重型汽车双层车架结构传力特征分析
汽车车架的动力学分析--模态分析
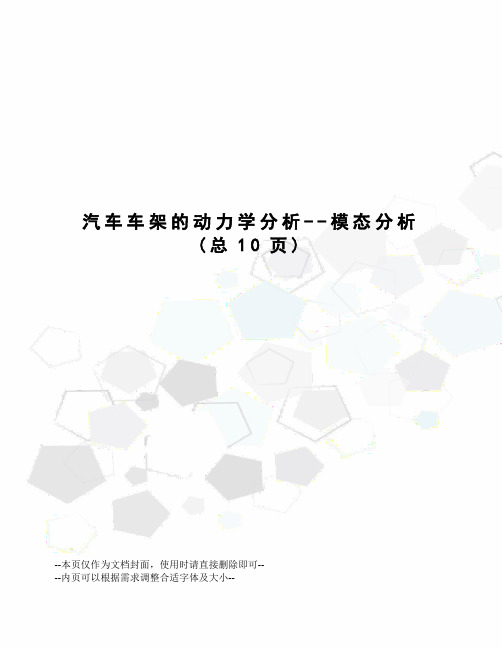
汽车车架的动力学分析--模态分析(总10页)--本页仅作为文档封面,使用时请直接删除即可----内页可以根据需求调整合适字体及大小--北京科技大学机械工程进展(论文)题目:汽车车架的动力分析计算(模态分析)院别:机械工程学院专业班级:机研106班学生姓名:学号:导师:评分:2010年11月26日轻型载货汽车车架模态分析摘要:车架作为汽车的承载基体,安装着发动机、传动系、转向系、悬架、驾驶室、货厢等有关部件和总成,承受着传递给它的各种力和力矩。
所以对车架的结构十分重要。
本文主要采用有限元方法对车架的进行模态分析,研究了车架结构与其固有频率及其振型的关系, 给出车架在一定约束下的固有频率及固有振型,为解决车架结构的动力学问题和结构的改进提供了一定的依据。
关键词:有限元方法;车架;固有频率;模态分析1 引言车架是一个弹性系统,在外界的时变激励作用下将产生振动。
当外界激振频率与系统固有频率接近时,将产生共振。
共振不仅使乘员感到很不舒适,还会带来噪声和部件的疲劳损坏,威胁到车架的使用寿命和车辆安全。
车架是一个多自由度的弹性系统。
因此,它也有无限多的固有振型,而作用在车架上的激励来自于悬架系统、路面、发动机、传动系等的振动,这些振动对车架的激励可以认为是全频率的,但是,路面和悬架系统对车架结构激励的特点一样,每种激励在所有频率范围内并不是等能量分布的,所以,试图在所有频率上消除作用在车架上的激励,与车架结构的某些振型的共振是不可能。
因此,只有将注意力集中在各激励的能量集中的频率上,使之与所关心的车架的某阶振型不发生共振。
因而对车架进行模态分析以掌握车架对激振力的响应,从而对车架设计方案的动态特性进行评价,己经成为车架设计过程中必要的工作[1]。
2 模态分析理论基础在有限元分析程序中,振动方程表示为:1-1该方程可作为特征值问题,对无阻尼情况,方程可简化为:1-2其中。
ω2(固有频率的平方)表示特征值;{μ}表示特征向量,在振动的物理过程中表示振型,指示各个位置在不同方向振动幅值之间的比例关系,它不随时间变化。
汽车车架的动力学分析--模态分析

图1-3 一阶弯曲
图1-4 二阶弯曲
图1-5 二阶扭转
图1-6 三阶弯曲
图1-7 前端局部模态
图1-8 弯扭组合
4.3汽车模态分析结果的评价指标
工程结构要具有与使用环境相适应的动力学特性。一辆汽车结构优劣的基本着眼点是在弯曲和扭转方面总的动态性能。如果汽车结构动力学特性不能与其使用环境相适应,即结构模态与激励频率藕合,或汽车子结构之间有模态藕合,都会使汽车产生共振,严重时会使整个汽车发生抖振,车内噪声过大,局部产生疲劳破坏等[5]。模态分析是计算结构的固有频率及其相应振型。结构的固有频率是评价结构动态性能的主要参数,当结构固有频率和工作频率一致时,就会发生共振现象,产生较大的振幅,大大降低寿命。固有振型是发生共振现象时结构的振动形式。
[6]黄华,茹丽妙.重型运输车车架的动力学分析[J].车辆与动力技术,2001.6
