《叶片修复复合材料》word版
风电叶片基础知识之复合材料篇三

2) 热固性玻璃钢 它是由60%~70%玻璃纤维(或玻璃布)和30%~40%热固性树脂 (环氧、聚酯树脂等)组成。 主要优点:密度小、强度高,耐蚀性、绝缘性、绝热性好;吸 水性、防磁、微波穿透性好,易于加工成型。 缺点:弹性模量低,热稳定性不高,只能在300℃以下工作。
(2)碳纤维―树脂复合材料 最常用的是碳纤维与聚酯、酚醛、环氧、聚四氟乙烯等树脂组 成的复合材料,具有高强度、高弹性模量、高比强度和比模量,还 具有优良的抗疲劳性能、耐冲击性能、自润滑性、减摩耐磨性、耐 蚀性及耐热性。缺点是纤维与基体结合力低。 (3)硼纤维―树脂复合材料 主要由硼纤维与环氧、聚酰亚胺等树脂组成。具有高的比强度、 比模量,良好的耐热性。其缺点是各向异性明显。 (4)碳化硅纤维树脂复合材料 由碳化硅纤维与环氧树脂组成的复合材料,具有高的比强度、 比模量。 (5)Kevlar纤维树脂复合材料 由Kevlar纤维与环氧、聚乙烯、聚碳酸酯、聚酯等树脂组成。 主要性能特点是抗拉强度大于玻璃钢,而与碳纤维―环氧树脂复合 材料相似;延性好,与金属相当;其耐冲击性超过碳纤维增强塑料; 其疲劳抗力高于玻璃钢和铝合金;减振能力为钢的8倍。
风电叶片基础知识之复合材料 篇三
6.3
1.常用增强纤维
常用的复合材料
一、纤维增强复合材料
主要有玻璃纤维、碳纤维、硼纤维、碳化硅纤维、Kevlar有机 物纤维等。
玻璃纤维布
玻璃纤维绳
玻璃纤维绳
纳 米 碳 管 纤 维 玻璃纤维纸
碳 纤 维 绳
(1)玻璃纤维 按玻璃纤维中 Na2O 和 K2O 的含量不同,可将其分为无碱纤维 (碱的质量分数<2%)、中碱纤维(碱的质量分数为2%~12%)、高 碱纤维(碱的质量分数>12%)。随着碱量的增加,玻璃纤维的强度、 绝缘性、耐蚀性降低。 特点:强度高,抗拉强度可达 1000 ~3000MPa ;弹性模量比金 属低得多,为( 3 ~ 5 )×104MPa ;密度小,为 2.5 ~ 2.7g/cm3 ;化 学稳定性好;不吸水、不燃烧、尺寸稳定、隔热、吸声、绝缘等。 缺点:脆性较大、耐热性低,250℃以上开始软化。 优点:价格便宜、制作方便
第5章 叶片材料及制造工艺
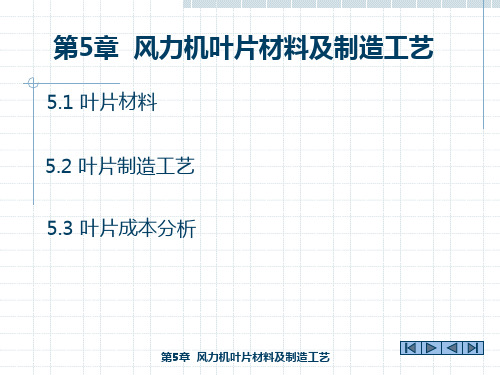
风力发电机叶片生产过程_腾讯视频 https:///x/page/g0331e7 8nfz.html?ptag=qqbrowser
5.2 叶片制造工艺
具体成型工艺大致可分为手糊成型、模压成型、拉挤 成型、纤维缠绕、树脂传递模塑、预浸料成型以及真空灌 注成型等7种工艺。
第 5章
风力机叶片材料及制造工艺
5.1 叶片材料
5.1.3.3 夹芯材料 夹芯材料一般使用在叶片前缘、后缘以及剪切腹板处, 可增加结构刚度,防止局部失稳,提高整个叶片的承载能力 并降低叶片重量。
1、硬质泡沫
2、轻木
第 5章
风力机叶片材料及制造工艺
5.1 叶片材料
5.1.3.4 胶黏剂 胶黏剂的作用是对叶片上壳体与下壳体、壳体与剪切 腹板进行黏接,并填实壳体缝隙。
5.2 叶片制造工艺
5.2.1 手糊成型工艺
传统的复合材料叶片多采用手糊工艺制造。
材料准备剪裁 手糊成型 制品固化 后处理
胶衣/树脂
第 5章
风力机叶片材料及制造工艺
5.2 叶片制造工艺
5.2.2 模压成型工艺 模压成型工艺首先将增强材料和树脂置于双瓣模具中, 然后闭合模具,加热加压,再进行固化脱模。
常见材料:一般的聚乙烯塑料和聚氯乙烯塑料都 是热塑性。雨衣,食品袋或包装袋
热固性
热固性指加热时不能软化和反复塑制,也不在 溶剂中溶解的性能,体型聚合物具有这种性能。
