损伤容限设计思想及分析方法综述
第八章-复合材料结构耐久性损伤容限设计4-3

课题第八章复合材料结构耐久性损伤容限设计(三)目的与要求提高零部件耐久性/损伤容限的特殊设计方法和材料使用因素损伤容限分析和疲劳特性概述了解耐久性/损伤容限设计实例复合材料制件的疲劳特性分析方法重点损伤容限分析和疲劳特性概述复合材料制件的疲劳特性分析方法难点复合材料制件的疲劳特性分析方法教具复习提问耐久性/损伤容限设计的特点是什么?复合材料制件的疲劳特性分析方法有哪些?新知识点考查损伤容限分析和疲劳特性布置作业课堂布置课后回忆损伤容限分析和疲劳特性?复合材料制件的疲劳特性分析方法有哪些?备注教员1.提高零部件耐久性/损伤容限的特殊设计方法1.1.损伤的极限1.1.1通常损伤程度●碳纤维复合材料存在缺陷/损伤时,因其强度下降时可能高达60%左右,因此按照损伤容限设计的结构厂采取较低的许用值进行控制,一般情况不超过4000μξ。
●零部件强度的下降必定导致系统性能的下降,设计过程中使用的降低了的许用值,必定不能充分发挥材料的最大性能,不但影响了设计的效率,而且给工艺制造过程和质量控制造成过大的裕度和能源浪费。
1.1.2当前的设计目标●为了充分发挥复合材料的潜在优势,近年来国内外提高了损伤容限,也提高设计许用值。
●从最初设计阶段、工艺制造过程和质量控制方面综合考察,要求设计许用值达到6000μξ。
●根据国外的相关报道,经过数年的科研工作,在飞机设计方面采用的复合材料构件已经达到上述要求。
✧机翼结构设计的拉、压设计许用应变值提高到6000μξ;✧剪切应变值提高10000μξ。
1.1.3设计思想●提高结构的抗损伤能力✧抑制损伤的形式;✧减少损伤范围,如减少冲击的区域;✧抑制或阻止损伤进一步发生。
●提高结构包容损伤的能力✧提高复合材料结构受损后的剩余强度和疲劳强度/疲劳寿命;✧采用更先进的复合材料成形技术,增加制件自身的性能;✧使用强度更高的体积材料和增强材料,保证“原材料”的性能;✧采用合理的浸润工艺,提高界面相的性能。
第07讲:损伤容限设计基本概念、原理和方法

25
破损安全止裂结构
破损安全止裂结构是在安全 破坏前使裂纹不稳定快速扩展停 止在结构的某一连接区域内而设 计和制造的结构。 该结构通过残存结构中的缓慢裂 纹扩展和在后续检查中觉察损伤 来保证安全。 一般结构采用多个元件组成,适 当安置止裂带。 这种设计概念对于较长较大的构 件常考虑采用.加筋板是这种结 构的典型代表。
17
要求全尺寸损伤容限试验的结构
对一架新研制的飞机,通常全尺寸损伤容限试验的结构项 目包括(不限于如下项目) ① 机身气密舱 ② 机身与机翼的结合部 ③ 发动机架或接头 ④ 前缘襟翼 ⑤ 后缘襟翼与副翼 ⑥ 机体结构的大型锻件 ⑦ 前起落架部件 ⑧ 主起落架部件 ⑨ 全机,带一段机身的机翼,带一段机翼和一段尾翼的机身
分散系数
4-7
2
S-N曲线 理论基础
疲劳累积损伤理论
线弹性断裂力学
6
疲劳安全寿命设计和损伤容限设计对比
a1:安全寿命终结点的宏观可检裂纹;a2 :外场检测手段能测定的裂纹尺寸; a0 :损伤容限设计起点的初始裂纹尺寸;acr—不稳定扩展的临界裂纹尺寸。
7
疲劳安全寿命设计和损伤容限设计对比
均是在不同意义上解决结构的使用寿命设计及飞机安全问题,
针对不同的结构类型、裂纹形式和可检查度有不同的初始 裂纹尺寸。
39
表面结构一般为可检结构,可考虑设计成破损安全结构.内 部结构当为不可检结构时,应设计成缓慢裂纹扩展结构.
