炼铁厂降硅途径探讨
浅谈第二炼铁厂喷煤节能降耗

2020年第4期南钢科技与管理37浅谈第二炼铁厂喷煤节能降耗张金山(第二炼铁厂)摘要:介绍第二炼铁厂喷煤喷吹系统自动化程序优化及喷吹模式创新,以喷煤制粉生产过程控制、降低氮气消耗为例阐述节能降耗措施,为高炉炼铁成本降低提供有力帮助。
关键词:喷煤工艺优化节能降耗Discussion on Energy Saving and ConsumptionReduction of Coal Injection in Iron-making Plant2#ZHANG Jinshan(Iron-making Plant2#)Abstract:This paper introduces the automatic program optimization and injection mode innovation of coal injection system in Iron-making Plant2#.Taking the pulverizing production process control and reducing nitrogen consumption as an example,the energy saving and consumption reducing measures are elaborated,which can provide powerful help for reducing the cost of blast furnace iron-making.Keywords:Coal Injection,Process Optimization,Energy Saving and Consumption Reduction引言高炉喷煤系统是组成炼铁生产工艺流程的重要一环,是高炉冶炼过程中以煤代焦、节约能源成本和焦炭资源的重要措施。
高炉对其生产过程的连续性、稳定可靠性要求很高,这就对喷煤的生产过程控制有很高的要求。
高炉炼铁中渣铁分离技术研究减少渣铁中的杂质含量

高炉炼铁中渣铁分离技术研究减少渣铁中的杂质含量炼铁过程中,高炉炼铁技术一直是主要的铁矿石还原冶炼方法之一。
然而,高炉炼铁过程中,渣和铁的分离问题一直是一个挑战。
其中,渣铁中的杂质含量是一个严重影响炼铁品质的问题。
本文将探讨高炉炼铁中渣铁分离技术的研究,以减少渣铁中的杂质含量。
一、高炉炼铁过程中渣铁分离问题在高炉炼铁过程中,铁矿石和燃料经过还原反应生成金属铁。
同时,一些杂质元素也存在于铁矿石中,如硫、磷、锰等。
在冶炼过程中,这些杂质元素会被部分还原,并被固定在渣中。
因此,高炉炼铁过程中需要有效地分离渣和铁,减少渣中的杂质含量。
二、渣铁分离技术的研究现状目前,研究学者们一直在寻找各种方法来解决高炉炼铁中的渣铁分离问题。
以下是一些常见的渣铁分离技术:1. 磁选技术磁选技术通过利用渣铁中铁矿石的磁性差异,将铁与渣有效地分离。
这种技术需要使用磁铁或磁场来实现。
2. 重力分离技术重力分离技术利用不同物质的密度差异,通过采用物理或机械设备,使重物质下沉,从而分离渣和铁。
3. 浮选技术浮选技术通过利用物质的表面特性,使一种物质在浮液中浮起,而另一种物质下沉。
这种技术可以用于分离渣和铁。
4. 气浮分离技术气浮分离技术利用气泡在浮液中产生的浮力,将一种物质从另一种物质中分离出来。
这种技术可以用于渣铁分离。
5. 浸出技术浸出技术通过使用溶剂,将需要分离的物质从固体中溶解出来。
这种技术也可以应用于渣铁分离。
以上是一些常见的渣铁分离技术,每种技术都有其优点和局限性。