第一次加热时可以软化流动,加热到一定温度, 产生化学反应一交联固化而变硬,这种变化是 不可逆的,此后,再次加热时,已不能再变软 流动了。正是借助这种特性进行成型加工,利 用第一次加热时的塑化流动,在压力下充满型 腔,进而固化成为确定形状和尺寸的制品。这 种材料称为热固性塑料。
风力发电机叶片复合材料性能分析【论文】

风力发电机叶片复合材料性能分析摘要:风力发电机叶片是风力机捕获、利用风能的重要部件,故为了优化风力发电机的性能,现阶段已经有越来越多的研究者重视起对风力发电机叶片的性能探索。
由此本文就对风力发电机叶片中复合材料性能进行分析,不仅阐述了风力发电机及其叶片的概念与重要作用,还通过利用真空灌注工艺以及如巴氏硬度计、万能试验机等设备开展了风机叶片的材料性能实验。
关键词:风力发电机叶片;复合材料;性能分析现代社会中可持续发展的环保理念不断普及,诸如太阳能、潮汐能、风能等可再生能源逐渐占据了更重要的地位。
由此现阶段的电力企业中也逐渐改变了过去仅依靠火力发电的模式,相关的风力发电机逐渐拥有了更为广泛的应用空间。
而作为风力发电机核心技术,风机叶片技术也同样受到了更多人的注重,由此本文就对风机叶片的构成、性能、结构等方面进行了深入探索。
1.风力发电机叶片作为风力发电机中的重要部件之一,风机叶片通常可占一架风机总成本的15%到20%,这主要是由于风机叶片的质量常会影响到风机性能及其相关效益,根据相关数据显示,风机叶片每增加6%的长度,风机对风能的利用率即可提升12%左右。
一般来说,风机叶片主要是由外壳、腹板、梁帽、挡雨环、人孔盖等结构组成,再经由相关结构的结合后,风机叶片常能够具备良好的力学性能和防水性,而且相关结构的连接也在一定程度上保障了风机叶片的质量。
并且随着现阶段复合材料在风机叶片制造中的广泛应用,风机叶片的性能、质量等也得到了良好提高。
而现阶段一个制造完成的风机叶片,其中复合材料可占整个叶片90%及以上的比重,故现代的风机叶片通常不仅具备有较轻的重量,其耐腐蚀、抗疲劳等性能也较为优越,相关特点往往来源于复合材料的特性。
同时,随着复合材料的多样化发展,如夹层结构复合材料、先进复合材料等材料的应用都在不同程度上提高了风机叶片的质量。
此外,现阶段在制造风力发电机叶片时,也常会根据所制造叶片部位的不同而使用不同种类的复合材料,如在叶片外壳的制造中常会选择玻璃纤维增强树脂作为原材料,而在叶尖、叶片主梁的制造中则会选用具备更高强度的碳纤维材料,只有叶片前缘、后缘和抗剪腹等处则常会以夹层结构复合材料为主要原材料 [1] 。
《复合材料的维修》PPT课件
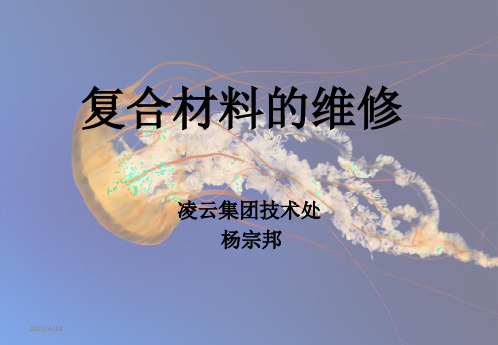
2021/4/24
24
(2)过渡性修理
这种修理主要针对有时间限制的许可损伤和可修
理的损伤,因不具备永久性修理的条件而进行的过渡
性修理。该修理要求恢复部件的强度,但不能恢复部
件的耐久性,它有不同于原始部件的检查间隔和检查
方法,最终也要被永久性修理所取代。这种修理也叫
“B级过渡性修理”。
(3)永久性修理
直径大于50mm,开胶直径75mm,层压板分层直径大 于75mm时,报废不再修理。
对于重要的复合材料构件,有专门的技术文件控 制损伤的大小,该文件与设计图纸配套使用,以保证 产品的质量。但一般还是由《结构修理手册》提供。
2021/4/24
16
第五节 复合材料修理的分类
从不同的角度,复合材料的修理方法不同,主要 有如下几种分类方法:
表面损伤的修理方法: ——用树脂填充划伤、刻痕,固化后磨平、涂漆; ——2021用/4/24混合物(相当于腻子)填充吹沙后的损伤区;31
图3-1 2021/4/24 表面划伤对拉伸强度的影响
32
——用清洁剂清洗凹陷区,后用胶黏剂填充,固化后
去除多余物,如需补漆再涂刷底漆面漆;
