精馏塔设计与优化
精馏塔控制和节能优化研究综述

173经济全球一体化以来,人们的生活质量以及生活水平逐渐提升,对石油化等工业需求越来越高,对产品纯度的需求也在逐渐提升,使精馏有了更加广泛的应用。
为了与绿色、节能理念相契合,给精馏过程带来了新的挑战,对精馏过程进行严格的控制以及优化是十分重要的。
但是,在对精馏塔进行控制以及节能优化之前,必须有效确保整个精馏过程中所生产的产品质量,只有产品达到了相关标准,才可以进行装置优化,从而降低能耗、有效提升回收率,做到将成本最大化的转变成经济效益。
1 精馏原理以及操作过程精馏就是将一定浓度的液体输送到精馏装置中,常见的精馏设备就是图1所示的连续精馏装置。
精馏装置主要分为五个大部分:一是精馏塔;二是冷凝器;三是再沸器;四是回流罐;五是回流罐。
连续精馏装置的工作原理是由进料泵将溶液供给到精馏塔,由于溶液中的液体沸点不同,就会将溶液分为低沸点组和高沸点组,低沸点组也就是易挥发组会因为汽化而向上升腾;高沸点组会因其难挥发而向下流淌,并与向上升腾的蒸汽在塔板之间发生接触,从而实现相际传质[1]。
在相对恒压的条件下,若对单组液体进行持续加热,温度并不会出现变化,但是,在对混合溶液进行沸腾后持续加热,其温度必然会发生变化。
在恒压的条件下,溶液的组分情况会与气相平衡有着密切的联系,其中组分的沸点与浓度成正比,沸点越高浓度就会越高,当然平衡温度也就会更高。
与纯物质相比,混合溶液中液相与气相均处于平衡状态下的温度是不一样的。
当沸点高的液体流到釜液泵后,就会成为塔底产品,而沸点低的液体就会成为塔顶产品,这两段操作的结合,可以将混合溶液中的液体分为两个部分,并进行分离,从而精馏出两种所需纯度的产品。
精馏可以将混合物液体进行分离,主要利用的就是液体的沸点不同,通过汽化以及冷凝的方式,经过精馏装置对其进行反复冷凝以及汽化,从而有效的不同组分的液体完全分离。
所以,整个精馏过程其实就是进行多次汽化、多次冷凝的过程,并且,溶液会在汽化以及冷凝的过程中会吸收和释放大量的热量,因此精馏装置必须具备冷凝器以及再沸器等装置给予辅助,从而实现整个精馏装置的完整运行,从而得到预期塔顶以及塔底的产品[2]。
精馏塔的设计

三、四、工艺计算及主体设备设计 (一)精馏塔的物料衡算与操作线方程 1)原料液及塔顶、塔底产品的摩尔分率苯和氯苯的相对摩尔质量分别为78.11和112.56kg/kmol 。
728.056.112/35.011.78/65.011.78/65.0=+=F x 986.056.112/2.011.78/98.011.78/98.0=+=D x2)原料液及塔顶、塔底产品的平均摩尔质量()kg/km ol 4804.8756.112728.0-1728.011.78=⨯+⨯=F M ()kg/km ol 592.7856.112986.0-1986.011.78=⨯+⨯=D M()kg/km ol 46.11256.11200288.0-100288.011.78=⨯+⨯=W M3)原料液及塔顶、塔底产品的摩尔流率依题给条件:一年以330天,一天以24小时计,有:h Kmol F /16.574804.871053=⨯=,全塔物料衡算:WD F WD F 00288.0986.0728.0+=+= ⇒kmol/h 00.15kmol/h16.24kmol/h16.57===W D F 4.求操作线方程 精馏段操作线:629.0362.011+=+++=x R xx R R y Dq 线方程为: x=0.72800288.056.112/998.011.78/002.011.78/002.0=+=W x提馏段操作线为过(0.00288,0.00288)和()893.0,728.0两点的直线。
