模具内模设计实用标准
汽车模具设计标准与要求
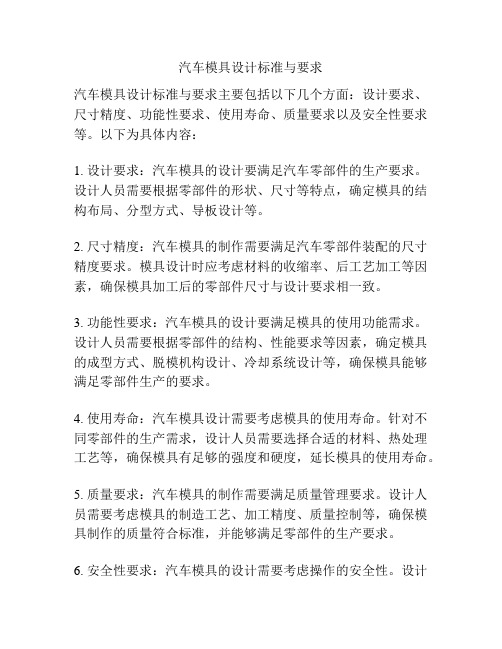
汽车模具设计标准与要求
汽车模具设计标准与要求主要包括以下几个方面:设计要求、尺寸精度、功能性要求、使用寿命、质量要求以及安全性要求等。
以下为具体内容:
1. 设计要求:汽车模具的设计要满足汽车零部件的生产要求。
设计人员需要根据零部件的形状、尺寸等特点,确定模具的结构布局、分型方式、导板设计等。
2. 尺寸精度:汽车模具的制作需要满足汽车零部件装配的尺寸精度要求。
模具设计时应考虑材料的收缩率、后工艺加工等因素,确保模具加工后的零部件尺寸与设计要求相一致。
3. 功能性要求:汽车模具的设计要满足模具的使用功能需求。
设计人员需要根据零部件的结构、性能要求等因素,确定模具的成型方式、脱模机构设计、冷却系统设计等,确保模具能够满足零部件生产的要求。
4. 使用寿命:汽车模具设计需要考虑模具的使用寿命。
针对不同零部件的生产需求,设计人员需要选择合适的材料、热处理工艺等,确保模具有足够的强度和硬度,延长模具的使用寿命。
5. 质量要求:汽车模具的制作需要满足质量管理要求。
设计人员需要考虑模具的制造工艺、加工精度、质量控制等,确保模具制作的质量符合标准,并能够满足零部件的生产要求。
6. 安全性要求:汽车模具的设计需要考虑操作的安全性。
设计
人员需要合理设置模具的安全装置、警示标识等,确保操作人员的人身安全。
总之,汽车模具设计标准与要求是为了保证模具能够满足汽车生产的需求,并达到高质量、高效率的生产目标。
模具设计人员应严格按照标准要求进行设计,确保模具的质量和安全性。
模具设计标准
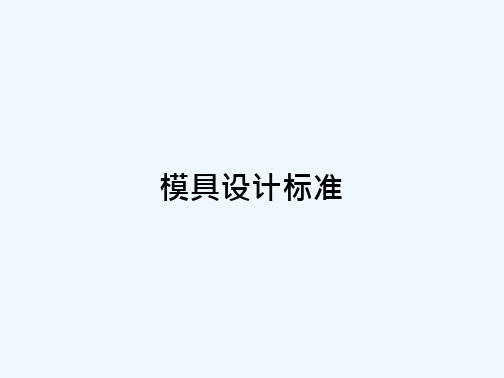
八、常用成型机得容模大 小
8、1 公司卧式注塑机规格表
55
九、常用模具结构
9、1、 插头模 9、1、1 两直扁PIN有孔,无滑块模具结构:
产品图
56
9、1、2 三斜扁PIN无孔,两滑块模具结构:
产品图
57
9、1、3三圆PIN,三面滑块模具结构:
产品图
58
十、钢材选用和热处理
10、1钢材各种材料得性能 10、2胶料得物性 10、3操作得影响 10、4钢材得热处理
四角R10
四角最小为R8、 0
模仁
模框
9
3、12、 A,B板开完粗后,叠在一起精镗四个导柱和导套孔,装上导柱和导套合在 一起用端铣机铣外形和做边锁,最后开精框
3、13、根据模胚得大小适当得选择吊模孔 3、14、没有要求得按龙记标准加工
