处理我国铝土矿的两段烧结法研究
烧结法
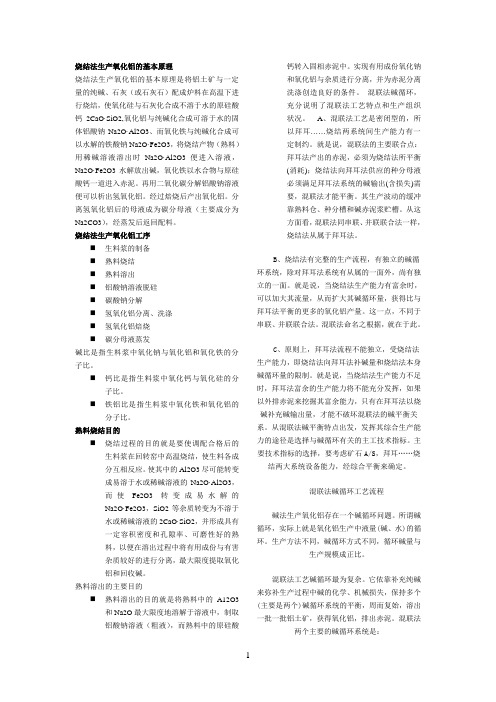
烧结法生产氧化铝的基本原理烧结法生产氧化铝的基本原理是将铝土矿与一定量的纯碱、石灰(或石灰石)配成炉料在高温下进行烧结,使氧化硅与石灰化合成不溶于水的原硅酸钙2CaO·SiO2,氧化铝与纯碱化合成可溶于水的固体铝酸钠Na2O·Al2O3、而氧化铁与纯碱化合成可以水解的铁酸钠Na2O·Fe2O3,将烧结产物(熟料)用稀碱溶液溶出时Na2O·Al2O3便进入溶液,Na2O·Fe2O3水解放出碱,氧化铁以水合物与原硅酸钙一道进入赤泥。
再用二氧化碳分解铝酸钠溶液便可以析出氢氧化铝。
经过焙烧后产出氧化铝。
分离氢氧化铝后的母液成为碳分母液(主要成分为Na2CO3),经蒸发后返回配料。
烧结法生产氧化铝工序⏹生料浆的制备⏹熟料烧结⏹熟料溶出⏹铝酸钠溶液脱硅⏹碳酸钠分解⏹氢氧化铝分离、洗涤⏹氢氧化铝焙烧⏹碳分母液蒸发碱比是指生料浆中氧化钠与氧化铝和氧化铁的分子比。
⏹钙比是指生料浆中氧化钙与氧化硅的分子比。
⏹铁铝比是指生料浆中氧化铁和氧化铝的分子比。
熟料烧结目的⏹烧结过程的目的就是要使调配合格后的生料浆在回转窑中高温烧结,使生料各成分互相反应。
使其中的Al2O3尽可能转变成易溶于水或稀碱溶液的Na2O·Al2O3,而使Fe2O3转变成易水解的Na2O·Fe2O3,SiO2等杂质转变为不溶于水或稀碱溶液的2CaO·SiO2,并形成具有一定容积密度和孔隙率、可磨性好的熟料,以便在溶出过程中将有用成份与有害杂质较好的进行分离,最大限度提取氧化铝和回收碱。
熟料溶出的主要目的⏹熟料溶出的目的就是将熟料中的A12O3和Na2O最大限度地溶解于溶液中,制取铝酸钠溶液(粗液),而熟料中的原硅酸钙转入固相赤泥中。
实现有用成份氧化钠和氧化铝与杂质进行分离,并为赤泥分离洗涤创造良好的条件。
混联法碱循环,充分说明了混联法工艺特点和生产组织状况。
A、混联法工艺是密闭型的,所以拜耳……烧结两系统间生产能力有一定制约。
烧结法
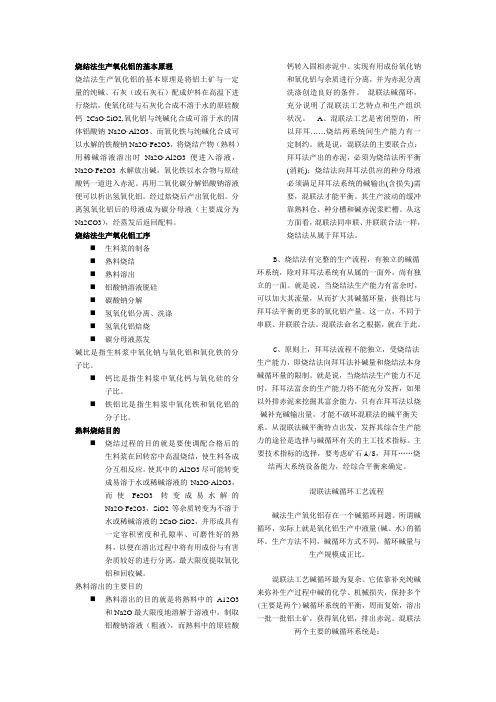
烧结法生产氧化铝的基本原理烧结法生产氧化铝的基本原理是将铝土矿与一定量的纯碱、石灰(或石灰石)配成炉料在高温下进行烧结,使氧化硅与石灰化合成不溶于水的原硅酸钙2CaO·SiO2,氧化铝与纯碱化合成可溶于水的固体铝酸钠Na2O·Al2O3、而氧化铁与纯碱化合成可以水解的铁酸钠Na2O·Fe2O3,将烧结产物(熟料)用稀碱溶液溶出时Na2O·Al2O3便进入溶液,Na2O·Fe2O3水解放出碱,氧化铁以水合物与原硅酸钙一道进入赤泥。
再用二氧化碳分解铝酸钠溶液便可以析出氢氧化铝。
经过焙烧后产出氧化铝。
分离氢氧化铝后的母液成为碳分母液(主要成分为Na2CO3),经蒸发后返回配料。
