汽车转向系的发展历史 英文翻译.doc
汽车转向系统的发展

1-方向盘 2-转向轴 3-转向中间轴 4-转向油 管 5-转向油泵 6-转向油罐 7-转向节臂 8转向横拉杆 9-转 向 摇 臂 10-整 体 式 转 向 器 (包 括 转 向 控 制 阀 、液 压 油 缸 、机 械 转 向 器 ) 11-转 向 直拉杆 12-转向减振器
图 1 液压助力转向系统构成
在此过程中,微处理器以 0.004s/次 的 频 率 持 续 不 断 地 反 复 进 行转向角度的计算和转向系统故障 自检,一旦四轮转向系统出现异常或 传感器出现错误时,后轴转向执行电 机立即自动驱动后轴回正,同时系统 由 4WS 模式切换至 2WS (传统的两 前轮转向)的安全转向模式。即便在 转向过程中 ECU 出现灾难性故障, 后轴转向齿条机构内部的回位弹簧 也能够使后轴慢慢回复至中立位置, 并同时使后轴转向电机关闭,以阻止 后轮的转向动作。
min 的发动机转速限制。 空调高压端:检测仪范围为 0~
459kPa,显示电压为 0~5V,所代表的 是空调制冷剂压力传感器的信号,压 力的数值表明安装在发动机上的空 调(A/C)压缩机的负荷,PCM 利用这 个信息来调整怠速并控制冷却风扇。
节气门全开(WOT)时 A/C 关闭 (OFF):检 测 仪 显 示“ 是 ”或“ 否 ”,显 示“是”表明 PCM 已使 A/C 压缩机离 合器继电器关闭,因为节气门位置 (TP)已超过 A/C 压缩机正常工作的
电子控制液压助力转向系也靠 液压力帮助驾驶员转向,但其液压泵 (齿轮泵)是通过电动机驱动的,与发 动机在机械上毫无关系,其助力效果 只与方向盘速度和车辆的行驶速度 有关。
1.系统结构和工作原理 电子控制助力转向系统
向系统。因为液压泵的供油量主要是 由方向盘转角变化量和车速决定的, 其共有特性更符合转向系统对助力 作用的实际要求,因此节省能量,并 能够获得更加理想的转向助力特性。 但是,它在不转向时仍然存在能量损 失,而且液压系统的固有缺陷仍然存
汽车转向系的发展历史

汽车转向系的发展历史大家好,欢迎来到攻城狮频道。
之前我们依次和大家聊过悬架系统、制动系统在基础底盘中,还剩下转向系统。
今天我们就和大家聊一聊转向系统。
在我们开车过程中手肯定是时时刻刻扶着方向盘的,这期视频我们和以前的介绍方式一样,先来说说汽车发展史中转向系统的发展历程。
乘用车的转向系统主要是以齿轮齿条式的为主。
在乘用车的转向系统中主要经历过几个发展阶段:第一阶段,最开始的,就是纯机械助力的转向系统,这种转向系统主要限制于以前的技术水平,车辆的转向全靠驾驶员的手力,毫无驾驶体验可言。
在第二阶段来就发明了液压助力的转向系统,也就是H-PS。
由于是液压助力的,就要有驱动装置,一般搭载液压转向系统的车上都会装个机械液压泵,通过发动机带动液压泵工作。
这种工作模式不仅会增加发动机的负载,而且在车辆没启动的时候,转向时处于无助力状态,会造成某些不便性。
所以后来市场上出现了通过电子液压泵提供转向助力的装置(EH-PS),由电子泵取代了机械泵,电子液压泵虽然能够解决发动机助力的一些弊端,但是液压助力转向系统本身还存在几个比较大的问题,首先就是转向助力的响应比较慢和液压系统的噪音比较大,其次,液压助力系统总体给人的驾驶感受就是方向盘太重,而且液压转向系统的手感调校是通过调节发动机转速和一些液压阀,在一些多种驾驶模式的车上,液压转向器的可调度是受到限制的。
接着就是第三阶段,采用电子助力转向系统阶段,目前市场上,新上市的车型,几乎都采用电子助力转向系统(E-PS)。
电子助力转向系统的工作原理是:当系统中的角度传感器检测到驾驶员的转向意图的时候,把这个信号发给控制器,控制器会做出根据控制策略做出决策,来控制电机的工作。
我们刚刚说的EH-PS是通过电子泵给转向液减压来提供助力的,而E-PS直接通过电机助力,传递效率更高,而且可以通过控制策略的优化,来实现比较好的转向手感。
在电子助力转向系统中,根据电机位置和传动方式的不同,电动助力转向系统中又可以分为C-EPS、P-EPS、DP-EPS和R-EPS,前面三种是通过蜗轮蜗杆传动的,而R-EPS是通过滚珠丝杠结构传动的。
汽车历史发展的有关介绍英语作文

汽车历史发展的有关介绍英语作文The Amazing Story of Cars!Have you ever wondered how cars came to be? Cars are such a big part of our lives today, but they haven't been around forever. The history of cars is a fascinating journey full of brilliant inventors, amazing machines, and world-changing innovation!Way back in the late 1700s, the very first self-propelled vehicles were invented. They were powered by steam engines and looked like small locomotives on wheels. One of the earliest was built in 1769 by a French engineer named Nicolas Joseph Cugnot. His steam-powered tricycle could barely go 4 miles per hour, but it marked the start of an incredible adventure!In the 1800s, many clever people experimented with different ways to power vehicles without using horses or steam. Some tried gas engines, while others used electricity or even gasoline. An important milestone was reached in 1886 when Karl Benz patented his Benz Patent-Motorwagen – one of the first true modern automobiles. It had a gasoline engine and could reach speeds of 16 mph!As the 1900s began, the car industry took off like a rocket! Henry Ford and others figured out ways to build cars quickly andcheaply using assembly lines. Suddenly, cars weren't just for the rich – regular people could afford them too. By 1927, Ford had sold over 15 million of his famous Model T cars!In the early 1900s, car races became hugely popular. Daring drivers would compete at breakneck speeds, pushing their vehicles to the limit. This intense competition drove car makers to make their cars faster, safer, and more powerful every year.After World War 2, cars became bigger, fancier, and filled with more gizmos than ever before. Tail fins, chrome, convertible tops – you name it! In the 1950s and 60s, American car companies like Ford, General Motors, and Chrysler ruled the roads.But then things changed. People wanted smaller, morefuel-efficient cars. That's when Japanese companies like Toyota and Honda arrived on the scene. Their well-made, economical cars gave Detroit's gas-guzzlers a run for their money.Today's cars are technological marvels. Satellite navigation, backup cameras, collision avoidance – modern cars have it all! And they're more environmentally friendly too, with