吊模孔
10
4、模胚设计注意事项:
4、1、顶针板必须加中托司且每块板都要有导套(所有板须叠在一起加工导套孔以保证精度)除插头 模只做2组EGP外,其她模均做4组EGP;顶针板尽量做小以减少B板得变形;且要加垃圾钉(产品上有 顶针得必须加)
X.XX
-0.02 -0.025
与前模配合面 比后模要松0、02MM
与后模配合面
0、
00
X.XX
-0.002 -0.003
26
3、5、耐磨块和斜压块斜度单边留0、05mm配模 3、6、后模放模条位置要做保护方梢(面板不封胶得不做)
模条面板 后靠型腔部分要避空和倒圆角,防撞伤型腔 模条面板
8MM
抛光
要倒圆角,以免刮伤线材 5MM
20MM
29
3、13、 进胶点要做活动镶件,并且统一尺寸 3、14、 线槽增加挤紧螺丝,须保证可挤紧SR镶件,SR镶件高度统一20mm
模具内模设计规范标准

4.2.4内模螺丝的布置
原则上前、后内模螺丝至少使用M10的螺丝,只有当内模尺寸很小时才可用M8;小镶件的螺丝最小可以使用M5。
4.3内模分型面、枕位、插穿位、碰穿位的设计
4.3.1.分型面设计注意事项
1).分型面应沿产品的外形拉伸,尽量避免线或点封胶.
b.内模框深≥150mm时.
c.内模高度太高,容易偏公时.
d.两块内模非平面拼合或多块内模拼合时.
e.产品插穿位多或产品夹线要求严格时。.
f.模胚加直身锁;
2).挤压块一般放在模胚非基准角的两边,放挤压块两侧的内模边与模框避空0.5。
3).平面方向挤压块的长度一般做到内模宽度的2/3。
4).高度方向,内模框深<70时,挤压块深度和框深一样或接近,5°斜度;
6).在满足制品外观和装配的情况下,分型面尽量避免过多起伏,转折处尽量采用圆角过渡.
7).尽量避免模具出现尖角.
4.3.2.内模枕位设计注意事项
1).在设计枕位时应充分考虑内模强度是否足够.
2).应尽量避免小端尺寸小于3mm的枕位设计,以免配模时断裂.
3).枕位的封胶位有10~15mm左右即可,其它部分避空.
1).产品排位时应以节约成本为原则。
2).产品排位时应尽量避免行位和斜顶产生复合抽芯角度,减小模具加工的难度。
3).一模多穴时,产品排位时应充分考虑保证塑胶流动顺畅和平衡性,并且进胶口都尽量位于产品的同一位置。
4).一模多穴时,产品间距的校核。
4.2内模的设计
4.2.1.内模的设计原则
在保证强度的前提下,尽可能的节约成本.
若前模采用原身止口与后模互锁的结构形式,厚度可适当减薄.
