碳化硅陶瓷
多孔碳化硅陶瓷及复合材料的制备与性能共3篇

多孔碳化硅陶瓷及复合材料的制备与性能共3篇多孔碳化硅陶瓷及复合材料的制备与性能1多孔碳化硅陶瓷及复合材料的制备与性能随着科学技术的发展和人们对环境保护的重视,传统陶瓷材料的应用范围已经不能满足人们的需求。
多孔碳化硅材料凭借其高度的化学稳定性、热稳定性和机械强度等优良性能,在高级材料领域应用广泛。
本文将介绍多孔碳化硅陶瓷的制备方法以及其在新材料领域的应用。
一、多孔碳化硅陶瓷的制备方法多孔碳化硅陶瓷的制备方法包括两种:一种是传统的陶瓷制备方法,一种是新型的多级微波制备方法。
1. 传统制备方法传统的多孔碳化硅陶瓷制备方法包括高温烧结和化学气相沉积两种。
高温烧结法是将混合了碳化硅粉末和其他添加剂或者硅的混合粉末,在高温下进行烧结得到多孔碳化硅材料。
化学气相沉积法是将氯化硅等硅源及碳源放入炉中进行化学反应,最终得到多孔碳化硅材料。
2. 多级微波制备方法多级微波制备法是指通过微波辐射、干燥和碳化构成,形成多孔碳化硅陶瓷材料。
首先将硅源和碳源均匀混合,然后使用微波辐射干燥,在多个微波腔中进行碳化反应,最终得到多孔碳化硅陶瓷材料。
二、多孔碳化硅陶瓷的性能分析1. 化学稳定性多孔碳化硅材料具有很好的化学稳定性,能够抵御酸、碱等强化学腐蚀,不会被氧化、退化,可长期使用于高温、高压等恶劣环境下。
2. 热稳定性多孔碳化硅材料热稳定性较高,耐热温度高达1500℃以上,不易熔化或瓦解,能够在高温下保持稳定结构和性能。
3. 机械强度多孔碳化硅材料具有很高的机械强度,能够承受很大的压力和载荷,保持长期的强度稳定性。
三、多孔碳化硅陶瓷复合材料的应用多孔碳化硅陶瓷复合材料是指将多孔碳化硅材料与其他材料(如金属、聚合物等)复合,形成性能更为优异的材料。
多孔碳化硅陶瓷复合材料具有多孔材料的高孔隙率和复合材料的高强度、高稳定性等优点,广泛应用于先进制造技术、光伏、半导体等领域。
结论多孔碳化硅陶瓷是一种具有高度化学稳定性、热稳定性和机械强度等优良性能的新型材料,在复合材料中具有广泛的应用前景。
树脂碳化硅陶瓷基复合材料

树脂碳化硅陶瓷基复合材料树脂碳化硅陶瓷基复合材料,这名字一听就觉得挺高级的,对吧?说实话,听到这个名词,脑海中就浮现出那些高科技的实验室,科学家们在里面穿着白大褂,眉头紧锁,埋头苦干。
不过,咱们今天就轻松聊聊这个看似复杂但其实也不那么神秘的东西。
树脂碳化硅陶瓷基复合材料就是把树脂和碳化硅结合在一起,形成一种特别的材料。
它有点像做菜,得把各种食材搭配好,才能做出好吃的菜。
咱们得知道,树脂就像厨房里的调味料,能让材料更加耐用,提升性能。
想象一下,树脂就像盐,不加的话,菜就没味道,材料也会觉得“乏味”。
而碳化硅则是主菜,哇,绝对是个硬汉!它的耐高温、耐磨损的特性,让它在工业上大显身手,简直就像是个战士,保护着其他材料不受伤害。
说到这里,有没有觉得这组合就像是“菜鸟与老鸟”的搭配?一个柔软,一个硬朗,简直就是天生一对。
这种复合材料可不是光说好听的,它在实际应用中也大有作为。
比如,在航空航天领域,飞机和航天器对材料的要求特别高。
想想看,飞得那么高,温度变化多大,压力多大,材料要是出点问题,后果可就严重了。
