行星齿轮减速器建模与运动学仿真_梁晓峰
行星齿轮传动的机构仿真及多体接触分析

O
0 0 2 0 0. 0 8 1 4 6 0
,s /
// _ 1
在
坐标 系 中 t 时刻 A 坐标 为 : 韵
() 1
Y = Fsn c i8
式中: n为中心距 ;c r 为行星轮半径 ; | t 8为 时刻行星轮相对行
星架 的转 角 , 卢=2 n 一 t 订( n )。 利用坐标变换公式 :
行 星轮 与 内齿 轮 节 点 处 啮合 位 置 , 时刻 A点 旋 转 至 A 点 。 t
程 万康 : 星齿轮 传 动 的机构 仿 真及 多体 接 触分析 行
轮 及 行 星架 的 受 力 情 况 。
架之问 的旋转 副施 加力 矩 59 9 3N・ l令 内齿 圈与行 星 6 . n, 架之间旋转副的转速 为 0 即行 星架 不输 出运 动 。利用 I , —
DA E S软件 进 行 力 学 仿 真 时 , 置 求 解 时 间 为 1s 求 解 步 数 设 , 为 300步 , 解 可 得 图 5 图 6及 表 3所 示 的 太 阳轮 、 星 0 求 、 行
个 行 星 轮 , 运 动 仿 真 过 程 中 , 动 副 的 定 义包 括 3个 旋 转 故 运 副 和 2个 齿 轮 副 。 即太 阳轮 与行 星 架 之 间 、 内齿 圈 与 行 星架 之 间 、 星 轮 与 行 星 架 之 间 用 旋 转 副 来 定 义 , 阳轮 与 行 星 行 太 轮 之 间 、 星轮 与 内 齿 圈 之 问 用 齿 轮 副 未 定 义 。 将 内齿 圈定 行 义 为 固定 件 , 太 阳 轮 与 行 星 架 之 问 的 旋 转 副 施 加 转 动 。 由 对 于 太 阳轮 额 定 输 入 转 速 为 4 0rmi( 6 83rs , 阳 轮 1 n 即 .3 / ) 太 /
KISSsys行星轮建模分析
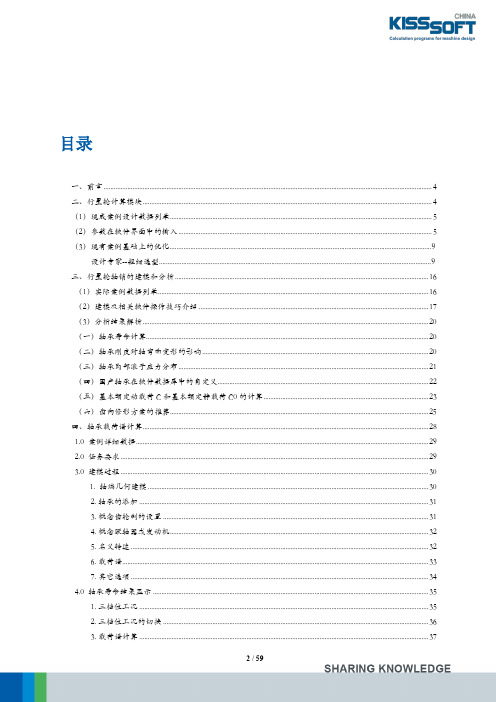
一、前言 ................................................................................................................................................................................................. 4 二、行星轮计算模块 .......................................................................................................................................................................... 4 (1)现成案例设计数据列举 .......................................................................................................................................................... 5 (2)参数在软件界面中的输入 ..................................................................................................................................................... 5 (3)现有案例基础上的优化.......................................................................................................................................................9 设计专家--粗细选型.............................................................................................................................................................9 三、行星轮轴销的建模和分析 ..................................................................................................................................................... 