y=00098.0228.1y -=-=X X VWX V L W (二)理论塔板层数T N 的确定苯-氯苯物系属于理想物系,可采用梯级图解法求取T N ,步骤如下: 1.由手册查得苯-氯苯的气液平衡数据,绘出y x ~图,如下图一;图解得11=T N 块(不含釜)。
其中,精馏段41=T N 块,提馏段8块,第5块为加料板位置。
精馏塔再沸器的控制方案及其优化
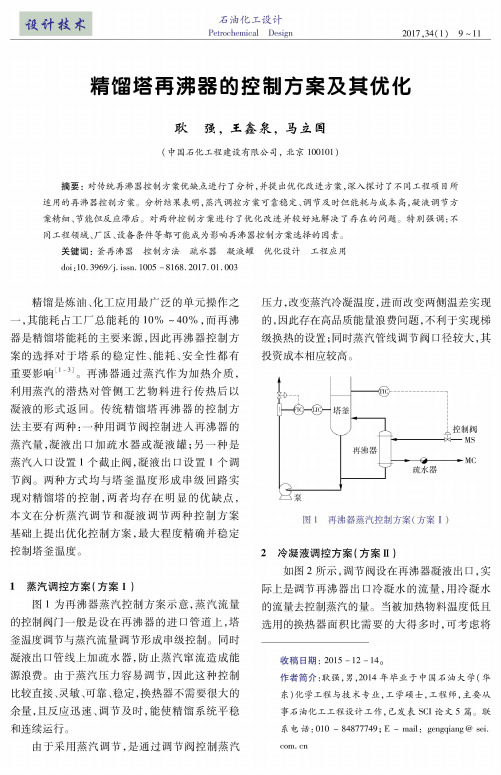
设针技术石油化工设计Petrochemical Design 2017,34(1) 9 〜11精馏塔再沸器的控制方案及其优化耿强,王鑫泉,马立国(中国石化工程建设有限公司,北京100101)摘要:对传统再沸器控制方案优缺点进行了分析,并提出优化改进方案,深入探讨了不同工程项目所 适用的再沸器控制方案。
分析结果表明,蒸汽调控方案可靠稳定、调节及时但能耗与成本高,凝液调节方 案精细、节能但反应滞后。
对两种控制方案进行了优化改进并较好地解决了存在的问题。
特别强调%不 同工程领域、厂区、设备条件等都可能成为影响再沸器控制方案选择的因素。
关键词:釜再沸器控制方法疏水器凝液罐优化设计工程应用doi%10. 3969/j.issn. 1005 - 8168.2017.01.003精馏是炼油、化工应用最广泛的单元操作之 一,其能耗占工厂总能耗的10%〜40%,而再沸 器是精馏塔能耗的主要来源,因此再沸器控制方 案的选择对于塔系的稳定性、能耗、安全性都有 重要影响[1_3]。
再沸器通过蒸汽作为加热介质,利用蒸汽的潜热对管侧工艺物料进行传热后以 凝液的形式返回。
传统精馏塔再沸器的控制方 法主要有两种:一种用调节阀控制进入再沸器的 蒸汽量,凝液出口加疏水器或凝液罐;另一种是 蒸汽入口设置1个截止阀,凝液出口设置1个调 节阀。
两种方式均与塔釜温度形成串级回路实 现对精馏塔的控制,两者均存在明显的优缺点,本文在分析蒸汽调节和凝液调节两种控制方案 基础上提出优化控制方案,最大程度精确并稳定 控制塔釜温度。
1蒸汽调控方案(方案I)图1为再沸器蒸汽控制方案示意,蒸汽流量 的控制阀门一般是设在再沸器的进口管道上,塔 釜温度调节与蒸汽流量调节形成串级控制。
同时 凝液出口管线上加疏水器,防止蒸汽窜流造成能 源浪费。
由于蒸汽压力容易调节,因此这种控制 比较直接、灵敏、可靠、稳定,换热器不需要很大的 余量,且反应迅速、调节及时,能使精馏系统平稳 和连续运行。
精馏塔优化设计的探讨
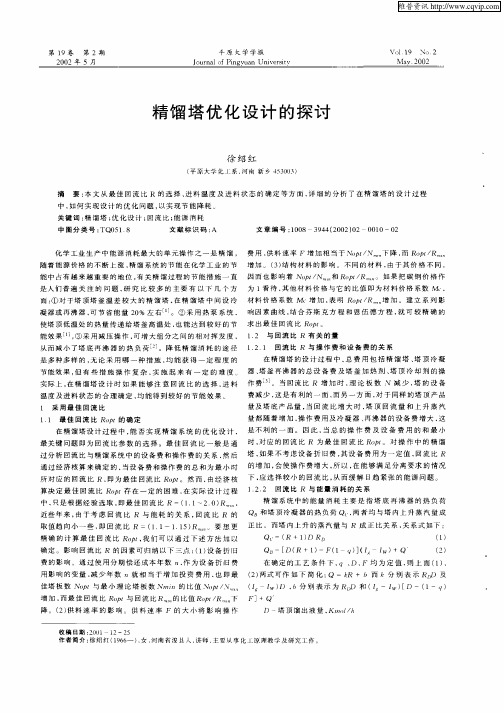
第 1 9卷 第 2期
2 0 年 5月 02
VO. 9 NO 11 2
M a 0 2 v2 0
精 馏 塔 优 化 设 计 的 探 讨
徐 绍 红
( 原大学化工 系, 南 新 乡 430 ) 平 河 5 0 3
摘 要 : 文 从 最 佳 回 流 比 R 的选 择 、 料 温 度 及 进 料 状 态 的 确 定 等 方 面 , 细 的 分 析 了 在 精 馏 塔 的 设 计 过 程 本 进 详 0
温 度 及 进 料 状 态 的 合 理 确 定 , 能得 到 较 好 的 节 能 效 果 。 均
1 采 用 最 佳 回 流 比 1 最 佳 回 流 比 Ro t的 确 定 1 p