——将冷树脂注射到气泡或分层区,室温固化。该法只
适用于﹤25mm的损伤区。固化时可用重物或夹紧法对
构件施加压力。
第二节 分层的修理
构件边缘是最易出现损伤的区域。边缘开胶和分
层可采用树脂注射法或混合物填充法进行修理,固化
时要施加压力。该法已广泛用于碳纤维复合材料的边
2021/4/24
33
缘分层修理。层压板内的分层可采用抽钉法修理。 见图3-2
2021/4/24
图3-2 分层修理
34
风电叶片基础知识之复合材料篇一

6. 无机胶凝复合材料 基体
气硬性胶凝材料:只能在空气中不能在水中硬化。 如石灰、 石膏、镁质胶凝材料等 水硬性胶凝材料:既能在空气中,又能在水中硬化 (常称为水泥)。如:硅酸盐水泥、 锂酸盐水泥、硫酸铝水泥、磷酸盐 水泥等。 水泥的凝结硬化过程是一个复杂的物理和化学过程,硬化后的 水泥是由晶体、凝胶体、未水化颗粒、游离水、气孔等组成的多相 不均质结构体,这一结构特征——→材料抗拉强度低,冲击韧性差 (性脆),易突然失效,不能作结构材料。 增强纤维:金属纤维、无机纤维、合成纤维、植物纤维等 复合的目的,是增强、增韧,用作结构材料。
(2)复合材料的特性(character) 一般特性: a. 可设计性 b. 构件复合与成型一次性完成,整体性好 c. 性能分散性大,性能对工艺工程及工艺参数甚至一些 偶然性因素都十分敏感,难以精确控制结构和性能 d. 复合效应(多种复合效应)(principle of combined action) 一般性能特点: a. 比强度、比模量大 b. 破坏安全性高 c. 耐疲劳性好 d. 阻尼减震性好 e. 耐烧蚀性能好
无机胶凝基复合材料(fiber reinforced concrete,FRC)
(1)组成(composition)
①基体(matrix)
②增强材料(reinforcement)(都是一个庞大的材料体系、品种繁 多,结构与性能呈多样化,复合体系的系统组合、排列给复合 材料的巨大的发展空间,原则上,基体与增强体结构与性能差 异越大,愈具复合价值,但更为重要的是基体与增强体之间的 匹配。) A. 颗粒增强体:高强、高模、耐高温的陶瓷和石墨等非金属材料 的微细粉末,主要起增强、增韧作用,而不是普通填料的填充 体积或降低成本的作用,增强体价格往往比基体还贵。 B.短纤维(晶须)(chopped fiber or whisker):长径比5~1000之 间,横截面积小于 52×10―5cm2 (当量直径约 1~10m )的含缺 陷很少的单晶纤维,其模量和强度接近其纯晶体的理论值。主 要有金属晶须、氧化物晶须、氮化物晶须、硼化物晶须和无机 盐类晶须。 C. 纤维及其织物(braided fabric or filament winding):植物纤维、 动物纤维、碳物纤维、合成纤维等
《复合材料》 知识清单

《复合材料》知识清单一、什么是复合材料在现代材料科学领域,复合材料正扮演着越来越重要的角色。
那么,到底什么是复合材料呢?复合材料是由两种或两种以上不同性质的材料,通过物理或化学的方法,在宏观上组成具有新性能的材料。
简单来说,它不是单一的一种材料,而是多种材料的组合。
这些组合在一起的材料,各自保持着自己的特性,同时又相互协同,使得复合材料具有了单一材料无法达到的优越性能。
二、复合材料的分类复合材料的种类繁多,常见的分类方式有以下几种:1、按基体材料分类金属基复合材料:以金属为基体,如铝基、钛基等,具有高强度、高韧性等特点。
陶瓷基复合材料:基体是陶瓷,具有耐高温、耐磨损等性能。
聚合物基复合材料:基体为高分子聚合物,比如环氧树脂、聚酯等,重量轻、耐腐蚀。
2、按增强材料分类纤维增强复合材料:常见的纤维有玻璃纤维、碳纤维、芳纶纤维等。
