乙醇精馏节能展望
国内乙醇发展现状及发展趋势

国内乙醇发展现状及发展趋势近年来,随着环保意识的增强和对可再生能源需求的提高,乙醇燃料逐渐成为国内能源领域的一项重要发展方向。
乙醇燃料是一种以生物质为原料通过发酵和蒸馏制得的液体燃料,具有低碳排放、可再生、燃烧清洁等优点,被广泛应用于汽车燃料和工业燃料等领域。
国内乙醇发展已经取得了一定的成绩。
首先,乙醇汽油的推广应用逐渐扩大。
乙醇汽油是指将乙醇与传统汽油按一定比例混合而成的燃料,目前国内已经形成了乙醇汽油的生产和销售体系。
根据国家能源局的数据,截至2021年底,全国共有357个乙醇汽油混合泵站,乙醇汽油销售量达到了260万吨。
其次,乙醇燃料乙二醇产业也在不断发展壮大。
乙二醇是一种重要的有机化工原料,广泛应用于纺织、化妆品、塑料等领域。
目前国内乙二醇产能处于高位运行状态,年产量已超过1000万吨。
然而,国内乙醇发展还面临着一些挑战和问题。
首先,乙醇燃料的生产成本相对较高。
由于乙醇燃料的生产需要大量的生物质原料和能源消耗,导致其成本较传统燃料高出一定比例。
其次,乙醇燃料的供应链建设仍不完善。
乙醇燃料的生产、储运和销售环节还存在一些问题,如生产设施不足、运输成本高、销售渠道不畅等,限制了乙醇燃料的推广和应用。
此外,乙醇燃料的技术瓶颈也是制约其发展的一个重要因素。
乙醇燃料的燃烧效率和动力性能相对传统燃料还有一定差距,需要进一步改进和提升。
为了推动国内乙醇发展,未来需要采取一系列措施。
首先,加大对乙醇燃料产业的政策支持力度。
国家应出台相关政策,提供财政补贴和税收优惠等扶持措施,降低乙醇燃料的生产和销售成本。
其次,加强乙醇燃料的科研和技术创新。
通过技术研发,提高乙醇燃料的燃烧效率和动力性能,降低其对发动机的影响。
同时,加强乙醇燃料的生产技术改进,提高生产效率和产品质量。
另外,加强乙醇燃料的供应链建设和市场拓展。
通过加大乙醇汽油混合泵站的建设和乙醇燃料的销售渠道拓展,提高乙醇燃料的供应稳定性和市场覆盖度。
总的来说,国内乙醇发展正处于快速发展阶段,取得了一定的成绩。
酒精蒸馏生产节能技术

酒精蒸馏生产节能技术摘要:我们国家的酒精生产行业呈现出发展速度持续加快的趋势,生产过程中主要采用手工蒸馏方法,因而要对蒸馏环节加以重点关注。
众所周知,蒸馏环节消耗的能量是非常大的,所以要对节能技术加以合理应用,如此可以使得生产成本控制在合理的范围内,可持续发展也可实现,除此以外,酒精产品的质量会有大幅提升。
对于酒精生产行业来说,应该要依据自身的实际情况对节能控制方法进行深入探索,如此方可保证市场竞争力大幅增强,进而使得行业发展更为稳健。
关键词:酒精;蒸馏生产;节能措施引言:在进行酒精生产时,蒸馏环节是不可忽视的,其对产品质量、产量均会产生直接影响,而且此环节消耗的能量也是非常大的。
从我们国家的食用酒精生产的现状来看,手工蒸馏操作的应用是较为常见的,因而在当下要对节能技术加以深入的研究,在保证产品质量达到要求的前提下,对能量消耗加以严格控制,如此方可使得企业投入的成本大幅降低,市场竞争力也会明显增强,自身的可持续发展也就可以得到保证。
1传统酒精蒸馏生产耗能状况1.1传统的直接发酵法过去很长一段时间内,酒精生产采用了传统发酵方法,也就是将原料确定后对其进行蒸煮,达到糊化状态后掺入淀粉酶,确保液化、糖化目的达成,之后将酵母加入其中,这样就可实现酒精的转化。
然而在新阶段,能源短缺问题越发严重,不少的国家针对节能技术展开深入研究。
众所周知,传统发酵方法需要消耗的能量是非常大的,尤其是蒸馏、发酵阶段的耗能所占比例达到了60%至70%,因而在当下,相关人员的研究方向放在了如何让生淀粉能够直接进行酒精发酵,以期使得能耗大幅降低[1]。
