最新工业炉窑热损失分析
水套加热炉热效率损失原因及对策分析

图2 加热炉烟道结垢情况
热效率表示水套加热炉体系中参与热交换过程中的热能利用程度。
它的供给能量有燃料热值和空气带入热能。
它的损失能量有散热的热量和排烟带走的热量。
=[(Q-Q损)÷Q]×100%=(1-Q损/Q)×100%
式中,η为热效率,Q为燃烧产生的热量,Q
损
过程中的各种热损失。
可知,当燃烧产生热量一定时,提高热效率的因素则为降低热损失。
通过分析加热炉实际运行过程,发现导致热损耗的因素主要有以下几个方面。
3.1 燃烧器自动化程度低
靖边气田加热炉使用各集气站自用气作为燃烧燃料。
工业炉窑节能

每小时蒸发量 ≤4t/h(锅炉炉体出 70~100 1.8~2.4
口处)
表6-3 工业炉过量空气系数表
燃料种类
燃烧方式
过量空气系数
煤 煤粉
机械化加煤 人工加煤
人工调节
1.2~1.4 1.3~1.5
1.15~1.25
重油 气体燃料
自动调节 人工调节
自动调节 人工调节 喷射式调节
1.1~1.2 1.15~1.25
4~5
5~8
3~4
2~3
链条炉
1.3~1.5
8~12
10~15 0.5~2.0 0.5~1.0
抛煤机
1.3~1.4
8~12
10~15
0.5~1.0
抛煤机链条 炉
1.3~1.4
8~12
10~15
0.5~1.0
往复炉排 1.3~1.5
7~10
9~12 0.5~2.0 0.5~1.0
煤粉炉 1.15~1.25
➢ 我国工业锅炉燃料以煤为主,加上煤种供应往往不符合设
计要求,并且多数管理水平不高,因此锅炉热效率较低, 平均仅为55~60%。这也说明,工业锅炉的节能潜力较大, 平均为30%左右。
➢ 我国现有各种工业炉14万台,平均热效率为
20~30%,年耗煤炭2亿多吨。
• 工业炉由于受产品生产工艺、生产组织、炉窑构
• 5. 按炉窑结构特征又可分为隧道窑、台车
窑、室式窑、网带炉、推板窑、推杆窑、 井式炉、环形炉、立窑、辊道窑、梭式窑、 钟罩炉、池炉、坩埚炉等。
• 6. 按窑炉内气体成份又可分为真空炉窑、
氢气炉窑、氮气炉窑、氢氮混合气体炉窑。
工业炉窑节能技术
1. 燃料燃烧的合理化 2. 传热的合理化 3. 减少散热、泄漏等损失 4. 充分利用余热 5. 工业锅炉节能技术 6. 工业炉节能技术
工业炉窑热效率

工业炉窑热效率标题:工业炉窑热效率:优化能源利用的关键概述:在工业领域,炉窑是一种非常重要的设备,用于加热、熔化或加工各种物质。
炉窑的热效率是衡量其能源利用效率的重要指标。
本文将深入探讨工业炉窑热效率的意义、影响因素以及如何优化能源利用,旨在帮助读者更全面地理解和应用相关概念。
一、工业炉窑热效率的意义1.1 工业炉窑热效率的定义与计算方法1.2 热效率对能源利用和生产成本的影响二、影响工业炉窑热效率的因素2.1 燃料选择与燃烧方式2.2 炉窑结构与设计2.3 热损失与余热利用2.4 传热方式与换热设备选型三、优化工业炉窑热效率的方法3.1 提高燃料燃烧效率3.2 优化炉窑结构与设计3.3 降低热损失与最大程度利用余热3.4 有效实施传热与换热技术四、工业炉窑热效率优化的实际应用与案例研究4.1 钢铁冶炼行业的热效率改进4.2 玻璃制造企业的炉窑能源利用优化4.3 化学工艺中的热效率提升实践总结与观点:工业炉窑热效率的提升对于能源节约、环境保护和企业竞争力的提升具有重要意义。
