第一章外排屑深孔加工技术
深孔加工简介

2.喷吸钻
喷吸钻是一种新型的内排屑深孔钻,主要用于加工直径18~ 180mm、深径比在100以内的深孔。加工精度为IT10~IT7,表面 粗糙度Ra3.2~0.8μm,孔的直线度可达0.1mm/1000mm。
(1)喷吸钻的结构
喷吸钻的组成结构
喷吸钻钻头结构
(2)喷吸钻的工作原理 喷吸钻利用液体的喷吸效应实现冷却排屑。即当高压
➢有利于分屑和排屑,可使径向分力得到较合理的平 衡,减少导向支承块上的支承力。
➢刀齿也可根据受力情况和切削条件不同,选用不同 的刀具材料。
错齿内排屑深孔钻的工作原理
一、深孔加工的特点
➢深孔加工时,刀杆细长,刚性差。 ➢切削液难以引入到切削区,切屑不易排出,钻尖冷却困难。 ➢切削刃上各点的切削速度变化较大,尤其是近中心处的切 削速度为零,切削条件差。 ➢转矩和轴向力大,钻进困难,且易引偏,致使刀具耐用度 及生产率很低。
二、深孔钻
(1)按切削刃的多少分 ➢单刃 ➢多刃
流体经过一个狭小的通道高速喷射时,在这股喷射流的周 围形成了低压区,将喷嘴附近的流体吸走。
3.错齿内排屑深孔钻(高压内排屑钻)
错齿内排屑钻由钻头和钻杆两部分组成。 用途:加工直径60mm以上、深径比在100以内的深孔。 加工精度为IT9 ~IT7,表面粗糙度为Ra6.3~1.6μm。
ห้องสมุดไป่ตู้
结构特点:切削刃成交错排列,刀具上无横刃。 优点:
(2)按深孔钻的排屑方式分 ➢内排屑 ➢外排屑
常用的深孔钻有枪孔钻、喷吸钻和高压内排屑钻。
1.枪孔钻
概念:枪孔钻是单刃外排屑深孔钻,因最早用于加工枪 管而得名。
特点:仅在轴线的一侧有切削刃,没有横刃,并分为外 刃和内刃两段,使切出的切屑短小,便于排屑。
机械加工深孔加工技术

机械加工深孔加工技术汇报人:2024-01-02•深孔加工技术概述•深孔加工的工艺流程•深孔加工的刀具与设备目录•深孔加工的质量控制•深孔加工的难点与解决方案•深孔加工的应用实例01深孔加工技术概述深孔加工技术是指对深度大于孔径的孔进行加工的技术。
定义深孔加工具有加工难度大、技术要求高、需要特殊的加工设备和工艺方法等特点。
特点定义与特点深孔加工在许多领域中都有广泛应用,如航空航天、能源、化工等,是满足产品性能要求的重要手段。
满足产品性能要求采用深孔加工技术可以大大提高生产效率,减少加工时间和成本。
提高生产效率深孔加工技术的精度和表面质量要求高,能够保证产品的质量和可靠性。
保证产品质量深孔加工的重要性深孔加工技术起源于20世纪初,随着工业的发展和技术的不断进步,深孔加工技术也在不断改进和完善。
现代深孔加工技术正朝着高精度、高效率、自动化和智能化的方向发展,未来将会有更多的新材料、新工艺和新设备出现。
深孔加工技术的历史与发展发展趋势历史回顾02深孔加工的工艺流程1 2 3钻孔是深孔加工的起始阶段,主要使用钻头在工件上打孔。
钻孔时需要控制切削速度和进给量,以获得良好的切削效果和孔径精度。
钻孔过程中需要使用冷却液来降低切削温度和润滑钻头。
扩孔是对已钻孔进行扩大直径的加工,以修正孔径偏差或得到所需直径。
