固化工艺对铁基纳米晶软磁材料磁性能的影响研究
铁基软磁非晶/纳米晶合金研究进展及应用前景

铁基软磁非晶/纳米晶合金研究进展及应用前景∗姚可夫† 施凌翔陈双琴邵洋陈娜贾蓟丽【摘要】非晶合金通常是将熔融的金属快速冷却、通过抑制结晶而获得的原子呈长程无序排列的金属材料.由于具有这种特殊结构,铁基软磁非晶合金具有各向同性特征、很小的结构关联尺寸和磁各向异性常数,因而具有很小的矫顽力Hc,但可和晶态材料一样具有高的饱和磁感强度Bs.优异的软磁性能促进了铁基软磁非晶合金的应用研究.目前,铁基软磁非晶/纳米晶合金带材已实现大规模工业化生产和应用,成为重要的高性能软磁材料.本文回顾了软磁非晶合金的发现和发展历程,结合成分、结构、工艺对铁基非晶/纳米晶合金软磁性能的影响,介绍了相关基础研究成果和工艺技术进步对铁基软磁非晶/纳米晶合金研发和工业化应用的重要贡献.并根据结构、性能特征将铁基软磁非晶合金研发与应用分为三个阶段,指出了目前铁基软磁非晶合金研发与应用中面临的挑战和发展方向.【期刊名称】物理学报【年(卷),期】2018(067)001【总页数】9【关键词】关键词:非晶合金,软磁性能,纳米晶合金综述非晶合金通常是将熔融的金属快速冷却、通过抑制结晶而获得的原子呈长程无序排列的金属材料.由于具有这种特殊结构,铁基软磁非晶合金具有各向同性特征、很小的结构关联尺寸和磁各向异性常数,因而具有很小的矫顽力Hc,但可和晶态材料一样具有高的饱和磁感强度Bs.优异的软磁性能促进了铁基软磁非晶合金的应用研究.目前,铁基软磁非晶/纳米晶合金带材已实现大规模工业化生产和应用,成为重要的高性能软磁材料.本文回顾了软磁非晶合金的发现和发展历程,结合成分、结构、工艺对铁基非晶/纳米晶合金软磁性能的影响,介绍了相关基础研究成果和工艺技术进步对铁基软磁非晶/纳米晶合金研发和工业化应用的重要贡献.并根据结构、性能特征将铁基软磁非晶合金研发与应用分为三个阶段,指出了目前铁基软磁非晶合金研发与应用中面临的挑战和发展方向.1 Fe基软磁非晶合金的问世磁性材料是最重要的功能材料之一,在现代科学技术和工业发展中、特别是电子技术发展中发挥着重要作用.铁磁材料在未磁化时,因其磁偶极子取向呈无序状态而使磁偶极子的矢量和为零,宏观上不呈现磁性.当施加外场后,磁偶极子受外场作用而转向外场,使材料内部磁偶极子呈现定向排列,从而呈现宏观强磁性.非晶合金因原子呈长程无序排列,曾被认为不具有宏观磁性.1960年,Gubanov[1]通过理论研究认为电子的能带结构主要由原子短程序决定,即铁磁性是由相邻原子的交换耦合作用产生,由此预测Fe基非晶合金具有铁磁性.这为铁基非晶合金可能具有铁磁性提供了理论基础.自1960年Duwez等[2]首次用合金熔体急冷方法制备出Au-Si非晶合金材料后,1967年,Duwez等[3]又用急冷方法制备出了Fe80P12.5C7.5非晶合金.通过磁学性能测试,发现Fe80P12.5C7.5非晶合金的饱和磁感应强度和矫顽力分别为6.8 kG(0.68 T)和3 Oe(240 A/m),证实了铁基非晶合金具有宏观磁性,尽管矫顽力稍大,但该铁基非晶合金仍为典型的软磁非晶合金材料.这个结果不仅从实验上证实了Gubanov的理论分析结果,也吸引了很多研究人员投入到Fe基软磁非晶合金材料的基础研究与应用研究中.2 铁基软磁非晶合金发展历程非晶合金是在快速冷却条件下,通过拟制结晶并快速将合金熔体冷却凝固而获得的原子呈长程无序排列的固体材料.但快速冷却时,合金熔体冷却速率的可控性较差,要使全部熔体的冷却速率一致,即获得的非晶合金的冷却与凝固条件一致是很困难的.为了解决这个问题,1969年,Pond和Maddin[4]研制出一种可以制备出非晶合金薄条带的新技术——合金熔体旋淬技术.这种技术将合金熔体直接喷射在旋转的铜轮上冷却,实现了可连续制备非晶合金薄带,并使薄带的冷却速率基本一致.这种新技术不仅使非晶合金薄带的制备速度大幅加快,从而显著提升了非晶合金材料的研发速度,还大幅提高了所制备的非晶合金薄带的成分与结构均匀性.这种技术的出现也为铁基非晶合金的发展带来了机遇.由于铁基非晶合金具有优异的软磁性能,同时还具有高硬度、高耐磨性能和优异的耐蚀性能等性能特征,使其具有广阔的应用前景,并受到了研究人员和企业界的高度关注.因此,合金熔体旋淬技术的出现引发了Fe基非晶合金材料基础研究与应用研究的第一个热潮,并使Fe基软磁非晶合金研究得到了快速发展[5].在20世纪70年代,基于合金熔体旋淬技术,研究人员研发出了很多新型Fe基软磁非晶合金材料.相继研发出了Fe-Ni-P-B,Fe-Ni-P-B-M,Fe-B,Fe-B-C,Fe-Si-B,Fe-Si-B-M系Fe基非晶合金[6−11]和Co基软磁非晶合金[12,13],发现它们多具有较好的软磁性能.同时,高质量、均匀、一致性好的非晶合金带材为促进了铁基软磁非晶合金相关基础科学问题的研究,逐渐揭示了合金化元素和加工工艺对Fe基、Co基合金的非晶形成能力和磁学性能的影响规律.首先,Simpson和Brambley[14]提出没有磁晶各向异性的非晶合金应具有很低的矫顽力,早期沉积法制备的Co-P非晶合金的矫顽力很高不是其本征性能,是成分不均匀性所致.这一点很快就被Chi和Cargill[15]用试验方法予以证实.另一个重要发现是软磁非晶合金制备过程中引入的内应力会显著增大其矫顽力.通过消除制备过程中产生的成分结构不均匀性和内应力,可以显著降低软磁非晶合金的矫顽力.如早期制备的FePC软磁非晶合金的矫顽力高达240 A/m便是与急冷过程中引入的高内应力有关,这种高内应力导致了大的应力-磁致伸缩各向异性.又如采用熔体旋淬技术制备的FeNiPB非晶合金条带的矫顽力约为8 A/m,文献[6,16]通过采用适当的低温退火工艺来消除其内应力,便可使该软磁非晶合金的矫顽力降低至约0.8 A/m.实验结果充分证明了消除制备过程中引入的内应力可显著降低软磁非晶合金的矫顽力.