1.2传统发酵法对传统原料进行蒸煮的过程中,糖化的实现难度是较大的,导致此种情况出现的原因是生淀粉分子有着自身的排列组合顺序,而且其细胞壁呈现出质地坚硬的特征,虽然经过了发酵,也很难破坏,如果这两个影响因素未能消除的话,原料想要经过发酵实现糖化是较为困难的。
在蒸煮原料的过程中,植物当中存在的生淀粉会发生糊化,持续的高温能够实现杀菌目的,这样一来,酒精产品的安全性就可得到保证,质量也会有明显提升,此种方法还可使得糖化发酵的便捷性大幅提升,并保证现行的酒精标准能够执行到位[2]。
精馏过程节能技术综述

精馏过程节能技术综述现代工业生产过程中,精馏过程是十分常见的一种操作,用于从混合物中分离出不同组分。
然而,传统的精馏过程存在能源浪费的问题,因为它需要大量的能源来进行加热和冷却。
因此,如何降低精馏过程的能源消耗成为了一个重要的研究方向。
在过去的几十年里,研究人员提出了多种节能技术,以下综述了一些常见的节能技术。
首先,改进传统精馏塔的设计是一种简单但有效的节能方法。
例如,使用多级精馏塔可以增加分馏塔的效率,减少需加热和冷却的动力。
此外,增加塔内的换热面积也可以改善能量利用率。
此外,通过使用先进的塔内填料和分布器,可以提高物质的传质效率,从而减少所需的塔高和物料回流比例。
其次,热力耦合是另一种常用的节能技术。
该技术通过将不同温度的流体进行热交换,来降低能源消耗。
例如,实施热力耦合可以将进出精馏塔的气体进行热交换,从而降低所需的加热和冷却负荷。
此外,热力耦合还可以用于塔内热交换,例如通过使用塔内回流来预热进入精馏塔的物料。
另外,采用较低的工艺温度和压力也可以有效地减少精馏过程的能耗。
降低工艺温度可以减少所需的加热负荷,而降低工艺压力可以减少所需的冷却负荷。
因此,在设计和操作精馏过程时,应考虑选取较低的工艺温度和压力,以降低能源消耗。
此外,使用较低的辅助能源,如太阳能、余热等,也是一种常用的节能技术。
太阳能可以用于提供所需的加热或冷却能量,从而降低对传统能源的依赖。
余热是指在其他工艺过程中产生的废热,在精馏过程中可以被回收利用,用于提供所需的加热或冷却能源,进一步减少能源消耗。
最后,引入新的分离技术也是提高精馏过程能耗效率的一种途径。
例如,膜分离技术被广泛应用于分离混合物中的气体或液体组分,并且其能耗通常较低。
相比传统的蒸馏过程,膜分离技术不需要额外的加热和冷却能源,因此能够有效地节约能源。
总的来说,精馏过程节能技术的研究和应用对能源的合理利用具有重要意义。
通过改进传统精馏塔的设计、热力耦合、降低工艺温度和压力、使用低辅助能源和引入新的分离技术等方法,可以有效地降低精馏过程的能耗。
精馏过程的节能降耗

精馏过程的节能降耗精馏过程在化工产业中是一项重要的分离技术,但是它也是能耗较高的过程。
为了降低能耗,节能降耗已经成为精馏技术的一个重要研究方向。
本文将介绍几种精馏过程的节能降耗技术。
首先,提高精馏塔的热效率是提高精馏过程的一个关键。
一种常见的做法是引入换热器网络来最大程度地利用出塔冷凝液和进塔蒸汽之间的热量传递。
这种方法可以降低所需的蒸汽量,从而降低了能耗。
此外,还可以使用多效精馏、热泵或采用废热回收技术进一步提高热效率。
其次,提高精馏过程的物质效率也是节能降耗的一个重要途径。
物质效率是指在精馏过程中使用的干燥剂或者吸附剂能够更有效地去除杂质,从而减少能耗。
通过改进精馏塔的操作条件,如温度、压力和液体流速等参数,可以提高物质效率。
同时,使用高效的精馏填料或者塔板也能够提高分离效果,减少杂质的含量。
此外,使用先进的辅助技术可以进一步降低精馏过程的能耗。
例如,在精馏过程中引入膜分离技术可以减少能源消耗。
膜分离技术是一种基于材料表面或孔隙的选择性渗透性原理分离混合物的方法。
与传统的溶剂萃取或者蒸馏技术相比,膜分离技术具有能耗低、操作简单、体积小等优点。
通过将膜分离技术与精馏过程相结合,可以实现更高效的分离效果。
最后,优化精馏过程的操作策略也是节能降耗的一个重要途径。