优化能源利用不仅需要技术手段,还需要企业加强管理和意识,推动能源管理和可持续发展的理念融入生产过程。
在未来的发展中,工业炉窑热效率的持续改进将成为能源转型和碳中和目标实现的重要环节。
观点:工业炉窑热效率的优化不仅仅是节约能源与降低生产成本的问题,更是践行可持续发展理念、减少对环境的负面影响的一项重要任务。
在工业发展中,更加注重绿色、低碳和高效的生产方式已经成为趋势,工业炉窑热效率的提升对于企业的可持续发展和环保形象的塑造至关重要。
通过有效的技术措施和管理改进,工业炉窑热效率的提高将成为企业实现节能减排目标的有效途径,也将为行业发展和可持续发展做出积极贡献。
文章分为四个部分,首先是对工业炉窑热效率的定义与计算方法进行解释,介绍热效率在能源利用和生产成本方面的重要性。
详细分析了影响工业炉窑热效率的因素,包括燃料选择、燃烧方式、炉窑结构与设计、热损失与余热利用以及传热方式与换热设备选型等。
工业炉窑保温技术通则

工业炉窑保温技术通则
工业炉窑保温技术是用于控制和减少炉窑热能损失的一种重要手段,其通则包括以下几个方面:
1. 保温材料的选择: 选用适当的保温材料是保温技术的基础。
常见的保温材料包括岩棉、硅酸盐纤维、高温陶瓷纤维等。
在选择材料时,需考虑其导热系数、抗温度变化性能、力学强度、防火性能等因素,并根据炉窑的工作温度和环境条件来确定合适的保温材料。
2. 保温层的设计和施工: 保温层的设计应合理,包括合适的保温厚度和层次结构。
施工过程中,需要注意保温材料的紧密连接,实现无孔隙、不脱落的施工效果,以减少热辐射和导热损失。
3. 炉窑结构和导热路径的优化: 合理设计炉窑的内部结构和元件,使得热流传递的路径最小化。
通过使用热桥隔断、空气隔热层、保温容器等手段,减少导热路径和热桥的存在,以减少热能的传输损失。
4. 密封系统的改进: 优化炉窑的密封系统,减少在工作过程中的热损失。
需要重视炉门、管道、法兰等连接部位的密封性能,以减少烟气
和热量的泄漏。
5. 热量回收系统的运用: 利用烟气或废热进行热量回收,在炉窑系统中进行再利用。
可以采用换热器、废热锅炉等装置,将热量转化为热水或蒸汽供给其他工艺使用,以提高能源利用效率。
6. 定期检查和维护: 保温层和密封系统是关键部位,需要定期检查和维护,确保其完好和有效。
这包括修复破损或老化的保温材料、更换老化的密封件、清理热交换装置等。
以上是工业炉窑保温技术的通则,根据具体情况和不同类型的炉窑,还需综合考虑炉窑的工作条件、产品要求、能源成本等因素,以制定适合的保温技术和相应的改善措施。
连铸坯热装热送装备的热损失减少方案

连铸坯热装热送装备的热损失减少方案随着工业化的发展,连铸技术在钢铁行业的应用越来越广泛。
而在连铸过程中,连铸坯的热装热送装备起着至关重要的作用。
然而,由于热能的传导、辐射和对流等多种因素的影响,连铸坯在装热送过程中会发生一定程度的热损失。
本文将针对这一问题,提出一些有效的减少连铸坯热损失的方案。