烧结法生产氧化铝工序⏹生料浆的制备⏹熟料烧结⏹熟料溶出⏹铝酸钠溶液脱硅⏹碳酸钠分解⏹氢氧化铝分离、洗涤⏹氢氧化铝焙烧⏹碳分母液蒸发碱比是指生料浆中氧化钠与氧化铝和氧化铁的分子比。
⏹钙比是指生料浆中氧化钙与氧化硅的分子比。
⏹铁铝比是指生料浆中氧化铁和氧化铝的分子比。
熟料烧结目的⏹烧结过程的目的就是要使调配合格后的生料浆在回转窑中高温烧结,使生料各成分互相反应。
使其中的Al2O3尽可能转变成易溶于水或稀碱溶液的Na2O·Al2O3,而使Fe2O3转变成易水解的Na2O·Fe2O3,SiO2等杂质转变为不溶于水或稀碱溶液的2CaO·SiO2,并形成具有一定容积密度和孔隙率、可磨性好的熟料,以便在溶出过程中将有用成份与有害杂质较好的进行分离,最大限度提取氧化铝和回收碱。
熟料溶出的主要目的⏹熟料溶出的目的就是将熟料中的A12O3和Na2O最大限度地溶解于溶液中,制取铝酸钠溶液(粗液),而熟料中的原硅酸钙转入固相赤泥中。
实现有用成份氧化钠和氧化铝与杂质进行分离,并为赤泥分离洗涤创造良好的条件。
混联法碱循环,充分说明了混联法工艺特点和生产组织状况。
A、混联法工艺是密闭型的,所以拜耳……烧结两系统间生产能力有一定制约。
熟料烧结(一)
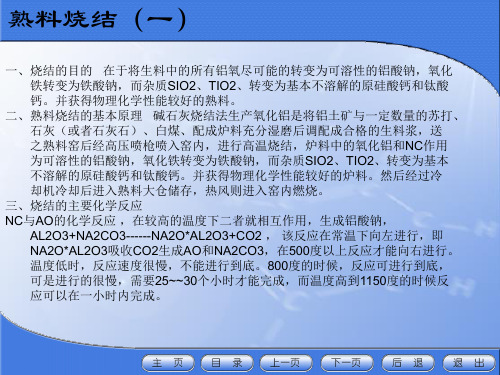
熟料烧结(一)
冷却带 从火焰后部到窑头的一带。高温熟料在冷却带由二次空气和窑头漏风冷却, 逐步冷却到1000以下下落到冷却机。 五、熟料窑结构示意图:
熟料烧结(二)之熟料窑系统
烧结温度范围和液相量控制的意义 液相量的出现和控制 在一定的烧结温度下,液相量很少,在该温度时只能使炉料体现有少许收缩,但尚 不能把粉状炉料粘结成颗粒状(叫黄料)。 提高一定温度,出现液相量较少,在凝结时,虽能把粉状炉料粘结成颗粒状,的温度,液相量达到一定的适当量时,才能出现颗粒度均匀,孔隙度大 并有一定机械强度的熟料,叫正烧结料。 又提高一定的温度,液相量较多时,产生的是致密而少孔的,机械强度很大的熟料, 叫过烧结料。 当液相量过多时,就产生坚硬无孔的,所谓熔融熟料。 生产上把产生以上近烧结熟料,正烧结熟料、过烧结熟料所对应的温度,称为近烧 结温度、正烧结温度、过烧结温度。而炉料从近烧结温度到过烧结温度所经过 的温度区间,叫烧结温度范围。一般来说,在炉料正常配方的情况下,近烧结 时液相量为5~~10%,正烧结时液相量为15~~20%,过烧结时液相量为大于 ~~20%以上。
熟料烧结(二)之熟料窑系统
熟料烧结(二)之熟料窑系统
熟料烧结(二)之熟料窑系统
熟料烧结(二)之熟料窑系统
熟料生产工艺流程图:
熟料烧结(二)之熟料窑系统