降低矫顽力可降低软磁非晶合金的磁滞损耗.非晶合金因原子呈无序排列,没有晶界阻碍磁畴壁的移动,使Fe基非晶合金具有小的矫顽力,因此磁滞损耗小;同时,原子的无序排列,使Fe基非晶合金具有较大的电阻率,因此,涡流损耗较小.所以与传统的晶态软磁材料相比,Fe基软磁非晶合金具有更小的铁损(铁损主要为磁滞损耗、涡流损耗和剩余损耗构成).随后的研究还发现,采用合适的退火和磁场退火处理,可使FeB系软磁非晶合金的矫顽力和铁损降低[17].研究结果表明,铁基软磁非晶合金具有优异的软磁性能源于其原子呈长程无序排列的结构特征,而成分、结构的均匀性及内应力等因素均对非晶合金软磁性能有重要影响.通过工艺方法改善非晶合金结构均匀性和消除内应力可显著提高软磁非晶合金的磁学性能.这些研究成果为Fe基软磁非晶合金的应用提供了理论依据.1979年联信(Allied Signal)公司开发出可以生产较宽带材的平面流铸造技术[18],为连续稳定地生产成分结构均匀性和一致性好的Fe基非晶合金带材奠定了技术基础.基于该技术,1982年建成了软磁非晶合金带材连续生产企业,开始生产在此前后注册命名的METGLAS系列Fe基、Co基和FeNi基系列非晶合金带材,软磁非晶合金进入了产业化和商品化时代.由于研发的METGLAS2605系列FeSiB系软磁非晶合金具有很好的综合软磁性能[19,20](见表1),被逐渐应用于变压器、电抗器、电磁屏蔽等众多电磁领域.用其替代硅钢制造配电变压器铁芯可显著降低铁损,空载损耗降低达70%以上,节能效果显著,性能十分诱人.1984年,美国四个变压器厂家在IEEE会议上展示了用非晶制造铁芯的实用非晶配电变压器,从而将铁基软磁非晶合金的应用研发推向高潮.在这期间,美国主要致力于非晶合金带材的大规模生产和节能非晶配电变压器的推广应用,主导了非晶变压器市场.到1989年,美国Allied Signal公司已经具有年产6万吨非晶带材的生产能力,全世界约有100万台非晶配电变压器投入运行,所用铁基非晶带材几乎全部来源于该公司[21].除美国之外,日本和德国在非晶合金应用开发方面也拥有自己的特色,重点是电子和电力电子元件,例如高级音响磁头、高频电源(含开关电源)用变压器、扼流圈、磁放大器等.但在1988年以前,铁基软磁非晶合金应用市场仍以美国为主导.在晶态软磁材料中,高Fe元素含量的纯铁、硅钢等具有高的饱和磁感强度,但矫顽力稍大.而且,因磁晶各向异性的影响和晶界缺陷的影响,矫顽力与晶粒尺寸D 成反比(见图1)[22,23].从图1可知,在晶粒尺寸大于约0.1µm的范围内,随着晶粒尺寸减小,矫顽力随晶粒尺寸D的倒数快速增加.因此传统晶态软磁铁合金,如典型的硅钢软磁合金常采用工艺方法来获得大的晶粒尺寸和择优取向、高斯织构([001](110))或立方织构([001](100))来优化软磁性能.而当晶粒尺寸减少至磁畴壁厚度尺寸量级时,由于磁晶各向异性的影响,矫顽力将非常大.非晶合金具有各向同性的特征,并具有很小的结构关联尺寸,即非晶合金的短中程序特征尺寸.软磁非晶合金的铁磁交换作用长度与合金系有关,Fe基非晶合金的交换作用长度一般为20—40 nm,Co基非晶合金的交换作用长度一般为5—10 nm[22,23].因此,对于特征尺寸(短、中程序)只有几个原子长度的非晶合金,其结构关联尺寸D远小于交换作用长度.根据随机各向异性模型,在铁磁交换作用长度范围内,磁各向异性被平均化和减小,使软磁非晶合金具有很小的磁各向异性常数,因而具有很小的矫顽力(图1)[22,23].实际上,若晶粒尺寸小至与非晶合金结构特征相近——原子间距尺寸相近的纳米尺度时,例如晶粒尺寸约为10 nm的铁基纳米晶合金,应具有与非晶合金相近的小的磁各向异性常数和矫顽力.但获得晶粒尺寸小于20 nm的铁基纳米晶合金材料却非常困难.1988年,Yoshizawa等[24]在FeSiB合金中添加少量Cu和Nb,开发出了Fe73.5Si13.5B9Nb3Cu1非晶合金,通过晶化退火获得了均匀析出、且弥散分布在非晶基体上的纳米尺度(10—15 nm)α-Fe(Si)相,这种新型纳米晶/非晶合金的矫顽力低至0.53 A/m,具有很好的综合软磁性能.该合金被注册为FINEMET,而后又开发出了FINEMET系列非晶纳米晶合金.该类Fe基非晶纳米晶软磁合金的特点是利用Cu元素微小尺度偏聚,在晶化温度之上退火时促进α-Fe形核析出.同时,利用Nb元素在α-Fe相中固溶度极低且扩散慢的特点,抑制晶粒长大,从而在工艺上较容易获得大量纳米尺度(15—20 nm以下)的α-Fe相弥散析出分布在非晶基体上,即获得铁基纳米晶/非晶复相合金.并常简称为铁基软磁纳米晶合金.Herzer[22,23]认为由非晶合金经热处理后析出的纳米级晶化相是随机分布的,因此晶化相的磁各向异性轴在晶粒尺寸内也是随机分布的,纳米晶合金具有与非晶态合金类似的由交换作用引起的随机分布的磁各向异性.交换作用长度L0(或Lex)为其中,A是相邻原子的交换作用刚度系数,K1是磁各向异性常数,φ0=1是比例因子.L0表征了一个最小尺度,当尺寸小于L0时,没有明显的外在磁化方向.因此,对于特征尺寸(短、中程序)只有几个原子长度的非晶合金和晶粒尺寸一般为10 nm左右的纳米晶合金,结构关联尺寸(晶粒尺寸)D都远小于交换作用长度.因此磁晶各向异性常数被平均化为〈K〉,即[22,23]式中χ为晶化体积分数,D为晶粒尺寸.另外,Herzer认为如果假设磁化过程是自旋的一致转动过程,矫顽力Hc和初始磁导率µi只与〈K〉有关,其关系可以表达为:式中,Pc与Pµ为常数,Js为饱和磁化强度,µ0为真空磁导率.因非晶、纳米晶合金的磁各向异性被平均化和减小,故表现出优异的软磁性能.此外,在纳米晶粒生成过程中,降低了合金的磁致伸缩系数,从而降低了磁弹性能,这也有利于降低磁各向异性,从而优化软磁性能.从(3)和(4)式可知,纳米晶合金的矫顽力和初始磁导率分别和晶粒尺寸D的六次方成正比和成反比[22,23].