hybrid and fully electric models available.But the auto industry never stops innovating. Maybe someday soon we'll all have self-driving cars that safely whisk us wherever we want to go while we sit back and enjoy the ride. Buckle up, because the driving adventure is far from over!Looking back, it's amazing how far we've come since those first sputtering steam wagons. Cars have transformed the world, connecting people and places like never before. They've given us freedom, opportunity, and some of the fastest thrills imaginable!So the next time you hop in your family car, remember the brilliant minds and world-changing inventions that made it possible. Cars are much more than just a way to get around –they're theoutriders of progress and innovation itself. What an incredible ride it's been!。
汽车的历史发展英语作文
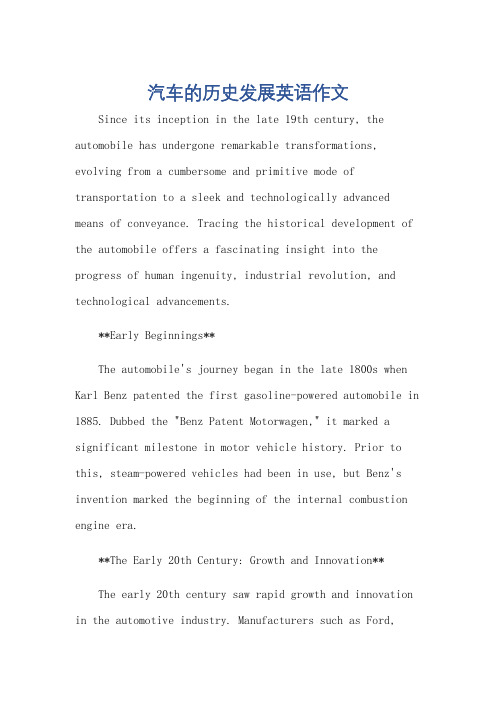
汽车的历史发展英语作文Since its inception in the late 19th century, the automobile has undergone remarkable transformations, evolving from a cumbersome and primitive mode of transportation to a sleek and technologically advanced means of conveyance. Tracing the historical development of the automobile offers a fascinating insight into the progress of human ingenuity, industrial revolution, and technological advancements.**Early Beginnings**The automobile's journey began in the late 1800s when Karl Benz patented the first gasoline-powered automobile in 1885. Dubbed the "Benz Patent Motorwagen," it marked a significant milestone in motor vehicle history. Prior to this, steam-powered vehicles had been in use, but Benz's invention marked the beginning of the internal combustion engine era.**The Early 20th Century: Growth and Innovation**The early 20th century saw rapid growth and innovation in the automotive industry. Manufacturers such as Ford,Chevrolet, and Packard emerged, and the assembly line production method revolutionized manufacturing, making automobiles more affordable and accessible to the masses. This period also saw the introduction of key features like electric starters, headlights, and windshields, whichgreatly enhanced the safety and comfort of driving.**The Mid-20th Century: Post-War Boom and Technological Leaps**After the World War II, the automotive industry experienced an unprecedented boom. With the advent of new materials like steel and plastics, cars became lighter and more durable. Technologies like power steering andautomatic transmissions further enhanced driving comfort. Additionally, the development of the interstate highway system in the United States and similar infrastructure globally facilitated the widespread adoption of automobiles. **The Late 20th Century and Beyond: Environmental Concerns and Technological Evolution**As the 20th century drew to a close, environmental concerns began to gain prominence, leading to the development of more fuel-efficient and environmentallyfriendly vehicles. Manufacturers like Toyota and Honda introduced hybrid cars, while Tesla and other electric vehicle startups emerged, revolutionizing the automotive landscape. Autonomous driving technology, connected cars, and electric vehicles are now the frontiers of automotive innovation, promising safer, more efficient, and sustainable modes of transportation.**Conclusion**The historical development of the automobile is a testament to human ingenuity and technological progress. From its humble beginnings as a cumbersome contraption to its current incarnation as a technologically advanced mode of transportation, the automobile has come a long way. Its evolution is not just a story of mechanical advancements but also a reflection of societal changes, environmental concerns, and the quest for a better future.**汽车历史发展的演进之旅:历史视角**自19世纪末诞生以来,汽车已经经历了显著的变革,从笨拙且原始的交通工具发展成为流线型且技术先进的运载工具。
汽车发展史【英文版】

Cadillac
Smaller air resistance, but narrow space and bad stability with cross wind.
➢ History---old stories
Real Automobile Era
Changed the style to be better!
➢The history of the car
Name: Student id:
➢ Car culture
How much do you
know about cars?