6参考文献
[1]余志生.汽车理论[M].北京:清华大学出版社, 1989
[2]丁丽娟.数值计算方法[M].北京:北京理工大学出版社, 1997
[3]王勖成,邵敏.有限元基本原理和数值方法[M].北京:清华大学出版社.1997
[4]傅志方,华宏星.模态分析理论与应用,上海交通大学出版社,2000
[5]《汽车工程设计》编辑委员会.汽车工程手册.试验篇.北京:人民交通出版社.2001.6
4车架模态计算与结果分析
4.1模态分析步骤
对车架进行模态分析主要有以下步骤:
(l)在Pro/E中建立车架的三维模型。
(2)施加边界条件和载荷(对于自由模态不施加约束条件),定义分析类型和求解方法并进行网格划分、提交求解器求解。
(3)提取结果,进行可视化处理,对结束进行分析。
矿用汽车车架结构分析
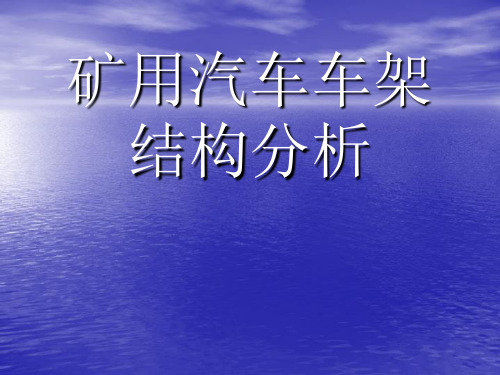
处于“面一面接触” 处于“面一面接触”状态。车厢与车架的 刚度共同决定了接触压力的大小与分布形 式,此问题属于静不定问题,无法事先知 道该接触力的大小。现有处理方法一般将 其看成均布载荷,这样处理不能准确定位 质心位置。本文将接触力分成两段不同的 均布载荷,以保证质心位置,其原理见图3 均布载荷,以保证质心位置,其原理见图3。 假设车厢与车架的接触长度为L 假设车厢与车架的接触长度为L ,则:
根据实际尺寸及上述公式,可得各 参数如表1 参数如表1示。
• 将各载荷按其坐标值、质心位置和分布情
况分别施加到车架上,再按各工况车架受 力情况分别进行约束,施加载荷与约束后 的模型如图4 的模型如图4~6所示。
3 各工况分析结果
3 各工况分析结果
3 各工况分析结果
本文针对车架在3 本文针对车架在3种典型工况下的主 要结构元件进行分析,
•
二、有限元分析
• 2.1 车架实体模型的建立Βιβλιοθήκη 2.1 车架实体模型的建立
• 由于车架模型比较复杂,所以先用Solidworks建 由于车架模型比较复杂,所以先用Solidworks建
立实体模型,然后通过Parasolid数据转换转到 立实体模型,然后通过Parasolid数据转换转到 ANSYS软件的前处理模块中,这样可以节省建模 ANSYS软件的前处理模块中,这样可以节省建模 时间。 在保证计算结果的准确性,尽量减少节点数量, 保证总体结构不变,保留危险部位的细节结构的 原则下,对车架三维实体模型进行简化,略去不 必要的小孔和圆角等不重要的细节以降低网格划 分的难度。简化后的实体模型如图I 分的难度。简化后的实体模型如图I所示。
2.3 典型工况的选取
重型车车架组合结构的有限元分析

按照实际试验和经验算法, 以垂直静力弯曲和 弯扭组合 2 种工况计算了车架的应力, 研究了货物 载荷的偏置及超载对车架应力的影响。重型车如遇 实际所承载荷过大、 路面不平及车速较高等因素 , 致 使行驶中的车架受到比较频繁的扭转和重载 , 很可 能会使得局部连接板区域及相关支架位置产生应力 集中, 从而产生车架的断裂破坏。 模态分析得出了该重型车车架的固有频率和振 型。计算表明, 车架在自然约束条件下低阶频率范 围在 9~ 45 H z, 车架振型表现为垂直弯曲、 面内弯 曲、 扭转及弯扭组合特征。 参考文献:
