变速器输入轴强度分析及其影响因素研究
汽车变速器输入轴断裂失效分析

汽车变速器输入轴断裂失效分析谢东;王方文;康人木;谭伟【摘要】某经渗碳淬火热处理的汽车变速器输入轴在行驶过程中断裂,采用断口宏微观分析、低倍酸蚀检验、硬度测试、渗碳层深度测定、金相检验、SEM断口分析及直读光谱成分分析等方法对输入轴断裂原因进行了分析.结果表明:样品断裂形式包括脆性断裂和疲劳断裂两种,断裂源均位于输入轴主副轴连接沟槽区域;样品主副轴连接沟槽区域的应力集中(机加工刀痕加剧了应力集中),是样品发生两种断裂失效形式的重要原因;行驶过程中的强受力,促进了脆性断裂失效的发生;非金属夹杂物在样品轴外表层的聚集,尤其在外表皮下的存在,加剧了应力集中,促进了断裂失效的发生.【期刊名称】《价值工程》【年(卷),期】2018(037)029【总页数】3页(P225-227)【关键词】输入轴;脆性断裂;疲劳断裂;应力集中【作者】谢东;王方文;康人木;谭伟【作者单位】德阳市产品质量监督检验所,德阳618000;四川劲威检测服务有限公司,德阳618000;德阳市重装检测有限责任公司,德阳618000;德阳市重装检测有限责任公司,德阳618000【正文语种】中文【中图分类】U463.2120 引言汽车工业已发展成为我国装备制造业的重要支柱产业。
提高汽车零部件产品质量,可有效推动汽车工业的质量竞争力指数提升[1],为发展汽车智能制造提供重要技术支撑。
某大型汽车企业生产的汽车变速器输入轴在汽车行驶过程中发生了断裂,该输入轴材质为20CrMnTiH1T,主要热处理工艺路线为900℃(±10℃)扩散渗碳+845℃(±10℃)淬火+150℃(±10℃)回火;热处理技术要求为渗碳层深度0.5-0.95mm,表面硬度720-850HV50,心部硬度260-460HV20,金相组织要求表面马氏体1-5级、心部铁素体1-4级、残余奥氏体1-5级、齿角碳化物1-4级。
据工厂技术人员反映,该输入轴运行总里程5500km左右,断裂时的汽车行驶速度50km/h左右。
自动变速器输入轴的工艺改进

自动变速器输入轴的工艺改进作者:孙哲来源:《科技资讯》 2012年第20期孙哲(宁波宏协离合器有限公司浙江宁波 315800)摘要:本文分析了一种自动变速器输入轴的工艺难点,以及机械加工过程中出现的情况,并针对这些存在的问题,通过工艺改进解决,实现了产品质量提高,加工成本降低。
关键词:输入轴工艺改进等温正火中图分类号:TH242 文献标识码:A 文章编号:1672-3791(2012)07(b)-0112-02输入轴是自动变速器中机械齿轮传动机构的重要零件,它通过输入轴花键和扭转减振器连接,并将发动机的输出扭矩传递给自动变速器,要求有极长的使用寿命,设计寿命一般要达到10年30万公里不损坏,下面我们分析一种自动变速器输入轴的加工工艺。
1 输入轴的结构和技术要求1.1 输入轴的结构尺寸(图1)1. 2零件材料输入轴零件材料采用齿轮钢20CrMnTi。
1.3 技术要求(1)机加工前,锻件需经正火处理,硬度160~210HBS;(2)渗碳处理,层深0.6mm~1mm,表面硬度58~62HRC,芯部硬度35mm~42HRC。
(3)花键齿表面硬度≤50HRC。
2 原机械加工工艺分析2. 1工艺流程锻造→普通正火→精车→滚花键→滚齿→涂防渗剂→渗碳淬火→低温回火→外圆磨→磨齿2.2 工艺实施的问题(1)输入轴花键通过滚齿的方式加工,效率非常低,并且还要定做专用刀具,成本较高。
另外,零件φ240-0.1外圆距离φ210-0.1很近,在滚花键根部时,无法避免的会加工到φ24的部位,使零件的美观性降低。