16 (1)实际案例数据列举 ............................................................................................................................................................... 16 (2)建模及相关软件操作技巧介绍 ....................................................................................................................................... 17 (3)分析结果解析 ........................................................................................................................................................................ 20 (一)轴承寿命计算...................................................................................................................................................................... 20 (二)轴承刚度对轴弯曲变形的影响 ...............................................................................................................................பைடு நூலகம்..... 20 (三)轴承内部滚子应力分布 ................................................................................................................................................... 21 (四)国产轴承在软件数据库中的自定义 ............................................................................................................................ 22 (五)基本额定动载荷 C 和基本额定静载荷 C0 的计算 ................................................................................................. 23 (六)齿向修形方案的推荐........................................................................................................................................................ 25 四、轴承载荷谱计算 ........................................................................................................................................................................ 28 1.0 案例详细数据 ............................................................................................................................................................................ 29 2.0 任务要求 ..................................................................................................................................................................................... 29 3.0 建模过程 ..................................................................................................................................................................................... 30 1. 轴端几何建模 ..................................................................................................................................................................... 30 2. 轴承的添加 .......................................................................................................................................................................... 31 3. 概念齿轮副的设置 ............................................................................................................................................................ 31 4. 概念联轴器或发动机 ........................................................................................................................................................ 32 5. 名义转速 ............................................................................................................................................................................... 32 6. 载荷谱 .................................................................................................................................................................................... 33 7. 其它选项 ............................................................................................................................................................................... 34 4.0 轴承寿命结果显示 .................................................................................................................................................................. 35 1. 三档位工况 .......................................................................................................................................................................... 35 2. 三档位工况的切换 ............................................................................................................................................................ 36 3. 载荷谱计算 .......................................................................................................................................................................... 37