因此,树脂碳化硅陶瓷基复合材料就像是超级英雄,凭借出色的性能,保护着飞行器的安全。
而且它还轻,减少了整体的重量,让飞行更高效,简直是“空中飞人”的最佳拍档。
说到这里,可能有人会问,树脂碳化硅陶瓷基复合材料还有什么优势呢?嘿嘿,除了高温和耐磨损,它还具备优良的化学稳定性。
意思就是说,它不容易被各种酸碱腐蚀,能在恶劣环境下“顽强生存”。
这就像是个“硬核”玩家,面对各种挑战都毫不畏惧,真是让人佩服。
在制造过程中,树脂和碳化硅的配比也是个学问。
有点像调酒,配对不当就容易出错。
科学家们得反复实验,寻找那个“完美配方”。
要是比例搞错了,材料的性能可就大打折扣。
想象一下,喝了太多糖的饮料,甜得让人受不了,那材料的“口感”也会变得糟糕。
选择适合的制造工艺,比如烧结、浸渍等,能让最终的材料如同精致的蛋糕,层次分明,口感绝佳。
碳化硅陶瓷的制备技术

喷嘴:作喷嘴的陶瓷材料有多种,常用
的是氧化铝、碳化硅和碳化硼陶瓷等。 氧化铝陶瓷喷嘴的价格低,但由于硬度 低,其耐磨性较差,多用于喷砂工作量 不大的场合。碳化硅陶瓷的使用寿命是 氧化铝陶瓷的3-5倍【】,与硬质合金 相当,多用于硬质合金的替代品,特别 是在手持喷枪的工况中使用。
磁力泵泵件:随着工业化的发展,特别
碳化硅陶瓷的制备技术及应用
一、碳化硅的前沿
二、SiC粉末的合成 三、SiC的烧结方法
四、反应烧结碳化硅的成型工艺
五、碳化硅陶瓷的应用
碳化硅陶瓷的制备技术及应用
1、前沿:
碳化硅陶瓷材料具有高温强度大, 高温抗氧化性 强、耐磨损性能好 ,热稳定性佳 ,热膨胀系数小, 热导率大, 硬度高 ,抗热震和耐化学腐蚀等优良特 性. 在汽车、机械化工、环境保护、 空间技术、 信 息电子 、能源等领域有着日益广泛的应用,已经成为 一种在很多工业领域性能优异的其他材料不可替代的 结构陶瓷。
以下是对四种烧结方法的一些概括: 实验表明,采用无压烧结、热压烧结、热 等静压烧结和反应烧结的SiC陶瓷具有各异的 性能特点。假如就烧结密度和抗弯强度来说, 热压烧结和热等静压烧结SiC陶瓷相对较高, 反应烧结SiC相对较低。另一方面,SiC陶瓷的 力学性能还随烧结添加剂的不同而不同。无压 烧结、热压烧结和反应烧结SiC陶瓷对强酸、 强碱具有良好的抵抗力,但反应烧结SiC陶瓷 对HF等超强酸的抗蚀性较差。就耐高温性能比 较来看,当温度低于900℃时,几乎所有SiC陶 瓷强度均有所提高;当温度超过1400℃时,反 应烧结SiC陶瓷抗弯强度急剧下降。(这是由 于烧结体中含有一定量的游离Si,当超过一定 温度抗弯强度急剧下降所致)对于无压烧结和 热等静压烧结的SiC陶瓷,其耐高温性能主要 受添加剂种类的影响
碳化硅和氮化硅硬度
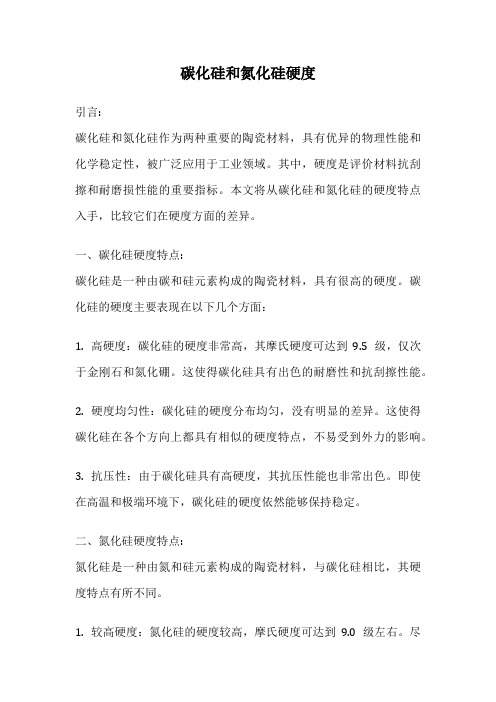
碳化硅和氮化硅硬度引言:碳化硅和氮化硅作为两种重要的陶瓷材料,具有优异的物理性能和化学稳定性,被广泛应用于工业领域。
其中,硬度是评价材料抗刮擦和耐磨损性能的重要指标。
本文将从碳化硅和氮化硅的硬度特点入手,比较它们在硬度方面的差异。
一、碳化硅硬度特点:碳化硅是一种由碳和硅元素构成的陶瓷材料,具有很高的硬度。