(2)输入轴花键硬度较高,极易出现崩齿现象。
由于花键齿的表面硬度要求低于50HRC,造成不能直接做渗碳淬火处理,否则花键的表面硬度会和其他部位一样都是58~62HRC。
硬度太高,零件的脆性很大,在使用过程中会出现崩齿现象,因此,在热处理前,增加了一道在花键的表面涂防渗剂,这样可以有效的降低渗碳淬火后花键表面的硬度,增加它的使用寿命。
某变速箱输出轴齿轮有限元强度分析
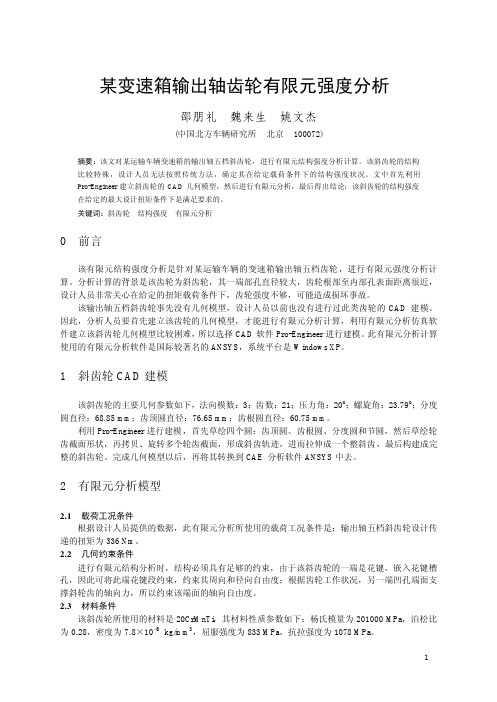
某变速箱输出轴齿轮有限元强度分析邵朋礼 魏来生 姚文杰 (中国北方车辆研究所北京 100072)摘要:该文对某运输车辆变速箱的输出轴五档斜齿轮,进行有限元结构强度分析计算。
该斜齿轮的结构比较特殊,设计人员无法按照传统方法,确定其在给定载荷条件下的结构强度状况。
文中首先利用Pro-Engineer建立斜齿轮的CAD几何模型,然后进行有限元分析,最后得出结论:该斜齿轮的结构强度在给定的最大设计扭矩条件下是满足要求的。
关键词:斜齿轮结构强度有限元分析0 前言该有限元结构强度分析是针对某运输车辆的变速箱输出轴五档齿轮,进行有限元强度分析计算。
分析计算的背景是该齿轮为斜齿轮,其一端部孔直径较大,齿轮根部至内部孔表面距离很近,设计人员非常关心在给定的扭矩载荷条件下,齿轮强度不够,可能造成损坏事故。
该输出轴五档斜齿轮事先没有几何模型,设计人员以前也没有进行过此类齿轮的CAD建模。
因此,分析人员要首先建立该齿轮的几何模型,才能进行有限元分析计算,利用有限元分析仿真软件建立该斜齿轮几何模型比较困难,所以选择CAD软件Pro-Engineer进行建模。
此有限元分析计算使用的有限元分析软件是国际较著名的ANSYS,系统平台是Windows XP。
1 斜齿轮CAD建模该斜齿轮的主要几何参数如下,法向模数:3;齿数:21;压力角:20o;螺旋角:23.79o;分度圆直径:68.85 mm;齿顶圆直径:76.65 mm;齿根圆直径:60.75 mm。
利用Pro-Engineer进行建模,首先草绘四个圆:齿顶圆、齿根圆、分度圆和节圆,然后草绘轮齿截面形状,再拷贝、旋转多个轮齿截面,形成斜齿轨迹,进而拉伸成一个整斜齿,最后构建成完整的斜齿轮。
完成几何模型以后,再将其转换到CAE 分析软件ANSYS中去。
2 有限元分析模型2.1载荷工况条件根据设计人员提供的数据,此有限元分析所使用的载荷工况条件是:输出轴五档斜齿轮设计传递的扭矩为336 Nm。
变速器输入轴断裂失效分析2

分
析
网
讨论和结论
图 6 X 射线衍射谱
材料分析结果表明,输入轴断裂属于疲劳断裂,裂纹扩展过程受到扭转疲劳应力的作用,因此结
构断裂部位疲劳强度不足是轴件断裂的基本原因。但是输入轴材料化学成分、渗层硬度和深度均符合
设计规定要求。分析看到裂纹是从油孔外侧边缘顶角开始向内扩展的,渗碳层大部分为沿晶断口, 因
max
0.3
0.25
1.45
0.65
0.035
微观断口分析
截取断口试样,清洗后在扫描电镜下观察断口形貌,如图 2 和图 3 所示。断裂起始于油孔处边缘
网 顶角,沿轴的环向扩展并最终断裂形成台阶,扩展方向如箭头所指。可以看到,起裂边缘存在明显的
飞边,起裂位置呈尖锐角状。断裂起始源区表面部分被磨损,但仍可以看到孔边缘的尖角。检查断面 微观形态可以看出,边部渗碳区断口主要为沿晶断口,中部裂纹扩展区为穿晶疲劳断口,汇合台阶区
记录号:JS-AL-转动设备(轴和外壳)-094
变速器输入轴断裂失效原因分析
摘要:试样为经过表面渗碳处理的变速器输入轴的断裂件,是在安装后和运行过程中发生断裂的。通