• Vehicle history • Auto and logo show • Conception car
➢ History---elder stories
Three Box Car (Boat) 1950s
For d
Chevrolet
Buick Cadillac
The world's largest number of a kind of models!
Conquered the instability with cross wind, but cannot run at high speed because of the strong air eddy.
Karl Benz made the first gasoline engine and used on the first 3 wheels automobile; Daimler manufactured the first four wheels car!
French, America, England, Japan and Russia started to their automobile era.
汽车转向系统英文文献
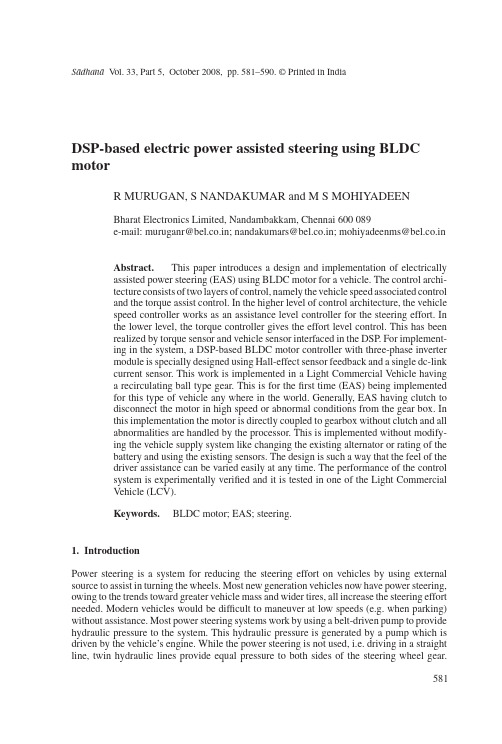
S¯a dhan¯a V ol.33,Part5,October2008,pp.581–590.©Printed in IndiaDSP-based electric power assisted steering using BLDC motorR MURUGAN,S NANDAKUMAR and M S MOHIYADEENBharat Electronics Limited,Nandambakkam,Chennai600089e-mail:muruganr@bel.co.in;nandakumars@bel.co.in;mohiyadeenms@bel.co.inAbstract.This paper introduces a design and implementation of electricallyassisted power steering(EAS)using BLDC motor for a vehicle.The control archi-tecture consists of two layers of control,namely the vehicle speed associated controland the torque assist control.In the higher level of control architecture,the vehiclespeed controller works as an assistance level controller for the steering effort.Inthe lower level,the torque controller gives the effort level control.This has beenrealized by torque sensor and vehicle sensor interfaced in the DSP.For implement-ing in the system,a DSP-based BLDC motor controller with three-phase invertermodule is specially designed using Hall-effect sensor feedback and a single dc-linkcurrent sensor.This work is implemented in a Light Commercial Vehicle havinga recirculating ball type gear.This is for thefirst time(EAS)being implementedfor this type of vehicle any where in the world.Generally,EAS having clutch todisconnect the motor in high speed or abnormal conditions from the gear box.Inthis implementation the motor is directly coupled to gearbox without clutch and allabnormalities are handled by the processor.This is implemented without modify-ing the vehicle supply system like changing the existing alternator or rating of thebattery and using the existing sensors.The design is such a way that the feel of thedriver assistance can be varied easily at any time.The performance of the controlsystem is experimentally verified and it is tested in one of the Light CommercialVehicle(LCV).Keywords.BLDC motor;EAS;steering.1.IntroductionPower steering is a system for reducing the steering effort on vehicles by using external source to assist in turning the wheels.Most new generation vehicles now have power steering, owing to the trends toward greater vehicle mass and wider tires,all increase the steering effort needed.Modern vehicles would be difficult to maneuver at low speeds(e.g.when parking) without assistance.Most power steering systems work by using a belt-driven pump to provide hydraulic pressure to the system.This hydraulic pressure is generated by a pump which is driven by the vehicle’s engine.While the power steering is not used,i.e.driving in a straight line,twin hydraulic lines provide equal pressure to both sides of the steering wheel gear.581582R Murugan,S Nandakumar and M S MohiyadeenWhen torque is applied to the steering wheel,the hydraulic lines provide unequal pressures and hence assist in turning the wheels in the intended direction.Electric Power Steering systems use electric components with no hydraulic systems at all.Sensors detect the motion and torque of the steering column and a computer module applies assistive power via an electric motor coupled directly to either the steering gear or steering column.This allows varying amounts of assistance to be applied depending on driving conditions.In the event of component failure,a mechanical linkage such as a rack and pinion serves as a back-up in a manner similar to that of hydraulic systems.Electric systems have an advantage in fuel efficiency because there is no hydraulic pump constantly running. Their other big advantage is the elimination of a belt-driven engine accessory,and several high-pressure hydraulic hoses between the hydraulic pump,mounted on the engine,and the steering gear,mounted on the chassis.This greatly simplifies manufacturing.The demand of electrically assisted power steering(EAS)has rapidly increased in past few years because of energy savings compared to Hydraulic Power Steering(HPS).Alternating current(ac)motors are designed to be highly efficient and easily controlled with modern power circuitry.Because of the developments in switching techniques,it is quite feasible to use ac motors with a battery supply as source.The traditional worm gear driven dc motor system is constrained by the limitations of the dc motor brushes and size of the motor for the same torque of BLDC.In this case BLDC motor has been used as an