几个概念: 烘窑 烘窑的目的是什么? 耐火砖砌好后,在点火开窑前必须烘窑, 使胶泥和耐火砖的水分缓慢的蒸发出来,以加强耐火砖和胶泥之间的结合,同 时可避免耐火砖温度急剧上升和水分剧烈蒸发而引起耐火砖表面爆裂,也防止 机械设备(领圈)因温度急剧升高而涨裂。 挂窑皮 窑皮是物料煅烧后粘附在烧成带耐火砖表面形成的保护层(过烧熟料层)。 它可以防止高温区物料对耐火砖的化学侵蚀和机械磨损,从而可以延长耐火砖 的使用寿命,提高回转窑的运转周期,同时可以增强传热效率,稳定窑的热工 制度,减少散热损失,所以挂好和维护好窑皮是保证优质高产的前提,而挂好 第一层高温窑皮尤为重要。 窑皮形成的机理: ;炉料在回转窑中由窑尾向窑头移动,当进入到分解带前沿时, 在一定温度下开始出现液相,随着温度升高液相量也相应增加,当增加到一定 数量时,炉料有黏结性,物料和耐火砖接触时,由于耐火砖向外散热,液相和 部分炉料就黏结在耐火砖表面而形成第一层窑皮,由于炉料推进,同时形成第 二层窑皮,第二层窑皮黏结后,第一层窑皮因为温度下降而凝固,这个过程继 续下去窑皮愈厚,当厚到一定程度时,由于窑皮的热负荷增加,窑皮表面温度 升高,液相黏度逐渐减小,由于向外冷却困难,液相过热,粘性不足,此时窑 皮就会停止生成。 结圈 炉料烧结过程中,由于液相的出现和凝结,在烧结带前后两端形成了致密而 高于窑皮的结圈称前结圈和后结圈。
金属冶炼中的烧结与煅烧技术
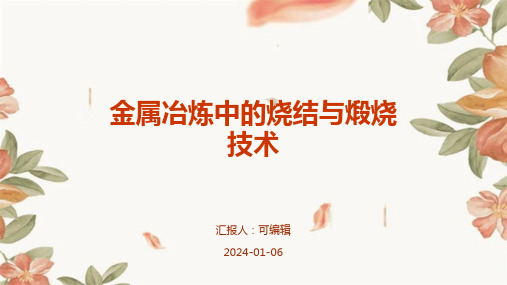
03
烧结与属冶炼中的重要环节,通过将 铁矿粉、熔剂、燃料等原料按照一定比例混 合,在高温下进行烧结,得到具有一定强度 和冶金性能的烧结矿。
烧结过程中,铁矿粉中的氧化铁被还原成铁 ,同时加入的熔剂和燃料等发生化学反应, 生成液相填充在矿粉颗粒之间,使烧结矿具 有较好的强度和冶金性能。
煅烧的原理与工艺流程
原理
煅烧的原理是利用高温下物料的物理和化学变化,使物料内 部的组分和结构发生变化,从而达到所需的性能和成分。
工艺流程
煅烧工艺流程一般包括原料准备、预热、加热、保温、冷却 等阶段。根据不同的物料和需求,煅烧工艺流程会有所不同 。在煅烧过程中,需要控制温度、气氛、时间等工艺参数, 以保证获得最佳的煅烧效果。
感谢您的观看
THANKS
和冶金性能。
铜矿烧结技术广泛应用于铜冶炼行业, 能够提高铜的产量和质量,降低能耗和
生产成本。
锌矿烧结
锌矿烧结是提取锌的一种方法,通过将锌矿石、熔剂、燃料等原料混合后进行高温 烧结,得到锌焙砂,再从中提取锌。
锌矿烧结过程中,锌矿石中的氧化锌被还原成锌,同时加入的熔剂发生反应,生成 液相填充在矿石颗粒之间,使烧结块具有较好的强度和冶金性能。
目的
烧结的目的是为了使物料中的各个组分或颗粒相互融合,提高其机械性能、物理性能和化学性能,以满足各种 工业应用的需求。
烧结技术的发展历程
古代烧结
早在古代,人们就已经开始使用烧结技术, 如陶瓷、砖瓦等材料的制作。
近代烧结
随着科技的发展,人们开始研究各种新型的 烧结方法和材料,如金属粉末烧结、陶瓷复 合材料等。
煅烧技术的发展历程
古代煅烧技术
现代煅烧技术
古代煅烧技术主要依靠自然条件下的 燃烧和焙烧,如烧制陶器、砖瓦等。
氧化铝冶炼工艺流程简介
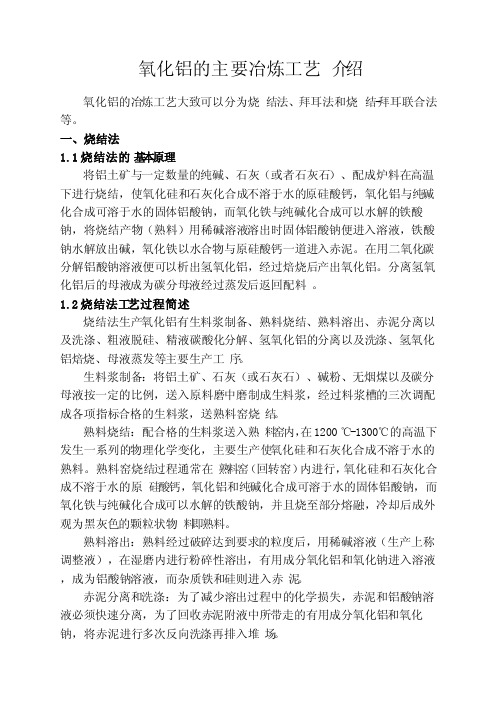