纤维的加入大大提高了材料的强度和刚度。
颗粒增强复合材料:例如碳化硅颗粒增强铝基复合材料,能改善材料的耐磨性。
晶须增强复合材料:晶须具有很高的强度,能显著提高材料的性能。
3、按用途分类结构复合材料:主要用于承受载荷,如飞机的机身、桥梁的结构件等。
功能复合材料:具有特殊的功能,如导电、导热、吸波等,常用于电子、航空航天等领域。
三、复合材料的特点1、性能可设计性这是复合材料的一个显著优点。
通过选择不同的基体和增强材料,以及调整它们的比例、分布和排列方式,可以定制出满足各种特定需求的材料性能。
2、比强度和比刚度高比强度是指材料的强度除以其密度,比刚度是指材料的刚度除以其密度。
复合材料在这两个方面往往表现出色,使其在轻量化设计中具有很大的优势。
3、抗疲劳性能好由于复合材料中的纤维能够阻止裂纹的扩展,所以它们通常具有较好的抗疲劳性能,能够在长期循环载荷下保持较好的性能。
4、耐腐蚀性强许多复合材料对化学腐蚀和电化学腐蚀具有良好的抵抗能力,适用于恶劣的环境条件。
四、复合材料的制备方法1、手糊成型这是一种比较传统的方法,工人将纤维增强材料和树脂等基体材料手工涂抹在模具上,然后固化成型。
大修航空发动机涡轮叶片的检修技术范本(二篇)
大修航空发动机涡轮叶片的检修技术范本航空发动机的涡轮叶片在飞行过程中承受巨大的热量和压力,因此需要定期进行检修和维护,以保证飞机的安全性和可靠性。
以下是一份大修航空发动机涡轮叶片的检修技术范本,共____字。
范本包含了叶片检查、修复、加工以及检测等方面的技术要点。
一、涡轮叶片检查技术1. 外观检查:使用增倍镜或显微镜检查叶片表面是否存在裂纹、磨损、疲劳等问题。
特别注意检查叶片根部和边缘是否有裂纹。
2. 尺寸测量:使用数字测量仪或三坐标测量仪测量叶片的长度、宽度和厚度。
与设计数据进行对比,确保叶片的尺寸满足要求。
3. 材料检测:使用金相显微镜对涡轮叶片材料进行金相分析,检查是否存在材料缺陷,如夹杂物、孔隙等。
4. 温度检测:使用红外测温仪对叶片表面进行温度检测,确保叶片在飞行过程中没有超温现象。
5. 喷淋孔检查:检查涡轮叶片上的喷淋孔是否堵塞或损坏,以保证涡轮叶片冷却系统的正常工作。
6. 涡轮轴向间隙检查:使用涡轮叶片间隙测量仪对涡轮叶片的轴向间隙进行测量,确保间隙在设计范围内。
二、涡轮叶片修复技术1. 磨损修复:对叶片表面的磨损进行修复,可采用砂轮磨削、激光熔敷或化学沉积等方法,复原叶片的表面形状。
2. 裂纹修复:对叶片上的裂纹进行修复,可采用复合材料补丁、激光焊接或电弧焊接等方法,修复裂纹并提高叶片的强度。
3. 根部修复:对叶片根部的磨损、裂纹进行修复,可采用砂轮修整、焊接或金刚石涂层等方法,恢复叶片根部的完整性。
4. 腐蚀修复:对叶片表面的腐蚀进行修复,可采用腐蚀清除剂、研磨或化学镀等方法,去除腐蚀物并修复叶片表面的光滑度。
三、涡轮叶片加工技术1. 切割加工:使用激光切割或电火花切割机对叶片进行切割,确保切割线平整、无毛刺,并且不影响叶片的结构。
2. 研磨加工:使用砂轮或研磨机对叶片表面进行研磨,使叶片表面平整、光滑,并且满足设计要求的粗糙度。
3. 高速铣削:使用数控铣床对叶片进行高速铣削,实现对叶片形状和尺寸的精确控制。
复合材料的定义以及修复的方法
复合材料是由两种或两种以上不同性质的材料按一定方式组合而成的新材料,具有综合性能优于单一材料的特点。
复合材料的修复方法可以根据具体情况选择,常见的修复方法包括:1. 补丁修复:将与原材料相似的复合材料片或布贴在损坏区域,使用胶水或树脂将其固定在一起。
2. 粘接修复:使用特殊的胶水或树脂将损坏的复合材料部分粘接在一起,使其恢复原有的结构和性能。
3. 层叠修复:在损坏区域的周围添加多层复合材料,以增加其强度和稳定性。