模板的厚度、材质、硬度与大小的设计规范

一、目的推行作业标准化,实现模具设计快速统一.二、适用范围龙光模具厂设计部三、内容一、模板厚度、材质设计规范(厚度T,单位mm)(1)连续模模板设计规范2)复合模设计规范3)冲孔模设计规范4)折弯模设计规范二、模板的规范1)在设计中,定模板尺寸大小时,模板的一边尽可能用尾数为50与00的整数,如(150*AA,200*AA,250*AA,300*AA),以方便机加工快速开料。
2)当模板需750*450线割机线割时,需线割的边到模板边不小于25mm,当模板需520*370,或500*350线割机线割时,需线割的边到模板边不小于20mm,当模板需320*220线割机线割时,需线割的边到模板边不小于14mm。
以上均为要保证一个直角边在此范围内,设计时,销钉孔、导柱孔位置应尽量考虑以上要求。
3)模板中,弹钉孔、定位避位孔,材料避位孔,且在钻铣加工时不会影响到有用工作部分,不用线割4)脱垫板(止挡板)一般不用线割,若需定位或安装入块时可线割或CNC加工。
5)优力胶孔、弹簧孔一般采用钻孔加工,而不用线割。
6)滑块和滑块主体一般情况下不需分开备料,滑块部份需磨好工作边。
(注:视情况也可用滑块分开备料)。
7)在备模板时,单块钢板的外型尺寸最大只能备长度不超650mm,宽600mm。
三、落料、冲孔模模具板料备料设计规范(上下垫板、上下夹板、脱料板、母模板)。
四、模座设计规范1、当模座长小于700时,上下模座厚度为35mm ;当模座长大700小于800时,上模座厚度35mm ,下模座厚度40mm ;当模座长度大于800小于1000时,上模座厚度40mm 下模座厚度40; 当模座长度大于10000时,上模座厚度50,下模座厚度50mm; 2、模座材质全部用A3。
3、模架标准形式有四种(如图4.1, 4.2, 4.3, 4.4,)模座模板图41图4模板模座模座模板模座模板图4图44、模座板板料备料规范有两种形式:1.第一种形式:没有外导柱情况下按下表2、第二种形式:有外导柱的情况下按下表。
齿轮模具设计及制作标准

齿轮模具设计及制作标准(一)
一:内模部分由齿片、齿座、镶针(或司筒)等组成,结构如下图:
(1)
1.齿片的厚度一般要做到4-6MM,齿轮的厚度在4MM以上,齿片厚度与齿轮的厚
度相同即可,如图(2)所示;若齿胶位厚度低于4MM,则齿片要加厚到6MM,以便与模胚的内孔配合良好,封胶位要做到3-5MM(图3中为4.29MM),结构形式、配合公差参考图(3);若齿形需要定位或齿片有顶针穿过时,齿片需止转;
2.齿座结构形式、配合公差参考图(4);
(4)
3.镶针的结构形式、配合公差参考图(5)
4.齿片的排气设计,排气一般开在齿片的底面,对于流动性较好PA、PPS等料建议先不要开排气,具体结构如图(6);
齿片底部排气
(6)
5.进胶点的设计,一般齿根圆直径在8MM以上时,采用三点进胶;小于8MM时可采用一点进胶;为保证进浇点压力对齿形的影响,浇口的位置可稍远离齿形,具体设计请参考图(7);
(71
A、B板的模仁孔
加工时A、B板装夹后,一同加工,下图为A板的模仁孔及定位器孔重点寸法的尺寸公差、形位公差,B板的标注与A板相同;
二、齿轮产品模具的基本结构:。
冲孔模具 设计标准

冲孔模具设计标准冲孔模具的设计标准包括以下方面:1. 冲头:必须使用带顶针的类型。
2. 脱料板:材质一般用A3,固定方式如结构简图所示,导柱导套品牌按客户要求选择。
为防止活动工件(比如弹簧)从模具中飞出造成伤害,脱料板周边需要加防护角铁。
3. 压料板:起压料作用,作用于料片上防止产品变形。
4. 弹簧:是模具中广泛应用的弹性零件,主要用于卸料、压料、推件及顶出等功能。
长度选择应保证开模状态下预压缩2mm左右,闭模状态弹簧压缩量小于或等于最大压缩量。
冲孔模和成形模用绿色弹簧,如有特殊需要,可考虑其它规格。
弹簧规格优先选用Φ25,特殊情况可选用其它规格。