碳化硅的硬度主要表现在以下几个方面:1. 高硬度:碳化硅的硬度非常高,其摩氏硬度可达到9.5级,仅次于金刚石和氮化硼。
这使得碳化硅具有出色的耐磨性和抗刮擦性能。
2. 硬度均匀性:碳化硅的硬度分布均匀,没有明显的差异。
这使得碳化硅在各个方向上都具有相似的硬度特点,不易受到外力的影响。
3. 抗压性:由于碳化硅具有高硬度,其抗压性能也非常出色。
即使在高温和极端环境下,碳化硅的硬度依然能够保持稳定。
二、氮化硅硬度特点:氮化硅是一种由氮和硅元素构成的陶瓷材料,与碳化硅相比,其硬度特点有所不同。
1. 较高硬度:氮化硅的硬度较高,摩氏硬度可达到9.0级左右。
尽管比碳化硅稍低,但仍然比大部分金属和非金属材料的硬度要高。
2. 硬度均匀性:与碳化硅类似,氮化硅的硬度分布均匀,各个方向上的硬度相差不大。
3. 耐磨性:氮化硅具有较好的耐磨性能,能够在高温和恶劣环境下保持较长时间的使用寿命。
三、碳化硅和氮化硅硬度的比较:碳化硅和氮化硅在硬度方面有一些不同之处。
主要体现在以下几个方面:1. 硬度值:碳化硅的硬度略高于氮化硅。
碳化硅的摩氏硬度可达到9.5级,而氮化硅的摩氏硬度约为9.0级。
2. 硬度均匀性:碳化硅和氮化硅的硬度分布均匀,各个方向上的硬度相差不大。
3. 应用领域:由于碳化硅硬度更高,常用于一些对硬度要求较高的场合,如磨料、陶瓷刀具等。
而氮化硅虽然硬度稍低,但具有更好的导热性能,常用于制造散热器、导热模块等。
结论:碳化硅和氮化硅作为重要的陶瓷材料,具有优异的硬度特点。
碳化硅的硬度略高于氮化硅,分别为9.5级和9.0级左右。
碳化硅陶瓷。ppt
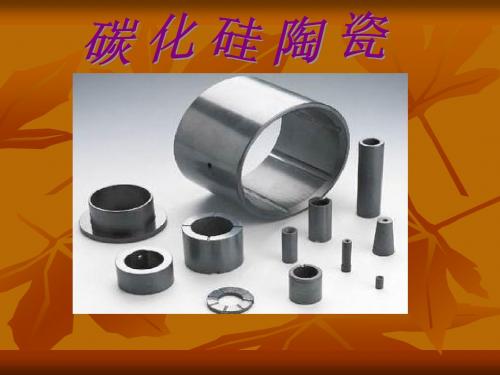
超细SiC纳米微粉的合成及意义
合成法:
用自制的树脂热裂解碳做碳源,用纳米级 SiO2微粉做硅源,在微波炉内合成。原料配比: 按反应式使C过量10%,以减少产品中的含氧量。 准确称取纳米级SiO2和树脂热裂解,以无水乙醇 为介质球磨24h之后烘干压制成型,在氮气下在 微波炉中进行烧结,烧结温度在1300到1500摄 氏度,时间10到20分钟
热压烧结能降低烧结温度,得到较致密 和抗弯强度高的SiC陶瓷,但是热压工艺效率 低,很难制造形状复杂的SiC 部件。
热等静压烧结能获得形状复杂且力学 性能较好的致密SiC 制品,但是因HIP 烧结必 须对素坯进行包封,目前难以实现工业化生 产。
反应烧结生产工艺成熟, 产品性能稳定, 生产的反应烧结碳化硅密度大于3.02g/cm3 目前此类产品国内需求量大,市场前景良好。
碳化硅(SiC)陶瓷具有优良的高温力 学性能, 抗氧化性强、耐磨损性好、热 稳定性佳、热膨胀系数小、热导率大、
硬度高以及抗热震和耐化学腐蚀等优 良性能,SiC陶瓷的缺点是脆性较大。 SiC陶瓷在石油、化工、微电子、汽车、 航天、航空、造纸、激光、矿业及原 子能等工业领域获得了广泛的应用。
领域
使用环境
热压烧 结
3.21
3.2
640 650 450 4.8 130 45
热等静 压烧结
3.21
3.8
640 610 450 4.7 220 50