2
车架有限元模型的仿真数据分析
车架钢板弹簧座 处每个节点的垂直位移被约
束 ; 在车架的左右对称面上 , 选取 2 个节点分别进行 水平面内纵、 横向的附加约束, 就可以求出变形引起 的节点位移。模型计算的静载荷包括驾驶室及驾乘 人员, 发动机及油箱, 货厢及货物。前面 2 种为集中 载荷, 在建立有限元模型时将作用点设置在节点上, 程序可以直接叠加到结构载荷向量中去 ; 货厢及货 物为均布载荷, 在有限元分析时 , 程序将它们放置到 单元节点上 , 形成单元节点力向量, 然后经由单元载 荷乘子 , 把载荷情况叠加到结构载荷向量中去。 弯扭组合状态即在钢板弹簧座的左前、 右后分 17
《机械与电子》2005( 2)
M PC 类型 R BE2 R BE3 Expl icit
[ 2]
图 1 板簧的简化
还有导向作用( 图 1b) , 即钢板弹簧在各个方向上均 有刚度 , 但其它方向上的刚度要比垂直方向的刚度 大得多 , n 、 p 节点间为一刚性梁[ 3] 。节点 m 和 n , p 和 q 之间弹簧元的刚度分别为 y K / ( x + y ) 和 x K / (x + y)。 与支架位置相关联的弹簧单元支承点, 取在连 接销的中心点位置, 这样有助于模拟板簧对支架位 置的弯矩作用。如图 2、 表 1 所示, 弹簧元的上端点 与该中心点之间建议采用 RBE2 或 RBE3 型多点约 束 , 以实现连接点的位移协调或总力平衡。
车桥结构
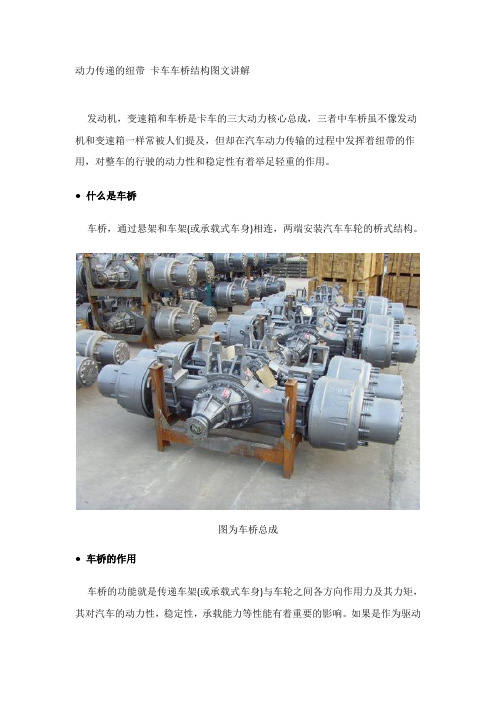
动力传递的纽带卡车车桥结构图文讲解发动机,变速箱和车桥是卡车的三大动力核心总成,三者中车桥虽不像发动机和变速箱一样常被人们提及,但却在汽车动力传输的过程中发挥着纽带的作用,对整车的行驶的动力性和稳定性有着举足轻重的作用。
● 什么是车桥车桥,通过悬架和车架(或承载式车身)相连,两端安装汽车车轮的桥式结构。
图为车桥总成● 车桥的作用车桥的功能就是传递车架(或承载式车身)与车轮之间各方向作用力及其力矩,其对汽车的动力性,稳定性,承载能力等性能有着重要的影响。
如果是作为驱动桥,除了承载作用外还起到驱动、减速和差速的作用。
● 车桥的结构卡车一般采用发动机前置,后轮驱动的布置方法。
一般情况下,前桥都是转向桥,而驱动桥在后桥。
前桥的结构前桥定型结构卡车前桥由主要由前梁,转向节,主销和轮毂等部分组成。
车桥两端与转向节绞接。
前梁的中部为实心或空心梁。
● 驱动桥结构驱动桥位于汽车传动系统的末端,主要由主减速器、差速器、半轴和驱动桥壳等组成。
驱动桥典型结构1.主减速器主减速器一般用来改变传动方向,降低转速,增大扭矩,保证汽车有足够的驱动力和适当的速度。
主减速器类型较多,有单级、双级、双速、轮边减速器等。
卡车后桥主减速器1)单级主减速器由一对减速齿轮实现减速的装置,称为单级减速器。
其结构简单,重量轻。
2)双级主减速器对一些载重较大的载重汽车,要求较大的减速比,用单级主减速器传动,则从动齿轮的直径就必须增大,会影响驱动桥的离地间隙,所以采用两次减速,通常称为双级减速器。