弹簧孔中心到距离约等于弹簧外径,与其它弹簧孔保持实际壁厚大于5MM。
弹簧排列优先考虑受力重点部位,然后再考虑整体受力均衡性。
5. 下模入子:固定在下模板内,正面不能倒角,其品牌按客户要求使用。
6. 球锁冲头:需要快拆,在不影响脱料板强度的情况下,优先选择快拆球锁座子。
7. 冲裁间隙:按结构通用标准()冲裁间隙做。
在客户没有特殊要求的前提下,冲头在脱料板的间隙放。
冲头进入凹模5-8MM(特殊情况下请部门负责人确认)。
8. 等高套筒:规格一般有M6、M8、M10三种。
综合考量活动板大小以及受力状况,一般优先选用M8,考量模板大小可选用M6、M10。
根据活动板行程,及相关板厚决定套筒长度。
一般排完等高筒后再排其它五金件。
优先考虑受力重点部位,其次考虑受力均衡性。
这些标准是根据一般的实践经验和行业规范总结出来的,具体的设计要求可能会根据实际的应用场景和客户需求有所不同,建议根据具体情况进行设计调整。
模具设计标准规范标准

模具设计标准规范1﹑目的:确保模具设计规范化,统一化.能将设计意图正确的传达给制造部门.避免或减少失误。
2﹑范围:工程部设计组接收工程部产品组转交的图文件、样品等资料到图纸发行为止之阶段均属之。
3﹑权责:3.1 工程部设计组:负责模具开发设计及设计变更、2D/3D产品图面设计、3D建模、设计模具的组立图、3D拆模与拆电极、绘制零件图.3.2 现场加工各组:加工各组的组长,在加工前需先审视加工图,若发现与原先检讨的不符合或有误,甚至不合理,需立即反应工程部检讨查核后,方可继续加工。
4. 名词释义:无5﹑作图环境标准:5.1文字标准5.1.1字体。
数字及英文使用“Arial”字体,中文使用“标楷体”。
5.1.2文字大小。
为了使整套图面文字视觉效果一致,在标准图框(即1:1图框,A4为297*210)中,设定字高为3.0,宽0.85。
5.2 图面标准5.2.1 图框:为了便于查阅,装订,保存,图框统一标准如下:A0图框:841*1189横印(附件一)A1图框:594*841横印(附件二)A2图框:420*594横印(附件三)A3图框:420*297横印(附件四)A4图框:297*210直印(附件五)5.2.2 图面要求5.2.2.1零件图面按照其在模具当中的位置分类摆放,以便于查找。
5.2.2.2尺寸标注方式。
除了圆以外,所有模板、模仁之尺寸均采用坐标标注方式。
5.2.2.3 视图投影关系:第三视角法。
5.2.3图档版本版本编号采用大写字母“A”加上一位数字序号,数字序号按照图文件完成的时间先后顺序进行排列。
例如A1、A2、A3等。
5.2.4 图层与线型:为了便于图形与尺寸的识别,图层与线型统一标准如下:5.3编码原则5.3.1模具结构和主要零件名称如下:5.3.2零件名称与对应的编号如下:5.3.2.1模胚部分编号零件名称编号零件名称A01 上固定板A09 脱料板A02 下固定板A10 推板A03 母模板A11 上流道板A04 公模板A12 电热板A05 母模承板A13 脚垫A06 公模承板A14 浇道脚垫A07 上顶针板A08 下顶针板5.3.2.2镶件部分5.3.2.3一般零件部分5.3.2.3一般零件部分(续)5.3.2.4特殊零件部分5.3.3编码方式5.3.3.1模具编码方式。
模具设计标准
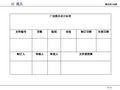
+0.00-+ 0.2 ⊥≦0.1
+1 --+3 ⊥≦1
+0.00-+0.1 ⊥≦0.08
1000以上
以上尺寸仅供参考;
参考值变 形量
调质的材料变形值为1000MM变形6-8MM 煅件的材料变形值为1000MM变形为0.3-0.5MM 热处理的材料变形值为1000为2-3MM 第6页
GC 模具
模胚
所有模芯的XY都以XY基准角单边碰数;Z对底面为O;模芯上面的小镶件,Z同 样对底为0;