研究者们正在不断探索创新的渣铁分离技术,以进一步降低渣铁中的杂质含量。
三、减少渣铁中杂质含量的挑战在研究渣铁分离技术的同时,我们也需要面对一些挑战,以减少渣铁中的杂质含量。
1. 操作和成本渣铁分离技术的操作和设备成本是在实际应用中需要考虑的重要因素。
一些高效的技术可能需要更多的经济投入,对实际生产造成一定的影响。
2. 杂质再分布即使通过分离技术成功减少了渣铁中的杂质含量,但在高炉冶炼过程中,杂质的再分布也会产生。
降低焦比的办法及途径
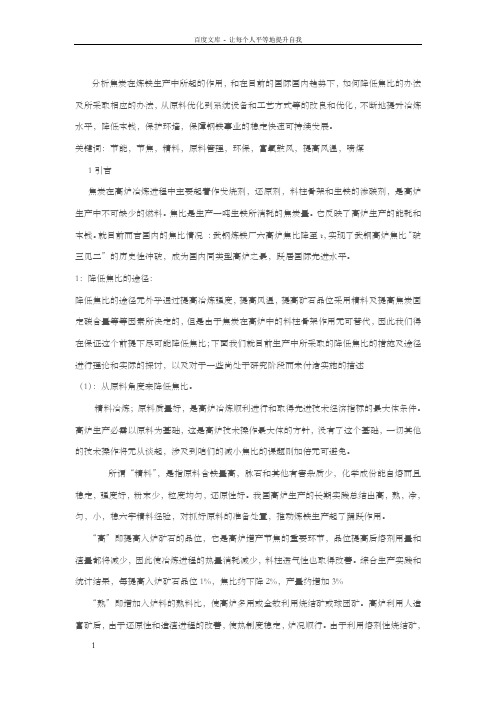
分析焦炭在炼铁生产中所起的作用,和在目前的国际国内趋势下,如何降低焦比的办法及所采取相应的办法,从原料优化到系统设备和工艺方式等的改良和优化,不断地提升冶炼水平,降低本钱,保护环境,保障钢铁事业的稳定快速可持续发展。
关键词:节能,节焦,精料,原料管理,环保,富氧鼓风,提高风温,喷煤1引言焦炭在高炉冶炼进程中主要起着作发烧剂,还原剂,料柱骨架和生铁的渗碳剂,是高炉生产中不可缺少的燃料。
焦比是生产一吨生铁所消耗的焦炭量。
它反映了高炉生产的能耗和本钱。
就目前而言国内的焦比情况:武钢炼铁厂六高炉焦比降至t,实现了武钢高炉焦比“破三见二”的历史性冲破,成为国内同类型高炉之最,跃居国际先进水平。
1:降低焦比的途径:降低焦比的途径无外乎通过提高冶炼强度,提高风温,提高矿石品位采用精料及提高焦炭固定碳含量等等因素所决定的,但是由于焦炭在高炉中的料柱骨架作用无可替代,因此我们得在保证这个前提下尽可能降低焦比;下面我们就目前生产中所采取的降低焦比的措施及途径进行理论和实际的探讨,以及对于一些尚处于研究阶段而未付诸实施的描述(1):从原料角度来降低焦比。
精料冶炼;原料质量好,是高炉冶炼顺利进行和取得先进技术经济指标的最大体条件。
高炉生产必需以原料为基础,这是高炉技术操作最大体的方针,没有了这个基础,一切其他的技术操作将无从谈起,涉及到咱们的减小焦比的课题则加倍无可避免。
所谓“精料”,是指原料含铁量高,脉石和其他有害杂质少,化学成份能自熔而且稳定,强度好,粉末少,粒度均匀,还原性好。
我国高炉生产的长期实践总结出高,熟,净,匀,小,稳六字精料经验,对抓好原料的准备处置,推动炼铁生产起了踊跃作用。
“高”即提高入炉矿石的品位,它是高炉增产节焦的重要环节,品位提高后熔剂用量和渣量都将减少,因此使冶炼进程的热量消耗减少,料柱透气性也取得改善。
综合生产实践和统计结果,每提高入炉矿石品位1%,焦比约下降2%,产量约增加3%“熟”即增加入炉料的熟料比,使高炉多用或全数利用烧结矿或球团矿。
硅铁在炼钢中的作用

硅铁在炼钢中的作用
硅铁是一种由铁和硅组成的合金,主要在炼钢过程中用作合金添加剂。
它的主要作用是改善钢铁的物理和化学性能,使其更加适合各种工业应用。
以下是硅铁在炼钢中的作用:
1. 去除氧化物
炼钢过程中钢液中会产生大量氧化物,硅铁可以作为还原剂去除这些氧化物。
氧化物会影响钢的质量,因为它们会让钢变得脆弱并降低其机械强度。
硅铁还可以与氧化物反应形成硅酸盐,这些硅酸盐可以很容易地被过滤掉。
2. 改善钢的质量
硅铁含有高硅和低碳,它们在炼钢中可以起到改善质量的作用。
硅铁作为钢的合金添加剂,可以提高钢的机械强度、耐磨性、耐腐蚀性和抗疲劳性。
特别是对冷轧钢、电动机和变压器的制造非常有益。
3. 调整钢的成分
硅铁还可以作为钢的调整剂来调整钢的成分。
硅铁可以增加钢中的硅含量,同时降低钢中的碳含量。
可以通过改变硅铁的成分来实现这一过程,例如增加硅的含量或减少碳的含量。
4. 增加钢的流动性