actuator in the application for electric power steering.The BLDC motor provides high torque and easy control(Chan &Fang2002;Chu et al2001;Desai&Emadi2005;Jun-Uk Chu et al2004;Kevin Brown et al1990;NamhunKim et al2007).The basic mechanical properties of the vehicle are essentially invariant among all of the available brands.The electrically assisted power steering system consists of BLDC motor mounted to the frame of the steering column and coupled to the wheels through a worm speed reducer.Electrically assisted power steering is shown in figure1.An electrically assisted power steering is composed of several parts such as torque sensor, engine speed sensor,vehicle speed sensor,steering column,torsion bar and electronic control unit.Figure1.Electrically assisted power steering.DSP-based electric power assisted steering using BLDC motor583 Torque sensor output gives the torque difference to be developed by the motor to reduce the effort required by the driver while he is steering.Engine speed signal is required to start the assistance only when the engine is ON in order to save the battery life.Vehicle speed signal is required to control the assistance developed by the motor(for the same level of torque signal)at various vehicle speed,as assistance requirement comes down as speed of the vehicle increases.The control architecture consists of two layers of control,namely the assistance level control and the torque control.In the higher level of control architecture,vehicle speed signal works as a reference for controlling the assistance to be developed by the motor.In the inner layer torque sensor signal performs generation of torque.The torque output from motor is a function of torque sensor signal and it depends on the torque difference between the steering wheel and the wheel.The vehicle speed signal and engine speed signals are pulses with variable frequency.For system implementation,a DSP-based BLDC motor controller with three-phase inverter module is specially designed using Hall-effect sensor feedback and a single dc-link current sensor.The torque and Back EMF equations of BLDC motor are similar to that of dc motor.The current sensing is ensured by a low cost shunt resistor and used for over-current protection and current feedback.The current control is achieved by PID controller and pulse width modulation(PWM) signals with varying duty rates.Hall-effect sensors are available to detect rotor shaft position, used for electronic commutation,motor speed and direction of rotation.2.Hardware architectureA block diagram of the power assisted steering is illustrated infigure2.The electrically assisted power steering system in a vehicle consists of the following parts.a.Digital signal processorb.Driver and protection cardc.Three phase inverterd.BLDC motor with Hall sensore.Reduction gear and sensors.Figure2.Block diagram of EAS.584R Murugan,S Nandakumar and M S MohiyadeenFigure3.DSP and protection card.2.1ProcessorThe DSP used for control and computation is TMS320F24XX.The processor is a single chip solution based on40MIPS,16bitfixed point DSP core with several associated peripherals such as Pulse Width Modulation generator(PWM)and Analog to Digital Converter(ADC) BPRA0551997;SPRU160C1999;SPRU161C1999.2.2Driver and protection circuitThe selected MOSFET Driver is from IR family.The PWM signals coming from the DSP are combined with protection logics and connected to MOSFET driver.The output of the driver is directly connected to the MOSFET switches through series gate resistor.The current sensing is done by the low cost shunt resistor.The voltage drop is processed with analog amplifier and connected to ADC module and used for current feedback and over-current protection.The protection card used here is shown in thefigure3.2.3Three phase inverter moduleThe three phase inverter module is developed by using MOSFETs with low ON state drop and high switching frequency.The three-phase inverter card used is shown infigure4.Figure4.MOSFET card.DSP-based electric power assisted steering using BLDC motor585Figure5.BLDC motor equivalent circuit.2.4BLDC motor with Hall sensorThe equivalent circuit of a BLDC motor is shown infigure5.The BLDC motor used here has8magnetic pole pairs on the rotor and a three-phase star connected windings on stator. The voltage equation of BLDC motor can be represented as⎡⎣V aV bV c⎤⎦=⎡⎣R000R000R⎤⎦⎡⎣i ai bi c⎤⎦+⎡⎣L000L000L⎤⎦ddt⎡⎣i ai bi c⎤⎦+⎡⎣e ae be c⎤⎦(1)R=Phase resistanceL=Phase inductanceV a,V b,V c=Phase voltagesI a,i b,i c=Phase currentse a,e b,e c=Back EMFs.The generated motor torque is given byT=e a i a+e b i b+e c i cω,(2)whereωis motor angular velocity.The motor is equipped with three Hall effect sensors.The Hall sensors produce three180◦(electrical)overlapping signals as shown in thefigure6.Thus it is providing six mandatory commutation