4. 纤维增强修复:在损坏区域附近添加纤维增强材料,如碳纤维或玻璃纤维,以增加复合材料的强度和耐久性。
5. 热压修复:使用热压机将损坏的复合材料部分与新的复合材料片压合在一起,通过热和压力使其粘接在一起。
6. 焊接修复:对于某些特殊的复合材料,可以使用适当的焊接方法将损坏的部分焊接在一起,使其恢复原有的结构和性能。
需要注意的是,复合材料的修复方法应根据具体情况和材料特性选择,并且修复后的材料可能会有一定的性能损失,因此修复后的复合材料应进行必要的测试和评估,以确保其安全可靠。
风电基础知识培训风机叶片修复方法解析
风电基础知识培训风机叶片修复方法解析风电基础知识培训-风机叶片修复方法解析导言:风电是一种可再生能源,其在全球范围内得到广泛应用。
作为风力发电的核心部件,风机叶片的状态直接关系到风电的发电效率和寿命。
因此,风机叶片的修复方法显得尤为重要。
本文将就风机叶片修复的方法进行解析和讨论。
一、修复方法的分类根据修复方法的不同,我们可以将其分为以下几类:表面修复、部分修复和整体修复。
1. 表面修复方法表面修复方法主要针对风机叶片的表面破损进行处理,常用的修复手段包括填缝补漆、刮平痕迹以及封闭裂纹等。
这些方法操作简单,成本较低,但只能对表面进行修复,无法解决内部结构的问题。
2. 部分修复方法部分修复方法可以针对风机叶片的特定部位进行有针对性的修复。
例如,对于断裂的叶片,可以采用胶接修复的方法;对于磨损严重的叶片,可以进行涂覆修复。
这种修复方法相对于表面修复来说,可以解决风机叶片的一些内部结构问题。
3. 整体修复方法整体修复方法通常是将叶片进行拆解,进行彻底的修复和加固。
这种修复方法的优势在于可以对叶片的各个部分进行全面的检查和修复,确保其恢复到最佳状态。
然而,整体修复方法需要更高的成本和时间,在实际应用中需要慎重考虑。
二、常见修复材料和工艺风机叶片的修复需要使用到一些特殊的材料和工艺,下面将介绍几种常见的修复材料和工艺。
1. 玻璃纤维玻璃纤维是一种常见的修复材料,其优势在于重量轻、强度高、价格低廉。
使用玻璃纤维进行叶片修复时,首先需要将受损部位清理干净,然后用玻璃纤维布进行包裹,并使用环氧树脂进行固化。
这种修复工艺简单易行,对于一些小范围的损坏非常适用。
2. 碳纤维碳纤维是一种高强度、低密度的复合材料,具有优良的抗拉强度和刚度。
使用碳纤维进行叶片修复时,可以通过预应力或者层叠等方式进行固化,以增加叶片的强度和稳定性。
碳纤维修复工艺比较复杂,需要专业的操作和设备。
3. 翻新涂料翻新涂料是一种常用的风机叶片表面修复材料,其不仅可以修复磨损和腐蚀部位,还能提高叶片表面的光滑度和抗紫外线能力。
复合材料—复合材料的修复(航空材料)
(3) 热黏结修理 在这种修理中,首先清除已破坏铺层,将新的修补层用共固化修补,以得到一个
气动埋头修理。 优点:具有恢复原有形状及保持光滑气动外形的能力,可以剪裁成任意尺寸、任意蒙 皮厚度和纤维方向; 缺点:环氧树脂体需要冷藏,许多情况下固化需要热源和压力源。
2. 修理的方法
➢ 热修补 ➢ 用湿法完成先进复合材料结构的热黏合修理时温度为93-110℃,121℃或177
复ห้องสมุดไป่ตู้材料的修复
复合材料的修复
1. 修理的类型
➢(1)螺接修理 将预固化复合材料补片或铝补片铆接或螺接在破损区的这种用紧固件连接修理的方法
称为螺接修理。 优点:可以快速作临时性的修理; 缺点:有时候找不到通向部件或层合板后面的通道,不能使受压部位回复到修理钱的强 度。 ➢(2)冷黏结 将预固化的补片粘结在破损的表面的修理方法称为冷粘结修理。 优点:在正确的条件下,它可作为一种非常快捷的永久性修理; 缺点:需要手头有足够数量的一定厚度、一定铺层方向、一定直径和形状的补片,切不 能用于大面积的修理。
