复合材料夹层结构
复合材料夹层结构蜂窝芯材的压塌分析

工艺与装备113复合材料夹层结构蜂窝芯材的压塌分析王凯(中国民用航空飞行学院洛阳分院,洛阳471001)摘要:本文分析了复合材料夹层结构蜂窝芯材常见的压塌损伤,介绍了固化过程中影响芯材压塌的原因、影响因素、芯材压塌的稳定性和芯材特性,给出了处理芯材压塌的常用程序和控制芯材压塌的常用方法,对于防 止复合材料夹层结构制造和维修过程中产生压塌缺陷具有较强的指导意义。
关键词:夹层结构芯材压塌复合材料引言复合材料夹层结构由面板、夹芯以及连接两者的某种手段(如胶粘剂或铜焊)组成。
夹层板的面案承受弯曲载荷(一块面板承压,另一块面板承拉)或在某些情况下承受面内剪切载荷,面板的主要性能为压缩、拉伸、剪切强度和模量,夹芯性能主要包括密度、压缩强度和模量、剪切强度和模量、拉伸强度。
夹层板有多种失效模式,每种失效模式都会限制夹层结构的承载能力。
夹层结构的失效可能由诸多因素引起面 板、芯材及胶层的强度发生变化,失效模式通常有面板失 效、芯材剪切失效、芯材压塌、芯材压溃、芯材拉伸失效、面板/芯材脱胶、对称面板皱曲、整体屈曲和剪切皱折等 形式。
由于在夹层结构的制造和修理固化过程中均可能发 生芯材压塌,而且除最轻微的压塌外,其他都是不可接受、不能修复的,因此分析夹层结构蜂窝芯材的压塌,具有较 强的理论和实际意义。
1蜂窝芯材压塌的理论分析芯材压塌一般是度量发生在固化时蜂窝芯材部位的变 形和位移。
理论上,将导致芯材压塌的发生归结为一系列 基本要素和摩擦。
部分导致芯材压塌的不可预测原因是摩 擦因数。
摩擦分为静态和动态摩擦,静摩擦比动摩擦要髙。
达到最大静摩擦前,基本不会发生位移。
一旦超过最大静 态摩擦,低一些的动摩擦导致快速的位移。
芯材的压塌一 般与倒角区域有关,在芯材平面,倒角区域一般在髙压容 器的压力下发生变形和移动,如图1、图2所示。
芯材的刚度一定程度上可以抵抗固化容器的作用力,一 般在厚度方向上比较好,但蜂窝倾向于在垂直芯胞方向的硬 度低一些。
复合材料蜂窝夹层结构在飞机中的应用

复合材料蜂窝夹层结构在飞机中的应用摘要:飞机结构设计的基本原则是在满足强度要求的情况下使结构尽可能轻,这一要求必然导致需利用稳定的薄蒙皮承受拉伸载荷和压缩载荷,以及剪切、扭转、弯曲载荷的耦合作用。
传统的飞机结构设计中使用了纵向加强件和增稳桁条、翼肋和隔框等结构加强蒙皮,这样不可避免会带来结构增重问题。
提高结构比刚度的有效结构形式之一是夹层结构,复合材料夹层结构具有重量轻、强度刚度好,耐热、吸声隔音、抗冲击、耐疲劳等特点,已被广泛应用于航空航天中。
关键词:复合材料;蜂窝夹层;飞机;结构设计蜂窝夹层结构复合材料是50年代末发展起来的一种轻质、高强、各向异性的复合材料。
蜂窝夹层结构的密度小,可以明显的减轻结构重量;它的导热系数低,可以作为绝热和保温构件使用;它的比强度和比刚度高,可根据特殊的要求进行各向异性设计与制造。
因此长期以来备受航空、航天等领域的关注,尤其在航空工业中,蜂窝夹层结构复合材料己成功的大量应用于飞机的主、次承力结构件,如机翼、机身、尾翼和雷达罩等部位。
由于飞机飞行的环境条件比较苛刻,要求飞机用材料不仅有足够的强度、抗冲击性和刚度,而且还需良好的耐疲劳性、阻燃性、减重及抗腐蚀等许多特殊要求。