硅铁可以增加钢液的流动性,这使得它更容易填充模具并形成所需的形状。
硅铁能够降低钢液的表面张力,从而防止气泡和其它不均匀性在钢液中形成。
这对于精密钢铸件和高压锅炉管道等制造非常重要。
总之,硅铁在炼钢中具有多种作用。
它可以改善钢的质量和性能,同时调整钢的成分和增加钢液的流动性。
这些功能使硅铁在现代制造业中至关重要。
硅铁的冶炼过程
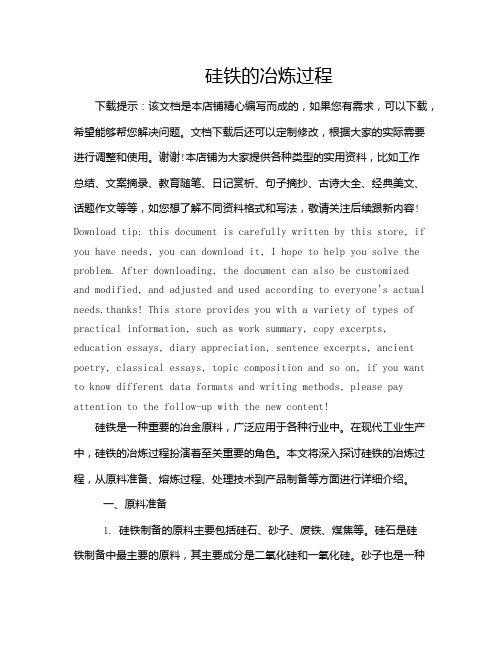
硅铁的冶炼过程下载提示:该文档是本店铺精心编写而成的,如果您有需求,可以下载,希望能够帮您解决问题。
文档下载后还可以定制修改,根据大家的实际需要进行调整和使用。
谢谢!本店铺为大家提供各种类型的实用资料,比如工作总结、文案摘录、教育随笔、日记赏析、句子摘抄、古诗大全、经典美文、话题作文等等,如您想了解不同资料格式和写法,敬请关注后续跟新内容! Download tip: this document is carefully written by this store, if you have needs, you can download it, I hope to help you solve the problem. After downloading, the document can also be customizedand modified, and adjusted and used according to everyone's actual needs.thanks! This store provides you with a variety of types of practical information, such as work summary, copy excerpts, education essays, diary appreciation, sentence excerpts, ancient poetry, classical essays, topic composition and so on, if you want to know different data formats and writing methods, please pay attention to the follow-up with the new content!硅铁是一种重要的冶金原料,广泛应用于各种行业中。
生铁硅高的原因

生铁硅高的原因
1.炉温和还原条件:
-高炉冶炼过程中,硅的还原需要较高的温度。
炉缸温度越高,越有利于SiO₂的还原为单质硅进入生铁中。
因此,如果炉温控制过高或维持在较高的水平,就会增加硅在生铁中的含量。
2.焦炭及其灰分:
-焦炭在高炉炼铁过程中不仅是能源和还原剂,其灰分中含有一定量的SiO₂。
焦炭灰分中的SiO₂活性较强,在高炉冶炼条件下更容易被还原成硅。
如果焦炭灰分中硅含量高,或是焦炭用量较大,那么由此带来的硅元素将会更多地转移到生铁中。
3.软熔带位置和过程控制:
-软熔带是指炉料开始熔化到完全熔化的过渡区域。
软熔带位置的高低直接影响铁滴下降过程中的还原和吸收行为。
软熔带位置越高,铁滴经过高温区域的时间越长,硅的还原和吸收就越充分,从而导致生铁中的硅含量上升。
4.操作参数:
-高焦比(即焦炭投入量相对于矿石的比例)、大煤气量等操作策略会导致炉内高温区范围扩大,间接促使软熔带位置升高,进而增加生铁中的硅含量。
要控制生铁中硅含量,就需要通过合理调控高炉的操作参数(如炉温、焦炭配比等)、改进焦炭品质、优化高炉冶炼工艺来实现。