五.其他小工件,如斜顶,行位,小镶件等 按照2D图纸标数为基准;特别的工件特别对待; 六.注意;为了检测模芯及模胚的垂直度,所有操作人员应引起高度重视, 基准边垂直度高度200以内公差0.02MM以内,高度200-400以内公差0.0 3MM以内。如超出公差范围必须请示部门经理。操作人员在检测好侧面 的垂直度后,应再检测验证一下平面的误差;特别是慢走丝;第8页GC 模具吊环模具设计标准
第9页
GC 模具
运水
模具设计标准
字休大小:小于500的模具8MM,大于500的模具10MM,深0.3 注意事项:
1:每条运水都需要有进出标识,模具小于500的由钳工用字码打字。 模具大于500的用晒纹晒字。 2:文字标识统一加工在运水下方,下方没位置的时候可放在上方或左右两边
第13页
GC 模具
倒角
模具设计标准
当分型面有尖角时,做渐 变R角过渡
第14页
GC 模具
运水与堵头
模具设计标准
所有模具注意此处的距 离,确保堵头能安装。 (PT1/4”保证有15mm,PT1 /8”保证有10mm,少于上 面尺寸需在评审时提出 确认
- 1、下载文档前请自行甄别文档内容的完整性,平台不提供额外的编辑、内容补充、找答案等附加服务。
- 2、"仅部分预览"的文档,不可在线预览部分如存在完整性等问题,可反馈申请退款(可完整预览的文档不适用该条件!)。
- 3、如文档侵犯您的权益,请联系客服反馈,我们会尽快为您处理(人工客服工作时间:9:00-18:30)。
1). 一般情况下的强度数据,数据只考虑了强度,没有考虑螺丝、运水、顶针、模大小等。
2). 当产品有下列情况出现时,产品到模边的距离可适当减小.
①产品中间部位存在有大面积的碰穿位,胶位对前模的冲击力小.所以胶位面到模顶的距离可适当减小.
②当产品整体比较平坦,只有局部有小面积凸台.
③当产品的截面形状大部分为圆弧,直身面较小
产品截面形状大部分为圆弧形,注射压力呈圆弧形分散
产品由中间到两端逐渐变细,钢料所受的注射压力相应变小.
3). 当产品有下列情况出现时,产品到模边的距离应适当增加.
①深腔型制品:制品的长、宽尺寸明显大于高度方向的尺寸,高度的尺寸达到150umm以上.
对于深腔型制品,一般前模采用原身留的形式,
若前模采用原身止口与后模互锁的结构形式,厚度可适当减薄.
4.2.4 模螺丝的布置
原则上前、后模螺丝至少使用M10的螺丝,只有当模尺寸很小时才可用M8;小镶件的螺丝最小可以使用M5。
4.3 模分型面、枕位、插穿位、碰穿位的设计
4.3.1. 分型面设计注意事项
1).分型面应沿产品的外形拉伸,尽量避免线或点封胶.
如果沿产品外形拉伸会产生尖角,可采用以下的方法避免.
2).排气不良,塑胶充填困难.
3).互换件:当一套模具需要生产产品的多种型号时,可使用互换镶件达到目的.如产品上的铭牌位等。
4).强度弱,易损坏的部位.
5).前后模局部细小的突起,基于节约成本的考虑.
4.6.2.模镶件的注意事项
1).模镶拼时,防止尖角的产生.
2).模镶件必须设计碰数平面,方便后续加工.
4.1 产品的排位
4.1.1.产品基准的选取
1).基准一般选取产品的对称中心、圆形的柱位和孔位、规则的凸台和凹坑等明显特征的中心。
2).若产品无明显规则的特征作基准,也可将产品四面分中取其中心作为基准。
3).高度方向应选取垂直于出模方向的产品平面作为基准。
4).产品基准到模中心必须是整数。
4.1.2 产品排位
4.5 模的基准角标识
为辨别加工的方向,必须在2D和3D上标示出模的基准角。基准角的方位同模胚基准角方位一致。
4.6 镶件的设计
4.6.1.模镶件的选用
1).整体加工困难(EDM、省模困难)
当骨位的深度H≥5mm时,常需做镶件,骨位尽量全部出在镶件上(外观面需客户确认),如左上图.
产品全周止口,需做镶CORE.止口胶位应留在模上.
2).产品有较严格的外观要求,后模部分的胶位应比前模稍做小0.2~0.3mm.
3).若产品没有平面,必须设计平面方便后续加工.
4).圆轴中间分型时为防止错位影响装配,后模部分的胶位应比前模做小0.1mm.