为了使飞机能正常进行飞行,在对所选用的材料性能进行全面的分析后,还需探索清楚构件性能与成型工艺之间的规律,这是材料应用的重要环节。
一、蜂窝夹芯结构的特点1、发挥复合效应的优越性。
夹层结构复合材料是由各组分材料经过复合工艺形成的,但它并不是由几种材料简单的复合,而是按复合效应形成新的性能,这种复合效应是夹层结构复合材料仅有的。
例如当夹芯板承受弯曲载荷时,上蒙皮被拉伸,下蒙皮被压缩,芯子传递剪切力。
从力学角度分析,它与工字梁很相似,面板相当于工字梁的翼缘,芯材相当于工字梁的腹板。
不同的是芯材与面板不是同一材料,芯材是分散的,而不是集中在狭腹板上。
由于轻质夹芯的高度比面板高出几倍,剖面的惯性距随之四次方增大,且面板有夹芯支持不易失稳。
夹层结构复合材料设计原理及其应用
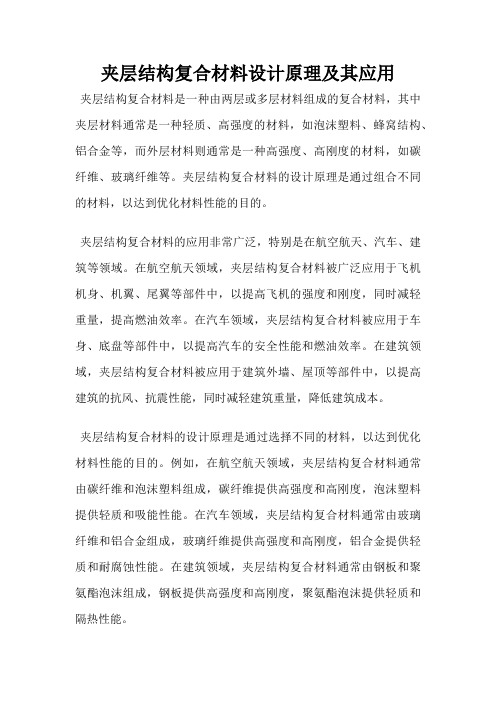
夹层结构复合材料设计原理及其应用
夹层结构复合材料是一种由两层或多层材料组成的复合材料,其中夹层材料通常是一种轻质、高强度的材料,如泡沫塑料、蜂窝结构、铝合金等,而外层材料则通常是一种高强度、高刚度的材料,如碳纤维、玻璃纤维等。
夹层结构复合材料的设计原理是通过组合不同的材料,以达到优化材料性能的目的。
夹层结构复合材料的应用非常广泛,特别是在航空航天、汽车、建筑等领域。
在航空航天领域,夹层结构复合材料被广泛应用于飞机机身、机翼、尾翼等部件中,以提高飞机的强度和刚度,同时减轻重量,提高燃油效率。
在汽车领域,夹层结构复合材料被应用于车身、底盘等部件中,以提高汽车的安全性能和燃油效率。
在建筑领域,夹层结构复合材料被应用于建筑外墙、屋顶等部件中,以提高建筑的抗风、抗震性能,同时减轻建筑重量,降低建筑成本。
夹层结构复合材料的设计原理是通过选择不同的材料,以达到优化材料性能的目的。
例如,在航空航天领域,夹层结构复合材料通常由碳纤维和泡沫塑料组成,碳纤维提供高强度和高刚度,泡沫塑料提供轻质和吸能性能。
在汽车领域,夹层结构复合材料通常由玻璃纤维和铝合金组成,玻璃纤维提供高强度和高刚度,铝合金提供轻质和耐腐蚀性能。
在建筑领域,夹层结构复合材料通常由钢板和聚氨酯泡沫组成,钢板提供高强度和高刚度,聚氨酯泡沫提供轻质和隔热性能。
夹层结构复合材料是一种非常重要的材料,它具有轻质、高强度、高刚度、吸能性能等优点,被广泛应用于航空航天、汽车、建筑等领域。
夹层结构复合材料的设计原理是通过选择不同的材料,以达到优化材料性能的目的。
未来,随着科技的不断发展,夹层结构复合材料将会得到更广泛的应用。
复合材料蜂窝夹层结构的优化设计

复合材料蜂窝夹层结构的优化设计摘要本文主要探讨了复合材料蜂窝夹层结构的优化设计方法。
首先介绍了蜂窝夹层结构的优点和应用领域,接着分析了其存在的问题和挑战。
然后,针对这些问题,提出了一系列优化设计方法,包括材料选取、蜂窝结构设计和界面优化等方面。
最后,通过具体案例分析,验证了所提出的优化设计方法的有效性。
1. 引言复合材料蜂窝夹层结构是一种在航空航天、汽车、建筑等领域广泛应用的先进结构材料。
其由两层面板夹持着一个蜂窝状的中间层,形成轻质且高强度的结构。
蜂窝夹层结构具有优异的性能,如高比强度、高比刚度、吸能能力强等,在许多领域都有广泛的应用。
2. 优点和应用领域蜂窝夹层结构具有以下几个优点: 1. 轻质高强度:蜂窝夹层结构由轻质面板和中间的蜂窝状结构组成,使其具有较小的自重和较高的强度。