费 减少 , 是 有 利 的一 面 , 另 一 方 面 , 于 同样 的 塔 顶 产 品 这 而 对 量 及 塔 底 产 品量 , 回 流 比 增 大 时 , 顶 回流 量 和 上 升 蒸 汽 当 塔 量 都 随 着 增 加 , 作 费用 及 冷 凝 器 、 沸 器 的 设 备 费 增 大 , 操 再 这
表 o t R… 增 加 。 建 立 系 列 影 面 : 对 于 塔 顶 塔 釜 温 差 较 大 的 精 馏 塔 , 精 馏 塔 中 间 设 冷 材 料 价 格 系 数 Mc增 加 , 明 R p / ① 在 凝 器 或 再 沸 器 , 节 省 能 量 2 % 左 右 … 。 ② 采 用 热 泵 系统 , 响 因 素 曲 线 , 合 芬 斯 克 方 程 和 恩 伍 德 方 程 , 可 较 精 确 的 可 0 结 就 o t 使 塔 顶 低 温 处 的热 量 传 递 给 塔 釜 高 温 处 , 能达 到 较 好 的 节 求 出最 佳 回流 比 R p 。 也 能 效 果 _ , 采 用 减 压 操 作 , 增 大 组 分 之 间 的 相 对 挥 发 度 , 1 2 与 回流 比 R 有 关 的量 l ③ J 可 . 从 而 减 小 了 塔 底 再 沸 器 的 热 负 荷 ] 降 低 精 馏 消 耗 的 途 径 1 2 回流 比 R 与 操 作 费和 设 备 费 的 关 系 。 . 1 是 多 种 多 样 的 , 论 采 用 哪 一 种 措 施 , 能 获 得 一 定 程 度 的 无 均 在 精 馏 塔 的设 计 过 程 中 , 费 用 包 括 精 馏 塔 、 顶 冷 凝 总 塔
精馏塔和蒸馏塔的优缺点

精馏塔和蒸馏塔的优缺点
精馏塔和蒸馏塔是化工领域常见的分离设备。
两者都是利用物质在不同温度下汽液相平衡的原理进行分离的。
下面将分别介绍精馏塔和蒸馏塔的优缺点。
精馏塔的优点
1.高效分离:精馏塔能够通过多级馏分来实现高效的分离过程,可以
得到高纯度的产品。
2.适用范围广:精馏塔适用于液体和气体的分离,适用于多种不同的
工艺和物料。
3.操作稳定:精馏塔在工业生产中有成熟的操作技术和经验,操作相
对稳定可靠。
4.节能环保:精馏塔可以通过优化设计和操作来实现能源的节约,对
环境友好。
精馏塔的缺点
1.能耗较高:精馏塔需要消耗大量的能源来维持分馏过程,存在一定
的能耗问题。
2.设备成本高:精馏塔设备复杂,安装维护成本较高,投资大。
3.对原料要求高:精馏塔对原料的质量要求较高,需要较纯净的原料
才能实现高效的分离。
蒸馏塔的优点
1.适用性强:蒸馏塔适用于各种溶剂和多种物质的分离,应用范围广
泛。
2.制备简单:蒸馏塔结构相对简单,制备过程也较简单。
3.维护方便:蒸馏塔的维护比较方便,易于清洗和维护,减少停机时
间。
蒸馏塔的缺点
1.分离效率较低:部分情况下,蒸馏塔的分离效率不如精馏塔,无法
获得高纯度的产品。
2.对操作要求高:蒸馏塔在操作过程中需要细致的控制温度和压力,
操作复杂。
3.产率较低:蒸馏塔在部分情况下产率不如精馏塔,无法快速得到大
批产品。
综上所述,精馏塔和蒸馏塔各有其优缺点,在实际应用中需要根据具体情况来选择合适的分离设备,以满足生产需求和经济效益。
精馏塔(板式)设计

PA α= ∗ PB
(三)塔板数的确定 1、作出x-y相图 、作出 相图 2、最小回流比及操作回流比 、 3、理论板数及加料位置 、 ①求精馏塔的汽、液相负荷 求精馏塔的汽、
∗
R = 1.5 Rmin
L′ = L + qF = RD + qF
V ′ = V + (q − 1) F = ( R + 1) D + (q − 1) F
化工原理课程设计