易更换的结构容易实现破损安全设计;不易更换的结构以采 取缓慢裂纹扩展结构为宜。
3.3飞机结构损伤容限分析

= KI
r
π
gi( I ) (θ )
,σ y = KI 2πr ,τ xy = 0
裂端正前方: θ = 0, σ x = 裂纹表面:
KI 2πr
θ = π , σ x = 0,σ y = 0,τ xy = 0
15
1.裂纹尖端应力应变场和应力强度因子
σ
(I ) ij
应力场公式的特点: 1)在裂纹尖端,即r=0处,应力趋于无穷大,应力在裂纹尖端 出现奇异性。 2)应力强度因子KI在裂纹尖端是有限量。 3)裂纹尖端附近区域的应力分布是r和θ的函数,与无穷远处的 应力和裂纹长度无关。 可以看出,用应力作为参量来建立如传统的强度条件失去了意 义。但应力强度因子是有限量,它不代表某一点的应力,而是 表征裂端应力应变场强度的参量。所以KⅠ 可作为参量建立破 坏条件是恰当的。强调:因KⅠ 由线弹性理论推出,所以一般 只适用于线弹性材料的断裂。由此建立起来的理论称为线弹性 断裂力学。
把握好含裂结构的裂纹的基本特性--断裂力学
6
2断裂力学基础
断裂力学概念 以含裂体的特征参数(几何、载荷)表征其内力、形变规律, 研究含裂体剩余强度规律及破坏准则, 包括交变载荷作用下 的裂纹演变规律及寿命估算分析等。
7
裂纹 按裂纹的几何特征分类
8
裂纹
按裂纹的力学特征分类
1型(张开型): 承受与裂纹面垂直的正应力σ, 裂纹面位移沿y方向,裂纹张开。 2型(滑开型): 承受xy平面内的剪应力τ, 裂纹面位移沿x方向,裂纹面沿x方向滑开。 3型(撕开型): 承受是在yz平面内的剪应力τ, 裂纹面位移沿z方向,裂纹沿 z方向撕开。
23
3.裂纹尖端塑性区
前面曾提到,根据弹性解,在裂纹尖端处应力趋于无 穷大,而实际上这是不可能的。事实上,当应力超过屈服 应力时,必然在裂纹尖端邻近区域产生塑性变形,从而使 裂纹尖端区的应力松弛,不可能达到无限大。应该说,材 料一旦屈服,就不遵从弹性规律,故线弹性断裂力学不适 用于屈服区。但如果屈服区很小(高强度、低中韧性材料 即如此)则其周围的广大区域仍是弹性区,经过必要的修 正后,线弹性断裂力学分析仍然有效。 那么如何就塑性区影响进行修正呢?