1. 热损失分析在开始介绍具体的减少热损失方案之前,我们需要先了解连铸坯的热损失原因。
连铸坯热损失主要包括以下几个方面:1.1 传导热损失:连铸坯与容器、输送设备等接触面隔热性能不佳,导致热量通过传导逐渐流失。
1.2 辐射热损失:连铸坯表面存在着辐射传热,高温连铸坯表面会对周围环境辐射热量。
1.3 对流热损失:连铸坯周围的空气在热送装备运输过程中会与连铸坯表面发生对流传热,导致热量散失。
针对以上热损失原因,我们可以采取一系列方案来减少连铸坯热损失。
2. 减少传导热损失为了减少连铸坯与容器及输送设备的传导热损失,可以采取以下方案:2.1 采用高温隔热材料:在连铸装备的接触面使用高温隔热材料,有效地降低传导热损失。
2.2 优化装备接触面:改善连铸坯与容器、输送设备的接触情况,提高密封性能,减少传导热损失。
3. 减少辐射热损失为了减少连铸坯表面的辐射热损失,可以采取以下方案:3.1 表面涂层处理:在连铸坯表面进行涂层处理,增加连铸坯表面的辐射热量反射率,减少热量散失。
3.2 安装热辐射屏蔽板:在连铸坯的热传输路径上安装热辐射屏蔽板,阻挡辐射传热,降低辐射热损失。
4. 减少对流热损失为了减少连铸坯在热送过程中由于对流而造成的热损失,可以采取以下方案:4.1 安装保温罩:对连铸坯进行保温罩加固,减少与外界环境空气的对流传热。
4.2 控制送风速度和温度:在热送过程中合理控制送风速度和温度,避免过大的对流传热。
5. 结束语通过以上几个减少连铸坯热损失的方案,可以有效地提高连铸坯的热装热送效率,减少热能浪费。
在实际应用中,我们需要根据具体的情况,选择合适的方案组合,并全面考虑设备成本和能源效益等因素。
工业炉窑热损失分析

工业炉窑路热损失分析工业窑炉根据其炉型的不同,炉窑中热量损失的途径也各不相同。
但是,诸如排烟热损失、不完全热损失等热量损失途径是各种炉窑所共有的,下面各项讨论炉窑中各种热损失的情况。
一、排烟热损失烟气离开炉窑时的温度大大高于冷空气的温度,一般可达到200--300℃,在未进行余热利用处理时,排烟温度甚至可高达600--700℃,造成排烟热损失。
排烟热损失是工业窑炉热量损失的非常重要途径。
二、气体不完全燃烧热损失燃料燃烧时常常会产生CO、H2、CH4等可燃气体,有时为满足工艺要求,在炉窑中的某些地段为还原性气氛,这时也会产生许多可燃气体。
在烟气排出窑炉时,部分尚未燃烧的可燃性气体也被排出了炉外,从而构成了气体不完全燃烧损失。
气体不完全燃烧热损失在一些特定工艺要求的炉窑中占据了比较重要的地位。
三、固体不完全燃烧热损失进入炉窑中的燃料往往不会被全部烧尽。
这些未燃烧的燃料中,大的颗粒会通过灰斗、炉渣排除,小的颗粒则随烟气飞出炉外。
四、炉体热损失炉体的热损失包括散热损失、蓄热损失、孔洞辐射损失和逸气损失,其中最主要的是散热损失和蓄热损失。
散热损失是指窑炉的外壁及各种管道向外散失的热量,有些保温措施不好的窑炉往往有比较严重的散热损失。
对于一些周期性操作的工业窑炉,如某些加热炉、热处理炉常常将物料加热到工艺要求的高温,然后进行保温、降温直至成品出窑。
炉体的温度也会相应的发生周期性变化,从而引起炉体的蓄热损失。