(6)冷凝器的选择 ) 塔顶产品(全凝器)和塔釜产品(冷却器) 塔顶产品(全凝器)和塔釜产品(冷却器) (7)加料方式的选择 ) 高位槽或泵 (8)工艺流程 ) 3、正戊烷和正己烷的性质、用途等 、正戊烷和正己烷的性质、
化工原理课程设计
二.工艺计算
主要内容是( 主要内容是(1)物料衡算 (2)确定回流比 (3)确定理论板数和实 际板数 (4)塔的气液负荷计算 (5)热量衡算 塔设备的生产能力一般以千克/小时或吨/年表示, 塔设备的生产能力一般以千克/小时或吨/年表示,但在理论板 计算时均须转换成kmol/h,在塔板设计时 在塔板设计时, 计算时均须转换成kmol/h,在塔板设计时,气液流量又须用体积 流量m /s表示 因此要注意不同的场合应使用不同的流量单位。 表示。 流量 m3/s 表示 。 因此要注意不同的场合应使用不同的流量单位 。 (一)全塔物料衡算 1、原料液及塔顶、塔底产品的摩尔分数 、原料液及塔顶、
化工原理课程设计
②求精馏段、提馏段的操作线方程 求精馏段、
R xD y= x+ R +1 R +1
③作图求出理论板数 ④逐板计算求理论板数
WxW L + qF y′ = x′ − L + qF − W L + qF − W
PRO/II对液化气分馏装置丙烯精馏塔的模拟与优化
PRO/II对液化气分馏装置丙烯精馏塔的模拟与优化摘要:利用PRO/II流程模拟软件,对液化气分离装置的丙烯精馏塔进行模拟计算。
利用灵敏度分析工具,对塔压,回流比,全塔热负荷等重要参数进行优化设计。
通过改变蒸馏塔进料位置和原料的进料状态,进行优化优化计算和经济效益比较,得到操作费用最低的进料位置和进料状态。
关键字:PRO/II;丙烯精馏塔;模拟优化Simulation and Optimization of the Operation of Liquefied Petroleum Gas Separation Unit of C3-spliter with PRO/II SoftwareAbstract: Using PRO/II process simulation software, the LPG separation unit of C3-spliter to simulate calculation of the column. Using sensitivity analysis tool, tower pressure, reflux ratio and the duty and other important parameters tower optimized design. By changing the distillation tower feeding position and raw materials incoming state, optimization calculation and economic efficiency comparison, get the feed of the lowest operation cost position and incoming state.Key Word: PRO/II;C3-spliter;Simulation and Optimization液化气作为燃料利用的途径被管道天然气取代是一种趋势。
简化外部热耦合双精馏塔的控制与优化
(— S EHI DDi C) i p o o e s r p s d。 wh r h e e te c a g r r s d t p r xma ee tr a e ti tg a in e et r eh a x h n e sa eu e oa p o i t x e n l a e r t h n o