双级减速器有两组减速齿轮,实现两次减速增扭。
双级主减速器为提高锥形齿轮副的啮合平稳性和强度,第一级减速齿轮副是螺旋锥齿轮。
二级齿轮副是斜齿圆柱齿轮。
主动圆锥齿轮旋转,带动从动圆锥齿轮旋转,从而完成一级减速。
第二级减速的主动圆柱齿轮与从动圆锥齿轮同轴而一起旋转,并带动从动圆柱齿轮旋转,进行第二级减速。
因从动圆柱齿轮安装于差速器外壳上,所以,当从动圆柱齿轮转动时,通过差速器和半轴即驱动车轮转动。
浅谈重型汽车车架设计共20页文档

61、辍学如磨刀之ห้องสมุดไป่ตู้,不见其损,日 有所亏 。 62、奇文共欣赞,疑义相与析。
63、暧暧远人村,依依墟里烟,狗吠 深巷中 ,鸡鸣 桑树颠 。 64、一生复能几,倏如流电惊。 65、少无适俗韵,性本爱丘山。
21、要知道对好事的称颂过于夸大,也会招来人们的反感轻蔑和嫉妒。——培根 22、业精于勤,荒于嬉;行成于思,毁于随。——韩愈
23、一切节省,归根到底都归结为时间的节省。——马克思 24、意志命运往往背道而驰,决心到最后会全部推倒。——莎士比亚
25、学习是劳动,是充满思想的劳动。——乌申斯基
谢谢!
半挂牵引车车架的强度特性分析

半挂牵引车车架的强度特性分析摘要:车架是车辆的关键承重结构,各种载荷最终都会传递到车架上。
因此,车架的结构性能直接关系到整车结构性能。
本文以某型半挂牵引车车架设计为例,采用有限元分析法对车架结构强度展开深入分析,提出优化方案并进行仿真验证,结果显示结构优化方案可显著降低车架关键测点的等效应力最大值,实现强化车架结构的目的。
关键词:半挂牵引车;车架;强度分析;有限元分析半挂车是公路运输的重要车型。
欧美等发达国家的公路货运绝大多数由半挂车完成。
而在国内,半挂车是目前第二常见的大型牵引车类型,其车架除了要承受发动机、车架和货物的重量,还要承受车辆行驶过程中产生的各种力和力矩,所以其可靠性不仅与承载能力有关,也关系到车辆的运行安全[1]。
车架出现疲劳裂纹会导致车架断裂等安全问题。
为确保车架结构强度符合要求,需对车架结构强度进行有限元分析,根据分析结果提出结构优化方案。
本文对某型半挂车车架结构强度进行了有限元分析,建立相关有限元分析模型,并利用有限元分析软件对半挂车车架的强度进行了有限元分析,根据分析结果提出车架结构的改进方案并进行验证。
1车架有限元模型建立1.1车架结构某型半挂车车架材料为16MnL,结构为梯形边梁结构,框架外宽876mm,内侧边梁与盖梁采用直径15mm的铆钉牢固连接。
前后梁为槽式结构,第二梁为圆管梁,中梁为铸件,平衡轴梁为背靠背槽式结构,其余梁为上下叶片结构体。
为了增加车架的坚固性和方便挂斗,在车架两侧的轴梁水平处铆接厚8mm的侧角板。
前桥悬架板簧满载垂直刚度为383 N/mm,中、后桥平衡器悬架板簧满载垂直刚度为2285 N/mm。
主成分材料的弹性模量为2.17×105,泊松比为0.30。
图1为优化前的原始车架结构设计。
图1 优化前的原始车架结构设计1.2模型构建改性半挂牵引车车架结构复杂,由大梁、立梁、双梁、平衡器轴、平衡器悬挂支架、前后板簧支架等众多大型部件组成[2]。