在某些特定场合如电弧炉炼铁,由于其特殊的反应机制,也可能导致硅含量偏高,这是因为铁在还原SiO₂的过程中起到了催化作用。
钢铁企业炼铁厂考试题库

钢铁企业炼铁厂考试题库一、选择题1.矿石含铁量每增加1%,焦比将降低( A )。
A.2% B.4% C.8% D. 6%2.休风复风后当风量达到正常值的( D )时开始喷煤。
A.50% B.60% C.70% D.80%3.一般鼓风含氧提高( A ),风口面积应缩小1.0%~1.4%。
A.1.0% B.1.5% C.2.0% D.3.0%4.按照炉料装入顺序,装料方法对加重边缘的程度由重到轻排列为( D )。
A.正同装-倒同装-正分装-倒分装-半倒装B.倒同装-倒分装-半倒装-正分装-正同装C.正同装-半倒装-正分装-倒分装-倒同装D.正同装-正分装-半倒装-倒分装-倒同装5.炉缸边缘堆积时,易烧化( D )。
A.渣口上部 B.渣口下部 C.风口下部 D.风口上部6.高炉喷煤后综合焦比降低的原因是( B )。
A.煤粉的热值高 B.间接还原发展 C.煤气量增加 D.直接还原发展曲线的形状为:( B )。
7.边缘气流过分发展时,炉顶CO2A.双峰型 B.馒头型 C.“V”型 D.一条直线8.高炉喷吹的煤种属于( B )。
A.炼焦煤 B.非炼焦煤 C.气煤 D.肥煤9.高炉冶炼过程中,P的去向有( D )。
A.大部分进入生铁B.大部分进入炉渣C.一部分进入生铁,一部分进入炉渣D.全部进入生铁10.焦炭的堆积密度一般在( C )之间。
A.0.40t/m3~0.45t/m3 B.0.45t/m3~0.50t/m3C.0.55t/m3~0.60t/m3 D.0.60t/m3~0.65t/m311.含铁矿物按其矿物组成可分为四大类:磁铁矿、赤铁矿、褐铁矿和( D )。
A.富矿 B.贫矿 C.精矿 D.菱铁矿12.高炉内型是指高炉冶炼的空间轮廓,由炉缸、炉腹、炉腰和( D )五部分组成。
A.炉身及炉顶B.炉基及炉顶C.炉身及炉基D.炉身及炉喉13.进行富氧鼓风时,一般采用的配合操作是( A )。
A. 喷煤B. 高压C. 大风量D. 小风量14.高炉煤气和部分焦炭夺取铁矿石中的氧,这一过程称作( D )。
铁水硅高条件下转炉的冶炼操作

铁水硅高条件下转炉的冶炼操作总结及对策9月份共有188炉造双渣,喷溅16炉,喷溅率8.5%。
造成石灰消耗、钢铁料消耗升高。
下表为8月份消耗与9月份造双渣消耗对比:一、16炉喷溅原因分析:除1#炉丙班、3#炉甲班没有喷溅外,其余10个小组都有喷溅,情况如下:具体分析:1、侥幸心理没造双渣,有5炉,造成4炉小喷,1炉中喷。
2、中期化渣早,控制不住,喷溅,有4炉。
通过分析此类喷溅特点是:倒渣后,吹炼枪位较高,在8~9分钟之间化渣,此类炉渣往往在提枪后30秒左右就能化透,比正常化渣时间提前了约2~3分钟。
炉渣呈泡沫渣,这时熔池内正处于碳氧强烈反应期,生成的大量的CO气泡携带着钢渣从炉口喷出。
3、中后期温度高造成的喷溅1炉。
分析为一次性加入冷料多,熔池温度骤然下降,温度上来后造成喷溅。
4、前期小喷7炉。
主要为泡沫渣喷溅。
渣量大,渣层厚,氧化铁聚集。
碱度低,生成的气体带动炉渣涌出。
5、从总体废钢来看,废钢数量较少,平均为每炉12吨;铁块每炉平均25吨。
二、铁水硅含量高,给转炉操作带来一定影响,造成金属、温度损失大,冶炼时间延长,为保证生产的顺利进行,特对铁水硅高条件下的转炉的操作做如下规定:操枪工接到倒罐站兑铁情况后必须对硅量进行计算,铁水硅含量≥0.8 %时必须采用双渣操作,具体操作如下:1、废钢的确定:铁水硅在0.8%~1.1%之间,铁水温度在1290~1310℃之间,加入废钢10吨,渣钢5吨,铁块为12~16吨;铁水硅>1.1%,铁水温度大于1310℃,加入废钢10吨,渣钢5吨,铁块为15~20吨。