5).分型面的选择必须考虑防止制品粘前模.
5).原则上模的封胶位最小在5mm以上.对于大面积的分型面,留15~20mm封胶即可,其它部分避空.
6).在满足制品外观和装配的情况下,分型面尽量避免过多起伏,转折处尽量采用圆角过渡.
7).尽量避免模具出现尖角.
4.3.2. 模枕位设计注意事项
1).在设计枕位时应充分考虑模强度是否足够.
2).应尽量避免小端尺寸小于3mm的枕位设计,以免配模时断裂.
3).枕位的封胶位有10~15mm左右即可,其它部分避空.
d.两块模非平面拼合或多块模拼合时.
e.产品插穿位多或产品夹线要求严格时。.
f.模胚加直身锁;
2).挤压块一般放在模胚非基准角的两边,放挤压块两侧的模边与模框避空0.5。
3).平面方向挤压块的长度一般做到模宽度的2/3。
4).高度方向,模框深<70时,挤压块深度和框深一样或接近,5°斜度;
模框深>100时,挤压块深度为框深的2/3,取3~5°斜度。
1). 产品排位时应以节约成本为原则。
2). 产品排位时应尽量避免行位和斜顶Leabharlann 生复合抽芯角度,减小模具加工的难度。
3). 一模多穴时,产品排位时应充分考虑保证塑胶流动顺畅和平衡性,并且进胶口都尽量位于产品的同一位置。
4). 一模多穴时,产品间距的校核。
4.2 模的设计
4.2.1.模的设计原则
在保证强度的前提下,尽可能的节约成本.
a.对于不需要定位的镶针,由顶针改制,其台阶尺寸直接参考顶针标准。
b.对于需要定位的镶针(顶部有碰穿,插穿或圆周上有异形),由顶针改制,
其台阶尺寸见左下图。
c.对于需要定位的圆形镶件(非顶针改制型),其台阶尺寸见右上图。
2).方形(平面为规则外形)
3).异形(平面为非规则外形)
异形镶件的外形一般用线切割加工,若有台阶,应注意台阶方向,并且台阶方向尽量留对刀距离(1~2MM),以便台阶的后续加工。
②深桶型制品:高度方向的尺寸达到150mm以上的圆柱形制品或者是长、宽方向尺寸明显
4)、模淬火,产品到模边、底的距离均应适当增加。
4.2.3 模挤压块
1).为了配框的方便,有以下任一情况的,必须做挤压块。如果无法设计挤压块,需提出。
a.模的长、宽尺寸≥350mm时.
b.模框深≥150mm时.
c.模高度太高,容易偏公时.
若镶件确实无法做到碰数平面.必须在材料还是完整的方料时,将镶件上的螺丝孔、顶针孔加工完毕.
3).模镶拼时必须考虑模的强度是否足够.
4).模镶拼时必须考虑是否影响产品的外观和装配,
一般前模尽量不镶,必须镶时需事先得到客户的同意。
5).模镶拼时应避免破顶针、镶针、司筒孔.
4.6.3.模镶件的形式及尺寸
1).圆形
模插穿方法的选用
4.3.4. 模碰穿位设计注意事项
1).对于面积超过2500mm的碰穿位,留有10~15mm的封胶位即可.其它部分避空.
2).大面积的碰穿位还需加工排气孔.
3).避空位的深度在0.1~0.15左右.
4.4 模虎口定位的设计
当产品有较严格的外观要求(如前后模包胶位)或分型面倾斜较大时,模应设计虎口定位。
4.6.4.模镶件的固定形式
枕位的斜度应保证斜面的上下落差至少0.25mm以上.
4).枕位的设计应避免45°以下的尖角的产生.
4.3.3. 模插穿位设计注意事项
一般情况下,模的插穿斜度应在2°以上.最好3~5°,空间有限时,斜度应保证斜面的上下落差至少0.25mm以上.对于细小的,单独凸起的插穿位应设计镶件,便于更换.镶件的材料应与模材料不一样,或材料一样硬度不一样,不锈钢材料尽量不用来做插穿位的镶件。