扩孔可以使用多种刀具,如扩孔钻、锪钻和车刀等,根据需要选择合适的刀具。
扩孔过程中需要控制切削速度和进给量,以确保孔径精度和表面质量。
01铰孔是对已钻孔进行精加工,以提高孔径精度和表面质量。
02铰孔使用的刀具有多种,如机铰刀、手铰刀和锥铰刀等,根据需要选择合适的刀具。
03铰孔过程中需要控制切削速度和进给量,以确保孔径精度和表面质量。
镗孔可以使用多种刀具,如镗杆、车刀和铣刀等,根据需要选择合适的刀具。
镗孔过程中需要控制切削速度和进给量,以确保孔的形状精度和表面质量。
镗孔是对已钻孔进行进一步加工,以修正孔的轴线偏差和提高孔的形状精度。
深通孔加工方法
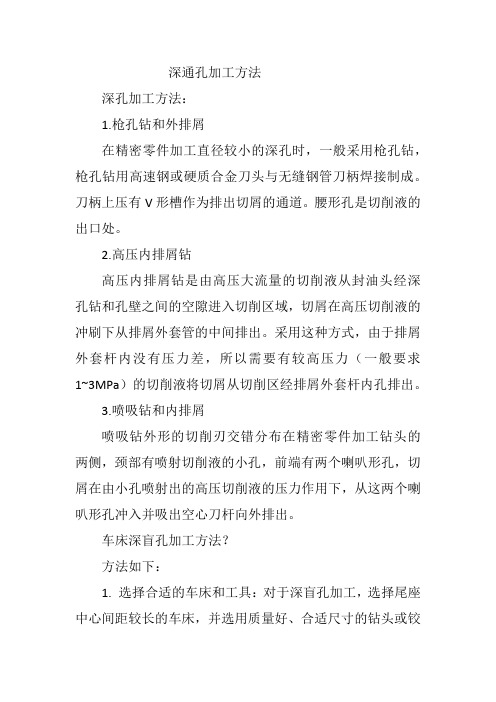
深通孔加工方法深孔加工方法:1.枪孔钻和外排屑在精密零件加工直径较小的深孔时,一般采用枪孔钻,枪孔钻用高速钢或硬质合金刀头与无缝钢管刀柄焊接制成。
刀柄上压有V形槽作为排出切屑的通道。
腰形孔是切削液的出口处。
2.高压内排屑钻高压内排屑钻是由高压大流量的切削液从封油头经深孔钻和孔壁之间的空隙进入切削区域,切屑在高压切削液的冲刷下从排屑外套管的中间排出。
采用这种方式,由于排屑外套杆内没有压力差,所以需要有较高压力(一般要求1~3MPa)的切削液将切屑从切削区经排屑外套杆内孔排出。
3.喷吸钻和内排屑喷吸钻外形的切削刃交错分布在精密零件加工钻头的两侧,颈部有喷射切削液的小孔,前端有两个喇叭形孔,切屑在由小孔喷射出的高压切削液的压力作用下,从这两个喇叭形孔冲入并吸出空心刀杆向外排出。
车床深盲孔加工方法?方法如下:1. 选择合适的车床和工具:对于深盲孔加工,选择尾座中心间距较长的车床,并选用质量好、合适尺寸的钻头或铰2. 制定加工方案:根据工件的形状和尺寸、材料以及待加工孔的位置和深度制定加工方案。
3. 用钻头或铰刀钻孔:在车床上,用钻头或铰刀逐步钻孔,每钻到一定深度,要及时切断切屑,保持孔内干净,避免堵塞。
4. 用扩孔器扩大孔径:钻完深孔后,用扩孔器逐步扩大孔径,使其达到要求。
5. 修整孔面:对于要求较高的工件,需使用磨头修整孔面,使其光洁度和精度达到要求。
6. 清洁孔内:在加工完成后,要用空气枪或其他工具将孔内的切屑、污物彻底清洁干净。
7. 检查孔的质量:最后,检查孔的尺寸、形状、表面质量和内部质量等,确保达到要求。
如盲孔底钻头角度存在可以的话,先用13.8的钻头打孔深50毫米(钻头尖除外),再有Φ14H7铰刀(上偏差为+0.015 下偏差为+0.007 单位均为mm,铰刀前面导向刃磨去)铰孔至尺寸。
如果盲孔是平底的话13.8钻头钻好孔后,再磨平底钻底面到50毫米深,用Φ14H7铰刀铰至尺寸,步骤如下:1.先在车床上将工件夹紧,确定好孔的位置和深度。
深孔加工及刀具设计与应用

四、内排屑深孔钻
(十一)切削参数的选用 (十二)压力和流量 (十三)深孔加工常出的问题、原因和改进措施 (十四)操作者操作中注意事项 (十五)套料钻
(一)内排屑深孔钻总体结构分析介绍