通过优化参数设定和控制策略,可以使精馏过程更加稳定和高效。
例如,采用先进的控制算法,如模型预测控制或者模糊控制算法,可以实现对精馏过程的快速响应和精确控制,从而降低了能耗和运行成本。
总的来说,精馏过程的节能降耗是一个涉及多个方面的工程问题。
通过提高热效率、物质效率,使用先进的辅助技术和优化操作策略,可以有效地降低精馏过程的能耗。
这些节能降耗技术不仅可以减少环境污染,还可以提高精馏过程的经济效益。
因此,精馏过程的节能降耗在工业应用中具有重要的意义。
精馏过程的节能降耗

精馏过程的节能降耗摘要:精馏过程的节能,对于减少能源消耗,降低生产成本和保护环境具有十份重要的意义。
在精馏过程中可以采用最适宜回流比操作和最佳进料状态,使用中间冷凝器和中间再沸器,多效精馏技术、热泵精馏技术。
合理安排多组分物料分离流程,提高过程的分离效率、提高物料回收率,进而降低能耗。
并介绍我国精馏过程的节能现状与趋势。
关键词:精馏过程;节能;回流比;降耗,0前言在化工生产过程中,分离是非常重要的一个过程单元,它直接决定了最终产品的质量和收率,工业生产中占据着主导地位的分离方法就是精馏。
精馏是利用混合物中各组分挥发度的不同利用能量进行分离的操作单元,具有独特的优势。
据估计,化工过程中40%~70%的能耗用于分离,而精馏能耗又占其中的95%。
因此随着世界能源的日益短缺,精馏过程一直是研究者节能挖潜的热点对象,它的每一个进展都会带来巨大的经济效益。
多年来,人们已采用了多种方法和手段对精馏过程进行节能降耗的研究,按照流程是否改变及是否利用过程技术可以将其分为三类:1)利用过程技术对精馏塔的操作条件进行优化,以减少精馏塔所消耗的能量,如以产品物流预热进料、增加塔板数、减小回流比、增设中间再沸器和中间冷凝器等;2)开发了许多高效节能的特殊精馏工艺流程,如热泵精馏、多效精馏等。
1.1最适宜回流比和最佳进料状态[1]回流比直接影响再沸器和冷凝器的热负荷,决定精馏分离的净功耗,因此大体上确定了操作费用,同时还与塔设备的投资密切相关。
在最小回流比Rmin附近,随R的增长,操作线与平衡线间的距离增大,达到规定分离要求所需的塔板数减少,使得设备费用下降。
如果进一步增加回流比,在塔板数减少的同时,塔中蒸汽流率和换热器热负荷的增大,造成塔径、再沸器和冷凝器传热面积增大,使设备费用增加。
因此,应当根据总费用最小原则来选取适宜回流比。
进料状态(用加料状态参数q表示)的不同,将造成塔中精馏段和提馏段气液相流率的变化,从而影响R,以及达到规定分离要求所需的理论板数和再沸器和冷凝器的热负荷。
乙醇行业发展前景与机遇展望报告
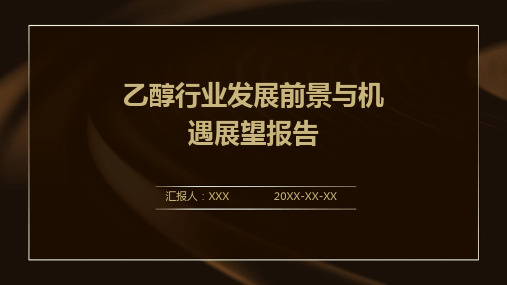
03
随着环保意识的提高和能源结构的调整,乙醇的应用前景 更加广阔。
乙醇的生产方法和现状
01
目前乙醇的主要生产方法有生物 发酵法和化学合成法。
02
生物发酵法是利用淀粉、纤维素 等含糖物质发酵生产乙醇,具有
成本低、环保等优点。
化学合成法是利用乙烯等原料通 过化学反应生产乙醇,具有工艺 成熟、生产效率高等优点。
CHAPTER 03
乙醇行业的机遇与挑战
政策环境对乙醇行业的影响
政策支持
政府出台相关政策鼓励乙醇行业的发 展,如生物燃料产业发展政策、可再 生能源发展政策等,为乙醇行业提供 了良好的发展环境。
限制措施
政府对环保要求的提高,对乙醇行业 的生产工艺和排放标准提出了更高的 要求,增加了企业的环保成本。
中国乙醇行业发展概况
中国乙醇行业在政策扶持和市场需求的双重驱动下快速发展,尤其在生物燃料领域取得显著成果。
中国政府出台了一系列政策鼓励生物燃料产业发展,如提高乙醇汽油掺烧比例、扩大生物燃料应用领 域等。
乙醇行业的技术创新和突破
纤维素乙醇技术取得重大突破,利用 农业废弃物如秸秆、稻草等进行发酵 生产乙醇成为可能,降低了生产成本 。