当退火获得的Fe基纳米晶-非晶软磁合金具有很小的晶粒尺寸时,如20 nm以下时,合金具有很低的矫顽力[23−25]和较高的磁导率.因此,FINEMET合金具有很低的矫顽力和高的导磁率(图1,(3)和(4)式).尽管FINEMET合金的饱和磁感应强度只有约1.24 T,低于常用的非晶合金和硅钢,但这类合金的突出优点在于兼备了铁基非晶合金的高磁感强度和钴基非晶合金的高磁导率、低损耗,并且是成本低廉的铁基合金(见表2).因此铁基软磁纳米晶合金的发明是软磁非晶合金材料的一个突破性进展,将铁基非晶态合金研发又推向了一个新高潮——即开启了软磁非晶(/纳米晶)合金研究与应用的第二个热潮.FINEMET软磁纳米晶合金可以替代钴基非晶合金、晶态坡莫合金和铁氧体,在高频电力电子和电子信息领域中获得了广泛应用,达到减小体积、降低成本等目的.在FINEMET软磁纳米晶合金问世后,日立金属公司很快便实现了产业化,并将相关产品推向市场.1992年,德国VAC公司开始推出纳米晶合金替代钴基非晶合金,尤其在网络接口设备上,如ISDN,大量采用纳米晶磁芯制作接口变压器和数字滤波器件.在此期间,美国Allied Signal公司(后被Honeywell公司兼并)也加强了非晶合金在电力电子领域的推广应用,先后推出了多个系列的铁芯制品[21].但FINEMET的饱和磁感应强度毕竟仅有约1.24 T,为达到相同的磁通量,与硅钢相比,需要更大的尺寸.因此,有必要提高其饱和磁感强度.合金的饱和磁感应强度取决于原子间的交换耦合作用,因此通常和Fe元素含量成正比,要提高合金体系的饱和磁感应强度就需相应提高Fe元素含量.1998年,Suzuki等[26]开发了高铁含量的FeZrB非晶纳米晶双相合金体系,并注册为NANOPERM合金.该合金的Bs远高于FINEMET合金(见表2).但该合金的矫顽力比FINEMET合金稍高,有效磁导率比FINEMET合金稍低.而且不能在空气中制备,因此难以低成本工业化应用.随后,Willard等[27]在该体系中加入Co,开发出FeCoMBCu(M=Zr,Nb,Hf)(如(Fe0.5Co0.5)88Zr7B4Cu1)纳米晶合金,并注册为HITPERM.该合金具有很高的居里温度,经过合适的热处理,可获得在非晶基体上均匀分布着细小纳米颗粒的非晶纳米晶双相组织.该纳米晶合金也具有较高的饱和磁感应强度,但矫顽力稍高(见表2),且大量使用Co使该合金成本较高.目前,已在工程中大量应用的非晶合金仍然是用于制造变电变压器铁芯的FeSiB 铁基软磁非晶合金[21],在我国的牌号是1K101,对应的国外牌号是METGLAS 2605SA1合金,其饱和磁感强度也仅为1.56 T,远低于硅钢(见表1、表2).若能进一步提高铁基非晶合金的饱和磁感强度,将可减小铁芯尺寸、提高工作磁感强度、降低铁损等,意义重大.因此,提高铁基软磁非晶合金的饱和磁感强度很有必要.但提高磁感应强度Bs,就需要提高铁磁性元素Fe的含量,而提高Fe含量,便需要减少非晶化元素B,Si等元素含量,这会使合金的非晶形成能力降低,从而使非晶合金制备难度增加.此外,加入一些元素时还需要考虑工业化规模生产时的可行性,因为工业化生产是在大气条件下进行的.因此,需要仔细进行合金设计研究.2006年,Ogawa等[28]发明了一种商品名为HB1的铁基非晶合金Fe81.7Si2B16C0.3和Fe82Si2B14C2,Bs分别达1.64 T和1.67 T.研究发现,相比饱和磁感应强度为1.56 T的1K101非晶合金,这种高Bs非晶合金在50 Hz,1.4 T工作磁感条件下的损耗值降低了15%.即具有更高Bs的HB1非晶合金在相同的工作条件下的损耗更低[29].这一研究结果引起了国内外同行的高度重视.尽管在工业化中仍存在不少问题,但这表明在不添加Co等贵金属元素的条件下,仍可进一步提高铁基软磁非晶合金的饱和磁感强度.2009年,Makino等[30,31]开发出了Fe-Si-B-P-Cu体系,该体系在纳米晶化后具有高达约1.9 T的饱和磁感应强度,可与硅钢相媲美,而且该合金具有高磁导率和较小的矫顽力,因此非常有吸引力.该铁基软磁非晶/纳米晶合金体系被注册为NANOMET.但该合金非晶形成能力低,纳米晶化过程要求非常严格,至今仍难商业化.尽管如此,HB1和NANOMET的出现极大地鼓励了研究人员[32],引起了铁基软磁非晶合金的第三次研究热潮,即导致了高Bs铁基软磁非晶/纳米晶合金的研究热潮.在这一仍在进行中的研究热潮中,我国学者都积极参与其中,取得了不少重要进展.2011年,Lü等[33]通过微量添加Cu元素同时提高了Fe76−xC7Si3.3B5P8.7Cux合金的非晶形成能力和饱和磁感应强度,当含0.7%Cu时,非晶合金的饱和磁化强度达1.61 T.而纳米晶化后,饱和磁感应强度进一步提高到1.79 T,矫顽力为11 A/m.同年,我们课题组[34]通过提高Fe含量,结合合金熔体提纯方法,开发出Fe81Mo1P7.5C5.5B2Si3非晶合金,饱和磁感应强度达1.64 T.Shen等[35]在Fe76Si9B10P5块体非晶软磁合金的基础上,提高Fe 含量,降低Si含量,制备出Fe80Si5B10P5块体非晶软磁合金,使饱和磁感应强度提高到1.6 T.2015年,Wang等[36],将Fe-P-C-B-Si体系的Fe含量提高到83 at%,同时通过调节类金属P,B,Si的含量,制备出一系列高饱和磁感应强度的非晶软磁合金,饱和磁感应强度达到1.61—1.68 T,矫顽力仅为2.4—4 A/m,磁导率为6000—10000.纳米晶化已被证明是提高铁基非晶合金饱和磁感强度和降低矫顽力的有效方法. 