1.总体结构分析 (1)小直径焊接式刀片(见图 8):一般在 φ 12~φ 30~φ 65, 优点: a.适用小孔径φ 30以下 b.制造精度高,刀头外径控制 在h7 c.制造简单 缺点: a.刀片直径不能调整 SANDVIK从φ 12.6~φ 65
钻套与机床主轴及工件的中心应对中,并应有严格 要求其跳动量不应大于0.02mm,如下图:
新的导套孔最好控制在比钻头大于0.005最佳,如果 旧导套孔大于钻头0.02时,则应更换导套孔,这样才能 获得最佳的加工效果。
(十)机床和刀具旋转的选用
最佳选择是钻头和工件为相反进行旋转,如以下各图:
a.最佳的直线度是有相 对旋转得到的,如钻 头和工件以相反的方 向进行旋转。
(六)材质的选用
a.一般钢材常选用:国际标准P类:P10-P20即YT15、 YT14等 b.不锈钢常选M类M15,即YW2A和K类YG813
C.钛合金常选K类
d.可转位刀片一般按样本YG8推荐材料选用
(七)内排屑深孔钻与钻杆外径及内孔之间的关系
深孔钻杆承受较大的切削力和压力,应选用强度较 好的含合金钢或结构钢,热处理后硬度为38~45HRC或 48~52HRC以提高强度与抗振性。在设计条件允许时应尽 量加大钻杆外径尺寸和减小内径尺寸,这时可提高钻尖 的强度与耐磨性,以适应高速、大进给钻削。 如钻头直径为D时,钻杆外径Ds=(0.9~0.95)D, 钻杆内径ds=(0.6~0.7)D; Ds/ds=1.4~1.9
(四)导条的形状
基于机械加工的深孔加工技术探析

基于机械加工的深孔加工技术探析发表时间:2019-09-06T09:49:12.727Z 来源:《防护工程》2019年12期作者:隋少玲[导读] 并对其中的关键工艺和过程进行分析,指出深孔加工技术中应当注意的技术要点。
费斯托气动有限公司山东省济南市 250100摘要:在机械加工中超 30%的部分需要进行孔加工,其中深孔加工占据孔加工比例的 40%,因此深孔加工是机械加工的重要形式之一。
深孔加工工艺特殊,无法直接观察到孔内部的情况,因此必须合理选择和设计孔加工的技术和工艺。
文章对深孔加工技术相关内容进行简述,并对其中的关键工艺和过程进行分析,指出深孔加工技术中应当注意的技术要点。
关键词:机械加工;深孔;加工技术1深孔加工技术的技术特点1.1深孔加工技术难度大首先,绝大部分的深孔加工在半封闭或者是全封闭的环境下实施,因此,加工切削以及走刀等问题工作人员无法直接的进行观察;其次,通常来说,深孔的半径与孔深两者之间的比值比较大,正因如此,容易出现金属屑难以排出堵塞孔洞的情况;最后,过长的钻头所导致的问题是会大幅度的降低钻头的刚性,以至于出现偏孔或者是抖动等方面的问题,也就难以有效的保障深孔加工的精度;此外,孔洞加工散热问题的影响,封闭环境下孔洞内温度上升会导致钻头的磨损。
1.2运动方式本身具有特殊性在深孔整个加工过程之中,工件以及刀具两者之间可以采用多种相互运行的方式,其中,就包括工件转动同时刀具进给;工件固定同时刀具进给以及二者以相反方向运行进给等,如何选择不同的运动方式是深孔加工技术使用的重点问题之一。
1.3深孔加工排屑问题深孔加工中排屑问题也是应当重点关注的问题之一,排屑方式主要分为两种,第一种是外排屑,在孔心钻杆处倒入冷却液,将切屑从切削区清理出;第二种是内排屑,在孔和钻杆外壁处倒入冷却液,将切屑从切削区域带出。