2. 吸能能力强:蜂窝夹层结构中的蜂窝层具有吸能能力,能够有效地吸收冲击能量,提高结构的抗冲击性能。
3. 隔热隔音:蜂窝夹层结构中的蜂窝层具有较好的隔热隔音性能,适用于一些需要绝热隔音的场合。
蜂窝夹层结构广泛应用于以下几个领域: - 航空航天领域:蜂窝夹层结构在飞机、航天器等领域中被广泛使用,能够提高载荷能力和提高飞行性能。
- 汽车领域:蜂窝夹层结构可以用于汽车车身、底盘等部件,提高汽车的强度和安全性能。
-建筑领域:蜂窝夹层结构可以用于建筑的外立面、屋顶等部件,具有较好的隔热隔音效果。
3. 问题和挑战尽管蜂窝夹层结构具有许多优点,但仍然存在一些问题和挑战: 1. 材料选取:蜂窝夹层结构的性能与所选用的材料密切相关,如何选择合适的材料成为优化设计的重要问题。
2. 蜂窝结构设计:蜂窝夹层结构的性能也与其内部的蜂窝结构密切相关,如何设计合理的蜂窝结构是优化设计的关键。
3. 界面优化:蜂窝夹层结构中各层面板和蜂窝层之间的界面连接也对其性能产生影响,需要进行界面优化。
4. 优化设计方法针对以上问题和挑战,可以采取以下优化设计方法来提升蜂窝夹层结构的性能:4.1 材料选取在进行蜂窝夹层结构的设计时,需要选择合适的材料。
复合材料夹层结构

49
② 压制固化
涂胶完毕后从叶轮转筒上取下的蜂窝叠块,按所 用胶的固化规范固化。压力大小以胶液不渗透到玻璃 布背面,保证蜂窝胶接边胶合良好为原则。
蜂窝叠块的厚度即布的层数,由产品的尺寸要求 来决定。可由以下公式算出:
51
浸胶这一工序对蜂窝夹芯的质量有着直接的影响。 玻璃布只有在浸胶固化后,才能承力。因此,胶的含 量和蜂窝格壁上胶量的均匀程度直接影响蜂窝夹芯的 强度。含胶量在工艺上主要通过胶液粘度或浓度或密 度来控制,尤其是用密度控制更为方便。
密度大——含胶量大,强度可提高,但较重; 密度小——含胶量小,强度低、刚度低。
5
新型轻质夹层结构复合材料
Z向缝合夹层结构
Z-pin夹层结构
新型轻质夹层 结构复合材料
连体织物夹层结构
点阵夹芯结构
6
Z向缝合夹层结构
上面板
泡沫 芯材
下面板
承力柱
突出平压强度 优异耐久性 良好隔热隔声性
主要几 何参数
承力柱高度 承力柱细度 承力柱分布密度
7
Z向缝合夹层结构
缝合工艺
上面板内层 上面板外层 承力柱纤维
45
46
印胶法的特点: 印胶法是常用的涂胶方法,其设备简单,机械
化程度较高,质量容易控制,生产效率高,适合大 量生产。针对不同粘度有胶液,可以通过调整带胶 辊、递胶辊和涂胶辊之前的距离,就可以印出满意 的胶条。但这各设备的胶槽不易密闭,在涂胶过程 中胶液的粘度易发生变化,产生缺陷。可以通过连 续往胶槽中加料解决。
53
夹层结构复合材料的应用
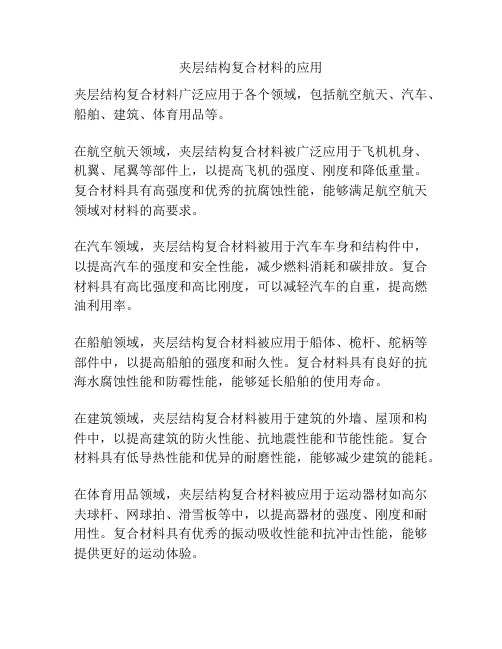
夹层结构复合材料的应用
夹层结构复合材料广泛应用于各个领域,包括航空航天、汽车、船舶、建筑、体育用品等。
在航空航天领域,夹层结构复合材料被广泛应用于飞机机身、机翼、尾翼等部件上,以提高飞机的强度、刚度和降低重量。
复合材料具有高强度和优秀的抗腐蚀性能,能够满足航空航天领域对材料的高要求。
在汽车领域,夹层结构复合材料被用于汽车车身和结构件中,以提高汽车的强度和安全性能,减少燃料消耗和碳排放。
复合材料具有高比强度和高比刚度,可以减轻汽车的自重,提高燃油利用率。