结构损伤容限分析
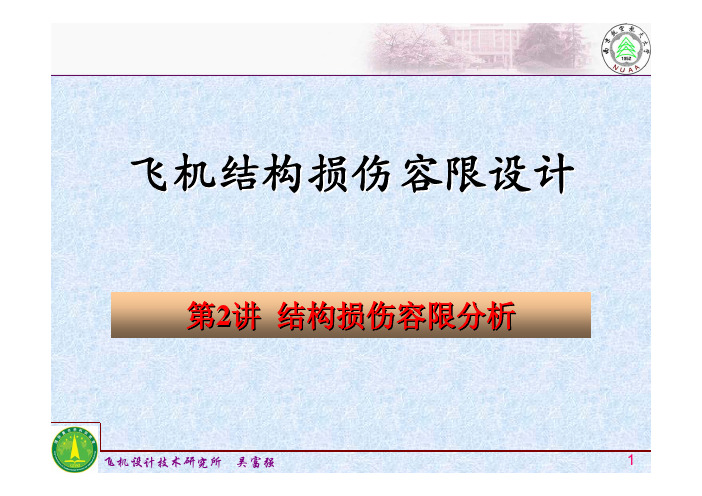
飞机结构损伤容限设计第2讲结构损伤容限分析内容概要1.损伤容限结构定义2.分析目标3.分析要素4.破坏准则5.分析流程损伤容限结构:容许结构存在一定限度的损伤,并依靠检查来保证安全服役的结构。
实践和分析都表明:把结构设计成能承受定量损伤并实施计划检查的损伤容限结构,是提高装备安全水平的有效途径。
结构损伤容限分析目标:通过损伤容限技术分析,可以准确定量评估结构的剩余强度、裂纹扩展寿命以及它们的可靠程度,并制定结构安全裂纹扩展寿命,即检查周期,保证结构在服役期内的安全。
组成结构损伤容限特性有三个同等主要的因素:损伤检测:结构检查部位、各种检查方法及检查间隔的选择;裂纹扩展:在该结构部位的载荷谱和环境谱作用下,裂纹从初始假设尺寸至某一确定尺寸之间的裂纹扩展期;临界裂纹尺寸:在剩余强度要求载荷下,结构允许存在的最大损伤;或在某一规定的损伤情况下,要求结构剩余强度能力大于对该结构的剩余强度要求值。
4 破坏准则结构损伤容限分析中的破坏准则:开裂结构的剩余强度(σS )、承载能力随裂纹长度的增长而单调下降,当结构剩余强度降低到使用载荷历程中的最大应力水平时,结构便会发生断裂破坏。
()max S C S K f a σσσ=⎧⎨=⎩求临界尺寸a cr 下的疲劳寿命N C求可检裂纹尺寸下的疲劳寿命N D确定结构类型计算裂纹扩展曲线a -N 剩余强度降曲线σS -N9GJB776-89规定;9破损安全结构;9缓慢扩展型。
确定未修使用期PUSU=N C -N DN C -N D ≥MPUSU符合规定,结束9结构材料;9a 0, a cr ;9裂纹扩展模型。
9断裂力学;9传力结构类型;9临界强度等。
9设计要求规定断裂应力。
9可检规范;9不可检结构,按”出厂时间”或“第1次飞行时间”;9制定检测周期。
9由标准文件给出最小未修使用期。
1. 裂纹扩展曲线a-N 图2. 结构强度降曲线σS -N 图3. 未修使用期示意图。
09_损伤容限设计

飞机结构损伤容限设计第9讲损伤容限设计内容概要1.损伤容限设计内容2.损伤容限结构类型3.损伤容限设计一般流程4.损伤容限设计要点5.损伤容限设计措施损伤容限设计技术的总目标:保证含裂纹结构在规定的未修使用期内,其承载能力不小于在这个期间可能遭遇到的最大载荷,从而使飞机结构不会因裂纹存在而发生灾难性破坏,保证飞机结构的安全。
飞机损伤容限设计内容:初始裂纹尺寸假设临界裂纹长度问题剩余强度问题裂纹扩展寿命问题设计方法论初始裂纹尺寸假设:新飞机出厂时,或已服役飞机经返修后可能预先存在于结构中的最大初始裂纹。
临界裂纹长度问题:在可能遭遇到的最大载荷作用下,允许结构存在的最大裂纹长度。
剩余强度问题:一个含裂纹结构在规定寿命期或检修期内要承受的可能遭遇到的最大载荷。
裂纹扩展寿命问题:从初始裂纹尺寸扩展到最大允许裂纹尺寸经历的寿命时间。
设计方法论:如何进行合理的结构设计、应力设计、材料选择、疲劳增强措施选择,规定适当的检修周期以满足结构损伤容限要求。
根据国军标GJB776-89的规定,按照损伤容限要求设计的结构分为两大类:缓慢裂纹扩展结构破损安全结构1) 破损安全多途径传力结构2) 破损安全止裂结构缓慢裂纹扩展结构使用环境中,结构缺陷或裂纹不允许达到不稳定扩展规定的临界尺寸,并在可检查度确定的规定使用期内,由裂纹缓慢扩展保证安全。