氧化铝的主要冶炼工艺介绍氧化铝的冶炼工艺大致可以分为烧结法、拜耳法和烧结-拜耳联合法等。
一、烧结法1.1烧结法的基本原理将铝土矿与一定数量的纯碱、石灰(或者石灰石)、配成炉料在高温下进行烧结,使氧化硅和石灰化合成不溶于水的原硅酸钙,氧化铝与纯碱化合成可溶于水的固体铝酸钠,而氧化铁与纯碱化合成可以水解的铁酸钠,将烧结产物(熟料)用稀碱溶液溶出时固体铝酸钠便进入溶液,铁酸钠水解放出碱,氧化铁以水合物与原硅酸钙一道进入赤泥。
在用二氧化碳分解铝酸钠溶液便可以析出氢氧化铝,经过焙烧后产出氧化铝。
分离氢氧化铝后的母液成为碳分母液经过蒸发后返回配料。
1.2烧结法工艺过程简述烧结法生产氧化铝有生料浆制备、熟料烧结、熟料溶出、赤泥分离以及洗涤、粗液脱硅、精液碳酸化分解、氢氧化铝的分离以及洗涤、氢氧化铝焙烧、母液蒸发等主要生产工序。
生料浆制备:将铝土矿、石灰(或石灰石)、碱粉、无烟煤以及碳分母液按一定的比例,送入原料磨中磨制成生料浆,经过料浆槽的三次调配成各项指标合格的生料浆,送熟料窑烧结。
熟料烧结:配合格的生料浆送入熟料窑内,在1200℃-1300℃的高温下发生一系列的物理化学变化,主要生产使氧化硅和石灰化合成不溶于水的熟料。
熟料窑烧结过程通常在熟料窑(回转窑)内进行,氧化硅和石灰化合成不溶于水的原硅酸钙,氧化铝和纯碱化合成可溶于水的固体铝酸钠,而氧化铁与纯碱化合成可以水解的铁酸钠,并且烧至部分熔融,冷却后成外观为黑灰色的颗粒状物料即熟料。
熟料溶出:熟料经过破碎达到要求的粒度后,用稀碱溶液(生产上称调整液),在湿磨内进行粉碎性溶出,有用成分氧化铝和氧化钠进入溶液,成为铝酸钠溶液,而杂质铁和硅则进入赤泥。
赤泥分离和洗涤:为了减少溶出过程中的化学损失,赤泥和铝酸钠溶液必须快速分离,为了回收赤泥附液中所带走的有用成分氧化铝和氧化钠,将赤泥进行多次反向洗涤再排入堆场。
烧结法的原理和基本流程

烧结法的原理和基本流程第一节烧结法的原理随着矿石铝硅比的降低,拜耳法生产氧化铝的经济效果明显恶化。
对于铝硅比低于7的矿石,单纯的拜耳法就不适用了。
处理铝硅比在4以下的矿石,碱石灰烧结法几乎是唯一得到实际应用的方法。
在处理SiO2含量更高的其它炼铝原料时,如霞石、绢云母以及正长石时,它也得到应用,可以同时制取氧化铝、钾肥和水泥等产品,实现了原料的综合利用。
据报导,国外以霞石为原料的烧结法企业,由于原料综合利用,实现了无废料生产,氧化铝的生产成本反而最低。
在我国已经查明的铝矿资源中,高硅铝土矿占有很大的数量,因而烧结法对于我国氧化铝工业具有很重要的意义。
我国第一座氧化铝厂——山东铝厂就是采用碱石灰烧结法生产的。
它在改进和发展碱石灰烧结法方面作出了许多贡献,其Al2O3的总回收率,碱耗等指标都居于世界先进水平。
法国人勒·萨特里在1858年提出了碳酸钠烧结法,即用碳酸钠和铝土矿烧结,得到含固体铝酸钠Na2O· Al2O3的烧结产物。