在实际加工过程中一般优先考虑内排屑加工方式,因为该方式不会造成孔壁二次摩擦,钻杆刚性较高更不会影响孔洞的表面质量。
浅谈深孔加工技术

技术与应用A PPLICATION157OCCUPATION2014 11摘 要:本文探讨了深孔加工的特点、关键技术、加工类型、刀具及结构等问题。
关键词:深孔加工 加工特点 关键技术 加工方法浅谈深孔加工技术文/杨营营所谓深孔,是指孔深与孔径之比大于5的孔。
深孔又分为一般深孔(L /d >5~20)、中等深孔(L /d >20~30)、超深孔(L /d >30~100)三类。
不同类型的深孔,其加工方法也不相同。
一、深孔加工的特点和关键技术1.深孔件加工的特点一是深孔加工时,孔轴线容易歪斜,钻削中钻头容易引偏。
二是刀杆受内孔限制,一般细而长,刚性差,强度低,车削时容易产生振动和“让刀”现象,使零件易产生波纹、锥度等缺陷。
三是钻孔或扩孔时切屑不易排出,冷却润滑液输入困难。
四是加工时难以观察孔的加工情况,加工质量不易控制。
2.深孔加工的关键技术深孔加工的关键技术是深孔刀具几何形状的确定和切削时的冷却、排屑问题。
在加工中可采用以下措施来保证加工质量:一是粗精加工分阶段进行,二是合理选择加工刀具,三是采用导向和辅助支承,四是配置冷却液输入装置。
二、深孔加工类型一是按其所用刀具分类,可分为实心钻孔法、镗孔法、套料钻孔法。
二是按运动形式分类,可分为工件旋转,刀具做进给运动;工件不动,刀具旋转又做进给运动;工件旋转,刀具也做反向旋转又做进给运动;工件做旋转运动与进给运动,刀具不动,这种形式采用不多。
三是按排屑方法分类,可分为外排屑、内排屑。
三、深孔加工刀具及其结构1.扁钻该刀具结构简单,容易制造,在钻削加工时冷却液由钻杆内部注入孔中,切屑从零件孔内排出,适用于精度和表面粗糙度要求不高的较短深孔。
图1 简易扁钻1-钻头 2-钻杆 3、4-紧固螺钉2.单刃外排屑小深孔钻该深孔钻由切削部分和钻杆焊接而成,切削部分用W 18Cr 4V 制造或硬质合金刀头镶制;钻杆为35#~45#钢无缝钢管,上压120°V 形槽用以排屑,中空可通过切削液,从自切削部分腰圆孔处进入切屑区域。
机械加工中深孔加工技术的研究

机械加工中深孔加工技术的研究摘要:在机械工程行业壮大发展的背景下,机械化工艺水平,深加工技术在现实生产活动中得到了广泛应用,该项技术虽然能创造出较好的效益,但是客观上讲技术应用中还滞留着一些问题。
本文简单分析了深孔加工技术应用的重点与难点,包括技术操作难度较高、钻孔操作有应局限性、碎屑外排环节有问题等,简单分析以上状况的成因,以促进深加工技术有效应用为目标,总结技术要点及应用策略,希望能给同行实践过程带来些许帮助。
关键词:机械化加工;深加工;难点分析;技术应用引言机械加工制造是我国的传统行业之一,其直接关系着国民经济的整体发展水平。
机械化加工生产中可供选择的技术方法有很多,深加工就是其一,其在促进我国机械加工水平全面提升方面表现出良好效能。
深孔通常是孔长度和直径比大于5~10的孔。