在船舶领域,夹层结构复合材料被应用于船体、桅杆、舵柄等部件中,以提高船舶的强度和耐久性。
复合材料具有良好的抗海水腐蚀性能和防霉性能,能够延长船舶的使用寿命。
在建筑领域,夹层结构复合材料被用于建筑的外墙、屋顶和构件中,以提高建筑的防火性能、抗地震性能和节能性能。
复合材料具有低导热性能和优异的耐磨性能,能够减少建筑的能耗。
在体育用品领域,夹层结构复合材料被应用于运动器材如高尔夫球杆、网球拍、滑雪板等中,以提高器材的强度、刚度和耐用性。
复合材料具有优秀的振动吸收性能和抗冲击性能,能够提供更好的运动体验。
总体而言,夹层结构复合材料在各个领域中都有广泛应用,通过其独特的性能和优势,为各行业带来了许多创新和发展机会。
复合材料夹层结构
复合材料夹层结构复合材料夹层结构的主要组成部分是纤维增强复合材料和基体材料。
纤维增强复合材料是指将纤维与基体材料相结合,形成具有特定性能和性质的材料。
常见的纤维包括碳纤维、玻璃纤维、聚合物纤维等,而基体材料则常常是树脂基材料。
夹层结构的设计要根据具体的应用需求来确定,一般包括夹层材料的选择、厚度的确定和夹层界面的处理。
在选择材料时,要综合考虑夹层的强度、刚度、耐热性、耐腐蚀性等性能。
对于不同的应用领域,要针对其特定环境和工况来选择夹层材料,以确保结构的可靠性和稳定性。
夹层结构的优势主要有以下几个方面。
首先,夹层结构能够结合不同材料的优点,提供更好的力学性能。
例如,纤维增强复合材料具有高强度、高刚度和低密度的特点,而基体材料则能提供耐磨损、耐腐蚀等特性。
其次,夹层结构可以提高整体结构的韧性和抗疲劳性能,减少开裂和断裂的风险。
此外,通过选择不同的夹层材料和界面处理方法,夹层结构还可以具有防火、隔热、隔音等功能,满足不同应用领域的要求。
然而,夹层结构在实际应用中也存在一些挑战和问题。
首先,夹层结构的复杂性增加了制造难度和成本。
其次,夹层结构的失效机制和破坏行为也较难预测和分析,对设计和维护提出了较高的要求。
此外,夹层结构的性能与结构参数之间存在一定的相互影响,需要通过研究和实验验证来进行优化和改进。
综上所述,复合材料夹层结构作为一种具有重要应用前景的结构形式,在不同领域和行业中发挥着重要的作用。
随着不断的研究和发展,夹层结构的性能和可靠性将会得到进一步提升,为实现更高效、更可靠的结构设计和应用提供了新的可能性。
复合材料夹层结构在航空领域的运用
复合材料夹层结构在航空领域的运用◎孙锐(作者单位:航空工业哈尔滨飞机工业集团有限责任公司工程技术部)设计人员在实际开展飞机结构设计工作时,始终面对强结构以及高效率这一要求。
各类结构在设计过程中都需要满足不失稳这一需求,尤其是在受到拉力、压力以及剪切荷载作用力的情况下结构不会发生改变。
在航空领域当中应用复合材料夹层结构是其发展的主要趋势与方向,也是在社会经济不断发展过程中提出的客观要求。
现阶段夹层结构在飞机结构设计中使用的范围不断拓宽,这充分说明复合材料夹层结构在航空领域起到的作用与价值。
一、常用芯材的客观分析1.蜂窝芯材的特性。
蜂窝材料具有各向异性的特点。
蜂窝因为存在开孔结构,不适用湿法工艺或树脂注射工艺(如RTM 树脂传递模塑)。
铝蜂窝或芳纶纸蜂窝具有压缩模量高和重量轻的优点,它们是飞机结构上广泛使用的夹芯材料。
但在某些情况下如面板出现裂纹和孔隙时,水或水汽就很容易进入蜂窝。