℃也可接受。结构维修手册为每个部件提供了修理数据,并规定了应用范围以 及最大尺寸。 ➢ 常用的维修工具:电热毯,电炉或者热压罐。 ➢ 冷修补 ➢ 使用湿法铺层材料的冷修补是在室温到66 ℃下进行的。为了加速树脂的固化时 间,允许使用电热毯、加热灯或者热空气烘箱。
- 1、下载文档前请自行甄别文档内容的完整性,平台不提供额外的编辑、内容补充、找答案等附加服务。
- 2、"仅部分预览"的文档,不可在线预览部分如存在完整性等问题,可反馈申请退款(可完整预览的文档不适用该条件!)。
- 3、如文档侵犯您的权益,请联系客服反馈,我们会尽快为您处理(人工客服工作时间:9:00-18:30)。
风机叶片修复材料浅谈内容摘要风力发电机组长期在恶劣的自然环境中暴露运行,不仅要承受强大的风载荷,还要经受气体冲刷、砂石粒子冲击,以及强烈的紫外线照射等外界侵蚀。
为了提高损伤修复过程中所使用复合材料的载荷、耐腐蚀和耐冲刷等性能, 必须对所使用叶片修复材料中的树脂基体系统进行精心研究和筛选, 对传统叶片修复工艺进行创新。
采用性能优异的环氧树脂, 改善玻璃纤维/树脂界面的粘结性能, 提高叶片的承载能力, 扩大玻璃纤维在大型叶片中的应用范围。
研究结果表明叶片修复过程中合理使用的复合材料完全可以达到在恶劣工作环境中长期使用的性能要求。
关键词:风力机; 叶片; 环氧树脂;引言随着风力发电机单机功率的不断提高,叶片的质量和尺寸也越来越大,对叶片的要求也越来越高:要求叶片质量轻且分布均匀,外形尺寸精度控制准确;具有最佳的疲劳强度和机械性能,能经受暴风等极端恶劣条件和随机负荷的考验;叶片旋转时的振动频率特性曲线正常,传递给整个发电系统的负荷稳定性好;耐腐蚀、抗紫外线照射和抗雷击的性能好;发电成本较低,维护费用最低。
叶片的材料越轻、强度和刚度越高,叶片抵御载荷的能力就越强,叶片就可以做得越大,它的捕风能力也就越强。
因此,轻质高强、耐蚀性好、具有可设计性的玻璃纤维增强环氧树脂复合材料是目前国内大型风机叶片生产及修复的首选材料。
本文主要探讨了风机叶片生产和修复过程中所用的主要材料玻璃纤维增强环氧树脂复合材料,以及PVC材料。
一、叶片损伤原因为了提高风机的发电效率,风机绝大多数处在地理、气候环境相对恶劣的地区,从而导致风机叶片容易遭受损伤。
其中对于风机叶片发生故障率最大的损伤原因是雷击,而且雷击往往会给风机叶片带来较严重的损伤甚至报废。
其次为风沙磨损、酸雨腐蚀,导致叶片表面出现麻点,影响风机使用寿命。
飞鸟撞击也是造成风机叶片损伤的一大杀手,由于风机所在地人眼稀少,所以飞鸟较多,飞鸟撞击往往会使风机叶片表面大面漆胶衣脱落。
另外由于风机叶片质量和体积较大,所以运输和吊装存在较大难度,不可避免的造成一定程度的损伤,发生率较小但若发生后果不堪设想,可能直接导致叶片报废,不可修复。
最后叶片材料老化也是导致风机叶片损伤的一大原因,但是由于材料质量在不断提高,所以发生概率会越来越小。
二、叶片损伤实例照片雷击造成损伤Lightning1253 4风沙磨损造成的损伤飞鸟撞击造成的损伤吊装运输是造成的损伤材料老化自然开裂造成的损伤三、叶片损伤部位及概率以装机容量为5万kw的某风场33台某国产风机为例,巡检33台投运将近2年风机,其中5台风机的5支叶片存在不同程度的损伤,单台风机叶片出现故障率高达15%左右,而且发现其中3台风机为叶片损伤部位在叶尖,叶尖损伤概率达60%。
四、叶片修复的必要性国内的风力发电场遍布大江南北,所处地理条件和气候环境各不相同。
北方的低温、风沙、强辐射、雷雨天气集中,南方的高温、高湿、盐雾、飞鸟多等都存在各自不同的自然条件。