通常而言,在机械化加工生产中,深孔的实际加工数量在总量内占比约50%。
综合以上数据,能够认识到做好深孔加工工作的必要性。
为了能全面提升深孔加工效率与质量,应积极研发适宜且高效化的深孔加工技术,并结合实际情况持续完善技术应用过程,彰显新技术的优势,促进我国机械行业获得更大的发展进步。
1深孔加工技术的重点和难点1.1技术应用难度较高主要体现在如下几个方面[1]:一是基本上是孔径小,孔深大的条件下进行生产,受限于设备或刀具因素的制约,加工时出口位置容易产生偏差。
二是由于孔深大,切削过程中切屑不能及时有效地排出孔,以致加工时容易发生金属屑堵塞造成孔壁局部的不良状况,甚至刀具断裂的情况。
三是配备的钻头及定位夹具均会对深孔加工技术应用效果产生较大的影响。
长时间进行深孔加工作业会导致定位导向件发生不同程度的磨损问题,以致深孔半径、深度等指标和设计要求之间出现很大的出入,不仅影响加工的精准度,还弱化深孔加工技术的价值。
四是造成钻头及加工夹具发生磨损情况的因素不唯一,而加工部位的冷却效果差、温度较高等被认定是引起磨损问题的两大主因。
1.2深孔钻加工有一定局限性钻孔作业过程中,加工零件的材质可切削性,被加工的孔深与孔径比例也局限于加工条件,钻孔的刀具刚性和排屑效果也会限制深孔的加工质量。
深孔技术要求

深孔技术要求
深孔技术要求包括以下几个方面:
孔径和孔深:根据不同的加工需求,深孔的孔径和孔深都有一定的要求。
孔径通常较小,需要高精度的钻头进行加工;孔深则根据实际需要而定,一般要求钻头具有较长的长度。
孔的直线度:为了保证深孔加工的质量,孔的直线度是一个重要的技术要求。
孔的直线度要求较高,需要使用高精度的钻头和机床,以确保钻头在加工过程中不会偏离中心线。
表面粗糙度:深孔加工后的表面粗糙度也有一定的要求。
粗糙度的大小直接影响孔的精度和密封性能,因此需要在加工过程中进行控制。
排屑:在深孔加工过程中,排屑是一个重要的问题。
排屑不好会导致钻头切削阻力增大,影响加工质量和效率。
因此,需要选择合适的钻头和加工参数,以确保排屑顺畅。
冷却润滑:深孔加工过程中需要使用冷却润滑剂,以减小切削热、提高切削效率、减小刀具磨损和提高加工表面质量。
因此,冷却润滑剂的选择和使用也是深孔加工技术要求的一部分。
深孔加工技术要求较高,需要使用高精度的钻头和机床,选择合适的加工参数和冷却润滑剂,以保证加工质量和效率。
- 1、下载文档前请自行甄别文档内容的完整性,平台不提供额外的编辑、内容补充、找答案等附加服务。
- 2、"仅部分预览"的文档,不可在线预览部分如存在完整性等问题,可反馈申请退款(可完整预览的文档不适用该条件!)。
- 3、如文档侵犯您的权益,请联系客服反馈,我们会尽快为您处理(人工客服工作时间:9:00-18:30)。
若想再增加过流截面积,只有采 用下述的两种形式。
(2)斜坡斜台型和斜坡平台型:如图 1.9-4(b)、(c)所示,这两种形式均 是斜坡型的改进型,是针对上述问题 采取的措施。台阶磨法可以获得较大 的过流截面积,并相应增加了内刃内 角的变化范围,为非标准型枪钻的刃 磨和使用提供了可能性。