反应烧 结
3.05
3.0
380 300 350 4.5 140 50
常压烧结被认为是SiC烧结最有前途的 烧结方法,通过常压烧结工艺可以制备出大 尺寸和复杂形状的SiC陶瓷制品。
碳化硅(SiC)最初的用途是作为磨
具、磨料和耐火材料,后发展到作为加热 元件——硅碳电阻棒的原料使用。直到2 0世纪中叶,特别是70年代以后,Si C独特的性能才被人们逐渐认识。因为它 具有耐高温、耐磨耗、耐腐蚀及高的热传 导率等特点,被开发的用途越来越多,应 用面越来越广,作为一种新型的精细陶瓷 材料,受到了人们极大的关注。
碳化硅陶瓷烧结工艺
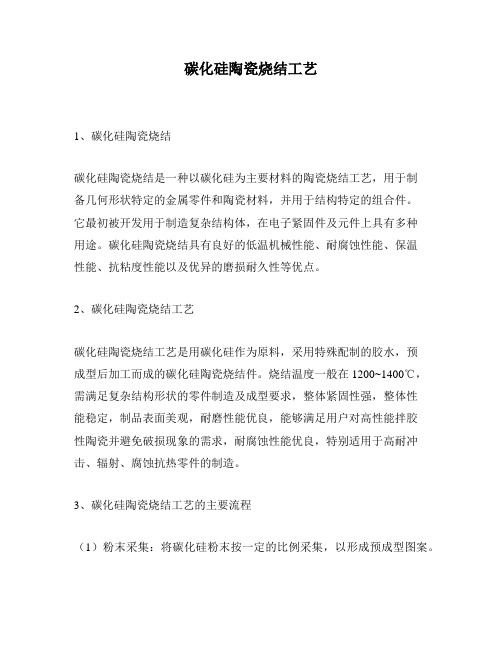
碳化硅陶瓷烧结工艺1、碳化硅陶瓷烧结碳化硅陶瓷烧结是一种以碳化硅为主要材料的陶瓷烧结工艺,用于制备几何形状特定的金属零件和陶瓷材料,并用于结构特定的组合件。
它最初被开发用于制造复杂结构体,在电子紧固件及元件上具有多种用途。
碳化硅陶瓷烧结具有良好的低温机械性能、耐腐蚀性能、保温性能、抗粘度性能以及优异的磨损耐久性等优点。
2、碳化硅陶瓷烧结工艺碳化硅陶瓷烧结工艺是用碳化硅作为原料,采用特殊配制的胶水,预成型后加工而成的碳化硅陶瓷烧结件。
烧结温度一般在1200~1400℃,需满足复杂结构形状的零件制造及成型要求,整体紧固性强,整体性能稳定,制品表面美观,耐磨性能优良,能够满足用户对高性能拌胶性陶瓷并避免破损现象的需求,耐腐蚀性能优良,特别适用于高耐冲击、辐射、腐蚀抗热零件的制造。
3、碳化硅陶瓷烧结工艺的主要流程(1)粉末采集:将碳化硅粉末按一定的比例采集,以形成预成型图案。
(2)成型:将预成型图案放入特殊设计的模具中,按照有组织的形式压制成型。
(3)烧结:将成型后的碳化硅陶瓷结构在高温热环境中进行加热烧结,形成非常坚固的结构模型。
(4)装配:将烧结后的碳化硅陶瓷件进行装配,经过成型和定型等处理,使之外形一致,形成安装形态。
(5)喷涂:将装配完毕的碳化硅陶瓷进行喷涂,涂上特定颜色的涂层,使之外观美观,具有防潮效果。
4、优点碳化硅陶瓷烧结具有良好的低温机械性能、耐腐蚀性能、保温性能、抗粘度性能以及优异的磨损耐久性等优点,烧结过程速度快,烧结时间短,过程温度低,温度分布均匀,可以减少烧结过程中的物理变化及化学变化,因此它能够生产出密度高、尺寸精确、尺寸大小稳定、层间黏结强度高的陶瓷结构件。
碳化硅陶瓷变形原因

碳化硅陶瓷变形原因
变形是产品烧成变形是陶瓷行业最常见、最严重的缺陷,如口径歪扭不圆,几何形状有不规则的改变等。
主要原因是装窑方法不当。
如匣钵柱行不正,匣钵底或垫片不平,使窑车运行发生震动,影响到产品的变形。
另外,产品在烧成中坯体预热与升温快时,温差大易发生变形。
烧成温度过高或保温时间太长也会造成大量的变形缺陷。
使用的匣钵高温强度差、或涂料抹不平时也会造成烧成品的变形。
1、制品造型设计在结构上不合理或不符合工艺材料和工艺技术要求:①重心位置处理不当,上重下轻。
②体形过高、过长;各部分厚度与尺寸不适宜、不匀称;蓄泥不当等。
2、坯料配方不当,使烧结和收缩不均衡:①坯料中高可塑性粘土用量过大,灼减量过大,使干燥收缩与烧成收缩过大。