中过宏观分析、材料化学成分分析、微观断口分析以及残余奥氏体检测,结果表明:油孔边缘存在飞边 产生较大应力集中和渗碳层组织存在晶界弱化是导致轴件疲劳断裂的主要原因。建议油孔外边缘进行 倒角和局部进行感应回火软化。 关键词:变速器;输入轴;疲劳断裂;应力集中;渗碳层组织;晶界弱化 国 材料种类/牌号:合金工具钢/SCM920HVSI 概述 试样为经过表面渗碳处理的变速器输入轴的断裂件,是在安装后和运行过程中发生断裂的。 应 变速器输入轴材料是 SCM920HVSI,要求渗碳后表面硬度大于 650HV,渗层硬化深度 0.4~0.7mm, 渗层中参与奥氏体含量 10~20%。 对试件断裂失效原因进行了分析。 急 测试过程与结果 宏观分析 送检的变速器输入轴断裂件和完整件的宏观形貌如图 1 所示,断裂位置如图中箭头所指,处于输 分 入轴与螺母连接一端的加工螺纹和花键齿之间的过渡区,断面与试件轴向并非垂直,而是呈一定角度, 看来导致断裂的应力除弯曲应力外,还有较大的扭力分量。断面恰经过该位置的油孔平面,仔细观察 可以看出裂纹是从油孔外边缘开始向内扩展的,裂纹扩展方向如图中箭头所示,在从两边分别向下扩 析 展的汇合处形成台阶。断口呈深灰色,断面相对平坦,部分已被磨损得断裂面呈光亮色。 网
汽车变速器输入轴断裂失效分析

汽车变速器输入轴断裂失效分析作者:谢东王方文康人木谭伟来源:《价值工程》2018年第29期摘要:某经渗碳淬火热处理的汽车变速器输入轴在行驶过程中断裂,采用断口宏微观分析、低倍酸蚀检验、硬度测试、渗碳层深度测定、金相检验、SEM断口分析及直读光谱成分分析等方法对输入轴断裂原因进行了分析。
结果表明:样品断裂形式包括脆性断裂和疲劳断裂两种,断裂源均位于输入轴主副轴连接沟槽区域;样品主副轴连接沟槽区域的应力集中(机加工刀痕加剧了应力集中),是样品发生两种断裂失效形式的重要原因;行驶过程中的强受力,促进了脆性断裂失效的发生;非金属夹杂物在样品轴外表层的聚集,尤其在外表皮下的存在,加剧了应力集中,促进了断裂失效的发生。
Abstract: A carburizing and quenching heat-treated automotive transmission input shaft breaks during driving, the cause of the input shaft fracture is analyzed by means of fracture macroscopic analysis, low-level acid corrosion test, hardness test, carburized layer depth measurement,metallographic examination, SEM fracture analysis and direct reading spectral composition analysis.The results show that the fracture forms of the sample include brittle fracture and fatigue fracture. The fracture sources are located in the main and auxiliary axis connecting groove region of the input shaft;the stress concentration of the sample primary and secondary shafts connected to the groove region (machined