2011年,Ohta和Yoshizawa[37]综述了铁基非晶合金纳米晶化研究进展,指出经过纳米晶化退火,Fe84−x−yCuxNbySi4B12(x=0—1.4,y=0—2.5)合金的中Fe82Cu1Nb1Si4B12的饱和磁化强度Bs达到1.78 T,矫顽力Hc只有3.2 A/m,不同条件下的铁损分别为(W/kg):P15/50=0.20,P10/400=1.3,P10/1000=4.4.其原因被认为是加入的少量Nb阻止了纳米晶粒长大,同时使饱和磁感应强度不降低,退火后纳米晶粒的尺寸仅为15 nm.随后,Shen课题组[38,39]报道通过添加P元素,提高了Fe83.3Si4Cu0.7B12−xPx纳米晶合金的软磁性能,其中,Fe83.3Si4Cu0.7B6P6纳米晶合金表现出优异的软磁性能,Bs达1.77 T,Hc为4.2 A/m,磁导率为11600.而添加微量铜元素可提高Fe84−xSi4B8P4Cux(x=0,0.75,1.0,1.25,1.5)软磁纳米晶合金的饱和磁化强度,当含1.25%Cu时软磁性能最优,Bs达到1.83 T,Hc为2.1 A/m,磁导率为31600,不同条件下的铁损分别为(W/kg):P10/400=4.60,P10/1000=13.5.2015年,Xiang等[40]报道了饱和磁化强度达1.73 T的Fe82Si4B10P2Cu1Nb1合金,它的矫顽力为4.5 A/m,磁导率为23000.日本东北大学的Sharma等[41]开发出饱和磁化强度达到1.85 T、矫顽力为6 A/m的Fe85Si2B8P4Cu1合金.2016年,日本国立材料研究所的Jafari等[42]开发出具有优异磁性能的Fe84.3Si4B8P3Cu0.7合金,饱和磁化强度达1.76 T.2017年,研究人员还发现[43],不加Cu的条件下,也同样可以通过控制晶化获得纳米晶组织,改善磁学性能.综上可知,在最近几年内,高饱和磁感强度铁基软磁非晶/纳米晶合金研究中取得了一系列很重要的进展,而我国学者已成为高饱和磁感强度铁基软磁非晶/纳米晶合金研究中的重要力量,已取得多项重要成果[33−36,38,39,41,44,45].随着我国研究队伍的不断壮大,投入不断增加,相信我国将会取得更多突破性进展.我国铁基软磁非晶合金研发与应用研究始于1976年,走了一条独立自主的道路[21].安泰科技股份有限公司历经40余载,先后突破了非晶带材在线自动卷取等技术,形成了带材连续生产的多个核心技术,先后建成了百吨级铁基非晶带材生产线、千吨级铁基非晶带材生产线、万吨级铁基非晶带材生产线,稳定生产带材宽度已可达340 mm.特别是2015开始,我国非晶合金带材产量显著增加.当年国内非晶带材销量9.4万吨:其中安泰科技约3万吨,青岛云路约1.8万吨,其他国产厂家共计约6000吨,日立金属株式会社在华销售量约4万吨.2015年国产带材销量首次占50%以上.2016年,中国非晶带材产能约14万吨以上,实际产量约11.3万吨,首次超过10万吨.2016国内有5家企业年产能达到万吨,其中安泰科技股份有限公司作为国内最大的非晶带材生产商,产能已接近8万吨.2016年,安泰、云路等企业实际产量均达到或接近3万吨.我国已成为国际铁基软磁非晶/纳米晶合金带材生产和相关产品制造大国.目前,软磁非晶/纳米晶合金材料已被大量应用于配电变压器、互感器、电抗器等器件,应用领域涉及电力电源、开关电源、仪器仪表、车载电子、工矿/石油、太阳能等领域.特别是在我国,上述各领域对软磁非晶/纳米晶铁芯的需求量仍在不断增加.此外,我国正在针对市场需求,开发专用软磁非晶/纳米晶合金材料,进一步拓展应用领域.同时,还瞄准高频高效节能电机等高端产品,开发高性能软磁非晶/纳米晶合金材料和相关产品加工制造核心技术,满足市场和高技术领域发展的需求.3 铁磁非晶/纳米晶合金面临的挑战和研发方向虽然铁基软磁非晶/纳米晶合金具有矫顽力低、有效磁导率高、铁损低等优点,与传统软磁材料相比,在众多应用中具有明显的优势,但仍存在很多挑战,需要深入开展研究,以满足工业领域和高新技术发展的要求.目前铁基软磁非晶/纳米晶合金研发和应用面临的主要挑战及研发方向有以下几个方面.1)非晶合金的脆性问题.铁基软磁非晶合金、特别是纳米晶合金存在延性低、脆性大的问题,需要深入研究影响其延性的因素,探索提升延性的方法,保证使用安全.2)饱和磁感强度Bs仍偏低,综合磁学性能仍有待进一步提升.目前,大量使用的Fe 基软磁非晶合金的饱和磁感强度Bs仍明显低于硅钢,仍有进一步提升的必要.目前已出现一些具有较高Bs的Fe基软磁非晶合金体系,但仍存在热处理工艺复杂等问题.需要进一步研究新工艺或工艺性更好的合金,使合金具有高饱和磁感强度、低的矫顽力和高的磁导率,即获得具有优异综合软磁性能的铁基软磁非晶合金或非晶/纳米晶合金.3)缺乏高效的非晶合金加工技术.非晶合金/纳米晶合金因硬度高、较脆,加工较困难,加工效率不高.需要深入研究影响软磁非晶/纳米晶合金加工性能的因素,探索提高加工效率和保证加工质量的技术方法.。
铁基非晶纳米晶软磁材料的研究及磁源的制备

铁基非晶纳米晶软磁材料的研究及磁源的制备引言在现代科技应用中,磁性材料起着至关重要的作用。
铁基非晶纳米晶软磁材料具有高饱和磁感应强度、低矫顽力、低损耗等优异特性,在电机、传感器、储能设备等领域具有广阔的应用前景。
本文将对铁基非晶纳米晶软磁材料的研究及磁源的制备进行全面、详细、完整且深入地探讨。
铁基非晶纳米晶软磁材料的特性铁基非晶纳米晶软磁材料具有以下特性:1.高饱和磁感应强度:铁基非晶纳米晶软磁材料具有高饱和磁感应强度,能够提供更强的磁场。
2.低矫顽力:铁基非晶纳米晶软磁材料具有低矫顽力,能够在较小的外加磁场下实现快速磁化与反磁化。
3.低损耗:铁基非晶纳米晶软磁材料具有低磁滞损耗和涡流损耗,能够减少能量的损耗。
4.高温稳定性:铁基非晶纳米晶软磁材料具有较好的高温稳定性,能够在高温环境下工作。
铁基非晶纳米晶软磁材料的研究方法为了研究铁基非晶纳米晶软磁材料的性质和制备磁源,科学家们采用了多种研究方法,包括但不限于以下几种:1. 高温熔融法高温熔融法是制备铁基非晶纳米晶软磁材料的常用方法。