连续作业炉在停炉、开炉时也会有蓄热损失。
五、灰渣物理热损失从炉窑中排除的高温炉渣所带走德尔热量就是灰渣物理热损失。
六、工艺热损失工件加热处理后自身要带走热量,有时工件所携带温度很高,生产工艺过程中造成工艺热损失。
例如在煅造工艺中,工件被加热到700--800℃的高温。
在工件被加热后,往往将工件自然冷却,从而将热量白白浪费掉,采取措施利用这些热量就是提高炉窑的热效率。
工业窑炉利用特点:工业窑炉既是燃烧设备又是传热设备,显然,燃烧和传热对热利用起至关重要的作用。
电站锅炉机械未完全燃烧热损失分析方法的分析

电站锅炉机械未完全燃烧热损失分析方法的分析【摘要】本文针对电站锅炉机械未完全燃烧热损失进行了深入分析。
在探讨了研究背景和问题概述。
在首先分析了锅炉机械未完全燃烧热损失的原因,然后探讨了影响因素,介绍了常用的燃烧热损失分析方法,并提出了改善的对策。
最后通过实例分析进行了具体验证。
在总结了本文的研究内容,并展望了未来研究方向。
通过本文的研究,可以更好地了解电站锅炉机械未完全燃烧热损失的问题,为提高电站锅炉的燃烧效率和节能减排提供了参考。
【关键词】电站锅炉、机械、未完全燃烧、热损失、分析方法、影响因素、对策、实例分析、总结、展望未来、研究方向1. 引言1.1 研究背景电站锅炉是热电联产系统中的核心设备,其燃烧效率直接影响着发电效率和环境保护水平。
在锅炉燃烧过程中,机械未完全燃烧是造成热损失的重要原因之一。
机械未完全燃烧不仅会导致燃料的浪费,还会产生大量的排放物质,对环境造成严重污染。
当前,国内外对电站锅炉机械未完全燃烧热损失的研究还比较有限,特别是对其影响因素和改善对策还存在许多未解之谜。
深入分析电站锅炉机械未完全燃烧热损失的原因和影响因素,探索有效的燃烧热损失分析方法,制定可行的改善对策,对提升电站锅炉燃烧效率,减少能源浪费,保护环境意义重大。
本文旨在通过对电站锅炉机械未完全燃烧热损失进行深入研究和分析,为提高电站锅炉燃烧效率和节能减排提供理论支持和参考。
1.2 问题概述电站锅炉机械未完全燃烧热损失是电站运行过程中的一个重要问题,直接影响着电站的热效率和经济性。
在锅炉燃烧过程中,燃料未完全燃烧会导致燃烧热量的损失,造成能源的浪费。
如何有效地减少电站锅炉机械未完全燃烧热损失,提高热效率成为了当前电站运行管理的一个重要课题。
问题概述主要包括以下几个方面:电站锅炉机械未完全燃烧热损失的存在会导致热量被浪费,给电站带来经济损失。
未完全燃烧会增加烟气中的有害气体排放,对环境造成负面影响。
未完全燃烧还会导致锅炉机械的运行不稳定,影响电站的安全运行。
瓷辊道窑炉的节能和燃烧效能提高方案
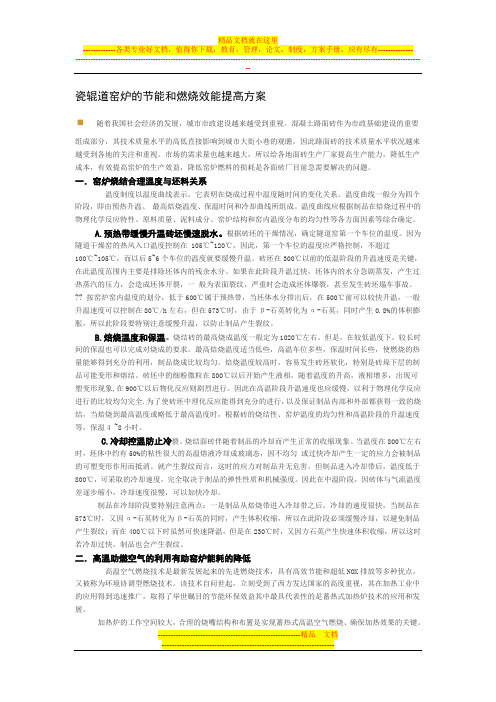
瓷辊道窑炉的节能和燃烧效能提高方案随着我国社会经济的发展,城市市政建设越来越受到重视。
混凝土路面砖作为市政基础建设的重要组成部分,其技术质量水平的高低直接影响到城市大街小巷的观瞻,因此路面砖的技术质量水平状况越来越受到各地的关注和重视。
市场的需求量也越来越大,所以给各地面砖生产厂家提高生产能力,降低生产成本,有效提高窑炉的生产效益,降低窑炉燃料的损耗是各面砖厂目前急需要解决的问题。