同时,在未修使用期内,带有亚临界裂纹的结构强度和安全性不应降到规定的水平以下。
破损安全多途径传力结构采用一个或多个元件组成的成段设计和制造的结构,来抑制局部损伤,以防止结构完全损坏,在后续检查以前,由剩余结构的裂纹缓慢扩展来保证安全,在未修使用期内不允许结构强度和安全性下降到规定水平以下。
破损安全多途径传力结构又分为两类:9多途径传力独立结构设计时,在多于一条传力途径的某个结构位置上不会存在由装配或制造过程引起的共同开裂源。
9多途径传力非独立结构设计时,在几个相邻传力途径的某个结构位置可能存在由装配或制造过程产生的共同开裂源。
耐久性损伤容限设计简介

年代这 ,0 年中继疲劳定寿发展起来的一种设计 思想。它是用疲劳设计定寿,用损伤容限设计保 证安全。二者 都 是 用 损 伤 容 限 设 计 概 念 保 证 安 全,不同的是,前者是建立在断裂设计概念的耐 久性定寿,后者是建立在疲劳设计概念的疲劳定 寿。可以说前者耐久性定寿是后者疲劳定寿的发 展和完善,后者疲劳定寿是前者耐久性定寿的基 础和原始阶段。两者不同之处见表 , 。
人员进一步认识到疲劳设计还远不能保证安全, 从而又增加了以断裂力学为基础的损伤容限设计 概念。!45* 年,美国空军提出用耐久性 ( 经济寿 命) 设计概念来取代原来的疲劳 ( 安全寿命) 设计 概念,并在这一基础上提出了包括以静强度、刚 度、耐久性和损伤容限为主要内容的飞机结构完 整性大纲。在此期间,美国空、海军相继颁布了 一系列军用飞机强度规范,详见表 $ 。 我国相应颁布的军用飞机强度规范详见计的基本思想
:< :; 耐久性损伤容限设计的基本思想 ( # ) 耐久性设计基本准则 ! :I ’ ! * 式中,! :I 为使用寿命; ! * 为耐久性寿命。 ( J ) 耐久性设计基本概念 认为飞机结构在使用前 ( 在制造、加工、装 配、运输时) 就存在着许多微小的初始缺陷,结 构在载荷 ! 环境谱的作用下,逐渐形成一定长度 和一定数量的裂纹和损伤,继续扩展下去将造成 结构功能损 伤 或 维 修 费 用 剧 增,影 响 飞 机 的 使 用,此时必须进行修理 ( 经济修理) ,这种修理可 以进行若干次,直到满足使用寿命。用公式表示 为: ! :I ’ % % * #
规范内容 总则 飞行载荷 其他载荷 地面载荷 水上 飞 机 的 承 载 和操作载荷 可靠 性 要 求 和 疲 劳载荷 气动 弹 性 不 稳 定 性 振动 地面试验 飞行试验 核武器效应 文件和报告 声疲劳 飞机要求
材料力学损伤容限知识点总结

材料力学损伤容限知识点总结材料力学中,损伤容限是指材料在受到外力作用下能够承受的最大损伤程度。
了解和掌握材料的损伤容限是进行材料强度评估和工程设计的重要依据。
下面将从材料损伤的概念、分类与特点、损伤容限的评估方法等多个方面进行知识点总结。
一、材料损伤的概念材料损伤是指在材料受到外力作用下,出现内部结构的变化和性能的下降。
材料损伤可以表现为裂纹、孔洞、塑性变形、断裂等不同形式和程度的破坏。
损伤过程是材料在外力作用下发生的物理和化学变化的结果。
二、材料损伤的分类与特点1. 功能性损伤和结构性损伤:功能性损伤是指材料在使用过程中,由于物理、化学或热力学原因导致性能下降,如疲劳、蠕变等;结构性损伤是指材料在外力作用下,发生裂纹、断裂等破坏,破坏了材料的结构完整性。