tool marks exacerbate the stress concentration) is an important reason for the two failure modes of the sample; the strong force during driving promotes the occurrence of brittle fracture failure; the accumulation of non-metallic inclusions on the outer surface of the sample shaft, especially under the outer skin, exacerbates stress concentration and promotes fracture failure.关键词:输入轴;脆性断裂;疲劳断裂;应力集中Key words: input shaft;brittle fracture;fatigue fracture;stress concentration中图分类号:U463.212 文献标识码:A 文章编号:1006-4311(2018)29-0225-03汽车工业已发展成为我国装备制造业的重要支柱产业。
汽车变速箱输入轴加工夹具的缺陷分析与优化改造
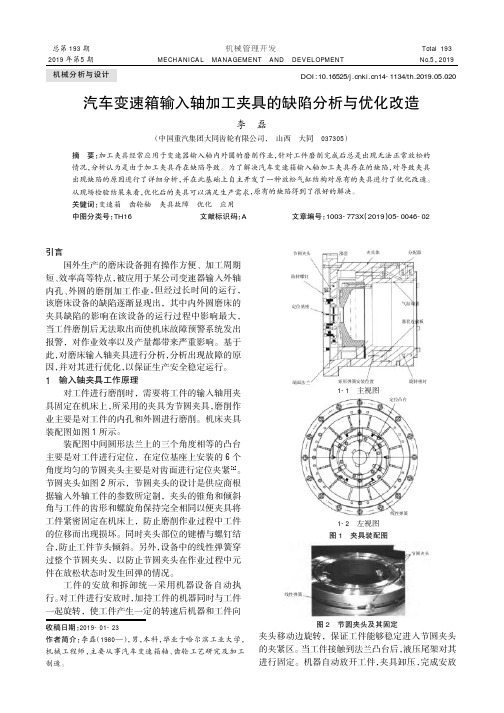
2019 年第 5 期
李磊:汽车变速箱输入轴加工夹具的缺陷分析与优化改造
· 47 ·
工序。由于实际产过程中所使用的工件普遍较长,为 了保证工件磨削时仍然能够保持夹紧稳定状态,采 用了三爪托架对工件进行支撑。尾夹顶尖和三爪托 架如图 3 所示。对工件进行磨削作业完成后,需要对 工件进行下料操作。下料作业主要还是通过压缩机 进行加压,将压缩空气充入夹具内部,工件与夹具分 离,使工件处于放松状态,此时的三爪托架退出,用 机器将工件取出。
机床的稳定位置,夹具上原有的其他设备均保持不
变。放松气缸在工件磨削过程中不会随着转动且放
松气缸的运动距离设置为 6 mm,远大于涨套连接板
的位移,在工件磨削、夹具体旋转时不会与周围其他
元件接触[2]。
圆柱推销
压缩弹簧 活塞Leabharlann 图 4 放松气缸装配示意图
总第 193 期 2019 年第5 期
机械分析与设计
机械管理开发 MECHANICAL MANAGEMENT AND DEVELOPMENT
Total 193 No.5,2019
DOI:10.16525/14-1134/th.2019.05.020
汽车变速箱输入轴加工夹具的缺陷分析与优化改造
工件的安放和拆卸统一采用机器设备自动执 行。对工件进行安放时,加持工件的机器同时与工件 一起旋转,使工件产生一定的转速后机器和工件向
收稿日期:2019-01-23 作者简介:李磊(1980—),男,本科,毕业于哈尔滨工业大学,
机械工程师,主要从事汽车变速箱轴、齿轮工艺研究及加工
制造。
节圆夹头 防转螺钉 定位基座
的分配器主要是为了对定位夹紧的工件进行卸压作
业,即使不采用分配器仍然能够完成,因此,仅从夹
变速器传动效率的影响因素与提升策略研究进展

变速器传动效率的影响因素与提升策略研究进展传动系统是汽车的关键组成部分之一,而变速器则是传动系统的核心。
变速器的传动效率直接影响到汽车的燃油经济性、驾驶舒适性和动力性能。
因此,研究变速器传动效率的影响因素及提升策略对于汽车工业具有重要意义。
一、影响变速器传动效率的因素1. 齿轮副摩擦力:齿轮副摩擦力是影响变速器传动效率的主要因素之一。