机械工程学院大学生课外科技训练减速器建模装配设计与运动仿真
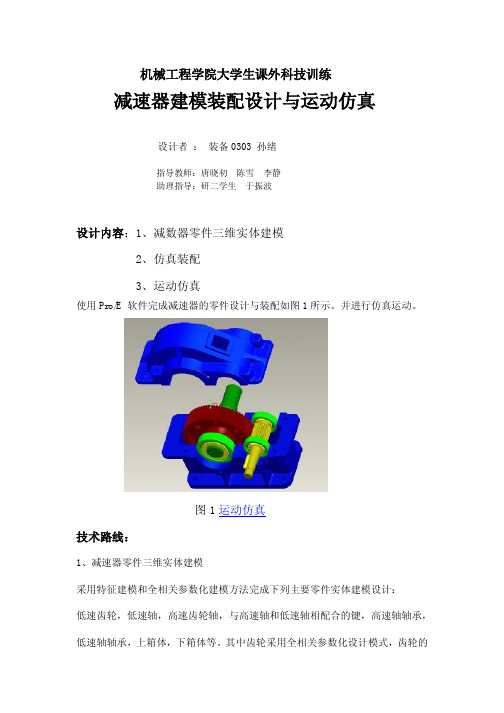
机械工程学院大学生课外科技训练减速器建模装配设计与运动仿真设计者:装备0303 孙绪指导教师:唐晓初陈雪李静助理指导:研二学生于振波设计内容:1、减数器零件三维实体建模2、仿真装配3、运动仿真使用Pro/E 软件完成减速器的零件设计与装配如图1所示。
并进行仿真运动。
图1运动仿真技术路线:1、减速器零件三维实体建模采用特征建模和全相关参数化建模方法完成下列主要零件实体建模设计:低速齿轮,低速轴,高速齿轮轴,与高速轴和低速轴相配合的键,高速轴轴承,低速轴轴承,上箱体,下箱体等。
其中齿轮采用全相关参数化设计模式,齿轮的参数为模数、齿数、压力角及齿轮厚度。
1.1 、参数化渐开线齿轮设计齿轮的三维建模在机器产品如减速器和齿轮泵的建模中具有广泛的用途。
实现齿轮参数化三维建模可以使齿轮的三维模型更加接近齿轮的真实三维模型,同时也可以提高产品的建模效率。
基于Pro/E的齿轮参数化三维建模的核心技术是根据齿轮齿廓渐开线的生成原理,利用齿廓渐开线方程计算出齿轮齿廓渐开线上点的直角坐标值,绘制出渐开线,按渐开线曲线拉伸成齿轮齿廓的实体。
齿轮齿廓渐开线生成原理基于Pro/E平台的齿轮参数化三维建模的关键是要绘制出二维的齿轮齿廓渐开线。
因此必须根据渐开线的生成原理,输入参数化绘制齿轮齿廓渐开线的方程。
图2显示了渐开线方程上任一点的参数关系。
有三个重要的基本角度,即:表示;展开角─基圆半径OA与OC之间的夹角,以фу渐开角─基圆中心O渐开线的直角坐标参数方程为:x﹦R b(cosφ+φ·sinφ)y= R b(sinφ-φ·cosφ) (1)式中: x,y―渐开线上任一点的直角坐标值R b—渐开线基圆半径φ—渐开线发生线在基圆上的滚动角度S b=π/z·R b+2 R b·invα (2)式中: S b—齿轮基圆的齿厚α—压力角根据渐开线参数方程(1),计算出渐开线上一系列点的直角坐标值, 完成齿轮参数化三维建模,该程序中主要的参数为模数m 和齿数z 、压力角ANGLE 和齿厚b ,输入以上参数后便可以自动生成直齿圆柱齿轮的三维模型。
行星齿轮减速器设计最终要点
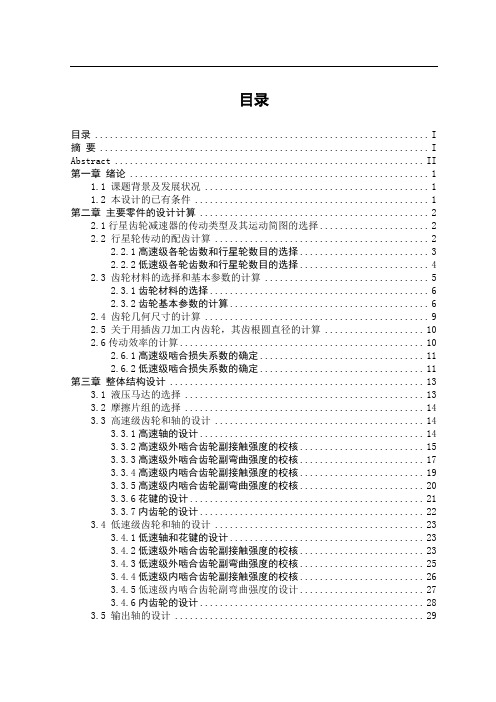
目录目录 (I)摘要 (I)Abstract (II)第一章绪论 (1)1.1 课题背景及发展状况 (1)1.2 本设计的已有条件 (1)第二章主要零件的设计计算 (2)2.1行星齿轮减速器的传动类型及其运动简图的选择 (2)2.2 行星轮传动的配齿计算 (2)2.2.1高速级各轮齿数和行星轮数目的选择 (3)2.2.2低速级各轮齿数和行星轮数目的选择 (4)2.3 齿轮材料的选择和基本参数的计算 (5)2.3.1齿轮材料的选择 (6)2.3.2齿轮基本参数的计算 (6)2.4 齿轮几何尺寸的计算 (9)2.5 关于用插齿刀加工内齿轮,其齿根圆直径的计算 (10)2.6传动效率的计算 (10)2.6.1高速级啮合损失系数的确定 (11)2.6.2低速级啮合损失系数的确定 (11)第三章整体结构设计 (13)3.1 液压马达的选择 (13)3.2 摩擦片组的选择 (14)3.3 高速级齿轮和轴的设计 (14)3.3.1高速轴的设计 (14)3.3.2高速级外啮合齿轮副接触强度的校核 (15)3.3.3高速级外啮合齿轮副弯曲强度的校核 (17)3.3.4高速级内啮合齿轮副接触强度的校核 (19)3.3.5高速级内啮合齿轮副弯曲强度的校核 (20)3.3.6花键的设计 (21)3.3.7内齿轮的设计 (22)3.4 低速级齿轮和轴的设计 (23)3.4.1低速轴和花键的设计 (23)3.4.2低速级外啮合齿轮副接触强度的校核 (23)3.4.3低速级外啮合齿轮副弯曲强度的校核 (25)3.4.4低速级内啮合齿轮副接触强度的校核 (26)3.4.5低速级内啮合齿轮副弯曲强度的设计 (27)3.4.6内齿轮的设计 (28)3.5 输出轴的设计 (29)3.6 行星齿轮的设计和基本构件上的作用力 (30)3.6.1行星齿轮设计 (30)3.6.2基本构件上的作用力 (31)3.7 其余零件的设计 (31)3.7.1转臂的设计 (32)3.7.2箱体及前后机盖的设计 (33)3.7.3标准件及附件的选用 (36)3.7.4密封和润滑 (37)3.8 运动仿真 (37)结论 (39)参考文献 (40)摘要减速机是工作机和原动机之间的独立的封闭式的机械传动装置,它能够降低原动机的转速或增大原动机的扭矩,是一种被广发应用在工矿企业、运输、建筑等部门中的机械装置。