政策支持
政府对可再生能源产业的支持力度加大,为乙醇 行业发展提供了有力保障。
技术进步
新技术的研发和应用有助于降低生产成本,提高 产品质量和市场竞争力。
乙醇行业的投资策略和建议
深入研究市场,了解客户 需求。
关注政策动向,把握政策 机遇。
投资策略
01
03 02
乙醇行业的投资策略和建议
• 加强技术研发,提高产品竞争力。
乙醇行业发展前景与机 遇展望报告
酒精蒸馏生产节能技术探析
酒精蒸馏生产节能技术探析摘要:目前,我国大多数酒精生产行业,都采用手工蒸馏操作的方法生产,在酒精生产的过程中,蒸馏既是最重要的生产环节,同时也是整个生产过程中能量消耗最多的环节。
因此,采用节能技术生产酒精蒸馏,不仅有利于酒精生产企业降低生产成本,实现可持续发展策略,还能够在满足合格酒精产品的要求上,实现节能控制的需求。
因此,酒精生产行业应积极探索节能控制的方法与手段,只有这样才能提升酒精行业的市场竞争力,并为酒精市场开拓出一片新的天地。
关键词:酒精;蒸馏生产;节能措施1 酒精蒸馏生产耗能现状1.1 最佳回流比的调节问题自国家食用酒精新标准GB10343—2008发布实施后,各普通级食用酒精生产品企业采用工艺都是三塔蒸馏—即粗馏塔、醛塔和精馏塔或是粗馏塔、精馏塔和甲醇塔。
在精馏塔中,较高纯度的酒精蒸气聚集在塔顶并经过塔顶冷凝器冷却成液体,贮存在贮罐中,其中一部分作为最终产品而采出,另一部分作为回流返回蒸馏塔。
回流量的大小取决于酒精生产要求的纯度,同时受设备运行状况的影响。
而回流量又在很大程度上决定了蒸馏过程的耗量消耗。
如何控制好工艺,在保证产品质量的前提下尽可能地节能,是蒸馏生产的难题。
1.2 采用直接加热蒸馏工艺在酒精生产企业中有很多企业采用蒸气直接加热醪液的生产工艺,因为是直接加热。
不能很好地利用好蒸气冷凝水回转供应锅炉生产用水,该蒸馏工艺既浪费了蒸气冷凝水又可能过多产生废液,同时也增加了能耗。
1.3 蒸馏生产是手动操作系统很多酒精生产企业在蒸馏生产中没有安装DCS自动操作系统,全部采用手动操作,而由于酒精蒸馏控制系统具有复杂性的特点,手动操作很难平衡生产的各参数,进气、排废操作也不能稳定,因此在生产中也易产生用汽过大而塞塔,从而影响产品质量,也耗去大量的蒸气,进而造成能耗的增加。
1.4 余热利用率低没有充分利用再沸器设备进行余热回收,特别是精塔废液的余热回收工作做得不好,造成高温废液中的低热值水蒸气随废液排走而造成浪费,无形中增加能耗。
化工精馏节能技术探讨
化工精馏节能技术探讨化工精馏是一种广泛的分离技术,广泛应用于炼油、化工、精细化工、制药等行业。
由于化工精馏的能耗和排放量较高,为了减少对环境的影响以及降低生产成本,探究化工精馏节能技术的应用显得十分重要。
一、精馏原理精馏是一种将混合物中的组分分离为一系列固定沸点组分的方法。
在一个精馏塔中,混合物在塔底蒸发后升往塔顶,通过多级板或者填料进一步蒸馏和分离。
不同沸点的组分会在不同的塔板或填料层凝结、液化分离出来。
经过多次分离,可以得到高纯度的分离产物。
二、节能措施1. 优化工艺参数通过客观分析和实验对化工精馏的工艺参数进行优化,可以达到节能的目的。
优化参数包括塔径、进料温度、进料速率、再沸点的选择等。
优化参数的主要目的是降低热量的损耗,提高再沸进料的回收,提高产品的纯度。
2. 应用热力学分析方法化工精馏通过热量供给来产生馏出性的分级蒸馏过程。
对于具有相同沸点的混合物,应用热力学分析方法来计算馏出程度,优化精馏条件,可达到节约热量、降低气体排放的目的。
3. 利用先进的装置技术采用先进的塔板、塔壳、填料技术,可以优化气液流动、充分利用热量,提高馏分的产量和质量。
例如,采用结构平面装置来提高塔顶的分馏效果,以及选用有效的填料来提高再沸孔的分馏效果等,都是有效的节能措施。