再加上国内投运风机型号种类繁多导致所使用叶片的结构、材料更是五花八门,其综合性能差异较大,风机选址也经常性的为了提高发电量而将风机树立在最高点,而致使风机遭受雷击的几率较高,叶片材料也随着投运时间的增长导致其各种性能不断降低而出现不同程度的老化情况。
而且风机总是处在条件恶劣的环境中,并且24小时的处于工作状态,这就使材料易于受到损害,一旦某一部位受损,这个部位就成为整支叶片的薄弱所在,如果不停机及时维修不仅会影响风机发电量及发电效率,而且如果事故扩大就会造成叶片折断、报废甚至出现倒塔等一些列不可预测的严重后果。
五、叶片修复材料的重要性高质量的叶片修复=50%的叶片修复材料质量+50%材料的正确使用叶片修复材料主要为环氧树脂材料,而环氧树脂的种类更是五花八门,所以正确的选择环氧树脂材料最为关键。
材料的性能上有很大差异,如使用不慎不仅不能达到修复的效果而且还会使损伤范围加大,造成不可修复的严重后果。
六、叶片修复材料性能要求恶劣的环境和长期不停地运转,对叶片的要求有:比重轻且具有最佳的疲劳强度和机械性能, 能经受暴风等极端恶劣条件和随机负荷的考验;叶片的玻璃纤维增强环氧树脂复合材料弹性、旋转时的惯性及其振动频率特性曲线都正常,传递给整个发电系统的负荷稳定性好;耐腐蚀、紫外线照射和雷击性能好。
但是随着风机叶片运行时间的增长伴随着叶片老化出现损伤,叶片修复材料必须达到以致超过出厂时的各项性能要求要求,叶片的原材料主要由增强材料、环氧树脂、夹芯材料三部分组成。
叶片修复材料6.1 增强材料对于同一种基体树脂来讲, 采用玻璃纤维增强的复合材料制造的叶片其强度和刚度的性能要差于采用碳纤维增强的复合材料制造的叶片的性能。
但是, 碳纤维的价格目前是玻璃纤维的10倍左右,由于价格的因素,目前的叶片制造采用的增强材料主要以玻璃纤维为主。
随着叶片长度不断增加,叶片对增强材料的强度和刚性等性能也提出了新的要求, 玻璃纤维在2MW 风机复合材料叶片制造中逐渐出现性能方面的不足。
为了保证叶片能够安全地承担风能载荷, 风机叶片可以采用玻璃纤维/碳纤维混杂复合材料结构。
但是在叶片修复过程中由于所用的碳纤维量较少所以完全可以应用碳纤维增强环氧树脂复合材料对损伤叶片进行修复。
6.2 环氧树脂环氧树脂应满足以下基本性能条件:固化方便:选用各种不同的固化剂,环氧树脂体系几乎可以在0-180℃温度范围内固化;粘附力强:环氧树脂分子链中固有的极性羟基和醚键的存在,使其对各种物质具有很高的粘附力。
环氧树脂固化时的收缩性低,产生的内应力小,这也有助于提高粘附强度;收缩性低:环氧树脂和所用的固化剂的反应是通过直接加成反应或树脂分子中环氧基的开环聚合反应来进行的,没有水或其它挥发性副产物放出。
它们和不饱和聚酯树脂、酚醛树脂相比,在固化过程中显示出很低的收缩性(小于2% );力学性能: 固化后的环氧树脂体系具有优良的力学性能;电性能: 固化后的环氧树脂体系是一种具有高介电性能、耐表面漏电、耐电弧的优良绝缘材料;化学稳定性:通常,固化后的环氧树脂体系具有优良的耐碱性、耐酸性和耐溶剂性。
像固化环氧体系的其它性能一样,化学稳定性也取决于所选用的树脂和固化剂。
适当地选用环氧树脂和固化剂, 可以使其具有特殊的化学稳定性能;尺寸稳定性:上述的许多性能的综合,使环氧树脂体系具有突出的尺寸稳定性和耐久性;耐霉菌:固化的环氧树脂体系耐大多数霉菌,可以在苛刻的热带条件下使用。
6.3 夹芯材料为了提高叶片的刚度同时又能减轻叶片的重量, 在叶片中添加了夹芯材料, 常用的夹芯材料有两种, 一种是轻木, 另一种是PVC 泡沫。
但是不管是哪种夹芯材料都应满足以下的特点:(1)比重小;(2)有极高的强度和硬度;(3)比热小, 受气温变化影响小;(4)有良好的抗化学腐蚀性能;(5)有良好的防火性能;(6)与树脂有良好的结合性。
