钢衬接触灌浆施工方案
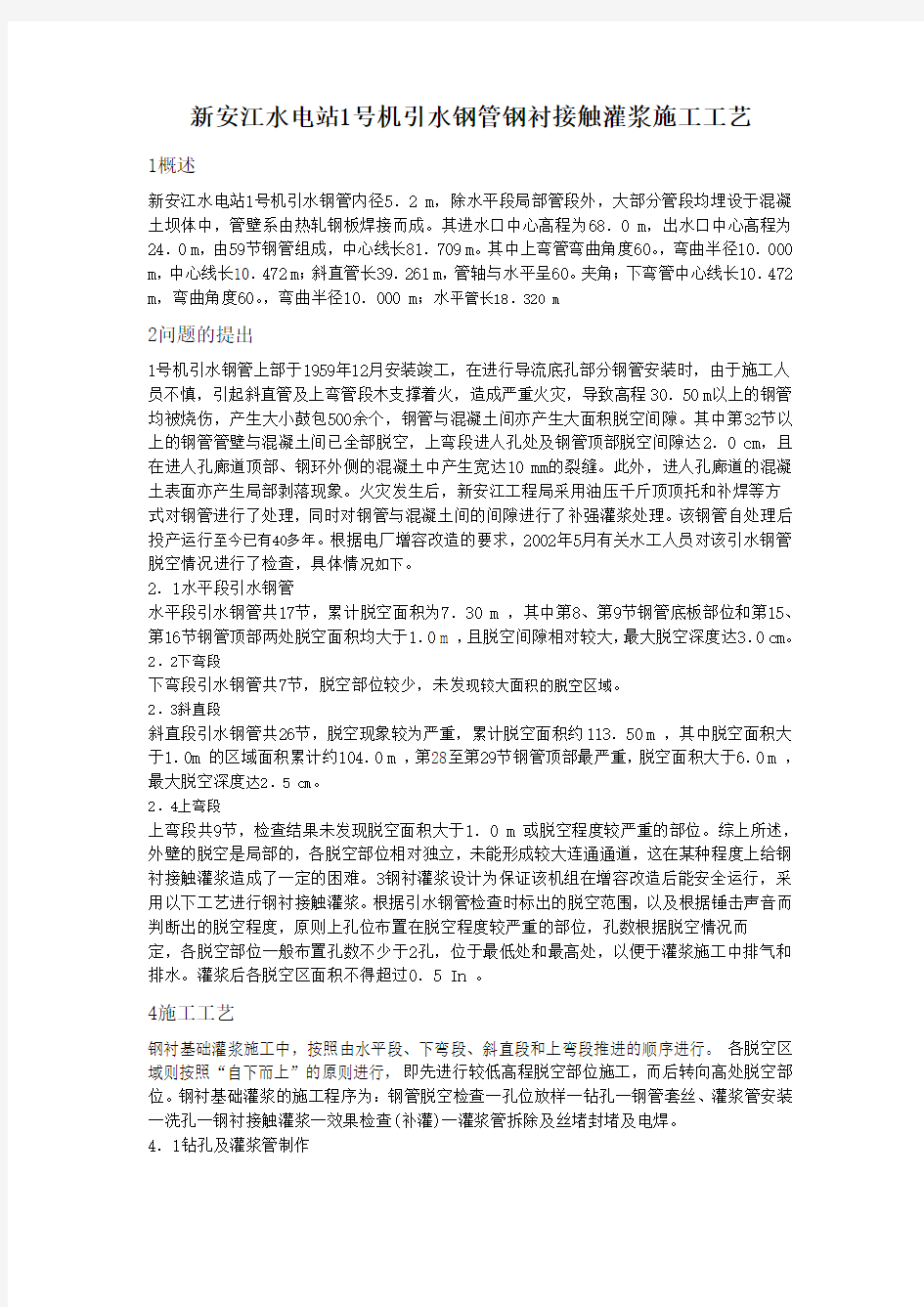
- 1、下载文档前请自行甄别文档内容的完整性,平台不提供额外的编辑、内容补充、找答案等附加服务。
- 2、"仅部分预览"的文档,不可在线预览部分如存在完整性等问题,可反馈申请退款(可完整预览的文档不适用该条件!)。
- 3、如文档侵犯您的权益,请联系客服反馈,我们会尽快为您处理(人工客服工作时间:9:00-18:30)。
新安江水电站1号机引水钢管钢衬接触灌浆施工工艺
1概述
新安江水电站1号机引水钢管内径5.2 m,除水平段局部管段外,大部分管段均埋设于混凝土坝体中,管壁系由热轧钢板焊接而成。其进水口中心高程为68.0 m,出水口中心高程为24.0 m,由59节钢管组成,中心线长81.709 m。其中上弯管弯曲角度60。,弯曲半径10.000 m,中心线长10.472 m;斜直管长39.261 m,管轴与水平呈60。夹角;下弯管中心线长10.472 m,弯曲角度60。,弯曲半径10.000 m;水平管长18.320 m
2问题的提出
1号机引水钢管上部于1959年12月安装竣工,在进行导流底孔部分钢管安装时,由于施工人员不慎,引起斜直管及上弯管段木支撑着火,造成严重火灾,导致高程30.50 m以上的钢管均被烧伤,产生大小鼓包500余个,钢管与混凝土间亦产生大面积脱空间隙。其中第32节以上的钢管管壁与混凝土间已全部脱空,上弯段进人孔处及钢管顶部脱空间隙达2.0 cm,且在进人孔廊道顶部、钢环外侧的混凝土中产生宽达10 mm的裂缝。此外,进人孔廊道的混凝土表面亦产生局部剥落现象。火灾发生后,新安江工程局采用油压千斤顶顶托和补焊等方式对钢管进行了处理,同时对钢管与混凝土间的间隙进行了补强灌浆处理。该钢管自处理后投产运行至今已有40多年。根据电厂增容改造的要求,2002年5月有关水工人员对该引水钢管脱空情况进行了检查,具体情况如下。
2.1水平段引水钢管
水平段引水钢管共17节,累计脱空面积为7.30 m ,其中第8、第9节钢管底板部位和第15、第16节钢管顶部两处脱空面积均大于1.0 m ,且脱空间隙相对较大,最大脱空深度达3.0 cm。2.2下弯段
下弯段引水钢管共7节,脱空部位较少,未发现较大面积的脱空区域。
2.3斜直段
