;
H——容屑槽实际导程。
a)
容屑槽 左旋
容 屑槽 右旋
b)
c)
图4
5
JB/T 10231.4- 2001
8. 2. 3 锥度螺纹丝锥 检测锥度螺纹丝锥的螺距时,用标准轮廓叠合法测量。见图 4c),选用合适的标准牙型轮廓或圆形
10. 2 检测方法 10. 2. 1 圆柱螺纹丝锥
在校准部分起点处测量。螺母丝锥的大径在校准部分第一个完整牙处测量。偶数槽丝锥用外径千分 尺,三槽、五槽丝锥分别用三沟千分尺、五沟千分尺测量。见图 6。 10. 2. 2 锥度螺纹丝锥