这种产物称为熟料或烧结块,将其用稀碱溶液溶出便可以得到铝酸钠溶液。
往溶液中通入CO2气体,即可析出氢氧化铝。
残留在溶液中的主要是碳酸钠,可以再循环使用。
这种方法,原料中的SiO2仍然是以铝硅酸钠的形式转入泥渣,而成品氧化铝质量差,流程复杂,耗热量大,所以拜耳法问世后,此法就被淘汰了。
用碳酸钠和石灰石按一定比例与铝土矿烧结,可以在很大程度上减轻SiO2的危害,使Al2O3和Na2O的损失大大减少。
这样就形成了碱石灰烧结法。
在处理高硅铝土矿时,它比拜耳法比越。
除了这两种烧结法外,还有单纯用石灰与矿石烧结的石灰烧结法,它比较适用干处理粘土类原料,特别是含有一定可燃成分的煤矸石、页岩等。
这时原料中的Al 2O 3,烧结成铝酸钙,经碳酸钠溶液溶出后,可得到铝酸钠溶液。
目前用在工业上的只有碱石灰烧结法。
它所处理的原料有铝土矿、霞石和拜耳法赤泥。
这些炉料分别称为铝土矿炉料。
2024年氧化铝生产中结垢清理的安全技术(三篇)

2024年氧化铝生产中结垢清理的安全技术我国铝土矿高铝、高硅、低铁的特点,决定了烧结法氧化铝生产工艺在我国有着非常重要的地位,特别是随着高品位铝土矿的日益匮乏,烧结法处理低品位铝土矿的优越性日益凸显出来。
而烧结法存在生产工艺流程复杂、工艺能耗高等不利因素,尤其是湿法系统的结垢问题,极大地加重了清理检修作业工作量,成为安全生产的制约因素。
脱硅器的清理方法在湿法系统的脱硅环节,溶液流经的每一根管道、每一个器壁和罐体都极易结垢。
各个氧化铝生产企业都在积极探索如何减轻脱硅系统的结垢量和清理脱硅器结垢的有效方法。
中国铝业中州分公司采用的就是烧结法生产氧化铝。
脱硅器是湿法系统的关键设备之一,属于密闭性的压力容器。
中州分公司氧化铝年产量从最初的20万t逐年递增,提升到现在年产80万t的生产能力,而脱硅器则仅在最初的4组直接加热脱硅器的基础上,增加了2组间接加热脱硅器,产量大幅度提高,清理作业也日渐频繁。
时间紧,工作量大,脱硅系统面临的压力愈来愈大。
如何采用行之有效的方法安全清理脱硅器,中州分公司在十几年的生产实践中,进行了积极的探索。
中州分公司目前运用的直接加热脱硅器和间接加热脱硅器规格分别为2.6m×9.5m和2.8m×12m,平均2个月就要清理一组,一般是5-7个脱硅罐,其结垢具有质密、厚度均匀等显著特点。
常用的脱硅器清理方法有以下3种。
1.人工清理法人工清理,就是在脱硅罐体内搭架子,然后人工用大锤等器具击打器壁,使结垢脱落。
人工法清理结垢较为彻底,但作业时间长,严重影响大液量生产的组织。
尤其是清理罐体上部的结垢时,一般都在十几米的高空作业,极易造成人员伤害。
2.爆破清理法利用炸药爆破原理清理结垢,对罐体内厚结垢非常有效,但对目前中州分公司脱硅器质密、均匀的结垢不适用,且爆破需要有专门的爆破作业人员,爆破作业杀伤力大,对脱硅器损伤比较大。
3.火烧清理法火烧清理法对密闭性容器的清理非常有效,它清理速度快,而且效果好。