斜直段引水钢管共26节,脱空现象较为严重,累计脱空面积约113.50 m ,其中脱空面积大于1.0m 的区域面积累计约104.0 m ,第28至第29节钢管顶部最严重,脱空面积大于6.0 m ,最大脱空深度达2.5 cm。
2.4上弯段
上弯段共9节,检查结果未发现脱空面积大于1.0 m 或脱空程度较严重的部位。综上所述,外壁的脱空是局部的,各脱空部位相对独立,未能形成较大连通通道,这在某种程度上给钢衬接触灌浆造成了一定的困难。3钢衬灌浆设计为保证该机组在增容改造后能安全运行,采用以下工艺进行钢衬接触灌浆。根据引水钢管检查时标出的脱空范围,以及根据锤击声音而判断出的脱空程度,原则上孔位布置在脱空程度较严重的部位,孔数根据脱空情况而
定,各脱空部位一般布置孔数不少于2孔,位于最低处和最高处,以便于灌浆施工中排气和排水。灌浆后各脱空区面积不得超过0.5 In 。
4施工工艺
钢衬基础灌浆施工中,按照由水平段、下弯段、斜直段和上弯段推进的顺序进行。各脱空区域则按照“自下而上”的原则进行,即先进行较低高程脱空部位施工,而后转向高处脱空部位。钢衬基础灌浆的施工程序为:钢管脱空检查一孔位放样一钻孔一钢管套丝、灌浆管安装一洗孔一钢衬接触灌浆一效果检查(补灌)一灌浆管拆除及丝堵封堵及电焊。
4.1钻孔及灌浆管制作
钢衬灌浆前需先制作灌浆孔和排气孔,钻孔采用磁座电钻成孔,孔径为 19 mm。各灌浆孔和排气孔钻孔结束后,进行孔内套丝,灌浆孔采用镀锌管一端与钢衬间丝扣连接,另一端装上阀门,接灌浆皮管,排气孔则无需接灌浆皮管。灌浆过程中,为加强施工人员联系,在钢管内外分别安装一部直通电话。
4.2洗孔
灌浆孔及排气孔制作结束后,即可进行脱空区域的洗孔,以便清除脱空区域的积水和杂质,并借此检查各脱空区域的连通性。洗孔采用高压风进行,冲洗压力为灌浆压力的80%。洗孔时选择较低孔作为进气孔,上部孔作为出气孔。各脱空部位洗孔前将各灌浆孔和排气孔阀门打开,要求各独立灌浆区域吹洗时间不得小于5 min。
4.3钢衬接触灌浆
洗孔结束后,即可进行钢衬接触灌浆。由于施工场地和钢管本身等条件的限制,灌浆系统布置在伸缩节廊道内,灌注水泥浆时采用SGB6—10三缸灌浆机作为动力设备,该设备具有工作压力较大和稳定性较好等特点,从而保证钢衬灌浆所需要的工作
压力。