科学家们将合适的金属原料在高温环境下熔融混合,然后迅速冷却,形成非晶态或纳米晶态的材料。
2. 离子束溅射法离子束溅射法是一种物理气相沉积方法,可以制备出具有高纯度和均匀性的铁基非晶纳米晶软磁材料。
通过束流中的离子轰击原材料的靶,将靶材溅射到基底上,形成薄膜材料。
3. 机械合金法机械合金法通过高能球磨、挤压等机械力作用,将金属粉末进行均匀混合和纳米晶化处理,制备出铁基非晶纳米晶软磁材料。
4. 液相合成法液相合成法利用化学反应在液相中合成铁基非晶纳米晶软磁材料。
通过合适的反应条件和控制方法,将溶液中的金属离子还原成固体材料。
铁基非晶纳米晶软磁材料磁源的制备铁基非晶纳米晶材料的制备是实现磁源制备的基础。
通过适当的处理和改性,可以获得具有优异磁性的铁基非晶纳米晶软磁材料磁源。
1. 形状设计根据具体的应用需求,可以对铁基非晶纳米晶软磁材料进行形状设计。
《2024年Fe基非晶纳米晶合金软磁材料MA球磨与SPS烧结制备技术研究》范文

《Fe基非晶纳米晶合金软磁材料MA球磨与SPS烧结制备技术研究》篇一摘要:本文着重研究了Fe基非晶纳米晶合金软磁材料的制备技术,采用机械合金化(MA)球磨与放电等离子烧结(SPS)相结合的方法,探讨其制备过程中的材料性能和工艺参数的影响。
通过实验数据的分析,本文对制备过程进行了解析,以期为相关领域的研发和应用提供理论依据。
一、引言随着科技的发展,Fe基非晶纳米晶合金因其独特的软磁性能在电子、电力、通信等领域得到了广泛应用。
其制备技术的研究对于提高材料性能、降低成本、推动产业发展具有重要意义。
本文采用机械合金化(MA)球磨与放电等离子烧结(SPS)相结合的方法,对Fe基非晶纳米晶合金的制备技术进行研究。
二、材料与方法1. 材料准备选用纯度较高的Fe、B、Si、Nb等元素作为原材料,按照一定比例混合制备成合金粉末。
2. 机械合金化(MA)球磨采用行星式球磨机对合金粉末进行球磨,通过高能球磨使粉末达到纳米级别。
研究球磨时间、球磨介质、球料比等参数对材料性能的影响。
3. 放电等离子烧结(SPS)将球磨后的粉末放入SPS烧结炉中,通过脉冲电流加热和压力作用,使粉末烧结成致密的合金材料。
研究烧结温度、压力、保温时间等参数对材料性能的影响。
三、结果与讨论1. MA球磨对材料性能的影响实验结果表明,随着球磨时间的延长,合金粉末的粒度逐渐减小,达到纳米级别。
同时,球磨过程中引入的能量使合金粉末发生非晶化,提高了材料的软磁性能。
此外,球磨介质和球料比也对材料性能产生一定影响。
2. SPS烧结对材料性能的影响烧结温度、压力和保温时间是影响SPS烧结效果的关键因素。
适当提高烧结温度和压力,可以加快烧结过程,使粉末颗粒之间的结合更加紧密,从而提高材料的密度和软磁性能。
同时,合理的保温时间可以保证烧结过程的稳定性,进一步提高材料的性能。
3. 制备工艺的优化通过调整MA球磨和SPS烧结的工艺参数,可以获得具有优异软磁性能的Fe基非晶纳米晶合金。
固化对纳米晶磁芯软磁性能影响的研究探究新

任森生 等
收稿日期:2018年1月19日;录用日期:2018年2月7日;发布日期:2018年2月14日
摘
要
本文将单辊快淬法制备的Fe基非晶薄带绕成磁芯, 经500℃退火2小时制成纳米晶磁芯, 然后选用有机硅、 聚氨酯和环氧树脂3种固化剂分别固化纳米晶磁芯。采用TD8120型软磁交流测试系统和TD8220-A型软 磁直流测试系统,分别测试固化前后纳米晶磁芯的交、直流软磁性能。对比分析采用3种不同固化剂固 化对纳米晶磁芯的矫顽力、磁导率、损耗等软磁参数的影响。研究结果表明,采用有机硅固化的纳米晶 磁芯的直流软磁性能受固化影响最小,其直流软磁性能最好;采用聚氨酯固化的纳米晶磁芯的交流软磁 性能受固化影响最小,其交流软磁性能最佳。固化成型是纳米晶磁芯制备的关键工艺,降低固化对纳米 晶磁芯性能的影响具有重要的现实意义。本文研究结果对于纳米晶磁芯固化成型工艺的改进具有参考价 值。
3. 结果与讨论
3.1. 固化剂对纳米晶磁芯直流软磁特性的影响
图 1 为固化前后各磁芯的直流磁滞回线,其中曲线 a 为未固化磁芯样品磁滞回线,曲线 b 为环氧树 脂固化磁芯样品磁滞回线, 曲线 c 为聚氨酯固化磁芯磁滞回线, 曲线 d 为有机硅固化磁芯样品磁滞回线, 表 1 为固化前后各磁芯的直流软磁参数。固化对磁芯饱和磁感应强度影响较小,使磁芯磁导率降低,矫 顽力升高,直流软磁特性减弱。其中环氧树脂固化磁芯软磁性能最差,矫顽力为 1.75 A/m (相比固化前升 高 42%),起始磁导率为 48.16 mH/m (相比固化前降低 40%),最大磁导率为 227.57 mH/m (相比固化前降
2. 实验
本文使用单辊快淬法制备的 Fe73.5Cu2Nb3Si12.5B9 (Fe 基合金)非晶薄带[12],宽 15 mm,厚 19 μm。将 其盘绕成内直径 29.5 cm,外直径 39.495~39.505 cm,质量约为 49.7 g 的环状磁芯。在氮气保护下,500℃
高性能Fe_Si软磁粉芯的制备及性能研究_李杨

粉芯的显微组织。 从图 3 中可以看出: 大颗粒紧密 接触, 小颗粒填充于大颗粒堆积的间隙之中 , 有的小 颗粒直接附着于大颗粒之上。一些小颗粒发生了团 SiO2 聚, 这可能跟原料中使用了纳米尺度的 Al2 O3 、 表面活性很 等粉末有关。因为纳米粉末比表面大, 高, 在混粉和压制过程中容易团聚。 热处理后样品 中仍然存在不少的孔隙, 但是孔隙尺寸均较小, 且分 布较为分散; 而随着压制压力的提高, 孔隙数量和孔 隙尺寸均减小, 说明样品的致密度随着压制压力的 提高得到了相应的提高, 这对于软磁粉芯磁学性能 的改善至关重要。
( a) 600MPa; ( b) 700MPa; ( c) 800MPa; ( d) 900MPa