②坯料中熔剂量过大。
Al2O3含量过低。
坯体在高温下液相量过多且粘度低。
③、坯、釉二者膨胀系数配合不当。
3、有颗粒杂质,制造设计工艺材料不过关。
厚度不均匀,一边重,一边轻。
4、温度不均匀,在烧制过程中坯体变形,重心偏离。
5、成形工艺不当,成形压力过小或过大,设备不精良,振动大。
6、材质达不到要求,局部膨胀所以控制变形应当首先清楚杂质,保持温度与厚度均匀,防止在操作过程中被外力触碰。
碳化硅陶瓷杨氏模量
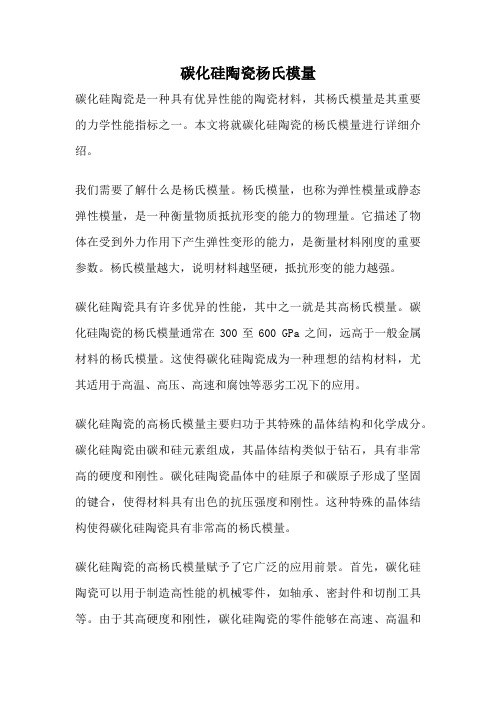
碳化硅陶瓷杨氏模量碳化硅陶瓷是一种具有优异性能的陶瓷材料,其杨氏模量是其重要的力学性能指标之一。
本文将就碳化硅陶瓷的杨氏模量进行详细介绍。
我们需要了解什么是杨氏模量。
杨氏模量,也称为弹性模量或静态弹性模量,是一种衡量物质抵抗形变的能力的物理量。
它描述了物体在受到外力作用下产生弹性变形的能力,是衡量材料刚度的重要参数。
杨氏模量越大,说明材料越坚硬,抵抗形变的能力越强。
碳化硅陶瓷具有许多优异的性能,其中之一就是其高杨氏模量。
碳化硅陶瓷的杨氏模量通常在300至600 GPa之间,远高于一般金属材料的杨氏模量。
这使得碳化硅陶瓷成为一种理想的结构材料,尤其适用于高温、高压、高速和腐蚀等恶劣工况下的应用。
碳化硅陶瓷的高杨氏模量主要归功于其特殊的晶体结构和化学成分。
碳化硅陶瓷由碳和硅元素组成,其晶体结构类似于钻石,具有非常高的硬度和刚性。
碳化硅陶瓷晶体中的硅原子和碳原子形成了坚固的键合,使得材料具有出色的抗压强度和刚性。
这种特殊的晶体结构使得碳化硅陶瓷具有非常高的杨氏模量。
碳化硅陶瓷的高杨氏模量赋予了它广泛的应用前景。
首先,碳化硅陶瓷可以用于制造高性能的机械零件,如轴承、密封件和切削工具等。
由于其高硬度和刚性,碳化硅陶瓷的零件能够在高速、高温和恶劣环境下保持稳定的性能,具有较长的使用寿命。
其次,碳化硅陶瓷还可以用于制造高温炉具和陶瓷加热器等高温设备。
碳化硅陶瓷的高杨氏模量使得它能够承受高温下的热膨胀和热应力,具有较好的热稳定性和耐热性能。
碳化硅陶瓷还可以用于制造电子器件和光学器件等高性能产品。
由于其高杨氏模量和优异的热导性能,碳化硅陶瓷可以用于制造高功率电子器件和高功率激光器等高性能器件。
同时,碳化硅陶瓷还具有优异的耐腐蚀性能和化学稳定性,可以在恶劣的化学环境中使用。
碳化硅陶瓷的杨氏模量是其重要的力学性能指标之一。
碳化硅陶瓷具有高杨氏模量的优点,使得它在许多领域都有广泛的应用。
通过进一步研究和开发,相信碳化硅陶瓷一定会在更多的领域发挥其独特的优势,为人类的生产生活带来更多的便利和创新。
- 1、下载文档前请自行甄别文档内容的完整性,平台不提供额外的编辑、内容补充、找答案等附加服务。
- 2、"仅部分预览"的文档,不可在线预览部分如存在完整性等问题,可反馈申请退款(可完整预览的文档不适用该条件!)。
- 3、如文档侵犯您的权益,请联系客服反馈,我们会尽快为您处理(人工客服工作时间:9:00-18:30)。
1、无压烧结