Ab t a t s r c :A w on r t uc ur f t e sm p ii d e e na l a —n e r t d o ne c t ols r t e o h i lfe xt r ly he ti t g a e d ubl itla i n c l m n e d s il to o u s
b t e h et yn / tipn et n ft ehg — rs ue ( ewen t e rci ig sr ig sci s o h ihp es r HP) / lw p es r L ) dsiain f p o o — rsu e ( P i lt tl o clmn . eh a uiso h o / otm e te c a g r r sd t o t l h o / otm rd c ou s Th e t t ftetp b to h a x h n esaeu e oc nr etp b to p o u t d e o t
第6卷 2
第 8期
化
工 学
报
Vo . 2 NO 8 16 .
Au gus 201 t 1
21 0 1年 8月
CI C J u n 1 ES o r a
简 化外 部热 耦 合双 精 馏 塔 的 控 制 与优 化
马 江鹏 ,陈海胜 ,黄 克谨
苯和甲苯精馏塔课程设计
苯和甲苯精馏塔课程设计一、引言苯和甲苯是两种常见的有机化合物,在工业生产中广泛应用。
为了提高产率和纯度,需要进行精馏分离。
本文将介绍苯和甲苯精馏塔的设计过程。
二、设计目标1. 提高产率:通过精馏分离,提高苯和甲苯的产率;2. 提高纯度:使得分离后的苯和甲苯纯度达到要求。
三、设计流程1. 确定塔型:选择板式塔或填料塔;2. 确定操作压力:根据组成和沸点差确定操作压力;3. 确定板数或填料高度:根据理论计算确定板数或填料高度;4. 确定进料位置:在塔的上部或下部进料;5. 确定回流比:根据经验确定回流比;6. 确定冷凝器类型:选择直接冷凝器或间接冷凝器。
四、详细设计过程1. 塔型选择根据实际情况,我们选择了板式塔。
板式塔结构简单,易于维护,适用于小规模生产。
2. 操作压力确定根据苯和甲苯的沸点差,我们确定了操作压力为1 atm。
3. 板数或填料高度确定根据理论计算,我们确定了塔的板数为10个。
每个板的高度为0.5 m。
4. 进料位置确定我们选择在塔的下部进料,以便更好地控制进料速度和分离效果。
5. 回流比确定根据经验,我们选择回流比为2:1。
6. 冷凝器类型选择考虑到成本和维护难度,我们选择了直接冷凝器。
五、设计结果通过以上设计过程,我们得到了苯和甲苯精馏塔的具体参数:1. 塔型:板式塔;2. 操作压力:1 atm;3. 板数:10个;4. 进料位置:下部进料;5. 回流比:2:1;6. 冷凝器类型:直接冷凝器。
六、结论通过本次课程设计,我们成功地设计出了苯和甲苯精馏塔,并得到了具体的参数。
在实际生产中,需要根据实际情况进行调整和优化。
正庚烷——正辛烷连续精馏塔设计
正庚烷——正辛烷连续精馏塔设计1.引言正庚烷和正辛烷是石油中较常见的两种烷烃化合物。
它们通常通过连续精馏过程从原油中分离出来。
在本文中,我们将设计一座连续精馏塔,以将正庚烷和正辛烷分离出来。
2.塔设计连续精馏塔是一种常用的分离设备,可以利用组分的不同挥发度将混合物分离成不同的组分。
在设计过程中,我们需要考虑以下几个方面:2.1塔型选择对于正庚烷和正辛烷的分离,通常选择塔顶回流塔。