4. 优化回收系统采用高效的回收系统能够有效地提高化工精馏的再利用效益。
例如,实施热回收技术来回收热量和回收常温下的再沸馏分等都能达到节能的目的。
三、总结化工精馏在工业生产和人类生活中有着广泛的应用,同时其高耗能、高排放的特点也给环境带来了不小的影响。
为了减少对环境的影响,降低生产成本,我们需要探究化工精馏的节能降耗技术。
采取以上措施,能够有效地降低化工精馏的能耗和排放,提高生产效益,是企业可持续发展的重要措施。
精馏过程节能技术综述
精馏过程节能技术综述摘要:精馏是化学工业中高能耗的操作单元,在当今能源紧缺的情况下, 对精馏过程的节能技术进行研究具有重要的社会意义和实际意义。
本文从精馏过程中热能的充分利用,提高精馏系统的热力学效率以及减少精馏过程对能量的需要这三大主要方面介绍了精馏过程的节能措施,对各个类型的主要节能方法、优缺点和适用范围进行了较为详细的叙述,并介绍了我国精馏过程节能技术的发展现状与趋势。
关键词:精馏节能前言:精馏过程是一个伴随传热和传质的复杂过程,被广泛应用于石油化工和精细化工等领域,是化学生产中主要的能源消耗环节,具有变量多、机理复杂等特点。
据相关资料统计,化工生产过程中有40%~70%的能耗用于分离过程,而精馏所消耗的能量就占据了其中的95%。
自从世界性的能源危机爆发以来,精馏过程的节能问题已经引起了人们的广泛重视。
因而降低精馏过程中的能耗,对于节约能源,降低生产成本有着至关重要的作用,本文就精馏过程中的节能措施进行了详细的介绍。
1.精馏过程节能技术现状:目前,随着化工生产中分离物料的组分不断增多,对产品纯度的要求也不断提高,但精馏装置操作往往偏于保守,操作方法、操作参数设置不尽合理。
典型的单级精馏装置中,混合物料从某一中间位置进入塔内,塔内设有塔板或填料促进汽液两相之间的相互接触,塔底液相在再沸器中被加热,塔顶的蒸汽在冷凝器中冷凝为馏出液。
在该精馏过程中所消耗的绝大部分能量被冷却水或分离组分带走,并非用于实际的组分分离,因此精馏过程的节能技术具有广阔的发展空间。
近年来,世界能源短缺状况加剧,各国对精馏节能技术的研究都很重视,以精馏过程节能技术为中心的研究和应用得到了飞速的发展。
据统计,我国的炼油厂消耗的原油占其炼油量的8%~10%,其中很大一部分消耗在了精馏过程中。
在现今能源资源紧缺的情况下,对精馏过程的节能研究就变得十分重要。
2. 充分利用精馏系统的热能:这类节能技术主要包括保温隔热,回收物料的部分显热或潜热,优化热交换器这三种方法。
乙醇燃料的技术改进和创新发展
乙醇燃料的技术改进和创新发展随着能源需求的不断增长和环保意识的加强,乙醇燃料作为一种新型清洁能源逐渐受到人们的关注。
乙醇燃料可以作为汽车、机器等各种机械设备的能源来源,同时也可以用作航空燃料和燃料电池等应用领域。
但是,乙醇燃料在其生产、储存和运输等方面仍然存在一些技术难点和瓶颈,需要不断进行技术改进和创新发展,以应对未来的新型能源需求。
本文将针对当前乙醇燃料技术发展的现状和挑战,探讨其技术改进和创新发展的方向和措施。
一、现状及存在的问题乙醇燃料的生产主要采用玉米、小麦、甜菜等作物为原料,经过发酵和蒸馏等工艺制成乙醇燃料。
目前,乙醇燃料已经成为全球应用最为广泛的生物质能源之一,但是其应用仍存在一些问题。
首先,乙醇燃料的生产成本较高。
乙醇燃料的生产需要消耗大量的原材料和能源,同时,生产过程中还会产生大量的二氧化碳等排放物,这些都会增加生产成本。
其次,乙醇燃料的储存和运输难度较大。
由于乙醇燃料具有易挥发、易吸水等特性,需要在生产后立即输送到使用地点,否则就会发生质量变化,影响使用效果。
同时,乙醇燃料运输过程中,还需要考虑安全问题。
最后,乙醇燃料的应用范围仍然不够广泛。
由于乙醇燃料的生产和应用仍处于起步阶段,各国的政策法规、技术标准等尚未完全统一,这给乙醇燃料的应用带来了一些限制。