温度下降后,进入蜂窝孔中的水被冰冻后体积会发生膨胀,将破坏邻近蜂窝孔格的粘接,降低了夹层结构的性能,这时必须对蜂窝材料进行维修。
强度以及比刚度较高,是铝蜂窝这一结构材料的明显特征。
剪切载荷较大的部位是铝蜂窝层结构应用的主要位置,一般会利用金属板材作为面板使用。
在一定重量条件下,铝蜂窝夹芯材料可以最大限度降低自身厚度。
同时这也是其缺陷,在壁厚太薄的影响下,蜂窝表面可能会有严重的局部失稳出现。
在同一阶段内使用铝蜂窝以及碳纤维面板时,无法顺利结合两种材料。
在膨胀系数方面,上述两种材料具备相当大的差异,所以会导致明显的固化变形问题出现。
两种材料之间极易发生电化学腐蚀问题。
没有恰当处理电绝缘是导致其出现的主要原因。
2.泡沫芯材的特征。
在隔热以及隔音能力方面,硬质聚氨酯泡沫远远高于其他泡沫,工艺简单、价格便宜是硬质聚氨酯泡沫的明显优势与特征,但是其存在力学性能较差这一缺陷,在机械加工中极其容易出现易碎或者掉渣的问题。
已成型的复合材料层压板蒙皮腔体内是注射硬质聚氨酯泡沫的最终位置。
复合材料中常见的夹芯材料介绍
复合材料中常见的夹芯材料介绍1、夹芯结构材料定义夹芯结构材料(sandwich material),又叫夹层结构材料,是一种复合材料夹层结构。
夹层结构材料的整体受力原理类似工字梁。
夹层结构材料的面板承受由弯矩引起的面内正应力和面内剪切应力,芯材主要承受由面板传来的横向剪切应力,与此同时还具有稳定两块面板,防止局部屈服的作用。
夹层结构材料具有优良的比刚度和比强度,即在同等刚度和强度下,重量更低。
此外,夹层结构材料还具有削弱噪音与震动、隔热、抗疲劳、阻燃、吸声、隔震等优点。
夹层结构材料通过合理选择芯材和面板,可以有效降低材料的单位体积成本。
常用的夹层结构材料芯材主要分为三类:硬质泡沫、蜂窝和轻木。
硬质泡沫主要有:聚氯乙烯(PVC)、聚醚酰亚胺(PEI)、聚氨酯(PU)、聚乙烯(PET)、聚甲基丙烯酰亚胺(PMI)。
蜂窝:常见的蜂窝芯材有NOMEX蜂窝、铝蜂窝、棉布蜂窝、玻璃布蜂窝等。
轻木:轻木芯材是一类天然可再生芯材,原料为巴尔沙轻木2、夹芯材料的应用介绍通常夹层结构材料的强度要高于单独的面板材料或芯材刚度、强度,且重量、成本等均低于单一材料,因此被广泛应用于建筑、公路运输、轨道交通、航空、传播、风电等领域。
芯材是风电叶片关键材料之一,在叶片的前缘、后缘以及腹板等部位,一般采用夹层结构来增加结构刚度,防止局部失稳,提高整个叶片的抗载荷能力。
叶片常用芯材为PVC 泡沫和Balsa。
随着风电市场的日趋成熟,叶片向大型化方向发展,对叶片的重量、质量、成本以及材料的一致性提出新的要求。
现已开发出不同的新型芯材,逐渐在风能行业中得到应用和认可,主要包括聚对苯二甲酸乙二醇酯泡沫(PET)、聚甲基丙烯酰亚胺泡沫(PMI)、聚醚酰亚胺泡沫(PEI)、丙烯腈-苯乙烯泡沫(SAN)、聚苯乙烯泡沫(PS)、纤维增强复合材料芯材等。
对于芯材,除了要求优异的力学性能外,还需考虑芯材的加工、承受的温度、制品形状以及在叶片中使用的工艺性能。
复合材料夹层结构分析
复合材料夹层结构分析复合材料夹层结构是指由两个或多个不同材料组成的结构,每个材料在夹层结构中的分布和相互作用对整个结构的性能起着重要的影响。
本文将从夹层结构的组成、分析方法和应用领域三个方面进行介绍,并重点探讨夹层结构的应力分析、强度计算和疲劳寿命预测等方面的问题。