重型商用车车架

重型商用车车架纵梁制造技术的研究与应用一、前言近几年,随着我国西部大开发和整体国民经济的快速发展及高速公路通车里程的不断增加,重型商用车出现俏销局面,由于国内汽车制造厂一直以生产中型车和轻型车为主,面对新的机遇,各制造厂家积极调整产品结构,以适应市场的变化。
生产重型车首先要解决的是底盘问题,底盘中,车架纵梁是关键的零件之一,是制约车架总成质量和能力的瓶颈。
我公司作为国内主要三大重型商用车生产厂之一,近两年也推出多种市场热销的重型车,这些新车型的车架纵梁都是全新结构设计,复杂程度及加工难度比以往车架纵梁都大,而且原有模具加工无法利用。
在这些新车型车架纵梁的生产准备过程中,如采用常规工艺和常规模具设计方案,不仅不能适应目前市场经济条件下的“多品种、小批量、多批次”的生产方式,而且投入成本很高,准备周期也很长,难以适应产品和市场的变化。
在参考国内、外纵梁制造技术和结合自身实际情况的基础上,我们将柔性化制造技术作为目标,一次规划,分期实施具体项目,逐步形成具有企业特色的车架纵梁柔性化制造体系。
二、重型商用车车架纵梁的产品特征重型商用车车架纵梁普遍采用双梁结构,纵梁与加强梁料厚匹配目前国内主要有:“7+5”、“7+7”、“8+5”、“8+7”等几种。
与中型商用车车架纵梁相比,主要变化是“加强、加长、加宽”等,产品特征如下:材料:高强度钢板16MnL,抗拉强度σb在510~610MPa,甚至更高。
结构:双大梁结构,即纵梁+加强梁料厚:纵梁:7.0mm,8.0mm加强梁:5.0mm,7.0mm断面尺寸:280mm,300mm,甚至更大长度:5600~11500mm车架宽度: 780~850mm纵梁和横梁连接方式:国内产品以翼面连接为主,采用铆钉铆接。
国外产品以腹面连接为主,采用高强度螺栓连接。
纵梁类型:通常有以下几种类型(见图一)断面形式纵梁形式备注等断面直线式多数变断面直线式等断面前段弯曲式装配大发动机变断面前段弯曲式装配大发动机三、国内外车架纵梁目前的制造技术概况(一)传统的冲压模具制造技术1、工艺和设备特点采用冲压模具制造纵梁是一种传统的制造工艺,工艺特点是生产效率高、质量稳定,适用于单一品种的大批量生产。
- 1、下载文档前请自行甄别文档内容的完整性,平台不提供额外的编辑、内容补充、找答案等附加服务。
- 2、"仅部分预览"的文档,不可在线预览部分如存在完整性等问题,可反馈申请退款(可完整预览的文档不适用该条件!)。
- 3、如文档侵犯您的权益,请联系客服反馈,我们会尽快为您处理(人工客服工作时间:9:00-18:30)。
重型汽车双层车架结构传力特征分析
作者:黄昶春沈光烈韦志林
1 前言
近年来,国内外多种中、重型汽车车架均采用双层槽钢纵梁。采用这种型式的车架纵梁,
可以减少对纵梁生产设备的要求,也可以适应生产变型车的需要[1-2] 。但是,由于设计中
对用铆钉连接的双层槽钢的传力特征认识不足,使得一些车架出现早期断裂现象,或使车
架材料用量过多,增加了生产成本和汽车质量。
作者经研究发现,双层槽钢的车架用铆钉连接时,内层槽钢受力参与程度不足,不符合梁