二、技术改进方向针对当前乙醇燃料存在的问题,可以从以下几个方面进行技术改进。
1.生产技术的改进。
为了降低乙醇燃料的生产成本,可以通过开发新型的生产工艺、优化生产流程等手段来提高生产效率。
比如,可以采用生物质催化裂解、化学催化转化等技术来实现乙醇的高效生产。
2.储存和运输技术的改进。
为了保证乙醇燃料的质量和稳定性,可以采用新型储存和运输方法。
比如,可以采用气体吸附、离子交换等技术来改善乙醇燃料的储存条件;可以采用专用运输设备,例如贮箱、泵等来保证乙醇燃料的运输安全。
3.应用技术的改进。
为了推广和应用乙醇燃料,可以加强相关政策的制定和推广,同时开发新型的应用技术,以提升乙醇燃料的适用性和竞争力。
- 1、下载文档前请自行甄别文档内容的完整性,平台不提供额外的编辑、内容补充、找答案等附加服务。
- 2、"仅部分预览"的文档,不可在线预览部分如存在完整性等问题,可反馈申请退款(可完整预览的文档不适用该条件!)。
- 3、如文档侵犯您的权益,请联系客服反馈,我们会尽快为您处理(人工客服工作时间:9:00-18:30)。
山东科技职业学院毕业设计(论文)题目乙醇精馏节能展望专业应用化工技术年级###姓名###指导教师###定稿日期: 2014 年 4 月 20日目录一.引言 (1)二.乙醇精馏提纯的基本原理 (2)三.乙醇精馏提纯的研究 (2)1.进料状态和进料位置的选择 (2)2.塔顶回流比的选择 (3)3.精馏过程进料温度的选择 (4)4.集热共沸精馏 (4)5.多效精馏节能技术 (5)6.高效导向筛板 (6)7.乙醇精馏的新进展及发展方向 (6)8.分割式热泵精馏节能技术 (7)9.乙醇精馏的新进展及发展方向 (8)四.结论 (8)参考文献 (8)致谢 (8)乙醇精馏节能展望###摘要:精馏塔广泛应用于工业乙醇的生产中,精馏过程的能耗占总能耗的比例相当大,精馏系统的节能在化学工业的节能中占有越来越重要的地位,也是企业的节能重点。
因此,在精馏系统的设计时需进行节能优化。
实际上,在精馏塔设计时如果能够合理选择进料状态和最佳回流比,以及进料位置和进料温度的合理确定,采用节能工艺回收利用余热,均能得到较好的节能效果。
不同的乙醇混合物精馏所采用的工艺参数是不同的,本文结合学习内容及实习期间学到的知识以乙醇-水的混合物精馏展开研究。
Future ethanol distillationZhang JianliangAbstract:distillation is widely used in the industrial production of ethanol, the energy consumption of distillation process accounted for the proportion of total energy consumption is quite large, energy-saving distillation system plays more and more important role in energy saving of the chemical industry, energy saving is the key of enterprise. Therefore, in the design of distillation system is required when the energy optimization. In fact, in the distillation tower design if reasonable selection of tower and filler, select the optimum reflux ratio, and reasonably determine the feed temperature and position, can get good effect of energy saving.一.引言乙醇是重要的有机溶剂,广泛用于医药、涂料、卫生用品、化妆品、油脂等各个方面。