这种塔型可以有效地分离轻质和重质组分,并提高分离效率。
2.2塔采用板式还是填料式?塔可以采用板式或填料式两种设计。
在本次设计中,我们选择填料式塔。
填料可以提供更大的表面积,增加相接触,从而提高分离效果。
2.3塔的电性能设计在连续精馏过程中,需要将混合物加热到适当的温度,以使其汽化。
此外,在塔中加入一定的沸点提升剂可以提高塔的分离效率。
因此,我们需要考虑塔的加热和冷却系统的设计。
2.4塔的操作参数在塔的操作中,我们需要确定适当的操作参数,包括进料温度、进料流量、塔顶回流比、底部回流比等。
这些参数将影响分离效率和产量。
3.热力学分析在进行连续精馏塔设计之前,我们需要进行热力学分析,以确定正庚烷和正辛烷的汽液平衡曲线和塔顶回流比与塔底回流比之间的关系。
这可以帮助我们确定最佳操作参数。
4.连续精馏塔的模拟在连续精馏塔的设计中,使用模拟软件进行仿真是非常有帮助的。
通过对塔的模拟,我们可以确定最佳的操作参数,并进行优化。
5.应用案例在连续精馏塔设计中,通过实际的应用案例,我们可以更好地理解设计原理和方法。
例如,可以选择一组原油成分,并基于该组分进行连续精馏塔的设计。
6.结论通过上述步骤,我们可以设计一座连续精馏塔,以将正庚烷和正辛烷有效地分离出来。
连续精馏塔的设计涉及到众多的参数和因素,需要综合考虑热力学和操作要求。
通过模拟和实际应用的结合,可以获得较为理想的设计结果。
- 1、下载文档前请自行甄别文档内容的完整性,平台不提供额外的编辑、内容补充、找答案等附加服务。
- 2、"仅部分预览"的文档,不可在线预览部分如存在完整性等问题,可反馈申请退款(可完整预览的文档不适用该条件!)。
- 3、如文档侵犯您的权益,请联系客服反馈,我们会尽快为您处理(人工客服工作时间:9:00-18:30)。
《读书报告》 1 / 6 精馏塔的设计与优化 1. 精馏塔的设计 精馏塔的设计牵涉到众多的参数:产品组成、产品的流量、操作压力、塔板数、进料位置、回流比、再沸器热负荷、冷凝器冷却负荷、塔径、塔高。精馏塔设计中常见的情况是已知进料条件,即进料物流的流量F、组成zi、温度TF、压力PF。通常也会指定塔顶产品的中轻关键组分浓度xD,LK和塔底产品的重关键组分浓度xB,HK[1]。因此,设计的问题就在于确立精馏塔的操作压力,塔板数,进料位置,回流比,以得到期望纯度的产品。当确定了操作压力、塔板数、进料位置、回流比以及期望的产品纯度,则相应的再沸器热负荷、冷凝器冷却负荷、塔顶及塔底流量、塔径、塔高也即为定值(具体的塔板类型及换热器结构不在讨论范围之内)。计算机编程能够精确的求解MESH方程组,但是简捷计算法仍被用于设计任务的初期,并且在界定问题上作为计算机的辅助手段,具有智能指导性的简捷计算法可以减少计算机的耗时和费用[2]。 1.1. 操作压力的确定 对于绝大多数精馏塔的设计问题而言,选择独立操作塔(即与过程中其余部分无能量集成的塔)的操作压力是一项相对简单的,直截了当的任务,考虑的重点只是塔顶馏出物的冷凝温度,使其能够在炎热的夏季也能用自来水将蒸汽冷凝下来[3]。 1.2. 塔板数与回流比的计算 在多组分精馏中,由于产品浓度不能完全确定,二元精馏中十分有效的逐板计算法在多元精馏中遇到了困难,多元精馏的设计计算至今尚无通用有效的方法,只能应用核算型算法经多方案试算比较,得到合适的设计结果[4]。图解法(即McCabe-Thiele法)能很好地图示出VLE、回流比、塔板数,但该方法仅限于二元体系。随着组分数的增多,图解法也无法应用了。 在多组分精馏中,对于有恒定α的多组分系统,可以用Underwood法求得最小回流比的精确解,其方程式为: 《读书报告》 2 / 6 njF,j