齿轮副摩擦力由于润滑油品质、温度、压力等因素的影响而产生变化。
合理选择润滑油品和优化润滑系统设计是降低齿轮副摩擦力的关键。
2. 齿轮副磨损:齿轮副磨损直接影响到传动效率。
齿轮的磨损主要包括微观接触疲劳、表面磨损和齿轮啮合误差等。
提高齿轮材料的硬度、减小齿轮啮合误差和合理设计齿轮的几何形状都可以降低齿轮副磨损,提高传动效率。
3. 润滑油粘度:润滑油的粘度会影响到变速器的传动效率。
过高或过低的润滑油粘度都会增加齿轮副的摩擦力和磨损程度,降低传动效率。
因此,选用适合的润滑油粘度是提高变速器传动效率的重要措施。
4. 轴承摩擦力:轴承的摩擦力也是影响变速器传动效率的重要因素之一。
合理选择轴承材料、润滑方式和减小轴承径向间隙都可以降低轴承摩擦力,提高传动效率。
二、提升变速器传动效率的策略在研究变速器传动效率的过程中,学者们提出了一系列的策略来提高传动效率。
1. 优化齿轮设计:通过改进齿轮的几何形状、材料和精度等方面来降低齿轮副的摩擦和磨损,提高传动效率。
2. 优化润滑系统:合理选择润滑油品、优化润滑油供应系统,以降低齿轮副的摩擦力和磨损,提高传动效率。
3. 应用液力变矩器和双离合器:液力变矩器和双离合器等新型传动技术能够降低传动时的能量损失,提高传动效率。
4. 研发新型材料:通过研发新型材料,提高齿轮和轴承等零部件的强度和硬度,降低磨损和摩擦力,提高传动效率。
总之,变速器传动效率的影响因素众多,研究者们通过优化设计、改进润滑系统和研发新材料等手段,不断提升传动效率,以满足汽车工业对于燃油经济性和驾驶舒适性的要求。
变速器装配线上轴承压装问题分析

变速器装配线上轴承压装问题分析作者:杨景璐陈源来源:《科技风》2017年第06期摘要:在研究汽车变速器装配过程中的质量控制时,要了解其变速器装配生产线上质量控制的重要控制变量及其过程,并分析其轴承压装的过程和控制变量的特性,在了解其应用的原理后进行应用分析。
对于汽车变速器装配生产线上的轴承压装问题进行研究,提高其变速器的装配质量。
关键词:变速器;装配线;轴承压装;分析在我国汽车生产的市场中,生产变速器的企业众多,而且其上生产线都配有进行汽车变速器性能的试验台,变速器一旦装配完成就要送到其试验台内,及时进行性能指标的合格测试,通过测试就会直接出厂,如果不合格就要返修。
汽车变速器类似这样的性能测试是必须要进行的,但其生产企业大多只是单纯的依靠这样的性能测试来检查汽车变速器的出厂质量,在生产装配环节不会进行检查着手,因此,在装配线上对其轴承压装问题进行分析,可以有效的提高其装配质量,实现变速器的质量控制。
一、变速器装配线上轴承压装(一)变速器及其轴承压装作为汽车传动系统中非常重要的组成部分,变速器的齿轮是其内部的最主要的一个元件,因此对其装配的精度就直接影响着变速器的性能和寿命。
在压装机上主要完成的是齿轮和主轴的装配,在压装机的设计制造就要尤其注重其精度。
对于压装装配的研究,国内学者主要的研究是单一压装机机身的有限元和关键零件的压装质量控制和工艺研究等问题。
而因为压装机是一种非标设备,所以不同的压装对象就有不同的压装机的设计参数[ 1 ],并没有一定的设计规范。
关于压装机的系统理论研究不多,也缺乏足够的理论支持。
(二)变速器轴承压装系统结构及原理1.压装系统的组成部分压装系统的主要组成部分就是机械系统和液压系统。
机械系统中主要有线体、顶板、弯板、升降小车、夹紧装置、顶升油缸、压装油缸。
而液压系统的主要组成是顶升油缸回路和推进油缸回路。
2.压装系统的工作原理轴承压装有这样的工作原理:运用轨道小车,完成变速器箱体到压装机工作位置的转移,再用顶升油缸进行举升,结合定位装置,保证轴承孔轴线、压装油缸轴线位置平行且固定。