1974年美国GE公司通过在高纯度β-SiC细粉中同时加入少量的B和 C,采用无压烧结工艺,于2020℃成功地获得高密度SiC陶瓷。目前, 该工艺已成为制备SiC陶瓷的主要方法。美国GE公司研究者认为:晶界 能与表面能之比小于1.732是致密化的热力学条件,当同时添加B和C 后,B固溶到SiC中,使晶界能降低,C把SiC粒子表面的SiO2还原除 去,提高表面能,因此B和C的添加为SiC的致密化创造了热力学方面的 有利条件。然而,日本研究人员却认为SiC的致密并不存在热力学方面 的限制。还有学者认为,SiC的致密化机理可能是液相烧结,他们发 现:在同时添加B和C的β-SiC烧结体中,有富B的液相存在于晶界 处。关于无压烧结机理,目前尚无定论。
碳化硅工艺流程
碳化硅(SiC)陶瓷,具有抗氧化性强,耐磨性能好,硬度高,热稳定 性好,高温强度大,热膨胀系数小,热导率大以及抗热震和耐化学腐蚀 等优良特性。因此,已经在石油、化工、机械、航天、核能等领域大显 身手,日益受到人们的重视。例如,SiC陶瓷可用作各类轴承、滚珠、 喷嘴、密封件、切削工具、燃汽涡轮机叶片、涡轮增压器转子、反射屏 和火箭燃烧室内衬等等。
SiC具有α和β两种晶型。β-SiC的晶体结构为立方晶系,Si和C分别组 成面心立方晶格;α-SiC存在着4H、15R和6H等100余种多型体,其 中,6H多型体为工业应用上最为普遍的一种。在SiC的多种型体之间存 在着一定的热稳定性关系。在温度低于1600℃时,SiC以β-SiC形式存 在。当高于1600℃时,β-SiC缓慢转变成α-SiC的各种多型体。4H- SiC在2000℃左右容易生成;15R和6H多型体均需在2100℃以上的高温 才易生成;对于6H-SiC,即使温度超过2200℃,也是非常稳定的。 SiC中各种多型体之间的自由能相差很小,因此,微量杂质的固溶也会 引起多型体之间的热稳定关系变化。
钠长石与钙长石以各种比例互相熔解,变成多种多样的长石。这些总称 为“斜长石”,它的性质依其中所含钠长石与钙长石的比例而定。还有 一种和正长石(钾长石)为同样成分而形状稍有变异的,至今也多误传
为正长石,其实这种应该叫做“微斜长石”。
3、瓷土(又名“高岭土”)——瓷土(H4Al2Si2O9)是陶瓷的主要原 料。它是以产于世界第一窑厂的中国景德镇附近的高岭而得名的。后来 由“高岭”的中国音演变为“Kaolin”,而成为国际性的名词。纯粹的 瓷土是一种白色或灰白色,有丝绢般光泽的软质矿物。
高纯氧化铝
钠灯管、荧光粉
低钠高温氧化铝 电子陶瓷、精细陶瓷
中钠高温氧化铝
结构陶瓷
低钠高温氧化铝 电子陶瓷、精细陶瓷、耐
超细微粉
火材料
中钠高温氧化铝 超细微粉
结构陶瓷、耐火材料
抛光研磨氧化铝
不锈钢抛光研磨
电工氧化铝
高压开关环氧树脂绝缘件 填料
普通拟薄水铝石
催化剂、粘结剂
特种拟薄水铝石
催化剂、粘结剂
4A沸石
1、石英——化学成分是纯粹的二氧化硅(SiO2),又名硅石。这种矿 物即使碎成细粉也无粘性,可用来弥补陶瓷原料过粘的缺点。在780℃ 以上时便不稳定而变成鳞石英,在1730℃时开始熔融。