考虑误差的行星齿轮啮合力仿真

广等优点,被广泛运用于车辆、工程机械传动等系统中。这 些都是由于在其结构上采用了多个行星轮的传动方式,充分 利用了同心轴齿轮之问的空间,实现了功率分流,但是行星 齿轮减速器在制造和装配中不可避免的存在误差,这就带来 了行星齿轮传动均载性的问题,从而使齿轮之间的作用力与 理想情况相差甚远,传统的计算行星齿轮啮合力的方法由于 没有考虑制造、装配误差以及各构件的弹性,使分析结果与 实际情况有很大出入。本文考虑了制造、装配误差,并采用 刚柔耦合的方法建立系统模型,分析了啮合力,有一定的可 信度。
:i巨一 {'…一u-u:…{
}
围4理想情况下行星轮l的啮合力
图5理想情况下行星轮2的啮合力
万方数据
圈6理想情况下行星轮3的啮合力
考虑误差情况下的啮合力曲线如下图7—9所示。
眦0 姗O 帅心 姗D
。 0(
田7考虑误差情况下行星轮1的啮合力
蕊一 划
图8考虑误差情况下行星轮2的啮合力
从两组曲线及表2中可以看出,理想情况下啮合力的波 动较小;而考虑误差时,由于存在均载的问题,啮合力波动很 大,计算结果与理论相符。 5计算啮合力的概率密度
万方数据
em4=Eb,+Ebp
esn4=Eh+瓯
(9) (10)
式中,e。~行星架弹性变形量沿内啮合线方向的投影,
e。~行星架弹性变形量沿外啮合线方向的投影,瓯一太阳 轮基节误差,氏~行星轮n基节误差,‰一内齿圈基节误
差。
将上述各项当量啮合误差叠加,得到两条啮合线上的累
积啮合误差:
em=eml+e吨+e帕+e,,14
Kl:5.5击^『/mm吾 墨:6.8 e5N/mm了3 碰撞力指数项e取为2.2,阻尼系数c取为50,碰撞有效 深度取默认值:0.1mm。
基于SolidWorks的行星齿轮机构运动仿真模型
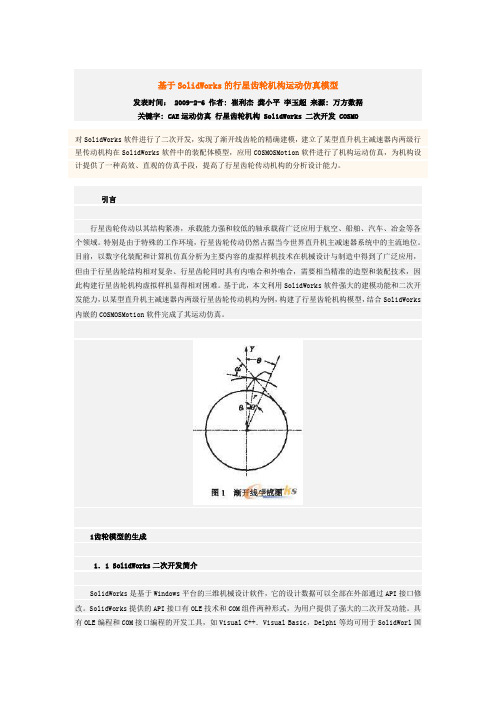
基于SolidWorks的行星齿轮机构运动仿真模型发表时间: 2009-2-6 作者: 崔利杰龚小平李玉超来源: 万方数据关键字: CAE运动仿真行星齿轮机构 SolidWorks 二次开发 COSMO对SolidWorks软件进行了二次开发,实现了渐开线齿轮的精确建模,建立了某型直升机主减速器内两级行星传动机构在SolidWorks软件中的装配体模型,应用COSMOSMotion软件进行了机构运动仿真,为机构设计提供了一种高效、直观的仿真手段,提高了行星齿轮传动机构的分析设计能力。
引言行星齿轮传动以其结构紧凑,承载能力强和较低的轴承载荷广泛应用于航空、船舶、汽车、冶金等各个领域。
特别是由于特殊的工作环境,行星齿轮传动仍然占据当今世界直升机主减速器系统中的主流地位。
目前,以数字化装配和计算机仿真分析为主要内容的虚拟样机技术在机械设计与制造中得到了广泛应用,但由于行星齿轮结构相对复杂、行星齿轮同时具有内啮合和外啮合,需要相当精准的造型和装配技术,因此构建行星齿轮机构虚拟样机显得相对困难。
基于此,本文利用SolidWorks软件强大的建模功能和二次开发能力,以某型直升机主减速器内两级行星齿轮传动机构为例,构建了行星齿轮机构模型,结合SolidWorks 内嵌的COSMOSMotion软件完成了其运动仿真。
1齿轮模型的生成1.1 SolidWorks二次开发简介SolidWorks是基于Windows平台的三维机械设计软件,它的设计数据可以全部在外部通过API接口修改。
SolidWorks提供的API接口有OLE技术和COM组件两种形式,为用户提供了强大的二次开发功能。
具有OLE编程和COM接口编程的开发工具,如Visual C++.Visual Basic,Delphi等均可用于SolidWorl国的二次开发,创建出用户定制的、专用的SolidWorks功能模块。
除此之外,SolidWorks还提供了内置的宏命令编程,使得SolidWorks的定制更加容易。
减速器的动态建模

减速器的动态建模03010,2014年第二阶段12K-V减速器的动力学建模1.1模型分析2K-V减速器的动力学模型因曲轴型号和数量的不同而不同。
然而,当曲轴对称分布时,动力学模型具有一定的规律性。
本文以2K-V320S三曲轴减速器为例,采用集总参数法建立了整机的系统动力学模型。
根据减速器的结构特点,整机的系统动力学模型基于以下假设:曲轴曲柄段的滚针轴承和两端的支承轴承在模型中用拉伸弹簧和压缩弹簧表示,它们的刚度为固定值。
忽略齿轮啮合中综合刚度的变化,将齿轮啮合刚度设为常数。
计算摆线针轮啮合刚度时,将啮合力视为集中力,大小方向与相同。
动态模型如图2所示。