2)枪钻钻型
除基本钻型外,还有一些变革钻型, 如图1.9-6所示。图1.9-6(a)为外刃倒角 型,此钻型可使刃口强度增加,延长刀 具寿命,并能起到一定的分屑作用。
图1.9-6(b)为外刃分屑型,主要用于直 径较大的枪钻。标准枪钻一般通过钻尖 来分屑,并且很不可靠。因长时间的切 削,钻尖变钝,切削作用必然减弱。特 别是当枪钻直径较大时,切屑厚而宽, 不易排出,必须采用此钻型进行分屑。
A、钻头头部
钻头头部有出油孔,出油孔的形状和大小主要根据 切削液流动特性和流动要求来确定。常用的形状有单 圆孔形、半月形、八字形及双圆孔形4种,如图1.3所 示。其中八字形及双圆孔形出油孔面积为最大,常用 于大直径枪钻或双刃枪钻。小直径枪钻或单刃枪钻常 用单圆孔形及半月形截面形状。
枪钻油孔形式
为了保证加工孔的精度,枪钻头部有两个导向块, 与副切削刃带形成三点定圆,自身导向。导向块的形式 随枪钻头部结构和直径而异,如下图所示。镶焊结构头 部,镶焊两个条块状导向块;整体结构头部,直径大的 直接制成;直径小些的可在圆柱面上磨出平面,自然形 成两个导向块。
2)切削部分倒锥值
倒锥的主要作用是: (1)减少钻头与工件孔壁间的摩擦,减少 切削热。 (2)保证有冷却润滑膜产生,防止钻头导 向块和切削刃表面的损坏。
倒锥值的大小直接影响枪钻的沿径向的磨损量越大。 因此,倒锥值的确定原则是:既要考虑 被加工另件的精度要求,又要尽量延长 枪钻的使用寿命。
(3)为了使钻头在钻孔时不被卡死,枪钻的 外圆圆周角大于炮钻(这同时有助于增大钻 头和钻杆的扭转刚度和弯曲刚度);
(4)为了使钻头的切削性能更好,在外刃的 周边磨出后角(边刃后角)。
❖为保证钻头 与钻杆准确对 接,并能承受 较大的转矩, 将二者的接口 部加工成互相 吻合的60°尖 角形,或90° 平底形(图1. 4),然后钎 焊为一个整体。
槽形角过大,则钻杆刚性减弱过多。 计算和实验表明,当θ= 110°时, 钻杆的扭转刚度为轧制前圆形钢管 的35%。
二、其他几何参数 1)零位芯柱
图1.9-3 枪钻零位芯柱
枪钻的主切削刃要通过钻头中心或略低
于钻头中心,不得高于钻头中心,避免崩刃。 由于内刃低于中心h值,形成了柱形芯棒 (零位芯柱),如图1.9-3所示。芯棒的形成 一方面可以减少轴向力,另一方面减少了孔 轴线的偏移,给枪钻以附加的导向,对钻削 是有利的。芯棒直径不宜过大,以便于自动 折断同切屑一起排出。通常取零位芯柱半径 h=(0.015一0.025)d0,一般不要大于0.4 mm。为了避免芯棒与钻头体之间的摩擦, 内刃一般少量超过钻头中心,超过的值用bc 表示,bc的值必须大于芯棒半径,一般取bc =(2~3)h。
• 图18为一种针对粘性材料设计的双油孔单边刃枪钻。 位于切削刃上方但位置靠后的第二出油孔,直接将 高压切削液冲击正在形成的切屑使之加工折断,同 时改善前刀面的润滑条件。这种钻头的主要缺点是 前刀面重磨有一定难度,用户较难掌握。
图1.9为一种断 面类似于麻花 钻的双刃外排 屑深孔钻,其 结构相当于带 直槽的油孔麻 花钻。