夹层结构的组成可以有很多种形式,例如纤维增强复合材料夹层结构、金属-复合材料夹层结构、复合材料-塑料夹层结构等。
其中,纤维增强复合材料夹层结构是最常见的一种形式。
在纤维增强复合材料夹层结构中,一般由多层纤维增强复合材料板材和粘接剂层组成。
其中,板材是由纤维和基体材料复合而成的,粘接剂层用于将不同板材连接在一起。
夹层结构的分析方法可以通过有限元分析、理论分析和试验分析等途径进行。
其中,有限元分析是最常用的分析方法之一、有限元分析可以通过将夹层结构离散化成有限个小单元,然后利用数值方法求解得到夹层结构的应力、应变和变形等信息。
在进行有限元分析时,需要考虑夹层结构的几何形状、材料特性和加载方式等因素,并选择合适的有限元模型和边界条件。
夹层结构的应力分析是夹层结构分析的关键一步。
应力分析可以通过解析方法、数值方法和试验方法进行。
在解析方法中,常用的有层合板理论、三维理论和剥离理论等。
层合板理论是最常见和简化的一种方法,它假设夹层结构是一个薄板,在板厚方向上应力变化不大。
三维理论则考虑了夹层结构的厚度效应,可以更准确地描述夹层结构的应力分布。
而剥离理论则主要用于描述夹层结构在受剪力作用下的剥离破坏。
夹层结构的强度计算是夹层结构分析中的另一个重要内容。
强度计算可以通过解析方法和试验方法进行。
在解析方法中,常用的有杠杆平衡法、层合板理论和损伤力学等。
杠杆平衡法可以用于计算夹层结构的最大弯曲应力和最大剪应力等。
层合板理论可以用于计算夹层结构的最大应力和最大应变等。
而损伤力学则可以用于描述夹层结构的疲劳寿命和损伤演化过程等。
夹层结构的疲劳寿命预测是夹层结构分析的重要内容之一、疲劳寿命预测可以通过数值模拟和试验验证相结合的方法进行。
- 1、下载文档前请自行甄别文档内容的完整性,平台不提供额外的编辑、内容补充、找答案等附加服务。
- 2、"仅部分预览"的文档,不可在线预览部分如存在完整性等问题,可反馈申请退款(可完整预览的文档不适用该条件!)。
- 3、如文档侵犯您的权益,请联系客服反馈,我们会尽快为您处理(人工客服工作时间:9:00-18:30)。
)T
避免缝线屈曲,提高斜缝合 泡沫夹层结构力学性能,尤 其是抗压性能;
便于制备大尺寸制件;
Z-pin夹层结构
应用领域
23
Z-pin夹层结构
24
连体织物及复合材料
面层
纤维 芯柱
面层
三维间隔连体织物是一种层与 层之间由连续纤维芯柱相接而 成一体呈空芯结构的编织物
面层之间芯柱经向呈“8”字形, 纬向呈“1”字形
3.0
70°-80°
2.5
60°-70°
Stress (MPa)
2.0
平
1.5
压
1.0
0.5
0.0 0.00 0.05 0.10 0.15 0.20 0.25 0.30 Strain
芯柱断裂破坏 芯柱与面层夹角成80°-90°时性能最佳
Stress (MPa)
1.2
1.0
剪
0.8
切 0.6
warp weft
Time / s
树脂沿芯柱纤维浸润距离-时间曲线
经向
纬向
上下面层异步浸胶方法:
首 先 将 其 总 量 的 30% 均 匀
涂覆在模具上,使树脂完
全浸入织物下面层,然后
将剩余树脂均匀涂覆在织
物上面层。
粘度越小下浸速度和上浸速
度差异越大
27
连体织物及复合材料
树脂含量对浸渗质量的影响
1.93 kg/m2