- 1、下载文档前请自行甄别文档内容的完整性,平台不提供额外的编辑、内容补充、找答案等附加服务。
- 2、"仅部分预览"的文档,不可在线预览部分如存在完整性等问题,可反馈申请退款(可完整预览的文档不适用该条件!)。
- 3、如文档侵犯您的权益,请联系客服反馈,我们会尽快为您处理(人工客服工作时间:9:00-18:30)。
【摘要】输入轴是变速器中机械齿轮传动机构的重要零件之一,其工作时承受弯矩和扭矩。
文章建立了某变速箱齿轮传动机构的模型,运用MASTA软件对输入轴进行了仿真分析,确定了输入轴承受较大应力的位置,并通过改变输入轴的设计结构,研究输入轴结构对轴的强度分析的影响因素。
结果表明,输入轴强度在结构设计上受多种因素影响,其中影响较大的因素为壳体刚度、轴过渡圆角设计和轴盲孔深度设计。
【关键词】输入轴;强度分析;MASTA;仿真分析【中图分类号】U463.212【文献标识码】A【文章编号】1674-0688(2019)04-0040-040引言输入轴是手动变速器齿轮传动系统中的重要零件之一。
输入轴通过其前端的花键与离合器从动盘花键连接,将发动机的输出扭矩传递给各级齿轮组和其他部件后传递至汽车车轮,使汽车能够正常行驶。
变速器的输入轴承受循环载荷,在工作时承受扭矩和弯矩,不仅要具备足够的强度和刚度,还要在设计过程中保证在最大载荷下有足够的疲劳安全系数,否则会出现输入轴强度不足、断裂或轴耐久疲劳失效导致的手动变速器无法换挡等问题,因此对变速器输入轴进行强度分析具有重要意义[1]。
本文主要使用传动系统运动分析软件MASTA建立变速器输入轴的运动仿真模型,对输入轴上各位置承受的应力进行分析,从而确定输入轴承受最大应力的位置,并通过改变输入轴的设计结构,研究输入轴结构对轴的强度分析的影响因素,进而总结出输入轴强度分析结果和结构因素及其贡献量。
1输入轴强度分析校核指标本文在MASTA软件中采用SMT方法进行轴类强度分析。
MASTA软件中轴类强度分析校核指标较多,按类型划分为位移量类、变形量类、应力值类、力矩值类、安全系数等。
本文采用疲劳安全系数、径向变形、弯曲应力3项指标进行分析。
1.1疲劳安全系数在MASTA软件中,安全系数(Safety Factor,SF)的定义为在所选工况或载荷谱完成后预测的轴离失效的接近程度。
安全系数大于1,表明轴在本载荷谱下不会失效;安全系数小于1,表明轴在本载荷谱下会失效。
在手动变速器设计过程中,当输入轴的疲劳安全系数大于1时,才能满足设计要求。
1.2径向变形径向变形(Radial Deformation,RD)指的是轴类零件的轴线在其轴截面的半径方向上的偏移量。
当输入轴发生径向变形时,轴线形状发生改变。
这将引起轴上齿轮错位,过大的错位将会使得齿轮间不能正常啮合,容易影响输入轴寿命及与其啮合的齿轮的寿命,并会产生传动系统运转不平稳进而产生NVH问题。
1.3弯曲应力弯曲应力(Bending Stress,BS)指的是轴类零件或梁类零件在承受纵面的横向弯矩或其他载荷时,其横截面上产生的应力。
其中,垂直于截面的应力称为正应力,在横截面内的应力称为切应力[2]。
弯矩产生的正应力是影响强度和刚度的主要因素,以下主要对弯曲正应力进行分析。
弯曲应力其最大值发生在壁厚的表面处,设计时一般取最大值进行强度校核。
本文研究的变速器输入轴属于转轴,既承受与传递发动机扭矩,也承受来自轴承及齿轮所给予的横向力,受力工况较为复杂。
当输入轴弯曲应力超过其材料许可应力极限时,输入轴将会发生失效,影响变速器正常工作。
2变速器输入轴强度分析2.1建立输入轴仿真分析模型本文使用传动系统运动仿真软件MASTA建立了变速器的运动仿真模型。