参考坐标系O-xyz建立在行星架上,以行星架轴线中点为坐标原点,Z为轴向,X点方向从原点到第一曲轴轴孔几何xx,坐标系绕其轴线以角速度V旋转,在O-xyz坐标系中,其他部件的坐标系为:(1)输入齿轮轴(太阳齿轮)坐标系(xt、yt、t),xt、yt为与X、Y方向相同的径向坐标,t表示输出齿轮轴绕其轴线的转角。
(2)行星轮坐标系(xxi,yxi,xi),其中i=1,2,3代表行星轮数。
Xxi、yxi为径向坐标,xxi方向的太阳轮几何xx指向行星齿轮I的几何xx,xi代表行星齿轮I绕其轴线的转角。
(3)曲轴坐标系(xqi,yqi,qi),其中i=1,2,3代表曲轴数。
Xqi和yqi为径向坐标,坐标方向与匹配的行星齿轮相同,qi代表曲轴I绕其轴线的转角。
(4)摆线坐标系(xbi,ybi,bi),其中i=1,2,3表示摆线数。
Xbi和ybi为径向坐标,方向与x和y相同,bi 表示摆线轮I绕其轴线的转角。
(5)行星架的坐标系(xH、yH、H)、xH、yH分别与X、Y方向相同,H代表行星架绕其轴线的旋转角度。
这样,系统有10个30自由度的运动部件。
1.2各运动部件的动力学方程由于弹性变形,接触部件之间存在反作用力,该力的大小与相对位移成正比。
因此,有必要确定相互作用的移动构件之间的相对位移。
基于UG建模的辛普森行星齿轮在ADAMS中运动仿真的实现

基于UG建模的辛普森行星齿轮在ADAMS中运动仿真的实现摘要利用UG参数化建模功能,建立了辛普森行星齿轮机构的三维模型,并成功将其装配体导入到专业运动仿真软件Adams中。
根据其真实的工作状态,通过添加约束、驱动,实现了对辛普森行星齿轮机构在各档位运动状态的仿真。
在后处理模块中,可以清晰的判定各个构件在不同档位时的转动方向及速度大小,更加直观的加深了对汽车自动变速器换挡机理的认识与了解。
关键词 UG建模辛普森行星机构 ADAMS仿真The Motion Simulation of Simpson Planetary Gear based on UG in ADAMS Abstract Take advantage of the parametric modeling in UG, the simpson planetary gear modeling have been made, then been imported successfully into the ADAMS. In the ADAMS, it was exerted constraint and driver according to the actual working status, and have achieved the motion simulation of the simpson planetary gear working in the different gears. In the post-processing module, it could be clearly determined what direction of rotation is and how much the angular velocity is when the various components working in different gears. It contributed to have a deeper and intuitive understanding about the gear shift principle of the automatic gearbox.Key words UG modeling Simpson planetary gear ADAMS motion simulation引言自动变速器在汽车中是仅次于发动机的关键部件,是机—电—液一体化的典型产品。
- 1、下载文档前请自行甄别文档内容的完整性,平台不提供额外的编辑、内容补充、找答案等附加服务。
- 2、"仅部分预览"的文档,不可在线预览部分如存在完整性等问题,可反馈申请退款(可完整预览的文档不适用该条件!)。
- 3、如文档侵犯您的权益,请联系客服反馈,我们会尽快为您处理(人工客服工作时间:9:00-18:30)。
机械 2008年第 5期 总第 35卷 计算机应用技术 ·45·
——————————————— 收稿日期:2008-01-08 作者简介:梁晓峰(1981-),男,工学硕士,助理工程师,主要研究方向为机械结构动态分析、结构可靠性。
行星齿轮减速器建模与运动学仿真 梁晓峰1,陈艳锋2 (1.海军驻航天七院军事代表工作组,四川 成都 610100;2.海军工程大学 船舶与动力学院,湖北 武汉 430033) 摘要:应用虚拟样机技术可以大幅缩短新产品开发周期和降低开发成本,获得高性能、最优化的产品。在I-DEAS软件中,对某行星齿轮减速器进行参数化三维实体造型,研究了人字齿轮实体建模及装配的关键点,并利用I-DEAS与ADAMS之间的接口技术,在ADAMS中建立了行星齿轮减速器虚拟样机,对其进行了运动学仿真分析,结果表明,所建立的三维模型及虚拟样机与实际相符。最后,指出了值得进一步研究的方向。 关键词:行星齿轮;三维实体造型;虚拟样机;运动学仿真 中图分类号:TH122 文献标识码:A 文章编号:1006-0316(2008)05-0045-04