2、头批渣料的确定:要求上炉留渣量大于1/2。
在留渣量为1/2左右时,头坯料为石灰6.5吨左右,轻烧白云石2.5吨左右;全部留渣时,要求石灰5.5吨左右,轻烧白云石2.5吨左右。
以保证前期石灰尽快熔化,炉渣碱度迅速达到1.7左右,氧化镁达到8%以上,减少炉衬的浸蚀。
3、硅高铁水降枪吹炼时火焰较少,火焰呈暗红色且火焰较直。
- 1、下载文档前请自行甄别文档内容的完整性,平台不提供额外的编辑、内容补充、找答案等附加服务。
- 2、"仅部分预览"的文档,不可在线预览部分如存在完整性等问题,可反馈申请退款(可完整预览的文档不适用该条件!)。
- 3、如文档侵犯您的权益,请联系客服反馈,我们会尽快为您处理(人工客服工作时间:9:00-18:30)。
炼铁厂降硅途径探讨 24南钢科技与管理2004年第3期 炼铁厂降硅途径探讨 陈一清 (炼铁厂技术技改部) 摘要:降低生铁含硅是一项系统工作.近年来南钢高炉强化水平不断提高,利用系数稳定在3.5以上,但 生铁含硅多年来未取得进步.本文根据低硅冶炼的特点,结合高炉目前的原燃料条件和生产的具体状况,对影 响高炉降低铁水含硅的各项因素进行全面系统的分析,以探讨为高炉降硅创造条件的可能性,寻求适合我厂条 件的降硅途径. 关键词:高炉降硅系统操作管理 DiscussionfortheSiliconReducingWayinIron-makingPlant ChenYiqing (TechnicalInnovationDepartmentofIron-makingPlant) Abstract:Siliconreducingincastironisasystematicjob.Theintensivelevelofblastfurnacehasbeenincreasinglyen— hancedandtheavailabilityremainedabovethan3.5,howeverlittleprogresshasbeenmadeonthecastironsiliconcon— tentformanyyearsBasedonthecharacteristicoflowsiliconsmelting,inconjunctionwithcurrentrawmaterialandfu— elsconditionandspecificoperationsituation,theoverallsystematicanalysisforvariouselementsinfluencingsiliceous castironwillbemadeinthefollowingSOastodiscussthepossibilityofsiliconreducingandseekthesiliconreducing methodssuitabletoOUFplant. Keywords:blastfurnace;siliconreducing;system;operation;management 1概述 随着钢铁行业技术进步和生产的快速发展,降 低生铁含硅越来越被钢铁企业所重视,降低生铁含 硅可以降低炼钢氧耗和造渣剂,缩短转炉吹炼时间, 同时降低高炉焦比,提高生铁产量,是钢铁企业降本 增产的重要手段.近年来,炼铁厂利用系数不断提 高,但铁水含硅及焦比指标停滞不前,表1是炼铁厂 高炉近年来的铁水含硅及其他部分技术经济指标, 南钢高炉降硅势在必行. 