理论中梁横截面平面变形的假设,用常用的梁理论计算会使计算应力比实际应力偏低,从
而导致车架刚度强度不足。针对以上问题,作者进行多种铆钉布局及间距方案的比较分析,
给出合理的计算模型及铆钉连接的设计方案,对此类结构设计有一定的帮助。
2 铆钉连接传力特征的分析
材料力学中梁的理论以及有限元法的空间梁单元理论都是建立在梁弯曲时横截面保持平面
这一假设基础之上[3] ,该假设称纳维什(Navier)假设。但是,这个假设并非对任何结构
型式的梁都适用,并使计算误差保持在工程上可以接受的误差范围之内。
双层槽钢梁外层受力变形后,它的变形通过铆钉将弯矩传递给内层槽钢。铆钉的刚度与内
层槽钢整个截面的刚度相比是非常小的。一般来说,车架纵梁的同一截面上仅用2 个低刚
度的铆钉连接传力,要使大刚度的内层槽钢横截面产生符合平面假设的变形,从理论和实
际上都是难以实现的[1-6] 。
为研究铆钉传力的特征,作者首先设计长度为500mm的槽形截面悬臂梁,在自由端通过
铆钉传力。整个结构用壳单元离散,在外层槽钢与铆钉之间建立刚性联接,给定一个强迫
转角位移,进行计算。图1表示Mises应力三维云图,从图中可以看出,传力路线从铆钉
开始,向上下翼板和腹板的交界棱线发展,高应力区仅占翼板的很小部分,且离铆钉越远
越小,应力分布也完全不符合平面假设。为更进一步从数量上分析,需计算悬臂梁在2种
情况下的应变能密度: (1)梁自由端横截面刚性转动1°强迫位移;(2)梁自由端仅通过2
个铆钉给定1°强迫位移。
图2和图3分别表示在这2种情况下的应变能密度沿梁轴线分布的曲线图。从图2可明显
看出,当自由端截面按平面假设整体转动时,沿整个轴线长度上的应变能密度量等值分布,
说明整个梁呈理想的纯弯曲状态。从图3可看出,仅铆钉所在截面,因应力集中形成一个
应变能密度峰值,而沿梁轴线,离铆钉距离越远则应变能密度越小。从数量上看,对应同
一截面,应变能密度在通过铆钉传力时,仅为自由端截面整体转动时的013~015左右。
图2和图3 的曲线从能量角度定量地说明通过铆钉连接时,传力程度不足,完全不符合梁
平面变形的假设。
3 双层槽钢铆钉连接合理布局的研究
为探讨不同计算模型对计算结果的影响,给出合理的铆钉连接设计方案,设计如图4、图5
表示的双层槽钢纵梁受力及截面结构图,用不同的计算模型进行计算,为此建立2种有限
元模型。
(1)不考虑铆钉因素,将双层槽钢看成整体结构,用一层梁单元、一层壳单元与一层体单
元计算。
(2)考虑铆钉的作用,将结构离散成双层壳单元,各层之间仅在铆钉处相连,分别在腹板
上或翼板上按100、200、400、500和800mm间距布置铆钉。
作者在研究中采用MSC /NASTRAN及其前后处理软件PATRAN作为分析工具。
4 计算结果分析
利用MSC /NASTRAN软件计算出各种情况下的位移与应力。为便于比较各种情况下的位
移与应力,排除壳单元受力处局部变形的影响,并使不同单元下计算的结果具有可比性,
取腹板下沿区域Y方向(垂直方向,见图4)的最大位移及应力(V·Mises应力)进行比
较。
4.1 位移结果分析
根据不同单元计算出来的腹板下沿区域Y方向的最大位移见表1。