points.The Hall sensor outputs are directly connected to processor and it generate the necessary switching sequence as per commutation.2.5Gear box and sensing circuitsThe BLDC motor is connected to a reduction gear system as shown infigure7.It drives the wheel.The torque difference between the steering wheel and wheel is sensed by a torsion bar.The output of the torsion bar is sensed by the torque sensor.The output of the torque sensor is directly connected to ADC for processing.586R Murugan,S Nandakumar and M S MohiyadeenFigure6.Hall sensor wave form.3.Controller design3.1Effort level controlThe electrically assisted power steering(EAS)incorporates a brushless electric motor located on the steering column,on the pinion that assists the driver when rmation like engine speed,and torque required are transmitted in real time to a DSP which deter-mines the optimal degree of assistance the electric motor should apply.Figure8shows the effort required by the driver without assistance and with assistance for a vehicle at static.Electrically assisted power steering eliminates the need for hydraulicfluids and complicated mechanical components(such as servo pumps),hydraulic lines,belts and pulleys,which add weight and volume.By eliminating the hydraulic pump,the EAS can operate without the help of the engine.Unlike a conventional hydraulic system,the EAS consumes energy only when providing assistance.The control algorithm for the electrically assisted steering system is shown infigure9.The effective torque and velocity control of a BLDC motor is based on relatively simple torque and Back EMF equations,which are similar to those of the DC motor.Figure7.Gear box with motor.DSP-based electric power assisted steering using BLDC motor587Figure8.Effort curve. During any120degree interval of phase current,I the instantaneous power(P)being converted from electrical to mechanical isP=ωT e=2EI(3)T e=Electromagnetic torqueE=Induced EMF per phase.The‘2’in this equation arises from the fact that two-phase are conducting.E=2NphB g Lrω,per phase induced emf.(4)Nph=Number of winding turns per phaseB g=Rotor magneticfield densityL=Length of the rotorr=Internal radius of rotor.Figure9.Control algorithms.588R Murugan,S Nandakumar and M S MohiyadeenUsing the above expression the electromagnetic torque is given by,T e=4NphBgLrI=KφI(5)K=Torque constantφ=Flux per pole pair.The system takes torque reference(I−ref)and feedback line current(Ifb)as input,produces duty-cycle reference as output.This is actually a PI controller.The following equation is implementedD−cycle=K p(I−ref−If b)+K pT i(I−ref−If b)dt,(6)Kp=Proportional constantT i=Time constant.Limiters are there atfinal controller output.Duty cycle reference is clamped to the peak of the saw tooth carrier wave.Current control is achieved by Pulse Width Modulation(fixed frequency20kHz)signals with varying duty cycles.PWM width is determined by comparing the measured actual current with the desired reference current.To sum up,the Back EMF is directly proportional to the motor velocity and the torque production is almost directly proportional to the phase current.In this control scheme,torque production follows the principle that current shouldflow in only two of the three phases at a time.Only one current at a time needs to be controlled so that only one current sensor is necessary.The positioning of the current sensor allows the use of a low cost resistor as a shunt.3.2Assistance level controlFigure10shows the effort required to be produced by the motor for various vehicle speeds.Variable steering assistance(higher at low vehicle speed and lower at high vehiclespeed),Figure10.Boost curve for various speeds.DSP-based electric power assisted steering using BLDC motor589Figure11.Driving effort outputfrom EAS.which improves drivability and active safety.This has been implemented by sensing the vehicle speed and accordingly modifies the effort to be produced by the electric motor by controlling reference to the controller.4.Experimental resultsIn this section,the result is presented(figure11)to ensure the validity of the proposed method at static driving.From the abovefigure,we can see that the effort required by the driver is almost constant entire steering wheel rotation.The effort reduction comes around75%.The motor is selected such that the cogging torque is very less.The maximum peak cogging torque of the motor used at10rpm is0·0056Nm compared to peak torque of2·45Nm.The acceleration and deceleration of the motor is done in such a way that the driver does not feel the torque ripple in his hand.The torque ripple generally felt at low speed,here the system in a loop such that the system is always in acceleration/deceleration phase,so feel of torque ripple is less.Further to above,the mechanical system itself is in variable gear ratio and