2. 非可逆性损伤和可逆性损伤:非可逆性损伤是指材料在外力作用下,发生永久性变形或破坏,无法回复到原始状态;可逆性损伤是指材料在外力作用下,发生临时性变形或破坏,能够回复到原始状态。
3. 累积性损伤和集中性损伤:累积性损伤是指在材料受到多次外力作用后,损伤逐渐积累、累加;集中性损伤是指材料受到单次外力作用后,损伤集中在特定区域。
三、损伤容限的评估方法1. 经验法:通过实验测试和工程实践总结出的经验公式和规范来评估材料的损伤容限。
例如,根据材料的断裂韧性和材料强度参数来确定材料的破裂容限。
2. 理论分析法:通过建立适当的材料力学模型,应用弹性力学、塑性力学、断裂力学等理论进行定量分析,得出材料的损伤容限。
3. 数值模拟法:借助计算机软件和数值模型,对材料在外力作用下的物理过程进行模拟,根据模拟结果来评估材料的损伤容限。
四、材料损伤容限的影响因素1. 材料性质:材料的组分、原子结构、晶粒形貌、晶界及其他缺陷对损伤容限有重要影响。
2. 外力条件:外力作用的类型、大小、方向和加载速率等外力条件会对损伤容限的评估结果产生影响。
3. 环境因素:如温度、湿度、应力腐蚀等环境因素会对损伤容限产生影响。
复合材料耐久性损伤容限设计

现有的飞机金属结构耐久性/损伤容限要求,原则上也适用于复合材料结构,但由于材料特性和破坏机理的不同,对复合材料结构有一些特殊要求,相应地在结构设计和分析过程中也会有一些与金属材料不同的特点。
金属结构的耐久性/损伤容限设计分析方法以金属断裂力学为基础,主要包括:改进的疲劳设计分析方法;确定性裂纹扩展方法;概率断裂力学法。
复合材料通常采用低应变设计和损伤无扩展概念来设计。
在试验验证和设计应用时,采用积木式设计试验验证方法。
3.1金属结构与复合材料结构的不同目前飞机复合材料结构的主要形式为由单向预浸带铺叠并固化而成的层压结构。
单向带呈现强烈的正交各向异性(沿纤维方向的性能和垂直纤维方向的性能差1-2个数量级),层压结构各向异性的另一个表现是层间性能远低于其面内性能,以及其组分材料—纤维与基体力学性能的巨大差距。
复合材料的层压板的各向异性、脆性和非均质性等特点,是复合材料层压板的失效机理与金属完全不同,因而他们的损伤、断裂和疲劳性能也有很大差别。
下表概述了影响复合材料结构与金属结构疲劳和损伤容限的主要因素。
(1)结构主要的缺陷和损伤类型裂纹是金属结构的主要损伤形式。
复合材料结构的主要缺陷/损伤形式是界面脱胶、分层和低能量(特别是低速)外来物产生的冲击损伤。
冲击损伤的威胁在于当内部产生大范围基体开裂和分层时,外表面往往仍目视不可检,但其压缩承载能力已大幅下降。
(2)复合材料结构的特殊要求:冲击损伤源:在设计时必须考虑使用引起的损伤(低能量冲击损伤等)研究它对修理、维护和功能可能产生的影响,并证实外表面不易检查出的损伤不会影响其耐久性。
重复的低能量冲击,要研究重复低能量冲击对结构耐久性影响(冰雹撞击、工具掉落或由于踩踏)。
(3)缺口敏感性金属一般都有屈服阶段,而复合材料往往直至破坏时,其应力—应变曲线仍呈现线性,所以复合材料的静强度缺口敏感性高于金属。
疲劳缺口敏感性则低于金属,其疲劳缺口系数(一定循环次数下,无缺口试件疲劳强度与含缺口疲劳强度之比)远小于静应力集中系数,并且在中长寿命情况下接近于1。
- 1、下载文档前请自行甄别文档内容的完整性,平台不提供额外的编辑、内容补充、找答案等附加服务。