七、满足性能要求的材料种类及特点7.1增强材料玻璃纤维增强叶片的受力特点是在玻璃纤维方向能承受很高的拉应力,而其它方向承受的力相对较小。
叶片结构是由蒙皮和腹板组成,蒙皮采用夹芯结构, 中间层是轻木,上下面层为玻璃纤维增强材料。
面层由单向层和,±45°层组成。
单向层可选用单向织物或单向玻璃纤维铺设,一般用7:1或4:1玻璃纤维布,以承受由离心力和气动弯矩产生的轴向应力。
为简化成型工艺,可不用±45°玻璃纤维布层,而采用1:1玻璃纤维布,均沿轴向铺设,以承受主要由扭矩产生的剪切应力,一般铺放在单向层外侧。
腹板的结构形式也是夹芯结构。
但是,在蒙皮与腹板的结合部位,即梁帽处必须是实心玻璃纤维增强结构。
这是因为此部分腹板与蒙皮相互作用,应力较大,必须保证蒙皮的强度和刚度。
经过对长度为10-60m的叶片进行的统计表明,叶片质量按长度的三次方增加。
叶片轻量化对运行、疲劳寿命、能量输出有重要的影响。
同时为了保证在极端风载下叶尖不碰塔架,叶片必须具有足够的刚度。
既要减轻叶片的质量,又要满足强度与刚度要求, 有效的办法是采用碳纤维增强材料。
碳纤维增强材料的拉伸弹性模量是玻璃纤维增强材料的2-3倍。
2MW叶片采用碳纤维增强可充分发挥其高弹轻质的优点。
经过分析,采用碳纤维/玻璃纤维混杂增强的方案,叶片可减重20%-40%。
因此采用碳纤维/玻璃纤维混杂增强对抑制质量的增大是必要的,同时降低了风能成本,叶片也可具有足够刚性和长度。
尤其是在翼缘等对材料强度和刚度要求较高的部位,使用碳纤维作为增强材料,这样不仅可以提高叶片的承载能力,由于碳纤维具有导电性,及可以有效地避免雷击对叶片造成损伤。
7.2环氧树脂根据分子结构, 环氧树脂大体上可分为五大类:缩水甘油醚类环氧树脂、缩水甘油酯类环氧树脂、缩水甘油胺类环氧树脂、线型脂肪族类环氧树脂和脂环族类环氧树脂。
复合材料工业上使用量最大的环氧树脂品种是缩水甘油醚类环氧树脂, 而其中又以二酚基丙烷型环氧树脂(简称双酚A 型环氧树脂)为主。
二酚基丙烷型环氧树脂实际上是含不同聚合度的分子的混合物。
其中大多数的分子是含有两个环氧基端的线型结构。
少数分子可能支化, 极少数分子终止的基团是氯醇基团而不是环氧基。
因此环氧树脂的环氧基含量、氯含量等对树脂的固化及固化物的性能有很大的影响。
环氧树脂的控制指标如下:环氧值: 环氧值是鉴别环氧树脂性质的最主要的指标, 环氧树脂型号就是按环氧值不同来区分的。
环氧值是指每100g 树脂中所含环氧基的物质的量数。
环氧值的倒数乘以100就称之为环氧当量。
环氧当量的含义为含有1mol环氧基的环氧树脂的克数;无机氯含量: 树脂中的氯离子能与胺类固化剂起络合作用而影响树脂的固化,同时也影响固化树脂的电性能, 因此氯含量是环氧树脂的一项重要指标;有机氯含量: 树脂中的有机氯含量标志着分子中未起闭环反应的那部分氯醇基团的含量,其含量应尽可能地降低,否则也会影响树脂的固化及固化物的性能;与其粘度或软化点。
应用于2MW 风机复合材料叶片的环氧树脂,最好选用高环氧值(> 0. 40)的树脂,如618、6101,其渗透性好, 强度较好。
环氧树脂一般和添加物同时使用,以获得应用价值。
添加物可按不同用途加以选择,常用添加物有以下几类: 固化剂、改性剂、填料、稀释剂等。
固化剂是必不可少的添加物,选用加温固化的固化剂,一般用酸酐、芳香类固化剂;改性剂的作用是为了改善环氧树脂的柔性、抗剪、抗弯、抗冲、提高绝缘性能等。
常用改性剂有: 聚硫橡胶、聚乙烯醇叔丁醛、丁腈橡胶类、酚醛树脂类、聚酯树脂、尿醛三聚氰胺树脂等。
7.3夹芯材料轻木, 又称南美轻木、巴尔沙木, 它是由紧密排列的细胞结构组成的, 经过烘焙, 杀菌处理, 具有轻质高强等特点。
是目前叶片夹芯材料中最优的选择。