2.31 kg/m2
Fiber volume fraction/% Distance/cm
50
5mm 8mm
10mm
40
30
20
10
0 0.00
0.02 0.04 0.06 0.08 Vacuum pressure/MPa
0.10
真空作用下层连织物的纤维含量
随芯柱高度增加,可达到更高体积分数
28 Vacuum bag with HPM(weft)
4
1 0 25 50 75 100 125 150 Time/s
树脂在不同注胶方式下流动规律
沿织物纬向渗透速率均快于经向
30
连体织物及复合材料
层连织物内树脂渗透与回复特性
30
25
渗
25
Distance/cm
透
20
特
15
性
10
5
20
Distance / cm
15
0.06MPa
10
0.08MPa
0.1MPa
面板铺覆
斜缝合
合模
热膨胀成型
忽略面板和缝线的体积,忽略缝线张紧后的长度变化 认为缝线对泡沫芯刚性约束,缝线张紧力等于泡沫芯对模具的膨胀压力
最终
(T2, P2, V2)
(b3)
(T2, P1)
+
(a)
(b2)
(T1, P1, V1)
(b1) +
起始
泡沫芯子
(T1, P1)
模具
P
K
F 2
(
F c
M c
25
Vacuum bag with HPM(warp)
Vacuum bag without HPM(weft)
22
Vacuum bag without HPM(warp)
Rigid mold without HPM(weft)
19
Rigid mold without HPM(warp)
16
13
10
7
0.00
0.01
上面层注入
下面层注入
注入示意图
充模时间/s
526
543
注入树脂质量/g
520
531
上表面
上下面层异步注入
381 722
下表面
11
Z向缝合夹层结构
工艺条件对承力柱孔隙的影响
宏观孔隙缺陷 延长真空作用时间,采用丝束小的纱线
5
4 4-5
3
3-4
2-3
2
1-2
1
0-1
d
0
c
30
150 270
390
510
b a
80
60
Y=1.38+0.31exp(0.00121X)
40
R2=0.99954
环氧E51流变曲线
20
0 0
1000 2000 3000 4000 5000 Time / s
120
100
Experimental data
Fitting experimental data 80
60
Y=0.43+0.07exp(0.00282X)
Lucas-Washburn方程
L2 cos rc t 2
14
12
Wicking distance / mm
10
8
6
4
Theoretical prediction
2
Wicking from top to bottom
Wicking from bottom to top
0
0
2000
4000
6000
0.0 0.00
0.02 0.04 0.06 0.08 Vacuum pressure/MPa
0.10
层连织物的厚度回复率
织物的厚度回复率随着压力增大而减小 随着芯柱高度降低,厚度更易回复
31
连体织物及复合材料
Resin content Resin content
Resin content
树脂分布影响因素
主要几 何参数
承力柱高度 承力柱细度 承力柱分布密度