it has inherent torque variation more than the motor torque ripple produced by the motor.Hence the driver is not able to feel the torque ripple compared with EAS ON mode and EAS OFF mode.From this result,it is seen that the proposed EAS has performed as expected.Maximum torque required(manual):32NmTorque required during power assistance:8NmPercentage assistance provided:75%Average current consumption:8A5.ConclusionFor equivalent power steering efficiency,electrically assisted power steering improves fuel consumption by4percent or more compared to conventional hydraulic systems.The elimina-tion of hydraulicfluids is also more environmentally friendly for End of Life Vehicle(ELV) consideration.Electronic data management(wheel angle,vehicle speed,etc.)can be used to fine-tune the power steering parameters,enhancing the car drivability.Variable steering assis-tance improves drivability and active safety.Steering force feedback incorporates controlled re-centre positioning of the steering wheel and active damping of highway vibration.590R Murugan,S Nandakumar and M S MohiyadeenReferencesBPRA055March1997DSP Solutions for BLDC motors.Literature number:Texas Instruments Europe Chan Lie-Tong Yan F,Shao-Yuan Fang2002In-Wheel permanent-magnet brushless dc motor drive for an electric bicycle.IEEE Trans.Energy Conversion17(2):229–232Chu C L,Tsai M C,Chen H Y2001Torque control of brushless DC motors applied to electric vehicles.IEEE Trans.on1–5Desai,Ali Emadi2005A novel digital control technique for brushless DC motor drives:Current control.IEEE Trans.326–331Jun-Uk Chu,In-Hyuk Moon,Gi-Won Choi,Jei-Cheong Ryu,Mu-Seong Mun2004Design of BLDC motor controller for electric power wheelchair.IEEE Trans.94–95Kevin E Brown,Rafael M Inigo,Barry W Johnson1990Design,implementation,and testing of an adaptable optimal controller for an electric wheelchair.IEEE Trans.on Industry Application26(6): 1144–1157NamhunKim,Hamid A Toliyat,Issa M Panahi,Min-Huei Kim2007BLDC motor control algorithm for low-cost industrial applications.IEEE Trans.1400SPRU160C June1999TMS320F/C24x DSP Controllers reference guide CPU and instruction set.Literature number:Texas Instruments EuropeSPRU161C June1999TMS320F/C240DSP controllers reference guide—Peripheral library and spe-cific devices.Literature number:Texas Instruments Europe。
汽车历史发展的有关介绍英语作文
汽车历史发展的有关介绍英语作文汽车历史发展的有关介绍。
英文回答:The history of automobiles can be traced back to thelate 19th century. The invention of the first practical automobile is often attributed to Karl Benz, who built the Benz Patent-Motorwagen in 1886. This marked the beginningof a new era in transportation.The early cars were quite different from the ones wesee today. They were powered by internal combustion engines and had a basic design with a single cylinder. These cars were not very powerful and had a limited top speed. However, they were a significant improvement over horse-drawn carriages and quickly gained popularity.As the technology advanced, cars became more sophisticated and efficient. Manufacturers startedexperimenting with different engine configurations and designs. The introduction of the Ford Model T in 1908 revolutionized the automobile industry. It was the first car to be mass-produced using assembly line techniques, making it affordable for the average person.Over the years, cars have undergone numerous changes and improvements. The introduction of electric cars and hybrid vehicles has brought about a shift towards more environmentally friendly transportation options. Advanced safety features, such as airbags and anti-lock braking systems, have also become standard in modern cars.The automotive industry has had a significant impact on society and the economy. It has created jobs, stimulated economic growth, and provided people with a convenient mode of transportation. Cars have also become a symbol of status and personal freedom.中文回答:汽车的历史可以追溯到19世纪末。
车的发展历史英语作文
车的发展历史英语作文Title: The Evolution of Automobiles: From Steam-Powered to Self-Driving。
Introduction。
The history of automobiles is a remarkable tale of human ingenuity and technological advancement. From the rudimentary steam-powered vehicles of the 18th century to the self-driving cars of the 21st century, the evolution of automobiles has profoundly impacted society, culture, and the global economy. This essay explores the key milestones in the development of automobiles, examining how they have transformed transportation and shaped the modern world.Early Beginnings: The Steam Era。