- 2、"仅部分预览"的文档,不可在线预览部分如存在完整性等问题,可反馈申请退款(可完整预览的文档不适用该条件!)。
- 3、如文档侵犯您的权益,请联系客服反馈,我们会尽快为您处理(人工客服工作时间:9:00-18:30)。
损伤容限设计思想及分析方法综述
1 损伤容限设计概述
1.1 损伤容限设计的技术目标
保证含有裂纹的结构在规定的未修使用期内,其承载能力不小于在这个期间可能着遇到的最大载荷,从而使机体不会由于裂纹存在而发生灾难性破坏,保证机体结构安全。
1.2 损伤容限设计内容
a. 一个含有裂纹结构在规定寿命期或检修期内要承受的可能遇到的最大载荷(剩余强度问题)
b. 在可能遇到最大载荷作用下,允许结构存在的最大裂纹长度(临界裂纹长度问题)
c. 新飞机出厂时,或已服役飞机经返修后可能预先存留在结构中的最大初始裂纹(初始裂纹尺寸假设)
d. 从初始裂纹尺寸扩展到最大允许裂纹尺寸经历的寿命时间(裂纹扩展寿命问题)
e. 如何进行合理的结构设计、应力设计、材料选择、疲劳增强措施选择,规定适当的检修周期以满足结构损伤容限要求(设计方法论)
1.3 结构损伤容限设计分类
按照损伤容限要求设计的结构可分为两大类:缓慢裂纹扩展结构和破损安全结构。
而后者又包括破损安全多途径传力结构和破损安全止裂结构。
我国军用飞机损伤容限要求在国军标GJB776-89《军用飞机损伤容限要求》中按不同类型分别作了规定。
1.4 缓慢裂纹扩展不可检结构损伤容限
有些结构设计要保证它在整个使用期内不需要修理就能满足寿命要求。
另一个用途是缓慢裂纹扩展不可检结构分析简单而且偏于安全,而判断结构是否具备破损安全条件是个复杂的问题。
所以,工程上不管结构是什么类型都作为缓慢裂纹扩展不可检结构设计。
1.5 缓慢裂纹扩展可检结构损伤容限
结构在使用中能够被检查、拆卸和更换,还可以利用结构的可检性提高它的剩余强度。
如果主受力构件在尚未达到设计要求寿命时,其剩余强度就已经下降到规定值以下,对结构进行维修更换,从而使整个结构的寿命得以延长
1.6 破损安全多途径传力结构损伤容限
破损安全多途径传力结构要求当主传力途径失效后残存结构仍能承担最小未修使用期内可能遭遇到的最大载荷。
因此,只有当结构满足如下条件时,才真正符合破坏安全多途径传力结构要求:
a. 在主传力途径失效前,要求结构能够承担在最小未修使用期内可能遭遇的最大载荷;
b. 在主传力途径失效时,残存结构必须有能力承受引起传力途径失效的载荷,再加上有断裂元件转嫁过来的载荷并考虑动载效应增量;
c. 必须有足够强的紧固件以保证将失效结构上的载荷传递到残存结构上。
1.7 破损安全止裂结构损伤容限
结构具有一定的止裂能力,加筋板可以看作是这种结构的典型特点。
1.8 损伤容限设计的一般程序
a. 确定损伤容限关键件和关键件的危险部位
b. 结构的初步审查
c. 合理选择结构材料
d. 获取应力谱或应力/环境谱
e. 获取细节应力分析结果
f . 确定剩余强度要求的最大应力
g. 考虑开裂顺序
h. 计算应力强度因子
I . 计算结构的剩余强度
j . 裂纹扩展分析
k. 判断是否满足设计要求
2 断裂力学介绍
损伤容限设计、分析及试验的理论基础是断裂力学
断裂力学典型开裂形式如下:
根据弹性力学复变函数对平面问题解答方法求得平面应力状态裂纹端距离为r,与裂纹面夹角为θ。
σx=σ√a
2r
cos
θ
2
[1−sin
θ
2
sin
3θ
2
]
σy=σ√a
2r