j=1j
njD,j
mj=1j
αx=1-qα-θ
αxR+1=α-θ
(1)
经验表明,最佳回流比的值往往处在1.03作回流比使R/Rm等于1.2。对于三元混合物的最小回流比的计算,Glinos和Malone给出了可以用来代替Underwood方程的表达式[3]:
BCAFBFCFAFACBCAFAC
BFBFCFBCAFACAFBFAFCF
a(x+x)xA/BC: Rm = +
fx(a-a)fx(a-1)
1f=1+x100(x+x)/(a-1)+x/(a-1)AB/C Rm=(x+x)(1+xx)式中,
: (2)
在多组分精馏中,对于有恒定α的多组分系统,Fenske导出了全回流条件下的最小塔板数的表达式:
,,,,,lg[()()]lgDlkBhkDhkBlkmlkhk
xxxxN (3)
式中αlk,hk是轻关键组分对重关键组分的相对挥发度,下标lk指轻关键组分,hk指重关键组分。当αlk,hk沿塔有些变化时,应取塔顶、加料和塔底处其值的平均值: 13=()DFB (4)
至此,对于理论塔板数的计算就可以通过查吉利兰图得到,或者通过吉利兰关联得到[4]:
0.5668m
N-N=0.75[1()]N+11mRRR
(5)
对于多组分精馏设计中理论塔板数和回流比的确定,还有一些其他的数学方法,但以上计算式因形式相对简单、精确度较高而使用的比较广泛。 在使用流程模拟软件时,在规定分离要求的情况下,对于最小塔板数的确定《读书报告》 3 / 6 还可以参用依次减少塔板数,直至所需的回流比变得非常大为止(期间假定进料级数随总级数的增加维持一个固定的比值);对于最小回流比的确定,可以不断的增加塔的级数,直至回流比不再下降为止[1]。 1.3. 进料位置的计算 Brown和Martin建议,适宜进料位置的确定原则是:在操作回流比下精馏段与提馏段理论板数之比,等于在全回流条件下用Fenske公式计算得到的精馏段与提馏段理论塔板数之比[5],即:
,,,,,lg[()()]lgDlkFhkDhkFlkmrlkhk
xxxxN= (6)
,,,,,lg[()()]lgFlkBhkFhkBlkmslkhk
xxxxNa (7)
同时,NrNmrNrNsNNsNms,可得进料板数为Nr+1。经验表明,如果精馏塔两产品D和B量大致相当,此方法计算结果较准确。 Kirkbrideulead提出了一个近似确定适宜进料位置的经验式:
,,B20.206RS,,NB=[()()()]NHKFLKLKFHKD
zx
zxD (8)
上述两种方法中,后者的计算结果稍好一些。 2. 精馏塔的优化
精馏过程的优化分为设计优化和操作优化。设计优化是根据目标函数求解最优的设计参数和操作参数,如塔板数、进料位置、回流比、操作压力等,以解决工艺和设备设计问题。精馏过程的操作优化是在保证产品质量和稳定操作的前提下,通过改变回流比、进料位置、进料状态等来提高产率,节能降耗[6],而对塔硬件不做改动。 在完成了物料和能量平衡自后,就可以用简捷法计算出设备的尺寸,然后可以用Douglas J. M在其著作《化工过程的概念设计》[3]附录E中给出的计算方法《读书报告》 4 / 6 计算出设备的建设费用和操作费用。对于单个设备的设计优化问题,通常都具有类似的结构:一个费用模型和若干个用等式来表示的约束条件;其都会表现出相似的特征:即在单调增与单调减的费用函数之间求取平衡,而且复合函数往往会有一个极值。现在比较通用的优化方法是选择一个目标函数,该目标函数可以包含设备费用和操作费用。比较常用的目标函数有:年度总费用(total annual cost,