在变速器总成组件里依次进行轴、齿轮副和同步器组件的建模,再从轴承库里选用各类轴承进行合理装配,对于壳体或差速器此类异形件使用有限元导入的方法完成建模。
最终搭建好的手动变速器的MASTA仿真模型如图1所示。
2.2仿真模型功率流分析仿真模型建好后,进行功率流分析,以检查模型的准确性[3]。
在变速器设计中,对前进挡而言,一挡速比最大,输出转速最低且输出扭矩最大。
故一挡100%扭矩工况下,一挡齿轮所传递扭矩最大,齿轮的啮合力最大,对于输入轴的考验也最大。
因此,本文采用一挡100%扭矩工况对变速器输入轴进行强度分析。
变速器输入轴强度分析及其影响因素研究黄德健1,杨晓彤1,陆凌云1,刘奕驿2,潘琦林2(1.上汽通用五菱汽车股份有限公司,广西柳州545007;2.武汉理工大学,湖北武汉430000)【作者简介】黄德健,男,广西河池人,本科,上汽通用五菱汽车股份有限公司技术中心工程师,从事变速器开发工作。
2.3输入轴应力分析为了识别出输入轴应力集中处,需要进行系统应力分析。
通过系统应力分析,可以得到系统中各部件在运行时的受力情况。
将运行工况设置为一挡100%扭矩工况,进行系统受力分析,得到输入轴各处的受力情况(如图2所示)。
观察图2可知,输入轴中间轴段承受的应力最大,如图3中A点处应力为257.5MPa,B处应力为218.9MPa,这两处最容易发生失效与破坏。
因此,本文着重研究A、B处,改变输入轴的结构参数,从疲劳安全系数、径向变形、弯曲应力3个指标进行对比分析,得到对输入轴的受力变形影响较大的因素。
3变速器输入轴强度影响因素研究3.1壳体对输入轴强度的影响图1表示含有变速器壳体的有限元仿真模型,其壳体的刚度根据设计阶段的实际数值设定。
在变速器实际工作时,壳体因受到悬置、变速器齿轮组及轴承的作用力而产生变形,导致轴承产生径向或轴向位移,输入轴的中心线产生偏移,影响轴上齿轮的正常啮合,进而导致输入轴产生变形。
为了更加直观地研究变速器壳体刚度对输入轴的影响,将图1中的变速器壳去掉,则MASTA会将原本安装在壳体轴承座上的外圈固定在软件设定的模拟地面上,相当于在图1的模型中将变速器壳体的刚度设置为无穷大[3]。
对此模型进行系统应力分析,计算输入轴的疲劳安全系数、径向变形、弯曲应力,并与在有壳体情况下的计算结果进行比较,得到变速器刚度大小对输入轴的几个指标的影响。
计算结果如图3所示。
由图3可知,使用壳体刚度无限大的变速器仿真模型计算,相对于有壳体的仿真模型,输入轴的疲劳安全系数有稍微减小,弯曲应力基本没有变化,而A、B处的径向变形明显降低。
这说明变速器壳体的刚度对输入轴的径向变形影响较大,对疲劳安全系数、弯曲应力影响较小。
3.2轴过渡圆角对输入轴强度的影响在轴的截面变化处(如台阶、横孔、键槽等),会产生应力集中,引起轴的疲劳破坏。
考虑此输入轴的A、B两处均为截面变化处,以下将分析A、B两处的过渡圆角的大小对输入轴的疲劳安全系数、径向变形、弯曲应力的影响。
按《机械设计手册》第5版第2卷要求:轴截面的过渡圆角与轴端直径比r/d>0.1。
分析原A处圆角为4mm,B处圆角为5mm,在满足设计要求的前提下改变过渡圆角的大小,具体分析方案见表1。
对修改圆角大小的仿真模型进行系统受力分析,并与原始模型进行比较,比较结果如图4所示。
由图4可知,轴端面的过渡圆角大小对轴的安全系数及弯曲应力有显著的影响。