乙醇做为一种有机溶剂,用于消毒剂、洗涤剂、工业溶剂、稀释剂、涂料溶剂等几大方面,其中用量最大的是消毒剂,浓度为70%~75%的乙醇溶液的杀菌能力最强;做为基本有机化工原料,乙醇可用来制取乙醛、乙醚、乙酸乙酯、乙胺等化工原料,也是制取医药、染料、涂料、洗涤剂等产品的原料;乙醇还可以调入汽油,作为车用燃料,美国销售乙醇汽油已有20年历史。
中国乙醇在汽油的比重占10%。
无水乙醇又称无水酒精,指浓度大于99%(质量)的乙醇。
主要作为溶剂,用于化妆品、制药等工业。
精馏塔是进行精馏的一种塔式汽液接触装置,又称为蒸馏塔。
有板式塔与填料塔两种主要类型。
根据操作方式又可分为连续精馏塔与间歇精馏塔。
蒸气由塔底进入,与下降液进行逆流接触,两相接触中,下降液中的易挥发(低沸点)组分不断地向蒸气中转移,蒸气中的难挥发(高沸点)组分不断地向下降液中转移,蒸气愈接近塔顶,其易挥发组分浓度愈高,而下降液愈接近塔底,其难挥发组分则愈富集,达到组分分离的目的。
由塔顶上升的蒸气进入冷凝器,冷凝的液体的一部分作为回流液返回塔顶进入精馏塔中,其余的部分则作为馏出液取出。
塔底流出的液体,其中的一部分送入再沸器,热蒸发后,蒸气返回塔中,另一部分液体作为釜残液取出。
精馏塔的工作原理是根据各混合气体的汽化点(或沸点)的不同,控制塔各节的不同温度,达到分离提纯的目的。
化工生产常需进行液体混合物的分离以达到提纯或回收有用组分的目的,精馏操作在化工、石油化工、轻工等工业生产中中占有重要的地位。
为此,掌握气液相平衡关系,熟悉各种塔型的操作特性,对选择、设计和分析分离过程中的各种参数是非常重要的。
要想把低纯度的乙醇水溶液提升到高纯度,要用连续精馏的方法,因为乙醇和水的挥发度相差不大。
精馏是多数分离过程,即同时进行多次部分汽化和部分冷凝的过程,因此可使混合液得到几乎完全的分离。
化工厂中精馏操作是在直立圆形的精馏塔内进行的,塔内装有若干层塔板或充填一定高度的填料。
为实现精馏分离操作,除精馏塔外,还必须从塔底引入上升蒸汽流和从塔顶引入下降液。
可知,单有精馏塔还不能完成精馏操作,还必须有塔底再沸器和塔顶冷凝器,有时还要配原料液预热器、回流液泵等附属设备,才能实现整个操作。
乙醇是用途广泛和用量极大的工业原料之一,在国民经济各部门中占有重要地位,与人民生活有着密切的关系。
乙醇广泛应用于食品、化工、医药、染料、国防等行业,同时也是十分重要的清洁能源。
精馏技术还是目前分离乙醇水体系的主要方法,但精馏技术能耗很高,特别是处于能源紧缺的现代,而且乙醇一水体系又是具有最低共沸物的体系,体系沸点组成及物理性质如下表所示:名称分子式分子相对质量密度20℃kg/m³沸点101.33kPa℃比热容20℃kg/(kg•℃)粘度20℃mPa.S导热系数20℃ω/(m•℃)表面张力σ×10³20℃N/m水H2O 18 998 100 4.183 1.005 0.599 72.8乙醇C2H5OH46 789 78.3 2.39 2.15 0.172 22.8二.乙醇精馏提纯的基本原理精馏是化工生产中分离互溶液体混合物的典型单元操作,其实质是多级蒸馏,即在一定压力下,利用互溶液体混合物各组分的沸点和饱和蒸汽压的不同,使轻组分(即沸点低和饱和蒸汽压高的组分)汽化,经过多次液相汽化和气相冷凝,使气相中的轻组分和液相中的重组分浓度逐渐升高,从而实现分离。
精馏过程中的主要设备有精馏塔、再沸器、冷凝器、预热器、储罐和输送设备。
精馏塔以进料板为界限,上部为精馏段,下部为提馏段。