一.窑炉烧结合理温度与坯料关系温度制度以温度曲线表示,它表明在烧成过程中温度随时间的变化关系。
温度曲线一般分为四个阶段,即由预热升温、最高焙烧温度、保温时间和冷却曲线所组成。
温度曲线应根据制品在焙烧过程中的物理化学反应特性、原料质量、泥料成分、窑炉结构和窑内温度分布的均匀性等各方面因素等综合确定。
A.预热带缓慢升温砖坯慢速脱水。
根据砖坯的干燥情况,确定隧道窑第一个车位的温度。
因为隧道干燥窑的热风入口温度控制在105℃~120℃,因此,第一个车位的温度应严格控制,不超过100℃~105℃,而以后5~6个车位的温度就要缓慢升温。
砖坯在300℃以前的低温阶段的升温速度是关键,在此温度范围内主要是排除坯体内的残余水分。
如果在此阶段升温过快,坯体内的水分急剧蒸发,产生过热蒸汽的压力,会造成坯体开裂,一般为表面裂纹,严重时会造成坯体爆裂,甚至发生砖坯塌车事故。
按窑炉窑内温度的划分,低于600℃属于预热带,当坯体水分排出后,在500℃前可以较快升温,一般升温速度可以控制在80℃/h左右,但在573℃时,由于β-石英转化为α-石英,同时产生0.8%的体积膨胀,所以此阶段要特别注意缓慢升温,以防止制品产生裂纹。
B.焙烧温度和保温。
烧结砖的最高烧成温度一般定为1020℃左右。
但是,在较低温度下,较长时间的保温也可以完成对烧成的要求。
最高焙烧温度适当低些,高温车位多些,保温时间长些,使燃烧的热量能够得到充分的利用,制品烧成比较均匀。
焙烧温度较高时,容易发生砖坯软化,特别是砖垛下层的制品可能变形和熔结。
- 1、下载文档前请自行甄别文档内容的完整性,平台不提供额外的编辑、内容补充、找答案等附加服务。
- 2、"仅部分预览"的文档,不可在线预览部分如存在完整性等问题,可反馈申请退款(可完整预览的文档不适用该条件!)。
- 3、如文档侵犯您的权益,请联系客服反馈,我们会尽快为您处理(人工客服工作时间:9:00-18:30)。
矿产资源开发利用方案编写内容要求及审查大纲
矿产资源开发利用方案编写内容要求及《矿产资源开发利用方案》审查大纲一、概述
㈠矿区位置、隶属关系和企业性质。
如为改扩建矿山, 应说明矿山现状、
特点及存在的主要问题。
㈡编制依据
(1简述项目前期工作进展情况及与有关方面对项目的意向性协议情况。
(2 列出开发利用方案编制所依据的主要基础性资料的名称。
如经储量管理部门认定的矿区地质勘探报告、选矿试验报告、加工利用试验报告、工程地质初评资料、矿区水文资料和供水资料等。
对改、扩建矿山应有生产实际资料, 如矿山总平面现状图、矿床开拓系统图、采场现状图和主要采选设备清单等。
二、矿产品需求现状和预测
㈠该矿产在国内需求情况和市场供应情况
1、矿产品现状及加工利用趋向。
2、国内近、远期的需求量及主要销向预测。
㈡产品价格分析
1、国内矿产品价格现状。
2、矿产品价格稳定性及变化趋势。
三、矿产资源概况
㈠矿区总体概况
1、矿区总体规划情况。
2、矿区矿产资源概况。
3、该设计与矿区总体开发的关系。
㈡该设计项目的资源概况
1、矿床地质及构造特征。
2、矿床开采技术条件及水文地质条件。