8
Z向缝合夹层结构
缝合工艺
上面板内层 上面板外层 承力柱纤维
泡沫芯材 下面板外层
下面板内层
9
Z向缝合夹层结构
缝合泡沫夹层结构制备方法
预成型体锁式缝合工艺
缝合泡沫夹层结构
缝合预成型体
复合工艺
10
Z向缝合夹层结构
缝合泡沫夹层树脂注入方法
树脂渗透方式
随着树脂粘度增加, 树脂渗透均匀性变
差
5 9 13 17 21 25
Distance/cm
0.7
0.6
0.5
0.4
0.3
0.1MPa
0.08MPa
0.2
5
10 15 20 25
Distance/cm
0.1
1
2
3
4
5
6
Distance/cm
32
连体织物及复合材料
力学特性与失效模式
3.5 80°-90°
0.4
0.2
0.0
芯柱根部断裂
0.0 0.2 0.4 0.6 0.8 1.0
Strain
纬向性能优于经向
33
连体织物及复合材料
力学特性与失效模式
400
300
Load (N)
弯
200
曲 100
weft warp
0
012345678 Displacement (mm)
Face sheet compressive stress (MPa)
加入芯材的目的是维持两面板之间的距离,这一距离使夹层 面板截面的惯矩和弯曲刚度增大。由于芯材的比重小,所以用 它制成的夹层结构能在同样承载能力下,大大减轻结构的自重。
5
夹层结构的面板材料可以是玻璃钢板、塑料板、铝 板、胶合板等。它是夹层结构的主要受力部分。
夹层结构的夹芯材料有蜂窝芯材、泡沫塑料、强芯 毯、软木等,它在夹层结构中起连接和支撑面板的作用, 承受的是剪切应力。
主要几 何参数
无面/芯剥离
抗冲击性能优异
芯柱高度 经纱密度 纬纱密度 间隔纱密度
25
连体织物及复合材料
应用领域
制备多层吸波材料 应用于F/A-18E/F
波兰的Bilsam aviation制造 的轻型运动飞机Sky Cruiser
小型飞机座椅
26
连体织物及复合材料
树脂对层连织物的毛细浸润
40
R2=0.99821
20 191树脂流变曲线
0 0 500 1000 1500 2000 2500 3000 Time / s
0 C expBt 环氧E51 191树脂
初始粘度/Pa•s
1.38
0.43
反应速率参数B 0.00121 0.00282 29
连体织物及复合材料
低粘度树脂真空辅助成型
0.7 0.6 0.5 0.4 0.3 0.2 0.1
0
0.7
0.6
0.3Pa·s 0.5Pa·s
高渗透率介质层有
0.7Pa·s
0.5
助于树脂均匀分布
0.4 0.3 0.2 0.1
1
Without high permeability media With high permeability media
0
0.00 0.05 0.10 0.15 0.20
Strain
13
Z向缝合夹层结构
缝合泡沫夹层结构力学性能
Load / N
1200
弯 800 曲
400
Stitched Sanwich Unstitched Sandwich
0 0
10
20
30
Displacement / mm
性能指标
平压强度 /MPa 平压模量 /MPa 侧压强度 /MPa 侧压模量 /MPa 弯曲强度 /MPa
复合材料夹层结构
2018.3.22
1
概述
先进复合材料的重要发展方向