Model and motion simulation of planetary gear drive LIANG Xiao-feng1,CHEN Yan-feng2 (1.Naval representative workgroup in The seventh academe of the Spaceflight technological company,Chengdu 610100,China;2.College of Naval Architecture & Power,Naval Univ. of Engineering,Wuhan 430033,China) Abstract:The application of virtual prototype technology can greatly shorten circle of new product development, decrease cost as well as get the most optimized capability of product. Introduce the methods of 3D solid modeling of planetary gear in I-DEAS. Study the key point of modeling herringbone gear. According to the I/O technique of I-DEAS and ADAMS, establish the virtual prototype of planetary gear in ADAMS. The motion analysis result proved that the model and virtual prototype is precision. Point out the further work in the end. Key words:planetary gear;3D solid modeling;virtual prototype;motion simulation
行星齿轮减速器以其传动效率高、体积小、重量轻、结构紧凑、传递功率大、负载能力高、传动比范围大等优点,广泛应用于需要大减速比但使用空间较小的场合,如作为飞机、舰艇、汽车等的标准减速装置 [1~4]。其缺点是结构复杂,制造精度要
求高,设计中要求考虑的问题错综复杂,计算工作量大。若在计算设计阶段,应用计算机辅助技术,则能大大加快设计过程、提高设计质量,使这种传动装置得到更广泛的应用。 本文将计算机辅助设计(CAD)技术及运动学仿真应用于行星齿轮减速器的设计之中,在I-DEAS中建立了行星齿轮减速器的三维实体模型,在ADAMS(Automatic Dynamic Analysis of Mechanical Systems)中建立了减速器的虚拟样机(Virtual Prototype),并进行了运动学仿真分析。通过仿真研
究结果与理论计算结果的对比分析,证明了模型的合理性,此种研究方法对其它同类产品的设计研究具有重要的参考价值。
1 减速器三维实体造型 随着CAD技术的广泛应用,针对齿轮实体造型技术的研究日益广泛[5~7],文献[8,9]对行星齿轮减
速器CAD技术的应用进行了研究,然而,对具有人字齿结构的复杂行星齿轮减速器造型技术的研究较少。人字齿轮结构相当于两个斜齿轮的组合,与直齿轮副相比,斜齿轮副的总接触面积增大,可以承受更大的载荷。另外,在制造过程中,采用高精密加工技术,可以将齿轮间侧隙控制在较小范围内,可以使齿轮在啮合时几乎沿着啮合线作纯滚动,从而降低振动噪声。斜齿轮副在啮合过程中必然产生沿轴线方向的轴向力,而采用人字齿轮结构,可以·46· 计算机应用技术 机械 2008年第 5期 总第 35卷 抵消轴向力的作用。因此,本行星齿轮减速器三维实体造型的难点在于人字齿轮的实体造型。
1.1 齿轮实体造型 本文所研究的减速器中各齿轮的基本参数如表1所示。 表1 各齿轮基本参数 参数 太阳轮 行星轮 内齿圈 模数/(mm) 3 齿数 27 63 153 螺旋角/(°) 17
人字齿轮可以分解为对称的两个斜齿轮,斜齿轮齿面是一渐开线螺旋面,每个齿的齿厚相同,并有严格要求,因此在对斜齿轮建立三维实体模型时,关键是利用数学公式来表达斜齿轮的特征,从而确定螺旋线、渐开线、齿根过度曲线和齿厚,最后利用软件中相关命令得到三维实体造型。 斜齿轮端面齿形为渐开线,首先根据渐开线方程及画法[10]绘制其端面齿形,在制图过程中要注意