图3 Fig. 3
不同压力压制热处理后坯体断面形貌
Fractography of samples compacted with different pressures and after heat treatment
2. 4
压制压力和粘结剂的含量对热处理后粉芯磁
试验中, 通过振动磁强计测试获得了热处理后 粉芯磁性能的相关结果, 并得到了饱和磁感应强度 BS 、 结果见表 1 所 矫顽力 H C 和磁导率 μ 等数据, 示。从表 1 中可以看出, 随着压制压力的增大, 饱和 磁感应强度和磁导率均逐渐增大, 这是因为: 压制压 力的提高会导致生坯致密度的提高, 而生坯密度与 热处理后样品的饱和磁感应强度和磁导率关系均为 同向变动。
2
2. 1
结果与讨论
温压温度对温压生坯密度的影响 图 1 是不同压制压力下, 压坯密度随温压温度
图2 Fig. 2 不同温度下压制压力对压坯密度的影响 Relationship between pressing pressure and
《Fe基非晶纳米晶合金软磁材料MA球磨与SPS烧结制备技术研究》范文

《Fe基非晶纳米晶合金软磁材料MA球磨与SPS烧结制备技术研究》篇一一、引言随着现代电子技术的飞速发展,软磁材料因其优异的磁性能在电力、电子、通信等领域得到了广泛应用。
Fe基非晶纳米晶合金软磁材料因其高饱和磁感应强度、低铁损等特性,在软磁材料领域具有重要地位。
本文将重点探讨Fe基非晶纳米晶合金软磁材料的制备技术,特别是机械合金化(MA)球磨与放电等离子烧结(SPS)烧结技术的研究。
二、Fe基非晶纳米晶合金软磁材料概述Fe基非晶纳米晶合金软磁材料是一种新型功能材料,具有优异的磁性能、良好的成型性及热稳定性等特点。
该材料的制备技术主要涉及到机械合金化、纳米晶化以及烧结技术等方面。
其中,机械合金化与放电等离子烧结是当前研究最为活跃的领域。
三、MA球磨技术MA球磨技术是一种通过高能球磨使粉末颗粒达到纳米级别的技术。
在Fe基非晶纳米晶合金软磁材料的制备过程中,MA球磨技术被广泛应用于制备非晶粉末。
该技术通过高能球磨使原料粉末在球磨罐内发生反复的碰撞、挤压和剪切,从而达到细化粉末、提高混合均匀性的目的。
此外,MA球磨还可以通过控制球磨时间和球磨介质等参数,实现对非晶结构的控制。
四、SPS烧结技术SPS烧结技术是一种利用脉冲电流进行快速加热和烧结的技术。
在Fe基非晶纳米晶合金软磁材料的制备过程中,SPS烧结技术被广泛应用于实现纳米晶的烧结和致密化。
该技术具有加热速度快、温度梯度小、烧结时间短等优点,能够有效地提高烧结体的致密度和磁性能。
此外,SPS烧结还可以通过控制电流、压力和温度等参数,实现对烧结体的微观结构和性能的控制。
五、MA球磨与SPS烧结制备技术研究针对Fe基非晶纳米晶合金软磁材料的制备,本文研究了MA 球磨与SPS烧结技术的结合应用。
首先,通过MA球磨制备出非晶粉末,并通过对球磨参数的控制实现非晶结构的优化。
其次,将非晶粉末进行SPS烧结,通过控制烧结参数实现纳米晶的烧结和致密化。
最后,对制备出的软磁材料进行性能测试和分析,探讨MA球磨与SPS烧结技术对材料性能的影响。
Fe基纳米晶_铁氧体复合材料磁粉芯制备及其软磁性能
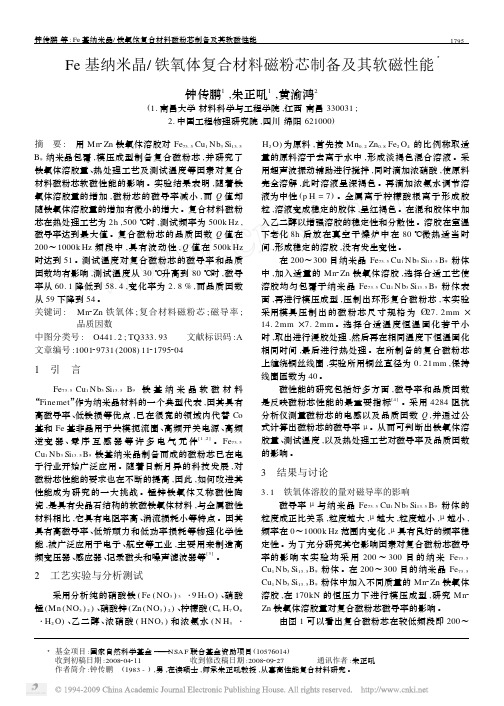
Fe基纳米晶/铁氧体复合材料磁粉芯制备及其软磁性能3钟传鹏1,朱正吼1,黄渝鸿2(1.南昌大学材料科学与工程学院,江西南昌330031;2.中国工程物理研究院,四川绵阳621000)摘 要: 用Mn2Zn铁氧体溶胶对Fe73.5Cu1Nb3Si13.5 B9纳米晶包覆,模压成型制备复合磁粉芯,并研究了铁氧体溶胶量、热处理工艺及测试温度等因素对复合材料磁粉芯软磁性能的影响。
实验结果表明,随着铁氧体溶胶量的增加,磁粉芯的磁导率减小,而Q值却随铁氧体溶胶量的增加有微小的增大。
复合材料磁粉芯在热处理工艺为2h,500℃时,测试频率为500k Hz,磁导率达到最大值。
复合磁粉芯的品质因数Q值在200~1000k Hz频段中,具有波动性,Q值在500k Hz 时达到51。
测试温度对复合磁粉芯的磁导率和品质因数均有影响,测试温度从30℃升高到80℃时,磁导率从60.1降低到58.4,变化率为2.8%,而品质因数从59下降到54。
关键词: Mn2Zn铁氧体;复合材料磁粉芯;磁导率;品质因数中图分类号: O441.2;TQ333.93文献标识码:A 文章编号:100129731(2008)11217952041 引 言Fe73.5Cu1Nb3Si13.5B9铁基纳米晶软磁材料“Finemet”作为纳米晶材料的一个典型代表,因其具有高磁导率、低铁损等优点,已在很宽的领域内代替Co 基和Fe基非晶用于共模扼流圈、高频开关电源、高频逆变器、零序互感器等许多电气元件[1,2]。
Fe73.5 Cu1Nb3Si13.5B9铁基纳米晶制备而成的磁粉芯已在电子行业开始广泛应用。
随着日新月异的科技发展,对磁粉芯性能的要求也在不断的提高,因此,如何改进其性能成为研究的一大挑战。
锰锌铁氧体又称磁性陶瓷,是具有尖晶石结构的软磁铁氧体材料,与金属磁性材料相比,它具有电阻率高、涡流损耗小等特点。
因其具有高磁导率、低矫顽力和低功率损耗等物理化学性能,被广泛应用于电子、航空等工业,主要用来制造高频变压器、感应器、记录磁头和噪声滤波器等[3]。
铁基非晶纳米晶软磁材料的研究及磁源的制备

铁基非晶纳米晶软磁材料的研究及磁源的制备
铁基非晶纳米晶软磁材料是目前磁性材料领域中研究热点之一。
该材
料具有高饱和磁通密度、低磁滞和低损耗等优良的磁学性能。
此外,
它还具有良好的加工性能,能够以极细的粒子尺寸制备出纳米级材料,这也为其在各种领域中的应用提供了广泛的可能。
目前,铁基非晶纳米晶软磁材料的制备方法主要有高能球磨、溅射和
快速凝固等。