2、长石——是以二氧化硅及氧化铝为主,又夹杂钠、钾、钙等的化合 物。因其所含分量多寡不同,又有许多种类。一般有将含长石较多的岩 石叫作长石的,也有以它的产地来命名的。现在把长石中具有代表性的 几种和它们的成分列于表1。其中前三种是纯粹的理论成分,后一类则 含有岩石中所有的不纯物质。
3、热等静压烧结:
近年来,为进一步提高SiC陶瓷的力学性能,研究人员进行了SiC陶瓷 的热等静压工艺的研究工作。研究人员以B和C为添加剂,采用热等静 压烧结工艺,在1900℃便获得高密度SiC烧结体。更进一步,通过该工 艺,在2000℃和138MPa压力下,成功实现无添加剂SiC陶瓷的致密烧 结。
研究表明:当SiC粉末的粒径小于0.6μm时,即使不引入任何添加 剂,通过热等静压烧结,在1950℃即可使其致密化。如选用比表面积
2、化合法:
在一定的温度下,使高纯的硅与碳黑直接发生反应。由此可合成高纯 度的β-SiC粉末。
3、热分解法:
使聚碳硅烷或三氯甲基硅等有机硅聚合物在1200~1500℃的温度范围 内发生分解反应,由此制得亚微米级的β-SiC粉末。
4、气相反相法:
使SiCl4和SiH4等含硅的气体以及CH4、C3H8、C7H8和(Cl4等含碳 的气体或使CH3SiCl3、(CH3)2 SiCl2和Si(CH3)4等同时含有硅和 碳的气体在高温下发生反应,由此制备纳米级的β-SiC超细粉。
以α-SiC为原料,同时添加B和C,也同样可实现SiC的致密烧结。
研究表明:单独使用B和C作添加剂,无助于SiC陶瓷充分致密。只有 同时添加B和C时,才能实现SiC陶瓷的高密度化。为了SiC的致密烧 结,SiC粉料的比表面积应在10m2/g以上,且氧含量尽可能低。B的 添加量在0.5%左右,C的添加量取决于SiC原料中氧含量高低,通常C 的添加量与SiC粉料中的氧含量成正比。
洗涤助剂
10X沸石
催化剂
铝酸钠溶液
氟化盐
固体铝酸钠
催化剂、凝聚剂
纯铝酸钙水泥
耐火材料结合剂
结构陶瓷
研磨介质
精细陶瓷
机械零件
陶瓷原料主要来自岩石,而岩石大体都是由硅和铝构成的。陶瓷也是用 这类岩石作原料,经过人工加热使之坚固,很类似火成岩的生成。因此 从化学上来说,陶瓷的成分与岩石的成分没有什么大的区别。如果是硅 和铝所构成的陶瓷,其主要原料有以下几种:
最近,有研究者在亚微米SiC粉料中加入Al2O3和Y2O3,在1850℃~ 2000℃温度下实现SiC的致密烧结。由于烧结温度低而具有明显细化的 微观结构,因而,其强度和韧性大大改善。
2、热压烧结
50年代中期,美国Norton公司就开始研究B、Ni、Cr、Fe、Al等金属 添加物对SiC热压烧结的影响。实验表明:Al和Fe是促进SiC热压致密 化的最有效的添加剂。
为24m2/g的SiC超细粉,采用热等静压烧结工艺,在1850℃便可获得 高致密度的无添加剂SiC陶瓷。
另外,Al2O3是热等静压烧结SiC陶瓷的有效添加剂。而C的添加对 SiC陶瓷的热等静压烧结致密化不起作用,过量的C甚至会抑制SiC陶瓷 的烧结。
4、反应烧结:
SiC的反应烧结法最早在美国研究成功。反应烧结的工艺过程为:先将 α-SiC粉和石墨粉按比例混匀,经干压、挤压或注浆等方法制成多孔坯 体。在高温下与液态Si接触,坯体中的C与渗入的Si反应,生成β- SiC,并与α-SiC相结合,过量的Si填充于气孔,从而得到无孔致密的 反应烧结体。反应烧结SiC通常含有8%的游离Si。因此,为保证渗Si的 完全,素坯应具有足够的孔隙度。一般通过调整最初混合料中α-SiC和 C的含量,α-SiC的粒度级配,C的形状和粒度以及成型压力等手段来 获得适当的素坯密度。
总之,SiC陶瓷的性能因烧结方法不同而不同。一般说来,
无压烧结SiC陶瓷的综合性能优于反应烧结的SiC陶瓷,但次于
热压烧结和热等静压烧结的SiC陶瓷。
氧化铝的用途
产品名称
主要品种
主要用途
普通氢氧化铝
联合法氢氧化铝
氟化盐、净水剂
拜尔法氢氧化铝
氟化盐、净水剂、活性氧 化铝
特种氢氧化铝
活性氧化铝 高纯氧化铝
现就SiC陶瓷的生产工艺简述如下:
一、SiC粉末的合成:
SiC在地球上几乎不存在,仅在陨石中有所发现,因此,工业上应用的
SiC粉末都为人工合成。目前,合成SiC粉末的主要方法有:
1、Acheson法:
这是工业上采用最多的合成方法,即用电将石英砂和焦炭的混合物加 热至2500℃左右高温反应制得。因石英砂和焦炭中通常含有Al和Fe等 杂质,在制成的SiC中都固溶有少量杂质。其中,杂质少的呈绿色,杂 质多的呈黑色。
有研究者以Al2O3为添加剂,通过热压烧结工艺,也实现了SiC的致密 化,并认为其机理是液相烧结。此外,还有研究者分别以B4C、B或B 与C,Al2O3和C、Al2O3和Y2O3、Be、B4C与C作添加剂,采用热压 烧结,也都获得了致密SiC陶瓷。
研究表明:烧结体的显微结构以及力学、热学等性能会因添加剂的种 类不同而异。如:当采用B或B的化合物为添加剂,热压SiC的晶粒尺寸 较小,但强度高。当选用Be作添加剂,热压SiC陶瓷具有较高的导热系 数。
瓷土是由云母和长石变质,其中的钠、钾、钙、铁等流失,加上水变化 而成的,这种作用叫作“瓷土化”或“高岭土化”。至于瓷土化究竟因 何而起,在学术界中虽然还没有定论,但大略可以认为是长石类由于温 泉或含有碳酸气的水以及沼地植物腐化时所生的气体起作用变质而成 的。一般瓷土多产于温泉附近或石灰层周围,可能就是这个原因。瓷土 的熔点约在1780℃左右,实际上因为多少含有不纯物质,所以它的熔点 略为降低。
陶瓷中最高级的是瓷器。作瓷器用的岩石究竟以哪样最好?由于瓷器必 须是白色。因而就不得不极力避免含有使陶瓷着色的铁分。含铁少而以 氧化硅及氧化铝为主要成分的岩石有:花岗岩、花岗斑岩、石英斑岩、 石英粗面岩以及由这类岩石分崩而成的水成岩等。
这里所说的花岗石乃至石英粗面岩(即在火成岩中也算是含有氧化硅及 氧化铝特别多而铁分子少的),都是以石英、长石为主,并含有若干云 母及富于铁分(氧化铁)的黑绿或黑褐色的矿物。假若仔细观察这些岩 石,便可看到许多像玻璃一般透明的颗粒和像瓷器一样鲜艳的白色或淡 红色的颗粒。前者是石英、后者是长石。这四种岩石的化学成分虽然相 同,但因为长石与石英等颗粒的大小不同,因而形成了不同的岩石。花 岗岩全体是由比较大的颗粒(直径1~7毫米)构成的。石英粗面岩是在
高温氧化铝
拟薄水铝石 沸石 铝酸钠
纯铝酸钙水泥 氧化铝陶瓷
白色氢氧化铝
阻燃剂、填料
超白氢氧化铝