中等品位铝土矿石灰烧结法提铝试验研究
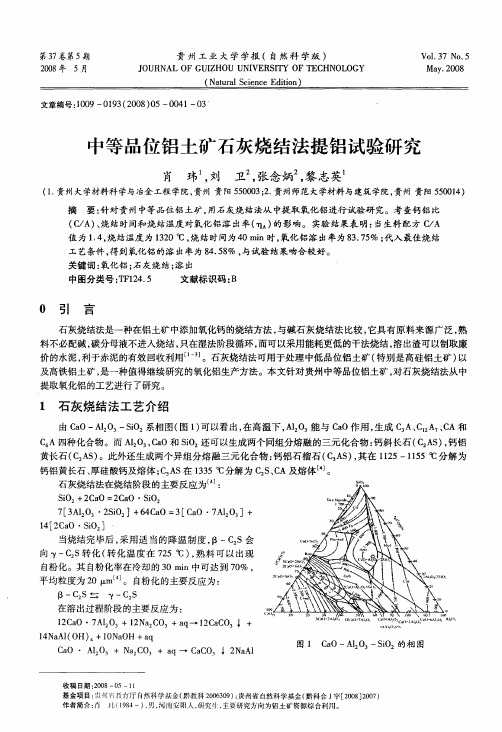
.
1 N A ( H) +1 N O +a 4 a 1O 4 0 a H q C O ・A 2 + N 2 O +a a 1 O aC q— C C 1』2 a l aO N A
图 1 C O—A 2 3 SO a 1 一 i2的相 图 O
收稿 日期 :0 8— 5—1 20 0 l
自粉 化 。其 自粉化 率在 冷却 的 3 i 0mn中可 达到 7 % , 0 平 均粒 度为 2 m 。 自粉 化 的主要 反应 为 : 0I x
p—C S! 2 ; 一 2 CS
在溶出过程阶段的主要反应为:
1 C O ・ A 2 3+1 N 2 O +a 一 1 C C 3J + 2a 7 1 O 2 aC 3 q 2 a O
S O2+2 O =2Ca ・S O2 i Ca O i
7 3 1 3 2i2 6 C O= [ a 7 1 3 [A2 ・ S ]+ 4 A 3 C O・ A2 ]十 O O O 1 1C O・ i2 42 A S ] O 当烧结完毕后 , 采用适 当的降温制度 , p—cs会 : 向 一Cs转 化 ( 化 温 度 在 75o , 料 可 以 出 现 : 转 2 C) 熟
l 石 灰 烧 结 法 工 艺介 绍
由 C O— I , SO 系相 图( 1 可 以看 出 , 高 温 下 , I 3 与 C O作 用 , a A: 一 i: O 图 ) 在 A 能 O a 生成 CA、 。 C 和 , C: 、A A CA 四种 化合 物 。而 A ,C O和 SO 还 可 以生成两个 同组 分熔 融 的三 元 化合 物 : IO ,a i 钙斜 长 石 ( : S , 铝 CA )钙
第3 卷第5 7 期
20 年 5月 08
- 1、下载文档前请自行甄别文档内容的完整性,平台不提供额外的编辑、内容补充、找答案等附加服务。
- 2、"仅部分预览"的文档,不可在线预览部分如存在完整性等问题,可反馈申请退款(可完整预览的文档不适用该条件!)。
- 3、如文档侵犯您的权益,请联系客服反馈,我们会尽快为您处理(人工客服工作时间:9:00-18:30)。
成 份
Al2 O3
SiO2
TiO2
Fe2 O3
CaO
A/ S
含量 % 67. 10
12. 45
3. 49
1. 40
0. 60
5. 4
纯碱 :化学纯
试验采用三因子三水平 L 9 (34) 的正交试验 ,结果见表 2
表 2 Ⅰ段烧结正交实验结果
条件 序号
碱 比 R
烧结温度 T 、℃
ηA
= Al2O3熟
-
Al2O3泥·CaO熟/ Al2O3熟
CaO泥
×100
%;
ηN
= Na2O熟
-
Na2O泥·CaO熟/ CaO泥 Na2O熟
×100 % ;
ηA 1
=
0. 153
-
0. 0276 ×0. 0. 1535
389/
0.