当r/d的比值小于0.1时,A处安全系图1变速器仿真模型图2输入轴在1挡100%工况下的受力情况图3有/无壳体输入轴疲劳安全系数、轴径向变形与弯曲应力对比序号分析位置分析状态圆角半径r(mm)轴小端直径d(mm)r/d值1A处原状态4250.16增大圆角6250.24减小圆角2250.082B处原状态5250.2增大圆角8250.32减小圆角2250.08表1轴过渡圆角与轴小端直径比值分析方案数降低9.11%,弯曲应力增加10.3%。
B处安全系数降低24.93%,弯曲应力增加34.3%。
圆角大小对于轴的安全系数影响较大的原因:当圆角很小时,应力集中现象将位于大、小轴段相交处附近,随着圆角半径的增大,应力集中部位由底部向相交处两侧转移,应力随之减少[4]。
但是无论增大还是减小圆角,对于A、B处的径向变形影响较小。
3.3输入轴尾部盲孔孔径与通孔方案对输入轴强度的影响本文研究的变速器输入轴后端有一长段盲孔设计。
盲孔设计既可以减轻输入轴的单体质量,也可以作为润滑油路的通路。
盲孔末端螺栓带有通孔,变速器油液可以从螺栓通孔处进入盲孔,再通过轴上的径向油道对轴上零件如滚针轴承等进行润滑。
以下分析盲孔孔径大小及将盲孔更改为通孔这种设计方案对输入轴疲劳强度的影响。
一方面,本文原模型中的输入轴后端盲孔孔径为14mm,改变孔径的大小,如分别减小2mm和增大2mm,考虑盲孔孔径大小对输入轴的几个分析指标的影响。
另一方面,在轴前端设计沿轴向的孔径为6mm的内孔,与输入轴后端的盲孔相连,考虑轴前端有无通孔对输入轴几个分析指标的影响。
对于这两种方案,分别重新计算输入轴的疲劳安全系数、径向变形、弯曲应力,再与原模型的计算结果进行对比,分析结果如图5所示。
由图5可以看出,与原模型相比,增大或减小输入轴后端盲孔孔径大小及在前端设孔这两类设计方案对输入轴A处的疲劳安全系数、径向变形、弯曲应力影响很小。
对输入轴B处,减小轴后端的孔径,其疲劳安全系数相对于原模型有明显的减小,弯曲应力略有增大,其他指标数值变化不大。
在输入轴前端设计6mm的内孔,除疲劳安全系数略有减小,其他指标数值基本不变。
3.4输入轴尾部盲孔孔深对输入轴强度的影响为了更加全面地研究输入轴尾部盲孔对其疲劳破坏指标的影响,在盲孔孔径大小保持不变的前提下,将盲孔的深度分别增加20mm和减少20mm,即将孔的位置左偏移20mm和右偏移20mm。
对新的模型重新运用MASTA软件进行分析计算,再与原模型进行对比,分析结果如图6所示。
由图6可以看出,与原模型比较,增大或减小输入轴尾部孔的深度,对于输入轴A处的疲劳安全系数、径向变形、弯曲应力几乎没有影响。
对于输入轴B处,尾部孔深度增加20mm,其疲劳安全系数相对于原模型明显减小,由原先的1.93减小为1.72,降低10.6%。
此外,弯曲应力也有明显增大,由原先的210.8MPa增加至233.6MPa,增加10.8%。
从结构上分析,如果盲孔过深且向左超过B处轴径大端端面,在B处产生的直径差达到1.66(根据《机械设计手册》第5版第2卷,对于阶梯轴,推荐直径差D/d<1.15~1.2,其中D为大端轴径,d为小端轴径),则在B处容易产生应力集中现象,导致弯曲应力变大而安全系数变小。
而输入轴尾部盲孔的深度减小20mm,对几个分析指标的影响较小。
图4轴过渡圆角对输入轴安全系数、径向变形和弯曲应力影响图5盲孔径对输入轴安全系数、径向变形和弯曲应力影响图6盲孔深度对输入轴安全系数、径向变形和弯曲应力影响4结论本文使用MASTA软件建立了变速器输入轴的运动仿真模型,结合变速器在疲劳测试过程中的实际负荷工况,对该变速器输入轴进行了强度分析,通过考核疲劳安全系数、径向变形和弯曲应力3个指标,确定了输入轴承受应力较大的部位,同时研究了结构因素对输入轴强度的影响及贡献量,得出了以下结论。
(1)变速器壳体的刚度、轴过渡圆角设计、轴盲孔深度设计是对输入轴强度影响较大的结构因素。