当作为梁单元计算时,得到的最大位移与我们利用梁的经典理论计算得到的挠度是一致的。
但作为一层体单元、一层壳单元计算则位移值偏大。
从表1可知,根据双层壳单元计算,当采用铆钉连接时,铆钉的间距与铆钉的位置都影响
梁的刚度。合理地布置铆钉对提高梁的刚度与利用率都很重要。表1也可直观地说明以下
问题。
(1)在相同铆钉间距下,双层槽钢在腹板处连接的刚度比在翼板处连接的刚度要大,特别
是随着铆钉间距的增大而变得更加明显。
(2)当铆钉同在腹板或翼板上时,随着铆钉间距的增大,槽钢的刚度越来越小。
(3)通过铆钉连接的双层槽钢的刚度比相同厚度的单层槽钢的刚度要小。
4.2 应力结果分析
通过MSC /NASTRAN计算各种情况下的应力输出,下面通过几种典型情况来分析说明。
从图6和图7的Mises应力云图看出,当铆钉间距为100mm时,内层槽刚翼板高应力区
应力传递基本连续,但其腹板处应力与外层相比则明显偏低。
从图8和图9的Mises应力云图可发现在相同区域上,当铆钉间距为400mm时,内层槽
钢翼板高应力区应力传递比铆钉间距为100mm时明显不连续,且在铆钉连接处产生较大
的应力集中,内层槽钢没有充分参与受力,导致外层槽钢最高应力上升。
对于铆钉布置在翼板时,应力分布也有相似的情况(限于篇幅,应力图没有列出)。但由
薄壁杆系结构力学可知,槽形截面梁在经受弯扭联合作用时,最大正应力发生在翼板边缘
上。当在翼板上用铆钉连接时,铆钉孔会削弱截面的强度使应力更高,因此不是一种好的
方案。
5 结论
(1)双层槽钢铆钉连接不能简单当作连续截面处理。随着铆钉间距的增大,双层槽钢铆梁
的刚度随之下降。
(2)当双层槽钢用铆钉在腹板连接时,内层槽钢腹板的应力比外层槽钢腹板的应力明显偏
低,外层槽钢腹板上的剪力不能有效地向内层槽钢传递。
(3)在翼板上用铆钉连接的梁,铆钉处应力集中程度较高,从总体上看,应力也高于在腹
板处用铆钉连接的梁。
(4)内层槽钢在铆钉间距为100mm时,翼板传力连续,整个翼板充分参与受力,而当铆
钉间距大于100mm时,在翼板处明显出现传力断续现象,应力集中也明显上升。
(5)当双层槽钢用铆钉连接时,在铆钉连接处应力集中,在设计中应充分考虑这些因素。
(6)优化设计的车架经柳州汽车厂多种型号的重型汽车使用证明,该车架性能优良。
参考文献
[1] 王烈,诸葛鸿程,陈细良. 汽车车架动应力均化分析与实验研究[J]. 汽车工程, 1998
(2) : 90 - 95.
[2] 冯国胜. 汽车车架结构参数优化设计[J]. 汽车技术, 1994 (3) :6 - 11.
[3] 冯国胜. 汽车车架动特性分析与应用[J]. 汽车技术, 1994 (8) :9 - 12.
[4] 朱杰,汪德容. 全板元模型在车架有限元分析中的应用[J]. 湖北汽车, 1995 (3) : 17
- 20.
[5] 张辉,张敬民. 重型自卸车车架的静态有限元分析[J]. 机械设计与制造, 1992 (4) :
38 - 40.
[6] 许尚贤,陈云飞. 特大型汽车起重机车架有限元分析[J]. 东南大学学报, 1995 (4) :
62 - 66.(end)