• 枪钻的这种不可拆卸结构,带来了一些 本质性的缺陷,如重磨时拆卸、安装不 便,钻头报废时钻杆不能重复使用,因 而也增大了刀具成本等等。钻头直径越 大,钻杆越长,上述弊端就越显得突出。 这是枪钻不适用于φ35mm以上深孔加工 的一个主要原因。历史上,曾经有不少 人多次尝试过采用可拆卸的连接方案 (如埋头孔销钉结合、埋头孔柄舌结合、 螺纹夹紧V形槽结合、凸轮面结合等), 但都因缺乏实用价值而以失败告终。
图1.9-1 枪钻切削部分要素
一、切削角度 1) 前角和后角
前角γ0=0°,便于制造和重磨;外刃 后角α1 = 8°~15°(切削钢料为8°~12° ,硬度高时取小值;钻削铝、镁及其合金时 为15°。内刃后角a2= 10°~15°, 接近钻 心取上限。
副切削刃后角α0= 12°~30 °,并留有 刃带宽度bα,ba=0.25~0.5mm,过窄易划 破油膜,过宽将增大摩擦力,引起卡钻。
三、过油通道和钻型 1)过油通道
为了增加切削液的流动空间,需要在钻头 内刃的延长线上磨出过油通道,如图1.9-4所 示。
图1.9-4枪钻的过油通道
为避免切屑堆积,使切削液易于流向V型 槽,还要在轴肩上磨出与径向成15°~30°, 宽度为0.2mm的倒角。
过油通道有以下3种形式:
(1)斜坡型:如图1.9-4(a)所示,刃磨方便,应 用较多。但这种过油通道的过流截面积较小, 并且难以增大。理由是该过流截面积取决于 内角ψrr,而内角ψrr受到钻头切削性能的限制, 不宜过大。如果过大,则导向块滞后量过大, 易引起入口处切削不平稳和切削液溢漏过多, 并可能使内刃径向力大于外刃径向力,造成 钻头走偏。标准枪钻一般取ψrr=20°。
图 导向块的形式
B、钻杆 枪钻钻杆一般用高强度合金钢管压制成。根据 钻孔的深浅和钻头的结构,可选用不同形式的钻 杆,如图下所示。
图1.a 枪钻钻杆的类型 (a)-D形;(b)-U形;(c)-V形;(d)-中心槽形; (e)-圆形;(f)-麻花形
C、钻柄
❖钻柄的作用:1)与机床实现对接、承受夹 持力、传递转矩及进给力;2)在密封条件下 向钻头传输高压切削液。其外径必须与钻杆严 格同轴,并且有足够大的直径以便于固紧。历 史上曾出现过多种型式的钻柄设计,图1.1-5 为其中最常见的型式。
K = 0.02d0
3)导向块滞后量
为了防止导向块前端先于刀刃参加切 削,要求导向块前端必须滞后外刃尖一 定距离,该值即称为导向块滞后量如书 中图1-28所示,P49。滞后量不能过大, 否则将引起入口处切削不稳定。通常滞 后量取为0.5~1.2mm,或取为(2~4)f(f 为进给量)。 但对于加工硬化剧烈的材 料,考虑到导条的磨损,滞后量可取大 些,像不锈钢,可取1.5-2.5mm。
图1.9-2枪钻不同刃形的受力状态
外刃径向力过大,如图1.9-2(a) 所示,将使作用于导向块的挤压力增 大,摩擦增大,已加工表面恶化,热 量增加.
内刃径向力过大,如图1.9-2(b) 所示,将使合力作用于内刀刃上,引 起较大的直线度误差,使孔径尺寸超 差、表面粗糙度增加、切削刀刃带过 早磨损等。
• 直径大的钻头可改用三片硬质合金镶在钢质 钻头体上,见图1.3(b).