一定温度和压力的物料进入精馏塔后,轻组分(CH3CH2OH )在精馏段逐渐浓缩,离开塔顶后经冷凝器冷却全部进入回流罐,馏出的轻组分(CH3CH2OH )一部分做为做为成品,一部分做为回流液重新进入精馏塔,进入精馏塔的目的主要有两个原因,一是补充塔板上的轻组分,使塔板上的液体组成保持稳定,二是将精馏塔顶温控制在一个稳定的范围内,保证精馏操作连续稳定的进行。
而重组分(即残液)做为塔釜产品排除。
精馏过程中绝大部分能量都消失在塔顶冷凝器中的泠凝水水和塔釜残液中。
三.乙醇精馏提纯的研究1.进料状态和进料位置的选择进料分为5种状态,分为过冷进料(q>1);泡点进料(q=1);气液混合进料(0<q<1);饱和蒸汽进进料(q=0);过热蒸汽进料(q<0);泡点进料时精馏段和提馏段的塔径相等,设计和制造比较方便,是精馏塔较为理想的进料状况,当进料状况发生变化时,应适当改变进料位置,并及时调节回流比R。
一般精馏塔常设几个进料位置,以适应生产中进料状况,保证在精馏塔的适宜位置进料。
如进料状况改变而进料位置不变,必然引起馏出液和釜残液组成的变化。
进料位置对精馏操作有着重要意义。
不同的进料状况,都显著地直接影响提馏段的回流量和塔内的汽液平衡。
当进料口位置高于最佳进料口时,会使在此状态下的进料板的液相组成中的轻组分(CH3CH2OH )高于最佳位置下该板的液相组成的轻组分(CH3CH2OH ),重组分(H₂O)低于最佳位置下的液相组成,相对于最佳位置而言,精馏段的塔板数减少,提留段的塔板数增加,所以此时塔顶产品质量会下降,同理,当进料口位置低于最佳进料口时,会使在此状态下的进料板的液相组成中的轻组分(CH3CH2OH )低于最佳位置下该板的液相组成的轻组分(CH3CH2OH ),重组分(H₂O)高于最佳位置下的液相组成,相对于最佳位置而言,精馏段的塔板数增加,提留段的塔板数减少,所以此时塔顶产品质量会提高重组分(CH3CH2OH)的含量。
在相同的分离条件下,非最佳进料位置将增大回流比,导致塔釜热负荷增大。
从理论上分析,当塔有几股进料时,不同组成的物料进入不同的位置,其分离效果最佳,节能也较显著,这是因为不同组成的物料混合就是有效能损失的过程。
2.塔顶回流比的选择(1)回流比R对设计的影响回流比R是精馏过程的设计和操作的重要参数。
R直接影响精馏塔的分离能力和系统的能耗,同时也影响设备的结构尺寸。
当回流比增大时精馏段操作线斜率R/(R+1)增大,则精馏段操作线远离平衡线,如图中绿线所示。
使得精馏塔内各板传质推动力及增大,使各板分离能力提高。
为此,完成相同分离要求,所需理论板数将会减少,由13块减为10块理论板。
然而由于R的增加导致塔内气、液两相流量增加,从而引起再沸器热流提高。
从而使精馏过程能耗增加,气相流量V及V'将影响塔径的设计。
需要的理论板数N的减少,可降低塔的高度。
(2)随着回流比R的减小,则精馏过程的能耗下降,塔径D也回随之减小。
但因R减小,使操作线交点向平衡移动,导致过程传质推动力减小,使得完成相同的分离要求所需理论板数N随之增加,使塔增高。
如图所示:当回流比继续减小,使两操作线交点落在平衡曲线上,如图中E点所示。
此时完成规定分离要求所需理论板数为∞。
此工况下的回流比为该设计条件下的最小回流比R min。
由图可得式中x e-平衡曲线上E点液相摩尔分数;y e-平衡曲线上E点气相摩尔分数。
3.精馏过程进料温度的选择精馏塔的分离动力来自塔釜再沸器的热量,而且全塔上下的负荷并不均匀,它与侧线采出和进料工况有关。
一般说来,塔底的气液量比塔顶的大,塔的液泛都从塔底开始。
当进料是冷态时,则要求塔釜再沸器提供较多的热量,也增加了塔底气液量。
对于给定的分离要求,精馏系统所需的热量基本不变,当提高进料温度时,就会减少再沸器的热负荷。
进料温度的降低,将增加塔底再沸器的热负荷,减少塔顶冷凝器的冷负荷;进料温度升高,则增加塔顶冷凝器的冷负荷,减少塔底再沸器的热负荷;当进料温度的变化幅度过大时,常会影响整个塔身的温度,从而改变气液平衡组成。