The journey of the automobile began in the late 18th century, with the advent of steam power. In 1769, Nicolas-Joseph Cugnot, a French engineer, built the first self-propelled vehicle, a steam-powered tricycle intended for military use. Although it could only travel at a modest speed and had limited range, Cugnot's invention laid the foundation for future developments in automotive technology.Throughout the 19th century, steam engines became more sophisticated, leading to the production of larger steam-powered vehicles like the "road locomotive." These vehicles were primarily used for industrial and agricultural purposes, with limited success in passenger transport dueto their bulk and inefficiency. Despite these challenges, steam power played a crucial role in the evolution of automotive technology.The Rise of Internal Combustion Engines。
车的发展历史英语作文
车的发展历史英语作文Cars have come a long way since their invention. From the first steam-powered vehicles to the sleek electric cars of today, the evolution of the automobile industry is truly remarkable.The early cars were bulky and slow, with limited range and reliability. But as technology advanced, so did the design and performance of cars. Today, we have cars that can go from 0 to 60 in a matter of seconds and travel hundreds of miles on a single charge.One of the biggest changes in the car industry has been the shift towards electric vehicles. With concerns about climate change and air pollution on the rise, more and more people are turning to electric cars as a cleaner and more sustainable mode of transportation.In addition to electric cars, we are also seeing the rise of self-driving vehicles. With advancements inartificial intelligence and sensor technology, cars are becoming smarter and more autonomous. In the near future,we may not even need to drive our cars at all.Despite all the changes and advancements in the car industry, one thing remains constant: the freedom and convenience that cars provide. Whether it's a road tripwith friends or a quick trip to the grocery store, cars continue to play a vital role in our daily lives.In conclusion, the history of cars is a story of innovation and progress. From the early days of steam-powered vehicles to the cutting-edge electric cars of today, cars have come a long way. And with new technologies on the horizon, the future of cars looks brighter than ever.。
汽车发展历史的有关介绍英语作文
汽车发展历史的有关介绍英语作文The History of Cars: Vroom Vroom!Cars are awesome! They can take us anywhere we want to go. But did you know that cars haven't been around forever? A long time ago, there were no cars at all. People had to walk everywhere or ride horses and horse-drawn carriages to get places. That must have been really hard work!The first modern cars were invented in the late 1800s. One of the very first was made in 1885 by a German named Karl Benz. His Benz Patent Motorwagen looked really weird compared to today's cars. It had three big wheels and basically looked like a horse carriage without the horse! But it was powered by a gasoline engine instead of a horse. Pretty cool, right?Another early car was made in 1908 by a company called Ford. It was called the Model T and it's one of the most famous cars in history. The Model T made cars affordable for regular people for the first time ever. Before that, only rich folks could buy the earliest cars. The Model T was cheap, simple, and reliable. Over 15 million Model Ts were made!As time went on, car makers kept finding ways to make cars better and better. They got faster engines, better safety features,smoother rides, and all sorts of cool gadgets inside. Nowadays, some cars can even drive themselves with special computer programs! Isn't that wild?My favorite kinds of cars are sports cars because they look so sleek and speedy. Sports cars like Ferraris, Lamborghinis, and Porsches are crazy expensive though. Maybe when I'm older and richer, I can buy one for myself! For now, I'll have to stick to dreaming about them.Some people think cars are bad for the environment because they burn gasoline made from oil and put out pollution. That's why companies are working on electric cars now that run on big batteries instead of gasoline. The batteries can be charged up with renewable electricity from wind farms, solar panels, and other green energy sources. Pretty neat, huh?Cars have also changed how cities and roads are built. A long time ago, streets were narrow and windy because they had to fit horse carriages. But as cars got bigger and faster, roads had to get wider and straighter. Parking lots and gas stations had to be built too. Huge highway systems had to be constructed to connect cities together.It's crazy to think that for most of human history, people couldn't really travel very far from where they were born. Butonce cars were invented, it became much easier for people and goods to travel all over! Cars really did change the world.I hope self-driving cars become a normal thing soon. How awesome would it be to have a car that could just drive you anywhere you wanted while you got to sit back and play video games? A kid can dream!Who knows what cars will be like 50 or 100 years from now? Maybe they'll be able to fly or teleport across the country in an instant! Or maybe we'll have figured out how to create a new environmentally-friendly fuel that doesn't cause any pollution at all. Whatever happens, I'm sure our great-great-grandkids will look back at today's cars and think they look just as goofy and outdated as those first cars from the 1800s. The history of cars is always bumping along to somewhere new and better!。