低硅冶炼是高炉的关键操作技术.生铁含硅的 高低是高炉的综合操作水平的反映,更是一个钢铁 企业综合管理水平的体现.低硅冶炼是一项系统工 作,生铁含硅多少必须跟据原燃料条件,设备装备水 平和运行状况,高炉操作水平,转炉需要等来决定. 2高炉内硅的还原机理 国内外研究结果表明,硅在高炉内主要有以下 还原与氧化行为: 焦炭灰分中SiO,极其活跃,在风口前高温作用 下发生气化反应(1),渣中SiO与接触焦炭发生反 应(2),风口以下渣中SiO:与焦炭发生气化反应(3) SiO,(焦)+C:SiOT+COT……………(1) SiO(渣)+2C=[si]+2COT……………(2) SiO,(渣)+C:SiOT+COT……………(3)
2004年第3期南钢科技与管理25 风口前产生的SiO气体在上升过程中与下滴的 渗碳铁水相遇发生吸硅反应(4) SiO气+[c]:[si]+COf………………(4) 风口以下直到炉缸,渣中SiO,产生的SiO发生 反应(4),同时渣中(FeO)等氧化性物质与铁水中的 [Si]发生脱硅反应(5) 2(FeO)+[Si]=(SiO2)+2Fe……………(5) 高炉中,在风口中心线以上区域,主要是由焦炭 灰分中SiO,产生的SiO气体引起的增硅反应;在风 口中心线以下区域,主要是由渣中SiO,产生的SiO 气体引起的增硅反应,但由于渣中SiO活度很低,所 以在风口中心线以下区域渣铁之间反应(5)占主导 地位,一直到炉缸都被脱硅反应所支配. 故高炉内可粗略划分为在风口中心线以上的铁 水吸硅过程和在风口中心线以下的铁水脱硅过程. 3控制生铁含硅的途径与措施 根据高炉内硅的氧化还原机理,降低生铁含硅 主要有以下几个途径. (1)提高矿石软熔温度,降低燃料比,让软熔带 位置下移,降低滴落带高度;提高冶炼强度,加快渣 铁滴落速度;缩短反应(4)的反应时间,减少SiO气 体中Si向铁水中转移. (2)降低焦炭灰分,提高矿石品位,减少矿石中 含SiO:的脉石量,减少入炉硅源;降低风口理论燃烧 温度,控制SiO挥发速度;减少(1),(3)反应,减少 SiO气体的发生量. (3)提高焦炭质量,特别是提高焦炭的反应后强 度,减少炉缸碎焦量;改善渣铁性能,减少渣铁通过 炉缸焦炭层时间;提高炉渣氧化性;控制渣铁与焦炭 的反应(2),促进渣铁脱硅反应(5)的进行. 根据降硅的几个途径,分析南钢现有条件的利 弊,应该采取相应的管理及工艺措施. 3.1加强原燃料管理.进一步作好精料工作 加强入炉原燃料的管理,稳定原燃料质量,是高 炉降低生铁含硅的前提.近年来,南钢的原燃料状 况逐步得到改善,但由于近期高炉利用系数的迅速 提高和原燃料市场的变化,不断带来新的问题,原燃 料结构及质量的不稳定成为当前的主要矛盾,由于 原燃料的波动,高炉不得不将操作炉温留有余地, [si]数的富余量一般都达到0.1%~0.2%不等.因 此,精料工作应该首先从稳定着手,在稳定的基础上 不断提高原燃料质量.通过加强精料工作,稳定高 炉顺行,降低焦比,同时得到高的矿石软熔温度,较 窄的软熔区间和合理的渣相结构,改善炉渣性能,提 高炉缸渣铁温度,从而为降低风口理论燃烧温度提 供了可能性,最大限度地降低生铁含硅. (1)改善用料结构.目前,南钢高炉的炉料为: 烧结矿58%~62%,本厂球团25%~28%,外购球团 (3~5种)3%~5%,块矿(1~3种)8%~12%.首 先尽可能固定矿种,特别要避免同一座高炉同时吃 百家矿,减少用料结构的调整;其次,在烧结比例大 幅度下降后,尽可能采购强度好,软熔温度较高的酸 性球团矿,减少生矿和质量差低软熔温度球团矿的 配加;球团矿和生矿软熔温度较烧结矿低,降低烧结 比例会导致软熔位置升高,铁水含硅量上升.国外