其中,快速凝固法是目前制备该材料最常用的方法之一。
通过快速凝固技术,可以制备出纳米晶非晶合金材料,如Fe-Si-B-Cu-Nb等。
这种材料具有优良的磁学性能和机械性能,非常适合作为磁源材料使用。
研究表明,铁基非晶纳米晶软磁材料可以广泛应用于磁记录、变压器、电感器、电源等领域。
尤其是在电动汽车、风力发电机等领域,它的
应用前景非常广阔。
铁基非晶纳米晶材料的制备技术和性能研究也有
望推动磁性材料产业快速发展。
在未来的研究中,铁基非晶纳米晶软磁材料的制备和性能研究仍需要
不断地深入探索。
尤其是在磁性材料的领域中,材料的微观结构和磁
性能的关系仍存在着很多未知的领域。
因此,需要加强对铁基非晶纳
米晶软磁材料的研究,提高其制备工艺和性能,以此为推动磁性材料产业的发展做出更大的贡献。
- 1、下载文档前请自行甄别文档内容的完整性,平台不提供额外的编辑、内容补充、找答案等附加服务。
- 2、"仅部分预览"的文档,不可在线预览部分如存在完整性等问题,可反馈申请退款(可完整预览的文档不适用该条件!)。
- 3、如文档侵犯您的权益,请联系客服反馈,我们会尽快为您处理(人工客服工作时间:9:00-18:30)。
-7.2
-3.35
第4期
钱坤明等:固化工艺对铁基纳米晶软磁材料磁性能的影响研究
47
固化前
B(×0.2 T) 5 4 3 2 1
-6 -5 -4 -3 -2 -1 -1
-2
-3 -4 -5
H(×16 A/m) 1 23 45 6
固化后
B(×0.2 T) 5 4 3 2 1
-6 -5 -4 -3 -2
第34卷 第4期 2011年 7月
兵器材料科学与工程 ORDNANCE MATERIAL SCIENCE AND ENGINEERING
DOI:CNKI:33-1331/TJ.20110704.1553.001 网络出版时间:2011-07-04 15:53 网络出版地址:/kcms/detail/33.1331.TJ.20110704.1553.001.html
表 2 固化前后样品的静态性能 Table 2 Static properties of samples before and after curing
性能
Br/T
Bs/T
Hc/(A·m-1)
矩形比α
固化前
0.60
1.12
1.11
0.536
固化后
0.58
1.12
1.03
0.518
变化率/%
-3.3
0
Abstract The effect of curing agent and curing process on the nanocrystalline soft magnetic properties of Fe72.5Cu1Nb2V2Si13.5B9 was studied. The results show that the use of special additives in the composition formula of curing agent helps reduce the change rate of magnetic properties. The samples show the lowest change rate of performance when cured at 100 ℃ for 1 h. The cured core shows a certain influence on the static performance,but the change rate is less than 10%. Key words nanocrystalline soft magnetic materials;cure;permeability;loss
摘 要 研究固化剂材料、固化工艺对 Fe72.5Cu1Nb2V2Si13.5B9纳米晶软磁铁芯磁性能的影响。结果表明:采用特种添加剂的 固化剂成分配方有利于降低铁芯固化后磁性能的变化率;100 ℃固化温度和 1 h 固化时间是铁芯固化最佳工艺,此时铁
芯的性能变化率最低;铁芯固化后对静态性能有一定影响,但性能变化率在 10%以内。
纳米晶软磁材料具有高磁导率、低损耗、高饱和 磁感应强度的特点,被誉为是 20 世纪继非晶合金后, 软磁材料领域的又一重大进展。经过多年的发展,纳 米晶软磁材料在逆变焊机电源、电流互感器、开关电 源、电磁兼容器件等中得到了广泛的应用[1]。因纳米 晶材料呈薄带状,材料较脆,易折断,在应用时一般将 其绕制成环状或马蹄形状,并装入护盒,难于制备出 复杂形状的纳米晶铁芯,导致了应用的局限性。此 外,作为变压器铁芯使用的纳米晶软磁铁芯,因变压 器绕组的绕线匝数多,一般预先绕好线包,再进行装 配。因此需要将铁芯进行切割,但纳米晶软磁材料因 其脆性无法进行切割。解决上述问题的途径就是对 铁芯进行固化[2],铁芯在固化过程中因受内应力作用 而使铁芯的损耗、磁导率等性能产生变化,国内外大 量学者和机构相继开展了此方面的研究工作,并取得 了积极进展[3]。作者以低损耗型 Fe72.5Cu1Nb2V2Si13.5B9 纳米晶软磁材料为研究对象,开展固化剂材料、固化 工艺等对材料磁性能的影响研究,以期得到较好的低 应力固化方法。
1 试验方法
1.1 样品制备 用带宽为 10 mm 的 Fe72.5Cu1Nb2V2Si13.5B9 纳米晶软
磁材料,绕制成ϕ20 mm×10 mm×10 mm 的环状样品, 用自制的气氛保护热处理炉进行热处理,保护气氛采 用氢气,处理工艺 560 ℃×40 min,快速冷却到室温,取 出样品备用。 1.2 固化工艺
QIAN Kunming1,DING Ang1,JI Song1,ZHANG Yansong1,XU Ying1,HE Yong1,2,DU Genzu3, DU Junyu3,CHENG Shougui3