公式中各变量单位的一一对应。斜齿轮轮齿的实体造型是应用齿面曲线沿螺旋线进行扫略(Sweep)后得到的。在I-DEAS中,通过控制螺距和圈数绘制螺旋线,将绘制的齿轮端面曲线沿螺旋线扫略,得到单个齿的实体造型,最后使用阵列命令得到完整的斜齿轮实体造型(图1)。内齿的绘制用相啮合的外齿轮与圆柱体进行布尔运算(cut)得到。
1.2 装配研究 行星齿轮减速器主要由行星轮系组成,齿轮是其主要零件,而齿轮副则是其主要约束。齿轮的装配无法简单的应用I-DEAS中的定位命令来实现。因此,要使齿轮准确啮合,就需要做很多的技术处理,例如要做大量的辅助平面和辅助线及辅助点等。行星齿轮系统涉及到行星轮同时和太阳轮、内齿圈啮合的问题,对单对齿轮啮合的装配问题已有一些研究,然而对于行星齿轮的装配方法的研究较少。 通过实践研究,得出了行星齿轮精确装配的方法,具体为: (1)选中齿轮渐开线分度圆上一点,通过它建立参考切平面,接着在与之相啮合的另一轮的相应轮齿分度圆上用同样方法创建参考切平面,然后使这2个参考平面重合。由于所建模型中相啮合的齿轮
副尺宽相同,所以首先要对齐齿轮端面,再沿着啮合面方向移动齿轮,直到两齿轮中心矩满足要求为止。至此,就实现了两个齿轮的精确啮合(图2所示)。 (2)按照中心距大小,将内齿圈放置到安装位置,通过旋转命令,使其与行星轮啮合,同时保证与太阳轮同心。 (3)依次将其它行星轮进行装配。此过程是个反复调整的过程,因此,要保证各个参数的准确控制,从而减少重复劳动。
图1 行星轮实体造型 图2啮合齿轮 虚拟装配的干涉检验技术主要包括零部件组选择、干涉和间隙体积计算、干涉零件创成、干涉检验报告生成等。干涉检验是装配完成的最后一步,通过检验可以验证装配的准确性,还可以检验零件设计图的缺陷,尽可能的把设计错误消除在制造前,减少重复工作和损失。 实现齿轮之间的精确啮合后,根据行星齿轮减速器的装配约束条件加入其它所需零部件,如轴、行星架、轴承、高速连轴器、盘车棘轮等,完成整个行星齿轮减速器的虚拟装配(图3所示)。
图3 行星齿轮装配图 2 减速器运动学仿真 2.1设置材料属性 减速器的运动分析是利用ADAMS软件来完成的,由于I-DEAS与ADAMS之间的文件传递存在质量特性丢失的现象,所以在ADAMS中首先要对减速器各零部件进行材料属性设置,然后软件会自动计算出各零部件的质量、转动惯量和质心的位置,为接下来的运动仿真分析提供必要的数据。 机械 2008年第 5期 总第 35卷 计算机应用技术 ·47·
2.2 添加约束 一个完整的运动学/动力学分析模型应包含以下基本要素:构件、约束、驱动和载荷。本系统定义如下约束:行星轮与行星轴之间定义旋转副,行星轴与行星架之间添加固定副;行星轮与太阳轮,行星轮与内齿圈之间组成行星机构,它们之间用齿轮副连接。在ADAMS中定义的齿轮副,关联两个运动副和一个方向坐标系,这两个运动副必须与一共同件关联,而且方向坐标系必须固定在共同件上。在本文所研究的减速器模型中,共同件只能是行星支架,基于此,还需要在太阳轮与支架之间、内齿圈与支架之间添加旋转副。
2.3 仿真分析 为了研究减速器的运动学特性,施加了转速驱动。根据实际情况,本文使用函数step使转速在2s内由0平缓地增加到10000 r/min(1047.2 rad/s),即step(time,0,0,2,1046.7)(time表示时间是自变
量),如图4。step(1100,,,,qxqxx
)按式(4)计算
[11]。
step=()⎪⎩
⎪⎨
⎧
≥<<∆−∆×+≤
11102000
,,23
,
xxqxxxaqxxq
(4)
其中:01qqa−=,)/()(010xxxx−−=∆。
图4 输入转速图 2.3.1 转速特征 对上述模型进行运动学仿真分析,仿真时间取2.5s,仿真步数设为8000,进行转速特征仿真,结果见图5,其中曲线由上往下依次为太阳轮、输出轴、行星轮的绝对角速度。由仿真结果可知,输出转速最终稳定在157.08 rad/s,从而得出仿真模型的传动比为i=6.667;行星轮自转速度为-224.4 rad/s,负号表示其转速方向与输入转速相反。仿真结果与理论计算结果完全一致,转速特征满足设计要求,
从而证明了上述建模过程的准确性。 2.3.2 加速特性 依据减速器实际加速过程,按图4所示输入电机启动特性进行加速特性仿真,得到减速器各部件的加速特性曲线(见图6)。仿真曲线由上往下依次为太阳轮、输出轴、行星轮的启动加速度。由仿真曲线可以看出,此减速器的加速过程比较平稳,完全符合设计要求。
图5 各部件速度变化图 图6 各部件加速度变化图 通过以上转速特性仿真和加速特性仿真研究,验证了减速器设计的合理性,与理论值完全相符,也反映了运动仿真分析结果是可信的,可以用于减速器的性能评价与优化设计的依据。