26南钢科技与管理2004年第3期 实验表明,全熟料条件下,球团矿配比增加10%,铁 水含Si升高0.04%~0.06%,生矿软熔温度较烧结 矿低200~C以上,对低硅冶炼尤其不利. (2)降低入炉焦炭灰分和硫分,提高焦炭反应后 强度.焦炭灰分,硫分及反应后强度影响入炉焦比, 不利于降硅;焦炭灰分是铁水含硅的主要来源,降低 焦炭灰分能够降低风口前SiO气体的发生量,减少 炉内si的还原;降低焦炭硫分可以减轻炉渣脱硫负 担,为降硅创造条件;提高焦炭反应后强度,减少风 口前及炉缸碎焦,能够降低SiO的挥发,减少渣铁与 焦炭的表面接触而抑制si的还原.南钢使用45% 的本厂焦,灰分12.5%~13%,硫分0.65%~0.7%, 反应后强度好,55%外购焦炭,灰分13%以上,硫分 0.7%上下,反应后强度偏差;有待进一步提高. (3)降低烧结矿SiO:及FeO,提高烧结矿品位及 还原性;南钢烧结矿R,保持在2.0~2.05,MgO含量 由1.8%逐步提高至2.5%,具有较高的软熔温度和炉 渣性能,提高了炉内初渣碱度,抑制了渣铁滴落过程 中si的还原,为降硅创造了良好的条件.但在提高碱 度和M的同时,烧结矿吨铁由58%降至55.5%~ 56%,SiO,高达5%,FeO仍保持在9%左右;如能在混 匀料中使用低si高品位矿粉,进一步优化烧结工艺, 降低烧结FeO和SiO:含量,改善烧结矿的还原性能, 提高烧结矿品位,减少入炉SiO:量,能够促进高炉的 稳定顺行,降低生铁含硅,降低焦比. (4)加强原燃料管理,稳定原燃料质量.南钢原 燃料供应系统能力满足不了炼铁生产能力的快速发 展,从而带来诸多不稳定因素,严重制约了高炉降硅 进程.原燃料接收场地偏小,槽下筛分能力不足,烧 结生产能力不足,设备老化,烧结矿质量不稳等等缺 陷只能通过严格的管理来弥补. 3.2高炉降硅操作的工艺措施 降硅工作最终要通过高炉操作来实现,高炉操 作制度及其他工艺参数的选择直接影响生铁含硅, 因此,高炉操作是降硅工作的关键. (1)选择合理的造渣制度.维持较高的炉渣二 元碱度,可以降低二氧化硅活度,抑制硅的还原,提 高炉渣的脱硫能力,提高炉渣熔化温度保证炉缸热 量,但碱度过高会导致流动性变差焦比升高,提高渣 中MgO除了有以上作用外,还能改善二元碱度提高 后的炉渣流动性.南钢经过一段时期的调整,渣相 已经趋向合理,渣中A1:O控制在15%左右,MgO已 提高至10%,通过和重大合作所做的南钢高炉渣试 验得出在目前条件下,R:在1.05~1.2范围内,炉渣 粘度不超过0.8Pa?S;南钢当前几座高炉的炉渣二 元碱度基本控制在1.05~1.1之间,根据降硅需要 有继续提高的空间. (2)控制好渣铁温度.在原燃料条件和冶炼参 数相对稳定的条件下,铁水含硅与渣铁温度是相对 应的,在保证渣铁性能的前提下,适当控制渣铁温 度,降低炉缸的过热度,能够抑制si的还原,降低铁 水含硅. (3)降低高炉燃料比.降低焦比是低硅冶炼的 目的之一,同时也是低硅冶炼的必要条件.首先,降 低燃料比可以减少焦炭灰分带入炉内硅源;其次,由 于炉内矿焦比的增加,煤气利用得到改善,矿石的还 原度降低,初渣中FeO增加,使得反应(4)减少,到达 风口时参加吸硅的铁量减少,渣中(FeO)数量增加, 促使风口以下的渣铁间的脱硅反应(5)的进行,有效 降低生铁含硅. ①提高富氧率,富氧鼓风可以改善炉内的热量分 布,提高高炉冶炼的强化水平,降低燃料比.目前南钢