TAC,capital costTAC= +energy costpayback period), 利润等。实际操作的时候通常是固定其余的优化变量,拿其中一个变量在合适的取值范围内寻找使目标函数取得极值的值,然后换做其他变量,依次迭代进行。这种优化措施虽然效果很好,但却很费时,所以对某些影响不明显变量,优化的时可以适当放宽步长。同时对于其他变量的优化,不一定都要追求最优解,有些情况下也可以用次优解代替。 当考虑循环的优化问题时,我们把循环的优化定义为影响一个循环回路内所有设备的投资和操作费用的某个设计变量的优化[3]。以下的讨论仅针对单塔操作进行。 2.1. 操作压力的优化 常规精馏塔单塔的压力优化相对较简单,在满足塔顶冷凝器的温度可以在最炎热的夏季也能够用自来水冷却的前提下,可以参用相对较低的操作压力以减少再沸器的热负荷。在实际设计的时候,由于增加壁厚而增加的设备费用将随着压力的增加而增大,在满足分离要求的前提下,低压(正压)相对有利。 2.2. 理论塔板数与回流比的优化 精馏塔最主要的设备就是塔器(高度L和直径D),以及两台换热器。其他较小的设备,例如机泵阀门以及回流罐,很少在概念设计阶段就予以考虑。塔盘的成本比起塔器和换热器而言显得很小,通常也忽略不计。对于精馏塔设计经济核算优化,经常使用比较简单的目标函数,例如年度总费用。对于塔板数和回流比的优化,都是在固定其他变量的情况下,单独变化塔板数或者回流比,计算出对应的年度总费用,然后找出使得年度总费用最小的塔板数或回流比。此时,往往需要采用迭代计算,以求出在所有变量的最优解。 《读书报告》 5 / 6 2.3. 进料位置和进料状态的优化 陆锡恩老师对精馏塔的进料状态[7]和进料位置[8]对整个精馏塔的操作费用的影响作了比较详细的论述,并得出了一些很有指导性的结论。 1). 进料状态对精馏塔操作费用的影响: (1)对于塔顶产品占主要比例的蒸馏塔,进料的气化率对塔釜再沸器的热负荷影响十分显著,随气化率的上升,再沸器热负荷以较大的比例下降,与此同时,塔顶冷凝器的热负荷只有中等程度的变化。此时进料以露点或过热为宜。 (2)对于塔釜产品占主要比例的蒸馏塔,进料的气化率对塔顶冷凝器的热负荷影响较为显著,随气化率的上升,冷凝器的热负荷以较大的比例增加,与此同时,塔釜再沸器的热负荷只有中等程度或很小的变化。对于冷凝器处于低温状态,使用冷剂的价格较高时,进料为泡点或过冷时,会取得十分显著的经济效益。 (3)当蒸馏塔进料来自上游塔的塔顶采出时,且该蒸馏塔塔顶出料占主要比例,则上游塔塔顶采出以气相为宜,而不应取泡点出料。这样前后两塔可以节省能耗。 2). 进料位置对精馏塔操作费用的影响: 蒸馏塔的最佳进料板位置可以从3个方面进行定义:①相同分离要求及板数下,回流比最小或冷凝器、再沸器热负荷最小;②相同板数及回流比下,塔顶和塔釜产品的分离纯度最高;③相同分离要求和回流比下,所需塔板数最少。 对于进料位置的优化,通常要借助计算机软件,采用灵敏度分析来进行。通常是在可行的进料板数范围内,逐板寻找使得热负荷最小的塔板作为进料板。
3. 总结
塔设计是塔优化的前提。在给定分离要求的前提下,对于塔设计就是要寻找适当的塔板数、回流比、进料位置、操作压力等来满足分离要求,得到满足要求的产品。塔优化是在塔设计提供的各个参数值作为初值的基础上,利用某个目标函数来完成设备费用和操作费用的权衡,使得操作费用和设备费用的总和最小,利润最大化。