• 枪钻继承了炮钻单边刃切削的构思,只用一 侧半径上的单边切削刃加工,但对炮钻作了 以下几项重大改进:
(1)将炮钻的平刃改为由外刃和内刃组成的 单边刃结构;
(2)炮钻的前刀面略高于中线,而枪钻的前 刀面不得高于中线,但允许略低于中线;
枪钻切削部分长度与孔精度和倒锥斜角之 间关系为:
ls=(dmax-dmin)/2tanα 式中 ls—枪钻切削部分长度mm;
dmax—最大孔径,mm; dmin—最小孔径,mm; α一倒锥斜角,(°)。
为适应多种切削加工的要求,标准枪钻一般 按每100 mm的长度上直径的减少量来标注,这 个减少量K可以按下式计算,即
❖由于其双刃完全对称,所以不具备枪钻的单边刃自 导向特征,原则上属于油孔麻花钻的变种,但刀具 刚度稍逊于麻花钻。由于不具备自导向作用且刚度 较低,虽然进给量稍大于枪钻,但钻头易走偏,加 工粗糙度也较大。
1.2.2、枪钻几何参数
枪钻切削部分要素如下图所示。有两条主切削刃 和一条副切削刃,靠近钻心的一条主切削刃称为内刃, 另一条主切削刃称为外刃,其交点被称为钻尖。
最好的情况是内、外刃径向力相等或
者外刃径向力稍大于内刃径向力,如图 1.9-2(c)所示,使合力作用于导向块上, 防止钻头走偏。在理论上,外、内刃径向 力平衡时,ψr、ψrr和e有如下关系:
通常取e= d0/4。考虑内刃切削速度 较低,钻心部分切削情况比较复杂,要
保证外刃径向力等于或稍大于内刃径向 力,必须使ψr>ψrr。加工一般材料时, 取e= d0/4, ψr为30°~40°,ψrr为 20°~25°,软材料取小值。用枪钻加
第一章 外排屑深孔加工技术
现代深孔钻削技术包含三项内容:
A、实体深孔钻削技术;B、套料钻削技术 C、深孔扩钻技术。其中,实体钻削占有主要 地位,也是深孔加工技术的核心。
外排屑深孔钻是20世纪30年代初最早用于 枪管制造的具有单切削刃、自动排屑及冷却润 滑、具有自导向功能的现代深孔刀具,通称 “枪钻”。在枪钻的基础上,随后又衍生出几 种双刃外排屑深孔钻。
有两个分设于直径对侧但刃宽不相等的切削刃
(每侧的切削刃又分为内刃和外刃),中央的通油孔 是偏心孔。因此,加工时两侧的切削刃都达不到中心, 从而留下一根直径不大的芯棒。由于有双刃参加切削, 可以适当加大进给量。另外,其中央芯柱对钻头也能 起到一定的定心作用,使钻头的走偏降低。其缺点在 于刀杆的制造难度较高,而且排屑槽较窄,不适于加 工韧性大的材料。
本章重点介绍枪钻技术
1.1 枪钻的由来
• 扁钻:书中图1.1,最古老的实体钻孔刀 具,用于木材、青铜器、铁器上短小孔 的加工,工效低,易走偏,钻出的深孔 弯曲而粗糙。由于其没有好的自导向, 跑偏是其致命的弱点。为了改善上述的 弱点,18世纪末出现了一种用于炮管钻 孔的单边切削刃钻头-炮钻。
炮钻:图1.2,亦称半圆钻,单边切削 刃钻头,自导向功能和良好的刚度;但 由于不能连续自动排屑,只能靠频繁的 退出钻头来实现排屑和切削刃的冷却润 滑,因此工效很低。可由于炮钻的单刃 切削和自导向功能的实现,成为实体钻 孔刀具的一大发明,所以说,炮钻可当 之无愧地被列为第一代深孔钻头。 枪钻:20世纪30年代诞生,能自动供油 排屑,单边刃切削,能自动导向。