5244
= 86. 66
% ; (与表
5
的试验结果相符)
ηA 2
=
文章编号 :100920193 (2003) 0520009204 Ξ
处理我国铝土矿的两段烧结法研究
何润德 ,车 蓉 ,毛小浩 ,黎志英 ,张念炳
(贵州工业大学冶金系 ,贵州 贵阳 550003)
摘 要 :研究了处理 A/ S = 5 ±的铝土矿两段烧结工艺 。试验表明 , Ⅰ段烧结最佳条件 :碱比为 112 、烧结温度 1100 ℃、烧结时间 40min ; Ⅱ段烧结最佳条件 :钙比 2125 、烧结温度 1200 ℃、烧结 时间 30min ; Ⅰ段溶出温度高于 95 ℃后脱硅作用明显 ,溶液硅量指数可达 400 以上 ;两段烧结 工艺氧化铝溶出率 ηA标可达 98122 % ,总的化学碱耗为 11126kg. 关键词 :两段烧结法 ; Ⅰ段烧结 ;溶出脱硅 ; Ⅱ段烧结 中图分类号 : TF821 文献标识码 :A
ηA = 0. 004375 C2 + 0. 26091665 C + 82. 44123
表 9 计算结果
T ,min ηA , %
20 86. 045
30 86. 635
40 86. 417
50 85. 393
60 83. 56
由上表可见 ,时间的影响不大 ,烧结时间 30min 左右均可 。
5 结 论
表 6 Ⅱ段烧结验证性试验分析结果
成份 , %
试样 熟料1
赤泥1
Al2 O3
15. 35 2. 76
SiO2
7. 84 25. 37
Fe2 O3
2. 42 3. 18
CaO
38. 90 52. 44
TiO2
5. 75 7. 36
Na2 O
试验条件
11. 19 0. 88
烧 结 条 件 : 钙 比 2125 , 1200 ℃, 20nim ; ( 标 准 溶
© 1995-2006 Tsinghua Tongfang Optical Disc Co., Ltd. All rights reserved.
1 0
贵 州 工 业 大 学 学 报 (自然科学版)
(表接上页) 6 7 8 9
1. 1
1200
20
1. 2
1000
60
1. 2
(下转 23 页)
© 1995-2006 Tsinghua Tongfang Optical Disc Co., Ltd. All rights reserved.
件下溶出 。考察钙比 、烧结温度 、烧结时间对氧化铝溶出率的影响 ,从而得出 Ⅱ段烧结工艺的最佳条件 。最
后以最佳条件进行验证性试验 。
2. 2 试验结果
在单因素试验的基础上 ,采用了三因子三水平 L9 (34) 的正交试验 ,结果见表 5.