cos
θ
2
[1+sin
θ
2
sin
3θ
2
]
τxy=σ√a
2r
sin
θ
2
cos
θ
2
cos
θ
2σz=0
上述应力分布公式可写为一般形式:
式中:K I 为I 型裂纹的强度因子。
I K σ=
对于不是无限大板的情况引入修正系数:
裂纹尖端塑性区修正
裂纹尖端附近有一定范围会发生塑性变形,在工程上经常引入一个圆形的塑性范围。
为了避免进行弹塑性分析,将包含塑性区范围在内的有效半裂纹长度 作为半裂纹长度。
eff y
a a R '=+
σij =
K I √2πr f ij (θ)
K I =σ√παf (αW )
f (αW )=√sec παW
a eff
为裂纹区扩展方向塑性区的中心长度。
平面应力状态塑性变形区的范围可表示为:
2
1
I y s K R σπ⎛⎫= ⎪⎝⎭
修正后的应力强度因子为:
I I K K '=
平面应力问题取c=1/2
断裂韧度
对于一定材料,当应力强度因子K 达到某一临界值c K 时,断裂随即发生。
c K 为材料固有属性,它是衡量材料抵抗裂纹失稳扩展能力的度量,称为断裂
韧性。
其值可通过实验可以测得。
能量释放率
裂纹扩展时,裂纹表面积会增加,设裂纹表面能为Γ,裂纹扩展形成上、下两个新面积,故裂纹扩展单位面积所克服的表面能为2Γ。
金属材料裂纹扩展前都要产生塑性变形,这就需要消耗更多的能量。
裂纹扩展单位面积塑性变
R ′y
形消耗的能量为p U ,则裂纹扩展单位面积所需要消耗的能量用R 表示:
2p R U =Γ+
变幅载荷谱中峰值载荷排列顺序不同,裂纹扩展寿命可能会表现出较大差异,课归纳为一下几种效应:
a. 超载迟滞效应: 正的超载能明显降低超载后的裂纹扩展速率(B )
b. 负超载加速效应:负的超载能显著增加超载后的裂纹扩展速率
c. 迟滞减缓效应:正超载后加上一个负超载,使迟滞效应减弱(C )
d. 多次正超载会很显著加强迟滞效应,延长裂纹扩展寿命(D )
e. 更大的超载甚至对后续的小载荷循环达到止裂效果(E )
两种理论模型解释扩展迟滞效应:
a. 裂纹闭合理论:当受正载荷作用后,在裂纹尖端和裂纹尖端后面的区域都有塑性区压缩应力,这一压缩应力使裂纹闭合,后续载荷欲使裂纹扩展,必须先克服裂纹闭合应力才能使裂纹张开,从而降低了有效应力强度因子幅值,延缓裂纹扩展速率,产生迟滞效应。
b. 残余塑性区压应力理论:在受到正超载作用后,裂纹端附近产生一个较大的塑性区。
卸载后,塑性区内产生残余压缩应力。
当后续载荷作用时,这个残余压缩应力降低了裂纹尖端附近的有效应力强度因子幅值,从而降低裂
纹的扩展速率,产生迟滞效应。
裂纹扩展率和寿命
对于高强度合金,采用裂尖应力强度因子作为裂纹扩展驱动力。
引入K ∆ 与max K 为变数。
max min K K K ∆=-
min
max
K R K =
一般已知K ∆和R 或max K 和R 即可描述疲劳载荷。
对于K ∆存在一个门槛值,在th K K ∆≤∆时,裂纹不会扩展。
裂纹扩展的整个过程大致分为三个阶段,第一阶段在ΔK tℎ附近,裂纹扩展缓慢(约为710- mm/周);第二阶段为一斜直线,是工程上最重要的裂纹扩展区;第三阶段很短,经历的载荷循环数很少,曲线呈S 形变化。
工程上一般使用第二阶段来估算寿命。
一般曲线的表达式可表现为
(,)da
f K R dN
=∆ (,)
cr
a a
da
N f K R =∆⎰。