(1.Ningbo Branch of China Academy of Ordnance Science,Ningbo 315103,China;2.Surface Engineering Research Center of Ningbo,Ningbo 315103,China;3.Ningbo Tonghe Transformer Limited Company,Ningbo 315030,China)
图 2 为不同固化温度下的磁导率、损耗的变化情 况。可以看出,随着固化温度的变化,磁导率和损耗变 化呈先下降后上升的趋势,在 100 ℃固化时两者同时 降到最低,而后随着固化温度的升高,变化率急剧上
磁导率的变化率/%
20
15
10
5
1#
2#
3#
4#
固化剂
图 1 不同固化固化剂对样品磁导率影响
Fig.1 Influence of different curing agent on the permeability
3)静态性能测试表明,铁芯固化后对静态性能有 一定影响,但性能变化率在 10%以内。
4 参考文献
[1]纪松,钱坤明,张延松,等. 非晶/纳米晶软磁材料及其应用
[J]. 兵器材料科学与工程,2005,28(1):51-55. [2]李映雪,丘渝青. 浸渍固化和切割气隙对非晶铁芯性能的影
响[J]. 金属功能材料,1996,3(1):21-23. [3]全白云. 非晶铁芯浸渍切割工艺进展[J]. 金属功能材料,
of samples
80
磁导率 损耗
28
24
损耗的变化率/%
磁导率的变化率/%
60
20
16
40
12
20
8
4
0 20 40 60 80 100 120 140 160 180 固化温度/℃
图 2 不同固化温度对样品磁导率和损耗的影响
Fig.2 Effect of curing temperature on the permeability and
46
兵器材料科学与测试 用 JP9710A 型高频功率测量仪测量样品的高频损
耗,测试条件为 100 kHz,0.3 T;用 3532-50 型 LCR 仪测 量样品在 1 kHz,0.08 A/m 条件下的电感量,根据电感 量 数 据 和 样 品 参 数 计 算 样 品 的 磁 导 率 ,用 MATS-2010DS 软磁直流磁测量仪测量样品的直流磁 性能,测试磁场为 96 A/m。
30 a—磁导率
磁导率的变化率/%
25 20
15 10
5
0.0
0.5
1.0
1.5
2.0
固化时间/h
5.2 b—损耗
损耗的变化率/%
5.0
4.8
4.6
5
4.4
4.2 0.0
0.5
1.0
1.5
2.0
固化时间/h
图 3 固化时间对样品磁导率和损耗的影响
Fig.3 Effect of curing time on permeability and loss of samples
loss of samples
升。可见,过高的固化温度降低铁芯的性能。 2.3 固化时间对样品磁导率和损耗的影响
图 3 为不同固化时间样品的磁导率、损耗的变化 情况。可以看出,固化时间 1 h 的工艺下,样品的磁导 率和损耗变化率最低,随着时间的延长,两者的磁导率 变化率随之上升,损耗变化幅度不大。分析认为,较短 的固化时间下,因固化剂没有完全固化,铁芯内部存在 较大的粘滞应力,导致磁性能变化异常。而较长的固 化时间,使得固化剂在短时间内硬化,易产生局部收缩 应 力 ,同 样 影 响 铁 芯 性 能 。 其 中 磁 导 率 对 应 力 的 变 化 尤 其敏感,导致磁导率的变化率要大于损耗。因 此,用 1 h 的固化时间有利于保持铁芯原始性能。 2.4 固化工艺对静态性能的影响
2 结果与讨论
2.1 固化剂种类对样品磁导率的影响 图 1 为 4 种不同固化剂配方固化后样品磁导率的
变化情况。可以看出,采用 4#配方固化的样品,固化后 磁导率变化率最小。这是因为 4#配方固化剂中添加了 低膨胀和收缩系数的特种添加材料,有效地减轻了固 化剂的固化收缩。前 3 种配方随着稀释剂二甲苯的加 入量增加,样品磁导率变化率逐步降低,因为加入适量 二甲苯可降低固化剂的黏度,减小固化剂的收缩率和 收缩应力。 2.2 固化温度对材料磁导率和损耗的影响
关键词 纳米晶软磁材料;固化;磁导率;损耗
中图分类号 TM271+.2
文献标识码 A
文章编号 1004-244X(2011)04-0045-03
Effect of curing process on the magnetic properties of iron⁃based nanocrystalline soft magnetic materials
1998,5(6):241-247.
高强度烧结 Mg 基合金
日 本 专 利 JP2008 7793 中 公 布 了 日 本 日 产 汽 车 股 份 公 司 等 机 构 研 发 的 高 强 度 的 烧 结 Mg 基 合 金 。 合 金 的 成 分 可 以 用 Mg-aZn-bRE(其中 0<a<10%(原子数分数),0<b<15%(原子数分数), RE 是稀土元素 Y、La、Ce、Pr、Nd、Sm、Eu、Gd、Tb、Dy、Ho、Er 或 Yb 中的至少一种)来表示。该合金具有细晶组织和长寿命堆垛有序相。该合金的制造工序是:采用快速凝固方法(冷却率不低于 10 000 ℃/s)将熔化的 Mg 合金制备成合金粉末,合金粉末平均直径最好不超过 100 μm;再采用脉冲电流加压烧结方法将合金粉末烧 结成不低于理论密度 90%的固体制件。脉冲电流加压烧结(如火花等离子烧结、放电烧结或等离子活化烧结方法)过程要在真空或 者惰性气体保护气氛中进行,烧结压力为 20~200 MPa,加温速率为 30~450 ℃/min,在 350~550 ℃的保温时间不超过 10 min。这种 Mg 合金可以用于制造活塞、阀门等发动机零部件。这种制备技术可以在较短的时间内制造出大尺寸、高强度的近净成型件。