表 5 Ⅱ段烧结正交试验结果表
条件 序号
碱 比 Rc
ηA = - 443. 5 A 2 + 2009. 15 A - 2188. 9511
表 7 计算结果
RC ηA , %
2. 05 66. 0
2. 15 80. 643ຫໍສະໝຸດ 2. 25 86. 418
2. 35 83. 323
2. 45 71. 3576
计算结果表明 ,钙比 2125 为佳 。钙比太高 ,多余的 CaO 在熟料中游离存在 ,会在溶出时造成 Al2O3 损 失 ;钙比太低 ,由于 N A S 2 不能完全分解而造成 Al2O3 和 Na2O 的损失[2 ] 。 4. 2. 2 温度对氧化铝溶出率的影响 (钙比为 2. 25 ,时间为 40min 时)
= 6. 5833 (kg -
Na2O/ t
-
Al2O3)
折合成纯 Na2CO3 为 11. 255kg/ t - Al2O3
4 试验结果讨论
4. 1 Ⅰ段烧结试验 烧结时间为 40min 时 ,烧结温度 、碱比 R 对铝土矿溶出率的影响曲线 : 由图 1 可看出 ,碱比等于 112 时 ,氧化铝溶出率最高 。碱比小于或大于 112 时 ,氧化铝溶出率降低 。当
ηA = - 0. 00032 B 2 + 0. 781466 B - 390. 542
表 8 计算结果
T, ℃
1100
1120
1160
1200
1240
1280
ηA , %
81. 8712
83. 29
85. 366
86. 418
86. 44
85. 44
计算结果表明 ,烧结温度 1200 ℃为宜 。温度低烧结反应进行不彻底 ;温度稍高对氧化铝的溶出率增加甚微 , 反而会增加能耗 ;温度再升高物料熔化使氧化铝溶出率降低 。 4. 2. 3 时间氧化铝溶出率的影响 (钙比为 2125 ,温度为 1200 ℃时)
碱比过低时 ,加入的碱不足以与矿中的氧化铝反应完全 ,部分氧化铝进入赤泥中造成溶出率降低 。当碱比
© 1995-2006 Tsinghua Tongfang Optical Disc Co., Ltd. All rights reserved.
1 2
贵 州 工 业 大 学 学 报 (自然科学版)
0 引 言
我国铝土矿的特点是高铝 、高硅 、低铁 、低铝硅比[4 ] 。铝硅比大于 7 的能够用纯拜耳法生产的铝土矿仅 占 10 % ,60 %以上的铝土矿铝硅比在 4~6 之间[3 ] 。贵州省有丰富的铝矿资源 ,但其特点也与上述相同 ,故 寻求一种较合理的处理中低品位铝土矿的方法 ,对我国以及地处我国西部大开发区域的贵州也有着十分重 大的现实意义和战略意义 。
烧结时间 τ、m i n
1
1. 0
1000
20
2
1. 0
1100
40
3
1. 0
1200
60
4
1. 1
1000
40
5
1. 1
1100
60
ηAl2O3 %
76. 26 82. 54 79. 23 82. 00 84. 51
(表续下页)
Ξ 收稿日期 :2003 - 06 - 12 基金项目 :贵州省科学基金资助项目[ 合同号 : (2001) 3072 ]
2003 年
图 1 烧结时间 (t = 40min) 时 ,温度 ( T) 、碱比 ( R) 对溶出率的影响曲线 过大时 ,过剩的碳酸钠在熟料溶出时进入溶液 ,会因碳酸纳浓度过高而增加二次反应而降低氧化铝的溶出 率[5] 。
烧结温度以 1100 ℃为好 ,因为烧结温度过低 、过高时 ,会使熟料欠烧或过烧 ,均使ηAl2O3降低 。 4. 2 Ⅱ段烧结试验 4. 2. 1 钙比对氧化铝溶出率的影响 (温度为 1200 ℃、时间为 40min 时)
SiO2
TiO2
Fe2 O3
含量 % 24. 62
28. 8
8. 37
3. 40
CaO 0. 80
Na2 O 17. 76
石灰 :化学
主要仪器设备 :马弗炉 ( SX - 4 - 13) 、增力电动搅拌机 、超级恒温水浴锅 、分析天平 ( T G328A) . 试验方案 :将 Ⅰ段赤泥按不同钙比配入石灰 ,和匀 、制团后置于刚玉坩埚中经马弗炉烧结后 ,在标准条
相关成份 %
Al2 O3
SiO2
25. 80
29. 43
2 85
8. 00126 45. 37
8. 72 2. 30490 26. 55
29. 07
3 90
8. 00086 45. 37
8. 72 2. 32838 25. 21
29. 67
4 95
7. 9942 45. 37
8. 72 2. 24302 26. 06
11
ηA = - 443. 5 A 2 + 2009. 15 A - 0. 00032 B 2 + 0. 7814666 B - 0. 0040375 C2
+ 0. 26091665 C - 2669. 887766 式中 : A —钙比 ; B —温度 ; C —时间 。
3 试验结果计算
在以上试验的基础上 ,又选择最好的条件做了进一步试验 ,试验结果如表 6
烧结温度 T 、℃
烧结时间 τ、min
ηA l2 O3 , %
1
2. 05
1100
20
62. 43
2
2. 05
1150
40
62. 46
3
2. 05
1200
60
61. 85
4
2. 25
1100
40
80. 58
5
2. 25
1150