- 1、下载文档前请自行甄别文档内容的完整性,平台不提供额外的编辑、内容补充、找答案等附加服务。
- 2、"仅部分预览"的文档,不可在线预览部分如存在完整性等问题,可反馈申请退款(可完整预览的文档不适用该条件!)。
- 3、如文档侵犯您的权益,请联系客服反馈,我们会尽快为您处理(人工客服工作时间:9:00-18:30)。
转向系统是在车辆系统是必要的基本制度,通过方向盘司机操纵和控制汽车的方向旅行,以实现他的驾驶意图。
在超过100年,汽车与机械和电子技术的发展和进步的产业。今天,汽车是不是单纯的机械感的汽车,它是机械,电子,材料等综合产品。转向系统随着汽车产业的发展后,长期的演变。
传统的转向系统是机械转向系统,汽车方向盘由飞行员控制的,通过这样的方向盘机械配件系列,以实现偏转,从而实现转向。
正如20世纪50年代,液压动力转向系统在汽车应用,标志着转向系统的开始。动力转向由以前的人力资源对人类和液压助力器。
液压助力器海港巡逻组(液压动力转向)在对机械和液压系统转向系统的基础上增加甲液压系统和发动机,当发动机的一般部分开始,提供汽车发动机的大前锋,另一个为电力液压系统动能的一部分。由于其工作可靠,成熟的技术仍然得到了广泛应用。该转向系统的主要特点是流体的压力,减少司机的方向盘的支持,改善了转向灯和自动运行的稳定性。 但与此同时,也有一些液压动力系统的缺陷:
针对车辆设计和制造,后转向动态特性不能改变车辆的完成。直接后果是,在低功率时的动力学特性,在低段车可以得到非常好的,但在高速时期具有良好的方法,意义,因为不能动态调整的特点,司机没有更好的办法, 针对车辆设计和制造,后转向动态特性不能改变车辆的完成。直接后果是,当在低功耗的动态特性,在低段车可以得到非常好的,但在高速期,好方法,以意义,因为可以不调整的动力特性,没有更好的办法司机,当在动态特性高功率,而不是非常低段tprompt效果好, 如果没有,目的是车辆的液压系统也必须在发动机驱动。因此,能源消耗,提高燃油发动机, 现有的液压油泄漏问题,不仅要对环境的污染,且易于其他组件, 针对低温,液压系统的性能很差。 近年来,随着电子技术的广泛应用,转向系统也越来越多使用的电子设备。转入电子控制系统,因此,相应出现了电液助力转向系统。电液助力转向可以分为两大类:电控ECHPS转向系统(液压助力转向)电动液压转向系统(电动液压动力 - 的EHPS)和电动液压转向。电动液压助力转向系统是在液压动力系统的液压助力系统的发展基础,不同的是,电动液压系统中的液压动力系统的动力源,而不是由汽车发动机电机驱动液压系统,节约能源和减少发动机的燃料消耗。电动液压转向传统的液压助力系统是建立在发展基础上,不同的是,电动液压助力转向系统,电子控制装置增加。电子控制装置可根据转向速率,车速自动液压系统运行参数,改变以不同的速度液压助力的大小,从而实现了改变,动态特性。但在电机驱动液压系统,反过来,电机可以停止转动,从而减少能源消耗。 虽然电动液压水力指点动力方向盘系统克服缺点。 但是由于液压机构,它的存在存在水力油漏出问题,并且电动液压的动力方向盘系统,被介绍的马达驱动系统是更加复杂,费用和可靠性。 为了避免电动液压转向系统,电力的电动助力转向(EPS)的现在应该转向系统。与转向系统,最大的区别在于它的各种液压系统并没有在电动助力转向系统。最初由汽车生产液压助力转向系统。电力一般由转向扭矩传感器和微处理器,电机等的基本原则体系是:当司机转动方向盘转动轴驱动,在传感器的扭矩和旋转轴的扭矩信号到电信号安装到微处理器,微处理器的速度和转矩信号的其他车辆运行参数,根据该功率电动机升压治疗的方向设置程序和助推器的大小。自1988年以来,日本铃木Cervo的汽车首次装备了助力转向系统,动力转向系统是广受人们的认可。 转向系在以下方面主要被实现: 阿助力转向系统可以提供不同的速度下的动态特性不同。在低的道路,转向系统,以增加更多的光线,减少在高速转向,甚至为了提高道路的增加潮湿。 仅在转向电机的工作动力转向系统,以提供电力,以减少能源消耗。 一个电机,由电池供电的电动助力转向系统,使发动机无法工作下的工作条件。 电动助力转向系统不应液压系统,液压助力系统相比,自动化装配。和电动助力转向系统可以改变助推器方案微处理器算法,动态特性的变化容易。 科学发展和技术的转变,转向控制(四轮转向),把传统的传导机制转向系统。但火花总是可以带来惊喜吧!电子转向系统转向线控转向(对线)改为三个微控制器最,它是由转向传动机构取代传统的概念,分为两部分三大部分。电子转向系统是最先进的技术和汽车转向系统。它主要由转向控制模块,执行模块和微控制器的三个模块。 转向控制模块的主要功能是扭矩传感器检测驾驶员的意图,并检测信号(包括旋转方向和旋转速度等)的巴士到微控制器,微控制器基于信号,速度反馈控制模块是一种方向盘,使司机能感受到道路。但是,这是道路,是根据测试的虚拟综合数据,形成发展“经验”,以及固化在微控制器的形式进程。因此,它与速度,转向的速度和扭矩大小有对应关系。 转向角传感器和执行器包括转向电机,转向电机控制器等优点,是微控制器的功能基础上的控制指令,驱动电机旋转角度来执行,完整的行动。此外,还有旋转角度传感器监测和反馈,以微控制器规模,形成一个完整的准确的闭环控制系统,转向运动。 微控制器是电子转向系的核心。 它接受信号检测,被处理发出对应控制信号。
由于微控制器取代转向传动机构,从而系统组件之间的机械连接,减少了响应速度和响应的准确性。并把战略,传输控制软件编程的任何设置,其他设备,如ABS,自动导航设备。传输机制,减少汽车带来了更大的内部空间,让乘坐更有趣。而转向行为都可以记录,保存在软件,它可以帮助进一步完善后,转向控制策略的EEPROM,甚至可以为交通意外的证据。 汽车安全问题一直是公众关注的焦点。转向系统和照明系统可以在夜间交通更好的安全性。页上面显示,传统的照明系统是一线照射车辆,车辆和行人在弯道如果司机将难以在角落里找到,行人的交通意外。如果照明系统相结合,转向系统,上面的照片时,在方向盘司机的方向盘角度,并享有的变化,从而更广泛的照明,照明灯,所以就在一个更广泛的行人路口很容易被发现。目前,照明技术在中端雪铁龙凯旋已丰田camrys使用。 目前,电子转向系统的可靠性和成本是阻碍了发展。如果微控制器,主要问题表现在,转向系统会彻底失败,其不喜欢在电机或液压系统的电动助力转向系统和电动液压助力转向系统,也可以与人的问题出现时,控制汽车。微控制器的电子助力转向系统故障,因为没有机械系统可以连接到方向盘和转向,因此无法控制汽车。但是,尽管电子转向系统转向系统仍然是未来的发展方向。 现代汽车转向装置的设计趋势 汽车1.1高速需要 从灯光控制,稳定和安全的角度,广泛应用于汽车制造更先进的技术,采用高刚性,转向齿轮比转向系统。 “比,高刚度是目前世界生产转向结构。 充分考虑安全性,可移植性1.2 汽车速度的提高与司机和乘客的安全,是非常重要的许多汽车在国内和国外已普遍增加,如安全督导带能量吸收装置,防止碰撞,等等,安全气囊,并逐步推广。从人体工程学,光操纵的看法已经逐步采用可调转向柱和动力转向系统。 130低成本,低油耗,专业化生产量 随着国际经济形势,石油危机,经济衰退,汽车产量更认真,更经济,因此,设计出低成本,低油耗,低成本,自动化生产线,实现大规模专业化生产的合理化。备件制造,尤其是转向器的生产,更加突出。 计算机化的1.4汽车redirector设备 The操舵装置设备,在途中的汽车对计算机的发展。 2现代汽车指点设备发展趋势使用动态的The现代汽车指点设备2.1与汽车制造业的迅速发展的一起,操纵的设备结构有巨大变动。 汽车从流行的redirector结构的当前使用,主要产品是: 有蠕虫萧伯纳(参考),涡轮(WR类型),循环球类型(BS类型)和机架和鸟翼末端(RP)的四种类型。 这四redirector,是用途广泛在公共汽车上。 正如我们已经了解到,在世界范围内,汽车循环球式转向器45%,齿条和小齿轮约40%的方向盘,蠕虫约10转向器,转向其他类型的5%%。循环球式转向器一直稳步发展。在西欧已在客运上,齿条和小齿轮转向很大的发展。日本是汽车转向器循环球式转向器的特点比例越来越大,对各种汽车发动机的类型不同类型的日本设备,采用不同类型的重定向器,在循环球式转向器巴士使用,已经从20世纪60年代,现代62.5%100%(蜗轮舵机组件在总线上的发展已被消灭。大型和小型卡车大多采用循环球式转向器齿条和小齿轮转向齿轮,而且发展。迷你车圆球式转向器65%,齿条和小齿轮35%。 产品品种的综合运用,得出以下结论: 球式转向器。循环架和小齿轮转向齿轮的组成部分,已成为世界上两个主要的汽车转向器,和蠕虫#0;蜗轮蜗杆式转向器肖,舵机组件被淘汰或保留较小的状况。 鉴于舵机客运发展的看法是不同的,美国和日本发展循环球式转向器的焦点,比例已达到或超过90%,西部大开发是关键齿条和小齿轮转向齿轮组成部分的比例,超过50%,法国95%。 齿条和小齿轮转向齿轮的组成部分,在应用程序(包括客运和货运站或小型货车小型车的优点)的跨越式发展,并为大型车辆循环球式转向器的主要结构。 循环球式转向器2.2 球类型redirector。 循环特征是: 高效率,光,一团光滑的控制力特征曲线的操作。方便的Decorate ..... 特别适用于大和中型车和动力方向盘系统与,容易转移信号、高效率、回归好推力水力助推器设备和行动。 为了实现比例,满足操纵可移植性的要求。中间位置,力小,而且往往用于敏感,因此,请求附近的小,为了提高灵敏度比中间位置。大视角的位置,但使用的抵制,因此较少以大角度的位置,速度,以减少武力。由于循环球式转向器可以实现比例越来越广泛的应用。 通过大量的钢材轧制,接触到交付部队,有实力和良好的耐磨性。与舵机可与设计等,是机械结构是其广泛应用的原因之一。 变结构具有更高的比,刚度,尤其是对车辆高速合适。在高速高速车辆需要一个更好的稳定性,必须保证高刚度指导。 J差距调节。齿条齿扇可以调整后的间隙副磨损,使转向齿轮传动有相应的差距,以改善生活,而且舵机转向的优点。 操舵装置生产在中国,除早蠕虫XieFangPai汽车生产之外; #与蠕虫萧伯纳, dongfeng汽车指点齿轮组分,其他的0,轮子指点齿轮组分使用圆球类型结构的多数模型,和有某一生产经验。 目前,在活跃发育周期的dongfeng,和有球类型redirector在第二HuanXing用途