4.3.1灌浆材料及浆液配比
钢衬灌浆材料设计采用改性水泥。改性灌浆水泥的研究和应用是“七五”国家科技攻关项目“提高灌浆帷幕的防渗能力和耐久性研究”的子题之一,由普通525号硅酸盐水泥为熟料掺入特殊组分的~t,/Ju剂进行改性研磨而成,改性主要是增加水泥的细磨程度,提高灌入细微裂隙的能力;内掺膨胀组分,使浆体在硬化过程中产生微膨胀,弥补细水泥的收缩效应,提高与被灌对象的粘结、抗渗性能;掺入高效分散剂,改善并提高浆液的流动性;掺加其它外加剂,主要是为了调整水泥的强度和水化速度,或提高水泥结石的耐久性能等。通过上述措施之后可综合改善水泥的可灌性(包括对细微裂隙的可灌性)和耐久性。
主要技术指标:该水泥最大粒径<30 la.m,d50<7la.m,水泥细度dq5≤30 la.m;3 d膨胀率>10.05%,28 d膨胀率≤0.60%;水泥浆体的稳定性W/C=I.0时:自由沉降率≤5%;马氏粘度≤20;水泥强度标号I>625号;水泥浆体可灌入<0.1 mm裂隙。此次钢管接触灌浆浆液水灰比采用1:1。浆液制作的程序如下:先在高速搅拌机内加入一定计量的水,根据规定配比加入相应量的水泥,高速搅拌2min以上,使水泥颗粒充分地分散开,形成稳定浆液,然后转入低速搅拌桶内以备灌浆用。
4.3.2灌浆工艺
灌浆工艺采用孔口循环、孔内填压式灌浆法,待处理区域各排气孔分别排出浓浆后,依次将其孔口阀门关闭。各脱空部位灌浆按先下部后上部的顺序进行,下部灌浆孔灌浆时,位于上部的排气孔阀门打开,以便钢衬间隙内的水和气体能充分地排出,并在灌浆结束后仔细敲击钢管,以判断被灌段脱空区域钢衬内浆液充填的密实性。
4.3.3灌浆压力
设计灌浆压力为0.20 MPa,施工过程中要求对灌浆压力进行严格控制,具体措施为分别在进、回浆管路上各安装一压力表,密切关注其变化,以保证施工过程中不发生钢管变形等不利后果。
4.3.4变形监测
为确保压风和灌浆过程中不发生钢衬抬动和变形,在严格控制压力的同时,加强了钢管变形的监测。在钢衬内部安设一定量的变位计,由专人观测,发现变形时则及时释放压力。4.3.5结束标准
在规定压力下,当各灌浆孔注浆率达到零时,延灌5 min即可结束。
4.3.6灌浆效果检查和灌浆孔封堵
各区段脱空部位灌浆结束7 d后,采用锤击法检查各脱空部位的充填情况,而后拆除灌浆管。